Meet the Presenter
This article is based on a Webinar presented by STLE Education on March 17, 2021. Troubleshooting Metalworking Fluid Field Problems - Part 1 is available at www.stle.org: $39 to STLE members, $59 for all others.
STLE member Patrick (Pat) Brutto is founder and technical application specialist for Faith-Full MWF Consulting, which provides services to all segments of the metalworking fluids (MWFs) value chain. Prior to founding this company, Brutto spent the early part of his career with Pennzoil Products Co. as an industrial grease formulator and most of his career serving in R&D and global technical services with ANGUS Chemical Co., a producer of specialty additives for MWFs and many other markets. He also provided field technical services for Hangsterfer’s Laboratories, a U.S.-based producer of MWFs.
Brutto holds a master of science degree in chemistry from DePaul University in Chicago, and he is an STLE Certified Metalworking Fluid Specialist™ (CMFS). He has served the STLE Chicago Section several times as program chair and education chair, and he also was section chair from 2012 to 2013. Brutto currently serves as vice chair of STLE’s Metalworking Technical Committee.
You can reach Brutto at patrick.e.brutto@gmail.com.
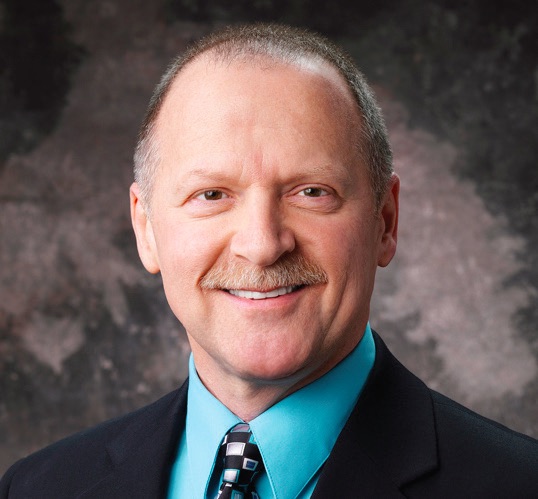
Patrick Brutto
KEY CONCEPTS
•
The right metalworking fluid (MWF) formulation keeps costs down by reducing surface finish problems, reducing maintenance shutdowns and fluid change-outs and lengthening tool life.
•
Fluid maintenance includes monitoring dilution water quality, MWF concentration, microbe levels, emulsion stability and contaminant and debris levels.
•
End-users must communicate with fluid, tooling and equipment suppliers to make sure that specific machining operations, fluid formulations and maintenance practices all work together.
Metalworking operations involve many interacting factors, only one of which is the metalworking fluid (MWF). Solving problems on the production floor requires identifying the factor (or factors) most responsible for the problem. Besides the MWF formulation, other contributors to machining performance include maintenance practices, the type of metalworking operation, machining variables (speed, feed, etc.), the workpiece metallurgy and the environment in the production area.
This article is based on an STLE Webinar titled Troubleshooting Metalworking Fluid Field Problems - Part 1 and presented by Patrick Brutto, founder and technical application specialist for Faith-Full MWF Consulting. See Meet the Presenter for more information. This webinar focuses on operational factors, and a second webinar—Troubleshooting Metalworking Fluid Field Problems - Part 2—focuses more specifically on the MWFs. That article will be published in the June TLT.
Metalworking fluid basics
The term “metal-removal fluid” (MRF) often is used interchangeably with MWF, but the same principles apply for MRFs and metal-forming fluids (MFFs), another subset of MWFs. Here, we focus on water-dilutable MRFs, which provide lubrication, cooling and chip removal for a variety of machining operations. Endusers buy MWF concentrates, which they dilute with water, as specified by the formulator (typically 5%-10% concentrate, 90%-95% water).
MWF concentrates contain as much as 70%-90% hydrocarbon oil, in the case of emulsifiable oil formulations. Semisynthetic concentrates contain 5%-50% hydrocarbon oils, and synthetic concentrates contain 0%. Alternatives to hydrocarbon oils include vegetable oils, esters and various water-soluble polymers. Water is the most effective cooling agent, but it also can introduce microorganisms that degrade fluid performance over time. Some MWFs contain registered biocides in the concentrates, and biocides can be added tank-side to the diluted fluids to prevent and control microbial growth. Tank-side biocide replenishment requires handling precautions and an awareness of health and safety concerns.
