KEY CONCEPTS
•
Wind turbine main bearings pose distinctive lubrication challenges related to size, operating conditions, location and environment.
•
Grease formulations and performance tests must consider multiple competing priorities to achieve an optimum balance.
•
Larger turbines and longer maintenance intervals are pushing the cost balance toward new technologies.
Wind turbines use the same types of mechanical components as other mechanical systems—bearings, gears and drive shafts—but their size, operating conditions and environments pose numerous challenges not observed in, say, the automotive industry. Wind farms are usually in remote locations, for example, far from manufacturing plants and maintenance personnel.
Newer turbines are becoming steadily larger—with the resulting higher loads, it is not uncommon to see main shaft bearings that are 2-3 meters in diameter (
see Figure 1), and some of the largest main shaft bearings are 6 meters in diameter. For the largest turbines, physical limitations on the maximum speed of the blade tips determine the much slower rotational speed of the hub. Arnoud Reininga, global engineering manager for Energy Industries for the SKF Group, notes that the largest wind turbines currently have rotor diameters of 220 meters. For these turbines, he explains, if the main shaft rotates at 10 RPM, the tips of the blades rotate faster than 100 m/s. (At ground level, the speed of sound in air is about 340 m/s.) The wind turbine’s main bearing is responsible for the efficient transfer of this slow-speed rotation energy to the gearbox, which steps up the rotational speed to power the electrical generator.
Unique challenges
Because wind turbine operation involves low rotational speeds, high loads, vibrations and other factors not commonly seen in other industries, certain wear modes not commonly seen elsewhere (e.g., micropitting, fretting and white etching cracks) can present significant durability and reliability problems for wind turbines. Other concerns are common to many applications, including corrosion and rust, viscosity changes, mechanical shearing, cold-temperature operations and ensuring adequate lubrication under start-and-stop conditions.
Although substantial work has been done to improve wind turbine gearbox lubricants, relatively little work has focused on greases.
1 Greases keep rotor assemblies, pitch and yaw control mechanisms, electric motor bearings and generator shaft bearings running smoothly over a wide range of wind conditions, ambient environments and temperatures (anywhere between 40 and 80 C). Wind turbine main bearings support the weight of the blade assembly, and they must hold up under high loads and high torque (
see Figure 2). The slow rotation speed of the main bearing can accelerate wear, and sudden changes in the speed or direction of the wind can introduce shock loading.
Figure 2. Rotor and nacelle of a three-bladed wind turbine with a horizontal rotation axis. The main bearing (gray ring around drive shaft) supports the weight of the blade assembly. Figure courtesy of Siemens, Inc., CC BY-SA 4.0.
Main bearings also are subjected to axial thrust from wind blowing against the blades, but the magnitude of this thrust has not been well quantified, says STLE member Dr. Gareth Fish, Technical Fellow and the technology manager for industrial additives and greases for The Lubrizol Corp. Some types of wear, like white etching cracks, are seen in the high-speed bearings and gears in wind turbine gearboxes but not commonly observed in slow-moving main bearings.
2,3
Doug Lucas, an advanced engineering technologist with bearing manufacturer The Timken Co., explained the importance of bearing design in high-load applications like wind turbine main bearings in a recent article.
4 A well-designed bearing has a longer service life, he says, because of reduced stress and bearing temperature. Bearings with the right amount of clearance ensure that the load is properly shared among the rollers, preventing misalignment, edge loading and sliding damage.
Lucas notes that tapered roller bearings (TRB) are beginning to replace spherical roller bearings (SRB) for main shaft applications, especially in the larger offshore wind turbines. Because tapered bearings can better support high thrust and radial loads, a smaller tapered bearing can be used, and it can stand up to harsh conditions and unpredictable changes in wind speed and direction. However, taking the specific demands of an application is critical to choosing the right bearing design, he adds.
TRBs experience sliding forces at the interface between rib and roller, and they require a different grease formulation than for SRBs, Fish says. As yet, there are no industry standard specification tests for SRBs, and this makes development of greases for these bearings difficult. Standardized performance tests do exist for TRBs that, along with existing bench tests (cone penetration, rust and wear tests, four-ball tests, etc.), can be used to develop greases for pitch and yaw bearings, but more needs to be done to extend these for use with main bearings, Fish says.
1
Vibration can cause fretting wear, says STLE member Joe Kaperick, senior R&D advisor for greases at Afton Chemical and past president of NLGI. Kaperick advises his customers, grease manufacturing companies, on additives for specific performance specifications. Fretting wear, he says, is especially an issue when a turbine has been stopped for maintenance or during high winds, because the lubricant is not circulating normally through the bearings. Moreover, the speeds and temperatures at which wind turbines typically operate are often not high enough to activate typical extreme-pressure (EP) and antiwear additives, which poses a particular concern with regards to fretting prevention. Finding additives that work well under those conditions can be difficult, he says, because of the scarcity of large test rigs and the difficulty in performing field trials. “That’s probably the biggest challenge,” he says.
