Meet the Presenter
This article is based on a webinar presented by STLE Education on June 18, 2024. A Review of Foam and Defoamer Theory for Aqueous Industrial Fluids is available at www.stle.org: $39 for STLE members, $59 for all others.
STLE member Stefanie Velez has worked at Münzing North America for over 10 years and is currently the industrial fluids applications manager. She is responsible for managing the technical service laboratory for industries including metalworking fluids, lubricants and other industrial markets. In this role, her responsibilities include overseeing the chemists working on customer projects in the technical service lab, new defoamer and testing development and providing technical support to the sales team and customers globally. She earned her bachelor’s degree in chemical engineering and her master’s degree in chemistry from the Stevens Institute of Technology. She is an active member of STLE and ASTM. You can reach her at s.velez@munzing.com.
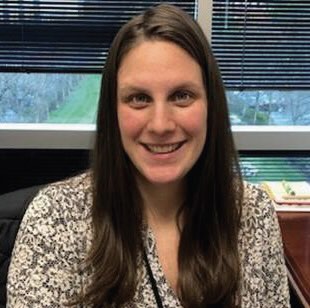
Stefanie Velez
KEY CONCEPTS
•
Foam is a dispersion of a gas phase in a liquid system and is undesirable for reasons that include its effects on the reduction of lubrication, heat removal and poor cleaning.
•
Defoamers are heterogeneous multicomponent systems composed of an active component, a carrier fluid and an emulsifier.
•
Identifying the correct defoamer for a particular application involves understanding the proper defoamer components for the application, as well as washability and relevant regulatory concerns.
The defoamer is a critical component of aqueous metal removal fluid formulation and industrial cleaner formulation. During use of the fluid, the defoamer functions to minimize foam buildup. Foam is undesirable for reasons that include its effects on the reduction of lubrication, heat removal and poor cleaning. Although the defoamer is expected to perform well initially, its defoaming properties should also persist over an extended period of time. There are many factors that affect defoamer performance, including inherent system foam tendency, filtration, defoamer chemistry and more. This article includes a review of what causes foam, defoamer chemistry types, the effect of filtration on defoamers, washability concerns and typical test methods.
This article is based on an STLE webinar titled A Review of Foam and Defoamer Theory for Aqueous Industrial Fluids presented by STLE member Stefanie Velez, fluids applications manager at Münzing North America. See Meet the Presenter for more information.
Why is foam an issue?
Foam is the froth of bubbles on top of a liquid. Entrained air is the dispersion of gas within the liquid rather than on top. Defoamer and antifoam are used somewhat interchangeably in the industry; however, a defoamer breaks existing foam, while an antifoam prevents foam formation. A deaerator is different in that it releases air to the liquid surface.
The specifics of form formation and its problems are different for every industry. For example, in metalworking, foam can lead to insufficient lubrication and cooling. In printed circuit boards (PCB), foam can lead to insufficient cleaning. In hydraulic fluids, the presence of foam can lead to a loss of pressure. In production, foam can lead to insufficient fill of containers, a reduction of machine speeds and feeds, higher down times, vacuum and pump problems and tank overflow. Foam can lead to decreased safety through reduced plant hygiene.
Foam is a dispersion of a gas phase in a liquid system. Air is introduced into the liquid mechanically or chemically. In a low viscosity, pure liquid, like water, bubbles coalesce, rise and burst rapidly. However, pure water is seldom used in a manufacturing situation where other chemicals are used to achieve different ends (e.g., lubricate, cool, clean, etc.). For example, surfactants orient at the air/water surface to lower the surface energy (i.e., surface tension, ɤ) of the fluid. This results in the air bubbles being coated by the surfactant. When the bubble goes to the surface to pop, the surfactant blocks the bubble. The liquid layer between the liquid and the air is called the lamella.
