KEY CONCEPTS
•
Testing is an inevitable part of new grease formulation.
•
Specialty greases undergo more strenuous testing versus general purpose greases.
•
In-service grease testing delivers beneficial insights.
The history of lubricating greases dates back to ancient times. As early as 1400 BC, attempts were made to reduce axle friction in chariots. Analyses from axel hubs indicate that fat and lime were used to make a complex lubricant.
1 Yet, the current state of lubricating greases only has less than a century of history. The first patents were issued during World War II. Clarence E. Earle, a researcher with the U.S. Naval Testing Station, applied for patents on lithium soap grease.
1 Significance of his work can be seen still today; globally, well over 70% of lubricating greases produced are based on lithium technology.
2
According to its definition,
3 “Lubricating grease is a mixture of three main components: lubricating fluid, performance enhancing additives and thickener. The lubricating fluid can be petroleum-derived lubricating oil, any of various synthetic lubricating fluids or vegetable-based oil. The lubricating fluid is usually the majority component in the grease formulation. The additives are typically present in relatively low concentrations and are added to the grease to provide enhancement in one of multiple performance areas. The thickener is what sets grease apart from liquid lubricants. This component gives the grease the property of consistency, making the product semi-solid rather than liquid. Many different chemical compounds can be used to thicken grease.” The following definition has evolved from the initial earlier one in the 20th Century: “A grease is a lubricant which has been thickened in order that it remain in contact with the surfaces and not leak out under gravity or centrifugal action, or be squeezed out under pressure. Thus, a major practical problem is the provision of a structure, which will stand up under shear, and a wide range of temperatures to which it may be subject during use.”
4
Historically, costs and volume were key factors in determining how greases were formulated. Nowadays, with stricter governmental regulations, and much more severe operating conditions for equipment (i.e., higher speeds, extreme loads and cycles, temperatures), the considerations to grease formulation become more comprehensive, tailored rather to unique applications versus a “one fits all” solution, balancing numerous requirements (
see Figure 1). Consequently, lubricating greases are subjected to multiple testing requirements to verify and improve their performance. Many of these tests are not only industry standard but also specific to component manufacturers (i.e., bearings, gears) and OEMs. STLE member David Turner, senior technical services representative, lubricants, CITGO Petroleum Corp., explains: “Some grease users, such as bearing manufacturers, have devised their own tests to measure the performance of grease in specific bearing types or conditions.”
Figure 1. The key in grease formulation is balancing all the requirements.
This article showcases considerations for lubricating grease testing while formulating, followed up by in-service testing practices discussion from industry experts. The American Society of Testing and Materials (ASTM) should be consulted for details on how the tests mentioned herein run, their significance and limitations.
Turner indicates that there are many typical tests that quantify the properties of greases. Most performance characteristics are measured using ASTM, German Standardization Institute (DIN), International Organization for Standardization (ISO), and there are several other standard test methods that can be used.
New grease testing
In general, all grease tests can be classified as chemical and mechanical. Chemical tests predominantly concentrate on certain lubricant properties, i.e., composition analysis, trace contamination detection, regulatory testing. Mechanical tests concentrate on simulation of operating conditions and their effect on a product. All the tests combined play a pivotal role in the formulation of lubricating greases. According to German Standard DIN 50 322, there are six different test categories (
see Figure 2).
5
Figure 2. Test categories according to German Standard DIN 50 322.5
Table 1 shows the most common ASTM tests methods used for grease testing. Their details can be found in “Guide to ASTM Test Methods for The Analysis of Petroleum Products and Lubricants.”
6 This list does not cover all the tests devised to determine the characteristics of greases under various conditions. However, it is a compilation of the most often used tests. The ultimate purpose of the testing is to determine whether the product meets all the necessary requirements.
