Tribological Behavior of AISI 52100 Steel and WC-Based Coatings Subjected to Increasing Reciprocating Sliding Velocities and Low-Viscosity Fuel Lubrication
Kelly Jacques | TLT Scholarship Research July 2021
Materials Science and Engineering Department, University of North Texas, Denton, TX
Editor’s Note: This month TLT profiles the 2020 recipient of The E. Richard Booser Scholarship Award, Kelly Jacques (University of North Texas). The Booser scholarship is awarded annually to undergraduate students who have an interest in pursuing a career in tribology. As a requirement for receiving an STLE scholarship, students are given the opportunity to participate in a tribology research project and to submit a report summarizing their research. For more information about the Booser scholarship, visit www.stle.org.
Jacques completed an undergraduate degree in materials science and engineering in May 2020 and has since received the DoD SMART Scholarship. Jacques has started studies in the materials science and engineering doctorate program at the University of North Texas. Their research was conducted under the mentorship of STLE member Dr. Diana Berman. Jacques’ extracurricular activities include painting and reading. You can reach them at KellyJacques@my.unt.edu.

Kelly Jacques
Abstract
Dynamic fluid pressure and flow within heavy-duty fuel engines can result in tribologically-induced failure of fuel injection system components, especially those that operate with low-lubricity fuels. As a result, there is a need for more robust fuel injection system materials that can sustain low friction contacts with non-ideal lubrication conditions. In order to achieve this, fuel pump materials should resist wear and corrosion when lubricated with low-viscosity, low-lubricity fuels under conditions of dynamic fluid pressure and flow. In this study, a high-frequency reciprocating tribometer was used to evaluate the performance of through-hardened AISI 52100 steel and WC-based coatings with increasing sliding velocities. Analysis of the coefficient of friction, surface roughness, hardness, and chemical compositions of the tribological specimens was conducted to evaluate their tribological performance. The AISI 52100 steel was found to exhibit increasing coefficient of friction values with increasing sliding velocities while the WC-based coatings exhibited a decrease in coefficient of friction with larger sliding velocities. The thermal and mechanical properties of the WC-based coatings provided superior tribological behavior relative to the AISI 52100 steel, indicating that these coatings are effective in protecting steel from excessive wear and oxidation in the presence of low-viscosity lubrication.
Introduction
An ongoing issue within modern heavy-duty fuel engines is the tribologically-induced wear and failure of the fuel injection system components, which is largely attributed to the properties of the fuel, corrosion, and excessive loading [1]. Severe tribological damage, such as scuffing, can lead to the seizure of components and overall failure of fuel injection systems. The contact conditions that lead to wear and seizure of sliding surfaces is still unclear, however, many models cite the increase in contact temperature between asperities as the major contribution [2-4]. Lubricity-aiding additives can be introduced to fuels in order to mitigate the heating and wear of fuel injection system components, however, altering fuel chemistries is not always acceptable. For example, the compression ignition engines used by the U.S. Department of Defense (DoD) are predominantly operated with JP-8 aviation fuel due to the single-fuel concept observed by the DoD [1]. Additionally, civilian heavy-duty diesel engines are limited by the continued reduction in sulfur within diesel fuels [5]. Importantly, the contacting components within fuel injection systems often experience the elastohydrodynamic, mixed, and boundary lubrication regimes [1], therefore the loads imposed on the components during operation are not fully supported by lubricant films and must be partially supported by the component materials themselves. In order to reduce wear and frictional heating during operation, the materials implemented in fuel injection systems are required to resist plastic deformation and sustain lubricant films under conditions of extreme load and speed.
It is generally accepted that the temperatures between dry sliding surfaces increase with increased sliding velocities, which can lead to adhesion between contacting asperities and increased coefficients of friction (COF) [6]. However, an opposite effect is often observed in the case of lubricated contacting surfaces [7-9]. Previously, various studies have sought to explain and quantify the relation between sliding velocity and COF in lubricated contacts. Ettles et al. proposed that at high velocities, the co- efficient of friction decreases between two sliding surfaces due to local melting of contacting asperities [7]. Another explanation was suggested by Thompson et al. and Cousseau et al.; the studies showed that the COF decreases with increasing sliding velocities due to an increase in the pressure and thickness of lubrication films [8, 9]. The inverse relation between the COF and sliding velocity in lubricated contacts is generally supported in the literature, however, these works largely focus on the effect of different high-viscosity, high-lubricity greases and oils in tribological contacts rather than the role of the materials or low-viscosity liquids.
In this study, a high-frequency reciprocating rig (HFRR) was used to study the response of AISI 52100 steel and two WC-based coatings to increasing sliding velocities while lubricated with ethanol, a low-viscosity fuel. Specifically, AISI 52100 steel, WC-17Co, and WC-10Co-4Cr were subjected to reciprocating sliding under ethanol lubrication, at ambient environmental conditions, at temperatures of 25 °C and 50 °C, and maximum linear velocities of 2.8 mm/s, 10 mm/s, and 20 mm/s. The AISI 52100 steel was found to experience an increase in the COF with increasing maximum linear velocity (MLV) that is attributed to frictional heating and oxidative wear of the steel surfaces. The WC-based coatings, meanwhile, generally showed a decrease in COF with MLV increase, which is attributed to improved lubrication efficiency of the coating due to an increase in the lubricant film thickness.
