The Lubrizol Corp.
How Choosing Energy Efficient Hydraulic Fluids Can Lower Total Cost of Ownership
By By Blayne McKenzie, Technology Development Manager, Industrial Products, The Lubrizol Corporation | TLT CMF Plus November 2022
By lowering operating temperatures and increasing energy efficiency, hydraulic fluids with performance polymers can extend oil-drain intervals and reduce maintenance costs.
As hydraulic hardware evolves to match increased demands in both mobile and stationary applications, a new generation of hydraulic fluids can enable more strenuous operating conditions by unlocking greater system efficiency and at the same time reducing fluid operating temperatures.
Multigrade hydraulic fluids, containing performance polymers, can reliably operate in a wider range of conditions than their monograde counterparts. Using a nonconventional structural design, certain performance polymers can now deliver enhanced hydraulic fluid performance through their influence on characteristics such as shear stability, viscoelasticity and fluid traction. Use of these polymers can ultimately drive improvements in hydraulic efficiency while reducing overall system temperatures.
In this article, we will be discussing the importance of selecting energy-efficient and cooler-running performance polymers when formulating multigrade hydraulic fluids, with an eye toward lowering the total cost of ownership (TCO) over the life of the machinery.
The Changing Infrastructure of Hydraulic Equipment
Mobile and stationary hydraulic systems have undergone revolutionary changes over the past decade as the emphasis has shifted to getting higher efficiency and lower costs. As a result, game-changing technological evolutions are happening every day, and modern machinery components have been affected by these changes.
One component of the hydraulic infrastructure that has seen dramatic changes in response to the technological changes: hydraulic fluids. As machine designs have changed, the operating conditions for these fluids have become even more difficult. Increased temperatures, combined with lower fluid volumes, mean the fluids must perform under conditions unlike any seen in previous machinery evolutions.
Traditional hydraulic fluids may not be up to the task. In fact, using older technology may increase costly downtime and shorten the life span of the equipment. That doesn’t have to be the future, however. New chemistries and performance polymers enable the latest hydraulic fluids to lower the total cost of ownership of today’s hydraulic equipment. All it takes is an understanding of what’s available and how it can affect the equipment’s overall performance.
Smaller, Lighter Machines Require New Chemistries
There are two major factors that influence hydraulic machinery original equipment manufacturers (OEMs) as they bring new equipment to market: cost control and higher efficiency. Combined, those two factors put additional stress on hydraulic fluids to perform under harsher conditions.
Smaller, lighter hydraulic machines have been designed to reduce the cost of materials required to manufacture them and they can frequently do the equivalent work of bigger, heavier equipment. In such instances, the machines are fundamentally more efficient and use less fuel over their lifetime.
One way these machines have been made smaller and lighter is by reducing the size of the hydraulic fluid sump. Though this practice does make the machine weigh less because traditional sumps are large and heavy, it also means less hydraulic fluid can be put in the machine at any one time. The lower the fluid levels, the more severe the operating environment, and fluids may become hotter more quickly. Smaller sump sizes prevent fluids from cooling sufficiently between duty cycles, so the fluid remains hotter over an extended period when compared to previous machines.
The additional heat can break down the hydraulic fluid, which can affect the durability of internal components and lower a machine’s functionality. The fluids can lose viscosity as they heat up, and protective layers get thinner and thinner. Additionally, long-term heat can oxidize fluids more quickly. The protection thicker films provide is compromised and can shorten the life span of the machine components, leading to costly downtime and repairs.
Modern hydraulic fluids are designed to reduce the heat that prematurely ages equipment. By lowering the amount of heat produced in a hydraulic sump, owners and operators of modern hydraulic equipment will spend less on maintenance, and equipment will need to be replaced less often. Now that there is an understanding of why modern hydraulic equipment needs new technology in its fluids, it’s important to discuss how additional performance polymers can help.
