The value of lubricant cleanliness
Jeanna Van Rensselar, Senior Feature Writer | TLT Best Practices October 2021
Best practices for transferring oil from storage into use and keeping it clean in operation.
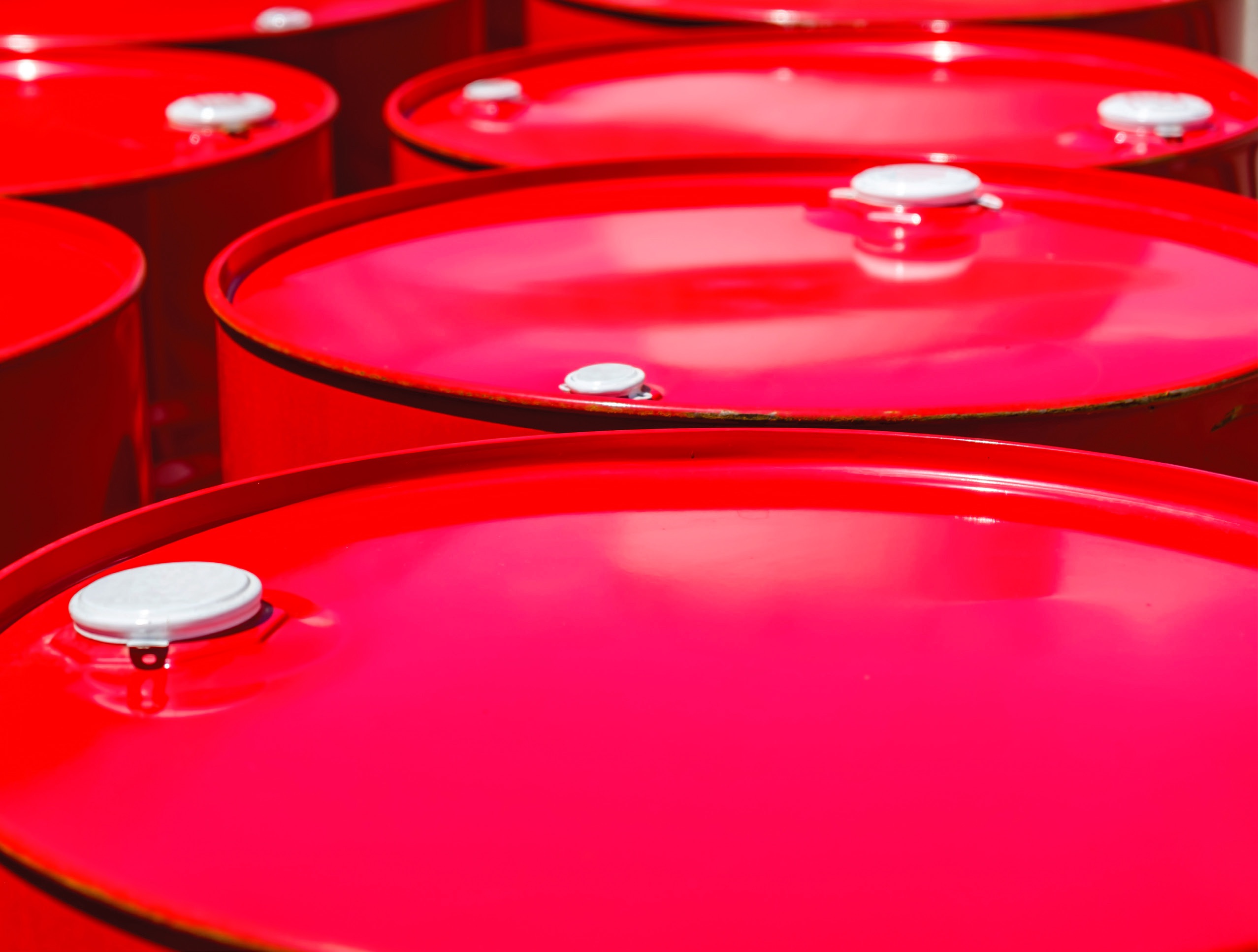
KEY CONCEPTS
•
Even the best, most costly lubricants can’t withstand the effects of contamination.
•
Lubricants need to be protected from contamination through the entire cycle—from production to transfer to storage to use.