Table 1. Most common lubricating grease tests
When developing a new lubricating grease, Turner notes the primary factors to consider for a new formulation are the operating conditions of the application. “Primarily, the temperature, load and speed of bearings or gears, and the type and size of the bearing,” he continues. “Those factors will typically help guide the formulator to the base oil viscosity required, the type of base oil (mineral, synthetic [and synthetic type] or vegetable), the thickener type and what types of additives are required. Another factor that must be known is the type and degree of contamination,” Turner says. “Water and dirt are common contaminants, but others, such as corrosive materials, solvents and even radiation, must be considered when formulating a product for a specific application. Most applications that require grease lubrication have a relatively clear indication of what is needed in the grease, based on the operating and environmental conditions of the application. Products can be formulated for extreme temperatures (high or low), heavy loads, shock load and vibration or high-water resistance,” Turner says.
The typical composition of grease includes up to 15% of performance additives, up to 20% of soap or other thickener and the remainder of up to 95% base oil. Once product requirements are known, a formulator would select blends of base stocks as well as a pre-mixed additive package or additive components, such as extreme pressure, antiwear, corrosion inhibitors, antioxidants, etc.
Turner explains that all grease components (oil, thickener or additives) influence the targeted properties. Each grease component affects certain properties of the grease. The thickener concentration determines the consistency of the grease (more thickener produces a stiffer grease), while base oil type has an effect on the amount of thickener required to produce the desired consistency (solvency of the base oil), he adds. The base oil viscosity is critical to proper lubrication in the intended application. Low-speed applications typically require higher viscosity base oils, while high-speed applications require a lower base oil viscosity. The additives incorporated into the grease determine many of the performance properties, such as extreme-pressure performance, oxidation resistance or corrosion protection. The overall formulation must be well balanced to produce a grease with all of the desired properties, Turner says.
Specialty greases are formulated to meet not only general requirements but also the requirements of various processes, parameters and any other factors which may influence performance. For example, requirements regarding operating temperature can be very diverse. Turner states that not only is the operating temperature critical to know, but startup temperature and the temperature at which the grease is applied also are important factors. If the grease must be pumped over a distance at low temperature before entering a machine that operates at elevated temperature, both situations must be taken into consideration when formulating the product, he adds. Other environmental conditions, such as where the equipment operates (indoors in a clean environment or outdoors in a dusty location) also must be considered.
Another very critical factor to consider is grease compatibility with other chemicals and greases when working on new grease formulation. Turner explains that grease compatibility is a somewhat contentious issue, as many compatibility charts do not agree. “Compatibility testing is always preferred,” he adds. “With regard to compatibility with existing products in the market when formulating a product for the same application, it is best to follow the market trend in thickener type,” Turner says. An example of this is an application for which several products exist, all based on lithium complex thickeners. “It would be prudent to introduce a new product for that application that also is based on lithium complex thickener technology, not, say, polyurea or aluminum complex,” Turner adds.
NLGI’s High-Performance Multiuse (HPM) Grease Specification evolved from widely used NLGI’s GC-LB specification, published back in 1989.
3 The new specification is a good example that shows how, nowadays, greases are subjected to more severe testing requirements.
Published by NLGI in 2020, Table 2 shows a comparison of GC-LB and HPM core specifications, and also the additional enhanced performance requirements for the newly created subcategories:
•
Water resistance (WR)
•
Saltwater corrosion resistance (CR)
•
High load (HL) carrying capacity
•
Low temperature (LT) performance.
Table 2. GC-LB comparison with HPM core testing and subcategories
As per NLGI, each subcategory (tag) can be added separately or in combination with other tags. For example, one grease may meet the HPM core specification, while another may meet the core plus one tag, or two or even all four tags (HPM+WR+HL+CR+LT).
3 NLGI states that they will continue to refine test requirements and adjust or add to specifications as needed to reflect testing capabilities; therefore, the tests requirements should be seen as “living documents”.
3
Sometimes a test for a characteristic other than those designated for grease must be used. For example, most recently, greases for electric vehicles such as dielectric, electrically conductive or thermally conductive have relied on tests that are not commonly used for lubricating grease (
see Table 3). As the industry goes through the most rapid acceleration in its history, gaps in the standard tests will continue to exist, and new requirements are evolving constantly.
