KEY CONCEPTS
•
Hydrogen fuel cell electric vehicles (FCEVs) and hydrogen internal combustion engines (H2- ICEs) are not new technologies, but it is the first time they are going into mass production with multiple units already in the marketplace.
•
Hydrogen-powered and battery electric vehicles (BEVs) will complement each other rather than compete against each other.
•
Modularity and standardization are key to reducing complexity and increasing flexibility to mass production, getting volumes up and costs down.
•
There are different fluids, lubricants and greases used for FCEVs and BEVs, and also for H2-ICEs versus other types of ICEs.
It is not the first time the world is experiencing a lot of attention drawn to hydrogen-powered vehicles. Although the first hydrogen-powered applications were developed back in the early 1800s, scaled usage began in the 1960s and through the 1970s driven by the Space Race when hydrogen fuel cells were mainly used in aerospace. The second wave of attention came in the early 2000s when U.S. President George W. Bush’s hydrogen fuel initiative envisioned the transformation of transportation fleet from a near-total reliance of petroleum to a steadily increasing use of clean-burning hydrogen. As we fast forward to today, it wasn’t until just a few years ago that many nations started working together on advancing R&D and deployment of hydrogen production once again. With many resources being dedicated to the storage, transport and end-use technologies with an important focus on “green hydrogen,” perhaps the third time around, hydrogen will be here to stay.
In this article, fluids and lubricants used in hydrogen-powered vehicles along with testing considerations will be discussed. Industry experts have shared their knowledge to propel innovative thinking on how to combat challenges to enable an emissions-free future as an industry together. The following key industry experts were contacted to obtain their expertise on fluids and greases for hydrogen-powered vehicles:
1.
Dr. Gareth Fish, The Lubrizol Corp.
2.
Dr. Christopher Cleveland, Afton Chemical
3.
Dr. Peter Lee, Dr. Graham Conway and Dr. Thomas Briggs, Southwest Research Institute (SwRI)
4.
Pierpaolo Antonioli and Alberto Vassallo, PUNCH Torino
5.
Dr. Raynald Gallant, Volvo Construction Equipment (Volvo CE)
6.
Dr. Gareth Moody and Nicholas Weldon, Croda
7.
Dave OudeNijeweme, Advanced Propulsion Centre (APC) UK
8.
Alexander Schnabel and Damian Bloomfield, AVL List GmbH.
Why hydrogen?
Hydrogen (H2) is an alternative fuel that can be produced from diverse domestic resources.
1 Although the use of hydrogen in transportation fleet is still in early stages, academia, industries and governments are working together to implement a safe, economical and clean “green hydrogen” production, which is planned to affect H2 internal combustion engines (ICEs) and fuel cell electric vehicles (FCEVs).
In certain regions around the world, light-duty H2 FCEVs are already being used in limited quantities. There is a particular interest in hydrogen applications for medium- and heavy-duty trucks, material handling equipment, buses, marine vessels, stationary equipment (such as generators) and material handling equipment. The hydrogen internal combustion engine (H2- ICE) market is rather niche, and although it is too early to indicate its full potential, compared to H2 FCEVs, they may be more optimal for medium- and heavy-duty applications, such as off-road equipment, due to the demands and cost that are considered in off-road job sites.
According to Dr. Gareth Moody, research and technology specialist, and Nicholas Weldon, technical marketing manager, Croda, “It still seems to be too early for the dominance or a particular application. All areas remain relatively small, and the next five to 10 years probably will reveal which applications will prevail. A prediction is that heavy-duty on-road applications seem to be a good fit for fuel cell technology.”
STLE member Christopher Cleveland, technical director, Afton Chemical, concurs: “Hydrogen fuel cell is likely to be suited more to long haul trucks as refueling is relatively quick, comparable with diesel, and range will be similar. The key thing is that the infrastructure needs to be in place—renewable energy generation, water electrolysis to produce the H2 as well as storage and transportation infrastructure. This will take at least seven to 10 years to put into place.”
Dave OudeNijeweme, head of technology trends, APC UK, adds: “Majority of applications for hydrogen combustion engines will be in the heavy-duty space.” He adds, “If nothing else, it’s a really good transition to net-zero technology, because legislators in both the UK and Europe are actively considering zero-tailpipe emissions.”