Several types of problems can affect the cost per part in a metalworking operation and have a negative impact on working conditions. Identifying and solving these problems requires a systematic evaluation of symptoms, observations of the machinery and operating conditions and communication among the key stakeholders. Stakeholders include MWF suppliers (formulators, field services), suppliers of other fluids and chemicals (slideway lubes, hydraulic fluids, cleaners, biocides), end-user representatives (machinists, fluid and plant managers, health and safety officers) and equipment suppliers (tooling, machines, filtration equipment, water treatment equipment, etc.).
Problem: Unacceptable surface finish
Improper MWF formulations
(see Fluid Condition Monitoring and Composition) can contribute to poor lubrication, residues, corrosion and other issues that affect workpiece surface finish
(see Figure 1). Surface finish problems also can be caused by bacteria and fungi, which can degrade the chemistry of the MWF over time
(see Fighting the Microbes). Regular monitoring can identify problems in the early stages and reduce the need to dump and replace the fluid. Water quality, including hardness cations, corrosive anions and other minerals and organics present in the dilution water, plays an important role in fluid performance and surface finish
(see Water Quality).
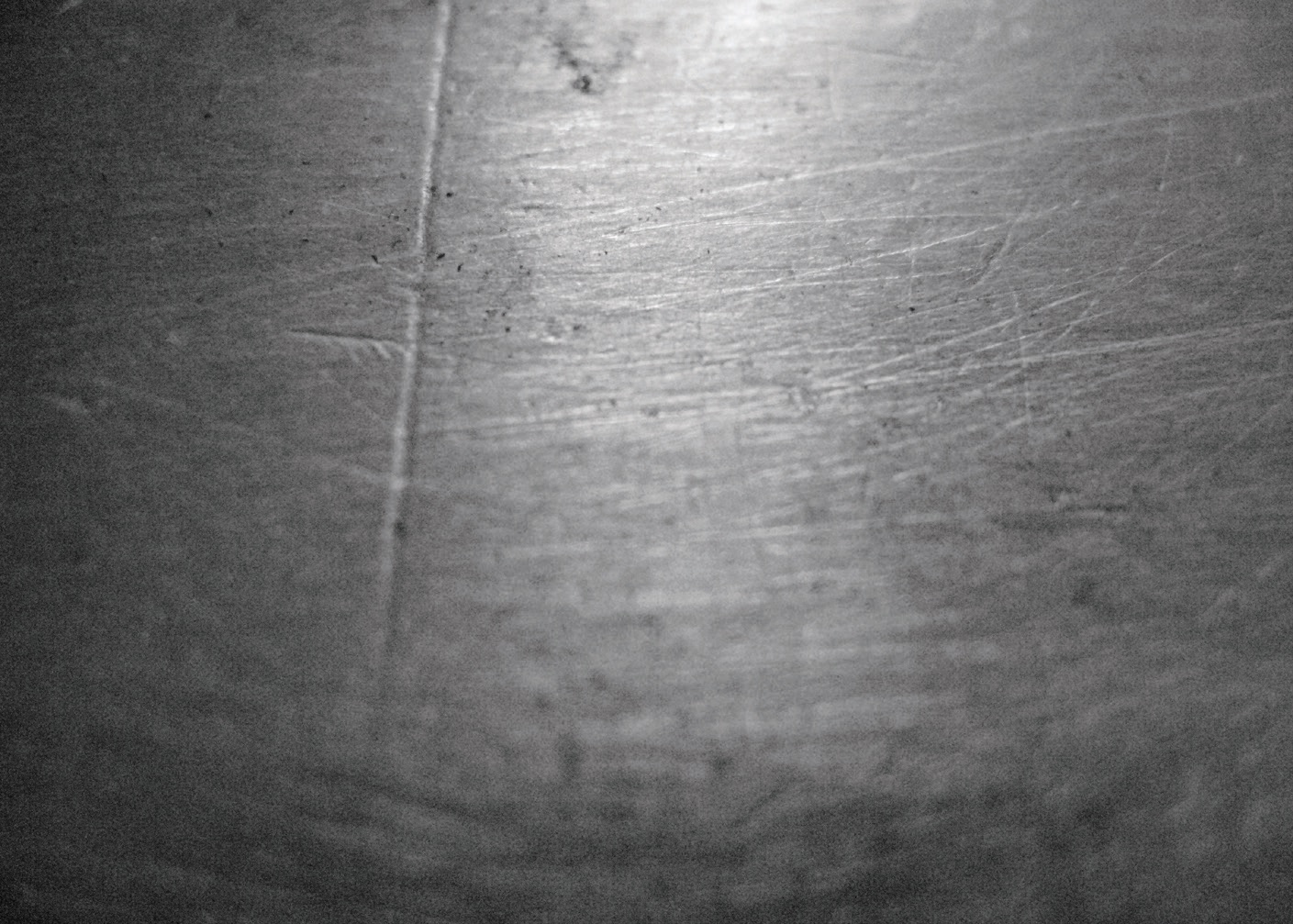
Figure 1. Scratches on a metal surface. Figure courtesy of Shaire Productions, CC BY 2.0.