Table 3. Most common lubricating grease tests on electrical-related properties
Extensive testing of a grease is fundamental to specialty grease formulation. Not only is it necessary to develop an optimum performing product for an application, but it also adds to the body of knowledge on the testing itself, which, in turn, is essential to advance the science and innovation. For example, Turner recalls the most interesting formulation challenge on the development of a grease for high-speed grease lubricated couplings. “General purpose greases had been used for many years in those couplings, with little success and sometimes very poor performance,” he says. “It was realized that separation of the base oil and thickener was occurring under the centrifugal force in a coupling rotating at high speed due to the difference in the density of the components. A development project was launched to formulate a product in which the density of the base oil and thickener were the same, or as close as possible,” Turner adds. He continues: “A new test, ASTM D4425, issued in 1984, had been developed specifically to measure the centrifugal separation characteristics of greases used in high-speed couplings. Using that test, a product was developed that had no oil separation under a centrifugal force of 36,000 G.”
Substantial formulation science takes place to achieve all of the requirements for premium and specialty greases. That’s how greases, which are tailored to specific applications and optimized quality, ensure long and trouble-free operation of the assets.
In-service grease testing
Oil analysis has been utilized to optimize reliability and performance of critical assets successfully for many years. Only recently, asset owners gained an opportunity to analyze greases while in-service with ASTM’s newly created two standard methods: D7718 first published in 2011, and D7918 first published in 2015. To create these standards, ASTM volunteer committees worked diligently for several years ensuring that samples from new processes and with new tools can be taken with the highest quality. These methods have finally allowed the inclusion of greases in asset lubricant analysis. Grease analysis methods enable scheduled maintenance actions and assist with investigation or identification of any concerns that may require immediate attention. From a small trendable sample size of only 1 gram, multiple different tests can be performed to determine contamination, wear, oxidation, consistency, etc.
STLE member Richard Wurzbach, president of MRG Labs, explains that when it comes to in-service grease analysis (as opposed to new grease quality or properties testing), there is an ASTM standard that addresses multiple analysis tasks, ASTM D7918, “Standard Test Method for Measurement of Flow Properties and Evaluation of Wear, Contaminants and Oxidative Properties of Lubricating Grease by Die Extrusion Method and Preparation.” He adds that this method allows for six tests to be performed on a 1-gram sample. This sample must be in a specific sampler, called a “Grease Thief,” which is described in the ASTM in-service grease sampling standard D7718 called “Standard Practice for Obtaining In-Service Samples of Lubricating Grease.” Figure 3 shows a grease sampler, and Figure 4a, b, c and d show steps of how the grease sample is taken.
Figure 3. Grease sampler. Figure courtesy of MRG Labs.
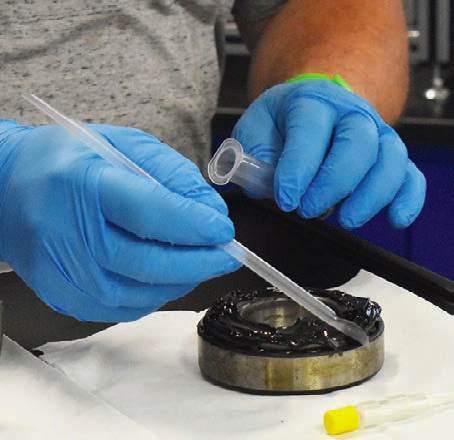
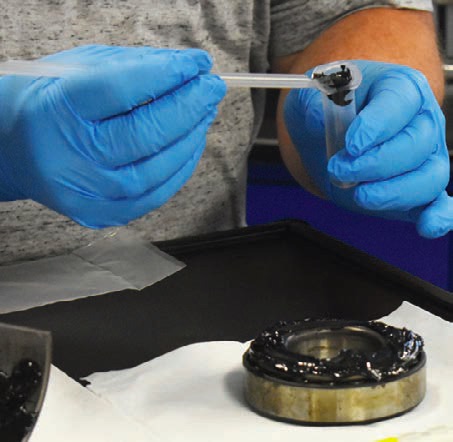
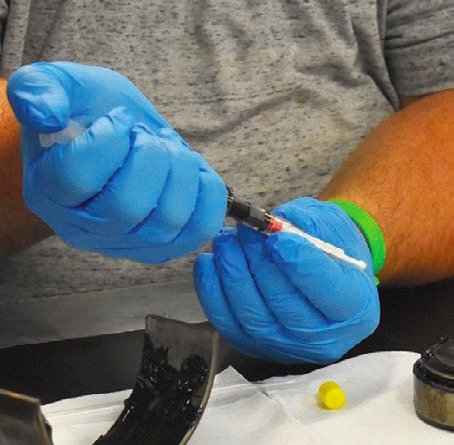
Figure 4a. Taking a sample, step 1. Figure 4b. Taking a sample, step 2. Figure 4c. Taking a sample, step 3. Figure 4d. Taking a sample, step 4.
