KEY CONCEPTS
•
Synthetic lubricants are slowly gaining ground over asphaltics and black greases.
•
Automated lubricant application and condition monitoring can increase a gear’s reliability and worker safety.
•
Optimal operation depends on the quality, design and condition of the gear set; lubricants that fit the operating conditions; and regular evaluations and maintenance.
Cement plants, paper mills, mineral ore processing plants and other large industrial operations rely on huge rotary drums to heat, grind or otherwise process raw materials into salable products. The giant-sized gears that turn these drums cannot be housed practically inside a gearbox, so they are often exposed to outdoor temperature extremes or environments that are dirty and dusty. Open gears must stand up under heavy loads and operate round the clock, often over a span of decades. The lubricants that keep them running are formulated to stand up to demanding conditions while meeting economic and regulatory demands, reducing operating costs and keeping downtime and equipment failures to a minimum.
Open gear lubricants are changing because machinery and industries are changing, says Jonathan Venditti, global market manager for the chemical industry at Klüber Lubrication, München, Germany. Many companies want to move away from open gears in favor of direct-drive and gearless drive systems when they install new machinery because of their lower maintenance costs and increased reliability. However, this is a long-term change with a long lead time, he adds.
Change has been slow in the open gear field, but it is happening, says STLE member Larry Ludwig, chief chemist and technical director at Schaeffer Manufacturing, St. Louis. The biggest changes have been in lubricant formulations, including transparent fluid lubricants and polymer additives that increase the viscosity of oil-based lubricants. Health and safety concerns regarding possible carcinogens and solvent fumes are driving a shift away from asphaltic formulations, he adds.
On the hardware side, automatic spray or immersion systems have largely replaced manual lubricant application
(see Figure 1). Manual application was messy, irregular and hazardous for the workers, Ludwig says. Some applications like mining shovels, kilns and sugar mills now use direct-drive electric motors (powered from the electrical grid or by an onsite generator) for some components. However, he says, running large open gears with electric motors isn’t efficient because of the size of the motor required, and the gears still require lubrication.
Figure 1. Manual application of lubricant to the teeth of an open gear. Figure courtesy of Klüber Lubrication.
The demand for open gear lubricants for specific applications depends largely on the demand for certain end products, which, in turn, is affected by constraints (e.g., raw material supplies and regulatory requirements) and initiatives (e.g., government-funded efforts and corporate strategies), says STLE member Darren Lesinski, technical director of marketing services for TotalEnergies Marketing USA, Inc., Linden, N.J. In the U.S., paper and cement making applications are going strong, he says. Government-funded infrastructure and power station initiatives are helping to drive cement making. Aluminum and iron production are ramping up in the U.S. and China. In Europe, some countries are returning to coal mining to make up for recent disruptions in petroleum and natural gas supplies.
Open gear lubricants have been affected “across the board” over the past few years, says Lesinski. “Not just from an application standpoint but the environmental concerns of certain chemistries that are utilized in open gears, and the logistics issues that we are experiencing post-COVID-19.” He cites examples of issues such as those posed by the war in Ukraine and disruptions in mining industry production, aluminum and steel processing industries and power generation. “So it’s evolving. It’s pivoting in a different direction as far as what’s available now, as far as chemistries.”
Selecting a lubricant
Open gear lubricant manufacturing is a medium to small industry sector compared to that for other lubricants, says STLE member Anoop Kumar, senior staff scientist, Chevron Products Co., San Ramon, Calif., and president of NLGI. As with any other type of gear system, selecting an open gear lubricant depends on gear size and design, operating load and temperature range and method of lubricant application.
1 Open gears come in many sizes, up to several meters in diameter, and they often rotate at slow speeds (e.g., about 10 rpms), so they require viscous lubricants, Kumar explains.
The old way of lubricating open gears, Kumar says, was to fill a sump with a semifluid lubricant. The girth gear—the large gear encircling a rotating drum, driven by one or more pinion gears
(see Figure 2)—would pick up the lubricant as it rotated and carry it up and around. This method was messy and wasteful, he says. The asphaltic lubricants commonly in use were viscous and drippy, and they attracted dust and dirt. The sump method eventually gave way to manual brush application of heated asphaltic lubricants. However, this was not only messy but also hazardous for the workers applying the lubricants to the moving gears. Today’s lubricant systems are automated, usually intermittent spray applications using a timer. In some cases, older systems can be retrofitted with automated sprayers, which enable operators to adjust the amount of lubricant, using only the amount needed for effectiveness.
Figure 2. Two pinion gears drive the girth gear on this double-drive cement ball mill. Figure courtesy of Lubrilog.
