KEY CONCEPTS
•
Oil analysis, i.e., MPC, RULER and APC, is still the best way to detect varnish, but other technologies, such as vibration analysis, make sense in some situations.
•
Between solvency enhancing additives, filtration and ion-exchange resins, there are proven ways to remove the varnish once it has formed.
•
Detection and remediation aren’t enough—the key to addressing the problem is getting to the root cause.
Despite advancements in terms of detection and remediation, the issue of varnish is not going away any time soon. So, the question is: What’s the best way to live with it? Regular oil analysis has always been critical for detecting build-up early, and now varnish removal technology is getting more effective.
STLE member Dr. Matthew G. Hobbs, manager, technical services, research and development, EPT Clean Oil, explains, “Unfortunately, varnish formation is an inevitability. Lubricant users can mitigate their risk of varnishing by selecting high-quality oils, but eventually all oil— regardless of formulation—will degrade. That breakdown can lead to varnish formation if it is not managed. The best way to protect against varnish formation is not to allow breakdown products to accumulate.”
The term “varnish” is commonly used as a catchall for byproducts of oil degradation. From the moment the lubricant enters the machine, it begins to degrade, and additives deplete. This becomes concerning when the additives are reduced to a point where they can no longer provide protection for the equipment. This also is the stage at which degradation greatly accelerates.
Sanya Mathura, MLE, MLT II, VPR, VIM, managing director, Strategic Reliability Solutions Ltd., compares varnish to cholesterol in the human body. “It can build up in our arteries and eventually cause clogs that restrict blood flow,” she says. “Cholesterol can be controlled through proper diet, exercise and with some condition monitoring in the form of blood tests. Similarly, a couple of approaches can be engaged to reduce the build-up of varnish or eliminate it altogether.”
Oil degradation and how it occurs
While “varnish” loosely refers to any form of deposit originating in lubricant, oil can degrade through several different mechanisms, each requiring various conditions for degradation to occur. So, just as important as detecting varnish is slowing further degradation by determining how it formed. According to Mathura, there are six major lubricant degradation mechanisms.
1 Each mechanism has unique environmental factors that contribute to producing different types of deposits.
1. Oxidation. This is the most common form of degradation. During the oxidation process, there is a decline in the concentration of antioxidants typically evaluated using the Remaining Useful Life Evaluation Routine (RULER) test. Eventually, the antioxidants become depleted, and the free radicals begin attacking the base oil. During this stage, polymerization can occur, which leads to the formation of deposits within the lubricant. When these deposits occur, they can get lodged in the smaller clearances (particularly servo valves), which leads to possible malfunctioning of the equipment. Due to the nature of varnish, it can act as an insulating layer, which increases the temperature throughout the equipment.
2. Thermal degradation. During thermal degradation, the oil can experience temperatures in excess of 200 C. At 200 C, the oil is cooked and produces carbon-based deposits, which is the characteristic type of deposit for this mechanism. The Fourier transform infrared (FTIR) analysis test is particularly useful in identifying the presence of these deposits.
3. Microdieseling. This is a form of thermal degradation. During microdieseling, air becomes entrained in the oil and moves from a low-pressure zone to a high-pressure zone. If the oil does not have good air release properties, then the entrained air will not make its way to the surface to dissipate. This entrained bubble in the oil can cause temperatures to rise. The bubble interface usually has some carbon accumulation and then implodes. This can be through a high implosion pressure, which results in soot, tars or sludge, or through a low implosion pressure, which can form carbon insolubles such as coke, tars or resins.
4. Electrostatic spark discharge. This may be classified under thermal degradation since it involves temperatures over 10,000 C. With this mechanism, oil builds up static electricity at a molecular level. Eventually, the static will build to a point where it produces a spark, and free radicals are formed. This can lead to uncontrolled polymerization producing varnish, sludge or other insoluble materials. One of the signs of this mechanism is the presence of burnt patches of membranes on the filters.
5. Additive depletion. Additives are sacrificial and will be depleted over time. This type of degradation can produce two types of deposits: organic and inorganic. The organic deposits are typically reacted rust and oxidation additives. Alternatively, inorganic deposits such as zinc dialkyldithiophosphate (ZDDP) can deplete and form a tenacious layer. The depletion of ZDDP will impact the rate of wear since this is the antiwear additive.