•
A contaminated lubricant has many consequences, including false positive results with oil analysis.
While there is much emphasis on using the best lubricant for the application, keeping the lubricant clean during production, in storage, during the fill process and in operation is just as, if not more, important. In fact, one could make the case that it doesn’t matter how much the lubricant costs or what kind of additives it has if it’s laden with particles and debris.
STLE member Roger Young, CLS, senior field technical advisor for ExxonMobil’s Mobil Serv, explains, “It seems every company faces constant challenges regarding lubricant cleanliness and product integrity, but the issues can be very diverse depending on location, environment, procedures, culture, competency, tools/equipment and budget, just to name a few. I have some customers that prioritize lubricant cleanliness from the moment it arrives on site (or even before) until it is at end of life in the particular system it was intended for. Some other customers really struggle with the processes necessary to execute a good program, even though they generally understand the importance of it.”
Contamination from water, dirt, failure debris and incompatible oil can severely and detrimentally affect the useful life of the lubricant. Even fresh oil in the barrel can be dirtier than the used oil that is drained from the system.
Naimesh Vadhwana, maintenance planner supervisor, Kruger Products L.P., points to time, use, neglect and changes in temperature as causes of deterioration.
Several studies have shown that at least 75% of hydraulic system failures can be linked to oil contamination. For example, a Nissan Motors study concluded that 85% of hydraulic equipment failures can be attributed to contamination. In addition, over the course of five years, Nippon Steel found that a proactive contamination control and maintenance program delivered an 80% reduction in hydraulic pump replacements, and a 75% reduction in oil consumption. Research by the British Hydromechanics Research Association (BHRA) and National Engineering Laboratory, and research by Oklahoma State University, reported that when fluid is maintained in a clean state, hydraulic pump life can be significantly extended.
1
Contamination standards include the ISO 4406 Cleanliness Code, the NAS 1638 Cleanliness Standard, SAE AS4059, the Russian GOST Standard and the Navy Standard for Hydraulic Fluids.
Consequences of contamination and benefits of cleanliness
Lubricants aren’t just for lubricating; a secondary function is to remove contaminants from contact surfaces. “If the lube starts off unclean/contaminated, instead of removing generated debris, it can introduce debris, which can lead to premature failure, and, thus, increase costs,” Vadhwana points out. “As well, if a lube is unclean, it can block passages leading to blown seals, lead to lube and/or process contamination and even to process slowdown or shutdown.”
On the other hand, if the lubricant is maintained in a clean condition, it can do its job of removing dirt and debris and cooling contact areas. This results in streamlined functionality and extended machinery life.
Emlyn Eager, P.Eng, fleet maintenance engineer, BC Transit, observes, “If the lubricant you’re putting into your equipment isn’t clean, then there’s a good chance you’re going to introduce some premature wear and reduce the life of that component. This can obviously increase maintenance costs and increase the total cost of ownership of that equipment.”
Young believes that lubricant quality and cleanliness are so important that they are the foundation of a successful maintenance and reliability program. “If you have a brand new piece of equipment and fill it with poor quality, dirty lubricant and continue with this practice over time, you will never achieve Predicted Component Replacement (PCR) benchmarks no matter what other great things are happening within the maintenance/reliability department,” he says.
Consequences of contaminated lubricant
Young warns that contamination can affect the outcome of used oil analysis. “It can cause false positives, making the data hard to trend for equipment health checks. It is quite difficult to plan for repair outages and have sufficient spares available when equipment is wearing prematurely. This causes issues with production targets and can cause stress on maintenance departments.
“From a high level point of view, like any other maintenance best practice or process, if the program falls off the rails, bad things will eventually happen. The end result will be poor asset life, difficulty in planning for maintenance activities, disruptions in production and likely scrambling to make repairs without proper plans in place. This can add stress to the entire organization and ultimately affect the bottom line, which shareholders are always keeping a close watch on.”
Young continues, “On a more basic level, there are many potential issues that will slowly (or maybe very quickly) arise that will eventually lead to larger concerns (
see A Few Basic Guidelines). If bulk tanks or transfer containers are constantly compromised with dirty lubricants, they will build up with moisture and sediment that will never go away until a complete drain, clean and flush can be performed. This is a big commitment and can be difficult to perform without proper planning and mitigation to reduce the risk of run-out at site.”
