What do HTHS and PSSI have to do with viscosity?
By Dan Holdmeyer, Contributing Editor | TLT Lubrication Fundamentals April 2023
High temperature high shear and permanent shear stability index are two critical characteristics for improving efficiency and preventing wear.
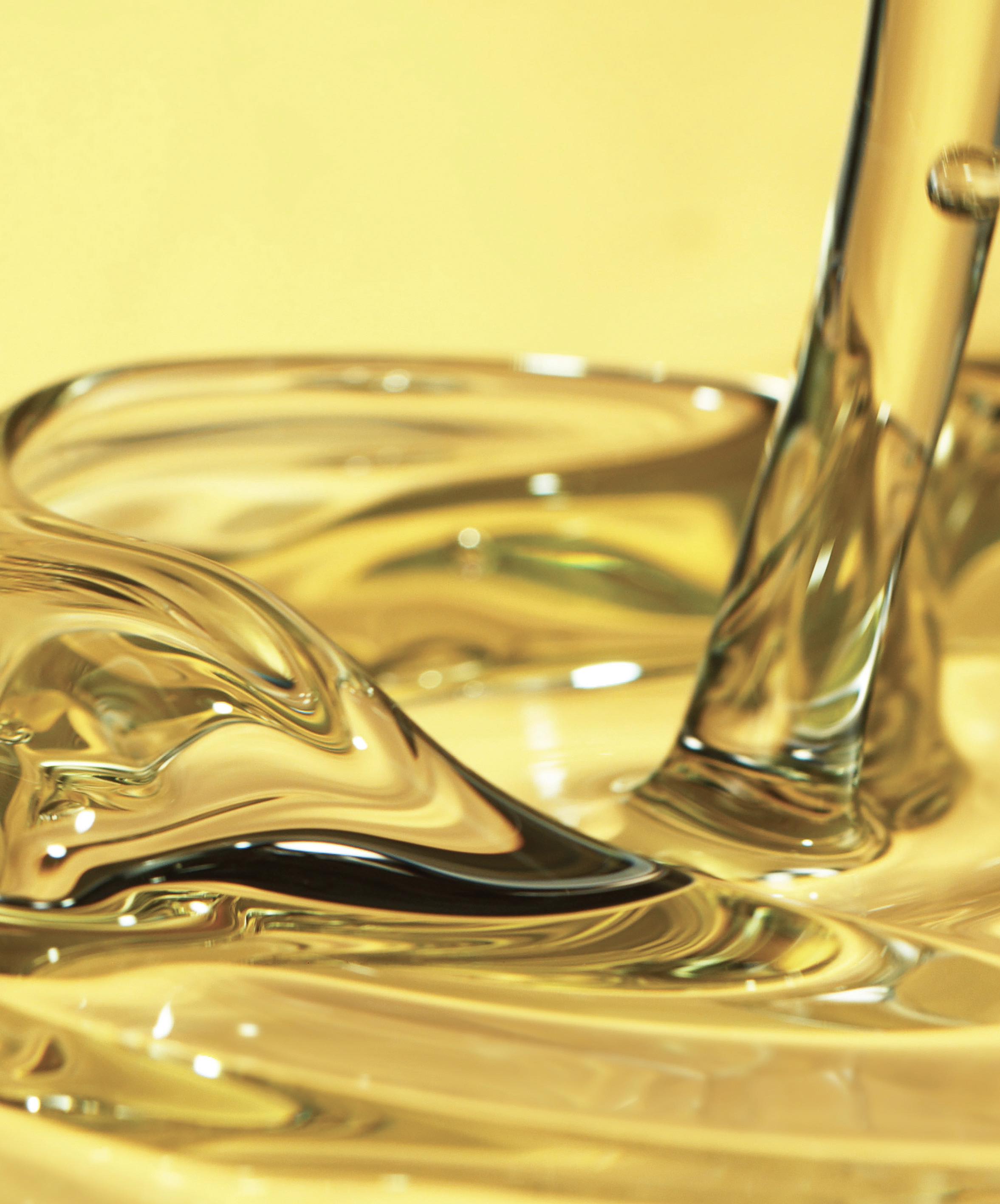
Two more characteristics to understand about viscosity under fundamentals of lubrication are high temperature high shear (HTHS) and permanent shear stability index (PSSI). Understanding these characteristics is critical for OEMs to meet higher and higher fuel economy requirements and for you to make sure you choose the right oil to protect your engine from premature wear.
