LANXESS
Additives and Synthetic Base Oils Designed for E-Mobility Lubricants
By Mary Moon, Presque Isle Innovations, LLC | TLT CMF Plus November 2021
Battery electric vehicles (BEVs) are reshaping the landscape of automotive lubricants. David Stonecipher, Head of Business Development of the Lubricant Additives Business (LAB) at LANXESS, anticipates that the requirements of new hardware plus growing acceptance of BEVs will produce strong growth in sales of specialized driveline fluids and battery coolant fluids.
LANXESS is prepared to work with lubricant blenders and automotive OEMs to customize components for novel fluids for e-mobility applications. LANXESS (Cologne, Germany) is a leading global supplier of more than 660 synthetic base stocks, additives and fully-formulated lubricants to over 800 customers worldwide. The lubricant additive portfolio includes antioxidants, detergents, anti-wear compounds, extreme pressure additives, corrosion inhibitors, friction modifiers and industrial additive packages. The synthetic base stock portfolio includes synthetic esters, phosphate esters and high viscosity polyalphaolefins (PAOs).
Battery Thermal Fluids
Travis Benanti, PhD, Technical Manager and Head of LAB Process Development, explains that BEVs have unique and critical needs for battery coolant fluids. “Most BEVs use Li-ion batteries or cells, similar to those in cell phones and laptops but differing in size, shape, and the number of cells required. For example, some automotive OEMs are using cylindrical Li-ion cells that resemble AA batteries, while other OEMs prefer batteries in a thin rectangular shape (prismatic). Many cells are connected together and packaged in a protective housing. Since the complete assembly is large and heavy, automakers often put it underneath the floor, as shown in
Figure 1. OEMs need to use enough cells to power a vehicle over a long distance, but battery weight and cost are the trade-offs. At present, there are no universal standards for BEV battery pack design, so there is a lot of activity in this area.
Figure 1. E-mobility lubricant applications
“One thing is certain: Li-ion batteries are sensitive to heat. For long life and reliability, it is essential that Li-ion batteries operate in their optimum temperature range of approximately 15-35 °C (60-95 °F). Their maximum tolerable temperature is around 60 °C (140°F), and Li-ion batteries undergo irreversible damage and break down near 90 °C (195 °F). Ambient temperature is a factor but not the biggest concern, except in extreme climates. Rather, the heat generated during battery charging and discharging is problematic because many Li-ion cells are packed tightly together in a sealed box. At present, most hybrid EVs circulate air or use natural convection for cooling because those battery packs are small. BEVs, on the other hand, have much larger batteries, and most circulate water-glycol mixtures through a system of pipes and heat exchanger—similar to a refrigeration system—to cool the Li-ion cells, as shown in
Figure 2. These two methods are fine, for now.”
Figure 2. Battery cooling concepts
But, according to Benanti, “Consumers are demanding BEVs that can be driven farther between charges and recharged quickly. OEMs are responding by using more Li-ion cells and higher voltages and currents to allow faster recharging. These trends mean increases in the rate of heat generated while fast-charging Li-ion batteries. Current methods of cooling Li-ion batteries may not be sufficient in future BEV configurations where charging may take only 20-30 minutes. Sure, most owners will probably be able trickle-charge their BEVs overnight, but having the option to fast-charge gives drivers peace of mind and makes BEVs suitable for longer trips.
“Direct cooling by immersing Li-ion batteries in a heat transfer fluid is an emerging trend that shows promise for the future. Immersion cooling can provide more uniform battery temperatures, higher cooling capacity, and faster recharging without overheating the cells. But success depends on the quality of the heat transfer fluid. The general target is to make heat transfer fluids with low viscosity and good thermal properties without causing material incompatibility or safety issues. This means formulating heat transfer fluids from appropriate lower viscosity base oils and the right combination of antioxidants, yellow metal inhibitors, and anti-foam additives.