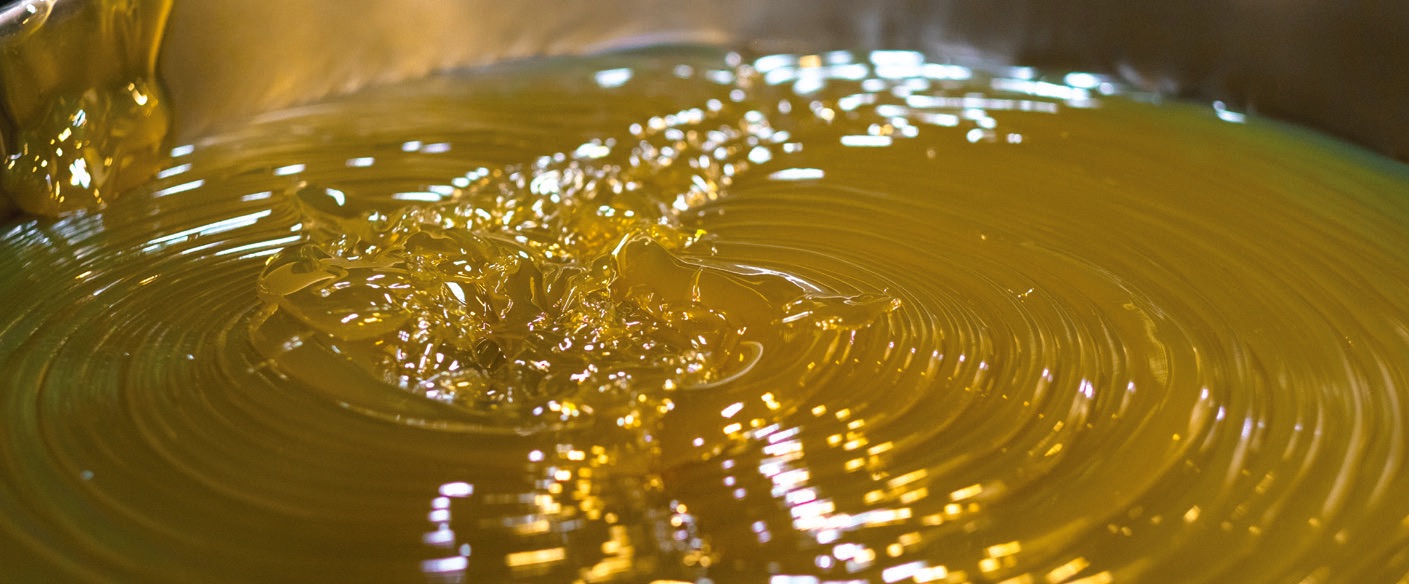
A few basic guidelines
From experience, Roger Young suggests a few rough guidelines for determining the level of contamination in a lubricant.
•
If particle(s) of contamination can be observed by the naked eye in a lubricant, it is severely compromised, and should not be used until it is properly cleaned. These visible particles are likely greater than 40 microns. For reference, ISO cleanliness codes address particles that are 4, 6 and 14 microns.
•
One particle of dirt will generate 5-20 new particles of dirt and wear metals. This process repeats itself exponentially unless caught in a filter.
•
In one year, an ISO 19/17/14 oil in a 50 gpm pump will circulate approximately 1,500 pounds of contaminant through the system.
•
Most rolling element bearings have a lube film thickness of 0.1-3.0 microns, so it is the extremely small particles that harm these components.
Vadhwana adds, “When lube cleanliness is ignored, failure rates can increase, leading to lower run time (as more time is spent on failure repairs) and, thus, increased cost. The failures can show up as premature wear of contact surfaces, increased temperatures at surfaces, as well as contamination.”
Benefits of lubricant cleanliness
Among the benefits of lubricant cleanliness that Vadhwana has witnessed are an increase in runtime, production and time spent on scheduled maintenance. There also are decreases in failures, unscheduled maintenance and overall downtime.
While Eager is currently working in the transit industry, his roots are in oil and gas and mining. He observes that robust lubrication programs are not as widely used in the transit sector. “With that being said, there is always a drive to reduce maintenance costs in any industry and to use better oils that provide better equipment performance, extend oil drains or maximize equipment life,” he explains. “Understanding equipment performance and condition using oil analysis also is a big part of our maintenance program.”
