Metal oxide tribofilms: Relating antiwear additive synergy with mechanical properties
By Daniel Delghandi1, Sage Fulco1, Pranjal Nautiyal1, Parker LaMascus1, Robert J. Wiacek2, Kevin T. Turner1, Robert W. Carpick1 | TLT Scholarship Research April 2023
1Department of Mechanical Engineering and Applied Mechanics, University of Pennsylvania, Philadelphia, Pa., USA
2Pixelligent Technologies LLC, Baltimore, Md., 21224, USA
Editor’s Note: This month TLT profiles the 2022 recipient of The E. Richard Booser Scholarship Award, Daniel Delghandi (University of Pennsylvania). The The scholarship is awarded annually to undergraduate students who have an interest in pursuing a career in tribology. As a requirement for receiving an STLE scholarship, students are given the opportunity to participate in a tribology research project and to submit a report summarizing their research. For more information about the Booser scholarship, visit www.stle.org.
Delghandi graduates with an undergraduate degree in mechanical engineering in May 2023 and will begin his doctoral studies in mechanical engineering in August. His research was conducted under the mentorship of STLE member Robert W. Carpick. Some of Delghandi’s interests and extracurriculars include volleyball, traveling and cooking. You can reach him at ddelgh@seas.upenn.edu.
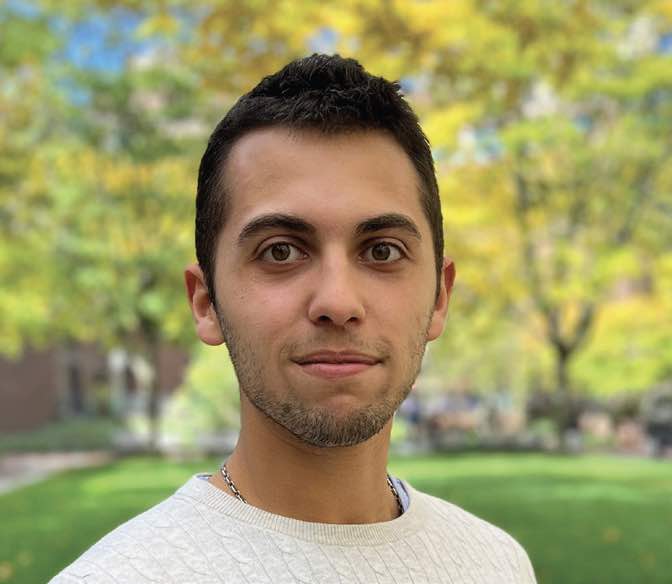
Daniel Delghandi
Abstract
A reduction in gear and engine oil viscosity is a potential solution in the quest for a higher efficiency transportation sector, but lower viscosity oil requires advanced antiwear additives. Zirconia nanocrystals form tribofilms that inhibit wear and scuffing while behaving cooperatively with commercial antiwear additives, suggesting that the antiwear additives may be integrated in the tribofilm, affecting its properties. This work investigates the mechanical properties of zirconia tribofilms formed with various concentrations of a phosphorus-based additive. Phosphorus integration is determined by spatially resolved compositional characterization, and nanoindentation is used to determine the mechanical properties of the formed tribofilms. We report that phosphorus can be integrated in the tribofilm bulk without influencing the hardness or elastic modulus of the tribofilm.
Keywords: nanocrystals, antiwear additive, tribofilm, nanoindentation and lubrication.
1. Introduction
The timeline to deal with impending climate change continues to shrink, demanding higher efficiency mechanical systems. The transportation sector accounts for 37% of U.S. energy consumption, making it a key area in need of improvement.
1 One highly sought and promising solution is a reduction in lubricant oil viscosity: lowering gear and engine oil viscosity by 25% would yield fuel savings of 2.5% and 5.5% respectively through a reduction in oil shear, churning and pumping losses.
2 However, with this viscosity reduction, there is an increased probability of direct asperity contact under high loads or system starting and stopping sequences. In turn, wear mechanisms such as scuffing and pitting may increase in prevalence.
3 As such, advanced antiwear (AW) and extreme pressure (EP) additives must be added to lubricants, or specialized coatings applied to surfaces, to maintain sufficient component lifetime.
