KEY CONCEPTS
•
Driveline fluids for EVs represent a potentially strong market for lubricants; in addition, there is the possibility that the concepts gained from these fluids will be applicable in other applications such as the cooling of high-performance computer servers.
•
Bench tests for driveline fluids are currently inadequate—OEMs, standards organizations and formulators are working on this.
•
There is an opportunity for standardization of EV lubricant test procedures, which some organizations have only begun to explore.
Electric vehicles (EVs) are becoming increasingly popular as auto manufacturers release new models and the cost of batteries decreases. In terms of traditional internal combustion engine (ICE) vehicles, EVs are a disruptive technology, not only with respect to fuel consumption, but also in terms of lubricants. The very good news for those involved in the lubricant industry—and the considerable challenge—is that driveline fluids for EVs represent a potentially strong market for lubricants.
There are similarities and differences between existing automatic transmission fluids (ATFs) and EV driveline fluids. While most EVs on the road today use versions of conventional ATFs, they might not be the best fluids now or in the future.
EV drivelines have fewer moving parts, incorporate different materials and operate under conditions that are, in many ways, different than those of ICE vehicles. Following are some fluid properties that are of concern in EV driveline fluids:
•
Copper compatibility. Fluids in contact with electric motors should not corrode copper windings.
•
Load-carrying ability. Electric motors produce very high torque, which stresses gears in new ways.
•
Aeration/foaming. The trend is toward higher speed electric motors (even higher than 10,000-15,000 rpm), which could lead to air entrainment in the fluid.
•
Electrical conductivity. There is a limit to how conductive the fluid can be without causing problems with electrical components. On the other hand, if the conductivity is too low, static electricity build-up could be a concern.
•
Thermal conductivity. Fluids with higher thermal conductivity would keep the motor and drive system running cool, but oils are intrinsically poor heat conductors.
•
Viscosity and friction. Any reduction in friction can extend the battery life and range of an EV.
These characteristics will drive the creation of new specifications and new fluid formulations to meet them.
While some believe that EVs pose a threat to the existing automotive lubricant supply chain, there also is an opportunity for innovation and cross-fertilization to adjacencies, such as electric transmission/transformer oils, high-performance computer server cooling, appliance A/C, control systems, etc.
Four Southwest Research Institute (SwRI) staff members contributed to this article as a group. Because of this, SwRI material will be attributed to “the SwRI staff” or just “SwRI.” The contributors are: Ian Smith, manager, electrified powertrain; Rebecca Warden, manager, fleet and driveline fluid evaluations; Yong-Li McFarland, senior research scientist; and STLE member Peter Lee, staff engineer and chief tribologist.
ICE vehicles and EVs—Differences in design and lubrication
According to the SwRI staff, because of the narrow best efficiency operating conditions of an ICE, there has been a substantial amount of effort into creating transmissions and control strategies that keep the engine operating at peak efficiency as often as possible. This has typically resulted in transmissions and differentials that keep the engine speeds less than 3,000 rpm under most driving conditions.
Additionally, the torque characteristics of an ICE (whether diesel or gasoline) are different than an EV. Peak torque would typically occur at 1,200-1,800 rpm in modern ICE vehicles. For reference, electric motors operate at speeds up to 18,000 rpm and beyond, and peak torque can be generated at zero rpm.
The design of an EV is much simpler than an ICE vehicle. “Because a pure electric vehicle will not have an engine, the power flow is significantly less complicated,” the SwRI staff explains. “Power goes from the grid to the vehicle’s batteries, which power the motor to drive the wheels.”
Internal combustion engines will typically operate at coolant temperatures that are between 80 C and 100 C, which results in significant heat rejection through the radiator—roughly half of all the fuel energy is lost through the tail pipe and coolant in an ICE.
Thermal management also is key with EVs. The motor and inverter should stay as cool as possible, but most will operate up to a coolant temperature of about 65 C. To maximize battery range, batteries shouldn’t exceed 45 C (
see Figures 1 and 2). Lithium-ion chemistry works best between 25 C and 35 C, so heating also is required at times. EVs can use permanent magnet motors that can lose their magnetism if they reach temperatures above their Curie temperature; even getting close causes degradation of the magnetism.
1
Figure 1. Volkswagen ID.3 battery EV on a chassis dynamometer for range and efficiency testing. Figure courtesy of Southwest Research Institute (SwRI).
