LANXESS
Sustainable Sulfurized EP Additives for Metalworking Fluids
By Mary Moon, Presque Isle Innovations, LLC | TLT CMF Plus November 2022
Specialists at LANXESS support customers by sharing their hands-on experience developing and manufacturing additives with sustainable chemistries. These additives help customers meet their sustainability goals by extending metalworking tool life, increasing process efficiency, and contributing to the production of critical components e.g., of electric vehicles (EVs).
Specialists in Sulfur Chemistry
According to Wilhelm Rehbein, Senior Manager Application Technology for the Lubricant Additives Business (LAB) (Mannheim, Germany), formulators can rely on a toolkit of light color, low odor sulfurized Additin® extreme pressure (EP) additives to optimize neat oil and water-based metalworking fluids (MWFs). Additin® EP additives are so-called sulfur carriers, sulfurized organic molecules that reduce friction and prevent adhesive wear and cold welding during metalworking processes. Many Additin® EP additives are produced from renewable (vegetable) feedstocks, and they are a sustainable choice for use in environmentally acceptable MWFs that comply with environmental regulations such as the EU Ecolabel.
LANXESS developed the first light color, low odor sulfurized additive sixty-five years ago. Florian Kirchner, Technical Service Manager (Mannheim, Germany) explains, “LANXESS has continued to develop their fundamental sulfur chemistry and now has a comprehensive set of Additin® EP products that cover a wide variety of process requirements. We work in close cooperation with universities, research institutes, formulators and end users to meet the demands of the newest trends with regards to materials and processes.”
Many different types of molecules can be used as carriers for sulfur atoms. LANXESS has deep expertise in the selection of raw materials and process parameters for conducting sulfurization reactions to bond sulfur atoms to organic molecules. Additin® additives are available with various sulfur activity, total sulfur content, polarity, molecular weight and other characteristics to provide specific performance properties such as lubricity, solubility, viscosity, pour point, biodegradability, and so forth.
Figure 1 and
Table 1 compare the main features of the major types of Additin® EP additives for ferrous metals. The RC 23XX series consists of biodegradable sulfurized esters with viscosities from 30 to 55 cSt (mm