“When choosing a heat transfer fluid or its components, here are several important considerations:
• Low viscosity and pour point
• High heat capacity and thermal conductivity
• Low electrical conductivity and high breakdown voltage
• High flash point and low flammability
• Compatibility with metals, plastics, and elastomers
• Environmental profile: non-hazardous, biodegradable, and recyclable
“Ester base oils are a good choice for immersion cooling fluids because they meet the above criteria. Hatcol® esters have long been used in demanding applications such as aircraft turbine engine oils, and they facilitated the switch to environmentally friendly refrigerants. Some of our lower viscosity Hatcol® esters tick all the boxes for BEV applications, which is exciting.
“We produce several ester base oils with low viscosities, high flash points, and low pour points
(Table 1). Many of our synthetic ester base oils are biodegradable, and some are fire-resistant.
Figure 3 shows that the thermal properties of our polyol esters (
red) and diesters (
black) are superior to those of 2 cSt PAO (
- - - ) and 4 cSt Group III (
- - - ) base oils. Importantly, if these product recommendations don’t match a customer’s needs, we’ll collaborate with them to develop a new base oil for immersion cooling.
Table 1. Lower viscosity Hatcol® ester base fluids
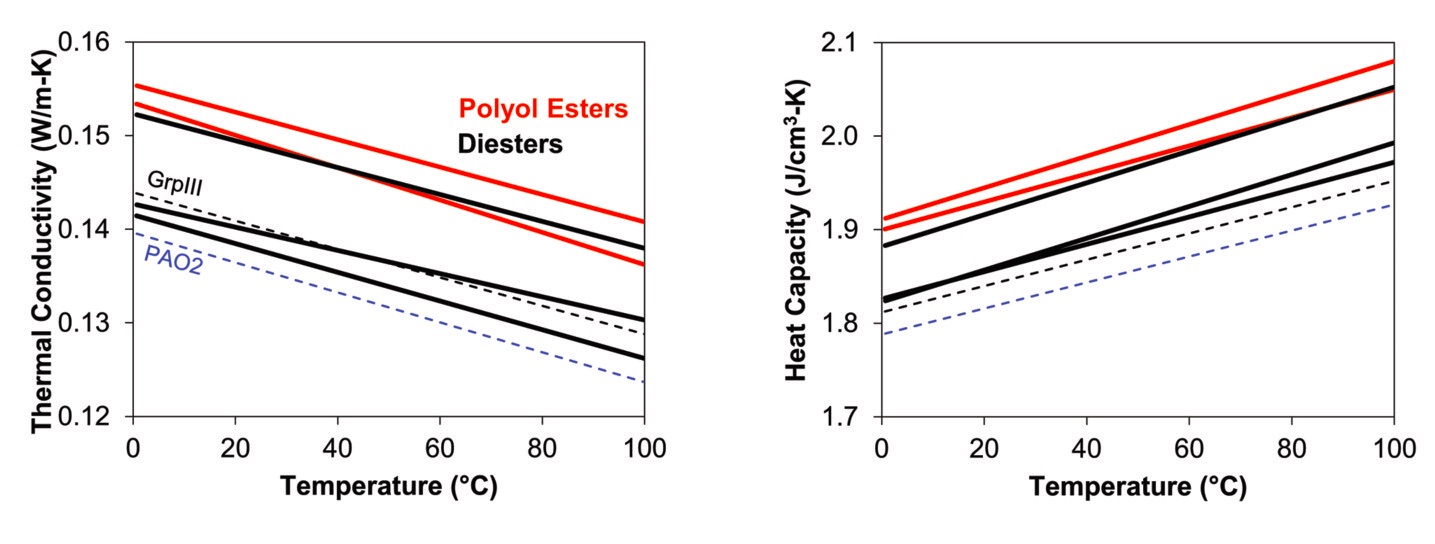
Figure 3. Thermal properties of Hatcol® esters, a low viscosity PAO and a Group III mineral oil
“In addition, LANXESS additives can provide essential performance for immersion cooling applications, protecting both fluids and vehicle components. For example,
Figure 4 shows that small amounts of Additin® triazoles effectively protect copper surfaces like those in BEVs and keep them bright and corrosion-free. Meanwhile, LANXESS phenolic antioxidants, such as Naugalube® 531, are well-suited to ensure long fluid life in BEV battery cooling applications. Additin® 8239 and Naugalube® 531 are liquids at room temperature, which makes blending easy, and both are on the EU EcoLabel LuSC list.