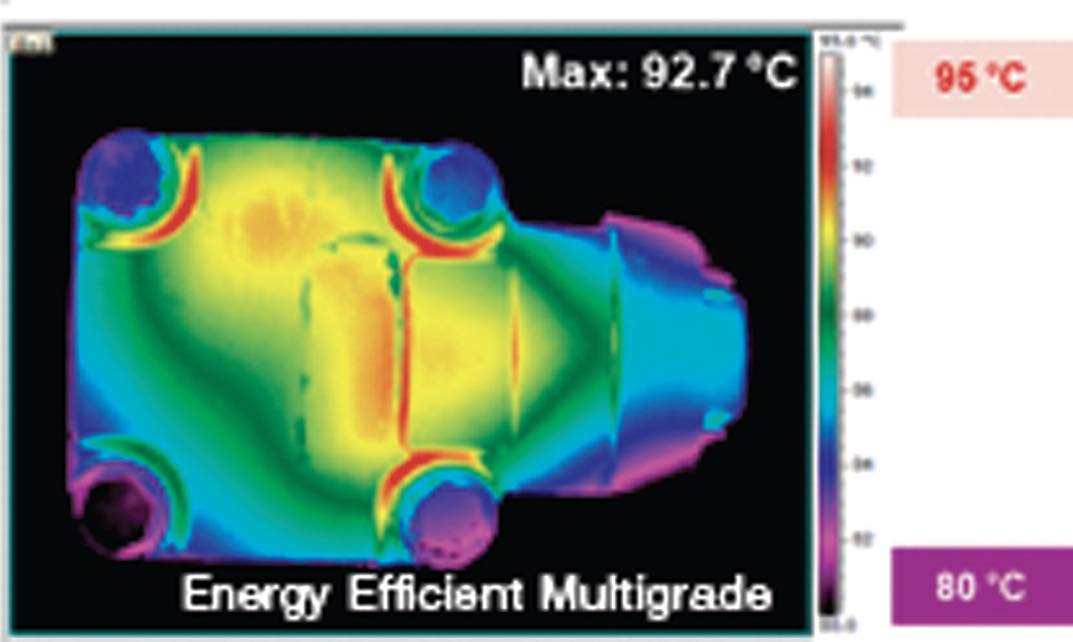
Operating temperature of a 20VQ pump after ~20 minutes.
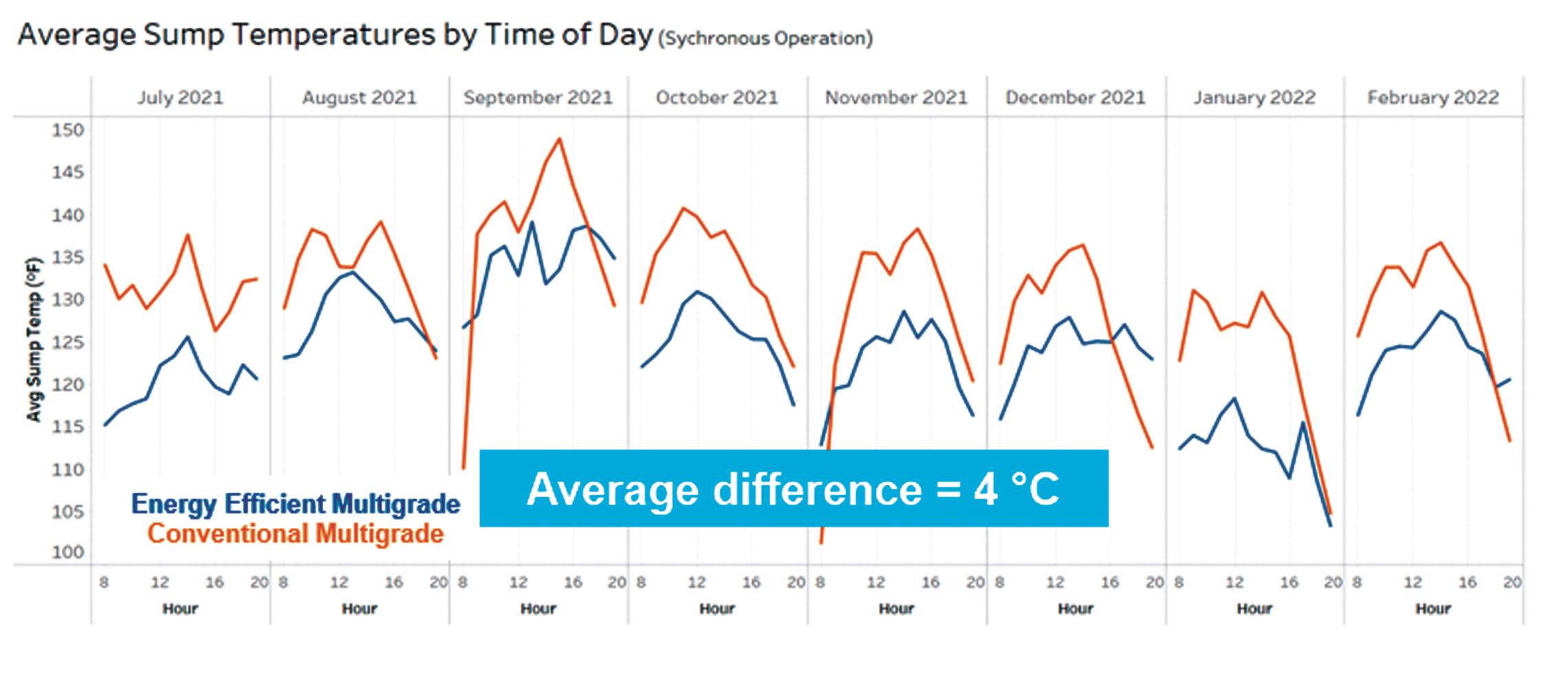
Material handler field trial capturing temperature reduction of 4°C.
