KEY CONCEPTS
•
Well-planned inventory consolidation can increase efficiency and reduce errors in grease purchasing, application and storage.
•
Greases with comparable characteristics are not necessarily compatible with each other or with the machines that they lubricate.
•
The cost of repairs and downtime, loss of product or possible safety hazards can far exceed the cost of using a specialty grease that prevents mechanical failures.
How do industrial and transportation operations reconcile the need to reduce lubricating grease costs with the desire to optimize equipment performance and avoid costly component failures? Inventory consolidation, which involves using fewer grease products to cover a range of applications, might be the answer. Eliminating specialty greases that are only used in a few applications can reduce costs and waste—infrequently used greases can reach their expiration date before an entire container is used—and it reduces the risk of accidentally using the wrong grease or cross-contamination between incompatible greases.
Some chemical plants have reported as many as 80,000 lubrication points, and their lubricant inventories may include as many as 25 brands of more than 200 unique products.
1 Vehicle fleets may use several different greases for the chassis, fifth wheel and trailer axle hubs.
2 Food processing plants use specialized greases for applications that might involve incidental contact with food products and a variety of other greases for the bearings and gears in other locations in the plant.
3 In some cases, a careful inventory of the greases currently in use, compared with the requirements of specific applications, can reveal opportunities to switch to a few types of multipurpose grease. However, a “one-size-fits-all” grease doesn’t exist, and for critical operations and equipment, the cost of a mechanical failure can far exceed the cost of even an expensive specialty grease.
Considering a change
Multipurpose greases work well in many applications in the construction, agricultural and automotive industries. In these and similar applications, bearings and gears operate under moderate speeds, loads and temperatures, and there is little risk of contaminating food or pharmaceutical products or contact with sensitive environments.
There are different definitions of multipurpose greases, but the formulations usually include lithium- or calcium-based thickeners and various combinations of extreme pressure (EP) and antioxidant additives, says STLE member Dr. Wei Dai, principal product development engineer at The Timken Co. in North Canton, Ohio. He notes that over the past four years, reliance on lithium and calcium greases has remained steady—a small decrease in lithium greases has been balanced by a corresponding small increase in calcium greases.
4 “I don’t see a big change on the production side of the multiuse greases,” he says, “but industry needs more specialty greases.”
Dai explains that many industrial and end-user applications involve higher loads, greater speeds and greater temperature extremes now, relative to the past. Not all applications require a single-use grease formulation; high-performance multipurpose greases can often provide the required performance. Thus, an NLGI steering committee is developing specifications for high-performance, multiuse (HPM) greases for specific applications. Currently, certification specifications for the HPM core and four performance enhancement categories have been published, covering water resistance, saltwater corrosion resistance, high-load-carrying capacity and low temperature performance.
5 Two additional categories—long life applications and high-temperature performance—are in progress, says Dai.
Other factors to consider include the effect of using a different grease on power consumption and the service life of a bearing or gear. A grease with a very viscous base oil requires more power to drive bearings and gears. A thick oil film also can increase power consumption by providing more resistance to shearing and more fluid friction. On the other hand, an oil or grease that is too thin provides insufficient lubrication, which increases friction and heat and causes premature wear or damage to the bearing or gear. Mixing two incompatible greases, for example, during a rolling changeover, can have a significant effect on the amount of base oil that a grease releases into the contact zone, even when the two greases are rated comparably with respect to performance and applications.
OEMs have invested significant effort into studying and testing the performance of various grease formulations in their equipment
(see Figure 1). “It’s difficult to find a perfect grease,” Dai says, so OEMs draft their own specifications using standard test methods and in-house tests, and they work with formulators to come up with recommendations for products already on the market or custom formulations. He adds that typically, no one grease significantly outperforms the others on all performance criteria. The OEM publishes rankings for various formulations with respect to individual properties, and the customer chooses a product based on their priorities and the specific characteristics of their application. Many OEMs can perform rig testing with a customer’s replacement grease candidate to verify its performance characteristics with a specific machine or component under the customer’s operating conditions.
Figure 1. Roll stability tests (ASTM D1831) measure mechanical stability by rotating a grease sample in a cylinder containing a roller. Cone penetration tests are run before and after rolling, and the results are compared. Figure courtesy of The Timken Co.
Comparability and compatibility
Dai says that he gets frequent inquiries from customers asking for recommendations or wanting to know if they can switch to a different type of grease for a given application. This may be because of recent increases in lithium prices or because a grease that they are currently using has become difficult to find—or discontinued entirely.
