Filters: Types, ratings and efficiencies
By Dan Holdmeyer, Contributing Editor | TLT Lubrication Fundamentals September 2023
Filtration is important in reducing wear in the equipment and maximizing the life of the lubricant and equipment.
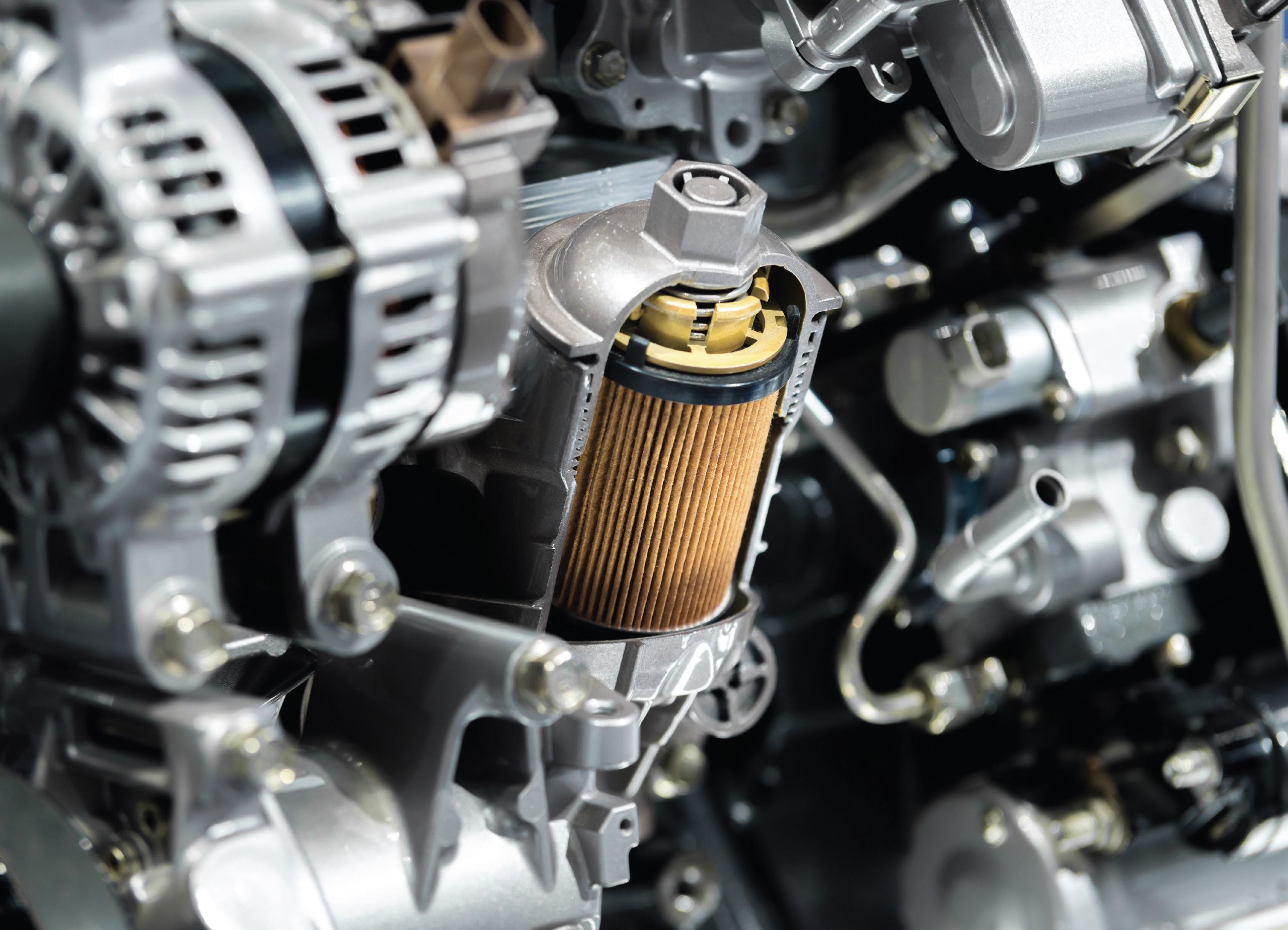
When you search “filters” on the internet, a myriad of water filters appear for a pool or house water supply, and even air filters for heating, ventilation and air conditioning (HVAC) systems. Add “oil” to the filter search (since this is a lubrication fundamentals article), and several web pages pop up on automotive filters.