2/s) at 40°C (ASTM D445) and very good solubility in Group I-V base oils; they are mainly used in cutting fluids. In comparison, biodegradable RC 24XX sulfurized triglycerides provide greater lubricity, are more viscous (220-350 cSt) and have higher pour points; they are used in all types of MWFs. Members of the RC 25xx series contain higher levels of sulfur and / or have a high polarity and high affinity to metal surfaces which makes them predestined for all kind of heavy duty metalworking processes. Additin® EP additives are recommended for machining low and high alloyed steels, stainless steels, aluminum alloys, titanium and nickel based alloys, yellow metals, or mixtures of metals.
Figure 1: Properties of Additin® RC 2XXX EP Additives.
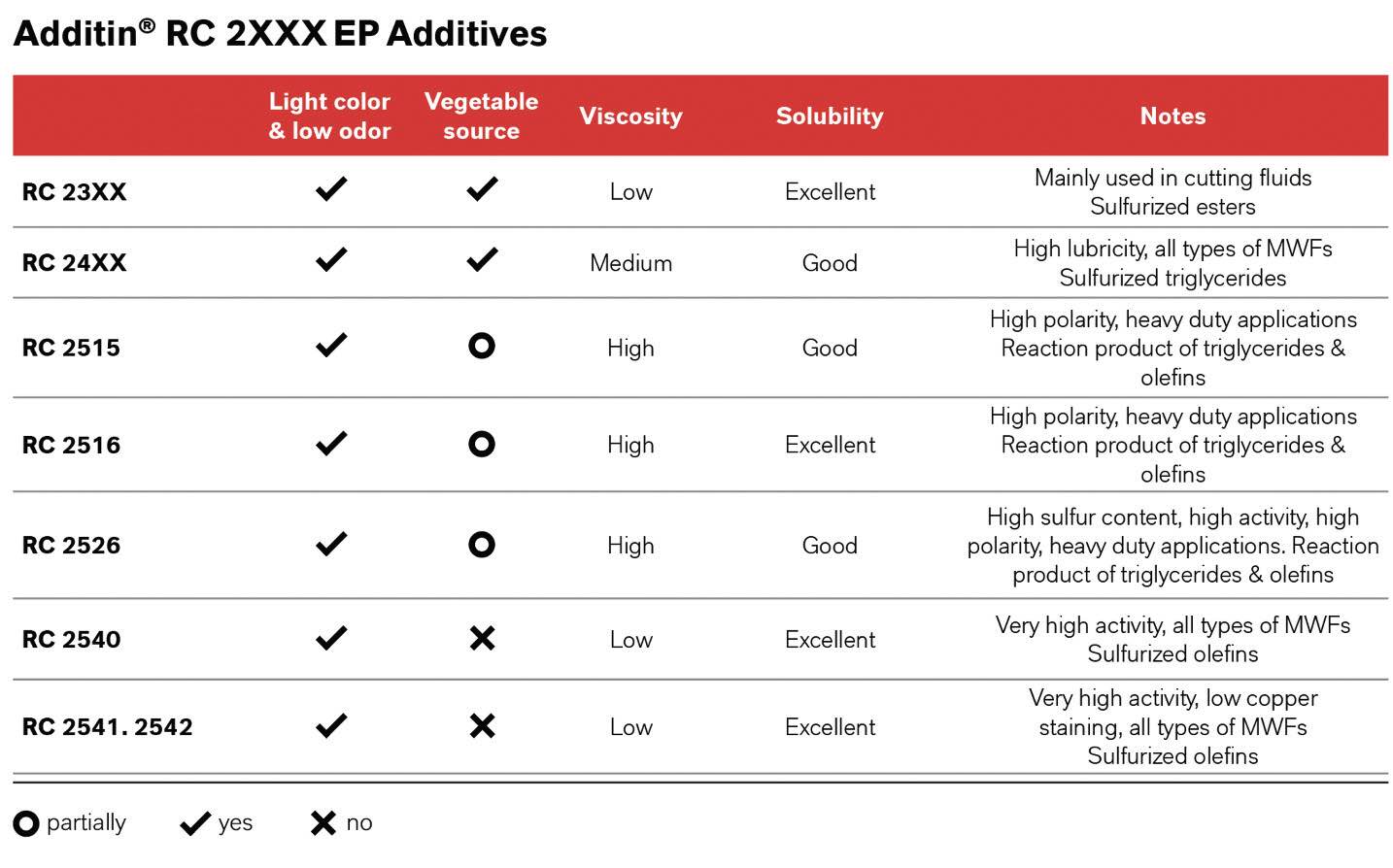
Table 1
Advantages of Sulfurized EP Additives
Rehbein and Kirchner expect that sulfur carriers will continue to be the EP additives of first choice. Polar groups on Additin® EP molecules readily adsorb on ferrous surfaces. During metalworking processes, mechanical and/or thermal stress causes chemical reactions between sulfur atoms in Additin® molecules and iron or other metal atoms. The result is a protective layer on the metal surface that is less stable to mechanical shearing than the metal structure itself and thus prevents galling and cold welding under a wide range of conditions.
Chlorinated paraffins (CLPs), a different group of EP additives, adsorb on ferrous metal surfaces and react to form protective layers of iron chloride. However, at high machining speeds and/or temperatures (or in the presence of liquid water or water vapor), CLPs decompose and form hydrogen chloride gas and/or hydrochloric acid (HCl), which can corrode machine tools and workpieces.
Some CLPs are banned in many countries, and others are heavily regulated, owing to the risks they present to human health and the environment. Additin® EP additives are much safer, more environmentally friendly and sustainable alternatives to CLPs.
Scientists and engineers at LANXESS determined that neat oil and water-based formulations that contained Additin® EP additives gave excellent results such as longer tool life and lower friction than those prepared with CLPs.
Milling
Rehbein explained that LANXESS conducted a field trial on a milling machine. MWFs were formulated from Additin® RC 2526 (a special sulfur carrier, based on a mixture of olefin and triglyceride, providing high sulfur activity and polarity), Additin® RC 3760 (an antiwear (AW) additive), and a medium-chain (chain length C14-C17) chlorinated paraffin (MCCP) in a Group III oil with kinematic viscosity 16 cSt at 40°C.
The milling tool was made of high-speed steel and TiN-coated. The workpieces were made of 42CrMo4V (AISI 4140) steel. The tool life was measured at cutting speeds from 28 to 55 m/min.