Before switching greases, customers must understand the difference between comparability and compatibility. Comparable products share similar characteristics, enabling their use in components of similar make, model and application. However, even greases with the same NLGI consistency and the same base oils may not be compatible with each other or with the mechanical parts they come into contact with. Incompatible greases can react with each other to form a hard mass that does not release sufficient oil to lubricate the part, or one grease can soften another, causing grease leakage. Some greases contain additive packages that can react with and damage seals, gaskets and metallic parts.
On the other hand, greases with compatible chemistries, which can work together without conflicting base oils, thickeners or additive packages, are not necessarily comparable. Thus, any planned grease switchover requires taking the operating requirements of the component or system into account as well as the chemistries of the new and old greases. This not only ensures reliable operation after the switchover, but it also determines the procedure used for the switchover itself. Comparable greases with low risk of incompatibility may be switched gradually, using a rolling switchover, whereas less compatible greases may require draining and flushing the old grease out of system before introducing the new grease.
6
Dai cautions that end-users should not rely entirely on published compatibility charts. “If the chart says the greases are not compatible, then they are definitely not compatible.” But if the chart says they are compatible, he adds, that’s not a firm guarantee. The best option when changing greases is to completely clean the old grease out of the system before adding the new grease, Dai says. If that’s difficult, however, end-users should run their own compatibility tests or have their supplier or other testing lab run them before mixing greases in their machines.
Specialty greases
For demanding or mission-critical applications, reliable performance and long service life take priority over grease purchase costs
(see Evaluating Criticality). For example, maintenance and repairs for operations in remote locations can be extremely costly, and site visits must often be scheduled far in advance. Dai cites the example of greases for wind turbine main shaft bearings, where the cost of a part failure can greatly exceed the purchase price of a specialty grease with the required characteristics. These large bearings operate at slow speeds under high loads, in outdoor environments that may experience wide swings in ambient temperature—and for offshore turbines, exposure to saltwater spray.
7
Evaluating criticalityA
For critical assets, reliable performance can take priority over lubricant cost. Some factors to consider when assessing the criticality of a machine or operation:
•
Employee health and safety
•
Customer impact
•
Environmental impact
•
Production cost impact
•
Cost and history of repair
•
Cost of long-term maintenance
•
Mean time between failures
•
Cost of machine replacement
•
Spare parts availability.