“We are moving from tail-pipe to net zero quite quickly. The mobility sector is changing its energy sources, moving from fossil fuels to renewables. Sustainable fuels are still quite expensive, mostly because of the inefficiency with their production. Current focus is on hydrogen and battery electric powered vehicles. Hydrogen is a good energy carrier, and its combustion is in principle a quick mechanism to convert energy into movement and power. For hydrogen fuel cells there is still a big cost curve to go through, but they look to become competitive relative to diesel and battery technology, on a total cost of ownership basis, for trucks in the 2030-2040 timeframe.
STLE member Dr. Peter Lee, staff engineer and chief tribologist; Dr. Graham Conway, principal engineer; and Dr. Thomas Briggs, staff engineer; Southwest Research Institute (SwRI), known as the team of scientists at SwRI in this article, concur: “The primary demand [H2 FCEV] is for on-road heavy-duty vehicles. That sector is not easily repowered with batteries but is most amenable to the changes required for hydrogen fuel cell power. There is some interest in the rail sector as well, though it is not clear how much of the locomotive fleet can be repowered with fuel cells at this time.”
Dr. Raynald Gallant, head of product management and productivity, Region America, Volvo Construction Equipment (Volvo CE), says that electric and hybrid options for heavy equipment such as excavators and wheel loaders have been available for a while, but it is uncertain if the off-road equipment industry will embrace hydrogen fuel yet
(see Figure 1). So far the battery electric option has shown a great adoption for compact and medium size machines. For larger machines, there are hybrid solutions available that focus on hydraulic efficiencies, drastically reducing fuel consumption and, thus, emissions. Gallant says, “Battery electric machines work well in urban construction applications where compact products play a key role, especially in areas that require low decibels and zero emissions. However, the weight and size of batteries are too impractical for heavier construction equipment, and at this moment, they do not meet job site expectations, especially if the machines require high cycle/duty work hours. For this reason, hydrogen is a promising alternative for the off-road industry.”
Figure 1. Share of assets (off-road machines, buses and trucks). Figure courtesy of Volvo Group.
He continues: “The cost of servicing hydrogen-powered machines, disposal of new elements such as fuel cells and the hydrogen infrastructure still remain major concerns that the industry needs to better understand.”
FLUIDS, LUBRICANTS AND TESTING CONSIDERATIONS FOR H2 FCEVS
Fuel cells are the most energy efficient devices for extracting power from different fuels, such as hydrogen, due to the conversion of chemical energy in hydrogen to electricity using pure water with potentially useful heat as the only byproducts.
2 Hydrogen-powered fuel cells are not only pollution free but also can have more than two times the efficiency of traditional gasoline combustion technologies in the U.S. market.
2 Both FCEVs and hydrogen ICEs offer competitive powertrain efficiencies, which can be optimized depending on the application.
FCEV heat transfer fluids The main types of fluids used in FCEVs are heat transfer fluids (HTFs), greatly discussed in detail in a previous TLT article.
3 Additionally, it is important to mention few critical points.
According to Alexander Schnabel, development engineer PEM systems, AVL List GmbH: “Cooling of low-temperature proton-exchange membrane (PEM) fuel cell vehicles is very challenging. Compared to conventional ICEs with the same power available for driving, usually larger radiators and coolant pumps are needed. This is due to the fact that nearly all the generated heat has to be dissipated by the cooling system, and only a very small fraction is transferred via exhaust gases. Additionally, the temperature difference between the coolant and ambient is lower. The maximum operating temperature for low-temperature PEM fuel cells is about 90-95 C, which must not be exceeded. Whereas in ICEs, the maximum allowed temperature for critical operating conditions is about 120 C.”
Schnabel continues: “A very central topic in the design of PEM fuel cell systems is material compatibility. This is not only of crucial importance for the gas paths but also for the coolant path. As the coolant passes live parts within the fuel cell stack (i.e., flow channels within the bipolar plates), it has to be electrically nonconductive. Therefore, every wetted material within the coolant loop has to be checked for material compatibility with the goal that the extraction rate of ionic species has to be as low as possible. Typical values for electrical conductivity of coolants are < 5 μS/cm at 25 C. The exact upper limit of the coolant conductivity usually is defined on a system level and is an aspect of design (i.e., geometry of coolant passages and their “connection” to the first grounded parts within the system). On the one hand, these challenges must be addressed by selecting the appropriate components and materials. On the other hand, the selection of proper cooling fluids also will have an impact on the cooling system design and performance.”