Viscosity index (VI) modified oils contain polymers to lower the change in viscosity with respect to temperature, which is quantified by the VI as we discussed in the March 2023 TLT. These polymers are not only affected by temperature but also by shear. Let’s look at what these polymers are and how they work to understand shear’s influence on them.
Polymers are high molecular weight, or long, viscous molecules that coil up tightly when cold and stretch out, or uncoil, when heated. When cold, and coiled up tight, these polymers do not significantly affect the viscosity of the base oil in which they are dissolved. However, when the finished oil, the base oil with these polymers, is heated up to operating temperature, the polymers uncoil and stretch out so that they interact with the layers of oil that are moving relative to two metal surfaces creating more resistance to flow, which we know as viscosity.
Imagine a new deck of cards on the poker table. Your hand pushes the top card horizontally. The top card slides with your hand, the bottom card stays where it was on the table, and the cards in between slide over each other at a gradient of distance proportional to the distance from either the table or your hand. Now imagine the cards are made of cardboard versus plastic, and a bit “fuzzy” on their surfaces. The fuzziness of one card interacts with the adjacent card to impede movement more so than the cards of the smooth plastic deck of cards. The uncoiled polymers of viscosity index improvers (VIIs) in oil act like the fuzziness of the cardboard cards to provide resistance to flow.
A finished multigrade oil is formulated with viscosity modifiers (along with other additives) in a low viscosity base oil. The base oil viscosity meets the targeted low temperature viscosity of the finished lubricant. The base oil viscosity, although relatively high at cold temperatures, decreases as the oil is brought up to operating temperature. As the temperature rises, the viscosity modifiers uncoil, “stretch out” and interact with neighboring layers of the oil to slow their movement causing more resistance to flow, or an increase in viscosity. The viscosity increase from the viscosity modifiers with increased temperature, however, is not enough to offset the decrease in viscosity of the base oil. Thus, even though an SAE 10W-30 acts like an SAE 10W at low temperatures and like an SAE 30 at operating temperatures, the oil’s viscosity is still less at operating temperature versus at low temperatures. (For more detail, see the March 2023 TLT Lubrication Fundamentals article titled “Viscosity index and classifications.”)
