Engine efficiency through surface engineering
Andrea R. Aikin, Contributing Editor | TLT Coatings January 2020
New research reveals how a more holistic approach reduces friction loss.
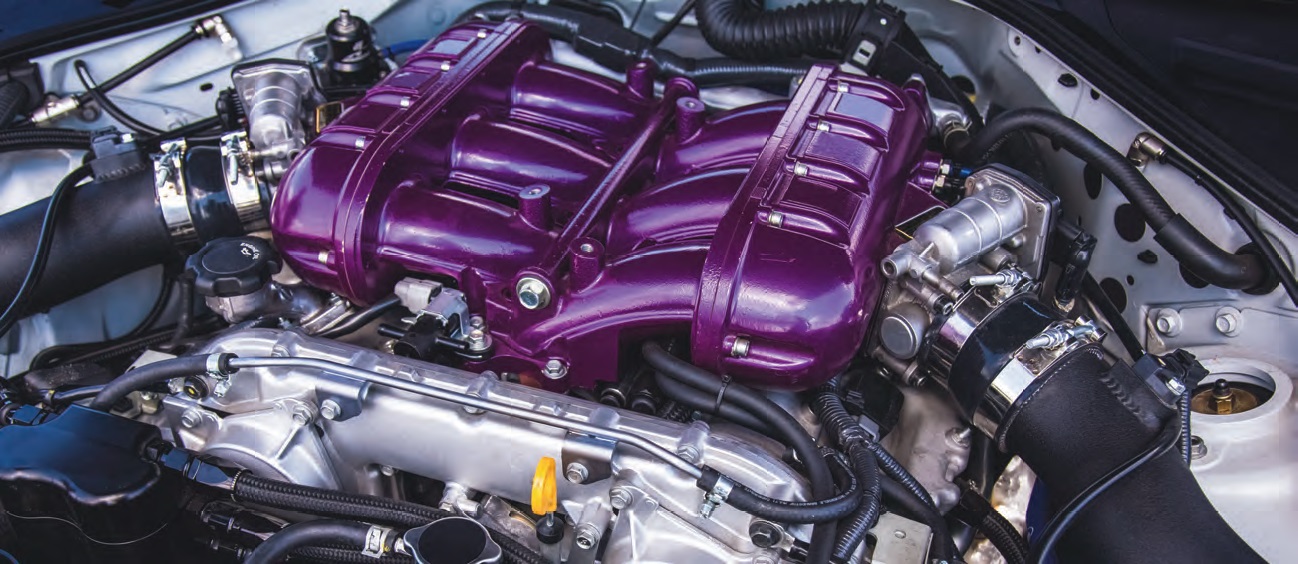
U.S. Corporate Average Fuel Economy standards require 3%-5% improvement in new vehicle fuel economy each year through 2025. Increasing engine efficiency continues to be a driving force behind engine design, with manufacturers looking at all options to reduce friction and increase fuel economy.
The different types of engines and their different uses, combined with the different types of fuels available, complicate the process of increasing engine efficiency. Although some technologies are well known, they still can be improved upon, and novel solutions to reduce friction and wear are being studied.
Modern engines use a wide range of coatings, surface finishes and texturing on engine parts to reduce wear and friction on moving parts. In addition to coatings, finishes and texturing, lubricant additives in engine oil are used to reduce wear and increase fuel economy. However, in some cases, the combination of coatings and additives can have antagonistic effects, increasing wear and friction inside the engine instead of reducing them. In response to this issue, research is being performed to produce engine coating/lubricant combinations that work synergistically to reduce wear and friction.
Coatings
STLE-member Arup Gangopadhyay, the Ford Motor Co. technical leader for Powertrain Tribology in Novi, Mich., states, “The interface between cylinder bore and piston (and rings) contribute about 45% of the total frictional losses in an engine.” Coatings and surface finishes offer opportunities to reduce this engine-friction loss.
STLE-member Hamed Ghaednia, director of research and advanced manufacturing at Gehring L.P. in Farmington Hills, Mich., notes that tribology improvements in cylinder bore coatings usually occur through the introduction of surface porosity, where the surface pores act as pockets that hold lubricant and deliver the lubricant to the piston group contacts. These surface pores also offer a texturing effect on the surface that can improve film thickness and reduce friction. This use of pores offers new ways to design final surface finishes for various applications to reduce friction and mitigate wear.
Spray bore coating has been used in engines for nearly three decades. These coatings are a substitute for cast-in liners and offer benefits that include weight reduction, improved heat transfer, reduced crevice volume and improved bore spacing. Ghaednia notes that new studies are being done to improve spray bore coatings in conjunction with surface finish to improve the overall tribology.
Gangopadhyay found that the Mo-NiCr coating is widely used in gasoline engines on piston rings. The coating is typically deposited using a plasma spray process that results in the coating being a little porous and rough. In addition, CrN, a physical vapor-deposited hard coating, and solid lubricant diamond-like carbon (DLC) coating have been used recently for friction and wear reduction. Both the CrN and DLC coatings tend to be smoother than the Mo-NiCr coating.