A. Johnson, M. (2011), “Building a reliability centered lubrication program,” TLT, 67 (6), pp. 35-42. Available here.
Grease performance also takes priority over price in situations where failures can endanger human lives. Dai cites the example of Alaska Airlines Flight 261, which crashed into the Pacific Ocean in January 2000, killing all 88 persons on board. The National Transportation Safety Board’s (NTSB) investigation concluded that inadequate lubrication had caused a horizontal stabilizer to stick and then release in such a way that the aircraft went into an almost vertical nosedive. Despite the pilots’ best efforts to right the plane, it hit the water at high speed, destroying the aircraft on impact
(see Figure 2).
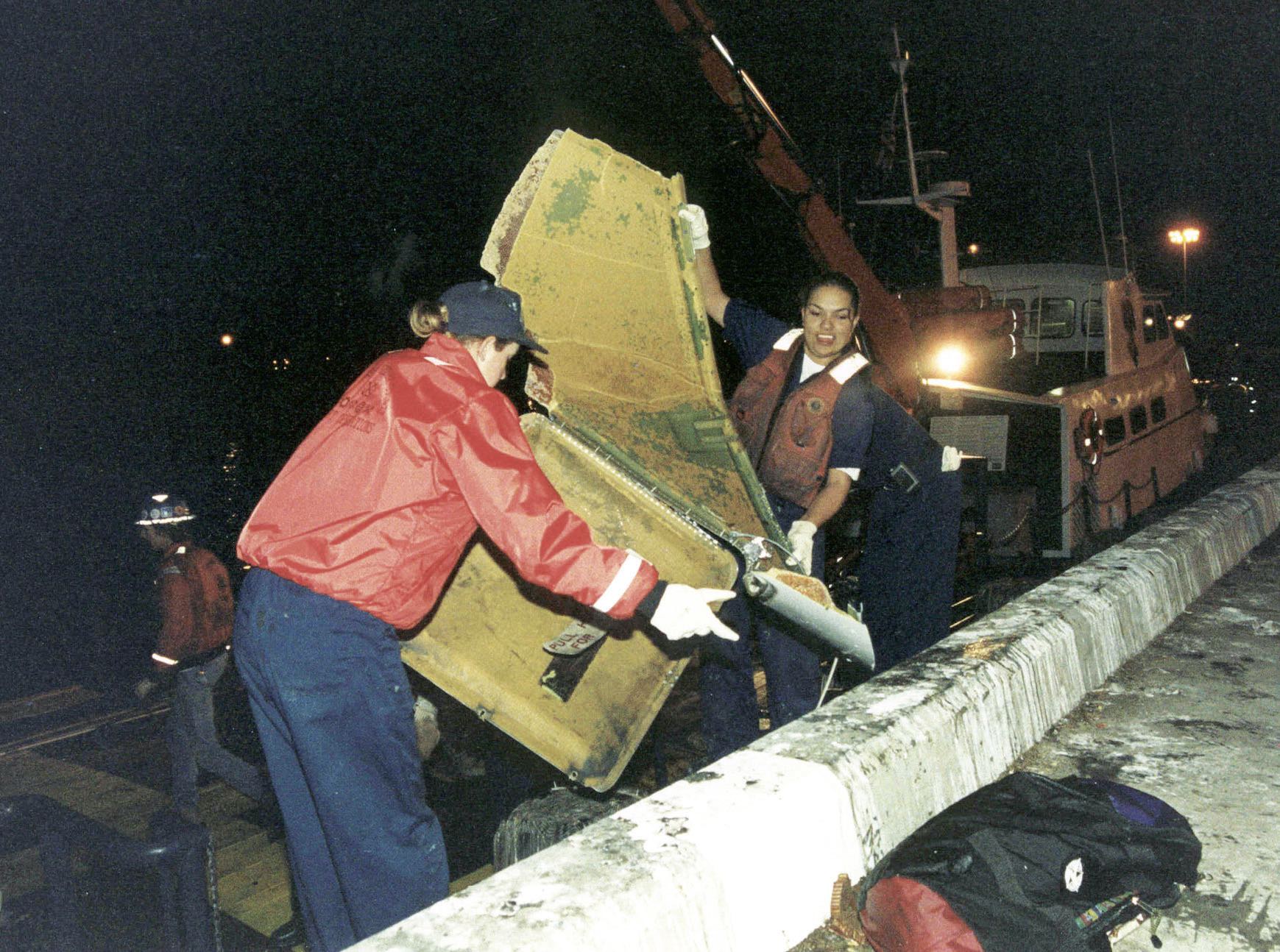
Figure 2. U.S. Naval personnel haul remains of Alaska Airlines Flight 261 from recovery vessels shortly after the flight went down off the coast of southern California. Figure courtesy of the U.S. Navy by PH2 (SCW) Lou Messing. Source: www.dvidshub.net/image/1080806/alaskan-airline-flight-261-crash.
The NTSB found that airline policies and actions of the maintenance staff had failed to adhere to practices, including recommended maintenance intervals, that met the OEM’s specifications.
8,9 A later analysis showed that the airline (with the approval of the OEM) had substituted another brand of grease that was slightly more susceptible to water washout for the previously approved grease as a part of an effort to standardize and reduce the number of greases in use. Early in the investigation, there was some speculation that an incompatibility between the two greases had contributed to the mechanical failure, but the NTSB later concluded that grease incompatibility was not a factor in the accident. Nevertheless, after the accident, the Federal Aviation Administration determined that the substantiating documents provided by the airline did not support the change of grease type, and the airline returned to using the previous brand of grease.
10
Balancing cost, supply and performance
Dai notes that some customers want to use a grease that they are familiar with rather than what an OEM recommends. However, using a better-performing grease, even a more expensive formulation, can pay for itself many times over in cost savings from increased bearing life and reduced downtime and product losses. The cost of using the right grease is much less than the cost of a bearing failure, Dai says. Some replacements result in acceptable performance, and the differences in formulations fall within acceptable ranges, but there is always some risk, he adds.
The number of greases in an inventory depends on the complexity of the operation. Machinery with various types and sizes of bearings and gears (each with its own speeds and loads) or a wide range of operating and ambient temperatures can require a larger inventory of greases than simpler setups. Specialized operations, such as food processing machinery (where incidental contact can result in a loss of product) or shipboard equipment in contact with seawater, must take health and environmental factors into account.