Figure 2 compares the results for tool life (m) vs. cutting speed (m/min) for three formulations. For a MWF with 15% MCCP (containing 50% chlorine), tool life decreased from 3.5 to 1.35 m (red bars) as cutting speed increased. This trend was caused by the decomposition of the MCCP at faster cutting speed, i.e., higher temperature, followed by corrosion of the milling tool.
Figure 2: Milling results for tool life (m) vs. cutting speed (m/min).
In contrast to the MWF with MCCP, a formulation with only 5% Additin® RC 2526 (grey bars) gave consistent performance (tool life between 3 and 4 m) at 28, 35, and 44 m/min. At 28 m/min cutting speed, the performance of Additin® RC 2526 was slightly lower than the 15% CLP, therefore 1% antiwear additive Additin® 3760 was added to the cutting fluid formulation (black bars). At higher cutting speeds, the Additin® RC 2526 became more efficient and clearly outperformed the CLP, even without the addition of an antiwear additive. At 55 m/min, the tool life with RC 2526 almost doubled to 6.4 m because of the high activity of the sulfur carrier.
Thus, the Additin® RC 2526 formulations, with and without Additin® RC 3760 AW additive, clearly outperformed the MCCP MWF at cutting speeds of 35, 44 and especially 55 m/min.
Fine Blanking
There is an increasing demand for rotors and stator sheets for electric motors for EVs. Fine blanking and stamping processes used to produce these components involve high surface pressures and require EP additives to prevent adhesive wear.
A press-in test was developed to simulate the tribology of fine blanking and massive forming processes. As shown in
Figure 3, an oversized steel bolt (30.1 mm diameter) is pressed into a die (inner diameter 30.0 mm). The better the load carrying properties of the lubricant, the lower the resulting pressing force.
Figure 3: Schematic diagram of the press-in test.
Figure 4 compares the results for a formulation with 40% MCCP (50% chlorine) in red, and those for a blend of 20% Additin® RC 8000 (a sulfurized polymer) and 3% Additin® RC 3880 (a metal-free AW additive) in black. The normal force was approximately 25% less for the Additin® formulation than the MCCP formulation, even though its treat rate was much lower. The load carrying ability of the blend of Additin® additives was superior to that of the MCCP.
Figure 4: Press-in test results for normal force (kN) vs. punch speed (mm).
Thread Forming
Four MWF formulations were prepared in a Group I mineral oil (ISO VG 46) and compared in a thread forming test shown in
Figure 5. Thread forming is a process of making threads in a hole by using a thread forming tool. The workpiece material was stainless steel , the diameter of the forming tool was 4 mm, and the forming depth was 6 mm. The better the EP performance and friction reducing properties of the lubricant, the lower the resulting torque.
Figure 5: Photograph of the thread forming test apparatus.
In
Figure 6, torque was quite high for the MWF with 10% MCCP (red), however the highest torque was observed for the MWF with 10% Calcinate™ C-400CLR, an overbased calcium sulfonate additive (black). Significantly better results were observed for the MWF with 10% Additin® RC 2540 (a sulfurized olefin EP additive, grey). The synergistic blend of 5% Additin® RC 2540 with 5% Calcinate™ C-400CLR (an overbased calcium sulfonate additive) in a MWF provided a clear additional improvement and the lowest torque in this test (yellow).
Figure 6: Thread forming test results for torque (N cm) vs. way (mm).
Strip Drawing
To simulate the tribological conditions of deep drawing of steel sheets, strips of stainless steel were drawn with 90° deflection. A lower measured drawing force indicates a better performance of the lubricant.
Additives (30% treat rate) were tested in Group I ISO VG 220 base oil. In
Figure 7, the coefficient of friction (CoF) was 0.14 for the MCCP. The CoF was similar or slightly higher for Additin® RC 3080 (zinc dithiophosphate), Additin® RC 3880 (metal-free dithiophosphate) and Additin® RC 8100 (polycarboxylate). Additin® RC 8000 (sulfurized and polymerized triglycerides, CoF 0.11) and Additin® RC 2515 (inactive sulfur, hydrocarbon and triglyceride, CoF 0.09) gave better results, and Additin® RC 2526 (active sulfur, hydrocarbon and triglyceride, CoF 0.08) was the best.
Figure 7: Strip drawing test with deflection.