The Stribeck curve
Dan Holdmeyer, Contributing Editor | TLT Lubrication Fundamentals July 2022
Have you heard of the Stribeck curve and its significance in understanding lubrication?
The Stribeck curve is referenced reverently when discussed in the field of tribology (see Figure 1). Tribology is the study of the effects of friction on moving machine parts, and of methods of minimizing them, such as lubrication.
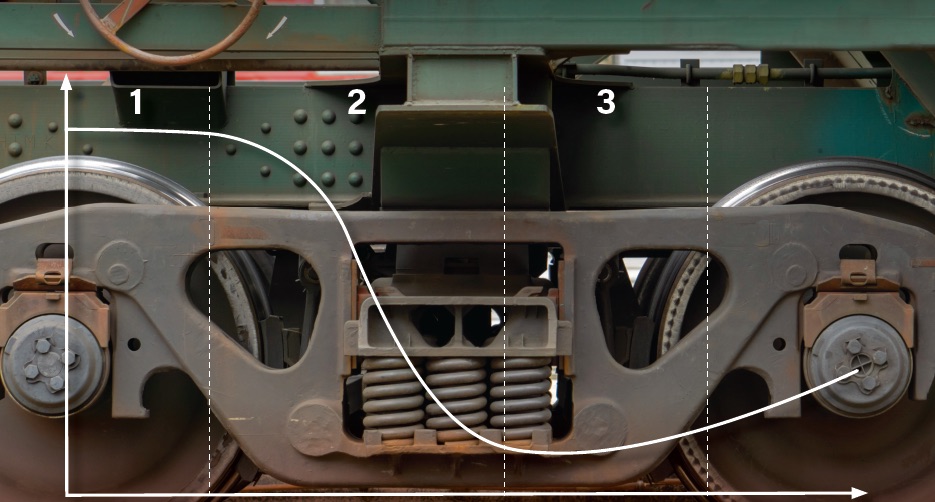
Figure 1. The Stribeck curve.
Near the end of the 19th and the beginning of the 20th centuries, Richard Stribeck and others were studying friction as it is affected by load, lubricant viscosity and bearing speed. Specifically, he was studying the frictional properties of lubricated railroad journal bearings. I emphasize lubricated journal bearings, which surely was a drastic improvement over non-lubricated journal bearings of prehistoric times. Archaeological evidence exists from over 2,000 years ago showing chariot bearings were lubricated. However, before these 20th century studies, little was known about the correlations between friction and the components of the Hersey number, which include journal rpm, shaft load and the lubricant viscosity.
So, what are some lubrication fundamental understandings derived from the Stribeck curve and related studies? The Stribeck curve graphically demonstrates three distinct ranges along the horizontal axis with unique slopes where the change in the coefficient of friction on the vertical axis is unique. These distinct ranges have since been identified as three lubrication regimes: boundary, mixed and hydrodynamic lubrication.
Boundary lubrication
The boundary lubrication regime starts when the journal begins to rotate from rest in the bearing, and the two, journal and bearing, are still in contact with each other. Prior to journal rotation, static friction must be overcome. Static friction is higher than kinetic friction. Think about sliding your couch across the living room floor. Once the couch starts moving, the effort to keep it moving is much less than required to start the couch moving. That is an example of overcoming static friction and continuing to work against kinetic friction. If the Stribeck curve graph starts at the “zero” mark along the x-axis, or where the rotational speed is zero, the coefficient of friction would be significantly higher than the lower and relatively flat curve of the boundary lubrication regime. Quite frequently this static friction is not shown on the Stribeck curve.
Even though the journal and bearing appear to be highly polished surfaces, they contain asperities, or microscopic hills and valleys. The full load is supported by the microscopic peaks of the asperities. In boundary lubrication, these asperities must slide over each other without lubrication film, as with pushing your couch across the floor, or with the assistance of the minimal amount of lubricant trapped in the asperity valleys.
If the load per square inch is high enough, though, surface-active additives, such as friction modifiers and antiwear agents, may be required to reduce friction and wear before a lubricant film is developed via the rotation of the journal. Such additives provide a sacrificial film that shears easily so that the asperities can slide over and past each other without gouging, or welding to, each other. If the load is high enough but surface-active additives are not used in the lubricant, “hydrostatic lubrication” may be used to reduce the pressure on the asperities. Hydrostatic lubrication is when a lubricant film separates the bearing asperities through oil pumped into the bearing. If the lubricant flow into the journal is enough to separate the asperities, the lubricant regime may become a “hydrodynamic lubrication regime” where the asperities are completely separated by a film of oil. Some may argue that hydrostatic lubrication is another lubrication regime, but it is more likely a lubrication method to affect an actual lubrication regime.