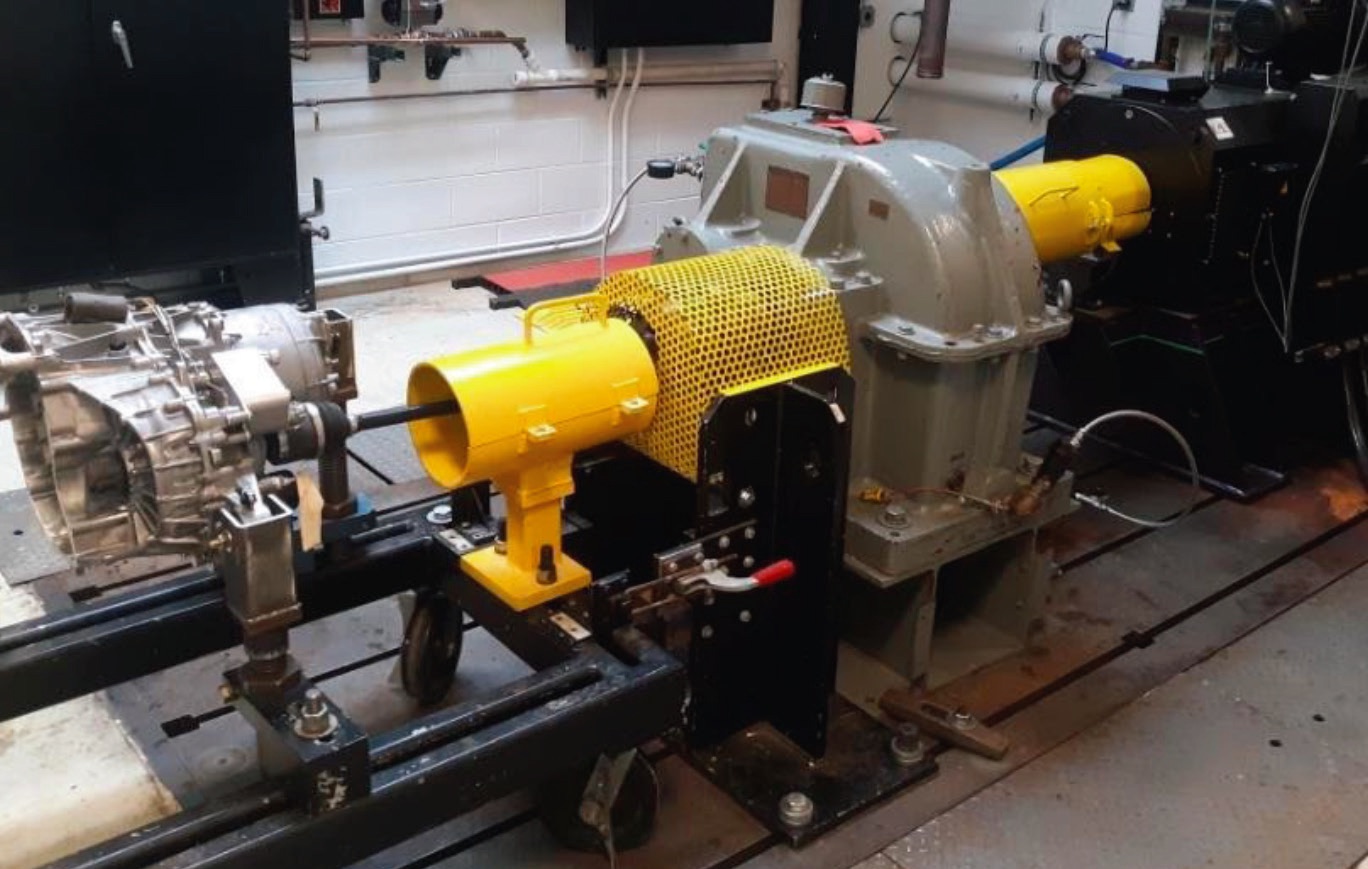
Figure 2. Tesla Model 3 electric motor and gearbox installed in a test cell and controlled with a fully open inverter to evaluate EV fluid performance. Figure courtesy of Southwest Research Institute (SwRI).
A hybrid EV uses the electric motor to maintain the engine in the most efficient state; when the engine is creating too much power, the power is stored in the batteries and is called up when the engine is not generating sufficient power on its own.