An over-reliance on just a few types of greases also can leave a company vulnerable to price fluctuations and supply disruptions for base oils, thickeners and additives. Greases using synthetic base oils can help customers avoid petroleum price increases, for example. Using calcium sulfonate thickeners rather than lithium soaps avoids lithium price increases caused by competition from the battery industry, as well as providing better performance and environmental safety.
Minimizing (or optimizing) grease consumption not only cuts grease purchase costs, but it can reduce disposal costs as well. On the other hand, using too much grease can drive costs up as well as have a negative effect on performance. Some customers think that if a little grease is good, more must be better, says Noel Layus, commercial technical engineer for Lubricantes Argentinos de Alta Performance SA (LAAPSA) in Buenos Aires, Argentina, but internal friction in a too-thick grease application increases the temperature at the interface, and it requires more energy to drive the bearings and gears.
Grease manufacturing and supply companies are constantly looking for new suppliers and ingredients that can provide products with the needed performance characteristics for an economical price, says STLE member Hernán Bellante, industrial lubricants global division manager for LAAPSA. Government incentives can help in this regard by providing tax breaks for critical imports and exports, he says. But because customers need to keep their operations running, they are generally willing to accept price increases. Grease producers and suppliers all face the same supply and price environment, he explains. “Everybody’s in the same situation. Customers don’t like it, but they have no options.”
The problems of proliferation
It might be tempting to buy a different kind of grease for every application to ensure optimal performance, but the cost of this approach can be prohibitive. Not only that, but managing large, complex inventories introduces complications like tracking usage for each type of grease to ensure that adequate supplies are on hand, but excess supplies do not go unused
(see Consolidate or Not?).
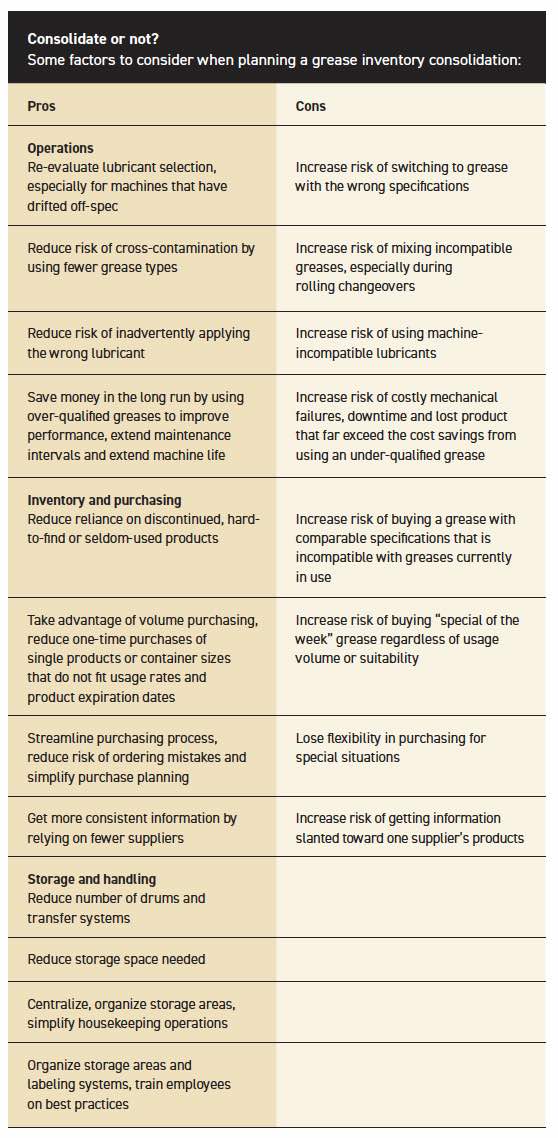
Sources: References 1, 3, 6, 11 and 15.
Adding a different grease to the one already in a bearing or gear, intentionally or not, can cause compatibility problems, even if the two greases have similar performance characteristics. The more types of grease a company keeps in stock, the greater this risk becomes. Color-coded packaging, colored greases and well-trained floor workers help to reduce the risk of using the wrong kind of grease, and simplifying the inventory reduces this risk still further.
Different greases also require different usage and disposal procedures, depending on whether the base oils are mineral or synthetic oils and whether certain types of additives are present. Keeping track of and complying with all the health, safety and environmental regulations involved can be expensive and time-consuming. Some companies outsource their lubrication services to avoid these risks and problems, but this approach might not be practical for smaller operations.