For vertically moving gears, the spray nozzles can be contained in a covered box that delivers an atomized, directed spray to the surface of the girth gear as it passes through the box, Kumar says. This type of gear assembly requires fluid lubricants. Although it’s more difficult to design similar enclosures for horizontal gears like those used in shovels, it is possible. In these applications, greases with a harder consistency (NLGI 1 and 2) have generally been found to be more suitable, he explains.
Type 1 gears require grease lubricants, says Ludwig. These bidirectional gears, used for mining shovels, excavators and drag lines, need constant replenishment and a lubricant that adheres well to the surface of the gear. Type 2 gears require liquid or semiliquid lubricants, applied using an intermittent spray or immersion system. These gears, which move slowly in only one direction, are used for mills, cement kilns and other processing equipment.
2
Most gear manufacturers work with lubricant manufacturers to ensure that lubricant formulations meet the manufacturer’s specifications for a given gear design, says Jean-Philippe Merlo, technical manager at Lubrilog SAS (a division of TotalEnergies), Romans-sur-Isère, France. The main lubricant requirements are high viscosity (which depends on operating temperatures and the method of lubrication), the proper types and amounts of extreme pressure (EP) additives and solid lubricants (depending on the type of lubricant, operating speeds and temperatures and defects on active gear flanks) and specified ranges for test results. Standard tests include FZG tests (a measure of an oil’s ability to provide resistance to scuffing and wear), four-ball weld tests, four-ball wear tests and Timken OK load rating (which measures how well EP additives are performing).
In addition, lubricant formulations for routine operations must be free of abrasive components. The choice of a lubricant formulation depends on the operating conditions of the rotary drum but also on a customer’s habits, Merlo says. “For good advice, you have to know the gear set and, above all, do not make the choice by comparing technical data sheets alone. A technical approach is imperative,” he explains.
Once the OEM has set their specifications, additional factors influence the choice of a lubricant type. In many countries, including those in the European Union, lubricants containing bitumen are banned. Oils, compounds and greases are available for spray, bath and circulation lubrication systems, Merlo says
(see Figure 3), and any of these lubricants can be used as long as they have the needed oil viscosity or NLGI grease consistency. The main factors influencing the choice of lubricant include the type of machine (slow-rotating like a cement kiln or fast-rotating like a mill, for example), the operating temperatures, the method of application and the maintenance protocol.
Figure 3. Oil lubricants can be applied using bath (splashing), circulation or spray systems. Figure courtesy of Lubrilog.
The condition of the gear also is a consideration when selecting a lubricant. Gears can continue to operate even if they have some amount of scuffing, pitting or other damage, Ludwig says. Temporarily using a lubricant with a higher viscosity, switching from oil to grease or increasing the amount of lubricant can allow a damaged gear to remain in operation until it can be repaired. Switching from oil to grease is a stopgap measure, he notes, and the gear must be cleaned before switching back to oil. These stopgap measures, however, require a great deal of caution, because using the wrong type of lubricant or keeping a badly damaged gear in operation can actually hasten equipment failure. Keeping open gear-driven equipment in operation is a high priority, he says. Facility managers might be tempted to keep things running regardless, but pushing a gear to the point of failure can be very expensive. An hour of downtime can cost as much as $175,000 in lost production, Ludwig says, and stopping operations, performing repairs and bringing the equipment back online can take on the order of 100 to 150 hours.
Asphaltic lubricants
Open gear lubricants fall into three major categories: asphaltics, greases and oils
(see Figure 4).