6. Contamination. This may be the most unrecognized form of degradation. This mode of degradation can be the initiator of other mechanisms such as oxidation, thermal degradation or even microdieseling. When contaminated with a foreign material in the lubricant, the foreign material can become a catalyst for one of the other forms of degradation.
Mathura concludes that identification of the type of degradation mechanism can aid in slowing the formation of varnish and/or filtering it. “Varnish exists in various forms and can consist of differing compositions,” she says. “Hence, it is important to understand the characteristics of the varnish being formed in a system before attempting to eliminate it. There are particular technologies such as solubility enhancers or specifically engineered filtration media that can be effective at removing varnish. However, this technology is heavily reliant on the type of varnish being formed and can be customized as per the system accordingly
(see Issues With the Term “Varnish”).”
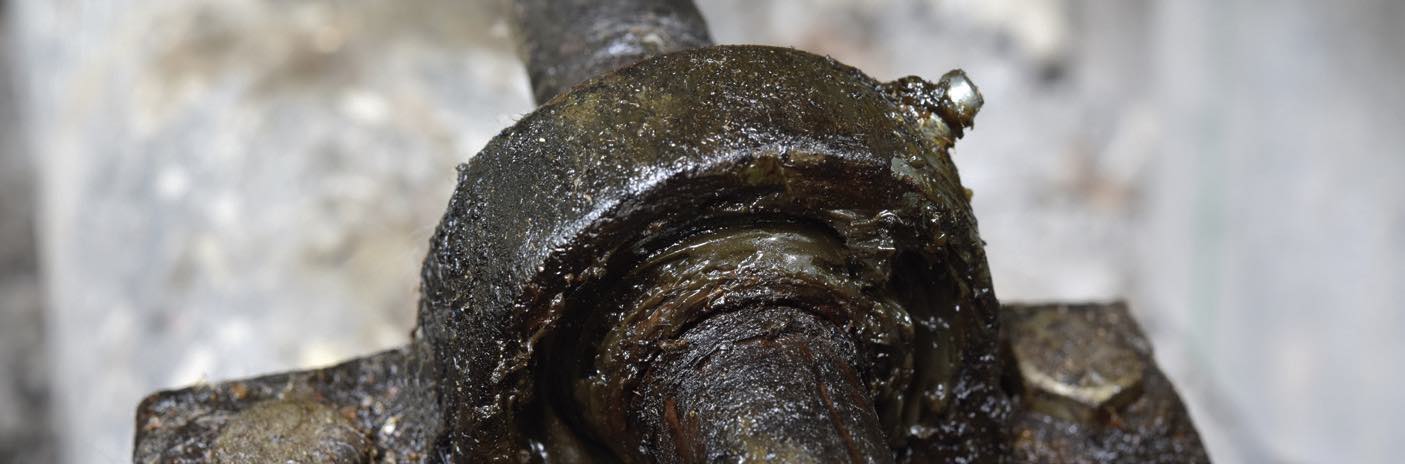
Issues with the term “varnish”
STLE Fellow Dr. John K. Duchowski, CLS, OMA I and II, corporate director R&D filtration, HYDAC FluidCareCenter® GmbH, is not a fan of the term “varnish” because it doesn’t specify the cause. “It is a word which I intensely dislike,” he says. “It is meant to sound technical but is anything but—in many cases it ignores the oil and application type and is ubiquitously applied across the board. There is talk of ‘varnish’ in phosphate ester hydraulic systems, turbine lube oil systems, paper machine oils, etc. So, any (say) soft insoluble material is then called ‘varnish’ without any attention being paid to how it could have formed.”
He observes that when insolubles form, they may at first appear gummy or gelatinous but look like cracked mud when dried. “All of these are then simply lumped together in the same statement, ‘You have varnish in your system,’” he says. “Then the focus oftentimes is on ‘varnish removal’ with not much attention to the root cause. And this, in turn, very often means that once the existing ‘varnish’ is flushed from the system, it is very likely to return after a certain time interval because the root cause has not been addressed.”
Oil analysis for detecting varnish formation STLE member Mary Messuti, president of Eurofins TestOil, observes, “Varnish deposits adhere to metal surfaces in piping, valves, strainers and heat exchangers. They decrease clearance zones, increase friction and lead to higher operating temperatures and ultimately increased wear rates. Oil analysis should be considered a mandatory tool for any system susceptible to varnish. By closely monitoring the contaminants that lead to varnish, reliability engineers can take appropriate corrective action before costly damage and unplanned downtime occur.”