The high cost of failure
Typically, bearing manufacturers will deliver ungreased bearings to original equipment manufacturers (OEMs), and the OEM chooses the grease (or greases) for the entire assembly. Different types of bearings operate at different speeds under different loads, thus placing different demands on their lubricants. However, maintenance is easier, and errors easier to avoid, if only a few types of greases are used. “You see quite a high level of standardization in the market for wind turbine greases, and it’s quite a conservative market,” Reininga says. He notes that wind turbines have an expected service life of 20 years or longer, with the trend going toward 25 or even 30 years, which presents a significant challenge for service life testing. Typical accelerated wear testing procedures, like using high loads or higher rotation speeds, change the kinematics and might not give an accurate estimate of service life.
Pre-greasing bearings before transporting them to the turbine assembly location helps to prevent false brinelling of the raceways and rolling elements during transportation, Fish says. At the installation site, the bearings are given another application of grease. Relubrication after every six months of operation is typical, although manufacturers are working to extend maintenance intervals where possible. OEMs typically issue 10- to 20-year warranties for their products, Fish says, and the warranty specifies the relubrication grease to be used for a given part or application. This specification is based on extensive testing to ensure that a grease can meet performance specifications. After the warranty expires, the operator is free to use other products, and price often becomes more of a driving factor at this point.
“A premature failure of a bearing or gear can cost around $100,000, and that’s not including downtime,” says STLE member Dr. Tabassumul Haque, global technology sponsor for industrial lubricants and greases at ExxonMobil. To help prevent such failures, the company’s grease formulations and manufacturing R&D group collaborates with the internal fundamentals research group and key equipment builders to develop new greases. They also work with industry partners and trade associations on setting grease specifications.
STLE member Dr. Aaron Greco notes that just the cost of the crane to swap out a gearbox or main bearing for a land-based turbine can run more than $100,000 a day. Expenses could be even higher for turbines operating in the ocean, where maintenance crews have to contend with wind and waves, he says. Greco is the group leader for interfacial mechanics and materials and the wind energy program manager in the Applied Materials Division at Argonne National Laboratory. His work, which is funded by the Wind Energy Technology Office of the U.S. Department of Energy, involves wind turbine drivetrain reliability and materials and quality issues. His group is currently looking at grease lubricants for main bearings and pitch bearings, with an eye toward preventing premature failure of these parts.
Like the rest of the turbine components, the main bearing is exposed to a wide range of temperatures and the effects of dust or salt spray in the atmosphere. “A lot of these wind turbines are 10 or 20 miles offshore,” and constantly exposed to salt spray, Kaperick says. However, the cost of the lubricant alone can exceed $5,000 for a complete drain, flush and fill for a midsized turbine, not including the costs of the crew, equipment and transportation.
5 “You don’t want to go out there and change the grease on it every six months. You want to leave it in there for as long as possible, so you want long life, you want corrosion protection, you want protection against the water environment.”
Predicting performance
STLE member Dr. Piet Lugt develops models that predict the performance of grease-lubricated bearings, which helps machinery operators know when to schedule maintenance operations. Lugt is a senior scientist at the SKF Group Research Centre and a professor of tribology-based maintenance at the University of Twente in the Netherlands. Performance depends on the design of the bearing, the application for which it is used and the formulation of the lubricating grease, as well as the interactions between these factors, he says. He notes that grease is 80%-90% oil, and the rest is thickener and additives. However, the amount of oil available for lubrication is relatively small, so the grease has to work efficiently.
The main factor is the ability of the grease to form a lubricating film between the contacting surfaces and maintaining an adequate film thickness. This does not prevent fatigue failure, but it does reduce or prevent failure due to wear. “Initially, you might have a very thick film, and everything is working very well,” Lugt explains. Generally, in rolling element bearings, the base oil evaporates over time, and it oxidizes, gets contaminated or leaks out of the bearing. Thus, the amount of oil and lubricity of the grease overall changes during service. “What we’re trying to predict is how that quality of lubrication is changing as a function of time,” he says.
Lugt explains that because grease is a semisolid material, its viscoelastic properties are intermediate between those of a solid and a fluid. During bearing operation, the grease is driven to the sides of the bearings, and then it comes back, and this circulation churns and shears the grease. Oil bleeds out of the grease to provide lubrication in the contact area. The bleed process is very slow, he says, so the balance between the lubricant feed (oil bleed) and the loss (e.g., from evaporation or leakage) stays fairly constant.
The microscopic flow is very much determined by the rheology of the grease, he continues, and this might change over time because of the large shearing forces on the grease, which can break down the structure of the soap thickener (
see Figure 3). The flow profile of the grease over time depends on the initial properties of the grease and the geometry of the bearing, which influence the type and magnitude of the loads that the grease encounters.