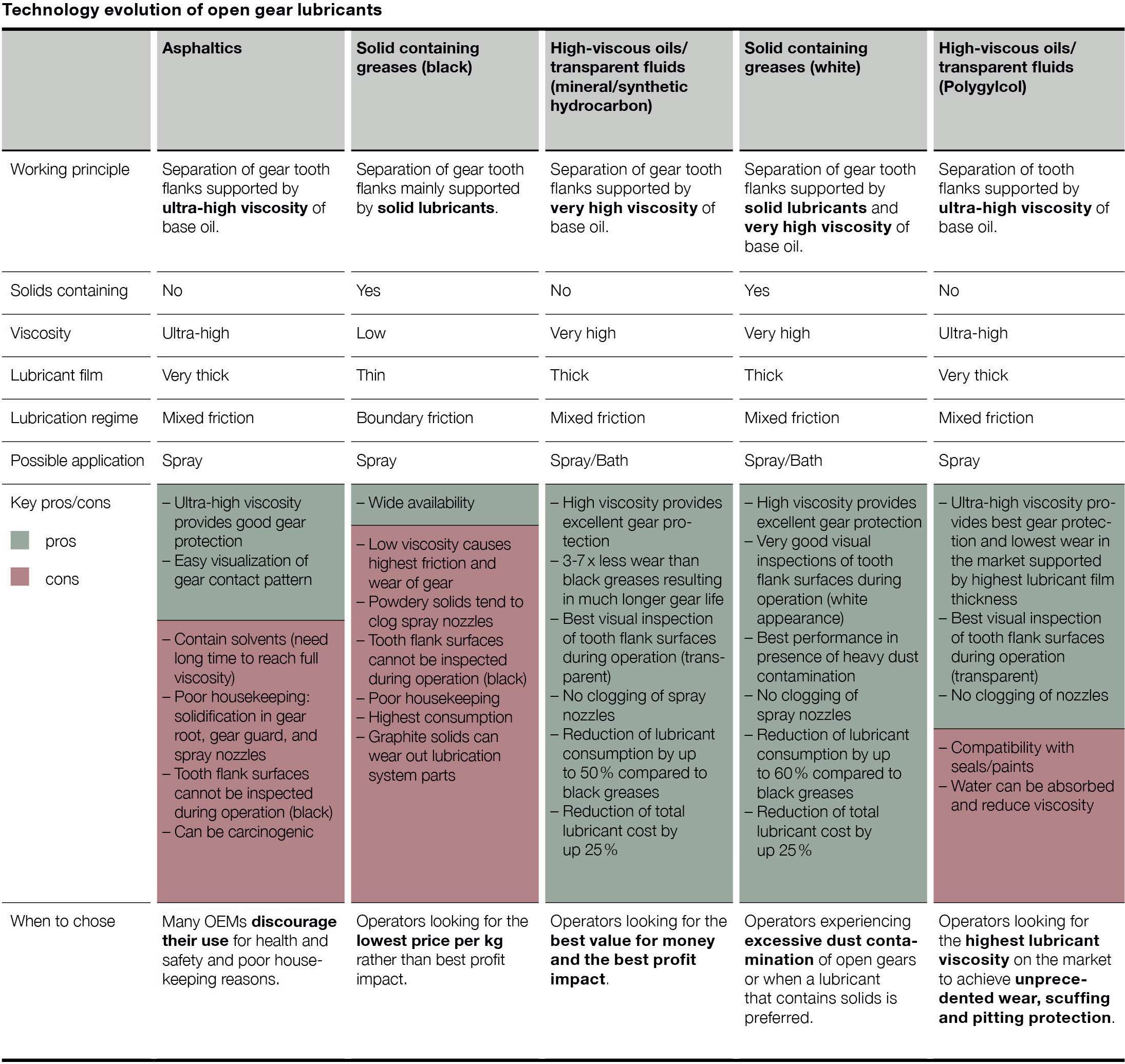
Figure 4. Comparison of various types of open gear lubricants. Figure courtesy of Klüber Lubrication.
Asphaltic lubricants are thick and adhesive. They provide good protection, but in a dusty environment like a cement plant, they also attract dust and other contaminants that can scuff gear surfaces or clog spray nozzles. Asphaltic lubricants contain bitumen, a dense, viscous hydrocarbon product that comes from crude oil refining residues. Originally, using bitumen in lubricants was a good way for oil refineries to monetize this residue, Venditti says, but issues associated with asphaltic lubricants can add to operating expenses for lubricant customers. For example, he says, used asphaltic lubricants are classified as hazardous waste,3 which adds to the expense and complication of disposal.
For outdoor open gear operations in cold climates (e.g., mining or cement making), lubricant pumpability and adhesion are major concerns. At low temperatures, asphaltic lubricants can flake off of the gear, especially if they have lost some of their base oil, says Kumar. Older asphaltic lubricant formulations rely on large amounts of volatile solvents to keep them from becoming too viscous in cold weather and to keep the lubricant liquid as it is being applied to the gear. However, some solvents pose flammability concerns, he adds.
Some solvents also pose concerns for worker safety. Before regulations and company health and safety rules came into play, manufacturers of asphaltic lubricants used chlorinated solvents and other volatile organic materials. “You would just approach the barrel and your nose would become itchy. Your contact lenses would feel like they were melting in your eyes,” Venditti says. Now, the solvents are safer, he adds, but a mechanic working near a gear on a hot day might notice an odor like diesel fuel or paint thinner.