Foam is thermodynamically unstable, so it can be broken by defoamers. Kinetic stability can come from the surfactant stabilization. Mechanisms include steric hindrance, electrostatic, surface transport (Gibbs-Marangoni Effect), Gibbs film elasticity, surface viscosity and bulk viscosity. Steric hindrance and electrostatic are the most common mechanisms. In aqueous fluids viscosity is usually fairly low, so the entrained air dissipates fairly quickly in most systems.
In order for foam to dissipate, the lamella must thin so the bubble can break. Adsorbed nonionic surfactant molecules inhibit thinning due to steric/entropic repulsion of the liquid-soluble part of the molecules. This involves larger surfactant molecules repelling each other and creates a thicker lamella than desired. This effect is called steric hindrance or entropic stabilization. A charged surfactant can have an electrostatic stabilization on top of entropic stabilization, which can result in an extreme amount of foam.
Defoamers are typically needed in most applications. Table 1 lists some of the larger applications needing defoamers.
Table 1.
Foam control mechanisms in aqueous fluids
When foam buildup occurs, the defoamer droplet is meant to act on the surfactant layers at the air/liquid surface. Controlled incompatibility is the goal for a defoamer. The defoamer must be incompatible enough to provide foam control but remain compatible enough not to cause any adverse effects to the fluid stability. The defoamer’s effectiveness is based on its chemistry and droplet size.
Velez identified three major requirements for a defoamer. The defoamer must:
1.
be insoluble in the formulation that is being defoamed,
2.
have a lower surface tension than the foaming system, basically more hydrophobic, and
3.
be the right droplet size to be dispersed in the system.
A defoamer destabilizes foam because the interfacial tension between the defoamer and the water-based fluid is high, as the defoamer is hydrophobic. Figure 1 shows the defoamer droplet in the water-based fluid. Once the defoamer droplet enters the air interface, the interfacial tension between the defoamer and the air becomes much lower than between the defoamer and the liquid. Because the interfacial tension is lower in the air surface (i.e., more energetically favorable), the defoamer will spread to increase the surface area with the lower energy environment. Eventually it will bridge the lamella and rupture the foam bubble. Once the bubble is ruptured, the defoamer droplet can split until it eventually becomes too small to be effective. This is one reason that defoamers have potential to lose foam control persistence over time.
Figure 1. Schematic of foam bubble on top of liquid. Figure courtesy of Münzing.
Defoamer droplet size is a big part of the performance factors for how a defoamer works. Tiny droplets are well dispersed, but don’t provide much foam control, as the droplet is too small to bridge the lamella. A large droplet size can provide a large foam decrease initially, but over time the effectiveness drops and the defoamer will most likely cause stability issues. How the defoamer is added and the chemistry of the solution must be considered when determining defoamer effectiveness and performance.
Thermodynamic considerations come into play in understanding the relative performance of materials and which materials will not work (e.g., silicone versus polyacrylate). In practice nothing is ever at equilibrium. This means that kinetic factors must be considered, which include the number of droplets, the droplet size, the rate of bubble formation, temperature and the changing system composition. These factors also explain why there are so many different defoamers available. Velez notes that an empirical approach to identifying the right defoamer is more useful than a theoretical approach.
Defoamer components
Velez identifies three components of a defoamer:
•
The active components perform the defoaming function and are hydrophobic and low in surface tension. Possible defoamer actives for aqueous fluids are listed in Table 2.
•
The carrier fluid lowers the defoamer viscosity to carry and help disperse the actives into the fluid to be defoamed. Some examples of carriers are oil, polydimethylsiloxane (PDMS), organo-modified siloxane (OMS), polyglycol or water.
•
The emulsifier aids the dispersion and stability of the actives in the fluid to be defoamed and can be non-ionic, OMS or anionic.
Table 2.
Defoamers are heterogeneous multicomponent systems. Permutation and combination of different tools help in formulating defoamers to meet diverse requirements. Selection of a specific defoamer for a given fluid is often empirically driven due to the large number of variables involved.