Functionalized zirconium dioxide (ZrO
2) nanocrystals (NCs) have shown promise as an AW additive that can enable effective low viscosity lubrication.
4-6 Through a stress- assisted sintering mechanism, coined tribosintering, the ZrO
2 NCs form a tribofilm at sliding and rolling interfaces. These tribofilms, typically 50-300 nm thick, have been shown to develop over a wide range of temperatures and on various substrates.
5,8 ZrO
2 NCs can be dispersed in base oils as an AW additive to form an optically clear lubricant, inhibiting scuffing and wear and behaving cooperatively with proprietary S- and P-based AW/EP additives.
6-8 Elinski
et al. showed that when combined with a commercial additive package, the ZrO
2 NC tribofilm enhanced wear protection. Through chemical characterization, they demonstrated the incorporation of phosphorus in the tribofilm. This indicates that the elastic modulus and hardness of the tribofilm, properties partly responsible for wear performance, may have been altered by this inclusion. Despite abundant work on the growth and AW functionality of ZrO
2 NC tribofilms,
4-8,10 little literature on the mechanical properties exists. One exception is the work of Khare
et al.
8 Forming a ZrO
2 tribofilm with an atomic force microscope (AFM) and a reciprocating tribometer, they measured a hardness of 7.3 ± 0.7 GPa and 7.9 ± 0.2 GPa respectively, even higher than the 6.7 GPa hardness typically measured for bulk monoclinic zirconia. This suggests that the hardness of the underlying 52100 steel (11 GPa) was influencing the measurements, a common phenomenon for thin film indents known as the substrate effect.
11
However, Khare
et al.’s data were for tribofilms generated in neat oils, with no co-additives. The antiwear benefits of P-based AW/EP additives motivate measuring the mechanical properties of tribofilms formed with such co-additives. Doing so will provide an improved mechanistic understanding of AW/EP additive synergies with NCs, allowing for more effective design of NC-containing additive packages. Accordingly, this study investigates the influence of a phosphoric acid ester co-additive on ZrO
2 tribofilm hardness and elastic modulus. A ball-on-disc tribometer was used to form ZrO
2 tribofilms and white light interferometry was applied ex situ to obtain the final tribofilm height. Time-of-Flight Secondary Ion Mass Spectroscopy (ToF-SIMS) was then performed to determine AW additive integration in the tribofilm before nanoindentation on the disc was conducted to discern mechanical properties. This work provides new insights for tuning the antiwear performance of nanocrystal additives.
2. Materials and methods
2.1 Lubricant samples
Table 1 summarizes the lubricants tested in this study. The oil formulations were provided by Pixelligent Technologies LLC, who also synthesized the ZrO
2 NCs. The NCs, 5 nm in diameter, are dispersed in a polyalphaolefin (PAO) base oil via a proprietary capping agent, resulting in a monodisperse, optically clear and stable dispersion. The commercial additive used is Additin RC3760 (Lanxess, Cologne, Germany). It is based on an amine-neutralized phosphoric acid ester and contains no sulfur. The treat rates of the additive were chosen such that the P content in the formulation was 100 ppm and 500 ppm by weight respectively.
Table 1. Investigated lubricant compositions.
2.2 Tribofilm formation, surface characterization and wear testing
Tribofilms were produced by running the selected lubricants in a ball-on-disc tribometer (MTM2, PCS Instruments, UK), shown in Figure 1(a). The testing parameters are summarized in Table 2. After the tribofilms were formed, the specimens were sonicated with toluene followed by isopropanol to remove any oil residue. They were then sputter coated (Sputter Coater 108, Cressington, UK) using a single Au/Pd target,
12 and the surfaces examined using white light interferometry (NewView 6000, Zygo, USA) as shown in Figure 1(b). This provided detail on the tribofilm morphology and step-edge height (height above the steel substrate).
Table 2. Summarized tribofilm formation conditions.
Figure 1. (a) Mini Traction Machine set up. (b) WLI used to measure tribofilm step-edge height.