Diluents have largely replaced solvents in newer asphaltic formulations; the diluent content can be about 10%-30%. Diluents take much longer to evaporate, often 12 to 24 hours, compared with about 15 minutes for solvents. Wear protection levels may be reduced while the diluent is evaporating, so the lubricant is sprayed onto the girth gear, which has more surface area and rotates more slowly than the pinion gear. This gives the diluent time to evaporate before it comes into the contact zone with the pinion gear. Because diluents never completely evaporate, Venditti says, they lower the viscosity of the lubricant, so these lubricants never reach the theoretical maximum viscosity of the pure asphaltic material. One drawback to applying the lubricant this way is that the lubricant is only in contact with the pinion gear for a small part of the rotation cycle. Most of the time, the lubricant is exposed to the dusty air inside the plant as it completes the rotation cycle on the surface of the girth gear. Fresh lubricant must be sprayed onto the girth gear often enough to avoid dry spots in the contact zone and to wash out any contaminants that might accumulate.
Another way of keeping asphaltic lubricants flowing in cold weather is to use a heating blanket and heat tracing cables (for temperature control) from the lubricant drum to the injection or spray point. Semisynthetic lubricants are more fluid than asphaltics, and they might not require the use of a heating blanket, Venditti says, which reduces energy costs.
Asphaltic lubricants are still used in some countries because of their low initial cost, Ludwig says. However, the European Green Deal
4 currently being implemented could place restrictions on asphaltic lubricants and the solvents they contain for health, safety or environmental reasons. In the U.S., he adds, restrictions on asphaltics pertain mostly to marine applications, including onshore cranes in ports and cranes and winches aboard ships. Open gear lubricants also are sometimes used as wire rope dressings, where the lubricant is in direct contact with the water, which makes it even more important to ensure that these lubricants are environmentally benign.
Venditti cautions that many of his company’s customers are very conservative, and they continue to rely on the supposedly greater protection provided by “the black stuff ” (i.e., asphaltic lubricants). However, he cites his company’s research and development efforts, including test rig data, which demonstrate that biodegradable oils like esters and plant-based lubricants provide a very good coefficient of friction, high adhesiveness to the gear and a high degree of protection.
Grease lubricants
One way to achieve wear protection without the problems presented by asphaltics is to use semifluid grease lubricants.
5 The grease thickener keeps the lubricant on the gear, which eliminates the need for tackifying additives. Even better, the grease does not have to have an extremely high viscosity, so the base oils can come from mineral, synthetic or semisynthetic sources. Solid additives used in greases form a barrier between the pinion and the girth gear, offering more complete protection in the contact area. All of these factors help to reduce the cost of buying and using grease lubricants, Venditti says.
Most open gear greases are NLGI grades 0 or 00, says Kumar. Grease lubricants for open gears mostly use aluminum complex thickeners because these are best for sprayable greases. However, other thickeners, including lithium soaps, clay or polymers, also are used. Polymer additives increase adhesiveness, and high-viscosity (3,000-40,000 centistokes) bright stock oils provide the needed lubricity.
Grease lubricants are especially useful in applications that require solid EP and antiwear additives. However, these additives are one reason that grease lubricants are less biodegradable than oils, says Ludwig. Reducing the amount of solid additive in a grease formulation is one way of making a more biodegradable product, but sufficient additives must be used to maintain the desired performance.
Unlike oil lubricants, which are often transparent, open gear greases tend to be opaque and black because graphite and molybdenum disulfide are the most commonly used solid EP additives
(see Figure 5). These EP additives also protect against wear under severely heavy shock loads. Some customers prefer black greases, Kumar says, because the color indicates the presence of solid lubricants. Because opaque greases prevent direct observation of the gear surface during operation, he says, it is important to perform routine condition monitoring of the wear pattern on the gears.
Figure 5. Many open gear customers rely on black greases, which contain molybdenum disulfide or graphite EP additives. Figure courtesy of Klüber Lubrication.
Black greases are less common than they once were, says Merlo. Fewer open gear lubricants contain bitumen, and the use of black aluminum complex greases containing graphite also is declining, as more and more operations shift toward white greases.
Grease lubricants form a tacky protective film on gear teeth, which helps to reduce accumulations of dust on the gear, and they don’t clog spray nozzles as badly as asphaltics do. However, greases can be hard to pump, especially in cold weather. Their main advantages are homogeneity, even distribution of the solid additives and good protection. Greases also stay on the gear surfaces longer than oil lubricants, which not only reduces the volume of lubricant that needs to be applied but also reduces the amount of used product that needs to be recovered for disposal. In the event of a failure of the lubricant application system, greases can allow a gear to run for a longer time without incurring damage.
Grease lubricants also are relatively inexpensive for a mineral-based product, Venditti says. Greases with aluminum complex soap thickeners and other similar thickeners also offer superior resistance to water washout and improved protection against corrosion, he adds.