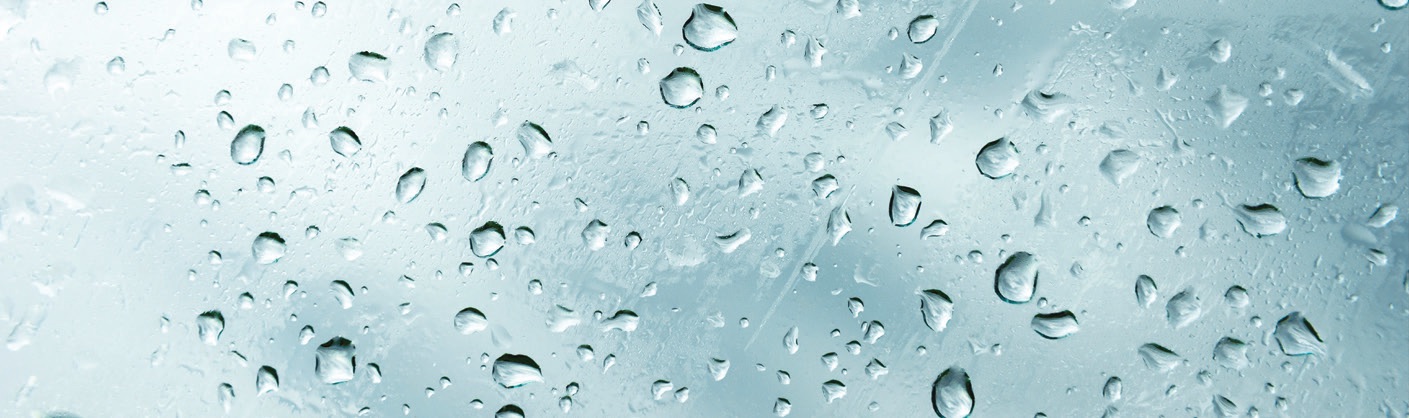
Fluid condition monitoring and composition
Water evaporation, which concentrates the MWF over time, is a common problem. Consistent monitoring can help ensure that the dilution concentration is being maintained according to the manufacturer’s specifications. Commercial test kits and handheld instruments (e.g., refractometers) are a quick, field-friendly, economical means to check the condition of used MWFs. They often can provide results on the spot, enabling timely adjustments to be made before problems occur. Test equipment and MWF suppliers often can recommend the best methods to use for specific operations, fluid formulations and required degree of accuracy.
Anti-rust, anti-corrosion and lubricity additives may need to be adjusted or replaced with more effective ones, specific to the process and alloys being machined. For example, various extreme pressure (EP) additives (chlorinated, sulfurized or phosphorus-based) are activated at different temperatures, so the process temperature and fluid formulation must be compatible. Other adjustments include increasing the oil content of the MWF or adding non-EP additives like fatty acids, esters and others.