Figures courtesy of POLARIS Laboratories®.
After the sample is taken, Wurzbach continues, “The 1 gram of grease is first inserted into an induction coil device to measure ferrous debris level and is then extruded through a flow die to measure consistency. The exit of that die conforms the grease to a thin film ribbon that is laid on a clear plastic substrate, that is divided into sections that each hold about 0.25 grams of the sample (
see Figure 5a and 5b),” he adds. While being extruded, a light source and high-resolution magnifying camera are used to count and size particulate in the grease thin film for a “grease particle count,” Wurzbach says. He continues, “Each individual section can then be pulled away from the backing piece to be used for a further test, which includes dissolving in solvent for elemental spectroscopy tests like inductively coupled plasma (ICP) or rotating disc electrode (RDE), particle identification such as analytical ferrography, Fourier-transform infrared spectroscopy (FTIR) analysis, RULER testing for antioxidant levels, adenosine triphosphate (ATP) testing for microbial content quantification, moisture by Karl Fischer or thermal transfer and humidity sensor.
Figure 5a. Die extrusion. Figure courtesy of POLARIS Laboratories®.
Figure 5b. The exit of the die extrusion. Figure courtesy of POLARIS Laboratories®.
Wurzbach notes that if less than 1 gram of grease is available, it may not be possible to run all the tests outlined, and so in that particular case, a priority should be given to the results that are most important to determine. He recalls: “In a project to test in-service greases for Chinook H-47 helicopters, some of the components being sampled, such as drive shaft splines, had very little grease available to sample, and the sample size was frequently less than 1 gram (
see Figure 6). Alternate test slates were designated based on the available amount. Three test slates were determined for samples with greater than 1 gram, those with 0.7-1.0 grams and those with 0.35-0.7, each optimizing results available for the sample obtained. In some cases, substitution of tests could be used that are more effective with smaller volumes. For example, when the sample size is less than 0.7 grams, a complete data set on consistency by die extrusion is not possible, but there still may be sufficient volume for rheometer testing to measure similar properties. In one case, we were presented with a data center micro-bearing, which only had a residue of grease adhered to it, and no way to harvest any usable volume for determining if the grease that had been applied was the correct product or had oxidized. We were able to place the entire bearing into a photoacoustic spectroscopy module for FTIR analysis to confirm grease chemistry. The total amount of grease available was less than 50 milligrams.”
Figure 6. In a project to test in-service greases for Chinook H-47 helicopters, a soldier took a grease sample, and the sample size was frequently less than 1 gram. Figure courtesy of MRG Labs.
Assets owners can combine information from analysis with other technologies such as ultrasound, vibration and thermography to gain better insight on assets condition. STLE member Lisa Williams, technical solution engineer, Spectro Scientific, explains that with any condition monitoring technique, it’s wise to pair with at least one other technology. Grease analysis does a good job picking up on issues earlier than vibration, she adds. “For example, in wind applications where you have a low-speed, high-load bearing, it may be tough for vibration analysis to pick up on faults and still give enough time for the problem to be addressed prior to a failure,” Williams says. “Grease analysis can pick up on those faults a little bit earlier, allowing the technician to address the problem sooner,” she adds.
When looking into monitoring live grease performance, Wurzbach says that relevant technology such as sensors is not yet available. “Partially due to the challenges of grease sticking to any sensor inserted into a bearing cavity,” he explains. Yet, there are very effective methods at sampling from running or shut down machines that can be accessed for this purpose, Wurzbach adds.