Materials and methods
The flat substrate materials used in this study include through-hardened 52100 steel and the thermal spray coatings PTI 188 (WC-17Co) and PTI 226 (WC-10Co-4Cr) deposited onto through-hardened 52100 steel. AISI 52100 steel was chosen as a tribological specimen and substrate for the thermal spray coatings as a representative of the hard tool steels typically used in heavy-duty fuel injection systems [5]. The AISI 52100 steel tribological specimens were through-hardened with a multi-step heat treatment procedure, including an austenizing treatment at 840 °C, water-quenching, and tempering at 190 °C. The WC-based thermal spray coatings were chosen as steel protection candidates due to their high hardness and wear resistance [l1]. The WC-based coatings were deposited onto the steel substrates via the High Velocity Oxygen Fuel (HVOF) technique [11]. The AISI 52100 steel and thermal spray coatings were polished to an average surface roughness value less than 2 μm to reflect the tolerance requirements of modern heavy-duty fuel injection system components [5].
The microhardness values of the steel and thermal spray coatings were measured with a Vicker’s microhardness indenter by indenting the surface with a load of 5 N for 10 seconds at ten randomly chosen positions. The average surface roughness of the steel and coatings was determined with a stylus profilometer with a 12.5 μm stylus radius and 1 mg force. At least three scans were conducted in the center region of each sample to provide the average surface roughness values. The polished surfaces of the WC-17Co and WC-10Co-4Cr coatings were analyzed with a Hitachi Tabletop Scanning Electron Microscope TM3030Plus (SEM) equipped with energy dispersive spectroscopy (EDS) to determine their composition and surface morphology.
The tribological tests were performed with a HFRR manufactured by Compass Instruments. This tribometer was chosen due to its ability to perform high-velocity reciprocating motion experiments. The counter bodies used for tribological experiments were polycrystalline Al
2O
3 balls with a diameter of 6 mm. Al
2O
3 was chosen as the counter body material to minimize wear of the counter body and allow for better analysis of the flat specimens. Ethanol was used as a lubricant for the tribological experiments as a potential low-viscosity (1.08 cSt at 40 ºC) fuel candidate that does not contain any lubricity-enhancing additives [12]. The tribological tests were performed in an ambient environment with a hanging load of 200 g (1.9 N), at a reciprocating frequency of 10 Hz, temperatures of 25 °C and 50 °C, and for a duration of 33 minutes, providing 19,800 reciprocations for each test. The stroke length in the experiments was varied from 0.14 mm, to 0.5 mm, and to 1 mm to provide three different MLV values of 2.8 mm/s, 10 mm/s, and 20 mm/s, respectively. After tribological tests, the counter bodies and flat specimens were rinsed with acetone and isopropyl alcohol and dried. The wear scars on the flat AISI 52100 steel were analyzed with SEM and EDS to determine the extent of oxidation that occurred within the wear tracks.
Results and discussion
The average surface roughness and hardness of the AISI 52100 steel and WC-based coatings were evaluated prior to tribological testing. As seen in Figure 1, the hardness values of the WC-17Co and WC-10Co-4Cr coatings are nearly identical and substantially higher than the hardness of AISI 52100 steel. In addition, the average surface roughness of the WC-based coatings is higher than that of the AISI 52100 steel, however, all the materials’ average surface roughness values were less than 100 nm, which is consistent with the tolerance requirements typical of components within heavy-duty fuel injection systems [5]. The polished surfaces of the WC-based coatings were analyzed with SEM and EDS, prior to tribological testing to assess the chemical composition, surface morphology, and coating thicknesses. In Figures 2 and 3, it is evident that both the WC-based coatings consist of WC particles, which provide high hardness and wear resistance surrounded by a binding metallic phase that provides toughness. In addition, Figures 2(e) and 3(f) indicate that the coatings are several hundred microns thick, even after polishing of the coatings was completed.
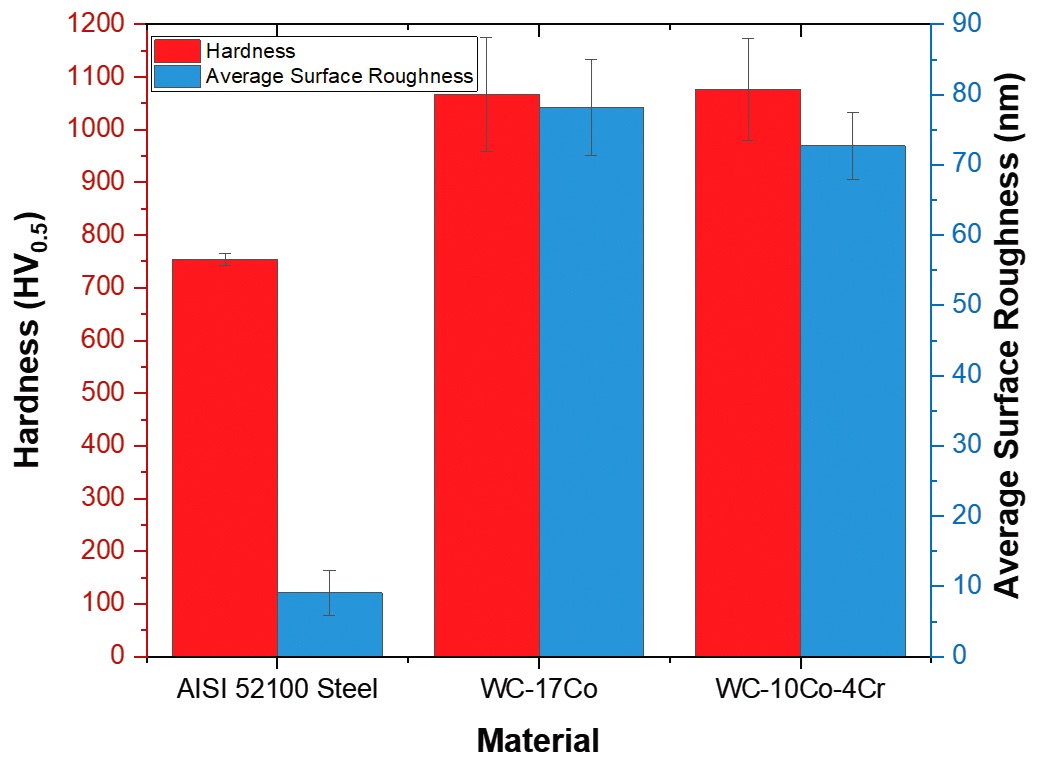
Figure 1. Average surface roughness and hardness values of the AISI 52100 steel, WC-17Co, and WC-10Co-4Cr specimens used in tribological testing.