Compliance with OEM specifications for equipment under warranty is a major motivation for keeping a variety of specific greases on hand, says Layus. OEMs work with lubricant manufacturers to develop specifications for lubricant characteristics, based on the operating design speed, load, temperature and function of the machine. However, even if the grease has the OEM’s name on the container, it might be a private-label version of a widely used lubricant. A consultation with the OEM’s service representative might reveal the names of compatible lubricants with the same performance specifications that can be substituted without voiding the warranty.
Matching the grease to the application
On the other hand, multipurpose lubricants should be reserved for machines that are generally low-duty, not process-critical and have a history of being very reliable. Specialized lubricants are required for machines that run under more extreme operating conditions, that routinely exceed rated loads and speeds, or where part failures or process interruptions could present unacceptable hazards or monetary costs.
“People like to use a multipurpose grease for all kinds of applications,” says Bellante. However, an inventory with too few greases can present a different set of problems, he explains. Some companies that make lubricant purchase decisions internally can take a “one-size-fits-all” approach, but one type of grease never fits all applications, Layus says. One type of grease may work for 60%-80% of an operation’s applications, he adds, but the rest need another formulation. Because a part failure or a faulty product batch can cost several times the price of using a better-performing grease, the “one-size-fits-all” approach may be very costly in the long run.
Another problem sometimes arises when a plant introduces new operations but continues to use the same greases that have proven effective in the past. Some customers will claim that a specific type of grease works well, but Layus asks, “Compared to what?” A supplier’s representative may be able to recommend a different grease that performs even better, resulting in cost savings from more efficient operations and less downtime.
Environmental safety and disposal regulations have a large influence on the choice of greases in Europe and the U.S., and these concerns also are increasing in other locations around the world. For example, Bellante says, sugar cane processing mills in tropical countries are moving away from asphaltic lubricants for their open gears because the newer synthetic greases and oils offer better pumpability, better protection of the gear teeth and fewer environmental hazards and disposal restrictions.
In addition to their environmental advantages, the newer semi-liquid open gear lubricants are especially formulated for the intermittent spray or immersion lubricant application methods and round-the-clock operations typical of mills, cement kilns and processing operations, says STLE member Larry Ludwig, chief chemist and technical director at Schaeffer Manufacturing in St. Louis, Mo. However, he adds, the bidirectional open gears typical of mining shovels, excavators and drag lines require lubricants designed for constant replenishment systems, and the lubricant must adhere well to the surface of the gear.
11
On the other end of the spectrum, electric motors require lubricants that can perform at high speeds and high temperatures, and they may need to be suited for use in vertical electric motors. Bellante notes that he and his colleagues have seen many instances where using a multipurpose grease in electric motor bearings has caused an increase in internal friction. The resulting temperature rise can reduce internal clearance, among other effects, which can cause bearing breakage, he says.
Other factors to consider (among many others) include the types of bearings and gears in use, lubricant compatibility with metal parts and whether a running-in period is practical. Long-life greases require base fluids and additives that retard wear, fretting and oxidation, says STLE member Gareth Fish, technical Fellow at the Lubrizol Corp in Wickliffe, Ohio. Sliding can reduce the efficiency of tapered bearings, so they need greases with friction-reducing additives, and they may require a grease with a higher coefficient of friction to reduce sliding or skidding, he says. Polyurea grease thickeners tend to make electric engines run more quietly because the thickener’s “rice pudding”-type microstructure helps the grease to flow more smoothly around the rolling element. In contrast, solid soap thickeners must be shear-softened during a running-in period to improve their flow. Fish also emphasizes that greases for use in electric motors must not contain additives that could promote corrosion of the copper wiring.
12
Many of the newer grease formulations offer more versatility, at an economical price, than their older counterparts, Layus says. However, “no one wants to be the laboratory,” he says, because of the potentially serious effects of switching to an unproven product. Suppliers can provide performance specifications based on laboratory tests and testimonials from other customers to help make the case for switching to a different type of grease. Follow-up visits from the supplier’s representative help to ensure that the various lubricants are performing as intended.
Whether the customer uses a new formulation or a reliable older one, the base oil viscosity must be adequate to provide sufficient lubrication at the mechanical interfaces over the range of operating and ambient temperatures. The additive package must fit the loads, speeds, wear conditions and rust and corrosion hazards for a given operation. Increased friction and wear reduce the life of a bearing or gear and increase the amount of energy required to operate the machinery—over the long run, the associated costs can far exceed the cost of buying and using a grease formulation that is well suited to the application.