Oil lubricants
Oil-type open gear lubricants are increasing in viscosity, Merlo says, because of the high loads typical of today’s open gear operations. These high-viscosity oil lubricants, many of which contain synthetic base oils and additives, are a good alternative to asphaltics or greases, but they must be suited to the demands of gears that are not enclosed in a gearbox.
5 The industrial applications that use open gears can have enclosed gearboxes between the pinion and the electric motor that drives the pinion, says Venditti. These gears can be lubricated continuously because the lubricant is contained within the gearbox. In contrast, girth gear lubricants are replenished by spraying the gears intermittently. Lubricant tackiness and high viscosity are essential to keeping the lubricant on the gear and avoiding dry spots. He explains that even though the pressure at any given point of an open gear is no greater than the pressure on gears in a closed gearbox, the same lubricant cannot be used for open and closed gears because of the differences between continuous and intermittent lubricant application.
Transparent synthetic oil lubricants are gaining popularity because they allow operators to observe the gear surfaces while the gears are in operation to ensure that the lubricant is distributed completely and evenly
(see Figure 6).3 In addition, they provide better performance than most of the greases traditionally used, Merlo says. Advantages of transparent lubricants over asphaltics include better characteristics for the same viscosity (and availability in a wide range of viscosities), no need to use solvents, less accumulation of contaminant particles near the root of the gear tooth and ease of application and cleaning. Transparent lubricants also have a viscosity index advantage—they maintain their characteristics over a wider temperature range than asphaltics. In addition, they present less risk to machine operators and to the environment.
Figure 6. Transparent lubricants enable automated or manual condition monitoring while the gear is in operation. Figure courtesy of Klüber Lubrication.
Using a transparent lubricant allows operators (or video cameras) to monitor spray patterns while the gear is in operation. Because a gear may be rotating at about 10 meters per second, some monitoring systems use a strobe light to illuminate the contact area
(see Figure 7). This produces a slow-motion effect that makes the evolution of the spray pattern easier to see, says Ludwig.
Figure 7. (Left) Stroboscopic monitoring of the lubricant spray pattern while the gear is in operation. (Right) Stroboscopic image of a pinion gear. Figure courtesy of Lubrilog.
Transparent lubricants also make it possible to use continuous or intermittent video monitoring to watch for problems like pitting, scuffing or polishing in the early stages, Venditti says. An operator or service representative can perform a visual inspection through an access door if unusual vibrations signal a potential problem. Inspecting a gear during operation not only provides information about the source of the problem, but it also eliminates the need to stop the equipment to perform the inspection, which reduces downtime.
Heavy oils can be used to lubricate medium to large girth gear drives. The viscosity for typical open gear semisynthetic lubricants runs between 4,000 to 8,000 centistokes, says Venditti. These lubricants can save energy by operating without the use of heating blankets at temperatures as low as -5 C (23 F), much lower than for asphaltics or greases.
Although oil lubricants aren’t as adhesive as asphaltics, they don’t require solvents or diluents, so they can be applied more frequently. Because high-viscosity oils, which are most likely semisynthetic formulations, don’t use diluents, they can be sprayed directly onto the pinion, where they are most effective. You can spray fresh lubricant onto the pinion gear every three minutes, says Venditti, “so you use less lubricant and more often, and then you get closer to the lubrication regime of an enclosed gearbox.”
More frequent lubricant spraying onto the pinion gear is an advantage, but it’s also a requirement, Venditti says. The girth gear generally lasts about 20-30 years, while the pinion gear generally lasts no longer than about five to eight years (you can extend this using hardened materials like carbides, he says). The pinion gear spins faster and operates at a higher temperature than the girth gear, which helps with cold-weather lubrication, but it also shortens the gear’s lifetime, he says, because friction resulting from insufficient lubrication can lead to overheating.
Venditti cites a field test in an ore processing facility in which a specialty open gear lubricant reduced the temperature of a pinion gear by 30 C (86 F) compared with an asphaltic lubricant. He notes that it was difficult to document any energy savings during this test because the customer kept the power level constant and increased the amount of production. However, the lubricant was successful in addressing the customer’s main priorities: reducing the operating temperature and reducing micropitting wear at the pitch line of the gears.
Polymer additives help a synthetic lubricant provide a hydrodynamic film without the use of asphaltics, and synthetic lubricants have less tendency than asphaltics to build up in a gear, Ludwig says. Synthetic lubricants have good pumpability at low ambient temperatures without the need for solvents, and they hold up well at the high temperatures typical of mills and cement kilns. Synthetic esters have less tendency to oxidize at higher temperatures than do heavy vegetable oils, and they also are more pumpable at low temperatures than vegetable oils.