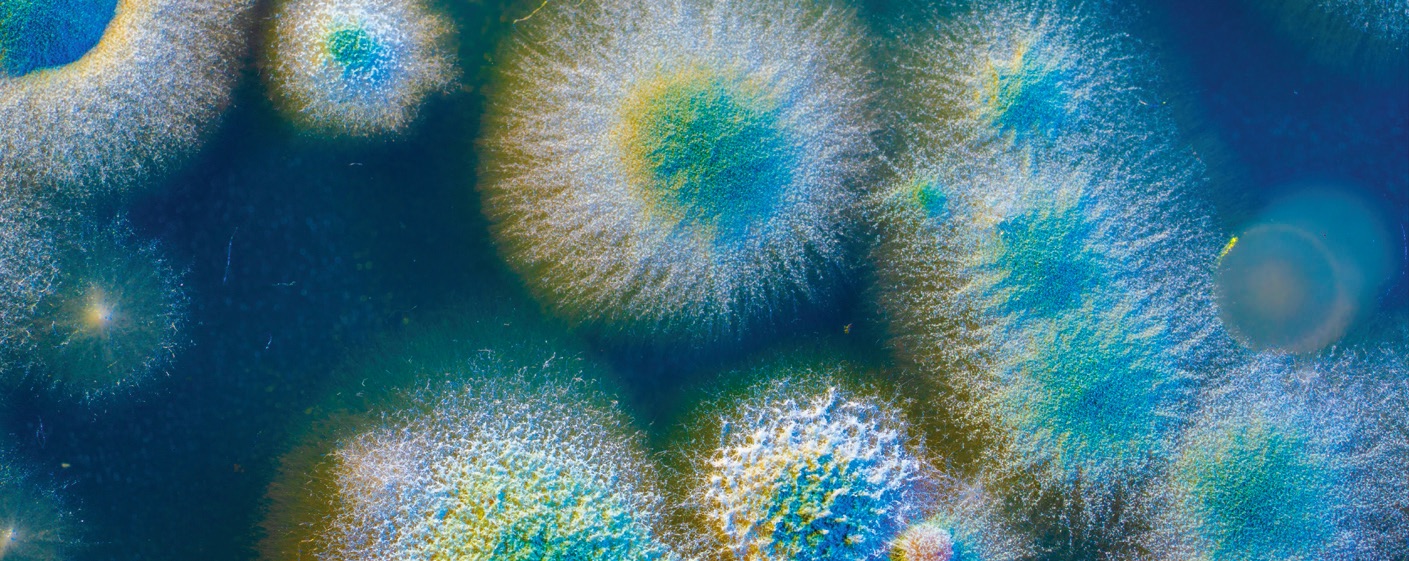
Fighting the microbes
Bacteria and fungi can degrade the chemistry of the MWF over time. Regular monitoring can identify problems in the early stages and prevent early fluid failure. Representative samples should be taken weekly from the delivery nozzle and sump or central system tanks and checked for total bacteria and fungi using dip slides.
If bacterial concentrations exceed 100,000 colony-forming units per milliliter (CFU/mL) or fungal concentrations exceed 1,000 CFU/mL, degradation of some fluid components is likely, especially if these levels persist for several weeks. The MWF supplier may recommend a tank-side biocide treatment, a partial dump and replenishment or a fluid recovery procedure. However, the system might need to be dumped, thoroughly cleaned and treated with a supplier-recommended quick-kill biocide solution, then rinsed and refilled with fresh fluid.
If the MWF is degrading despite the recommended monitoring and maintenance procedures, it might be necessary to reformulate it. The biocide chemistry must be compatible with other MWF components, and the concentration should be optimized. If necessary, bio-supportive ingredients like triethanolamine (TEA) and phosphorus, sulfonate and vegetable-based additives should be reduced or replaced with more bioresistant performance equivalents.