Performance features of different defoamer actives are listed in Table 3. Some of the actives filter well, but some do not. Silica, wax, metallic soaps and molecular defoamers listed in Tables 2 and 3 can be options but are not strong at defoaming in the industrial market. Figure 2 shows the defoamer toolbox or how a droplet of defoamer works in a solution.
Table 3.
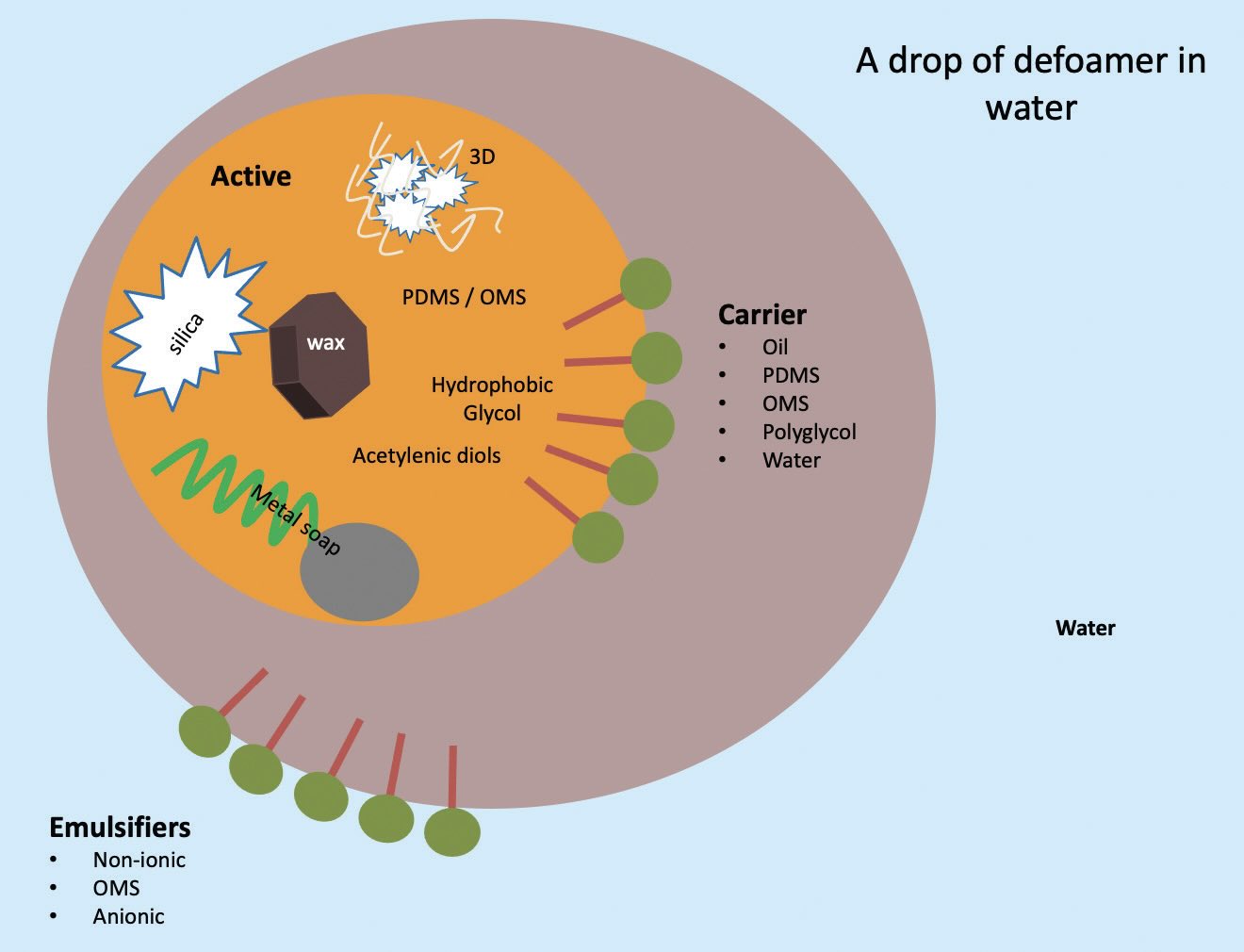
Figure 2. The defoamer toolbox. Figure courtesy of Münzing.