Moody and Weldon say: “The sensitivity (and extremely low conductivity requirements) of a fuel cell system must be taken into account and may dominate decision making. All this must be done whilst minimizing the number of cooling circuits within a vehicle. Properties that must be considered include low viscosity, high specific heat capacity, thermal conductivity, good material compatibility and a very low electrical conductivity. There are some chemistries typically used to develop HTFs such as a standard ethylene glycol-based system, which has excellent thermal properties but high electrical conductivity. These fluids must be kept away from sensitive components requiring engineering solutions such as jacket or plate cooling with an ion removal system to maintain low electrical conductivity. From what we understand, there appear to be two different systems within a FCEV: the ‘standard’ coolant that is used with coldplate cooling solutions and a separate ‘special’ coolant with very low conductivity for cooling the fuel cell stack itself.”
Schnabel says: “With regards to cooling performance, pure water would be the ideal cooling fluid. However, it will freeze at temperatures below 0 C and won’t provide corrosion protection for metals. In fuel cell vehicles today, mixtures of monoethylene glycol and deionized water are used. These usually contain several additives to improve its properties with regard to corrosion protection of metal parts and, therefore, to minimize release of ions from corrosion reactions. Stainless steel, aluminum, copper and brass shall be covered by these corrosion inhibitors. Nevertheless, most of these cooling systems have ion exchangers included to catch possible released ions and maintain low conductivity values. Special fluids are available, which contain nanoparticles that aim to replace the function of the ion exchanger and have better heat transfer properties. However, these fluids still require further development before use in practical applications.”
Schnabel adds: “Depending on the exact application (e.g., agricultural), the toxicity level of the commonly used ethylene glycol might be an issue. In this case, propylene glycol will be a possible option, although it is more expensive and its cooling capabilities are worse because of its higher viscosity.”
Moody and Weldon add: “Fuel cell vehicles won’t need to consider fast charging as batteries do, so battery needs require far less cooling versus in a battery electric vehicle (BEV). FCEVs need to accomplish motor and fuel cell cooling collectively. A lot of the future requirements will revolve around fuel cells and the type (its size and output) used.”
Pierpaolo Antonioli, CEO and board chair, and Alberto Vassallo, technical specialist, combustion systems, PUNCH Torino, say: “Fuel cell fluids are mostly intended for cooling purposes. In typical automotive solutions, coolant flows through fuel cell bipolar plates. For this reason, coolant development is intended to improve both heat removal and dielectric characteristics to avoid creating short-circuit inside the fuel cell stack system.”
They add: “There is no specific lubrication required in fuel cell balance of plant (BOP), with the exception of the air compressor. In this case, in order to avoid contamination of the cathodic air, the technological trend is toward utilizing air-suspended bearings for the compressor shaft.”
OudeNijeweme concurs: “If the filtration of the air is not good enough, any dirt going into the fuel cells can affect the technology. Another issue is the removal of heat due to heat transfer being a lower temperature oxidation process, making the life span of the fuel cells a concern.” He continues: “The other area is DC/DC conversion of the energy to electricity, which is complex. From a technical side, there are no issues that engineers are not able to overcome, but commercially there are multiple concerns at this moment.”
Schnabel says, “One of the key challenges of the coolant is its degradation. Degradation of glycol coolants can be caused by oxygen, temperature stress (on surfaces or generally when operated at high temperatures) or catalytic activity of metals within the coolant path. The observed effect is oxidative degradation of glycol into acidic components. As counter measures, additives for controlling pH value, corrosion protection and antioxidants are used.”
Requirements for testing
Schnabel says: “Qualification and testing of fuel cell coolants will typically include stability/durability tests at elevated temperatures. During these tests, several parameters like temperature and electrical conductivity shall be monitored. After the tests, analysis of pH value and concentration of breakdown acids might be measured, next to other possible analyses. Additionally, corrosion testing or hot surface corrosion tests (ASTM D4340) with various metals is recommended.”
FCEV driveline fluids
Current requirements for driveline applications in FCEV are very similar to BEVs, which were also discussed in great detail in a previous TLT article.
4
Schnabel states: “A FCEV is very similar to a BEV, as they are electrically driven vehicles. Except for the fuel cell coolant loop, there also will typically be a coolant loop for power electronics/e-motor and a separate coolant loop for the high-voltage battery. If the air conditioning system is included, there might be four separate cooling loops in FCEVs.”
Cleveland concurs: “Typically the fuel cell will supply electricity to a smaller battery, probably still lithium ion, and the battery will power the e-motor. So, from a lubricant perspective, it will be similar to a BEV. There will, however, be coolant required for fuel cell as well as the battery, and also for wet e-axles fluids with sufficient gear and bearing protection whilst being compatible with the electronics and e-motors and provide sufficient cooling capability.”