Mixed lubrication
As the journal begins to rotate faster and faster, it drags the lubricant between itself and the bearing. This lubricant begins to lift the journal asperities off the bearing asperities reducing their contact and, thus, friction, as depicted in the mixed lubrication portion of the Stribeck curve. This portion of the Stribeck curve has the steepest slope where the coefficient of friction is significantly reduced over relatively small change in rotational speed as fewer and fewer asperities of the journal and bearing contact each other.
In its simplest form, the Stribeck curve graphically shows how the coefficient of friction of a journal bearing is affected by the speed of the shaft rotation. Lubricant viscosity, load and surface roughness are held relatively constant while changing the speed of the journal rotation only. In its more complete form, the Stribeck curve incorporates the Hersey number, named after Mayo D. Hersey, whose studies enhanced the Stribeck curve. The Hersey number is essentially the lubricant viscosity (μ) times the journal speed (N) divided by the load (P).
Hydrodynamic lubrication
The hydrodynamic lubrication regime is where the journal and bearing asperities no longer come in contact with each other and starts at the lowest coefficient of friction point of the Stribeck curve. Hydrodynamic lubrication also is known as “full fluid film lubrication” because the load is carried entirely by the lubricant film. This usually occurs when the lambda ratio reaches 3. Lambda ratio, sometimes just called lambda (λ), is a parameter used to distinguish the lubrication regimes. Lambda is the ratio of the lubricant film thickness to the combined root mean square of the surface roughness of the journal and bearing.
In the hydrodynamic lubrication regime, as the speed increases, the coefficient of friction begins to increase. It is the first time the coefficient of friction increases with increased speed, and it is due to the lubricant’s viscosity. Viscosity is a measure of the lubricant’s internal resistance to flow, thus with higher speeds the oil provides more resistance or friction.
Surface roughness also affects the Stribeck curve as does increased load. Increased surface roughness or increased load pushes the curve up and to the right, i.e., it takes increased speed to reach the hydrodynamic lubrication regime with increased load or increased surface roughness. Conversely, a reduction of load, or surface roughness smoothening via “run-in,” moves the Stribeck curve down and to the left.
We can relate this to a common experience of driving in the rain. Think of the rainwater on the road as the lubricant. Your tires and the road are the journal and the bearing. Parked in the driveway, your tires are in full contact with the road. As you drive away, your tires still make good contact with the road. Representationally, the road and tires asperities are in contact and carrying the load of your car. A few minutes later, while driving at highway speeds, you hit a puddle of water and begin to hydroplane. Your tires are no longer in contact with the road. The weight of your vehicle is lifted from the road by the water. Ideally you would slow down once you start to hydroplane so your tires could regain contact with the road. On the Stribeck curve, slowing your vehicle would be the equivalent to moving left along the x-axis (horizontal), transitioning from hydrodynamic lubrication to mixed lubrication and possibly to boundary lubrication. With new tires, at a given speed, you are less likely to hydroplane when you drive through a puddle of water than if you had nearly bald tires, i.e., less surface roughness, or tires with excessive “run-in.” Similarly, a heavier vehicle requires higher speeds to hydroplane than light vehicles given the same level of tire tread.
Now, back to lubrication and further uses of the Stribeck curve and the Hersey number. Measuring Stribeck curve can be useful to evaluate the performance of lubricants. The pin-on-disk test is a common way to measure Stribeck curves. The pin is pressed against a rotating disk under a given load.
The traction coefficient of various lubricants can be quantified by plotting the Stribeck curve of various lubricants while other parameters of the Hersey number are held constant. For example, such studies have shown that polyalphaolefin (PAO)- and polyalkylene glycol (PAG)-based lubricants have lower traction coefficients than mineral oils, and, thus, would potentially increase machine efficiency.
Those are the fundamentals of the Stribeck curve that helped discover several fundamentals of lubrication and are used today to further understand lubrication and lubricant characteristics.
Dan Holdmeyer is retired from Chevron Lubricants and is based in Washington, Mo. You can reach him at dan.holdmeyer@gmail.com.