2.3 Nanomechanical characterization
Hardness and elastic modulus of the tribofilms formed on the discs were measured as a function of depth using a nanoindenter (TI-950 TriboIndenter, Hysitron, USA) equipped with a Berkovich diamond tip of 1140 GPa elastic modulus and 0.07 Poisson’s ratio. A tip area calibration on a fused quartz sample of known elastic modulus was performed. Both load-controlled (LC) measurements and continuous stiffness measurements (CSM) were taken across the width of the tribofilm, resulting in a robust data set of over 200 indents for each tribofilm. The hardness was then found through the ratio of the peak applied load to the projected contact area, and the Oliver- Pharr method was used to determine the reduced modulus.
13 Figure 2 highlights a typical load-displacement curve obtained during an LC measurement. To avoid measurement artifacts due to surface roughness, measurements were taken at indent depths greater than 10 nm. To avoid the influence of substrate properties, indents were made at depths less than ~20% of the tribofilm thickness. This is a difficult threshold to determine, as it is common for the tribofilms to be embedded in the steel, meaning the measured step-edge height with WLI does not reflect the true tribofilm thickness, but rather is a lower bound.
Figure 2. Representative load-displacement curve taken by indenting ZrO2 tribofilm at 125 μN load.
2.4 Compositional characterization
Compositional characterization of the tribofilm was performed with the use of ToFSIMS. This allows for spatially-resolved measurement of the chemical species in the tribofilm. The measurements were performed using a TOFWERK compact ToFSIMS (CTOF) spectrometer fitted inside a Tescan S8252X dual-beam plasma focused ion beam scanning electron microscope (FIB-SEM). ToF-SIMS was only performed on the ZrO
2 + RC3760 tribofilm formed with the higher concentration of phosphorus in the lubricant (500 ppm).
3. Results and discussion
All three formulations formed tribofilms under the chosen experimental conditions. Figure 3 highlights the surface morphology, profile, and step-edge heights of the three tribofilms formed on the disc substrate. For brevity, the tribofilms will be referred to as ZrO
2, ZrO
2 + 100 ppm P and ZrO
2 + 500 ppm P, although it is the lubricant used to carry the additives that contains this phosphorus concentration and not the tribofilms themselves. Toward higher treat rates of P in the lubricant, a tribofilm of greater step-edge height is produced, indicating enhanced antiwear performance. This is in line with the results of Elinski
et al.,7 showing the cooperativity between the employed AW additive and the ZrO
2 NCs.
This increase in height with higher P concentrations indicates that the inclusion of co-additives in the tribofilm may allow for thicker tribofilms. ToF-SIMS was performed on the ZrO
2 + 500 ppm P tribofilm to confirm this. Figure 4 shows the top-down view and cross-sectional view of the ZrO
2- and PO
2- ions recorded in the tribofilm. As expected, a strong zirconia signal is seen through the thickness of the tribofilm. Moreover, the milling process allowed for a more accurate estimation of tribofilm thickness than the height provided through WLI, indicating this tribofilm is ~350 nm thick. This exceeds the measured step-edge height of Figure 3, indicating that part of the tribofilm is embedded below the nominal steel height. The strong presence of the PO
2- ions confirms that P is integrated with ZrO
2 in the bulk of the tribofilm.
Figure 3. Scanning WLI images and corresponding height profiles of tribofilms formed on disc.