For operations where bearings and gears operate at lower speeds, greases with calcium sulfonate thickeners perform well for a variety of purposes, says Bellante. Mining and steelmaking equipment benefit from the high-temperature, high-load and water resistance properties of these greases. Paper mills and pellet mills require greases that stand up to high temperatures, pressures and humidity levels. Calcium sulfonate greases that are formulated for these applications can increase bearing life by more than a year, he says. Layus adds that over-based calcium sulfonate serves as a common starting point for a wide variety of greases, each with its own strengths and limitations. Base oil properties and additives must be suitable for the state of the equipment and the operating conditions.
Using a grease with the wrong consistency or base oil viscosity can increase friction and energy consumption, increase sensitivity to particle contamination or cause insufficient lubrication at the interface. Any consolidation effort should begin with an evaluation of machine specifications, expressed in basic engineering terms (loads, speeds and temperatures, etc.), including anticipated extremes as well as averages. In some cases, using a single grease that meets one machine’s specifications and exceeds another machine’s requirements could save money in the long run by enabling extended maintenance intervals and part service life.
1
Regular site visits from a vendor’s representative can prevent problems that arise from using a multipurpose grease for applications for which it was not intended, Layus says. Customers can educate themselves, he adds, by attending presentations at conferences and universities and at user events sponsored by OEMs and lubricant suppliers.
Inventory consolidation done right
Grease consolidation efforts that involve switching machine components to a different type of grease should be approached systematically. For small-scale or noncritical operations, planning a grease inventory consolidation involves making an inventory of machine components that require greases and sorting them into groups based on generic types (e.g., bearings and gears, speeds, loads and temperature ranges). A similar inventory of greases currently in use can be sorted into groups that share generic performance characteristics (e.g., NLGI consistency, oxidation stability, film strength, resistance to water washout, temperature range). Comparing the categories of parts with the categories of lubricants can reveal overlap areas where grease substitutions might be feasible.
1
In applications where a switch from a specialty grease to a multipurpose grease makes sense, verify whether the two types of greases are compatible by testing them outside the machine parts. For systems with a low risk from compatibility issues (the two greases are compatible and the system is not a critical or high-risk process), a rolling changeover might be appropriate. If the risk is moderate, drain the old grease before adding the new one. Systems with a high risk require draining the old grease and thoroughly flushing the system before the new grease is added. After the lubricant change, monitor the system frequently to check for wear debris, vibrations, temperature changes, noise, motor currents or other signs of mechanical problems.
1
Companies with more complex operations or those that lack the in-house expertise to perform the needed tests and evaluations can benefit from hiring a certified lubrication consultant or scheduling a site visit from their lubricant provider’s technical support staff. These experts can provide advice on how best to reduce the number of greases in use without compromising mechanical performance.
Just as in the basic procedure, planning begins with inventorying the types of machines currently in use and sorting them into groups based on generic engineering specifications rather than manufacturers or brands. The engineering specifications for each machine should include thorough, verified information on the machine type, operating conditions (loads, speeds, temperatures), operating context (ambient environment, processing chemicals, duty and loading cycles), OEM recommendations and warranties and the criticality of reliable performance. Specification lists for individual machines can be sorted into groups, and high-priority specifications from each group can be used in grease selection: robustness, volume currently used, price, etc.
1
Likewise, lubricants in stock should be assessed in generic engineering terms rather than by brands or suppliers. Lubricants should be classified by mineral-based or synthetic types, base oil viscosity and viscosity index, load-carrying capability, NLGI grade, water washout resistance and other such characteristics.
13 Lubricant descriptions should be in a form that is easily compared with the engineering specifications inventory for the mechanical assets, regardless of what types of grease the machines currently use. Look for overlap between products, and determine which lubricants provide the best match to the specifications for each group of lubricated assets.
A qualified lubrication engineer should be involved in this matching process to ensure that machine performance is not compromised. The engineer should evaluate loads, speeds, pump types and any other requirements that should be considered when selecting a lubricant.
14 Are any of the grease applications automated? What environmental or other regulations apply to the lubricants currently in use?
15
Also, which pieces of equipment are the most critical, and which ones are under warranty? It may be advantageous to switch to a different type of lubricant, even in machines that are under warranty. However, if the lubricant you switch to can be proven to have caused a mechanical failure, the OEM can void the warranty.