Most automotive filters are cannister type, or spin-on filters, making them simple and easy to use (see Figure 1). Auto parts stores have reference manuals to identify what size filter is needed for each specific engine and vehicle. The engine compartments in most modern vehicles have little extra space for any oversized filters.
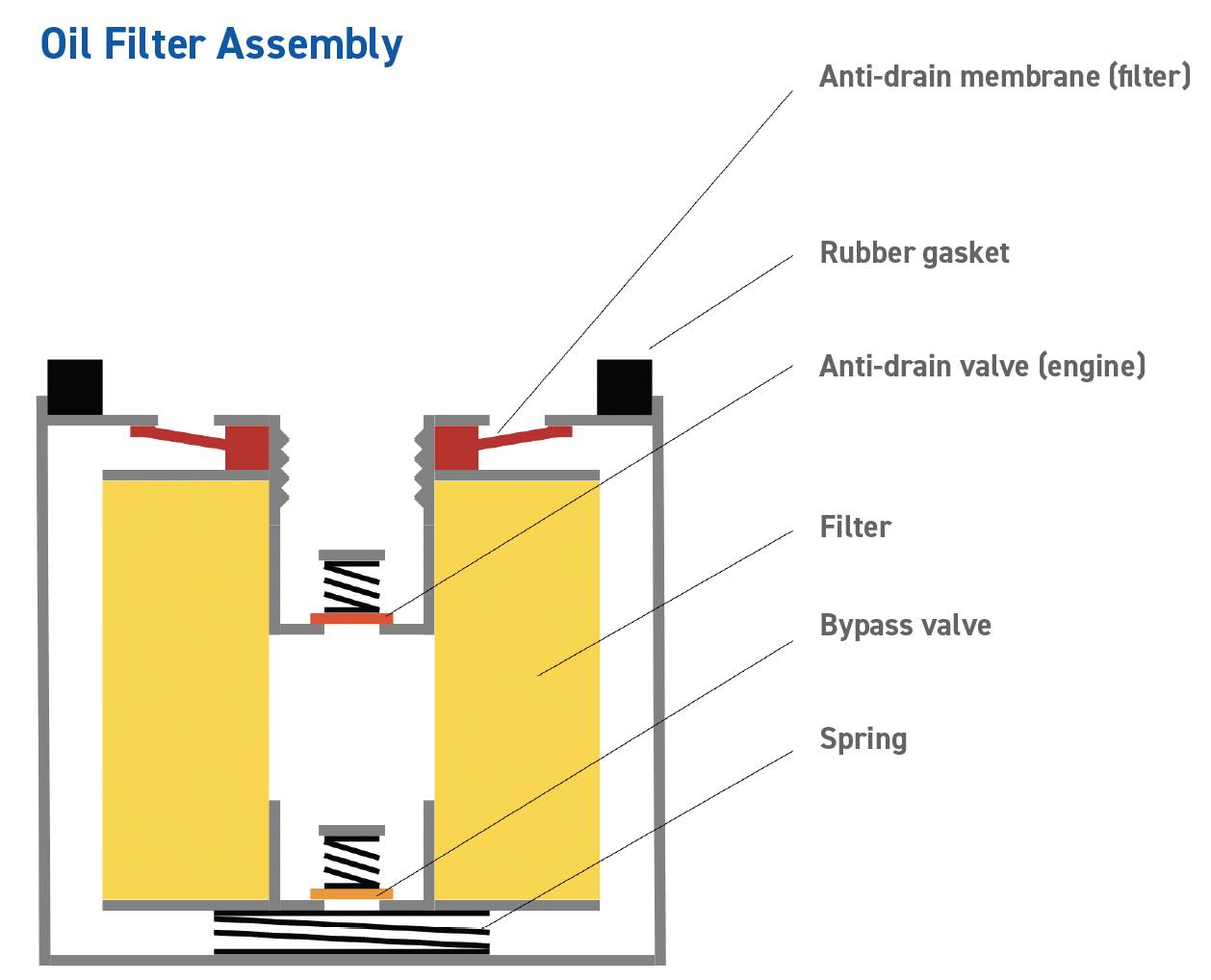
Figure 1. Spin-on (canister) filter. Figure courtesy of Sebastian Wendel, CC BY-SA 4.0, via Wikimedia Commons.