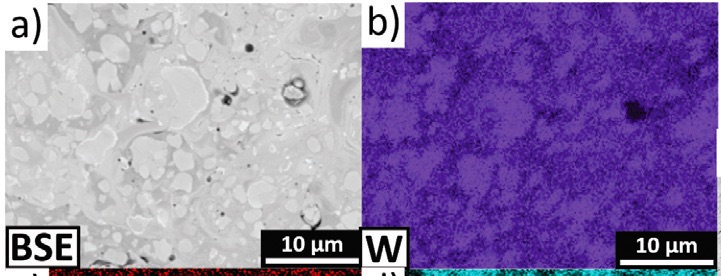

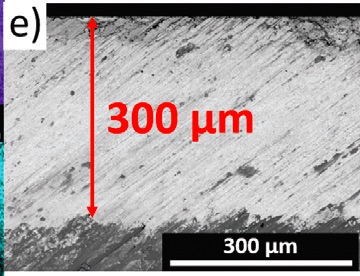
Figure 2. SEM and EDS analysis of the polished WC-17Co coating surface, a) BSE image, b) tungsten EDS map, c) carbon EDS map, and d) cobalt EDS map. e). The thickness of the polished WC-17Co coating shown in BSE image of the coating cross-section.
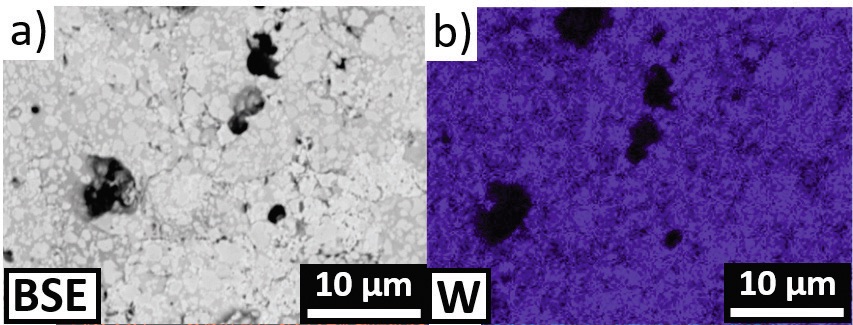
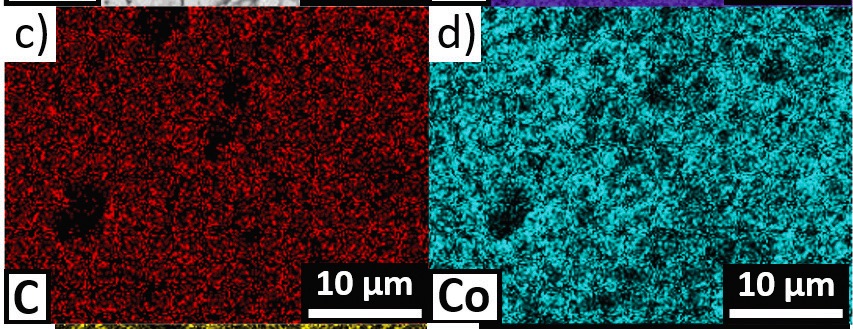
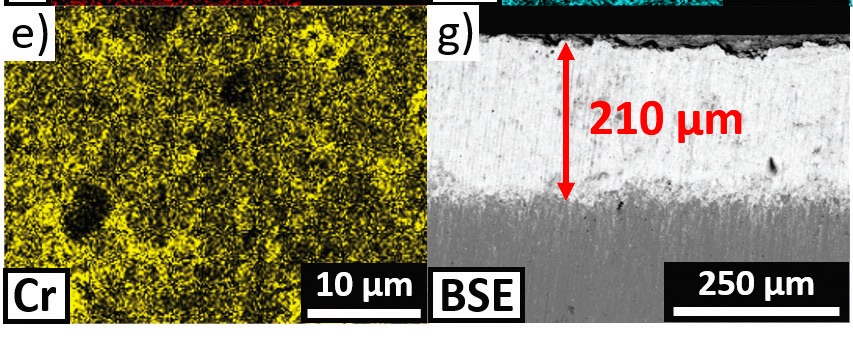
Figure 3. SEM and EDS analysis of the polished WC-10Co-4Cr coating surface, a) BSE image, b) tungsten EDS map, c) carbon EDS map, and d) cobalt EDS map, and e) chromium EDS map. f) The thickness of the polished WC-10Co-4Cr coating is shown in BSE image of the coating cross-section.