13 The costs, hazards and liabilities associated with a mechanical failure can far exceed the cost savings and purchasing efficiency gained by switching to a different grease, so a careful assessment is essential.
In addition to matching lubricated parts with the corresponding lubricants, an assessment of current lubricant purchasing, usage and storage practices is in order. Persons conducting the survey should determine the total number of different types of lubricant currently in storage and how many suppliers provide these lubricants. Determine what selection of products each supplier offers and the performance and price characteristics of these products. How extensive are the supplier’s technical support services? How quickly and reliably can they deliver the needed products?
14
How many lubricant storage locations does your plant or fleet have, and how clean and organized are they? How often do you run out of particular types of lubricants, and are there any little-used lubricants that commonly reach their expiration dates before a container is emptied? Workers should be surveyed to determine whether and how often the wrong lubricant is mistakenly used in specific pieces of machinery or the wrong lubricant is ordered by mistake. Is there a record of the proper lubricant specifications for each piece of equipment, and are these records updated to reflect any changes in lubricant application parameters?
3 What person or persons coordinate the company’s lubrication program?
15
If it is determined that an inventory consolidation is in order and that certain machines and parts could operate as well (or better) using a more common type of grease, the type of switchover should be based on compatibility between the old and new greases, as well as the criticality of the system. Just as in the basic approach, a rolling changeover should be reserved for systems with a low risk of compatibility issues. Moderate-risk systems can use a drain-and-change procedure, and high-risk systems should be drained and flushed before introducing the new grease. Like the basic switchover procedure, follow-up monitoring includes frequent checks for leakage, temperature changes, vibrations or other warning signs of a change in operating conditions.
1
The big view on smaller inventories
Inventory consolidation that works over the long run requires the right combination of several interacting factors. Keeping inventories at a manageable size and complexity is important, but so is having greases on hand that fit each application in the plant or fleet. Training workers to know how often to apply each type of grease and how much to use, as well as the importance of avoiding grease mixing and contamination, pays off in terms of fewer part failures and less downtime. The most expensive lubricants do not necessarily offer the best performance, but investing in a more expensive grease that significantly improves performance, reliability and service life can pay for itself many times over. And using a supplier that provides solid advice on lubricant choices, regular site visits and technical support is critical to keeping all of these factors in balance.
REFERENCES
1.
Fitch, J. (May 2011), “Lubricant consolidation: Steps and benefits,”
Machinery Lubrication. Available
here.
2.
Cannon, J. (April 29, 2021), “Consolidating grease products will lower cost, simplify shops,”
Commercial Carrier Journal. Available
here.
3.
Sander, J. and Calk, C. (November 2010), “Hidden benefits of lubricant consolidation,”
Innovations in Food Technology, pp. 80-81. Available
here.
4.
2021 NLGI Lubricating Grease Production Survey. Available
here.
5.
High-Performance Multiuse (HPM) Grease Certification, NLGI. Available
here.
6.
Heston, S. (2012), “Managing a lubricant changeover,” TLT,
68 (3), pp. 28-33. Available
here.
7.
Lucas, D. R. and Mistry, K. K. (2021), “A tale of two greases,” Timken Technical Article No. 11367, p. 15. Available
here.
8.
Aircraft Accident Report (Alaska Airlines Flight 261), NTSB/AAR-02/01, PB2002-910402, pp. 34–36. Available
here.
9.
Alaska Airlines Flight 261 Final Report Released, Aero News Network, Dec. 12, 2002. Available
here.
10.
Miletich, S. (April 26, 2002), “NTSB rejects Alaska theory on crash of Flight 261,”
The Seattle Times. Available
here.
11.
McGuire, N. (2022), “Open gear lubricants evolve slowly but surely,” TLT,
78 (12), pp. 50-63. Available
here.
12.
McGuire, N. (2021), “The electric vehicle grease industry finds its bearings,” TLT,
77 (11), pp. 32-40. Available
here.
13.
Noria Corp., “Optimizing your lube inventories,”
Reliable Plant. Available
here.
14.
Barnes, M. (Sept. 18, 2020), “Fight lubricant proliferation,
Efficient Plant. Available
here.
15.
Stern Co. (Jan. 11, 2021), “Benefits of lubricant consolidation.” Available
here.
Nancy McGuire is a freelance writer based in Silver Spring, Md. You can contact her at nmcguire@wordchemist.com.