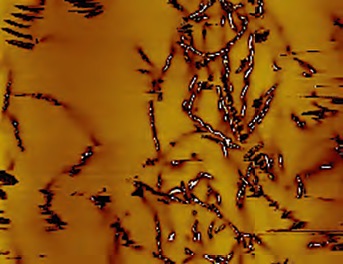
Figure 3. (a) Thickener structure in fresh grease and (b) after shearing. Figure courtesy of Piet Lugt, SKF.
We know a lot about the traditional lubrication mechanisms for the small bearings, Lugt says. “For the larger bearings, it becomes much trickier,” he explains. Gravity plays a significant role for the large volumes of grease required for a typical wind turbine main bearing. “If you have a very small bearing, then it very easily sticks on the cage, because the volumes are very small. If you now have a really big bearing, then [the grease] will drip off.” Grease is less mobile in smaller bearings, and it tends to form reservoirs, which affects the replenishment of lubricant to the contact area. Lugt adds that even though the grease is much more mobile in the larger bearings, when the grease is pushed to the sides of the bearing during operation, the distance that the oil has to travel to return to the contact area is much greater.
In many wind turbines, gearboxes convert the slow rotation of the main shaft to the faster rotation required for power generation (
see Figure 4). Bearings in the generator require a less viscous grease formulation because of the faster operating speeds, and the gearboxes are oil lubricated, Reininga says. Pitch bearings, which adjust the angle of the blades, with respect to the main shaft depending on wind direction, generally produce small oscillations, which require greases with yet another set of properties.
Figure 4. Three-point (top) and four-point (bottom) drivetrain configurations. Figure courtesy of National Renewable Energy Lab. Source: Guo, Y., Parsons, T., et al., (2016), “A systems engineering analysis of three-point and four-point wind turbine drivetrain configurations,” Wind Energy, DOI: 10.1002/we.2022.
Unlike cars, which start and stop often and spend long periods not moving at all, wind turbines are in motion more or less continuously, Reininga says, noting that starting and stopping is still an issue. “Depending on the location where you are, starting conditions can be quite difficult,” he says. “If you are in Alaska in the wintertime, and you have to stop [the turbine], there’s a very cold condition, and that has a lot of impact on the starting condition of the grease.” In general, he says, unless you’re doing an emergency stop for a windstorm, the amount of inertia involved makes starting and stopping a wind turbine more gradual than for cars.
After a complete stop, hydrodynamic action stops, and the lubricating film thickness goes to zero. Also, the system cools down, so starting again is difficult, Lugt says. In cold climates, the grease might cool below its minimum operating temperature, making it too stiff to prevent damage to the bearings when the turbine is restarted. “Under Arctic conditions, that is one of the criteria for selecting a grease for such an application,” he says.
Micropitting and grease films
Greco notes that although main bearing failure mechanisms are still not fully understood, micropitting, a type of surface-initiated fatigue failure under cyclic loading conditions, is the most common wear mode that contributes to early failure. This type of highly localized damage can increase the internal clearance of bearing rollers and raceways, producing edge stresses that can ultimately result in macropitting and failure.
6
Micropitting is more common in the wind industry than in other areas. Although the reasons are not fully understood, there are several contributing factors. In contrast with, say, automotive vehicles, large commercial wind turbines are designed to run continuously for 20 years. The winds that drive the turbines vary in amplitude, direction and gust. Water (including salt water), dirt and wear debris contaminants can accelerate wear through chemical reaction or abrasion. Slow rotation speeds can result in high friction and a reduction in the thickness of the lubricating film. The frequency and duration of various stages in the bearing’s duty cycle—starting, operation, stopping and no-load periods—also factor in.
6
Micropitting in gears has been well studied, and oil lubricants have been developed to protect against this type of failure, Haque says. The causes of micropitting in the grease lubricated main bearings are less well known, he adds, noting that grease formulations to address this are in an earlier stage of development. Although industry standard tests and OEM specifications cover a wide range of performance properties for wind turbine main bearings and their lubricants, he says, there is no counterpart to the FZG FVA 54 gear oil test that can quantify a grease’s ability to protect against micropitting.
Haque cites several potential causes of micropitting in bearings that are under investigation, including high loading, microcrack opening driven by pressure exerted by lubricant films and chemical stress corrosion. Some lubricant components can actually accelerate micropitting, he adds, but the right formulation protects surfaces instead. A careful selection of additives can form tribofilms under boundary lubrication conditions that retard microcrack formation and smoothen tribological contacts.
Some operators try to use a very thick lubricant film to keep the contact surfaces separated, Haque says, but very thick, viscous films undergo a substantial amount of mechanical shear, which can generate heat, shear thinning and oxidation issues. “We need to keep a consistent film thickness under any given conditions throughout the lubricant’s life,” he explains.
