Upcycling of nitric oxide to nitric acid
By Dr. Neil Canter, Contributing Editor | TLT Tech Beat August 2025
A zero-gap electrolyzer that allows for the starting materials to be fed into a membrane electrode assembly was used to produce nitric acid.
HIGHLIGHTS
A process has been developed for taking a known pollutant, nitric oxide, and converting it to nitric acid.
Electrochemical oxidation of nitric oxide in a gas-diffusion electrode linked to the hydrogen evolution reaction, achieved a greater than 90% Faradic efficiency for nitric acid.
When flue gas, a byproduct of combustion that contains carbon monoxide, carbon dioxide and sulfur dioxide in addition to nitric oxide was used, the conversion to nitric acid was also successful.
Nitric oxide is a major component in nitrous oxides (NOx), which are a major contributor to air pollution. Emissions of NOx have been regulated in such applications as mining (see Figure 2) where heavy duty diesel engines are used.
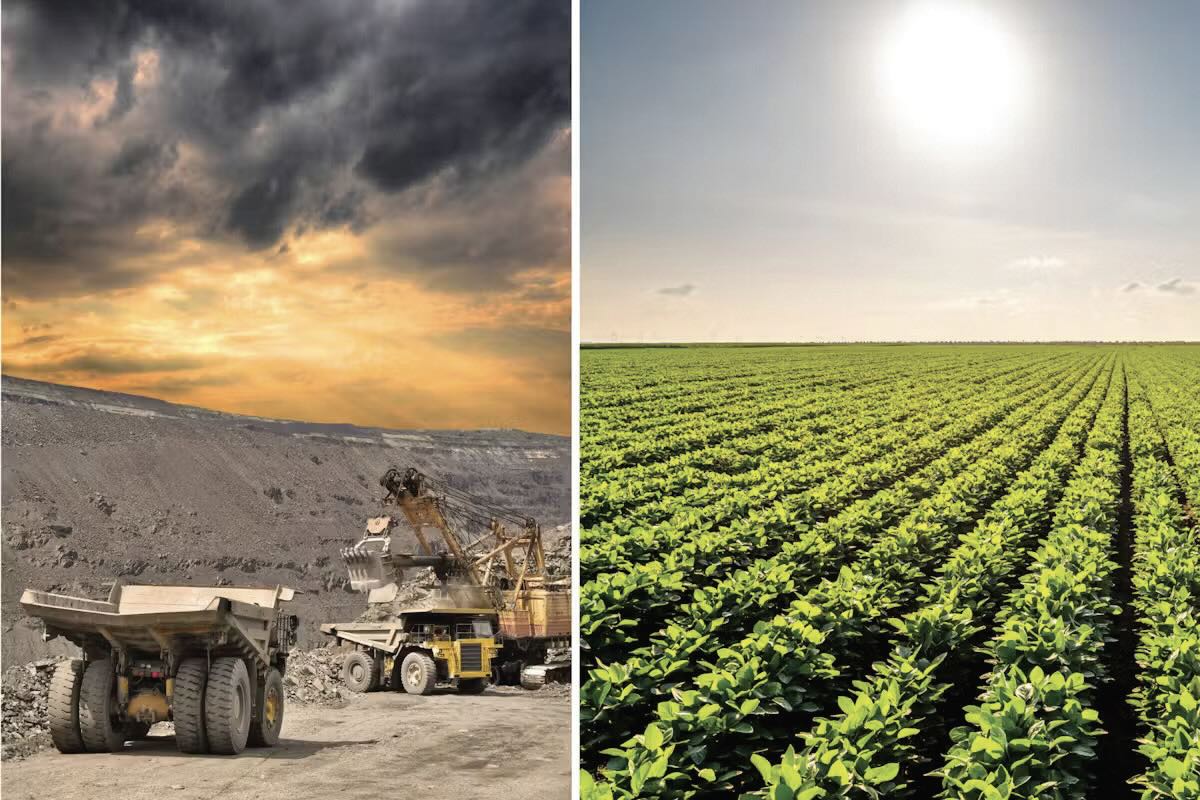
Figure 2. Nitric oxide, a byproduct from combustion of heavy-duty vehicles (see left image) can undergo an electrochemical oxidation reaction to produce nitric acid which is used in a wide range of applications including fertilizer production (see right image) and metal processing. Figure courtesy of Washington University.
Nitric oxide is also produced in stationary industrial applications such as those occurring in chemical plants and metal processing facilities. Combustion of fossil fuels in power generation applications can produce nitric oxide.
Nitric oxide is also produced as part of the main pathway used to manufacture nitric acid commercially. Ammonia, now under evaluation as a fuel in marine applications, can be oxidized to produce nitric acid with nitric oxide formed as a byproduct. Feng Jiao, the Lauren and Lee Fixel Distinguished Professor in the McKelvey School of Engineering at Washington University in St. Louis, Mo., says, “The use of ammonia in the Ostwald process to manufacture nitric acid is economical as long as a large-scale process is used. The reaction is conducted at high temperature using a catalyst which makes it capital-intensive and energy intensive. In addition, the Ostwald process requires a nitric oxide concentration above 10% to be efficient.”