The CrN and DLC coatings are used on the engine’s top compression ring and occasionally also on oil control rings. Both CrN and DLC coatings are hard, wear-resistant coatings that could be beneficial when a low-viscosity engine oil is used.
In newer engines, thermal spray coatings are being used on cylinder bores with the coating directly deposited on the aluminum bores, eliminating cast iron liners, which can save between 4-8 pounds of engine weight, depending on the engine architecture. The deposition process introduces porosity that is mostly less than 2%. However, Gangopadhyay noted that this friction reduction is attributed to oil retention, combined with the pores acting as randomly distributed texture that results in improved oil film thickness, which reduces asperity contacts. Asperity is the unevenness of a surface; even when polished to a mirror finish, some microscopic unevenness remains.
Gangopadhyay stated that “polymer coatings in crank bearings are increasingly used to protect against wear and seizure for turbocharged direct injection engines and engines with start/stop features in micro, mild and full hybrid applications.” These crank bearings contain solid lubricant particles that are mixed with hard particles in a polymer matrix. When low-viscosity engine oil is used, further improvements may be needed in wear protection.
Jianliang Lin, principal research scientist at Southwest Research Institute® (SwRI®) in San Antonio, Texas, and his team have two patents for the development of a special piston ring coating that has been shown to reduce friction and wear in both gasoline and diesel engines. The work was originally funded by the SwRI Internal Research Project with the goal of developing advanced low-friction nanocomposite coatings for piston rings for improving engine fuel economy.
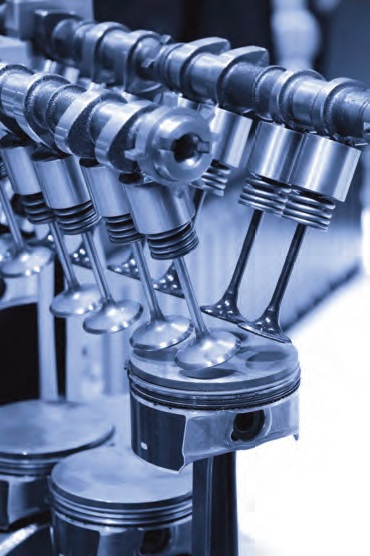
The interface between cylinder bore and piston contribute 45% of an engine’s total frictional losses.
The SwRI TiSiCN nanocomposite coating consists of 5-10 nanometer TiCN-nanocrystals embedded in a SixCyN-based amorphous phase. For the piston ring application, the coating can be 15-40 microns, although more than 500-micron thick coatings have been developed for other applications. The plasma-enhanced magnetron sputtering (PEMS) technique was used for depositing the piston ring coatings with the coatings’ structure and composition tailored to achieve multifunctionality (i.e., good adhesion, low friction, low wear rate and sufficient thickness).
Lin says, “The piston ring coating was iteratively optimized for its tribological performance in a series of tests including sequentially, pin-on-disc test and Plint TE77 test to narrow down the selection of the coating, single cylinder gasoline engine test to determine the piston ring friction contribution to the entire engine friction loss and heavy-duty diesel engine test to determine the coating wear.”
Then the best-performing coating was selected and deposited on the actual piston rings of a four-cylinder gasoline engine, which was then tested using the EPA standard method to determine fuel efficiency in city and highway driving. The SwRI research team found that the coated piston rings exhibited “approximately 1% of improvement in fuel economy,” compared to the vehicle engine without the coating.
Surface finishes
The surface finish that exists on cylinder bores is another area of study. Gangopadhyay notes that the typical surface roughness of bores is “about 0.3-0.4 µm (Ra).” Some recent engines have shown improved surface finishes; however, to realize the full benefit from surface finishes, the surface finish of the bore must be appropriately matched with rings and appropriate coatings.
Gangopadhyay noted that in the early 2000s many engines with sliding valve trains were produced with surface finishes and coatings on the cam followers to reduce friction. The recent trend is to use the roller finger follower valve train design, which offers less opportunity for coatings and surface finishes to be used.
According to Gangopadhyay, an optimal solution that considers coatings and surface finishes on cylinder bores, piston skirts and piston rings, “can show up to 2% fuel economy improvement in U.S. metro/highway drive cycles.” The full potential of these coatings can be realized by minimizing cylinder bore distortion.
Ghaednia noted that the laser texturing of surfaces (i.e., laser honing when applied to cylinder bores) introduces depressions in the surface in the form of pockets, lines or complex geometries. The goal of the texturing is to increase surface oil retention as well as introducing a texturing effect to control the oil film thickness and reduce wear. Ghaednia stated that one of the reasons laser honing is being evaluated again is that state-of-the-art computer-aided engineering tribological models are more effective at predicting the effect of textures on the surface.
Results
When looking at the different operating conditions of engines (i.e., gasoline vs. diesel, standard internal combustion engines vs. electric vehicle engines, etc.), the friction reduction benefits of these technologies varies depending on engine speeds and operating temperatures. For example, some piston ring coatings show significant benefits at low speed and high temperature, while others show a friction increase at low speeds but a friction decrease at higher speed.