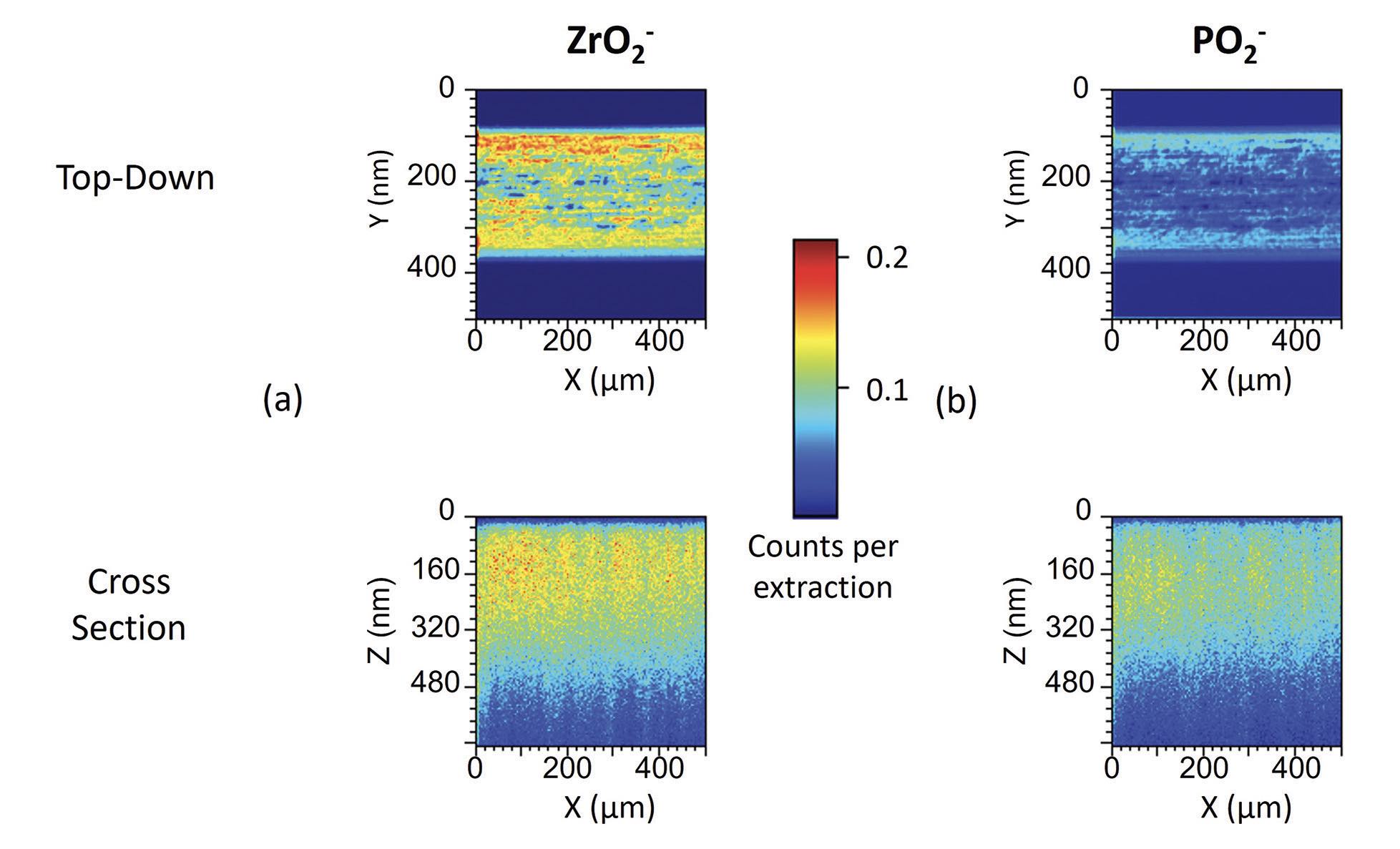
Figure 4. ToF-SIMS characterization of (a) Zirconia (m/Q = 122) and (b) phosphorus (m/Q = 63) integration in the ZrO2 + 500 ppm P tribofilm on the disc specimen.
Having confirmed the integration of P in the bulk of the ZrO
2 + 500 ppm P tribofilm, hardness and elastic modulus data were obtained as a function of depth via nanoindentation on all three tribofilms. The measured reduced modulus is defined by Equation 1, where E
R is the reduced modulus, and E
s, v
s, E
i and v
i are the elastic modulus and Poisson’s ratio of the sample and indenter respectively.
Consequently, the indentation modulus, E
s *, is defined by Equation 2 and corrects for the properties of the indenter tip.
14
Figure 5(a) shows the indentation modulus for the three tribofilms and bare steel as a function of indentation depth. The average value of the indentation modulus of the steel substrate beyond a depth of 30 nm is 234 GPa. Using 52100 steel’s known Poisson’s ratio of ~0.3, produces to a measured elastic modulus of ~ 213 GPa in agreement with the well-established modulus of 210 GPa.