“ASTM D7718 outlines the considerations and proper methods to ensure that any sample is representative of the condition of the grease and the machine,” Wurzbach says. He continues, “The challenge is to identify the “live zone” of the grease in the machine, where it is actively being utilized to provide lubrication and also contains any contaminants being introduced along with wear being generated. To access this location typically requires specially designed tools, and traditional methods of oil sampling that rely on vacuum, such as vacuum pumps and syringes that are often ineffective.”
“Once the representative sample is secured, 10 or more tests can be performed on the typical 1-gram sample size. Six tests are listed in D7918, including ferrous content, die extrusion (for consistency), colorimetry, particle count, linear sweep voltammetry (RULER antioxidants) and moisture,” Wurzbach says. Other tests possible but not included in that method are analytical ferrography, FTIR, elemental spectroscopy and microbial content (by ATP test).
When selecting a grease for application, all the properties of the grease must be considered, and the same goes for in-service grease testing. Wurzbach notes: “Grease must be analyzed holistically, as the components of grease behave as a system. Some properties that are measured are influenced by all components, such as flow characteristics and consistency. One area that presents a component specific challenge to measurement is moisture. For oils, whether by direct injection or oven-method transfer to Karl Fischer, the flow and currents in oils ensure that moisture present has the opportunity to be liberated to the reaction of the Karl Fischer reagent if proper setup is provided.” He adds, “However, the matrix nature of grease presents challenges to that transfer, and the mechanism is a function of the individual polarities of each component. In the method we prefer for measuring ppm moisture levels in greases, a humidity sensor plot displays the moisture transfer rate to the sensor, and it can often be seen in a given sample heating profile, that distinct time-related releases occur that correspond to differences in the hygroscopic nature of the thickeners, base oil and even, possibly, additives.”
An asset owner can easily document its reliability with the long-standing industry methods. Williams explains that in oil analysis, many have adopted the “stop light” (red–yellow–green) philosophy to evaluate the condition of a sample in three key areas: wear, contamination and physical properties. She adds that with grease analysis, the same evaluation technique can be used—but with an additional component such as thickener component of the grease. The thickener component also can be referred to as the NLGI grade or consistency. “It’s important to understand the consistency of the grease and how it has changed over the service life of the grease,” Williams adds. Figure 7 shows a sample of a grease analysis report.
Figure 7. In-service grease analysis report example. Figure courtesy of POLARIS Laboratories®.
In-service grease testing builds a proper trail of information to document performance. The testing is repeatable, and it is reliable. Wurzbach notes that the keys to grease testing being repeatable and reliable are in both the effectiveness and consistent method of sampling, and the use of defined and standardized methods for analysis.
“Presently, ASTM is conducting an interlaboratory study for ASTM D7918 to determine statistical repeatability and reproducibility of this method at 14 participating laboratories. ASTM D7718 provides the necessary guidance for tools and methods to achieve the consistent sampling required,” Wurzbach adds.
The in-service testing results offer significant insight into the performance of the grease. Wurzbach states that in-service tests can be used to evaluate the effectiveness of a given lubricant in the specific application. “Grease analysis can be used to monitor machine health by determining wear quantities, materials and modes,” he adds. “Contaminant levels can be quantified to determine the effectiveness of sealing mechanisms, or the rate of regreasing used to purge those contaminants present in the immediate environment. The consistency of the grease can be measured to ensure that the grease continues to possess the qualities needed from the grease: to stay in place where applied, and to flow as needed to provide lubrication to moving parts,” Wurzbach says. He then adds that the oxidation condition of the grease, as measured by FTIR and antioxidant measurement (RULER), shows the life of the grease and helps to optimize replenishment frequency and quantity. “If these four aspects of grease performance, wear, consistency, contamination and oxidation, are monitored and lubrication practices adjusted to achieve optimization, that life of the grease and the lubricated asset can be maximized,” Wurzbach explains.
Additionally, in-service grease results can be trended to prevent failures. Williams says that in condition-based maintenance, results should always be trended in order to make the best decision in the future. “Rarely an analyst would take a single point in time and make a decision about a component,” she adds. “Rather, an analyst would establish trends and statistics that let evaluate deviations from the trend as compared to a brand-new sample. Figure 8 shows a grease analysis report with trends and comments.