Nitric acid is used as a raw material in the manufacture of fertilizers (see Figure 2) and can be utilized in the etching, refining and passivating of metals. Finding a more sustainable approach for producing nitric acid will assist users with their product carbon footprint and potentially expand the use of this material.
Jiao says, “An appealing option would be to find a pathway for converting nitric oxide to nitric acid under mild conditions that will be suitable for use at a smaller scale than the Ostwald process. Nitric oxide can react with air and water to produce nitric acid, but the process is very slow and requires elevated temperature conditions.”
Development of an electrochemical process to manufacture nitric acid is an appealing alternative according to Jiao. He says, “Using electrochemistry enables the reaction to be driven by electrons. This approach can potentially be conducted under near-ambient temperatures and pressures. Another benefit is that an electrochemical method is more suitable to lower production scales allowing for decentralized nitric acid production near nitric oxide waste sources. Potentially, the nitric acid could be manufactured in a concentrated form and be free of salts. The latter would minimize costs associated with product separations.”
Currently, no electrochemical process has been reported for converting nitric oxide to concentrated nitric acid. Jiao and his colleagues have now developed a procedure for achieving nitric acid manufacture that meets many of the objectives previously discussed. This represents a sustainable pathway for upcycling nitric oxide, a known pollutant and waste product, into a useful reagent, nitric acid, that can be used in many industrial applications.
Critical intermediate: nitrous acid
The researchers carried out a nitric oxide electrochemical oxidation reaction in a gas diffusion electrode that was linked to the hydrogen evolution reaction. By using a gas-diffusion electrode, the gas flow chamber was separated from the anolyte to allow for the direct introduction of gaseous nitric oxide and its co-reactant, water vapor, to the electrode surface. Vulcan carbon was used as the anode, 10% platinum on carbon was the cathode, and the anolyte was a dilute sulfuric acid solution.
Jiao says, “Vulcan carbon has been studied as a catalyst. This material is low cost but is not stable for prolonged operation, degrading over time due to oxidative corrosion.”
A greater than 90% Faradic efficiency for nitric acid was achieved when conducting the reaction at near ambient temperature using pure nitric oxide. When the concentration of nitric oxide is reduced to 0.5 volume %, the Faradic efficiency is still 76%. Both yields were obtained with a current density of 100 milliamps per square centimeter.
An additional experiment using flue gas (a byproduct of combustion also containing carbon monoxide, carbon dioxide and sulfur dioxide) was successful in affording a Faradic efficiency of 87.5% at a current density of 1 milliamp per square centimeter. This work demonstrates that the electrochemical oxidation can take advantage of nitric oxide produced at specific manufacturing sites and that other byproducts of combustion do not interfere with the conversion of nitric oxide to nitric acid.
The researchers used a technique known as flow electrochemical mass spectrometry (FEMS), which is a modified mass spectroscopy method, along with isotope labeling experiments to determine the reaction mechanism. Jiao say, “FEMS enables the mass spectrometer probe to be directly inserted into the electrochemical cell, enhancing the detection of reaction intermediates.”
To assist with this analysis, a modeling study was conducted by modifying active sites on the Vulcan carbon catalyst with hydroxyl, carbonyl, carboxy and quinone groups. Jiao says, “We found that hydroxyl groups may play a role in influencing the reaction which is consistent with the pathway from nitric oxide to nitric acid proceeding through a nitrous acid intermediate.”
The next step was to determine if nitric acid could be produced from nitric oxide using a zero-gap electrolyzer where the starting materials are fed into a membrane electrode assembly. When coupled with the hydrogen evolution reaction, nitric acid and hydrogen were both successfully produced.
Jiao says, “This experiment was conducted to demonstrate that salt-free nitric acid can be produced at a high concentration (32% in water). Without the need to use a supporting electrolyte, the process is more sustainable as energy is not needed to separate nitric acid from salts.”
Future work will further evaluate feedstocks that do not contain pure nitrous oxides and may include particle contaminants to understand if the electrochemical oxidation can produce nitric acid using waste streams that are generated industrially.
Additional information can be found in a recent article1 or by contacting Jiao at jiaof@wustl.edu.
REFERENCES
1. Xia, R., Dronsfield, S., Lee, A., Crandall, B., Liang, J., Hasa, B., Redder A., Wu, G., Goncalves, T., Siahrostami, S. and Jiao, F. (2025), “Electrochemical oxidation of nitric oxide to concentrated nitric acid with carbon-based catalysts at near-ambient conditions,” Nature Catalysis, 8, pp. 328-337.
Neil Canter heads his own consulting company, Chemical Solutions, in Willow Grove, Pa. Ideas for Tech Beat can be submitted to him at neilcanter@comcast.net.