You can see in Figure 1 how VIIs affect the VI relative to temperature, and how that provides the desired result of expanding the operating range of the equipment and lubricant. The VIIs react to temperature but also are affected by shear and exhibit both temporary and permanent shear characteristics.
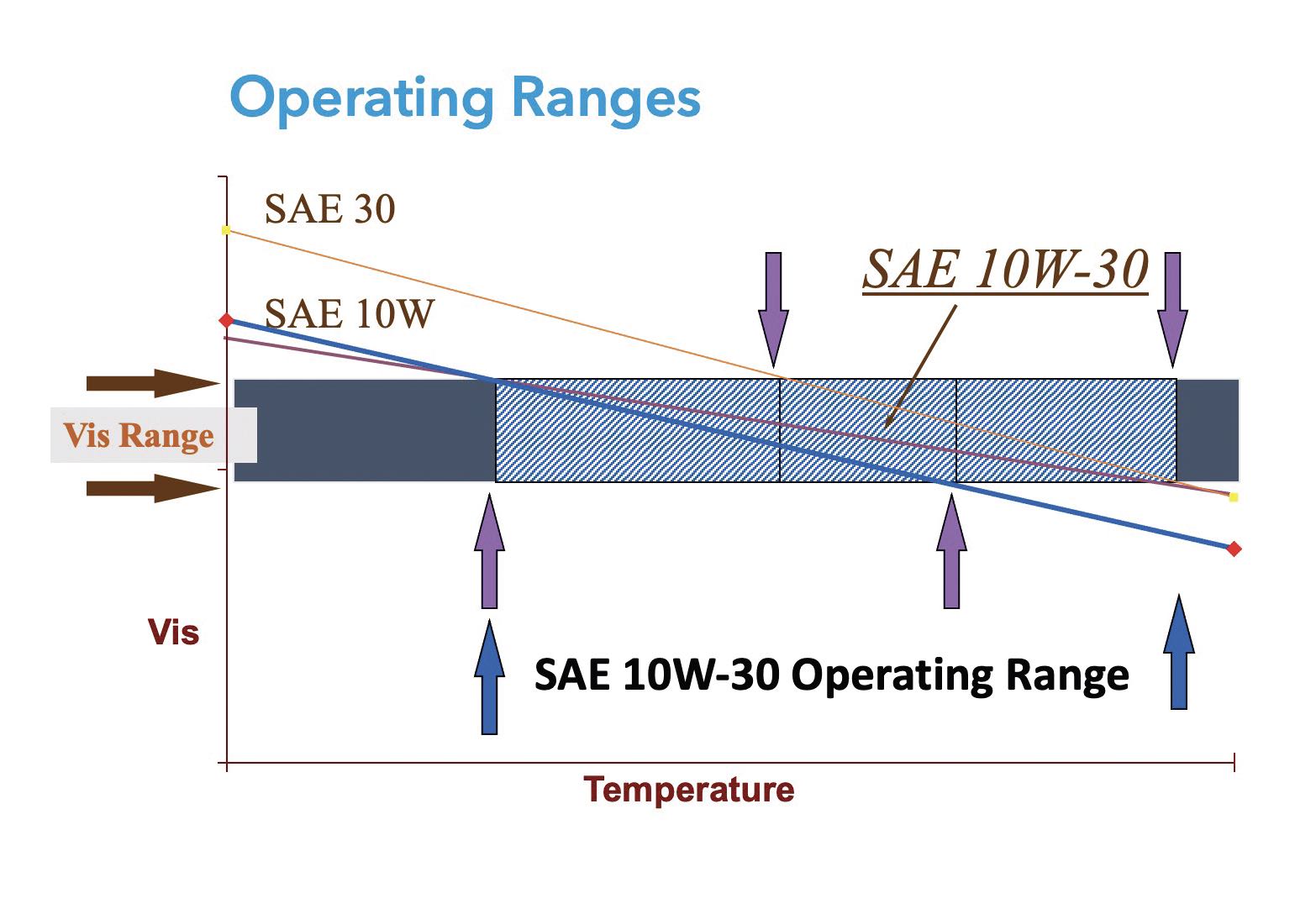
Figure 1. Operating ranges.
Temporary shear happens when the VIIs experience moderate stress that compresses the uncoiled molecules, so they don’t interact as much with adjacent layers of oil. The finished oil’s viscosity is temporarily lowered, but not down to the base oil viscosity at the given temperature. The viscosity returns to the finished oil’s original levels when the stress is removed. Common areas of moderate oil stress in an engine are the bearings and in the piston-ring-cylinder liner interface. This temporary shear is desirable in these regions as the temporarily lowered viscosity helps reduce the internal engine resistance providing higher fuel economy. However, the oil must still protect the engine from excess wear. Therefore, a lubricant’s temporary shear potential needs to be quantified to enable OEMs to meet fuel economy requirements and still protect their equipment.
HTHS viscosity measurements simulate the high temperature and shear conditions in the tight tolerances and fast-moving components in the engine. The HTHS test subjects the oil to constant shear at a constant temperature of 150 C. Switching engine oils from an SAE 15W-40 to an SAE 5W-40 with low HTHS provides a fuel economy improvement anywhere from 0.5%-1.5%, which is a big savings for over the road trucking.
Most people are familiar with the SAE J300 Engine Oil Viscosity Classification basically setting the minimum viscosity at operating temperature for SAE 20, 30, 40, 50 and even 60. News to some may be that there are now three more SAE viscosity grades: 8, 12 and 16. All of these classifications are quantified with a minimum kinematic viscosity at 100 C, which is a low shear condition measurement. HTHS is another SAE viscosity grade quantifier for the minimum viscosity under high shear condition at high temperature, 150 C. This is like the concept of cold cranking, a low shear condition test, and low temperature pumpability test via a mini-rotor viscometer, a high shear condition test, for quantifying the SAE xW viscosity grades.