Figure 8. In-service grease analysis report example. Figure courtesy of POLARIS Laboratories®.
When necessary, an asset owner can implement an “onsite” analysis of grease to ensure performance remains high. Wurzbach states that there are several onsite tools available for grease testing. “There are kits that allow testing of greases for contaminants, consistency and a sort of thermal separation point,” he says. “It involves using a microscope to look at the grease through a clear plate for contaminants and wear particles, a weight that is used to squeeze a small grease amount and give insight to the NLGI grade based on its movement and a paper and hotplate method that allows a measure of the oil bleed into the paper.” Wurzbach continues: “For perhaps less subjective testing, a mini lab also is offered that works with the “Grease Thief” sampler outlined in D7718. It utilizes an induction coil that is calibrated to the sample geometry to produce a ppm level for ferrous debris. It is complemented by a colorimeter method that prepares precise thin films of the grease for a transmission cell visible light spectrometer. This produces spectral color data and a CIELAB Delta E value, similar to the Membrane Patch Colorimetry measurement, that can be compared to new greases to generate trendable values and action criteria.” These two instruments can be battery operated and can communicate with Bluetooth to mobile devices, and are referred to as the Grease Thief Mini-Lab.
While it may be commonly expected, the results of in-service grease testing don’t always propel a selection of a different grease for the application. Wurzbach explains that sometimes asset owners are looking for easy fixes to complex equipment problems, and switching to a different type of grease is often seen as such a fix. However, switching greases potentially creates its own set of problems due to grease mixing and incompatibility, he says. Because grease is designed to stay in place, getting it “all out” can be particularly tricky, Wurzbach adds. “Grease testing occasionally shows inadequate performance of a grease, and further engineering evaluation of the equipment requirements sometimes reveals that the grease currently in use was not properly selected for the application. But grease performance issues are more often related to inadequate grease delivery, incorrect replenishment frequency or quantity, contamination or other issues,” Wurzbach explains. The great benefit of grease sampling and analysis is that such issues can be determined based on grease analysis results, and date-driven decisions can improve performance, he notes. “When there is a determination that the grease in use is inadequate, a new grease can be selected, and its use piloted while carefully monitoring performance through grease sampling and analysis,” Wurzbach suggests. “When grease products must be changed, testing grease compatibility under conditions similar to the application are very important to ensure good results,” he adds.
Wurzbach states, “Formulation inadequacies that could be found with grease analysis could include poor film formation leading to higher than expected wear levels. Rapid loss of antioxidants could show that the grease may not be properly designed for the degradation stresses of the application. Significant changes in consistency could show that the pumping or shearing conditions are compromising the selected thickener. Or very high moisture levels might show that a grease that has better moisture-resisting properties should be used.”
Detecting a potential problem also is possible with the in-service testing. Wurzbach gives an example: “In paper mills or food processing facilities, for instance, the prevalence of moisture in the process creates a threat of grease biofouling. This issue can be insidious, as colonies of microbes can be established in the grease inside a bearing housing, and grease replenishment does not eliminate this. In these environments, testing for ATP levels in the grease determines the presence of active colonies, which can lead to acidic damage or hydrogen embrittlement conditions for the shaft and bearing, and in food processing microbes can threaten product safety.” He then adds, “In other applications, ambient contaminants might be the most significant threat to both grease and component life, and effective sampling and analysis to measure and monitor their levels is important to protect machine condition.” Sometimes, monitoring something as simple as just the grease color spectrum and ferrous content can be sufficient for a screening test that allows large numbers of components to be tested economically to find those outliers that require further testing to pinpoint the nature of the changes seen, Wurzbach adds.
“With timely follow-up testing, this sampling and screening test is often the most efficient and effective method to protect grease-lubricated components,” Wurzbach offers.