Some formulators use a base oil with a very high viscosity to provide a thicker lubricating film, Lugt says, but his group’s research shows that at ultralow speeds, films are thicker than expected. He attributes this to the contribution of the grease thickener, in addition to that of the base oil, to the thickness of the film.
7,8 The thickener’s contribution decreases somewhat as the grease ages and shear forces break down the soap fiber structure, but some of the thickener is always in the contact area
9 (
see Figure 5).
Figure 5. Interferometry measurement of grease film thickness in an EHL contact, simulating the contact between bearing rollers and rings. At slow speeds, grease thickener lumps enter the contact area, contributing to the development of a lubricating film. Figure courtesy of Piet Lugt, SKF.
Grease formulations for wind turbine bearings
Making sure a lubrication system works as intended requires input from several sources, Kaperick says. Recurring problems can quickly become very expensive, so manufacturers of additives, greases and equipment might all be called in at some point to assist a wind farm operator, especially for systems that are still under warranty. Kaperick notes that additive manufacturers can help to determine causes by working with OEMs and lubricant suppliers and sometimes recommend additive solutions for specific problems like micropitting or fretting. For a turbine that represents a multimillion-dollar investment, getting to the root cause of a part failure is well worth the investment.
Haque notes that his company’s formulation strategy is to use a balanced lubricant formulation approach for preventing failures and maximizing lubricant lifetime. Although some grease manufacturers make products that maximize performance in a few specific areas (e.g., load bearing capability), Haque and his colleagues optimize performance over a broad range of characteristics, establishing a window that encompasses the best combination of characteristics. Thus, they take into account such things as friction, wear, corrosion, oil bleed, shear stability, low-temperature flow, thickener structure, elasto-hydrodynamic lubrication (EHL) film thickness under a wide speed range and many more (
see Elastohydrodynamic Lubrication).
Elastohydrodynamic lubrication
Elastohydrodynamic lubrication (EHL) occurs when the pressure in the contact area is high enough to alter the shape of the surfaces, which considerably alters the shape and thickness of the lubricant film in the contact. This elastic deformation, coupled with pressure-driven increases in lubricant viscosity, enhances the level of hydrodynamic action. EHL films, typically less than a micron thick, are the primary lubrication mechanism in the non-conformal contacts common in wind turbine bearings and gears.
EHL films depend on lubricant viscosity, speed and load. Ball-on-disc tests, which use a camera and interferometry to measure the local film thickness, are used to measure the EHL performance for oils, Haque says. It’s harder to determine EHL for greases, he says, because variations in contact geometry and grease consistency make it difficult to introduce and maintain the right amount of grease in the contact. One way to estimate grease film thickness is to test the base oil alone, and then apply a “starvation factor” to estimate the film thickness of the corresponding grease using that base oil.
EHL films are less effective under slow speed, transient loading and start–stop situations, which starve the contact area of lubricant. Protecting bearings from wear under these conditions requires the use of surface treatments (including lubricant additives) and coatings. However, additives must be selected carefully. “Some additives are known to form patchy protective films that can promote fatigue wear, including micropitting,” Haque says. Many OEMs super-finish their bearing surfaces or use coatings like DLC to minimize local stresses caused by friction, but these approaches can be fairly expensive.
10 Greases that provide optimum EHL films and excellent surface protection under starved conditions appear to be the most practical and effective way to address main bearing micropitting failures, he says.
“If you take care of load bearing capability by increasing viscosity and EHL film thickness, it might create other problems like high friction, heat generation and energy loss,” Haque explains. “Then, if you think about increasing film thickness using higher thickener content or polymer, you might negatively impact low-temperature performance.” He adds that achieving balanced performance requires a broad range of tests to ensure that the formulation falls within a range that optimizes a range of properties. “You cannot just pick one performance criterion and then sacrifice others,” he says.
Selection of the optimum base oil viscosity based on bearing design and operating conditions is especially important, he notes. Low temperatures also are a concern because the system that circulates the grease can be close to ambient temperature (which can be as low as -50 C in high-latitude locations), even though the operating temperature inside the bearing is warm enough to be within specification.
Some grease formulations rely on polymers and thickeners to provide a more robust and thicker EHL film thickness to improve load bearing capability. Haque notes that he and his colleagues avoid this approach because boosting film thickness in this manner can interfere with the grease’s ability to release oil during operation and also hurt low-temperature properties. His company’s formulations let the thickener and the oil do their respective jobs rather than performing multiple functions, he says.
High-performance multipurpose greases are typically used to lubricate main shaft bearings in wind turbines, Kaperick says. These greases must be pumpable, and they must use base oils with viscosity profiles that enable them to provide effective lubrication over a wide range of temperatures. Solid particle contaminants like dust can abrade metal surfaces, but greases can provide a barrier, working along with filtration systems and seals, he says. Lugt adds that greases also must resist water contamination, including from condensation that forms at cold temperatures.