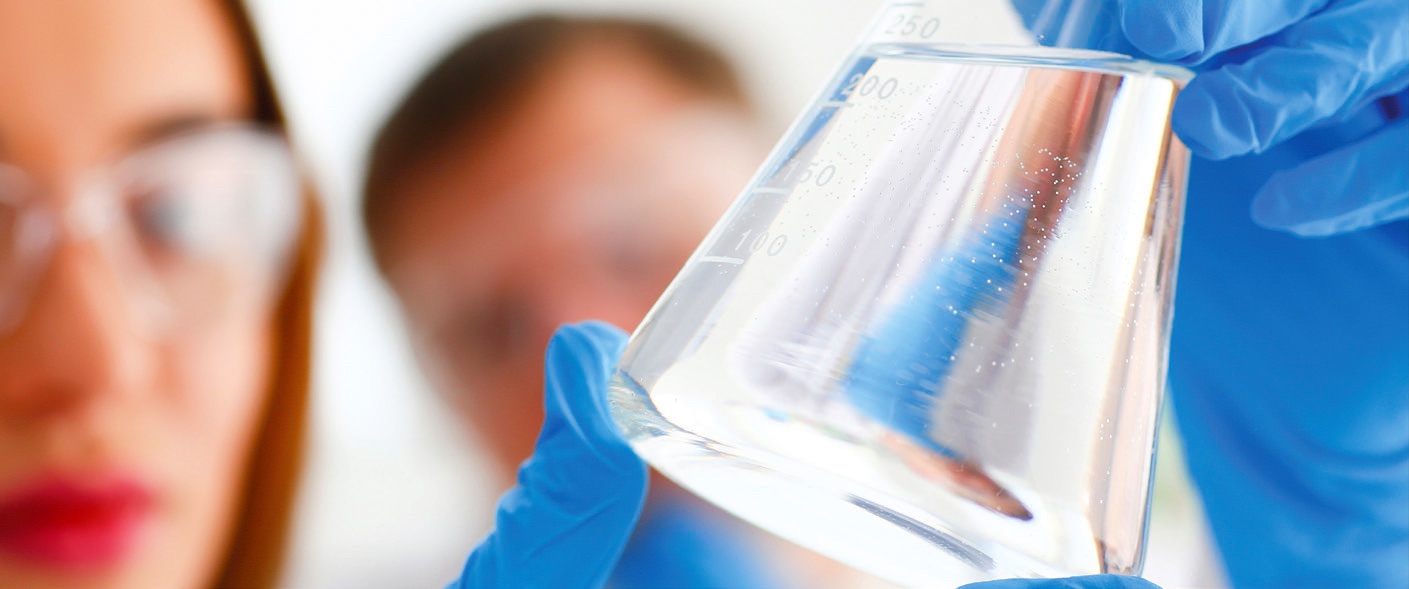
Water quality
A fluid supplier can test various MWF formulations in the lab using “synthetic hard water” that has been made to simulate the end-user’s dilution water. Water pre-treatment should be recommended if tests show undesirable levels of total hardness (> 125 ppm), chloride (> 50 ppm), sulfate (> 100 ppm), conductivity (> 500 μS/cm), bacteria (> 100 CFU/mL) or fungi (> 10 CFU/mL).
Hard water pretreatments include softening to remove divalent cations (primarily calcium and magnesium); deionization to remove cations and corrosive anions; and reverse osmosis to eliminate cationic, anionic and microbial contaminants. Water softening is the least expensive option, but it will not remove corrosive anions. A deionization (DI) or reverse osmosis (RO) system installed after the softener can further improve water quality and extend fluid life. Foaming can be a problem with softened, DI or RO-treated water, and adding a supplier-recommended defoamer should help.
If the same batch of MWF is being used to machine multiple metals, contact between particles of these dissimilar metals can cause galvanic corrosion on workpieces, tools and machine surfaces. A simple “sandwich” test to determine if this is the source of the problem involves placing the MWF between coupons of the various metals involved to see whether corrosion occurs. Increasing the fluid concentration might help to reduce or prevent corrosion, or it may be necessary to modify the corrosion inhibitor system. A consultation with the MWF supplier can help the end-user to decide if the system should be dumped and replaced or if tankside treatment could help.
Contaminants entering the MWF circulate throughout the system, and these can have a negative effect on surface finish as well. Metal chips and fines can accumulate if filtration systems are not properly configured and maintained
(see Filtration and Chip Removal). Tramp oil can enter the system through leaking seals and other sources. Floor and parts cleaners can accidentally (or intentionally) find their way into sumps
(see Leaks and Contaminants). Improper MWF formulations can contribute to poor lubrication, residues, corrosion and other issues that affect workpiece surface finish.
Filtration and chip removal
A consultation with the filter supplier can help ensure the proper selection and size of conveyor, chip removal and filtration systems, based on the metals being machined, the machining process, the MWF recirculation rate and the type of MWF being used.
To determine the level of metal fines that are present, small samples of used MWF should be taken from various locations in the system (sump, before and after filters, delivery nozzles, etc.) and heated in a muffle furnace until a stable weight is achieved. The weight percent solids should then be compared with freshly diluted fluid at the same concentration and water hardness.
Conveyors, chip separators and filters should be inspected regularly for proper operation, buildups and leaks (see Figure A). Sumps should be checked for accumulations and the systems cleaned and flushed as needed.