The tribological tests were performed with the HFRR setup (
see Figure 4). The HFRR is housed within a home-built enclosed experimental environment that allows for controlled environments and limited vibrations. The coefficient of friction (COF) values for the tribological experiments are shown in Figure 5. The AISI 52100 steel experienced significant increases in the COF when the MLV was increased (
see Figure 5(a) and 5(d)). This increase in COF with increasing MLV is attributed to the greater effects of frictional heating and oxidation experienced by the AISI 52100 steel surface during the higher MLV experiments. The contact geometry of these experiments provides an elastohydrodynamic and/ or mixed lubrication regime, indicating that even at the presence of a protective lubricant film some of the steel asperities experience periodical direct contact with the Al
2O
3 counter body. The low-viscosity of the ethanol and lack of lubricity-aiding additives resulted in these contacting asperities being subjected to frictional heating which led to the oxidation of AISI 52100 steel. This frictional heating was more pronounced as the MLV increased due to insufficient time for the AISI 52100 steel surface to cool, prior to subsequent passes of the counter body. This effect can be clearly seen in Figure 6, which indicates an increase in the oxygen content within the wear scars on the AISI 52100 steel substrate when the MLV was increased for the experiments conducted at 25 °C.
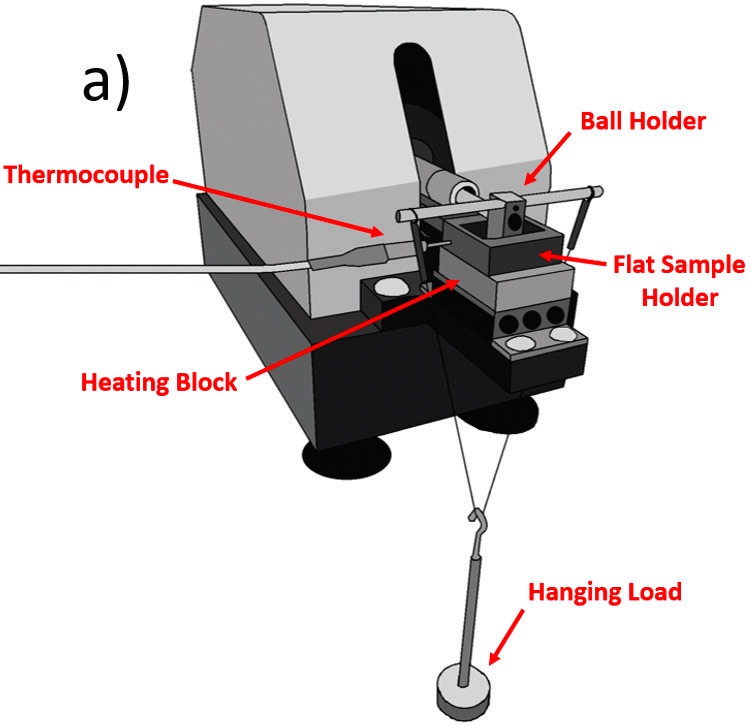
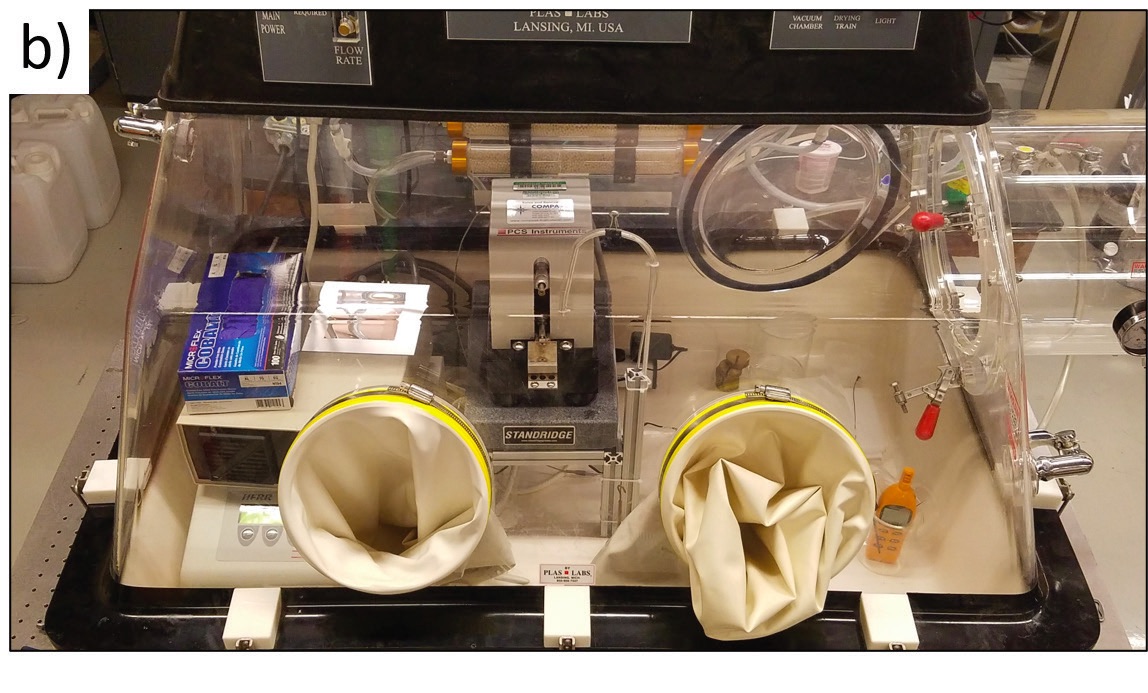
Figure 4. a) Schematic of the HFRR mechanical unit and b) image of the enclosed experimental environment.