Gangopadhyay notes that this behavior “could be very easily altered when combined with a spray bore coating,” which indicates that benefits vary depending on the application and the different operating conditions. For example, diesel engines tend to run at lower speeds and at lower engine oil temperatures than gasoline engines. In contrast, in hybrid engines, the oil temperature tends to be cooler than in standard engines as a result of the intermittent engine usage. These variables mean that friction benefits need to be evaluated depending on specific usage to identify the different operating conditions and the best technologies for those conditions.
Even when considering the finances of vehicle manufacturing and the competition between engine manufacturers, Ghaednia does not see barriers to introducing new manufacturing techniques and coatings because engine manufacturers “are open to bringing new manufacturing solutions and are investing in developing flexible and new techniques constantly.” This means that the number of new additives and coatings used in vehicles and engines is on the rise.
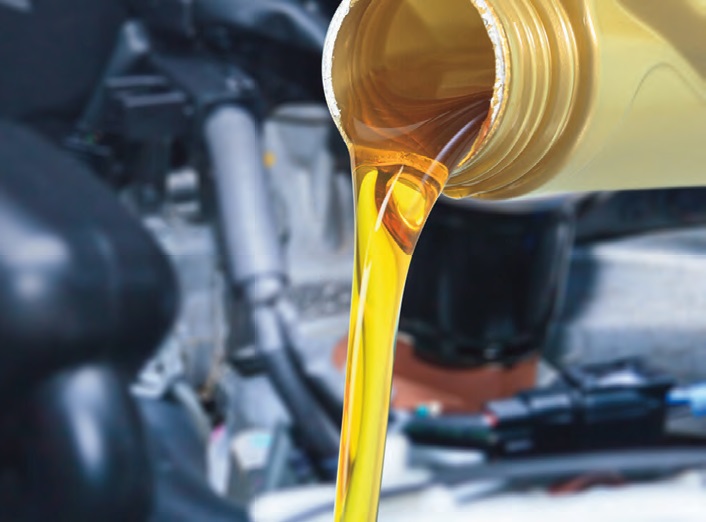
Lower-viscosity engine oils means new coating technologies are needed for wear protection on critical engine components.
Future focus
There is a trend toward using lower-viscosity engine oils from 5W-20 to 0W-20 and lower (e.g., 0W-16, 0W-12 and even 0W-8). This trend means there will be a need for new coating technologies for wear protection on critical engine components (i.e., valve and valve guide interface, piston skirt, bearings, etc.). If these coatings also can reduce friction, that will be a plus. However, these coatings need to ensure that other performance attributes like oil consumption and NVH (noise, vibration and harshness) are not compromised. Lower-viscosity oils also might need an improved surface finish on components like crankshaft journals, camshaft journals, etc., to best operate.
Lin notes that current SwRI research is focusing on using the previously described special piston ring coating on other moving components in an engine (e.g., camshafts, fuel intake valves, exhaust valves, etc.) to further improve fuel efficiency and reduce friction. The coating has already been used in other applications where low friction and high wear resistance are needed, including in the oil and gas field and in cutting tools. Lin has found industry manufacturers to be interested in this new coating and noted that SwRI is “working with several international automotive business-related companies on research projects for further optimizing the coating microstructure and architecture for reducing friction and wear for engine components.”
REFERENCES
1. Lin, J. and Wei, R. (2018), “A Comparative Study of Thick TiSiCN Nanocomposite Coatings Deposited by dcMS and HiPIMS With and Without PEMS Assistance,” Surface and Coatings Technology, 338, pp. 84-95.
2. Lin, J., Wei, R., Bitsis, D.C. and Lee, P. (2016), “Development and Evaluation of Low Friction TiSiCN Nanocomposite Coatings for Piston Ring Applications,” Surface and Coatings Technology, 298, pp. 121-131.
Want more on coatings? Check out these TLT Archives stories.
1. Canter, N. (2010), “Oxidation-Resistant Metal Coatings,” TLT, 66 (11). Available here.
2. Canter, N. (2011), “Drying of Coatings,” TLT, 67 (4). Available here.
3. Zhmud, B. (2011), “Developing Energy-Efficient Lubricants and Coatings for Automotive Applications,” TLT, 67 (9). Available here.
4. Canter, N. (2014), “In Situ Testing of Jet Engine Turbine Blade Coatings,” TLT, 70 (12). Available here.
5. Canter, N. (2016), “‘Flip-flop’ Coatings: Impart Surface Versatility,” TLT, 72 (4). Available here.
6. Canter, N. (2016), “New High-Temperature Solid Lubricant Coating,” TLT, 72 (3). Available here.
7. Sniderman, D. (2016), “How Coatings and Surface Engineering are Shaping Tomorrow’s World,” TLT, 72 (6). Available here.
Andrea R. Aikin is a freelance science writer and editor based in the Denver area. You can contact her at pivoaiki@sprynet.com.