Wind turbine gearbox oils and lubricating greases often use synthetic base oils like PAOs, and some manufacturers formulate PAO-based greases specifically for main bearings. Although these greases are more expensive, a formulation that takes factors like additive and thickener compatibility into account can save money by extending the maintenance cycle. Fish notes, however, that low-polarity PAO base oils can be incompatible with the more polar lithium soap greases, which requires using a much higher thickener content or structural modifiers to prevent excessive oil bleed. One way around this problem is to use a base oil that combines the PAO with a more polar oil like an alkylated naphthalene, which results in a much better grease structure.1 Some specifications don’t allow that, he says, adding that alkylated naphthalenes add to the cost of the finished grease.
Fish notes that OEMs who write grease specifications for their bearings sometimes fail to integrate knowledge of how greases perform with knowledge specific to wind turbine operations. “You have to pass the specification to get into a field trial, and then when you get [the greases] into the field trial, you then find out if they really work,” he says. Often, greases that pass the specification fail in the field trial, he says, but it’s not because the grease does not perform as expected but because the specifications were mismatched.
For example, one wind turbine specification calls for a lithium complex grease with a very high dropping point, Fish says. Dropping point is a quality control test to determine whether you’ve made the thickener system correctly, he explains. However, in some grease specifications, it is used as an arbiter of high-temperature performance, even though the documentation on the test method clearly states that the test is not intended for that purpose. Using dropping point as a specification skews the choice of a thickener toward a high-temperature thermally stabilized lithium complex thickener system. This type of thickener ensures performance up to 150 C, even though the main bearing’s operating temperature never goes above about 80 C, Fish says. If OEMs didn’t have this requirement, he adds, they could probably use a grease thickened with lithium soap or calcium sulfonate, but most specifications require the lithium complex grease, which requires a more concentrated lithium hydroxide solution to manufacture. This can raise the cost of a grease, especially when the price of lithium fluctuates, as it did in 2016 and 2017.
11
As with any grease formulation, certain tradeoffs have to be made to optimize the overall performance. A finished grease has to pass tests including oil bleed, rust resistance, fretting, water resistance and Riffel tests, Fish says, and all these require different additives. However, too much rust inhibitor can cause a grease to fail the fretting test, and too much antifretting additive can interfere with rust prevention. Also, as it stands now, grease specifications are similar for offshore and onshore wind turbine applications, he says, but the two environments present different issues. For example, offshore turbines need a higher level of protection against rust and corrosion than land-based turbines do. “Basically, the specifications are written around the worst-case scenario, not necessarily optimized for the actual application,” he says.
NLGI will release a new high-performance multiuse (HPM) grease specification in January 2021. The new specification will cover greases that deliver higher performance than the existing GC-LB automotive grease specification. It also covers characteristics typically needed for wind turbines, including water and corrosion resistance, low-temperature performance and performance under high loads.
12 “I can’t say that any of the new specifications would be a direct match for a wind turbine grease,” Kaperick says, but citing compliance with the new specifications could facilitate a conversation between a grease manufacturer and an OEM. He adds that OEMs will probably run additional in-house tests to address more specific performance characteristics. “If you have this core performance that everybody can accept, that’s a good place to start.”
Bench, rig and field tests
One challenge faced by grease developers and OEMs alike is translating grease performance under standard testing conditions into predictions of performance in the field. For example, many of the common bearing tests are less relevant to wind turbine main bearings.
To do a true service life test, ideally you would need to test 15 or more full-sized bearings, Lugt says, which is currently not practical. Typical tests involve smaller bearings, which might have different wear mechanisms from the full-scale bearings. “So, extrapolation is very dangerous, and strictly speaking, you should never do that, of course,” he says. “Upscaling is a topic that needs much more attention.”
One important issue is understanding the loading, Fish says. “You’ve got wind blowing the blades, and then they rotate. And then you get wind shear and other effects, the different loading and tilting. And it’s only relatively recently they’ve instrumented wind turbines in operation and can measure the transient loads.” He explains that in the absence of measurements in the field, assumptions were made as to what the loading on the bearings would be. If the basic assumptions about the load were wrong, engineers could specify bearings that were too large or too small. Oversizing the bearings ensures that they can support the load, and this is often done, but this practice also increases cost and weight, he explains. Undersizing the bearings can result in premature failures. Once quantitative knowledge of the loading was available, engineers could size and design the bearing to suit the application.