Figure A. Conveyors and chip separators should be routinely checked for proper operation.
Leaks and contaminants
Leaking hydraulic fluids, slideway lubricants, spindle oils and other fluids can contaminate MWF in circulation. Faulty seals and other leak sources should be repaired or replaced, and the end-user should check the tramp oil removal equipment for proper operation. Floor cleaners or parts cleaners that make their way into the MWF sump or storage tank can be corrosive to workpiece materials and tools, and they can destabilize emulsions and chemically degrade MWF components. If significant contamination is present, it may be necessary to dump, thoroughly clean and refill the system with fresh fluid.
If tramp oil removal equipment is not available, a belt skimming or coalescing device should be installed—coalescing devices, in particular, are inexpensive, have small footprints and are very effective.
Even the best MWF can fail if the wrong tools are being used. Discussions of the process and workpiece metallurgy should involve the end-user, MWF supplier and tooling supplier to ensure that the tool material, type and geometry, as well as the machining conditions (speed, feed, depth of cut, etc.), are optimized based on the workpiece metallurgy and machining process. The MWF must be applied to the proper location at the tool-workpiece interface
(see Figure 2). For maximum lubrication, fluid should be directed to the underside of the chip, but for maximum cooling, the fluid should be directed across the cutting edge, preferably at higher pressures.
Figure 2. (Left) For applications where lubrication is most important, fluid is applied to the top and bottom of the chip and up into the cutting zone. (Right) For greater cooling, fluid is applied along the tool edges. Figure courtesy of Byers, J., Metalworking Fluids, Second Edition, CRC, Taylor & Francis Group LLC, 2006 (p. 63, figure 3.17).
Sometimes, the problem isn’t the MWF at all: a discussion between the end-user, MWF supplier and tooling supplier might determine that the machining variables are not optimized. Feed rate (how fast the workpiece is fed into the cutting zone), cutting speed (the rotational speed of the cutting tool), depth of cut and other process variables must be optimized to meet surface finish, dimensional tolerance and tool life requirements.
Problem: Unacceptable part tolerances
Various machining processes produce parts with different tolerances—the amount of permissible variation of a specific part dimension. Incorrect tool choice, poor tool alignment and insufficient tool rigidity can cause part dimensions to routinely fall outside of tolerance specifications. The wrong MWF composition or concentration can contribute to the problem, and microorganisms in the MWF can degrade lubricity additives.
Thermal expansion and differential cooling rates contribute little, if any, to overall changes in part dimensions, especially if the MWF has effective cooling properties. Machining affects temperatures mostly at interfacial surfaces, with little change in the bulk temperature.
Problem: Residues forming on parts and machines
Using an MWF concentration above the recommended range can promote residue formation, which can adversely affect machining operations and tooling. Removing residues from workpieces adds to the time and cost of producing parts. Fluid concentrates should be diluted according to the supplier’s recommendations and monitored regularly to ensure that water evaporation is not causing concentrations to rise above acceptable levels. Concentration checks should be made at the beginning of every shift, with water or makeup fluid added to maintain the MWF within range.
Some MWFs contain residue-forming components, like some boron compounds that can form sticky or hard residues. If freshly diluted MWF forms residues on lab samples, reducing concentration to the low end of the recommended range may help. If the freshly diluted MWF forms a residue even at lower concentrations, it may need formulation adjustments (e.g., higher oil concentrations or reduction or elimination of residue-forming components). If a residue only forms with the used fluid, the problem could be due to high concentration, high water hardness due to water evaporation, tramp oil, metal fines or other contaminants.
Problem: Reduced tool life
Selecting the right tool (insert, grinding wheel, etc.) and using tools that are properly aligned and sufficiently rigid can pay off in terms of longer tool life (
see Figure 3). The tool supplier can offer advice on using the correct insert material or grinding wheel abrasive for the process workpiece metallurgy and MWF type. Checking to ensure that the tool is properly secured to avoid misalignment and chatter is critical.