19 For all tribofilms, we observe a decrease in E
s * until the 30-45 nm range, where the modulus appears to plateau, indicating this is the bulk tribofilm modulus. Moreover, within the uncertainty of measurement, E
s * is comparable for all three tribofilms, at 124 ± 20 GPa.
Figure 5(b) shows the hardness of the tribofilms as a function of depth. As with modulus, the tribofilms exhibit higher hardness at shallow indentation depths but then stabilize in the 30-45 nm range at 4.5 ± 0.8 GPa across the three tribofilms.
Figure 5. (a) Indentation modulus and (b) hardness plotted as a function of indentation depth for all tribofilms and the steel substrate.
The similar behavior and magnitudes of both hardness and indentation modulus for all three tribofilms indicate that P integration in the bulk does not measurably influence the tribofilm hardness or elastic modulus, but rather, ZrO
2 dominates the mechanical properties. Albeit, Scratch hardness, a potentially more directly translatable mechanical property to abrasive wear,
15 may not exhibit this same trend and will be the subject of future investigations. Furthermore, the commensurate properties across all tribofilms
(see Figure 5) suggest that they may be of comparable thickness with varying embedment into the substrate, indicated by the variation in step-edge height
(see Figure 3). The variation in embedment indicates that the P-containing AW additive may inhibit initial stage wear of the steel, prior to full tribofilm formation. This is in line with the mechanism proposed by Elinski
et al., where the adsorption of AW and EP additives on the steel surfaces protects against early adhesive wear.
7 The synergy between ZrO
2 NCs and AW additives will likely depend on additive chemistry and test conditions. This is outside the scope of this work but is the subject of a current investigation. At very shallow indents, between 10-20 nm, the ZrO
2 and ZrO
2 + 100 ppm P tribofilms both exhibited a higher hardness and indentation modulus than the ZrO
2 + 500 ppm P tribofilm. Likewise, the hardness and indentation modulus for all tribofilms was seen to decrease in the 10-30 nm range, prior to plateauing. These results may be due to an indentation size effect compounded by uncertainties introduced at extremely shallow indents,
16 but further discussion of this is out-of-scope.
Table 3 provides a comparison of hardness and indentation modulus data for 52100 steel and ZrO
2 collected in this study in comparison to the work of Khare
et al.8 The indentation modulus and hardness measured in this study are 30% and 38% respectively lower than the values recorded by Khare
et al., likely a result of the tribofilms being formed under different conditions, but also because of the depth at which indents were taken. We believe that thicker tribofilms formed in this study allowed for more accurate mechanical property measurement.
Table 3. Average nanoindentation hardness and indentation modulus for ZrO2 and steel from this study and existing literature.
Classical work on AW films has been based on Archard’s model for wear in sliding interfaces, where the wear volume is inversely proportional to hardness.
19 More recent work, however, has shown that the ratio of hardness to elastic modulus can provide a more accurate proxy for wear resistance than hardness alone.
20-23 This ratio represents the elastic strain to failure of the coating. Landauer
et al. posit that a lower
H/E ratio results in lower wear for sacrificial and self-healing tribofilms due to an enhanced ability to absorb energy upon asperity collisions in rolling and sliding contacts.
22 Similarly, they claim a higher
H/E ratio is preferential for bulk or coated material as it indicates a greater resistance to plastic deformation and hence wear.
As two points of comparison to our results, we consider zinc dialkyl dithiophosphate (ZDDP) and diamond like carbon (DLC). For sacrificial and self-healing tribofilms, particularly for automotive engines, ZDDP has remained the state-of-the-art AW additive for the past 70 years.
24 DLCs have been used as coatings for over 50 years and are used as coatings on upwards of 100 million parts per year.
25 While the mechanical properties of ZDDP tribofilms depend on the conditions in which the tribofilms were formed, Landauer
et al. found ZDDP tribofilms formed in the boundary regime to have an E
s* of 139 ± 27 GPa and hardness of 5.1 ± 1.4 GPa at room temperature.
21 DLC also ranges mechanical properties, but Chowdhury
et al. produced an amorphous DLC coating with a hardness of 15 GPa and an elastic modulus of 135 GPa.