Defoamer testing
Foam is a concern for metalworking fluids (MWFs), and an understanding of foam performance is needed prior to field tests. General considerations include water type (e.g., deionized water, hard water, etc.), the age of the concentrate, how the dilution is performed and if the foam tests are relevant to the specific situation. Refer to the ASTM E3265-21 Standard Guide for Evaluating Water-Miscible Metalworking Fluid Foaming Tendency for foam tendency test methods used for aqueous fluids.
Compatibility and stability are key considerations for both the concentrate and in the emulsion if there is a dilution. This is a visual assessment of an additive’s separation compared to the concentrate without any additive. A sample of the concentrate including defoamer is made in a glass jar and allowed to age for a specific amount of time depending on the application. The assessment involves looking at the appearance in the jar of the concentrate’s surface (i.e., oil droplets/slick particulates cling to the container wall), body (i.e., haze, turbidity) and bottom (i.e., sedimentation, particulates). The point is to visually assess if the defoamer droplets are too small or too well dispersed or too large prior to putting the fluid into the testing system. The additives can be rated on a 1-5 scale, where 1 indicates no instability. This assessment is repeated as the concentrate ages to determine which additive is the most compatible with the concentrate. The stability of the dilution in water can also be monitored this way.
Foam testing can be performed using a number of different methods:
•
Shake testing can be performed in a jar or cylinder using hand or mechanical shaking, recognizing that mechanical shaking is more reproducible than hand shaking. The benefits of this approach are that it is fast and easy with a minimal amount of material consumed. However, this test represents only low shear that measures foam break and does not measure foam persistence.
•
Air sparging testing is another method where the diffuser type, flow rate and volume can be changed. The benefits of this method are that it is quick, consumes minimal material and provides a slight measure of persistence. However, the foam builds differently between bubbling versus agitation at the surface of the fluid and larger bubbles tend to form.
•
Blender testing offers speed and volume variations with the benefits of being quick, consuming minimal material with very high shear and small bubbles. However, this is not a persistence over time test.
•
Recirculation testing can be a longer-term test using different variations of equipment (e.g., fish tank, CNOMO [NR T 60-185], small scale peristaltic). This type of test is a better measure of foam tendency under continuous shear for a prolonged period of time, so it does measure persistence. However, this method can take longer, use more fluid and potentially requires custom equipment
(see Figure 3). CNOMO recirculation is a set method with a specific flowrate and time that consumes two liters of emulsion and requires specific equipment
(see Figure 4).
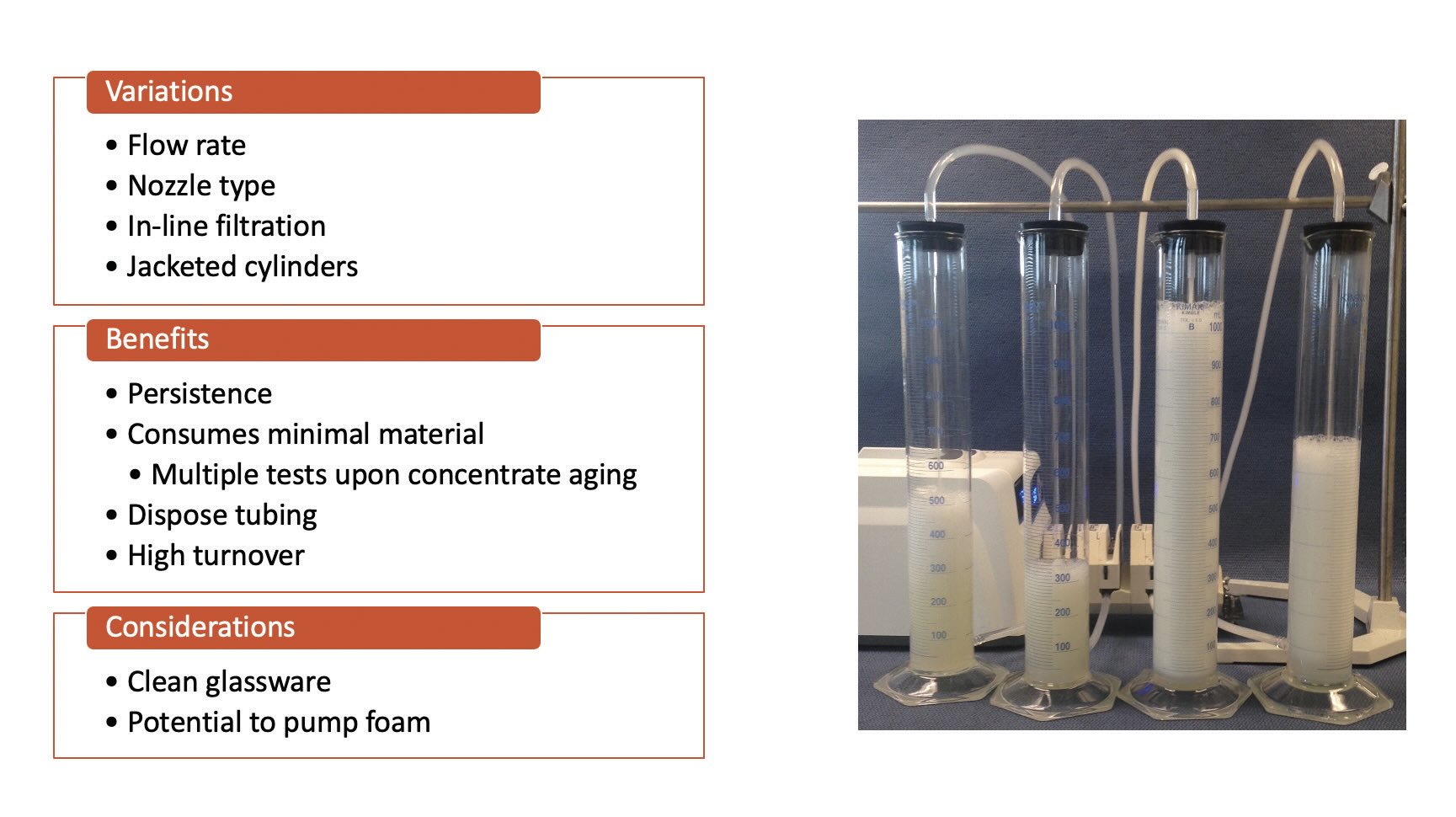
Figure 3. Small scale peristaltic recirculation. Figure courtesy of Münzing.