Performance additives tend to last longer in synthetic lubricants, and they can provide a lower coefficient of traction, which results in less energy required to rotate the gear, Ludwig says. Using synthetic lubricants doesn’t eliminate the need to periodically clean the gears, but cleaning is much easier for these formulations than for asphaltics or greases, an advantage that is not lost on the workers assigned to this unpleasant task.
3
Venditti notes that different base oils are being investigated for open gear applications—including water-based lubricants, polyethylene glycol, polyalkaline glycols (PAGs) and esters. These lubricants act as coolants, reducing friction by enhancing the coefficient of friction, which helps to reduce the operating temperature of the mechanical components. Semisynthetic waste products are not considered hazardous, so you can recycle them (and sometimes get paid for it), he says.
The disadvantage to using gear oils rather than semisolid open gear greases is the limitations to their viscosity and their tendency to leak, Kumar says. However, thickeners and viscosity modifiers help with this. The decision to use oil or grease lubricants depends on the application and performance required, he adds.
1
Environment and regulations
“Everybody’s talking about environment, social and corporate governance factors (ESG) and lowering carbon,” Kumar says, which is leading many industry sectors to consider more environmentally sustainable feedstocks, processes and products. However, he says, conventional products may have the advantage in performance and price, which requires industries in general to evaluate their priorities when deciding how to balance these factors. Also, there’s not a clear-cut path for disposing of gear greases, Kumar says, adding that disposal depends mostly on local regulations, and greases are complicated to recycle.
A drive toward greater sustainability and less polluting practices, driven by company initiatives and government mandates, is behind some of the current changes in machinery and lubrication. Because most equipment that uses open gears is located outdoors, spray lubrication “goes everywhere,” including into the surrounding environment, says Venditti
(see Figure 8). To make sure that this practice does not run afoul of anti-pollution initiatives, researchers are actively looking into biodegradable lubricants, based on plant materials. One challenge is that oils derived from plant matter tend to have low viscosity, but some companies, including Venditti’s, are developing products that overcome this challenge.
Figure 8. Biodegradable lubricants lessen the harmful effects of spray lubricants on the surrounding environment. Figure courtesy of Klüber Lubrication.
Research efforts on plant-based polymers and biodegradable formulas, including synthetic ester compounds, are particularly interesting to operations like marine applications that have a high potential environmental impact, but mining operations are moving in this direction as well. OEMs also are starting to look at biodegradable lubricants when they set their specifications, Ludwig says. Spills involving biodegradable lubricants must still be reported to the relevant government agency, but because they are considered less persistent in the environment and they are easier to clean up, fines may be lower than for other types of lubricant, or the fines may be waived entirely. That’s one reason that biodegradables, which are initially more expensive, may save money in the long term, while offering the same performance as other lubricants, he says.
Some specialized areas require formulations that meet strict health, safety and environmental regulations. For example, open gear mills for food products—sugar processors, for example—drive a demand for more sophisticated lubricants to meet H1 regulations and other regulatory requirements.6 Marine and freshwater applications, including canal locks and hydropower plants, require open gear lubricants that will not pollute the surrounding water.
Open gear lubricants are moving away from asphaltics and chlorinated solvents; “asphaltics are high maintenance,” Lesinski says. Depending on the application, he adds, customers can choose to use grease and synthetic lubricant technologies such as products containing perfluoropolyether (PFPE) and polytetrafluoroethylene (PTFE). These products are environmentally cleaner than asphaltics, and they provide a better return on investment and total cost of operation, he says.
Maintenance and repair
Large open gears mounted on industrial machines like grinding mills, kilns and debarking drums (which remove the bark from logs) have a service life that can span up to 40 years. However, it is not uncommon for poor maintenance practices or contamination to reduce open gear service life to as little as eight years, Venditti says. Thus, new project installations and replacement of damaged gears ensure a continuing demand for purchase and installation of new open gears.
OEMs are developing their metallurgy to produce more robust gears that require less frequent cleaning and repair than older gears. Nevertheless, because of the long lifetimes of open gear equipment, lubricant manufacturers must provide a range of legacy products to cover a broad range of OEM requirements for lubricants, cleaners and solvents. “Most of our portfolio hits most applications, but sometimes an OEM will require tweaks to a formulation,” Lesinski says.
Periodic maintenance of lubricant application systems ensures that they function properly, which reduces downtime. Some operations monitor vibrations and temperatures to catch problems in the early stages, but regular gear inspections are still necessary. Regular visits during normal operations from a lubricant supplier’s representative provide opportunities to prevent problems before they occur by identifying lubricant system deficiencies and optimizing lubricant application.