RULER oil analysis can provide early detection of oxidation. According to Mathura, RULER analysis will show that the concentration of phenols will typically deplete more quickly than the amines. “This can provide the analyst with a good overview of the amount of oxidation that has taken place in the lubricant,” she explains. “Unfortunately, other oil analysis tests, such as viscosity and acid number, only show significant changes after the deposits have been formed. At this time, it may be too late to implement technologies to mitigate against the formation of varnish.”
Among the other oil analysis tests Mathura is referring to and the test she finds most useful for evaluation is membrane patch colorimetry (MPC) (ASTM D7843), which provides insight into the approximate amount of insoluble varnish in the system. The results are segmented into three main ranges that identify the severity of the varnish.
“This test is unique in that it allows for the simultaneous detection of insoluble and soluble varnish in an oil sample,” Hobbs notes. “Since a fluid’s likelihood of forming harmful varnish deposits relates to both of these varnish levels, this test is unique in that it allows for the evaluation of an oil’s true varnish potential. Other tests may prove useful for evaluating insoluble levels (particle count, etc.) or soluble breakdown levels (acid number, FTIR oxidation, etc.), but these largely fail to capture the overall varnish picture for most oil samples. MPC allows end-users to do just that.”
STLE Fellow Dr. John K. Duchowski, CLS, OMA I and II, corporate director R&D filtration, HYDAC FluidCareCenter® GmbH, observes that there are several notable drawbacks of MPC, including preparation as well as the very narrow field of sample interrogation with a hand-held pen-like reflectance UV- vis spectrophotometer. “The material deposited on the membrane has to be really homogeneously deposited to reduce or eliminate variation in patch luminosity (lightness or darkness) in order to obtain a representative result,” he cautions. “I would prefer to see a method where the sample preparation plays a minimal role or no role at all and the entire UV-vis wavelength range (350 nm-750 nm) is scanned.”
While MPC may be the most common method for detecting varnish, other tests may include automatic particle count (APC)
2 at room and elevated temperatures (80 C) to allow the organic insolubles to redissolve in the warmer oil.
Duchowski says, “In some cases, an ultracentrifuge also may be employed. The use of a centrifuge may be misleading because it will knock out both organic and inorganic particulate as well as water. Arguably, you also can use infrared spectroscopy (IR) and look for the presence of a carbonyl group with a very sharp, well-defined band at ca. 1,725 cm
—1, but that too can be misleading if a viscosity index improver, such as polymethyl methacrylate (PMMA), has been blended into the oil. Moreover, it’s debatable if IR spectroscopy can be used in a truly quantitative manner because the intrinsic band intensities vary widely depending on the so-called oscillator strength. Without going into too much detail, one only needs to look at the spectrum of acetone where a single –C=O carbonyl group easily ‘outshines’ 6 –C-H
3 in intensity.”
Methods, other than oil analysis, for detecting varnish formation
While oil analysis is by far the most common method for detecting varnish, there are other tests that are best for some applications. An example is vibration analysis and bearings.
“In some cases, when high levels of varnish are present, it may form deposits on bearing surfaces, particularly on journal bearing pads that offer a larger surface area for deposit formation,” Duchowski says. “In severe cases, this can translate into elevated bearing temperatures and vibration. But it is highly advisable not to let things go that far.
“So, consequently, some way of monitoring varnish content on a continuous basis and having the ability to implement appropriate corrective action well in advance of bearing failure would be most highly recommended. Sticking to one method and carrying it out in a consistent manner should nevertheless provide sufficient advanced warning on the rate of varnish build-up. Here, I would most likely vote for the MPC as long as it is carried out in a consistent manner as described in the ASTM procedure.”
Mathura agrees that vibration analysis can be helpful. “There have been instances where shafts in rotating equipment have been moved due to the build-up varnish,” she says. “When vibration analysis is used, it can detect any small changes in the alignment of the shaft in rotating equipment. As varnish continues to build on the inside of the component, vibration analysis can detect if the shaft is misaligned. This may be easy to miss as sometimes the varnish, which has built up, can be wiped away causing the shaft to resume its proper alignment. Thus, analysis technologies should be used in tandem before conclusions are made about the presence of varnish.”