A filter wrench, one of many different available designs, is required to remove the old filter. A dab of fresh oil applied to the seal or gasket of the new filter is needed so the material is not torn as the filter is tightened in place, and so the seal or gasket is easily removed with the filter at the end of the filter’s life. The filter is mounted to the engine via a central threaded pipe and tightened snuggly by hand. No tool needed.
Simple to use, but with so many available from each of the sellers, there must be differences in what’s inside the filter housing, and there are. All automotive filters have the same basic components, but the component material and construction make a difference in how long a filter will last.
Generally, the less expensive filters are made with cellulose fiber filter media that will last about 5,000 miles under normal operating conditions. These filters work well with conventional motor oils that require a change out at 3,000 to 5,000 miles. Many engine OEMs today recommend synthetic, semisynthetic or synthetic blend engine oils, for better engine protection and longer oil drain intervals. To accommodate these longer drain intervals without having to change the spin-on filter in between oil changes, the filter media must be stronger and able to hold more contaminants without bursting or plugging and not filtering the oil. Fiberglass and polyester fibers provide added strength and contaminant storage capacity compared to cellulose fiber filters. Some filters place a steel mesh around the pleated filter media to provide added strength and life to the filter. The synthetic fibers and additional support raise the cost of the filter but are worth the expense to protect the engine and maximize its life.
Most filter OEMs in the automotive industry do a good job identifying not only the filter size but also the recommended miles for each of its filters for a particular engine and vehicle. Additionally, most will market the use of synthetic media in the filter to justify the additional cost, and some will describe the added media support built into the filter design. This information provides insight into what is inside the filter and how well it will perform for a better cost comparison.
Some additional marketing terms, appearing technical, may be used such as “98% efficient,” or a “10-micron filter.” These statements don’t include enough information to be technically specific and informative. Not all contaminants are the same size, thus a filter may be 98% efficient at removing large particles but not so efficient at capturing small particles. Or a filter may capture 10-micron size particles but at a lower efficiency level. Most spin-on automotive filters are 98% efficient at removing 40-micron size particles and larger.
Automotive engine filters are full-flow filters. They filter all the oil from the engine oil pump before the oil circulates through the engine. Some larger or high-performance engines may have an additional separate bypass filter circuit. The bypass filter is typically supplied by a separate smaller pump and filters out smaller sized contaminants before the oil is returned to the sump. This finer filtration helps clean the oil to extend the oil drain interval when monitored with used oil analysis while the full-flow filter protects the engine from excessive wear due to larger particles circulating through the engine. The bypass filter flow rate is much lower than the full-flow rate to reduce the amount of pressure buildup from the oil passing through a finer filter.
Some automotive OEMs are switching to cartridge filters (see Figure 2) to reduce metallic waste. The filter media element, made of cellulose, fiberglass or polyester fibers, is all that is replaced. The filter bowl, or container, is removed to access and replace the element. Other components found in a spin- on filter remain attached to the engine, such as the piping to and from the filter and the pressure relief valve. The filter bowl houses springs, seals and seats to prevent oil flow from bypassing the filter media element.