How Performance Polymers Play into Modern Hydraulic Fluids
Many modern hydraulic fluids are engineered with performance polymers to address the potential damage excess heat and smaller sump sizes can cause—but they go much further than that. They can enhance a wider variety of performance attributes in the fluids and oils that allows current equipment to operate at peak performance.
For example, an energy-efficient ethylene propylene copolymer (OCP) can be used to improve fluids’ ability to maintain appropriate viscosity levels, as well as improve shear stability. Research has shown that an ISO 46 formulation with an OCP performs better at protecting equipment under all circumstances than a conventional ISO 46 multigrade baseline. And the testing conditions don’t matter—the improvement appears in bench tests, total hydraulic system test rigs and in real-world mobile and stationary hydraulic applications.
Recent testing in laboratory pumps revealed through thermal imaging cameras that the difference in surface temperature was nearly 3 degrees Celsius. Those findings indicate the pump’s internal operating pressure is much lower than fluids with conventional thickeners. Once the bench tests showed promise, the fluid was tested in a full-scale mobile hydraulic field trial. Thermocouple data on those machines showed an average drop of 4 degrees Celsius during an eight-month period. Secondarily, the spike in operational temperatures over time was also reduced.
The reason for this performance is in the molecular structure of the performance polymer. It reduces fluid friction or traction throughout the entire system. Cooler operating temperatures can lengthen the oil-drain interval and provide shorter equipment downtimes as well.
Lower operating temperatures also mean the machine can operate more efficiently. Both in climate-controlled laboratories and on-site, hydraulic fluids in off-highway hydraulic equipment were tested. The fluids with performance polymers far outperformed an ISO 46 monograde control fluid. In fact, fluid formulations containing OCPs increased the efficiency of the equipment between 1.4% and 8.5% in the varied equipment in which they were tested: backhoe loaders, wheel loaders, injection molding equipment and more.
How You Benefit
Significantly reducing operating temperatures in the sump and hydraulic lines allows the equipment to perform properly for longer periods of time and offers other operational and maintenance benefits for equipment owners. Moderated temperatures eliminate some of the concerns discussed earlier, including losing viscosity and premature oxidation. As these problems recede, the high-performance fluids will protect equipment from component damage, expanding not only its protective properties but its performance properties as well.
Lower temperatures can allow operators to have longer oil-drain intervals (ODIs), which means that extensive and costly fluid replacements can happen less frequently saving time and money in the process. Operators understand that fluid changeouts consume significant time during regular maintenance of modern hydraulic equipment. In some cases, this could mean shutting down the equipment until all the hydraulic lines are flushed.
For example, in a mobile excavator, the old fluid must be eliminated from the lines that extend from the cab to the boom. Such flushing is labor intensive and can force equipment out of circulation, which in mission-critical industries like commercial mining can cause significant losses in productivity and profitability. Using modern hydraulic fluids, on the other hand, will keep the equipment productive longer and can provide fewer instances of taking equipment out of the field entirely during the year.
The use of modern hydraulic fluids also improves the energy efficiency of the equipment, meaning it can produce more in less time, which improves profitability. Since the fluid needs to be changed less often, there are advantages to the environment as well. The most recent data reveals that modern formulations allow equipment to move hundreds of thousands more tons, save tens of thousands of dollars on fuel and utility costs and significantly reduce the amount of carbon dioxide produced. All of this suggests that companies that align their hydraulic equipment with the latest technology can positively affect their bottom lines.
In summary, using outdated fluid technology in modern hydraulic equipment does not make financial sense. It is critical to use higher-performing fluids that will help your equipment adapt to today’s harsher operating conditions. In addition, the changes in equipment outlined in this article are expected to continue well into the future. That’s why it’s essential to do the important research necessary to ensure the hydraulic fluids being used have the right chemistry designed to help modern equipment reach its full potential. With the combination of lower operating temperatures and reduced maintenance time, the total cost of ownership can be lowered significantly. Consulting with a reputable fluid supplier will help identify and adopt such formulations, which will contribute directly to the bottom line.
For more information on hydraulic fluids and lowering total cost of ownership, visit Lubrizol360.com.