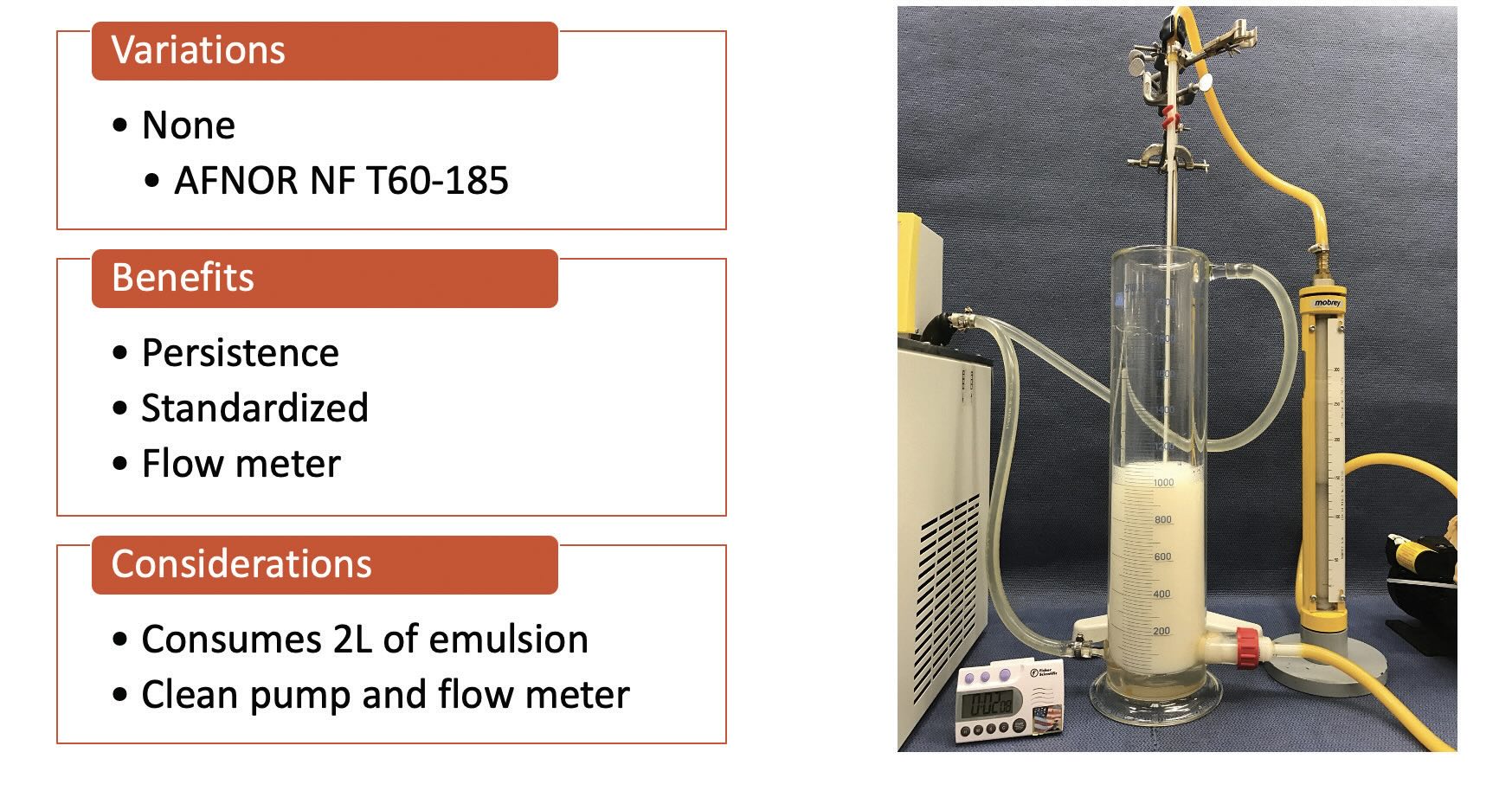
Figure 4. CNOMO recirculation. Figure courtesy of Münzing.
Filtration can affect defoamer performance in aqueous fluids. The filter material matters as nylon is hydrophilic (polar) and typically more expensive while polypropylene is hydrophobic (non-polar). Nylon filters typically do not really affect defoamer performance. Polypropylene filters can reduce the effect of a defoamer within the system. The filter pore size is less important than the filter material, although filter size of 5 micron or larger is always the best-case scenario to avoid filtering out too much of the defoamer itself. If the defoamer has the chance to connect with another hydrophobic surface (i.e., polypropylene), it is going to stay there, compared to a nylon hydrophilic filter, which the defoamer will see as the same as the system, so is less likely to be caught there.
Washability
Washability can be a concern for defoamers in aqueous solutions. Residual antifoam on a substrate can cause coating defects (e.g., craters, pinholes) due to low surface tension. Silicone-based antifoam droplets can readily spread on substrates and the adsorbed silicone layer can be difficult to remove completely, meaning that historically silicone is associated with coating defects
(see Figure 5). 3D siloxane-based antifoams show superior washability as their crosslinked nature inhibits spreading of droplets on substrates.