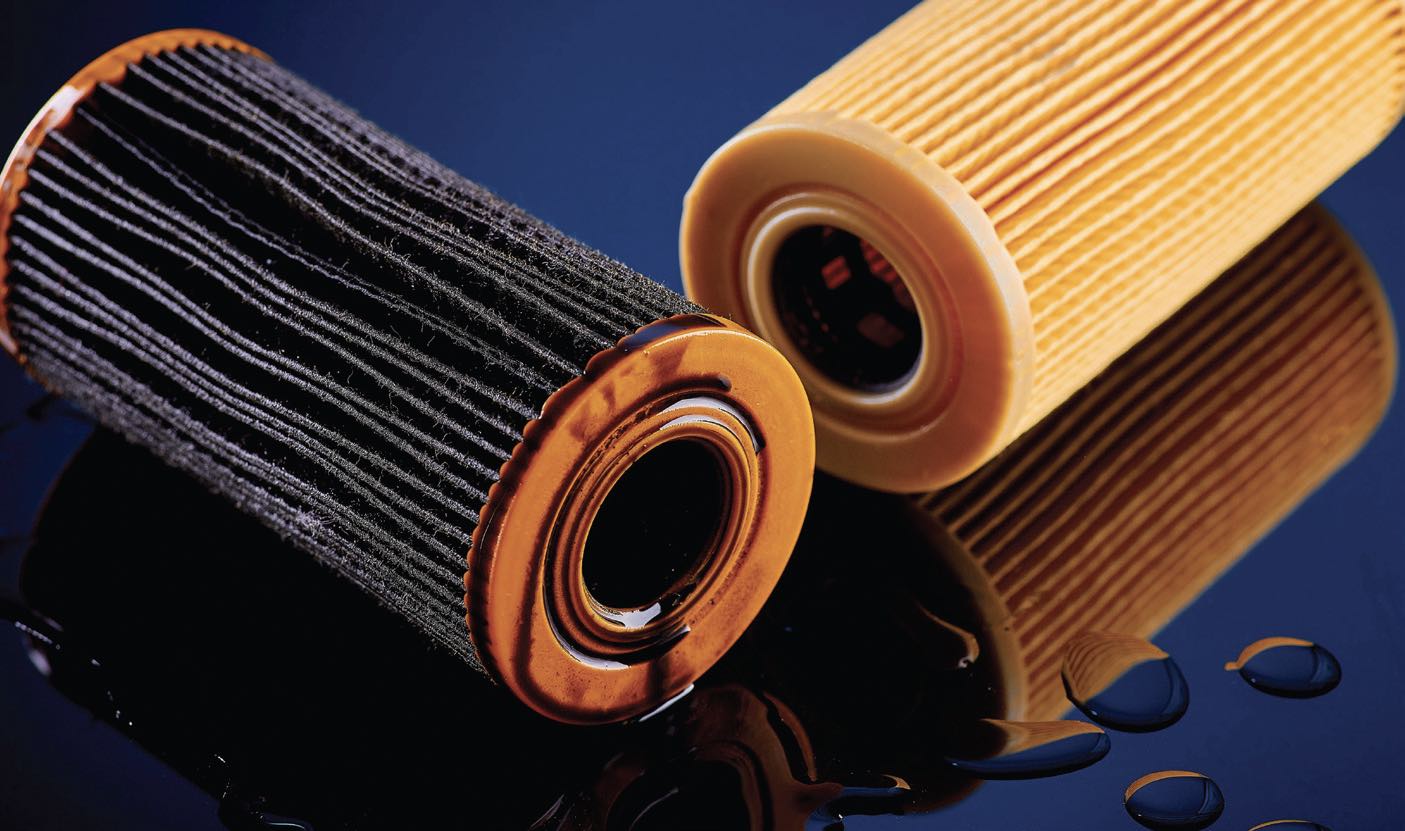
Figure 2. Cartridge filters.