“We do a lot of inspection of components that come in from the field and try to ascertain what the failure mechanism is, and for what we can, [we determine] the root cause,” Greco explains. “A lot of times these things come in so battered up, it’s hard to see the initiation of failure (
see Figure 6).” These inspections can involve optical and electron microscopy of cross sections—and sometimes high-energy X-ray microtomography—to determine the types of wear and fatigue cracking that occur under various conditions. They also try to replicate failure mechanisms in the laboratory under controlled conditions using benchtop test methods in order to understand the root causes of these failures. “[This] also gives us a platform to test new greases or coatings or whatever new material technology. People are looking to mitigate those failures and do it in an accelerated way.”
Figure 6. Wind turbine field sample showing extensive wear. Figure courtesy of Aaron Greco, Argonne National Laboratory.
Greco notes that few labs have testing equipment for full-sized bearings, and testing at that scale is expensive in terms of both time and money. At the benchtop scale, they can run more contact cycles, upward of a million cycles per hour. “If you are looking at inducing the same number of contact cycles in the main bearing, you have to turn that whole big mass faster,” he says. “Physics starts to work against you.” He notes that his lab is able to impose a range of contact condition and loads to replicate transient extremes in the field. They can vary these factors independently to pin down sources of failure.
Often, his lab will have to devise their own test methods, because current ASTM standard tests are not specific to conditions that wind turbines encounter. Grease manufacturers typically list specifications for their products on the basis of standard tests that these greases pass, but the conditions of the test might not be predictive of performance in the field.
Greco’s group is working to develop test methods that allow users to compare various grease formulations and rank them as to what their performance would be under field conditions. They are looking at factors not typically represented in the standard tests that can accelerate early failure and induce wear modes like micropitting. Other failure modes that are hard to quantify include false brinelling (fretting caused by small oscillations or vibrations) and electrically accelerated white etching cracks.
13
Haque notes that his lab uses the same type of balanced approach to testing their grease formulations that they use in developing the formulations. The variety of bench and rig tests they use to determine the characteristics of their grease formulations ensure that a formulation can deliver optimum performance across a broad range of properties. Even though bench and rig scale tests might not completely correspond to conditions in the field, the combination of tests is what gives them confidence for successful performance in the field, he says. After a formulation has passed a series of standard tests, it moves on to a set of builder-specific tests, followed by up-tower field trials.
“We do a lot of performance testing from an additive perspective,” says Kaperick. “Often, our customer will have a good idea of the type of grease thickener-base oil combination that they want to put into a wind turbine. They’ll send us this base grease without the additives in it. And then we will additize that grease and do the testing in our lab to make sure that it passes the standard industry tests that the customer believes will ensure that it is fit-for-purpose in the application.” Such tests might include EMCOR rust, a four-ball EP or wear, fretting wear, structural stability or a host of other bench tests designed to predict performance with respect to important grease attributes. He doesn’t always know what the end application will be—especially if the grease is intended for multiple purposes—so the focus is on characterizing the grease’s performance with respect to standard benchmarks.
“Standard lab tests will tell you which formulations work best under the conditions of the test, but it’s not always simple to translate test results into predictions of performance in the field. You can’t run a field trial on every formulation,” says Kaperick. “We’re not going to put in three formulations and try them out in three wind turbines for three years to see how long or how well they last.” For this, they rely on parts and equipment manufacturers who do rig testing, often using their own test methods, and have a track record of experience with how various systems perform under operating conditions.
Kaperick notes that the Riffel test, which mimics the fretting that can occur due to vibrations under high loads in the presence of salt water, can be a better predictor of fretting that can take place in a wind turbine application. However, the test is not widely available—only a few test rigs currently exist—and so it can be difficult to screen greases routinely with it.
However, “It doesn’t make sense to have a Riffel test in a main bearing [grease] specification,” Fish says. In the Riffel test, the bearing is held vertically in a hydraulic press, and it does not incorporate rotation. This situation is typical of pitch or yaw bearings, which experience mostly oscillating or vibrating motion. Main bearings are mounted horizontally, and they are rotating any time the wind is blowing. The Riffel test does not account for grease entrainment into the contact areas during main bearing rotation, he explains, noting that residual grease is compressed into the track surface, which helps with lubrication.
OEMs sometimes include other requirements in their main bearing grease specifications that are not directly relevant to typical operating conditions, Fish says. For example, one wind turbine manufacturer requires greases to pass an FE9 test (DIN 51821), which uses a small angular contact bearing rather than the spherical or tapered rollers typical of wind turbine main bearings. The FE9 test runs at 6,000 RPM and a temperature of 120 C. However, a small wind turbine main shaft bearing runs at a speed of 60 RPM, and larger turbine shafts rotate even more slowly. Also, the temperature inside the nacelle rarely, if ever, exceeds 80 C. The maximum base oil viscosity that is appropriate for an FE9 test is ISO VG 220, Fish says, but most wind turbines require ISO VG 460 main greases to support the large loads under the slow rotation speeds. The FE8 test (DN 51819) is meant for bigger bearings, he continues, and you can run it at 7.5 RPM or 75 RPM. This test can be used on bearings under heavily loaded low speed conditions, which are more closely relevant to conditions in a wind turbine. Some grease specifications require both the FE9 test and the FE8, he adds.