“However, more often than not, the electric continuously variable transmission (eCVT) approach is used to modify the speed ratio of the transmission to keep the engine operating at best brake-specific fuel consumption like a conventional CVT,” the SwRI staff adds. “In some instances, the engine will be used to charge the battery pack, but this usually isn’t the case as your best use of the energy is to move the vehicle rather than have all the losses associated with converting mechanical energy to electrical stored energy.”
Today, because an electric motor has a very wide speed range of efficiency, EVs are equipped with a single-speed gear reduction device (and, in most instances, no reverse gear).
“While moving to a multi-speed transmission would improve the efficiency and range of the vehicle, many current manufacturers have decided that the cost outweighs the benefit,” the SwRI staff says. “Notable exceptions are the Porsche Taycan with a two-speed transmission for the rear motor; however, this was selected due to performance reasons and not efficiency/range reasons. The single-speed gear reduction can be rather large (up to 11.5:1).”
With little waste heat from the power source, keeping the passenger compartment warm during cold weather is another important aspect for the EV manufacturer to consider. Possible solutions are heat pumps and smart waste heat management to maintain comfort without significantly affecting range.
Ultimately, one of the biggest differences between EVs and ICE vehicles is that the EV range and performance can change constantly by remotely sending a software update to the battery management system and to the electric motor inverter to change the calibration (
see Figure 3). This is not something that is currently feasible for ICE vehicles.
Figure 3. Chevy Bolt electric motor and gearbox installed in a test cell controlled with the OEM inverter and SwRI controller to evaluate EV fluid performance. Figure courtesy of Southwest Research Institute (SwRI).
In terms of lubricants, STLE Fellow Dr. Edward P. Becker, president of Friction & Wear Solutions, LLC, explains that, for the body and chassis, there is not much difference. However, in the powertrain, there are several major differences.
“Probably the most significant difference is that EV lubricants don’t have to deal with the heat, pressure and contamination from combustion,” he says. “These are the three main effects that limit the life of oil in the ICE. EV powertrain lubricants can be expected to last much longer than conventional engine oils. The other main difference is in the gears. Nearly all current EVs use a single-speed reduction gear (as the electric motors typically turn much faster than the wheels), and the loads on these gears are quite high at low speed. In ICE vehicles, high load occurs typically at high speed.”
Because of this, Becker goes on to explain that EVs won’t affect professionals involved in body and chassis lubrication. Powertrain lubrication is a different story. “In powertrain lubrication, the major issue will be developing an EV lubricant that maximizes protection during low-speed, high-load operation,” he says. “Other considerations include compatibility with materials in electric motors, such as large amounts of copper, and the conductivity of the lubricant.”
Fluids and lubricants for EVs
EVs do not need engine oil because they have no engine. However, driveline components will still require lubrication.
2 While, other than engine oil, most EVs use the same types of fluids that are in conventional ICE vehicles, the operating conditions are very different. “For example, motor speeds are very high, pushing 20,000-30,000 rpm in some R&D applications at the top speed,” the SwRI staff explains. “Also, the high gear reductions are significantly greater than that of a conventional drivetrain.”
These driveline lubricants have their own set of requirements: such as higher load, higher temperature, faster speed and different material compatibilities. Current lubricants are not optimized for the low-load, high-speed conditions in EV gears.
The drivetrain lubricant has even been used as a cooling fluid for the electric motor—cooling the electric motor as well as providing appropriate gear protection for the reduction gears. This highlights the importance of thermal capabilities.
To protect the life of the motor, it’s vital to keep it cool. As power densities of EVs increase, the cooling function of the lubricant plays an increasingly important role.
Regarding the coolant, the SwRI staff observes, “A glycol-water mixture is the coolant of choice as it is readily available and still meets the performance/cooling requirements set forth by the OEMs. This coolant is used for cooling the battery cells through a cold plate or cooling ribbons in the battery pack, and it is used for cooling the electric motor through a water jacket around the stator or even a small plate stack heat exchanger for the lubricating oil (
see Figure 4).”
Figure 4. Test stand to evaluate the safety performance of immersed coolants on lithium-ion battery cells and modules. This specific test stand is designed to precisely control the temperature and flow rate of the coolant and penetrate the module with a steel nail to understand how well the fluid mitigates fire. Figure courtesy of Southwest Research Institute (SwRI).