26 Table 4 compares the
H/E ratio for our ZrO
2 tribofilms, a ZDDP tribofilm and a DLC coating. The ZrO
2 and ZDDP tribofilms are very close in value while the DLC is an order of magnitude larger, aligning with the hypothesis that higher
H/E correlates to enhanced performance for coatings. The similarity in
H/E between the ZrO
2 tribofilm and ZDDP tribofilm suggests that ZrO
2 tribofilms can provide high quality wear protection in environments like gearboxes, where ZDDP is unavailable. However, this does not consider the difference in composition between ZDDP (a phosphate glass) and ZrO
2 (a ceramic). Further work is needed to determine the suitability of ZrO
2 tribofilms as a permanent coating. '
Table 4. Comparison of hardness to elastic modulus ratio for ZrO2 tribofilm, ZDDP tribofilm, and DLC coating.
4. Conclusion
This work presented preliminary results on the mechanical properties of ZrO2 tribofilms formed in situ at a mixed sliding rolling contact with varying degrees of phosphorus integration.
• ZrO2 tribofilms formed with higher concentrations of a phosphorus-based antiwear additive exhibited enhanced tribofilm height, smoothness and wear performance, while also showing phosphorus integration in the bulk of the tribofilm.
• A ZrO2 tribofilm was shown to exhibit a bulk hardness of 4.5 GPa and indentation modulus of 124 GPa, exhibiting a comparable H/E ratio to ZDDP tribofilms.
• Phosphorus integration in the ZrO2 tribofilm does not influence the tribofilms hardness or elastic modulus, although this may vary with other forms of phosphorus or other types of co-additives.
The presented work is one of few to provide hardness and elastic modulus data on ZrO2 tribofilms, furthering the exploration of AW additive synergy with ZrO2 NCs. The elucidated mechanical properties showcase the robustness of ZrO2 tribofilms generated in situ at lubricated contacts, without the need for expensive manufacturing technologies used for depositing traditional antiwear coatings. This finding illustrates the promise of employing nanocrystals in lubricants for surface protection against harsh contact conditions in engines and gearboxes and opens new avenues of study. For one, a detailed exploration of the behavior in mechanical properties of ZrO2 with depth provides an important stepping-stone for developing a fundamental understanding of tribosintering theory. Exploring other mechanical properties, such as scratch hardness, may reveal further valuable information.
5. Acknowledgements
Daniel Delghandi gratefully acknowledges STLE for bestowing him with the E. Richard Booser Scholarship, which funded his research. He also acknowledges the Rachleff Scholars program at the University of Pennsylvania. This work was conducted in part at the Singh Center of Nanotechnology, which is supported by the NSF National Nanotechnology Coordinated Infrastructure Program under grant NNCI-2025608. This material is based upon work supported by the U.S. Department of Energy’s Office of Energy Efficiency and Renewable Energy (EERE) under the Advanced Manufacturing Office, Award Number DE-EE0009120.
REFERENCES
1. Dunn, D.R. (2022), “October 2022 Monthly Energy Review,” US Energy Information Administration, pp. 36.
2. Holmberg, K., Andersson, P., Nylund, N.O., Makela, K., Erdemir, A. (2014), “Global energy consumption due to friction in trucks and buses,” Tribology International. 78, pp. 94-114.
3. Stachowiak, G. W., Batchelor, A. W. (2014), “Engineering tribology,” Elsevier Inc. 4.
4. Dai, W., Kheireddin, B., Gao, H., Kan et al. (2016), “Formation of Anti-Wear Tribofilms via α-ZrP Nanoplatelet as Lubricant Additives,” Lubricants. 4, 28.
5. Kato, H., Komai, K. (2007), “Tribofilm formation and mild wear by tribo-sintering of nanometer-sized oxide particles on rubbing steel surface,” Wear. 262, pp. 36-41.
6. Lahouij, I., Gould, B., Demas N. et al. (2022), “Inhibition of Micro-pitting by Tribofilm-Forming ZrO2 Nanocrystal Additives: A Micro-pitting Rig and Transmission Electron Microscopy Study,” Tribology Letters. 70, 13.