Unlike automotive filtration requirements, industrial systems and filtration requirements vary greatly across the various industries and even within a given industry.
Most industrial lubricant filters are cartridge type filters. Fluid flow rates in industrial applications can be much greater than automotive engine oil flow rates and, thus, may require larger filter elements to accommodate the flow rates. Compared to a spin-on type filter, a cartridge filter replacement not only reduces the larger metallic waste potential but also the weight of the fluid-soaked filter and the amount of fluid waste.
Filter media efficiency is a critical specification for industrial applications. Industrial applications, particularly hydraulic systems, require finer filtration than provided by automotive engine oil filters. Many hydraulic valves require removal of particles smaller than 10 microns to reduce wear and help prevent valve sticking. Therefore, a typical engine spin-on filter is not recommended for use in high pressure industrial hydraulic systems but may be suitable for an industrial gear application. Each industrial application has unique requirements and, thus, a system, or systems, of comparison is necessary to achieve desired filtration, or oil cleanliness, goals.
A “nominal” 10-micron rated filter can remove 10 micrometers-sized particulate— however it also may allow larger particles to pass through. A nominal filter rating is a manufacturer’s arbitrary specification with no industry sanctioned rating system.
An “absolute” 10-micron rated filter will allow any particle up 10 micrometers in size to pass through but will capture particles larger than 10 micrometers. Although absolute is a better effectiveness rating than nominal, there is still no industry standardized test method for this value.
“Beta ratio” provides a more scientific method to rate filter element efficiency. In 1981, the industry published the International Organization for Standardization (ISO) 4572 to quantify filter efficiency. ISO 4572 has since been replaced by ISO 16889, with ISO 16889:2022 being the most recent version, which also is a multi-pass test methodology to report filter efficiencies. The multi-pass methodology is necessary as filtration media do not provide absolute results as there are many factors that affect filtration effectiveness. Thus, average numbers from all the multiple passes are used to get a beta ratio. The most commonly used beta ratios are 75, 100, 200 and 1,000.
Beta ratio is the number of particles of a given size and larger upstream of the filter divided by the number of same sized particles and larger downstream of the filter. For example, a β5 = 200 (a five-micron filter with a 200 beta ratio) would on average allow only five out of every 1,000 five-micron and larger sized particles from the upstream fluid to pass through the filter. Or another way to look at it is that for every five-micron and larger particle downstream of the filter, there were 200 five-micron and larger particles upstream of the filter, on average. The efficiency of the filter can then be calculated from the beta ratio via the formula ((β5 – 1)/ β5) x 100%, or ((200 – 1)/200) x 100% = 99.5% efficient (see Table 1).