Figure 4. Effectiveness of Additin® yellow metal inhibitors in Hatcol® ester base fluids
E-driveline Fluids (or e-Driveline?)
According to Steffen Sandhoefer, PhD, LANXESS Germany GmbH, one of the newest innovations is a “booster package” for automotive lubricants. He explains, “We see the main challenge for EV drivelines to be achieving a balance between decreasing wear and preventing copper corrosion. Both performance properties are critical to vehicle efficiency and range as well as fluid longevity. Furthermore, it is necessary to achieve this difficult balance in not one or two but dozens of commercial transmission and driveline fluids. By topping up with additives, it is possible to boost the EP/AW performance of existing fluids and make them suitable for future BEV applications. Our approach saves OEMs and lubricant suppliers from formulating new transmission fluids from scratch.
Sandhoefer explained, “There are many good lubricants on the market. But it’s not clear how well they will perform under particularly harsh operating conditions in next-generation EVs. “Wet” BEV designs are already in use, where OEMs typically use standard automatic transmission fluids (ATFs) for these applications, as shown in
Figure 5. We are confident that wet e-drivelines will dominate in the future, and the operating conditions will be more severe (higher temperatures, voltages, currents, and gear box speeds). Moreover, there are expectations for fluids with longer, even “lubed-for-life”, service.
Figure 5. Wet eDrivelines may use a single fluid for the transmission and axles
“Looking ahead, BEVs will need transmission fluids with much greater thermal stability, heat transfer, and electric properties than current products. Current ATFs were developed to lubricate gear boxes and clutches, but OEMs are developing gear boxes that operate at increasingly higher speeds and do not have clutches. Fluids will be needed to provide even more protection from friction, wear and foaming in gear boxes plus be compatible with copper and insulating materials.
“Material compatibility is a major concern in wet designs. The transmission fluid will be in contact with the insulation protecting the copper windings of the e-motor. The current generation of transmission fluids are formulated with additives that are known to corrode copper. If the insulation fails, there is a risk that the copper windings will corrode, and the BEV engine will fail.
“Transmission fluids are formulated with extreme pressure and anti-wear additives to protect the gears in the driveline. OEMs need fluids that provide even greater protection for steel gears against friction and wear to improve vehicle range and engine efficiency. But OEMs also want fluids that minimize the risk of damage to insulation and copper corrosion and withstand high temperatures during rapid charging and discharging of the batteries.
“LANXESS focused on developing a new generation of EP additives that are less reactive toward copper and have better stability, to withstand high temperatures and provide long service life, than current additives. We harnessed the efforts of our 65 technical staff members who perform approximately 200 test methods in our four laboratories and technical centers around the globe. In addition to running the FZG scuffing and micropitting tests to test EP/AW additives for protecting gears, our staff developed three new tests specifically for wet e-drivelines: copper wire insulation (CuWIT), copper wire corrosion (CuWCT), and conductivity of lubricants (COLT).
“
Figure 6 shows our ’phase diagram’ of EP performance (FZG testing), copper corrosion and temperature stability. We have developed two booster packages, E 559 and E 560, to meet this target. Test data for fluids formulated with E 559 and E 560 are given in
Figure 6. LANXESS is ready to provide samples of both boosters for evaluation.
Figure 6. An EP/AW additive package for e-driveline fluids
“Working on these battery thermal and E-driveline projects has focused our attention on the future needs of the automotive industry for high-performance fluids that provide optimum performance for BEVs and set the stage for the development of lubricant standards for BEVs”, concludes Davison. LANXESS is proud to propose innovations in base fluids as well as additives for BEV fluids and looks forward to partnering with lubricant suppliers and automotive OEMS to realize the commercial potential of our products in these applications.