With the current global supply chain constraints and fluctuating material costs, it is imperative that key industries increase equipment life, reduce maintenance costs and avoid downtime. This article will discuss Cargill’s newly acquired product line REWITEC and how this technology is helping industries increase uptime and extend the lifetime of critical equipment.
REWITEC develops, produces and markets innovative and patented oil and grease additives which have a protective, optimizing, and repairing effect.
The technology consists of phyllosilicates in the form of micro and nano particles and the active system oil or grease carries REWITEC to reach the loaded contacting metal surfaces, i.e., gear mesh or bearing roller race, and coats them by adsorption. During the absorption phase, REWITEC can reverse and repair most surface damage up to 30 microns in size. The new, modified surface has a significantly lower roughness, which leads to a more even load distribution in the system and thus considerably reduces local loads. This protective effect will extend the life of the components as well as reducing frictional forces and therefore operating temperatures in gearboxes, bearings and other rotating or sliding components. This innovative technology has been tested in cooperation with several universities and is being used successfully worldwide.
Here we present data on DuraGear™, REWITEC’s industrial oil additive and show the effects discussed above. Utilizing a 2disk test rig at the University of Mannheim Tribology Lab, Cargill tested popular wind industry gearbox oils both with and without REWITEC. Data sets were taken before and after treatment and both friction and surface roughness were measured.
Figure 1 shows that REWITEC reduced the friction force by up to 55% and improved the surface roughness by up to 54%.
Figure 1: Friction and roughness reduction with REWITEC.
An FE-8 test was conducted with REWITEC DuraGear
(Figure 2), in which a roller bearing test was run with a premium synthetic oil for wind turbine gears. Next, REWITEC was added to another sample of the same oil. The results are substantial and show the protective effect REWITEC has on working metal surfaces.
Figure 2: FE-8 roller bearing test.
The repair effect of REWITEC DuraGear in a 2MW gearbox is shown in
Figure 3. The top image displays gear tooth surface wear in the form of micro-pitting and macro-pitting, oxidation, and debris dents prior to treatment. The second image, post treatment shows how REWITEC has removed oxidation while micro-pitting and debris surface damage have been completely reversed, with macro-pitting substantially repaired.
Figure 3: Repair effect of REWITEC.
REWITEC’s DuraGear and GR400 products are used as a service treatment for equipment in steel mills, cement plants, mining equipment and wind turbines. We recommend treating critical equipment, including gearboxes, 3-5 years after commissioning and re-treating the system every 2-3 years based on operating conditions. If contact fatigue and pitting are the limiting factors on equipment life, then utilizing REWITEC will extend the life of the components and resulting systems.
Figure 4, the results of which were created with Romax Engineering, highlights the potential increase in service life of a wind turbine main bearing after treatment with REWITEC.
Figure 4: Romax Engineering Study.
With the rising costs in the supply chain, various industries utilizing REWITEC products benefit from both its protective, optimizing, and repairing effect and reduction in operating costs.
Meeting the Lubricating Challenges of Tomorrow’s Electric Vehicles with Ester Base Oils
By Nick Weldon, Technical Marketing Manager, Cargill
Challenges of Lubricating Electric Vehicles
While electric vehicles (EVs) lack the complex orchestra of moving parts that make up the internal combustion engine, EV components such as the transmission and motor must still be lubricated and cooled to preserve efficiency and increase component life. EV transmissions are subjected to high torque from low speeds, electrical fields, high voltages, and greater localized heat loads, all of which require novel lubricating solutions. Lubricants for EVs must also have specific performance characteristics, including low electrical conductivity, low viscosity, low traction, offer good heat transfer properties and protect against wear. Standard automatic transmission fluids have been utilized in EVs, but these fluids are not fully optimized for the conditions found in a typical EV drivetrain and novel solutions can offer additional performance benefits.
Improving Efficiency of EVs
While over the last decade battery prices have reduced significantly, they remain the single most expensive component in an EV.
Figure 5 shows how the efficiency of an EV decreases as the mass increases: For every additional 1000kgs, efficiency decreases by about 1 mile per kWh, or 26%. A battery with 100 miles of range in a 2500kg vehicle can cost $1000 more versus one for a vehicle weighing 1250kg. With these facts in mind, getting the most out of a battery pack by increasing efficiency is of significant interest.
Figure 5: Relationship between EV efficiency and mass.
*Based on WLTP test and total battery capacity
Improving Gearbox Efficiency by Reducing Traction
In a transmission, traction is a friction effect caused by the shearing force of the oil in the rolling/sliding condition between gear teeth. Higher traction means higher resistance to movement, and this causes drag, reducing efficiency and so vehicle range. A formulator can reduce lubricant viscosity to reduce drag, but as viscosity is reduced, wear protection can be compromised. Here we present our development Group V ester base oil, DE 10766.
Figure 6 shows that at 40°C, this product has the same traction as Group III at 100°C, even though it has more than three times the viscosity, offering potential for wear protection without loss of efficiency.
Figure 7 displays results in fully formulated lubricants at 4.5 cSt. Adding 20% DE 10766 into a group III or group IV base oil reduces traction by 8%, even under harsh conditions.
Figure 6: Traction coefficient of neat DE 10766 vs neat group III.
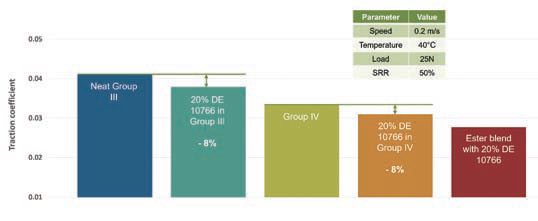
Figure 7: Adding 20% DE 10766 to group III or group IV.
Reducing Traction vs. a PAO 100 Thickened Formulation
Perfad™ 7726 and Perfad™ 7782 are unique, patented, high viscosity traction reducing co-base fluids. These increase viscosity of a gear oil without impacting traction, making them especially suitable for applications that require high levels of gear wear protection.
Figure 8 displays results of traction testing in a fully formulated Group III base oil. Adding 5% of our new high viscosity co-base oil reduces traction by up to 32% in a fully formulated Group III base oil.
Figure 8: Adding 5% of high viscosity co-base oil to Group III.
Reducing Gearbox Wear
Figure 9 displays the results of profilometry after running the FZG on SRV gear contact mimic test. A group III base oil fails the test at 78 minutes. Adding 10% DE 10766 low traction ester base oil to a Group III base oil significantly reduced wear. Adding an additional 5% Perfad 7782 reduced wear even further. We also performed this test in a group IV base oil and saw similar results. In a Full FZG A10/16.6R/90 test, adding 20% DE 10766 and 5% Perfad 7782 outperforms a fully formulated Group IV base oil by two load stages. Perfad 7726 and Perfad 7782 are organic and do not increase electrical conductivity or copper corrosion.
Figure 9: profilometry after testing wear performance with FZG on SRV.
Here we have given a quick overview of Cargill’s products and products in development specifically designed to improve efficiency and reduce the risk of wear in both wind turbines and electric vehicle gearboxes.