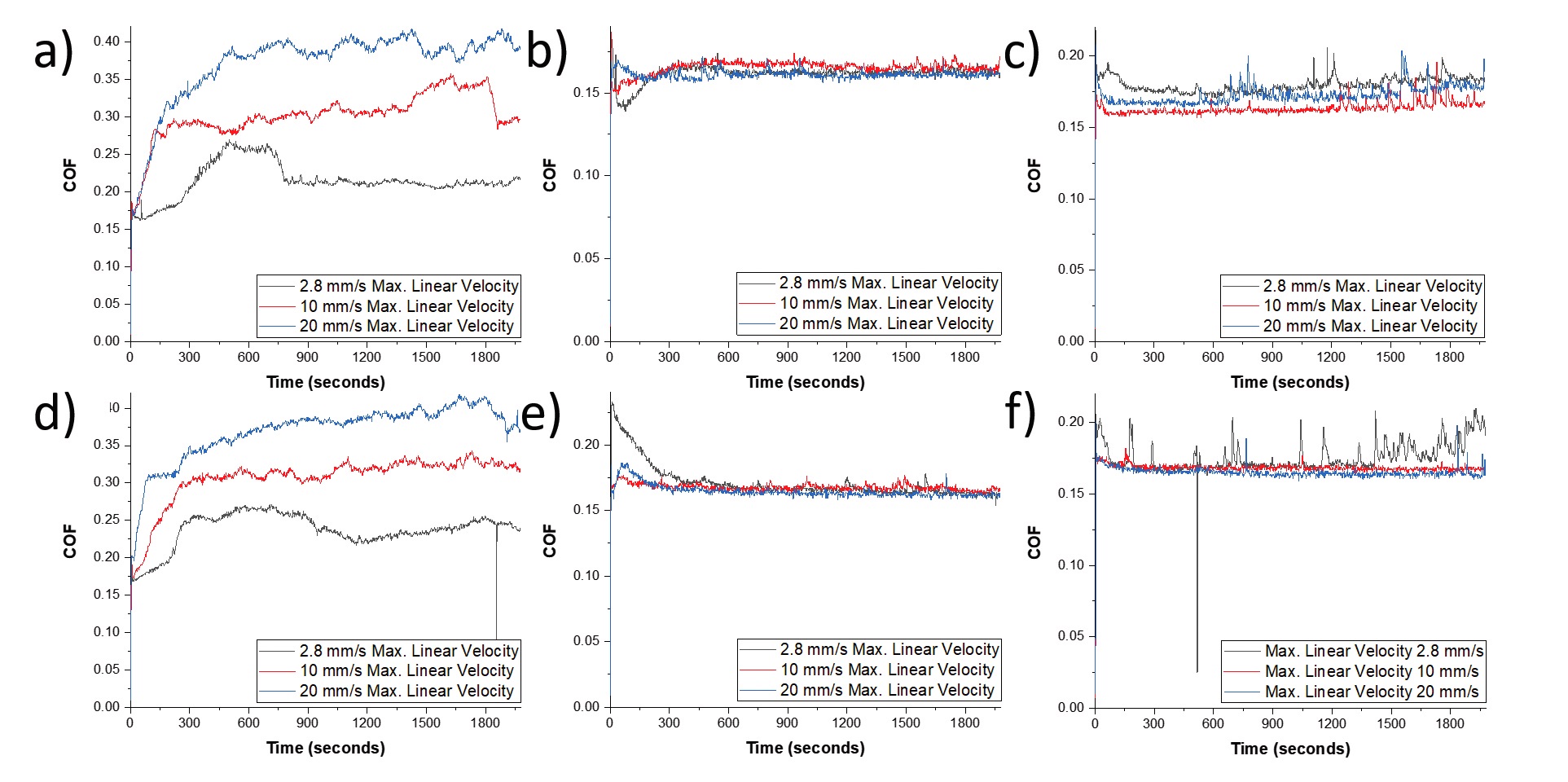
Figure 5. COF vs. Time results for the tribological experiments conducted with a) AISI 52100 steel at 25 °C, b) WC-17Co at 25 °C, c) WC-10Co-4Cr at 25 °C, d) AISI 52100 steel at 50 °C, e) WC-17Co at 50 °C, and f) WC-10Co-4Cr at 50 °C.