Most standard tests use systems with fairly constant loads, but because a wind turbine’s blades rotate depending on wind direction, the loading on the bearing contact is not completely even. That, along with pulsing caused by wind gusts, complicates load calculations, Fish says, which, in turn, poses difficulties for developing grease specifications.
Data input for models
Performance predictions come from a combination of theoretical models, testing results on smaller bearings, functional testing on full-sized bearings and field observations from the application engineers, Lugt says, adding that there are still knowledge gaps to be addressed. Current research focuses on areas including the ways that flow properties change as a grease ages and undergoes mechanical work, better representations of how the oil bleeds out of the grease and film formation under starvation conditions.
Input to these models comes from a variety of sources, including data from the SKF Sven Wingquist Test Center in Schweinfurt, Germany, which opened in 2017. The largest test rig at this center accommodates bearings with an outside diameter as large as 6 meters, as well as complete bearing assemblies (
see Figure 7). In September 2020, the SKF University Technology Center, a collaboration between SKF and the University of Twente, opened its doors. This center focuses on research for grease lubrication in rolling bearings, and it will allow industrial and academic researchers to share laboratory resources and to interact with each other.
Figure 7. The 125-metric-ton, 7-meter disc is lifted into position in the lower half of a test rig at the SKF Sven Wingquist Test Center in Schweinfurt, Germany. This rig can test bearings up to 6 meters in diameter, as well as complete bearing assemblies. Figure courtesy of SKF.
Nondeterministic effects are another area of research, although it is unclear how big an effect this has in larger bearings. “Everything is very nonlinear,” Lugt explains. “Grease lubrication is actually a chaotic process; small disturbances produce a big effect later on.” For example, research on smaller bearings showed that it’s almost impossible to fill a bearing with grease in exactly the same way twice, he says.
One issue that is evident in larger bearings is how the grease flows after the bearing has been filled. There is a need to understand this flow better, says Reininga, to ensure consistency in the availability of lubricant in the contact areas over time. Flow in a bearing is actually a three-phase problem, involving air, grease and oil that has separated from the grease. The lubricant film might be several microns thick, but the bearing components are on the scale of meters. Modeling these systems requires incorporating physics and chemistry over this wide range of scales, using high-performance computing resources.
Trends in turbines and greases
In addition to solving complex flow problems, Lugt and his colleagues are trying to reduce the application of this knowledge to practical engineering rules, using simpler equations that incorporate the most relevant parameters and relations. Better models could help turbine operations optimize the amount of grease they use—enough to provide reliable performance, without the need to use excessive amounts as an “insurance policy” against premature failure. This could prove useful with newer wind turbines, especially the largest ones, which use automated replenishment systems rather than relying on a twice-yearly service call by a maintenance technician, he says. He notes, however, that most of the progress in this field is a refinement of existing technologies rather than revolutionary changes in grease formulations.
Kaperick observes that as wind power becomes more mainstream, demand for additives for wind turbine greases is rising as well. “Twenty years ago, you might sell a drum of additive for an application, because there weren’t that many of them out there,” he says. “Now, it’s definitely more mainstream. People know what you’re talking about more, and I think grease manufacturers are coming up with greases specifically marketed toward those areas.”
Although most current demand involves standard types of additives already established in the market, additive suppliers continue to come up with innovative solutions such as new components or nanoparticle additives to solve specific challenges, in anticipation of a day when the savings on maintenance and repair justifies the extra expense. Kaperick notes that using a better lubricant can be more economical than investing in more expensive bearings. In some situations, however, using long-lasting bearing materials like ceramics can extend service life while requiring less lubrication. As more turbines are coming off warranty, he says, operators might be more amenable to using newer replacement parts and lubricants—or they might revert to more tried-and-true solutions to lessen the risk of a failure.
Wind energy operations also are starting to look more at wear protective coatings as a way to increase intervals between maintenance and repairs. In a recent article, Lucas and his colleague Vikram Bedekar discussed the use of protective coatings to prevent steel-to-steel contact, the trigger for virtually all bearing-related issues in wind turbines.
14 This problem has become more acute and more expensive as wind turbines become larger and generate more power. Over the past decade, they reported, physical vapor deposition (PVD) coatings like tungsten carbide began to come onto the market. PVD coatings on bearing rollers provide a hard, non-steel surface that reduces friction between the roller and the steel raceway, even under extreme loads. They cited the example of a 1.5 MW wind turbine that was taken out of service for upgrades after seven years of operation. There was so little adhesive wear from the PVD coated rollers on the raceway of the main shaft bearing that this bearing did not have to be replaced; the engineers were confident that the bearing could continue operating without issues over a 15- to 20-year lifetime.