Now, when you view SAE J300 Engine Oil Viscosity Classification charts, you will see both low shear and high shear tests quantifying the maximum viscosity for SAE 0W, 5W, 10W, 15W, 20W and 25W and minimum viscosity for SAE 8, 12, 16, 20, 30, 40, 50 and 60. Interestingly SAE 40 has two different HTHS limits. For SAE 0W-40, 5W-40 and 10W-40, the HTHS limit is 3.5, whereas the limit is 3.7 for SAE 40, 15W-40, 20W-40 and 25W-40.
It is important to know that older engines typically are not compatible with low HTHS oils. Be sure to use the right viscosity grade lubricant for your particular engine.
Permanent shear happens when the VIIs are subjected to high stress, and the long molecular structure is broken into shorter polymers. The shorter polymers no longer provide the desired viscosity at the operating temperature. The oil no longer “stays-in-grade,” or instead of being an SAE 10W-30, it now has the viscosities of SAE 10W-20 or lower.
A common area of high shear would be in the lubricant film between the engine cam lobes and tappets, or between the meshing of heavily loaded gear teeth in the transmission or final drives of mobile equipment. This is one of the reasons the viscosity of used automotive applications oils, or oils with high VIs, should be monitored at 100 C to see if the VIIs have experienced permanent shear and need to be changed out.
PSSI is a measure of how much a VII permanently shears under specific conditions. A VII with a PSSI of 10 loses 10% of its viscosity contribution to the finished oil’s viscosity, and a VII with a PSSI of 50 loses 50%. Therefore, the lower the PSSI, the more stable the VII is.
There exist several different ASTM methods for measuring PSSI. So, when comparing PSSIs of finished lubricants, it is critical to know the test method used. Some procedures pass the oil through a fuel injector, and different ASTM test methods require different pressures and number of passes through the injector. Another two ASTM test methods utilize a sonic oscillator to cavitate the oil creating the shearing mechanism. Although the shearing mechanism of the sonic and the injector methods are different, the results do correlate fairly well with each other. A more severe shear test is the KRL test, which utilizes tapered roller bearings under load for a specified duration and rpm. The KRL test is typically used for gear applications, whereas the injector and sonic tests are commonly used for engine and hydraulic lubricants.