Because there is such a strong link between varnish and temperature— especially since it forms an insulating layer and traps heat—Mathura says that monitoring temperature fluctuations also can be helpful. “Bearings that are experiencing varnish tend to display increases in temperature,” she explains. “Typically, these temperature patterns assume a sawtooth pattern where temperatures rise continuously as the varnish builds up. Then someone wipes away the varnish, and there is a drastic reduction in temperature. This sawtooth pattern of temperature variation is characteristic of varnish formation.”
She adds that, in some cases, the formation of localized deposits on bearing surfaces may cause temperature escalations without a corresponding MPC increase. In this case, the bulk oil may not show any form of degradation, yet temperature excursions may be experienced at the bearing surface.
Varnish removal
Khashayar Hajiahmad, lubrication management specialist, MLA III, MLT II, VPR, VIM certified, EPT Clean Oil business development manager, notes that turbomachinery users are changing from a predictive maintenance strategy, performing oil analysis and changing the oil when needed, toward proactive maintenance, applying filtration technologies to avoid or remove varnish. But there are limits.
“Mechanical filtration, electrostatic or deep filtration methods remove only solids and, thus, need to wait for insoluble varnish to form,” he says. “They do not address the root cause, which is chemistry related. Oxidation byproducts are polar, saturate the lubricant and finally become insoluble. Addressing soluble varnish and removing the molecules not needed in the oil while they form is the right approach for varnish removal.”
Hobbs explains that there are three strategies for mitigating varnish.
1. Solvency enhancing additives. These increase varnish solubility in an oil and can redissolve previously deposited varnish. They do not remove it but suspend it within the oil instead. As varnish continues to accumulate or the solvency enhancers themselves degrade, this can eventually lead to more significant varnish problems. These products tend to defer varnish problems but do not offer a true solution, Hajiahmad says.
2. Conventional filtration. Regardless of the specific filtration technology, this strategy is limited in that it fails to remove soluble varnish and its precursors. Since this varnish is dissolved, it passes right through conventional filters at typical operating temperatures. “These products improve particle count and can even remove insoluble varnish, but they fail to solve varnish problems since they fail to address their root cause: soluble varnish,” Hajiahmad clarifies.
3. Ion-exchange resins. This involves the use of ion-exchange resin-based soluble varnish removal systems. Well-engineered ion-exchange resins can selectively remove soluble varnish and its precursors (acids, oil oxidation products, etc.). Hajiahmad says that removing these contaminants addresses the root cause of varnish problems and allows oil to be maintained in a like-new state.
According to Mathura, the combination of filtration and solubility enhancers can be quite effective. “Solubility enhancers solubilize the varnish back into the oil solution. When these deposits are reintroduced into the oil, they can then be removed using resin-based filtration. With this method, the media is specifically designed to allow for the adsorption and removal of the varnish, which presently exists in the oil.”
Conclusions
Duchowski cautions against spending too much time searching online for solutions to varnish issues. Instead, he recommends books by industry experts and scientific articles (preferably in peer-reviewed journals)— all of this followed by timely action. “Very often, too much online research can result in analysis paralysis,” he says.
Both Duchowski and Mathura conclude that the key to varnish control lies in identifying the root cause mechanism. “Oil health monitoring needs to be a well-rounded program that includes several variables,” Duchowski says. “It is not possible to base everything on particle count or varnish content. Moreover, the variables should not be evaluated in isolation but examined to find commonalities in behaviors and trends. Ultimately, oil condition monitoring belongs in the realm of chemistry and physics and should be examined from that point of view. A more thorough understanding of the underlying processes in terms of the occurring chemical and physical processes will translate into an improved understanding of the root cause and effect relationship. This will improve our capabilities for the implementation of the most suitable remedial action.”
Mathura sums up, “There is no cookie- cutter method to eliminate varnish from a system, since it is a complex deposit. Similar to practices we observe with our bodies in the instances of cholesterol build-up, we can employ methods of dissolving the varnish and removing it while monitoring for possible recurrences in the future.”
REFERENCES
1.
Mathura, S. (2020),
Lubrication Degradation Mechanisms (CRC Press Focus Shortform Book Program), 1st ed., CRC Press.
2.
The automatic particle count (APC) method is the ISO 11500:2008 procedure, “Hydraulic fluid power — Determination of the particulate contamination level of a liquid sample by automatic particle count- ing using the light-extinction principle.”