Figure 5. What is washability? Figure courtesy of Münzing.
To test washability in the lab, the metal panel can be placed into the MWF containing the defoamer to soak, which is the worst-case scenario. The metal panel is then washed or rinsed only with tap water and hung in an oven to dry. A primer and lacquer are then each applied to paint the metal piece. This results in a wide range of results as shown in Figure 6. Table 4 lists the typical effects of silicon on washability.
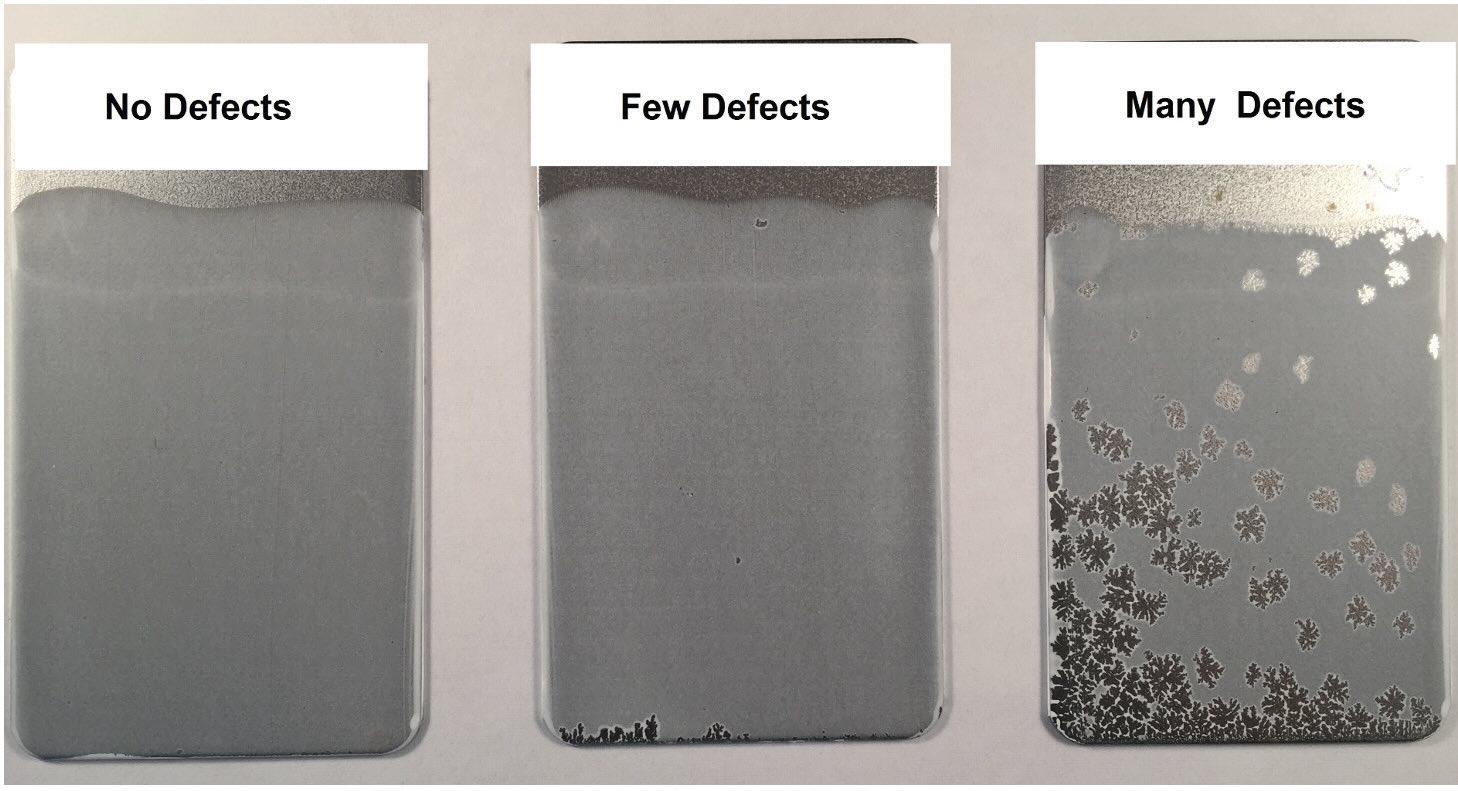
Figure 6. Substrate rating. Figure courtesy of Münzing.