Lubricant cleanliness best practices
The cleanliness regimes for stationary and mobile equipment are similar but do vary to some degree. The fundamentals are to not introduce contaminants and to store lubricants at recommended temperatures.
Stationary equipment
Some of Young’s customers filter all drums of fresh product to a predetermined ISO cleanliness code and transport the lubricant in clean sealed transfer containers. They also use dedicated quick-connect fittings to enter the lubricant compartment for top-ups or oil changes. Young says this is considered a best practice—start clean and finish clean.
These best practice businesses use site glasses on all assets to prevent environmental ingress while checking fluid levels. They also incorporate the use of high quality desiccant breathers on all plant assets in order to keep moisture and particulate ingress to an absolute minimum. All critical assets are monitored with routine used oil analysis, and any problematic equipment is fitted with additional kidney loop filtration to keep contamination and wear metals in check.
Mobile equipment
Young says that it’s not uncommon for lubricant in bulk storage to get transferred to smaller storage facilities on site, lube trucks or even into pails or drums in order to service field equipment. “This creates multiple opportunities to introduce contamination, and each transfer needs to have a mitigation process,” he explains. “This often is accomplished by utilizing high-efficiency single pass filtration for each transfer, and ensuring each transfer tank is clean, dry and has proper breathers in place.”
He advises that lubricant flowing through any hose reel or wand in the shop, and any lube truck hose reels, should be filtered, and any alternate lube islands in the field also should have single pass filtration installed.
If using pails or drums, extra care needs to be taken to ensure a clean transfer, even though it may be difficult to achieve. The top of the container should be clean and dry, the funnel should be freshly cleaned, the container should only be opened when absolutely necessary, and the compartment should be closed as soon as the oil transfer is complete, Young says.
The use of dedicated quick connect fittings on mobile equipment also is encouraged, as well as sample ports, in an effort to keep exposure to a minimum. Some large compartments such as hydraulic systems, transmissions and differentials/final drives also will benefit from kidney loop filtration during preventative maintenance services, or even on-board 24/7 bypass filtration in some applications.
“All lubricants should be stored in a clean, dry, temperature-controlled environment,” Young warns. “If any of these three descriptors are not met, you likely are introducing contamination to your stored lubricants.”
Eager notes that the two key principles in lubricant cleanliness are sampling and filtration. “This doesn’t just mean on the equipment the lubricant is used in,” he says. “This includes bulk storage tanks, oil drums, etc. Anything lubricants are stored in for an extended period of time should likely be sampled to ensure there is no significant contamination or degradation of the lubricant.”
He adds, “Any storage containers also should be regularly inspected and maintained. Filtering between storage containers and prior to entering equipment also is key. Equipment manufacturers often have guidelines for acceptable levels of contamination or particulate in new lubricants entering equipment. This can help owners/operators to quantify the cleanliness of their lubricant storage and delivery systems. Keeping dispensing tools clean and well labeled also is key to ensuring the lubricant entering the equipment is correct, clean and not contaminated with other lubricants.”
Vadhwana advises, “Some ways that deterioration can be combated include increasing the monitoring of lubricants, shortening intervals between samples—thus catching changes early, increasing filtration to remove the larger particles and replacing a percentage of the lubricant during service with new lubricant.”
Conclusions
If leadership is on board for lubricant cleanliness, it encourages a culture of best practices. This means management needs to invest in human resources, training, tools, equipment and worker hours. “For many companies, change can be very difficult to initiate and execute,” Young says. “This is where training and knowledge are key; once employees understand the importance and result, the change has a much better chance of success.”
Eager concludes, “Without employing some of the basic principles to ensure that your lubricant is clean in your equipment and prior to entering it, your equipment will suffer regardless of how good your lubricant is. All the science and technology that goes into creating top-notch lubricants cannot save your equipment from dirty storage tanks, dispensing systems or components.”
REFERENCE
1.
Mačužić, I. and Jeremić, B. (2004), “Proactive approach to oil maintenance strategy,”
Tribology in Industry, 26 (1, 2). Available
here.
Jeanna Van Rensselar heads her own communication/public relations firm, Smart PR Communications, in Naperville, Ill. You can reach her at jeanna@smartprcommunications.com.