Table 1. Efficiency and beta ratio
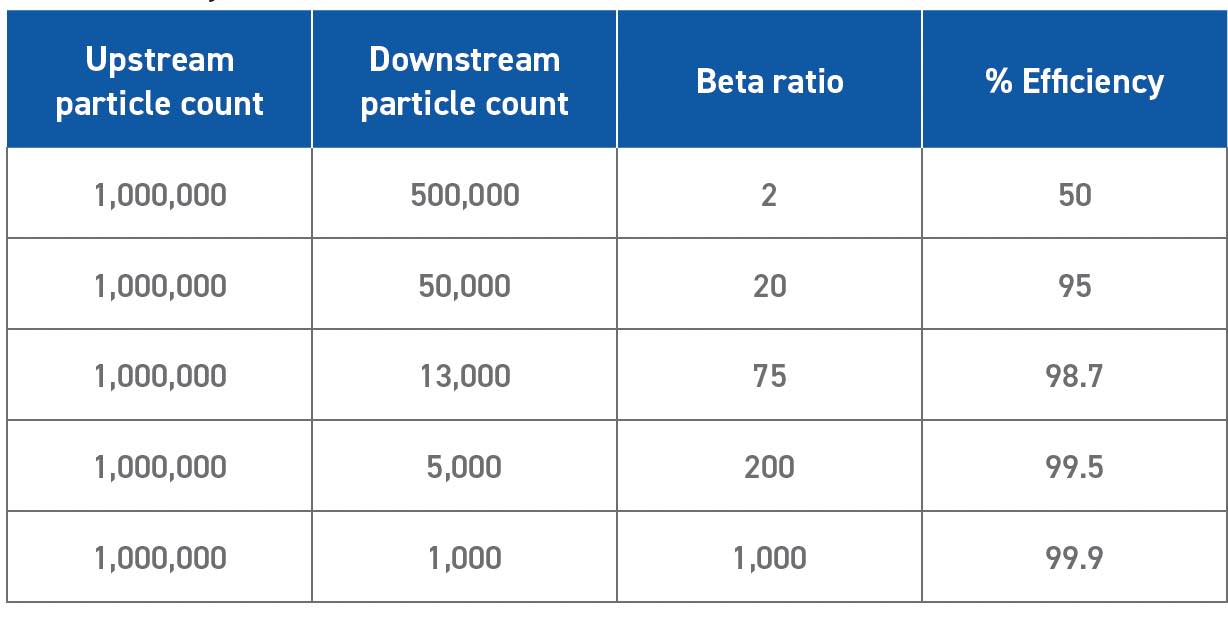
Beta ratio is an ISO standard to compare various filter elements’ media pore size, on average and expected performance. It does not indicate “dirt holding capacity.”
Dirt holding capacity is the weight of contamination the filter can capture and hold without bursting, plugging or reaching the maximum delta pressure across the filter allowed by the bypass valve. The size of the filter element gives good indication of the relative dirt holding capacity, but the filter media type also affects the capacity. Synthetic fibers are stronger and more uniform in structure than cellulose fiber filters providing for greater dirt holding capacity.
Fluid flow rate capacity is another critical factor in industrial system fluid filtration. Industrial lubricants have a wider range of viscosities in use, and the filter must be able to allow flow through the filter without going into bypass mode. Cold start up fluid viscosity needs to be calculated and compared to the filter’s capacity to assure filtered oil during startup.
Lubricant pressure and potential for pressure surges also affect filter choices. Beta stability measures the filter element’s ability to maintain its beta rating up to a given pressure. The robustness of the filter element also must be able to withstand system pressure and surges without collapsing or tearing apart. Metal mesh and metal element end caps will help sustain the element under these conditions.
Depending on the type of lubricant being filtered, the media, seals and adhesives used may need to be altered. The synthetic fibers may be used more in industrial applications because of the greater potential exposure to unique contaminants and various types of synthetic lubricants, not just mineral or synthetic hydrocarbon fluids. Cellulose fibers would swell and plug or disintegrate with different types of fluids.
Bypass filtration is another common system in industrial applications where a reduced flow of lubricant is taken from the reservoir, filtered and returned to the reservoir to clean the system lubricant. This is not to be confused with filtration bypass when the delta pressure across the filter is exceeded and the filter bypass valve opens to keep lubricant flowing to the system.
Duplex filter arrangements may be necessary on equipment that cannot be shut down for filter change out, such as electric power generating turbine. A duplex filter arrangement allows one filter to be changed while the parallel flow filter remains in operation (see Figure 3).