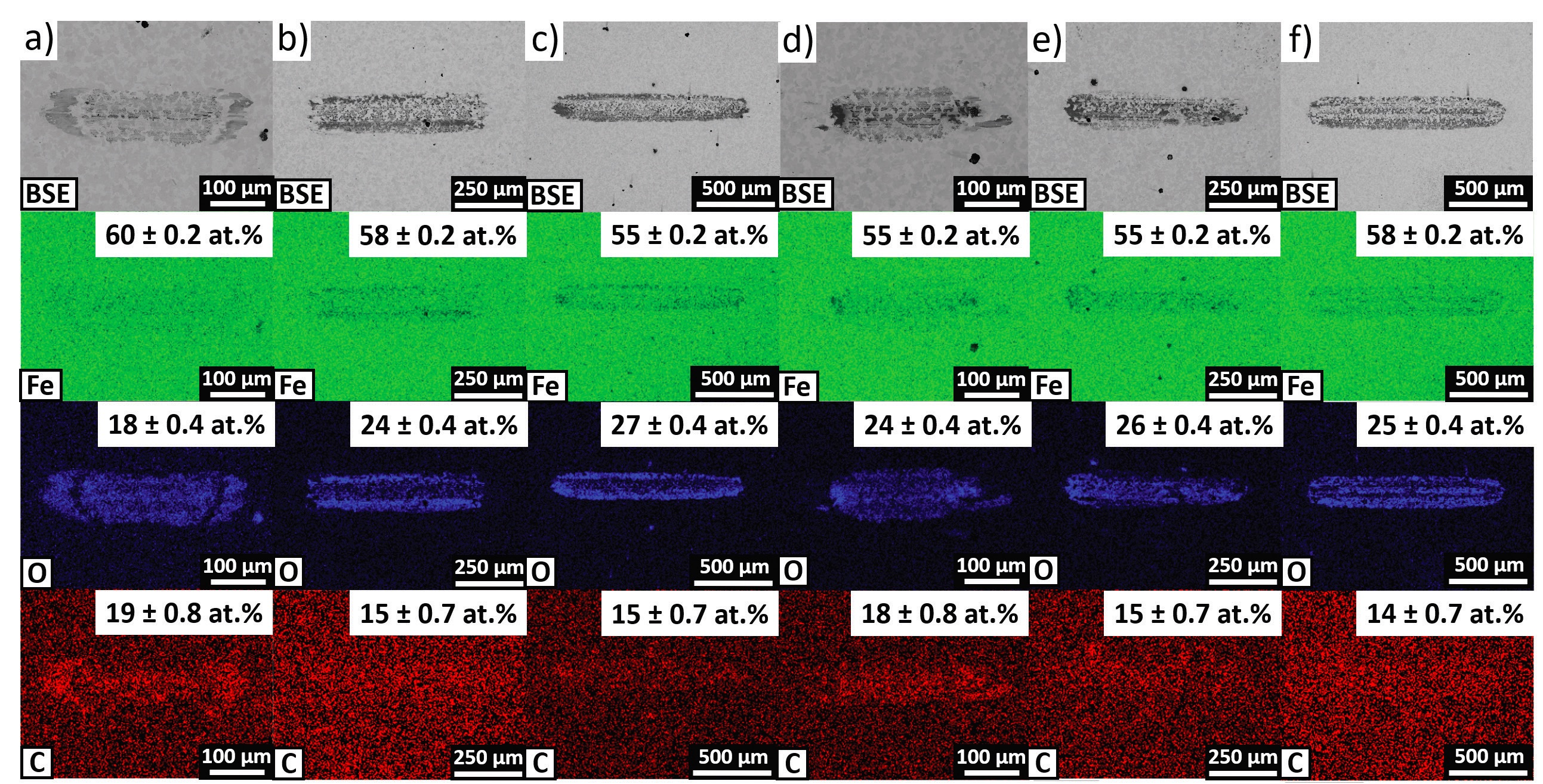
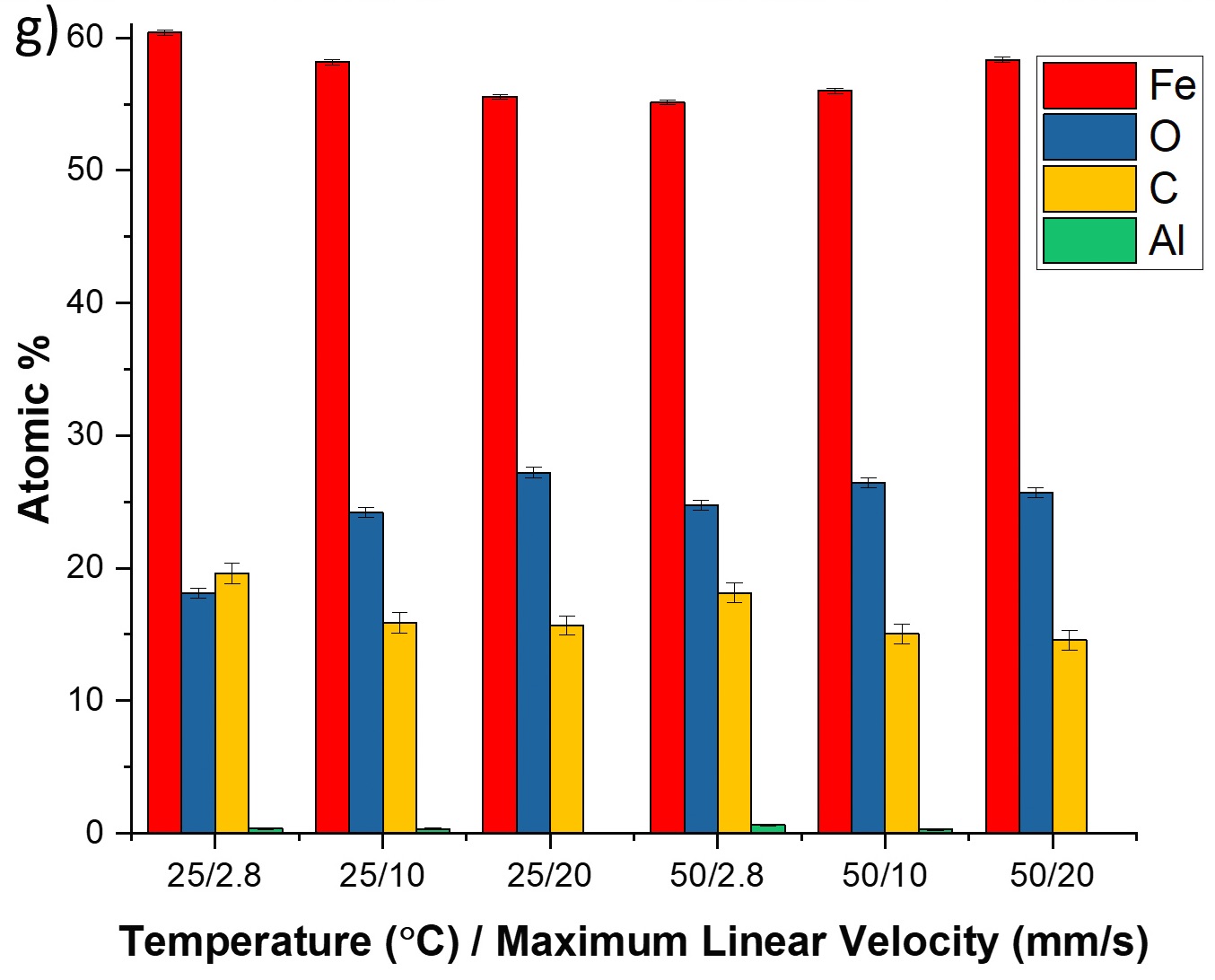
Figure 6. BSE images, iron EDS maps, oxygen EDS maps, and carbon EDS maps (from top to bottom) for experiments conducted on AISI 52100 steel with a) MLV of 2.8 mm/s at 25 °C, b) MLV of 10 mm/s at 25 °C, c) MLV of 20 mm/s at 25 °C, d) MLV of 2.8 mm/s at 50 °C, e) MLV of 10 mm/s at 50 °C, and f) MLV of 20 mm/s at 50°C. The text insets in the upper right corner of each EDS map indicate the atomic percentages within the wear track for the respective elements. g) Atomic percentages of iron, oxygen, carbon, and aluminum within the wear scars produced with tribological experiments conducted on the AISI 52100 flat specimen.
The WC-based coatings did not follow the direct relation between COF and MLV exhibited by the AISI 52100 steel. In the case of WC-17Co, the COF did not vary as much with temperature changes and the tests conducted with a MLV of 20 mm/s provided lower COF values than the tests conducted at 2.8 mm/s for both temperatures (
see Figures 5(b) and 5(e)). Similarly, for WC-10Co-4Cr, the tests conducted at 10 mm/s and 20 mm/s provided lower COF than those conducted at 2.8 mm/s (
see Figures 5(c) and 5(f)). While the frictional heating and oxidation of the AISI 52100 steel surface led to an increase in the COF with increasing MLV, the thermal and mechanical properties of the WC-based coatings allowed for an opposite trend to exist. As the majority of the WC-based coatings consist of ceramic particles with higher hardness and thermal conductivity than AISI 52100 steel, these materials were able to dissipate heat generated due to friction, resist oxidation, and prevent physical deformation more effectively. The ability of the WC-based coatings to maintain the integrity of their surfaces allowed for an increase