The SwRI staff continues: “One major difference the fluid sees is the temperature. In a conventional vehicle, the temperature of the coolant easily reaches 80 C to 100 C; however, for an EV, the bulk temperature of the coolant will likely not exceed 65 C. Research is being conducted to look at immersed (or direct) coolant technologies for batteries in EVs. This type of fluid is electrically non-conductive but still has high thermal conductivity. The immersed coolant would directly interact with the battery cells to extract heat up to 50-100 times more effectively than a conventional cold plate or cooling ribbon design. This technology used to be relegated to motorsports and aerospace applications; however, there are a number of automotive manufacturers who are bringing this technology to market (Volvo for electric refuse trucks and Mercedes AMG for the new C63 plugin hybrid).”
This type of coolant technology would allow the battery to be operated at higher charge/discharge rates while keeping a temperature similar to a conventional design.
Because many of the materials used in EVs are unique, material compatibility is more critical. “There has been a considerable amount of work already conducted into seeing what the ideal fluid would be given the differences in operating conditions compared to the traditional vehicle,” the SwRI staff explains. “For any ‘wet’ motor, where the lubricating oil also is used to help cool the motor, the fluid will be in contact with copper, large electric and magnetic fields and very high speeds compared to a conventional drivetrain.”
An additional consideration is the effect of operating speed on a lubricant; instead of entrainment into components such as gears, the lubricant becomes a mist changing the way these highly loaded components are lubricated.
Automatic transmission fluid
Becker reports that BMW has publicly announced its intention to offer a multi-speed EV transmission; however, since all major transmission manufacturers (ZF, Getrag, Eaton, etc.) have announced plans to produce such transmissions, more announcements from other auto manufacturers are likely in the near future.
“Multi-speed transmissions are a good idea for EVs for the same reasons they are used in ICE vehicles: the power, torque and efficiency of both types of motors vary with motor speed,” Becker says. “By using different gear ratios between the motor and wheels, the motor can be run closer to its peak efficiency more often, resulting in greater range. The disadvantages of multi-speed transmissions are mechanical complexity, weight and, of course, cost.”
Dr. Steffen Sandhoefner, head of package and eDriveline development, LANXESS Lubricant Additives, explains that the base ATF is usually a higher grade mineral oil alone or in combination with PAOs, esters and other types of base fluid components. “Rheology of the fluid is of high importance,” he says. “To adjust the rheological properties, viscosity index improvers, as well as pour point depressants, are used. For the wide set of performance requirements, proper additivation is necessary.”
Per Sandhoefner, important ATF additives are antioxidants, corrosion inhibitors (for ferrous as well as yellow metals) and antiwear additives. Since frictional properties must be met, one or a combination of different friction modifiers is used. Surface active components like dispersants and antifoam additives also are needed.
International specifications for lubricants are typically developed by organizations such as SAE, but do not exist for ATFs today other than JASO 1-A.
3 OEMs have created their own ATF specifications. Examples of such widely known OEM specifications are the GM DEXRON® and Ford MERCON® groups of technical specifications.
4
Additives
Dr. Gregory Hunt, senior research chemist, Lubrizol Ltd., notes that an additive package consists of specially designed molecules that ensure optimum performance, whether it’s for friction, oil oxidation, gear wear or corrosion protection. “In addition to these performance areas, antifoam agents, dispersants, oxidation inhibitors, detergents, pour point depressants and viscosity modifiers are all called into action in a modern automotive transmission fluid,” he says.
Hunt continues, “Traditionally, lubricant technology is reactive to changes in the market: new developments in hardware generate the need to refine the lubricants used. Therefore, existing additives are compatible, as they are already in use in earlier generations of EVs. However, these fluids were never designed to cope with the new duty cycle, and there are material compatibility concerns.”
The newly designed fluids that Hunt refers to are sometimes termed “efluids.” “As with all lubricants, they operate by minimizing wear in the moving parts,” he says. “However, they’re also specifically designed to combat corrosion of copper in both solution and vapor phases, and remove heat from the e-motor where the lubricant is in direct contact.”
Another concern is sulfur in the additives themselves. Additives with sulfur serve different functions, usually for extreme pressure or antiwear. Some types of sulfur will contribute to copper corrosion. If the hardware is exposed directly to the lubricant, Hunt says tailored corrosion inhibition and/or an alternative antiwear or extreme pressure solutions should be considered in balancing with other performance requirements.
