Limitless possibilities
Evan Zabawski | TLT From the Editor November 2016
Letting go of static alarm limits might be for the best.
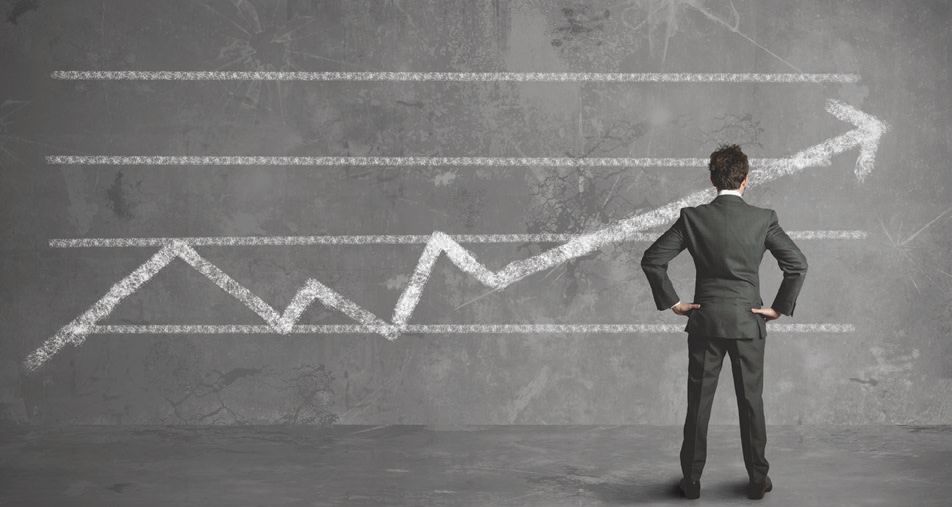
Trending provides a way to catch problems even the most up-to-date and specific limits will miss.
© Can Stock Photo Inc. / alphaspirit
A FREQUENTLY ASKED QUESTION TO AN OIL ANALYSIS LAB is, “What is an acceptable level for ____?” The answer is invariably it depends. There was a time when finite answers could be given, but times have changed.
The beginnings of the in-service fluid analysis industry dealt mostly with large fleets of mobile assets, and the vast majority of the samples were taken during oil drains that occurred at reasonably consistent intervals. Examining sample data from a high number of identical assets taken at the same interval lends itself to establishing normal ranges and reasonable alarm limits.
Where this concept begins to fall apart is when samples are taken between oil drains and/or when oil drain intervals are extended. An alarm based on data from 500 hours of service will be of little value to samples taken at 250 or 1,000 hours. One key factor is the starting point; after an oil has been drained it never resets to exactly the values of virgin fluid.
The primary cause is referred to as oil hang-up, namely the approximately 25% volume of old oil that is retained between oil changes. Samples pulled immediately after an oil change confirm that upward of 40% of the wear metals and contaminants will be carried over.
Therefore, a mid-interval sample trends normally at around 75% of levels found at drain, not 50%, and a sample taken after doubling the drain interval shows around a 50% increase rather than 100%.
Even consistent sampling/drain intervals have their issues. As an example, consider three sets of data where the alarm is set to go off when the value exceeds 20: Dataset A—2, 2, 2, 2, 2, 18; Dataset B—11, 13, 15, 17, 19, 21; and Dataset C—18, 19, 20, 21, 22, 23. Though Dataset A has the lowest final value, it has the greatest overall change and rate of change; Dataset C has the highest final value and the lowest overall change and rate of change. What this shows is sometimes the most significant change will not set off alarms, while relatively insignificant changes can, and, in doing so, will produce a cry wolf effect.
One other major consideration is sump volume; a similar asset with twice the volume of fluid in it will require twice as much wear or contamination to achieve the same value. Lubricant type or grade variances also become a factor for wear metals; so the number of variables relating to it depends becomes practically unmanageable.
What is needed to differentiate a false alarm from a true alarm is to supplement limits with trending. Trending provides a way to catch problems even the most up-to-date and specific limits will miss. It has long been my belief that routine oil analysis is all about establishing what is normal, and then waiting for the results to not be normal. Whatever normal is will vary from asset to asset and change over time, but a moving trend will stay abreast of individual traits and variations from operation.
The one caveat is that trending relies on reasonably consistent intervals, which should not be an issue to users dedicated to getting the most from their condition monitoring program. They should understand that neglecting to pull samples consistently (by location, procedure and timing) will have an adverse effect on the value of the data.
The best advice I can give regarding interpreting data from in-service fluid analysis is to look at the trend first and treat any non-regulatory limits that exist as a guide. Any deviation from trend—even if it looks better—that cannot easily be explained by recent activity must be either noted and monitored or investigated, depending on perceived severity and criticality.
Evan Zabawski, CLS, is the senior technical advisor for TestOil in Calgary, Alberta, Canada. You can reach him at ezabawski@testoil.com.