in the hydrodynamic pressure of the lubricant film formed between sliding interfaces. This increase in film pressure results in a thicker lubricant film that is able to support a greater amount of the load imposed between the contacting materials and, thus, reduce the direct solid-solid contact and, therefore, the friction [8, 9].
Figure 6 shows the effect of the increasing MLV on the amount of oxidation exhibited within the wear tracks on the AISI 52100 steel. The amount of oxygen present within the wear tracks produced during the experiments conducted at 25 ºC increased significantly with increases in the MLV, as seen in Figures 6(a)-6(c) and Figure 6(g). The experiments conducted at 50 °C show a slight increase in the oxygen content of the wear tracks between the 2.8 mm/s experiment and higher velocity experiments (
see Figure 6(d)-6(g)), however, this increase is less pronounced due to the generally higher temperature of the surrounding fuel. These results indicate that the experiments conducted with high MLV values resulted in a greater amount of frictional heating and oxidation of the AISI 52100 steel surface.
Conclusions
In conclusion, the effect of increasing the MLV on the tribological properties and corrosion behavior of AISI 52100 steel, WC-17Co, and WC-10Co-4Cr under ethanol lubrication was examined with high-frequency reciprocating tribological testing. The AISI 52100 steel exhibited greater oxidative wear and COF values with increasing MLV attributed to the frictional heating experienced by the contacting asperities. In contrast, the WC-based coatings showed less variation in COF values and demonstrated a slight decrease in the COF with the MLV increase attributed to the increase in pressure and film thickness in the lubricant formed between the coating surfaces and counter body.