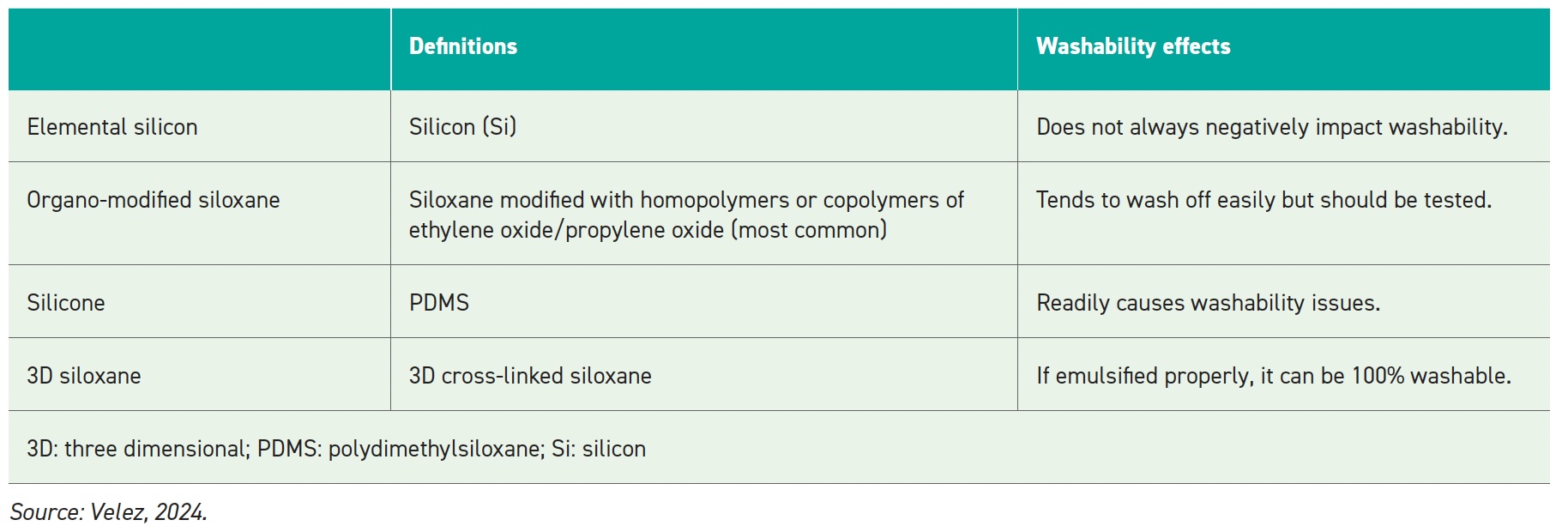
Table 4.
Regulatory concerns
Defoamers are much more heavily regulated now, especially in relation to aquatic toxicity. Regulations from Europe and California’s Prop 65 can be concerns, especially for cyclosiloxanes. If present in the mixture, biocides can also be a regulatory concern. As an example, the aerospace industry wants defoamers to be completely siloxane free.
Conclusions
Identifying the correct defoamer for a given application requires a thorough understanding of the industrial process and the possible defoamer components. Washability of the defoamer and regulatory concerns are also important factors to consider. The defoamer is a critical component of aqueous metal and industrial cleaner fluid formulations.
REFERENCE
1.
https://store.astm.org/e3265-21.html
Andrea R. Aikin is a freelance science writer and editor based in the Denver area. You can contact her at pivoaiki@sprynet.com.