When many of today’s wind turbines were manufactured, “a lot of the OEMs wouldn’t put coatings on the bearings,” Greco says. “But once the turbines are out of warranty, [wind farm operators] will opt for coatings to extend the life. And so now you’re seeing a trend more where those coatings are being specified for the factory components.” This is happening more with gearboxes, but Greco also is beginning to see coatings applied to main bearings. Black oxide (an iron oxide surface treatment originally designed as a rust preventive) is a common choice because of its lower price. The higher performing and more expensive diamond-like-carbon (DLC) coatings are becoming more common as rolling element coatings. Limiting these coatings to the rolling elements requires less coating material, and the practical aspect of fitting the parts into the vacuum chamber for the plasma vapor deposition coating process also comes into play. “There are other varieties of coatings, or more advanced coatings that are being developed all the time,” Greco says, adding that his group and others at Argonne are currently developing various types of advanced coatings.
15
“We’re also working on some new additives for grease,” he continues. “We are currently looking at developing nanoparticle additives. There are some products already out there using nanoparticles or near nano. We find that comparing a nanoparticle versus a chemical additive, the tribofilm formation processes are different—different kinds of physics and chemistry.” This can be leveraged to enhance the surface protection provided by the lubricant, he says.
“Cost is always a factor,” Greco says, “and the wind turbine industry is certainly not immune. It’s a very cost-constrained industry.” However, he adds, as turbines become larger and as more turbines are installed offshore, there is a push toward longer maintenance intervals. Operators have to balance initial investment costs with ongoing operation and maintenance costs, along with the costs of transporting equipment and personnel to remote (and sometimes hazardous) locations to handle unexpected parts failures. “The cost balance is getting more in favor of entertaining new technologies,” Greco says.
REFERENCES
1.
Fish, G. (2020), “The development of lubricating greases for wind turbine applications,”
NLGI Spokesman, 84 (1), pp. 36-45. Adapted from Fish, G. (2019), “The development of lubricating greases for wind turbine applications,” NLGI Paper #1924, 86th NLGI Annual Meeting, June 8-11, 2019.
2.
Haque, T., Korres, S., et al. (2018), “Lubricant effects on white etching cracking failures in thrust bearing rig tests,”
Tribology Transactions, 61 (6), pp. 979-990. Available
here.
3.
Franke, J., Carey, J.T., et al. (2018), “White etching cracking—Simulation in bearing rig and bench tests,”
Tribology Transactions, 61 (3), pp. 403-413. Available
here.
4.
Lucas, D. (Aug. 2019), “How to choose the right bearings for offshore wind turbines,”
Windpower Engineering and Development, pp. 42-45. Available
here.
5.
Kaperick, J. (June 11, 2018), “Tilting at Wind Turbines: An Adventure in Lubrication,” 85th NLGI Annual Meeting, June 9-12, 2018.
6.
National Renewable Energy Laboratory (February 2010), “Wind Turbine Micropitting Workshop: A Recap,” Shuangwen Sheng, Editor, Technical Report NREL/TP-500-46572. Available
here.
7.
Morales-Espejel, G.E., Lugt, P.M., et al. (2014), “Film thickness in grease lubricated slow rotating rolling bearings,”
Tribology International, 74, pp. 7-19. Available
here.
8.
Cen, H., Lugt, P.M., Morales-Espejel, G. (2014), “On the film thickness of grease-lubricated contacts at low speeds,”
Tribology Transactions, 57 (4), pp. 668-678, DOI: 10.1080/10402004.2014.897781.
9.
Cen, H., Lugt, P.M., Morales-Espejel, G. (2014), “Film thickness of mechanically worked lubricating grease at very low speeds,”
Tribology Transactions, 57 (6), pp. 1066-1071, DOI: 10.1080/10402004.2014.933936.
10.
Sniderman, D. (2016), “How coatings and surface engineering are shaping tomorrow’s world,” TLT,
72 (6), pp. 52-63. Available
here.
11.
McGuire, N. (2020), “Lithium’s changing landscape,” TLT,
76 (2), pp. 32-39. Available
here.
12.
NLGI media release. (April 13, 2020), “NLGI High-Performance Multiuse (HPM) Grease Specification Update. Available
here.
13.
Gould, B., et al. (2020, in press), “The effect of electrical current on premature failures and microstructural degradation in bearing steel,”
International Journal of Fatigue.
14.
Bedekar, V. and Lucas, D. (March/April 2020), “Engineered coatings for roller bearings help avoid costly repairs,”
North American Clean Energy. Available
here.
15.
McGuire, N. (2020), “Solid coatings: Not just for space vehicles anymore,” TLT,
76 (10), pp. 38-48. Available
here.
Nancy McGuire is a freelance writer based in Silver Spring, Md. You can contact her at nmcguire@wordchemist.com.