7. Elinski, M., LaMascus, P., Zheng, L. et al. (2020), “Cooperativity Between Zirconium Dioxide Nanoparticles and Extreme Pressure Additives in Forming Protective Tribofilms: Towards Enabling Low Viscosity Lubricants,” Tribology Letters. 68, 107.
8. Khare, H., Lahouij, I. et al. (2018), “Nanoscale Generation of Robust Solid Films from Liquid-Dispersed Nanoparticles via in Situ Atomic Force Microscopy: Growth Kinetics and Nanomechanical Properties,” ACS Applied Materials & Interfaces. 10, 46, pp. 40335-40347.
9. Demas, N.G., Gould, B.J., Greco, A.C., et al. (2019), “Scuffing Performance of Low-Viscosity Gear Oil Containing ZrO2 Nanocrystals,” Proc. STLE/ASME Int. Jt. Tribology Conference.
10. Thrush, S.J., Comfort, A.S. et al. (2019), “Stability, Thermal Conductivity, Viscosity, and Tribological Characterization of Zirconia Nanofluids as a Function of Nanoparticle Concentration,” Tribology Transactions. 63, 1, pp. 68-76.
11. Saha, R., Nix, W.D. (2002), “Effects of the substrate on the determination of thin film mechanical properties by nanoindentation,” Acta Materialia. 50, pp. 23-38.
12. Benedet, J., Green, J.H., Lamb, G.D., Spikes, H. (2009), “Spurious Mild Wear Measurement Using White Light Interference Microscopy on the Presence of Antiwear Films,” Tribology Transactions. 52, 6.
13. Oliver, W.C., Pharr, G.M. (1992), “An improved technique for determining hardness and elastic modulus using load and displacement sensing indentation experiments,” Journal of Materials Research. 7, pp. 1564-1583.
14. Pereira, G., Munoz-Paniagua, D., Lachenwitzer, A. et al. (2007), “A variable temperature mechanical analysis of ZDDP-derived antiwear films formed on 52100 Steel,” Wear. 262, 3, pp. 461-470.
15. Vencl, A., Manic, N., Popovic, V., Mrdak, M. (2010), “Possibility of the Abrasive Wear Resistance Determination with Scratch Tester,” Tribology Letters. 37, pp. 591-604.
16. Fischer-Cripps, A.C. (2011), “4.7 Indentation Size Effect,” Nanoindentation, Springer. 3rd edition.
17. Savchenko, N., Sevostyanova, I., Sablina, T. et al. (2014), “The influence of porosity on the elasticity and strength of alumina and zirconia ceramics,” Proc. AIP Conference.
18. “AISI E 52100 Steel (100Cr6, SUJ2, UNS G52986),” MatWeb.
19. Archard, J.F. (1953), “Contact and Rubbing of Flat Surfaces,” Journal of Applied Physics. 24, 981.
20. Beake, B.D. (2022), “The influence of the H/E ratio on wear resistance of coating systems – Insights from small-scale testing,” Surface and Coating Technology. 442, 128272.
21. Ni, W., Cheng, Y., Lukitsch, M.J. et al. (2004), “Effects of the ratio of hardness to Young’s modulus on the friction and wear behavior of bilayer coatings,” Applied Physics Letters. 85, 4028.
22. Landauer, A.K., Barnhill, W.C., Qu, J. (2016), “Correlating mechanical properties and anti-wear performance of tribofilms formed by ionic liquids, ZDDP and their combinations,” Wear. 354, pp. 78-82.
23. Leyland, A., Matthews, A. (2000), “On the Significance of the H/E ratio in wear control: a nanocomposite coating approach to optimized tribological behavior,” Wear. 2, pp. 1-11.
24. Spikes, H. (2004), “The history and mechanisms of ZDDP,” Tribology Letters. 17, 3.
25. Bewilogua, K., Hofmann, D. (2014), “History of diamond-like carbon films – From first experiments to worldwide applications,” Surface and Coatings Technology. 242, pp. 214-225.
26. Chowduhry, S., Laugier, M.T., Rahman, I.Z. (2004), “Characterization of DLC coatings deposited by rf magnetron sputtering,” Journal of Materials Processing Technology. 153, pp. 804-810.