Moody and Weldon conclude: “The evolution from standard automatic transmission fluids to fluids for hybrid and BEVs has seen a huge reduction in electrical conductivity of the fluids and a shift to higher thermal conductivity with better material compatibility to materials such as copper. However, these fluids are not sufficient for fuel cell driveline applications.”
Requirements for testing
Industry experts state that there is no significant difference in the driveline fluids testing required between BEVs and FCEVs. Cleveland says, “The focus will be on mechanical protection (gear load carrying, bearing protection), materials compatibility (copper and electronics protection, seals and coatings protection), high-speed foam and aeration control and, finally, on thermal properties and viscometrics and their impact on efficiency.
The more significant transition over the past few years has been from traditional transmission fluids to the electric drive fluids (EDFs) for BEVs. So, the fluid performance needs for FCEV fluids will basically match those for BEVs.
SwRI’s team agrees: “The hydrogen FCEV is essentially a battery-powered vehicle as the fuel cell is a steady-state device that maintains battery charge like a range-extender hybrid.” Regarding considerations for the FCEV versus ICE driveline: “The primary issue will be how the electric motors are integrated. For a transmission or axle with the electric motor inside the gear casing, the fluid must be suitable for high voltages. The STLE Tribology and Lubrication for E-Mobility Conference in November 2021 showed that there are a number of concerns regarding electric vehicle (EV) fluid testing and no real tribology testing capabilities.”
FCEV grease
EV greases were greatly discussed in detail in a previous TLT article.
5 There are few factors to consider when selecting a grease for FCEV applications versus BEVs. For example, Moody and Weldon say: “FCEVs require special EV driveline greases to cope with electrically induced wear.”
STLE Fellow Dr. Gareth Fish, grease technical Fellow, The Lubrizol Corp., outlines the following perspective: “The biggest difference that I can see is the weight of the propulsion system in battery-powered EVs is much higher than the weight of the hydrogen gas and cylinders and fuel cells. The hydrogen gas cylinders will be made of carbon fiber composites, which is much lighter than traditional steel tanks and not as prone to hydrogen embrittlement. 6.3 kg of hydrogen supplied into a fuel cell can produce about 95 kWh of electricity. One midsized production vehicle with fuel cells weights approximately 4,000 pounds (1,800 kg) and has a range of about 380 miles.”
He continues, “A similar sized production BEV with a 100 kWh battery pack weights approximately 4,900 pounds (2,200 kg) and has a range of 370 miles. The hydrogen tank in the FCEV weighs about 260 pounds (120 kg) compared to the weight of the BEV battery pack that weighs 1,050 pounds (480 kg). A similar sized ICE-only vehicle would weigh about 4,000 pounds (1,800 kg), and the hybrid versions would weigh about 4,800 pounds (2,100 kg), similar to that of the standard BEV. FCEVs are a better bet for longer distance EVs as extra or bigger hydrogen tanks are a lower price add-on compared to adding more batteries. So, in terms of componentry and greases, things like wheel bearings, steering systems and transmission joints would need to be beefed up for the extra weight of the BEV but would not need to be beefed up for a FCEV and could be similar to ICE. For both FCEVs and BEVs, in the longer term, energy efficient greases would be needed.”
Schnabel says: “Any material which is used within the balance of plant components of a fuel cell system needs to be checked for its material compatibility. Certain species (which might be extracted from these materials) are known for being harmful to the fuel cell stack. These contaminants can have several origins and are summarized in Table 1. Mainly the gas paths components (e.g., catalyst layer, membrane, gas diffusion layer, etc.) within the fuel cell stack are affected. But (as described previously), the coolant path also can be affected if ions are released. The list of contaminants also includes oils from compressors and indicates the reason why compressors with air bearings often are used for FCEVs. However, proper design of compressor bearing or selection of media for lubrication also might solve this issue. For example, polytetrafluoroethylene-based lubricants/greases are typically used as assembly aids for fuel cell systems. But a closer look has to be taken on the exact amount that is used and that might accumulate within the stack over lifetime. Testing of greases and other assembly aids usually is conducted by hot water extraction tests where test samples are put into deionized water at elevated temperature, and the extract solution is analyzed subsequently.”