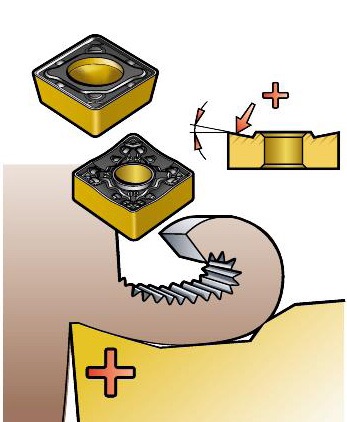
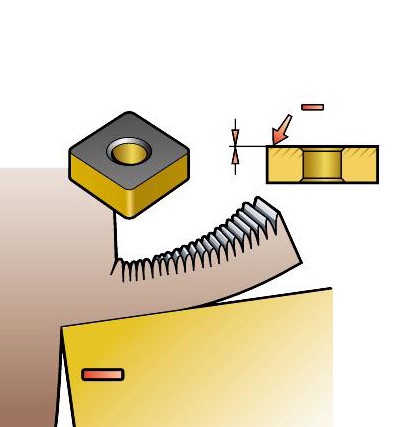
Figure 3. (a) The insert rake angle (the angle between the top face of the insert and the horizontal axis of the workpiece) and tool inserts can be positive or negative, which determines the type of cutting action. (b) (Top) Turning, which often involves continuous cuts at high temperatures, requires a durable edge that retains good chip breaking ability and resists wear and plastic deformation. (Middle) Milling tool edges must have good bulk strength and resistance to thermal cracks to avoid breaking during intermittent cutting actions. (Bottom) Drilling edges must be strong enough to last at very low cutting speeds, and they must break chips efficiently for ease of transport out of the narrow chip flutes and from inside the drill hole. Coolant and chip removal fluid causes temperature variations that put the edge under stress. Figure courtesy of Sandvik Coromant.
Often, higher speeds and feeds are required to activate certain extreme pressure (EP) additives to maximize lubrication. Faster cutting speeds can shorten tool life, while feed rates and cutting depth have smaller effects.
MWF dilution concentrations that are out of range or not optimized for the process, tool and workpiece also can shorten tool life. Concentrations should be checked and adjusted as needed at the beginning of every shift. For processes where lubrication is a priority, MWF concentration can be increased in ~2% increments, or as recommended by the fluid supplier, to evaluate the effects on tool life. If the process requires maximum lubrication, the MWF formulation may need a higher oil content, a higher concentration of lubricity additive(s), a different type of lubricant or one or more different types of lubricity or EP additives (which activate at various temperatures). For grinding applications, where cooling is a higher priority, the MWF concentration may need to be reduced, in consultation with the MWF supplier.
Increasing the MWF flow rate can increase tool life by improving cooling and ensuring more complete removal of contaminants, chips and metal fines. However, for milling processes, reducing the flow rate can minimize thermal shock to the tool (consult with the tool supplier). The tool supplier also can help the end-user determine whether the fluid is being directed to the proper location in the cutting zone, based on the process, tool and workpiece materials.
Even a well-formulated MWF can be ineffective if it is contaminated with hydraulic fluids, slideway lubricants or floor cleaners, or if it contains high levels of metal fines. Tramp oil contamination, which is present to some extent in most systems, can shorten tool life, so it should be removed regularly.
If necessary, the system should be dumped and cleaned thoroughly to remove chips, fines, biofilm and other contaminants. If microbial growth is degrading the MWF, a solution of quick-kill biocide should be circulated through the system followed by thorough rinsing (as recommended by the MWF and biocide suppliers), and the system should be refilled with freshly diluted MWF. The MWF should always be recirculated, even during shutdowns, to reduce the risk of anaerobic bacterial growth and formation of toxic, corrosive hydrogen sulfide.
Problem: Oil accumulates on the MWF surface
Oil accumulation on the MWF surface could indicate that the emulsion is losing stability. If the root cause is determined to be an unstable fluid, possibly due to poor hard water stability or microbial contamination, the system will likely need to be dumped, cleaned and refilled with a more physically stable or microbially resistant MWF. If the accumulation is primarily tramp oil, it should be regularly removed using a skimming or coalescing device.
Problem: MWF performance varies with machine
The same fluid formulation can perform differently in different machines, even in the same facility. Comparing process design and operating parameters can identify differences that are due to the machines themselves, rather than the MWF. Contact machine suppliers, tool manufacturers and MWF suppliers to determine if differences in design and operating variables could be contributing to the observed performance differences.