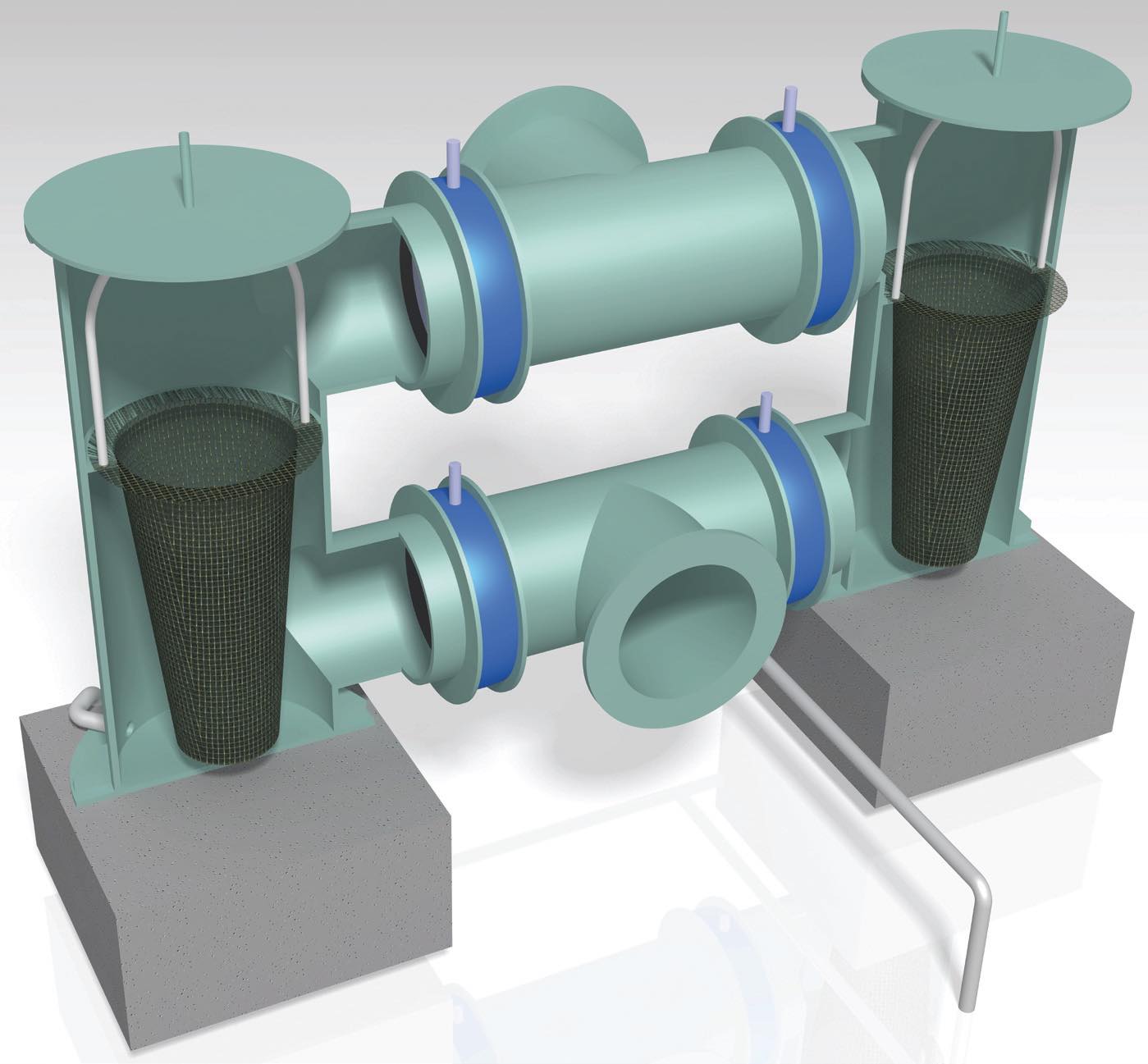
Figure 3. A duplex filter.
Delta pressure gauges on the filters are frequently used to determine the optimum time to change filter elements. Although some industrial system filters are changed on a calendar or hour meter basis.
Filtration is important to remove contaminants from the lubricant to reduce wear in the equipment and maximize the life of the lubricant and equipment. Thus, it is important to install the right filter. The filter must meet OEM specifications in dimension, filter media type, dirt holding capacity (filter life), efficiency, pressure capacity, flow capacity and compatibility.
Dan Holdmeyer is retired from Chevron Lubricants and is based in Washington, Mo. You can reach him at dan.holdmeyer@gmail.com.