Hunt observes that with some EV designs, the development of hardware and lubricants is occurring concurrently, rather than reactively. “As such, the lubricant helps the equipment to do its job longer and more consistently and effectively,” he adds.
Bench tests for EV driveline and cooling fluids
According to Hunt, the most widely available test for assessing copper corrosion is the ASTM D130 strip test, which is a qualitative image-based assessment. An alternative is a quantitative wire corrosion test. He explains, “This offers real-time corrosion rate information in both the solution and vapor phase. The direct measurement of the corrosion rate is extremely useful when assessing corrosion performance but also for making predictions relating to motor burnouts. This new test is available in external labs.”
Because of challenges assessing corrosion products, a conducting layer deposit test also has been developed. Together these tests can offer a more complete picture of what is happening within the hardware, which helps develop a more robust system.
Sandhoefner observes that a large set of tests required in specifications use standard laboratory equipment for tribology tests. Examples include tests for rheology, corrosion, antiwear and extreme pressure.
He cautions, “Nevertheless, special friction tests need specific test equipment, which is not necessarily available in most of the laboratories. To evaluate the properties in these specific tests for any given developmental fluid in advance, these parameters could be simulated by using scientific friction and wear equipment.
Examples for these machines Sandhoefner is referring to are mini traction machines, micropitting rigs and SRVs. “Final proof of performance needs to be done on larger test equipment that can simulate reality and, if everything is well within the specification limits, fleet tests have to be performed,” he adds. “The decision about the overall performance is done by an approval committee and could not be done by self-certification only.”
So which bench tests for EV driveline and cooling fluids are most important? All tests are important, according to the SwRI staff. “The problem in the industry right now is there aren’t many test methods that allow you to compare fluid performance in a relevant manner,” SwRI concludes. “In many cases, existing methods are being used, but they were developed to evaluate the fluid at very different operating conditions than in an EV. Fluid performance metrics such as durability, aeration, oxidation, thermal capacity, electrical conductivity, etc. are all critical for a good EV fluid.”
The SwRI staff continues: “Unfortunately if you can’t evaluate those fluids in a relevant manner, the formulators can’t determine if the change they’re making is going to have an impact on the vehicle, and the hardware manufacturers can’t determine if they’re making the best choice for their application.”
There is an upcoming SAE document (SAE J3200) recommending bench tests in areas of thermal and electrical conductivity, oxidation, copper corrosion, aeration and material compatibility for EV fluids. “The hope is that most of the important properties and measurement methods are included, but there are some areas of unknowns or gaps in knowledge also to be documented,” the SwRI staff adds. “Something new that was introduced is the consideration of the fluid after it’s been aged with materials—to run additional tests on the aged fluid to see if the material has any detrimental effects on the fluid.”
Conclusions
Hunt summarizes, “Ultimately, the specification for EV fluids will be hardware-dependent; it is difficult to generalize when there are so many different hardware designs. First generation hardware was concerned with electrical conductivity, and as the technology advances and solutions are found, other areas are coming to the fore. For example, materials compatibility, thermal transfer and aeration will become more important as designs develop. Alongside new technologies, industry standards for lubricants are emerging.”
Sandhoefner calls for an open information exchange between additive and lubricant developers and hardware OEMs on all levels in order to foster an efficient and focused innovation process. He also says that proper standardization is a crucial factor, since unlike ICE components that are fairly straightforward, EVs continue to introduce many different concepts and technologies with individual requirements that need to sync with each other.
“At the moment, there is an opportunity for standardization of EV lubricants, which some organizations have only begun to explore. STLE members should consider becoming involved in these activities,” Becker advises.
REFERENCES
1.
The Curie temperature is the point above which materials lose their permanent magnetic properties.
2.
Note that the drivetrain and driveline are not the same. The driveline consists of all of the powertrain’s components, except for the engine. It connects the engine and transmission to the wheel axles. The drivetrain consists of everything after the transmission (not the engine or transmission)—all drive-shafts, axles, joints, differentials and wheels.
3.
Japanese Automotive Standards Organization (JASO) consists of major vehicle manufacturers in Japan. JASO-1-A is a specification defining a DEXRON ATF type.
4.
MERCON is the trade name for a group of technical specifications for automatic transmission fluid created by Ford. Originally MERCON was associated exclusively with ATFs; later Ford released MERCON gear oils and other lubricants.