Table 1. Major contaminants identified in the operation of PEM fuel cells6
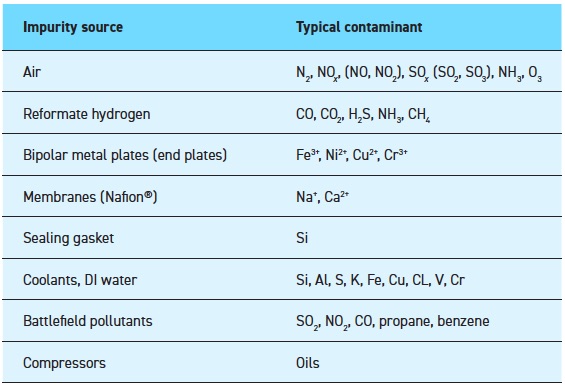
LUBRICANTS AND TESTING CONSIDERATIONS FOR H2-ICE
Piston (reciprocating) engine The ICE is an engine in which the combustion of a fuel occurs with an oxidizer (usually air) in a combustion chamber.
7 In an ICE, the expansion of the high-temperature and high-pressure gases produced by combustion apply direct force to some component of the engine.
7 The term ICE usually refers to an engine in which combustion is intermittent, such as the more familiar four stroke and two stroke engines, along with variants, such as the six-stroke piston engine and the Wankel rotary engine.
7 A second class of ICEs use continuous combustion: gas turbines, jet engines and most rocket engines.
7 There were many designs of ICEs built throughout the past years.
Recent regulations on exhaust emissions have led the industry to seek “green” fuel options to power ICE applications. As mentioned previously, hydrogen seems to be the most suitable solution. In a hydrogen ICE, hydrogen and air burn through an ignition spark. From the combustion characteristics, it can count on very high efficiency and low polluting emissions (NO
x), also allowing the use of ultra-lean (air-fuel) mixtures. There are several differences between diesel/gas and H2-ICE engine types, mainly related to design and structural materials used.
For example, during piston engine operation, the exhaust gases entering the crankcase can condense when there is no provision of proper ventilation.
8 Water mixing into the crankcase’s oil (lubrication oil) reduces its lubrication ability, and, as a result, there occurs a higher degree of engine wear.
8
The main challenges to consider when selecting an optimal engine oil for H2-ICE, according to Damian Bloomfield, skill team leader, mechanical development and validation, AVL List GmbH, are: “With hydrogen engines, there are characteristics of the combustion system, the lubrication system as a whole, as well as the blowby and breather systems, which all contribute to the oil performance. The very nature of hydrogen combustion means that its impact on lubricity as well as longevity is an ongoing effort together with oil concerns to review and optimize additive packages. Water content in oil, especially with hydrogen engines, requires careful development and consideration due to the impact on functional operation and especially bearing performance and lifetime. Friction reduction remains a necessary continuous development with respect to oil specifications as well as the design and validation of the engine.”
Cleveland explains: “Hydrogen burns hotter than gasoline or diesel, so it may be necessary to cool the combustion chamber with water injection into the combustion chamber. This is a proven technology but may lead to corrosion and oil emulsion problems. High temperatures of combustion could stress antioxidation performance and affect useful life of the oil.”
Moody and Weldon concur: “For H2-ICE, fluid longevity will be an issue. Emulsification of oils or polar additives leaching into aqueous layers could be a huge problem. Water evolution in the engine is likely to accumulate in the sump. Certain additives could emulsify this water into the oil, leading to problems or possibly even critical issues as the water will accumulate and sit in the sump causing corrosion problems. This will be made worse in vehicles that see little use where water is not evaporated off.”
Moody and Weldon continue: “Because engine oil longevity is a big unknown, field trials will be required. Heavy-duty engine oils have a massive drain interval. Maintaining this with hydrogen technology will be a huge challenge. Parts longevity in heavy-duty and off-road applications also will be a huge challenge. Future fluids will need better component protection for basic things such as corrosion.” OudeNijeweme adds: “There are concerns on lubricants and how they deal with hydrogen coming past the piston rings into the crankcase, whether the hydrogen may get absorbed into the lubricant and become contained within the crankcase, so there will be a need to have a lot of ventilation embedded into the engine design to prevent trapping of any hydrogen, preventing entrance in the engine where one doesn’t want it—as it may spontaneously combust, which is a major safety issue.” He also agrees with other industry experts: “Water has always been a problem for engines. Every time you stop the engine, there’s a water ingress past the piston rings condensing in the crankcase, so there will be potentially more water, too.”
OudeNijeweme also says that it is likely H2-ICE will have a unique lubricant developed for it, and testing requirements also still need to be developed. “OEMs are considering durability and longevity; they are running long cycles to meet market demands and customer expectations,” he says.