Overall, the superior thermal and mechanical properties of the WC-based coatings provided lower wear and COF values relative to AISI 52100 steel. These results indicate that WC-based coatings are a promising candidate for protection of fuel injection system components, especially in applications that have strict limitations for fuels that compromise their lubrication abilities.
Acknowledgements
The author would like to thank the Society of Tribologists and Lubrication Engineers for awarding the E. Richard Booser Scholarship. This research was financially supported by the Army Research Laboratory under Cooperative Agreement Numbers W911NF-20-2-0060, W911NF-19-2-0281, and W911NF-20-2-0198. The views and conclusions contained in this document are those of the author and should not be interpreted as representing the official policies, either expressed or implied, of the Army Research Laboratory of the U.S. Government. The U.S. Government is authorized to reproduce and distribute reprints for Government purposes notwithstanding any copyright notation herein. Dr. Satish Dixit (Plasma Technologies Inc., USA) is appreciated for supplying the coatings. Additionally, the author appreciates the mentorship and guidance provided by Dr. Diana Berman (University of North Texas) and Dr. Stephen Berkebile (Army Research Laboratory).
REFERENCES
1.
Lacey, P.I. and Lestz, S.J. (1992), “Effect of low-lubricity fuels on diesel injection pumps- Part I: Field performance,”
SAE Technical Paper Series.
2.
Bowman, W.F. and Stachowiak, G.W. (1996), “A review of scuffing models,”
Tribology Letters, 2 (2), pp. 113-131.
3.
Blok, H. (1939), “Seizure-delay” method for determining the seizure protection of ep lubricants,”
SAE Technical Paper Series.
4.
Blok, H. (1987), “Thermo-tribology—fifty years on,”
Institution of Mechanical Engineers, International Conference on Tribology, London,
1, pp. 1-8.
5.
Qu, J., Truhan, J.J., Blau, P.J. and Meyer, H.M. (2005), “Scuffing transition diagrams for heavy duty diesel fuel injector materials in ultra low-sulfur fuel-lubricated environment,”
Wear, 259 (7-12), pp. 1031-1040.
6.
Bhushan, B. (2013),
Introduction to Tribology, Hoboken: John Wiley & Sons.
7.
Ettles, C.M. and Hardie, C.E. (1988), “The friction of some polymers and elastomers at high values of pressure x velocity,”
Journal of Tribology, 110 (4), pp. 678-684.
8.
Thompson, P.M. (2000), “The effect of sliding speed on film thickness and pressure supporting ability of a point contact under zero entrainment velocity conditions,” (doctoral dissertation).
9.
Cousseau, T., Björling, M., Graça, B., Campos, A., Seabra, J. and Larsson, R. (2012), “Film thickness in a ball-on-disc contact lubricated with greases, bleed oils and base oils,”
Tribology International, 53, pp. 53-60.
10.
Cartier, M., McDonnell, L. and Cashell, E. (1991), “Friction of tungsten carbide-cobalt coatings obtained by means of plasma spraying,”
Surface and Coatings Technology, 48 (3), pp. 241-248.
11.
Schwetzke, R. and Kreye, H. (1999), “Microstructure and properties of tungsten carbide coatings sprayed with various high-velocity oxygen fuel spray systems,”
Journal of Thermal Spray Technology, 8 (3), pp. 433-439.
12.
Sivaramprasad, G., Rao, M.V. and Prasad, D.H. (1990), “Density and viscosity of ethanol + 1,2-dichloroethane, ethanol + 1,1,1-trichloroethane, and ethanol + 1,1,2,2-tetrachloroethane binary mixtures,”
Journal of Chemical & Engineering Data, 35 (2), pp. 122-124.
13.
Szeri, A.Z. (1980),
Tribology: Friction, Lubrication and Wear, Washington: Hemisphere.
14.
Tian, X. and Kennedy, F.E. (1993), “Contact surface temperature models for finite bodies in dry and boundary lubricated sliding,”
Journal of Tribology, 115 (3), pp. 411-418.
15.
Archard, J. (1959), “The temperature of rubbing surfaces,”
Wear, 2 (6), pp. 438-455.
16.
Dyson, A. (1976), “The failure of Elastohydrodynamic lubrication of circumferentially ground discs,”
Proceedings of the Institution of Mechanical Engineers, 190 (1), pp. 699-711.
17.
Jiajun, L., Zhiqiang, L. and Yinqian, C. (1990), “The study of scuffing and pitting failure of cam-tappet rubbing pair,”
Wear, 140 (1), pp. 135-147.
18.
Moore, M. (1974), “The relationship between the abrasive wear resistance, hardness and microstructure of ferritic materials,”
Wear, 28 (1), pp. 59-68.
19.
Wagner, J.R., Marotta, E.E., and Paradis, I. (2001), “Thermal modeling of engine components for temperature prediction and fluid flow regulation,”
SAE Technical Paper Series.
20.
Qu, J., Truhan, J.J. and Blau, P.J. (2005), “Investigation of the scuffing characteristics of candidate materials for heavy duty diesel fuel injectors,”
Tribology International, 38 (4), pp. 381-390.
21.
Russ, J.C., Frs, M.A., Kiessling, R. and Charles, J. (2013),
Fundamentals of Energy Dispersive X-Ray Analysis Butterworths Monographs in Materials, Burlington: Elsevier Science.