OEMs generally provide recommendations on maintenance procedures and scheduling as a condition of their warranties, but operations managers usually keep up with routine maintenance as a matter of course. “It’s part of the culture to keep the equipment running,” Ludwig says. During maintenance, a representative from the lubricant supplier is typically on site to make sure the lubricant is being applied properly, he adds. The supplier’s representative can help with troubleshooting problems and offer guidance on lubricant application and the direction and timing of the spray, and they can help track down the root cause of an equipment failure.
The direction the industry is going in is a cradle-to-grave approach, Lesinski says, going beyond just selling chemistries or lubricants to the customer. Lubricant manufacturers support customers by being present at the customer’s facility for change-outs and repairs.
Routine maintenance depends on the country in which the operation is located, Merlo says. Different regions take different approaches to maintenance. However, customers who regularly schedule plant visits from a lubricant supplier’s technical representative find valuable information in the technical reports they receive after these visits. During a site visit, the technical representative observes the quality of the lubrication and the condition of the open gear set. Merlo says that technical reports often contain information on the plant conditions that the technical representative encounters during a site visit, along with a comparison with conditions observed during previous visits. The reports also advise actions to be taken to ensure the best and safest use of the gear set. These specialist reports supplement the site visits from a plant’s technical department, and they assist the maintenance manager in making decisions.
Every phase of open gear operations requires a different type of lubricant, says Venditti. When a new gear is put into operation (or during an emergency situation requiring diagnosis of a problem), a colored priming lubricant reveals the contact pattern between the pinion and the girth gear.
Some OEMs and service companies use a running-in fluid, which contains a chemical etching compound, during the first week to month of operations to remove asperities and metalworking marks on the gears and match the pinion to the girth gear, Venditti says. Then, they switch to another type of lubricant for use during normal operations.
Other types of lubricant use abrasives or etching compounds to repair scuffed areas after mishaps like a mechanic dropping a screwdriver or bolt into the contact area or an undetected interruption in the lubricant application that causes the gears to run dry for a day
(see Figure 9). “You need to know what you’re doing with this; otherwise, you can cause even more damage to the gear,” Venditti says.
Figure 9. Scuff marks on the surface of a gear tooth. Figure courtesy of Schaeffer Manufacturing.
Merlo and Lesinki agree—lubricants used for normal operations should never contain abrasives. Special lubricants containing abrasives can be used for making repairs, “but never by the customer, always by a technician with special training and always after performing a damage analysis,” Merlo says
(see Figure 10).
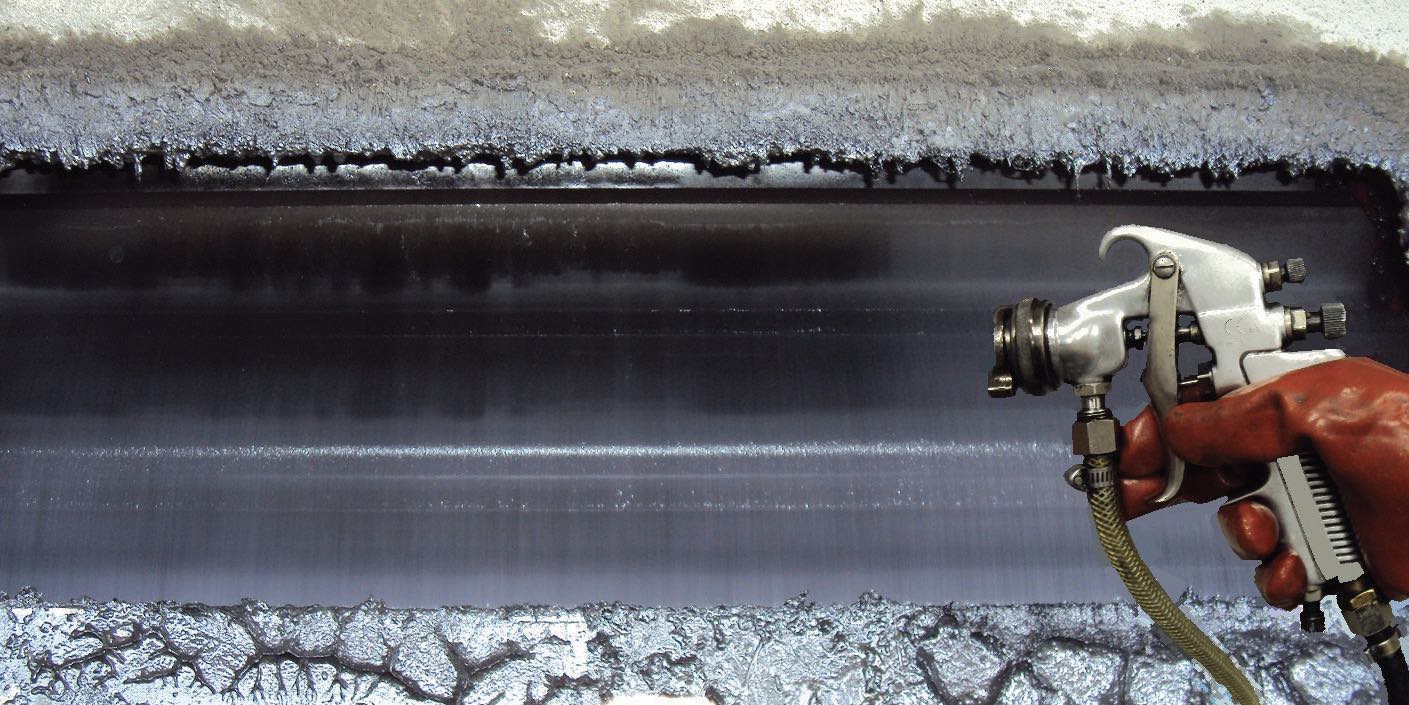
Figure 10. Special repair lapping lubricants, which contain abrasive components, must be applied by qualified technicians.