Antonioli and Vassallo also concur: “H2-ICEs pose unique challenges to engine lubricants because of the specific properties of the H2 fuel and its combustion products, mainly, the high content of water. Among the oil properties, there are a few important ones to “tune” for hydrogen that they list:
•
Suppression of preignition, due to the H2 high sensitivity to this combustion anomaly.
•
Very high chemical stability to hydrogenation, resistance to mixing with water and formation of white sludge.
•
Finally, since hydrogen is a dry fuel, oil needs to provide lubricity whilst reducing depositable material (soot).
In conclusion, Antonioli and Vassallo add: “Let’s not forget that oil is the only source of particulate in H2-ICE—therefore its consumption should be minimized as much as possible to improve the sustainability of this proposition.”
Antonioli and Vassallo say: “In the field of lubricants technology for H2-ICE, we believe that sustainability will play an ever-increasing role with respect to today, starting from recycled lubricants to biolubricants to e-lubricants (synthetic oils derived by CO
2 capture and renewable electricity).” As far as future requirements, there are still important challenges to work through. Antonioli and Vassallo say: “We would highlight the need for oil compatibility with the aftertreatment system that H2-ICE may need for some heavy-duty lean-burn applications directed to very strict environmental standards. Finally, we are convinced that the oil, which will be used for H2-ICEs, should be developed in such a way to be back-compatible with existing engines, thus, facilitating the successful commercial introduction of this new sustainable propulsion system.”
Testing requirements
Antonioli and Vassallo state: “It is important to highlight that oil compatibility to hydrogen needs to be verified at the beginning of the engine development phase because H2 combustion is sensitive to oil properties as explained previously and, therefore, can influence the combustion process. This is not what typically happens with diesel, and to a lesser extent with gasoline and compressed natural gas.”
Bloomfield says, “The targets for the functional and durability development of the ICE continually evolve, and for the hydrogen engine it is no different. However, the robustness growth of the engine in the development phase is paramount so that the engines can be brought into the market faster and/or with improved reliability. Therefore, applying a robust validation methodology toolbox means that an optimal testing program can be defined within a given testing time framework. This means that by understanding the main failure parameters, the lubricating system, as well as other systems and components of a hydrogen engine, can be successfully validated as required and in time.”
Summary
The future of hydrogen technology depends largely on legislation, hydrogen’s “from cradle-to-grave” sustainability, infrastructure, robustness of components and total cost of ownership to end-users.
We should not overlook that not only applications discussed previously will call for a new fluid technology but also the applications themselves will go through numerous advances, i.e., a hydrogen-powered engine can be of a hybrid technology, dual-fuel or new design type, and not only powertrain but driveline components will be impacted as well.
There is no doubt that zero-emission power alternatives are on the horizon for all vehicles. The momentum is definitely accelerating along the entire value chain while the economy of scale is reducing the cost. So perhaps the third time is the charm?
REFERENCES
1.
U.S. Department of Energy (2022), “Alternative Fuels Data Center: Hydrogen basics.” Available
here.
2.
U.S. Department of Energy. (2015), “Fuel cells facts sheet. Available
here.
3.
Canter, N. (2021), “Heat transfer fluids: Growing in visibility and importance,” TLT,
77 (12), pp. 28-40. Available
here.
4.
Rensselar, J. (2021), “Driveline fluids for electric vehicles,” TLT,
77 (8), pp. 42-47. Available
here.
5.
McGuire, N. (2021), “The electric vehicle grease industry finds its bearings,” TLT,
77 (11), pp. 32-40. Available
here.
6.
Cheng, X., Shi, Z., Glass, N., Zhang, L., Zhang, J., Song, D., Liu, Z., Wang, H. and Shen, J. (2007), “A review of PEM hydrogen fuel cell contamination: Impacts, mechanisms, and mitigation,”
Journal of Power Sources, 165 (2), pp. 739-756.
7.
Patadiya, V. N. and Bhatt, V. (2014), “Performance analysis of two stroke SI engine with methanol blending,”
International Journal of Engineering Sciences & Research Technology, 3 (2).
8.
Fayaz, H., Saidur, R., Razali, N., Anuar, F. S., Saleman, A. R. and Islam, M. R. (2012), “An overview of hydrogen as a vehicle fuel,”
Renewable and Sustainable Energy Reviews, 16 (8), pp. 5511-5528.
Dr. Yulia Sosa is a freelance writer based in Peachtree City, Ga. You can contact her at dr.yulia.sosa@gmail.com.