Problem: Mist forms in machining areas
Trends in machining operations are moving toward higher fluid pressures and recirculation rates, and these can increase misting. If the process allows, reduce the recirculation rate, or use a wider-diameter delivery nozzle. Ask the machine supplier if plastic shields are available to divert mists away from workers. For a closed machining center, consider adding a mist collector. Adding or increasing local exhaust ventilation can direct mists to a safe area. High tool speeds and large-diameter tools, including mills and grinding wheels, also can increase misting. If the process allows, reduce tool speed and increase the MWF feed rate.
Some misting problems are related to the MWF rather than the machine. Loosely emulsified or “free” oil, possibly caused by a loss of emulsion stability or tramp oil contamination, can increase misting. Check for proper operation of tramp oil removal equipment, clean or repair as needed and implement a regular maintenance schedule. If tramp oil is well controlled, determine whether the emulsion is losing stability. Ask the MWF supplier to determine the condition of the fluid (microbial contamination, hardness, pH, etc.). If the fluid is performing well and other parameters are in control, the supplier might suggest a tank-side treatment with an emulsifier or demisting additive.
Early investments pay off in cost reductions later on
Excessive machining time can increase production costs. Small changes add up, so this optimization is critical if large quantities of a specific part are being produced. Many factors influence the performance of machining systems, and many of them are interdependent. Some issues are more related to operational factors and others more related to the MWF formulation and maintenance.
The MWF supplier can recommend the best fluid formulation to use for reducing tool cost and increasing performance and longevity. Relevant factors include water quality, machine type and machining process, workpiece metallurgy, dimensional tolerance and surface finish requirements, tooling type and contamination control (tramp oil, metal fines, etc.).
Even if the right fluid is in use, inadequate maintenance can cause substandard performance. Regular maintenance and recordkeeping for each machine should include MWF concentration, pH and reserve alkalinity, water hardness, conductivity, bacterial and fungal levels, makeup volumes and concentrations, tank-side treatments (type, amount, frequency) and analyses for tramp oil, metals and other contaminants. Regular cleaning schedules should be implemented for sumps, flumes and sluiceways, chip conveyors, settling tanks and filtration devices.
Regular record-keeping and maintenance routines, as well as good housekeeping procedures, can pay off in terms of better product quality and reduced operating costs. Good communication among all stakeholders can lead to faster problem solving and better long-term outcomes.
RESOURCES
•
STLE Metalworking Fluid Short Course, two-part online course. Available at
www.stle.org.
•
Byers, J. P., ed. (2017),
Metalworking fluids, third edition. Boca Raton: CRC Press Taylor & Francis Group.
•
Springborn, R. K. and American Society of Tool and Manufacturing Engineers. (1967),
Cutting and grinding fluids: Selection and application. Dearborn, Mich.: American Society of Tool and Manufacturing Engineers.
•
Drozda, T., Wick, C., Benedict, J. T., Veilleux, R. F., Bakerjian, R. and Society of Manufacturing Engineers. (1983),
Tool and manufacturing engineers handbook: A reference book for manufacturing engineers, managers, and technicians. Dearborn, Mich.: Society of Manufacturing Engineers.
•
Rossmoore, H. W. (1995),
Handbook of biocide and preservative use. London: Blackie Academic & Professional.
•
Oberg, E. and Green, R. E. (1996),
Machinery’s handbook: A reference book for the mechanical engineer, designer, manufacturing engineer, draftsman, toolmaker, and machinist. New York: Industrial Press.
•
Machinability Data Center (Cincinnati, Ohio (Etats-Unis)). (1980),
Machining data handbook: 1. Cincinnati: Machinability Data Center, Metcut Research Associates.
•
Metalworking fluids: Safety and health best practices manual. Occupational Safety and Health Administration (OSHA), Washington, DC. Available
here.
•
Mist control considerations for the design, installation and use of machine tools, American National Standards Institute (ANSI) Technical Report B11 TR 2-1997, New York, N.Y., 1997.
•
Coromant, S. (1996),
Modern metal cutting: A practical handbook. Gimo: Sandvik Coromant.
•
Salmon, S. C. (1992),
Modern grinding process technology. New York: McGraw-Hill.
•
Sandvik Coromant training handbook: Metal cutting technology. Available at
www.sandvik.coromant.com.
•
Schey, J. A. (1983),
Tribology in metalworking: Friction, lubrication, and wear. Metals Park, Ohio: American Society for Metals.
•
Vocational Information Center, Machining tutorials. Available at
http://khake.com/page88.html.