Williams notes that from her experience, the most common root cause issues when it comes to grease-related failures are grease mixing and improper base oil viscosity chosen for the application. “Changes in the consistency of the grease using a rheometer, or the “Grease Thief” analyzer, will tell if the grease has significantly changed in consistency as compared to a brand-new sample. When two incompatible greases are mixed, the oil will separate from the thickener and leave the thickener in the bearing to do the lubricating. The thickener is not designed to lubricate the bearing. The oil is intended to shear from the thickener and lubricate the bearing. When the user starts to see puddling of oil, oil dripping from the bearing or channeling/tunneling of the grease inside the bearing, chances are some incompatible grease mixing is occurring,” Williams explains. She adds: “It’s fairly common to see some consistency drop when the grease is in-service, but it’s those significant drops of greater than 30% or so where we start to question if grease mixing is an issue. To further confirm which grease types have been mixed, the analyst can use an FTIR to take a fingerprint of the grease to confirm contamination with another sample. Elemental spectroscopy will help confirm additive mixing as well. I’ve also seen the RULER device used to confirm additive mixing.”
Williams further notes that improper base oil viscosity selection is another common root cause when it comes to grease-lubricated failures. She says, “This property is often overlooked because, with grease, there is so much focus on the NLGI grade (consistency). It must be kept in mind though that the oil is what is actually doing the lubricating, so the base oil viscosity is a very important factor in grease selection. As the oil shears from the thickener, it’s important to understand if that oil is creating a sufficient film.” Williams continues: “An analyst can indicate when viscosity selection is incorrect based on the type of wear that forms under these conditions. Insufficient lubricant conditions will often result in black oxides formation. If wear levels are elevated, analytical ferrography can be done to determine what type of wear is present (proper solvent selection is critical).”
Not all the grease chemistries are created equal. There are few that make it challenging to perform in-service testing. Wurzbach says, “For instance, most greases respond fairly well to a solvent mixture that also can be effective at preparing ferrography slides for particle inspection. But some greases do not dissolve in these hydrocarbon solvents. Very soft and very hard greases, which can be the condition of normal greases after extended time in service, can be difficult to handle and need special testing for the die extrusion process. Greases with very high particulate contamination levels also can clog extrusion dies and interfere with rheological measurements, as well as causing damage to crystals used to measure FTIR properties.” Williams adds that from her experience specifically fluorinated greases are challenging to deal with. “They don’t dissolve well with solvents commonly used in the lab, so it makes it challenging to introduce them into many instruments used for grease analysis. Fluorine is particularly challenging to excite in elemental spectroscopy methods like rotating disc electrode (RDE), so other higher-end spectroscopy methods generally need to be used to get the most accurate numbers,” she says.
For those who are interested in formal training on in-service grease testing, Williams recommends the International Council for Machinery Lubrication (ICML) courses, as, recently, they have started to incorporate grease sampling and analysis into their course curriculum. “In these courses, the end-user learns how to take an optimal sample and also learns about the test slates available to determine the condition of the grease. ASTM standards D7718 and D7918 also are helpful for someone who wants to learn more on in-service grease testing,” Williams adds.
ACKNOWLEDGEMENTS
The author would like to thank Emily Featherston and Dave Tingey, POLARIS Laboratories®, for the graphics and general discussions on in-service grease analysis.
REFERENCES
1.
NLGI (1989),
NLGI Lubricating Grease Guide, NLGI, Kansas City, Mo.
2.
NLGI (2021),
2020 Grease Production Survey Report, NLGI, Kansas City, Mo.
3.
NLGI (2017), available
here.
4.
Vold, M. J. and Vold, R. D. (1952), “Lubrication and lubricants,”
J. Inst. Petroleum Technology,
38, pp. 155-163.
5.
Czichos, H. (1995), “Metrology of wear,” in: Dyson B.F., Loveday, M.S. and Gee M.G. (eds.),
Materials Metrology and Standards for Structural Performance, Springer.
6.
Nadkarni, R. A. and Nadkarni, R. A. (2007),
Guide to ASTM test methods for the analysis of petroleum products and lubricants,
44, West Conshohocken: ASTM International.
Dr. Yulia Sosa is a freelance writer based in Peachtree City, Ga. You can contact her at dr.yulia.sosa@gmail.com.