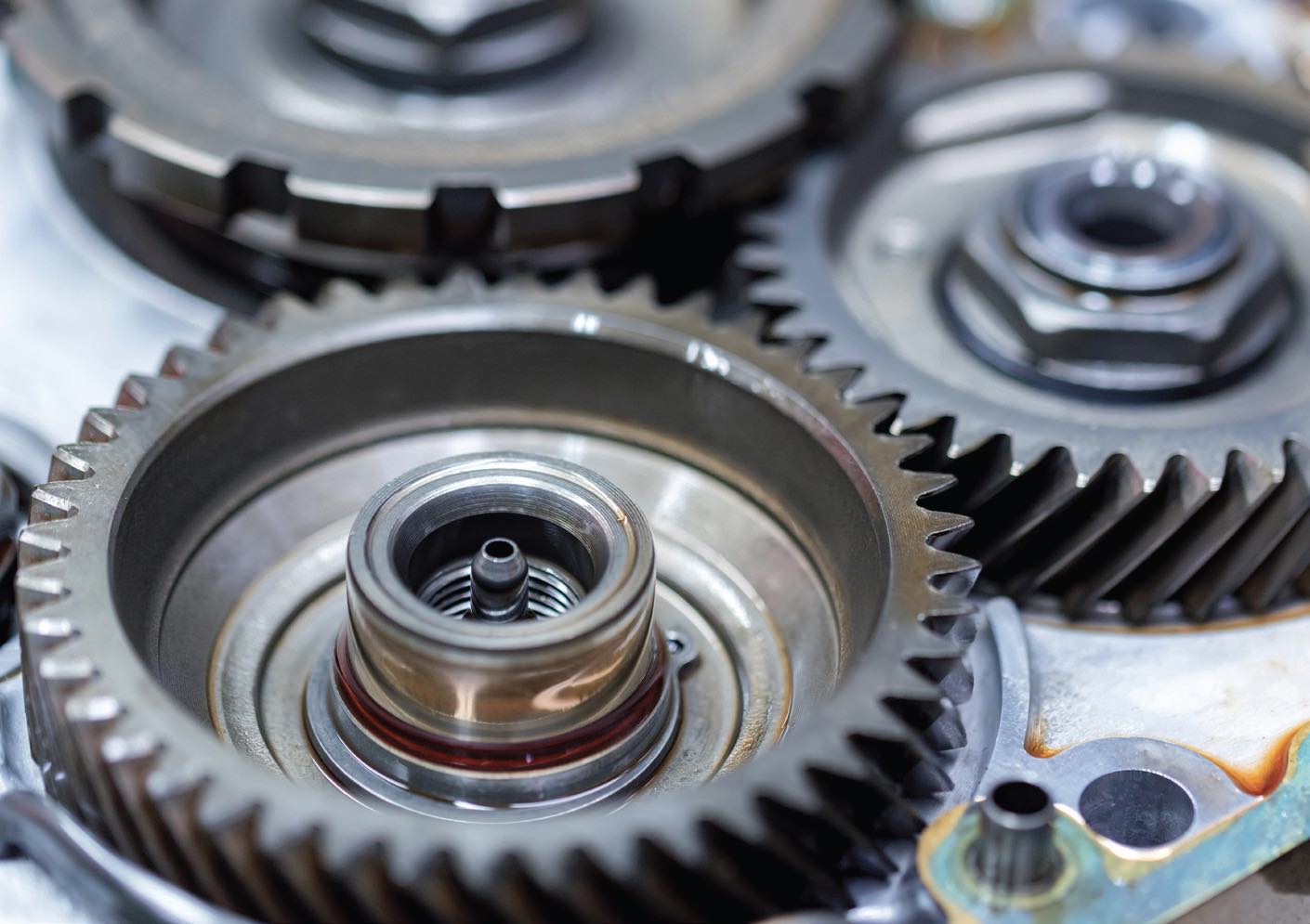
A common area of high shear would be in the lubricant film between the engine cam lobes and tappets, or between the meshing of heavily loaded gear teeth in the transmission or final drives of mobile equipment.
Shear stabilities of VIIs are inversely proportional to their molecular size. Generally, larger, or longer, polymers are more susceptible to shearing compared to shorter polymers. Consider how much easier it is to break a new standard-length pencil compared to the short golf course type pencil. The longer polymers are more efficient in providing the required VI, in that it takes a lower dosage of the long polymer VII than the shorter more durable polymers, and, thus, the cost of the finished lubricant can be lower. This is partially why the early versions of multigrade oils were known for not staying “in grade.” The early multigrade finished lubricants utilized the new-at-the-time polymers to enhance the VI of engine oils, but it quickly became evident more durable VIIs were needed. Shorter polymers improve the durability issue but require a higher dosage, and, thus, higher cost, to acquire the same level viscosity modification, but they do stay “in grade.” The appropriate compromise of efficiency versus durability, and cost, must be considered for the finished lubricant life in a given application. Extended life lubricants require more durable polymers to be able to provide protection over the life of the lubricant. Automotive driveline and other gear sets also should lean more toward the more durable VIIs having a lower PSSI.
PSSI is not a typical performance data result provided on product technical data sheets. However, if the kinematic viscosity at 100 C in used oil analysis results drops more than 10% before the oil change out, a shorter drain interval may be required. Or a switch to a “long-drain” interval oil that likely is formulated with more shear stable VIIs that also is likely more expensive could be cost effective.
Dan Holdmeyer is retired from Chevron Lubricants and is based in Washington, Mo. You can reach him at dan.holdmeyer@gmail.com.