Figure courtesy of Lubrilog.
Still other formulations are required for operations in remote locations, Venditti says. These operations sometimes keep an extra gear in storage as a backup, because waiting for a replacement gear to be shipped to the site would cause an unacceptable amount of downtime. The spare gear is often stored outside, so it requires a protective coating containing anticorrosion agents to keep it in good condition, ready for the day when it is put into use.
Insurance companies require open gear equipment to be cleaned and inspected every year or two, Venditti says, and specialized gear cleaning formulations help with this task. Cleanup can require as many as five mechanics working for several days using dry ice and copious amounts of solvent to clean the lubricant and contaminants off the gears. “It’s really painful and disgusting for the team,” he says, but he adds that other cleaners on the market can reduce the time and effort significantly.
Lesinski notes that environmentally friendly volatile organic compound (VOC)-free cleaning solvents are available for routine maintenance. When used properly, environmentally friendly solvents are low impact with respect to skin contact and inhalation. “Asphaltics take a lot of solvent to clean,” he says. The move away from asphaltic lubricants and toward VOC-free solvents and cleaning solutions reduces the amounts used, which not only is better for the environment, but it saves money as well.
Several publications from the American Gear Manufacturers Association (AGMA) offer guidelines on industrial gear operation and maintenance. For example, AGMA 919 covers the basics of condition monitoring and diagnostics for gear units and open gears. ANSI/AGMA 9005-F167 offers general guidelines for lubricating enclosed and open industrial gears, including baseline engineering specifications for the type and amount of lubricant used, based on pitch line velocity, the diameter and face width of the gear, its metallurgy, rotation speed and mode of lubricant application (e.g., brush or spray).
Long-term benefits for long-term operations
Effective lubrication and maintenance might not provide direct energy savings in the short term, Merlo says, but it offers other cost-saving benefits. Because a significant amount of energy is required to manufacture girth and pinion gears, keeping them in service longer offers indirect energy savings. Operations also can reduce equipment failures and downtime by extending the life of the gear set. Reducing friction reduces the amount of energy needed to turn the gears, and it reduces heat production and prevents defect formation that can accelerate wear. Some customers find that they can use less lubricant by using spray applications, he adds, but the main saving comes from keeping the gear set in service longer. For an open gear on a rotary drum, he says, the fundamental points are the quality and design of the gear set, sufficient lubrication and regular technical follow-ups.
What’s more, operations that work with a good service company find it easier to maintain open gear equipment, Venditti says. “Open gears are still on the market,” he adds. “They will not disappear tomorrow.”
REFERENCES
1.
McCoy, B. (2019), “Choosing the right open gear lubricant,” TLT,
75 (11), pp. 22-23. Available
here.
2.
Ludwig, L. G. (July 2006), “Practical lubrication of open gearing,”
Machinery Lubrication. Available
here.
3.
Sander, J. (2018), “Benefits of using the right open gear lubricant,”
CBM Connect. Available
here.
4.
European Commission, “A European Green Deal: Striving to be the first climate-neutral continent.” Available
here.
5.
Shell Lubricants, “The asphaltic alternatives.” Available
here.
6.
McGuire, N. (2019), “Incidental contact lubricants for the food industry,” TLT,
75 (12), pp. 18-24. Available
here.
7.
Industrial gear lubrication, ANSI/AGMA 9005-F16 (Reaffirmed October 2021). Available
here.
Nancy McGuire is a freelance writer based in Albuquerque, N.M. You can contact her at nmcguire@wordchemist.com.