Screw compressors are common in many commercial and industrial applications because of their high efficiency and reliability to compress a wide variety of gases, including air and natural gas. Rotary screw compressors can be remotely located requiring only minimal service and maintenance while working continuously for weeks, months and even years at a time. Rotary screw compressors are named after the nature of their design: Gas enters a sealed chamber and gets held between the screws, also called rotors, which rotate to reduce the gas volume in order to compress it.
Rotary screw compressors are largely versatile units (
see Figure 1). George Lutzow, manager, SKF application engineering experts for SKF USA Inc., says, “The most common screw compressor designs have two rotors counter rotating with bearings at each end.” There are oil-free and oil-injected designs available to accommodate numerous uses and applications. Oil-injected rotary screw compressors operate with oil injection that seals clearance between the rotors and the cylinders. The oil is necessary to perform several crucial functions, such as cooling, sealing, lubrication and noise reduction. “The oil that lubricates the bearings also is injected into the compression process for cooling, rotor lubrication and to improve efficiency by creating a dynamic seal between the rotors and the compressor housing (
see Figure 2).” He continues, “The oil is critical to separating the rolling and sliding contacts within the bearing. The lubricant also provides corrosion protection and cooling to the bearings.” Although oil-free rotary screw compressors still use lubricants, these lubricants are typically formulated to last the lifetime of the compressor. STLE Past President Dr. Maureen Hunter, technical service manager for King Industries, Inc., explains, “Lubricants are multifunctional, but they are primarily used to reduce friction and wear between moving surfaces.”
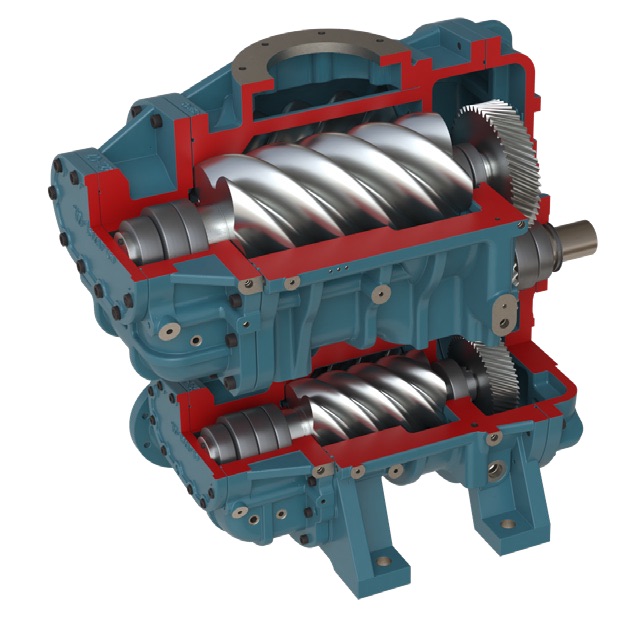
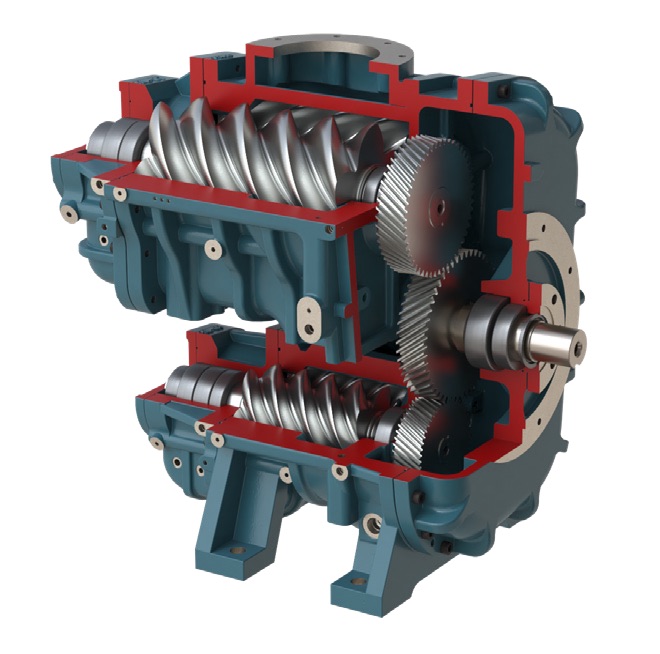
Figure 1. Two-stage rotary screw compressor, SKY2. Figure courtesy of Kaishan Compressor.
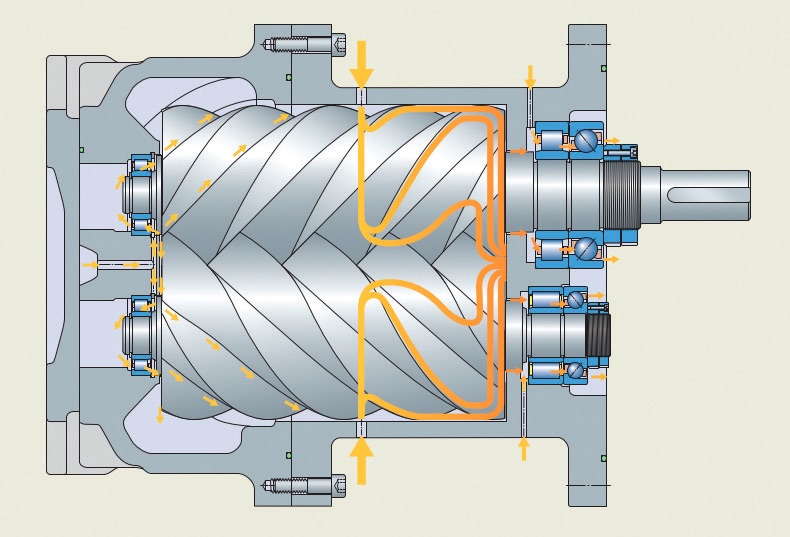
Figure 2. Typical oil injected compressor cross section. Figure courtesy of SKF USA, Inc.
The biggest challenge of rotary screw compressor OEMs is to design them more efficiently, consuming less energy. Nowadays, in industrialized countries, compressors absorb 15%-20% of the total electrical power generated.
1 Energy consumption makes up about 86% of the cost of purchasing and running a rotary screw air compressor for the initial five years.
2 Hence, there is a continuing demand to improve their energy efficiency. An optimum combination of hardware design and lubricant chemistry is being challenged to find solutions.
Different compressor types have different bearing designs (
see example in Figure 3). Typical bearings used in rotary screw compressors are roller, sleeve, ball and journal bearings. The rolling bearings in screw compressors provide precise positioning of the rotors and support rotor loads. Lutzow explains, “Many of the compressor designs have a single bearing on each rotor at the inlet end to support radial load while the discharge ends use a bearing arrangement that supports load in both the radial and axial directions. In operation, the primary force on the rotors is from the compression gases that push the rotors apart from each other and away from the discharge end of the compressor case.” Dr. Yan Tang, general manager for Kaishan Compressor, says, “The loads present on the bearings during startup change from low to high, and the direction could change, too, whereas during the operation, the load level and direction are relatively stable—but the level of the load might have some fluctuation.” Lutzow concurs, “Typically, the bearing loads would be considered moderate. The bearing selection is a balance of trying to have the smallest ‘footprint’ to reduce the space requirements and maintain low friction while also offering a long service life. Many compressor OEMs have a warranty period, and we work to design a bearing solution that will offer service life well beyond that period. As a result, the relative bearing loads are managed to achieve this longer service life.”
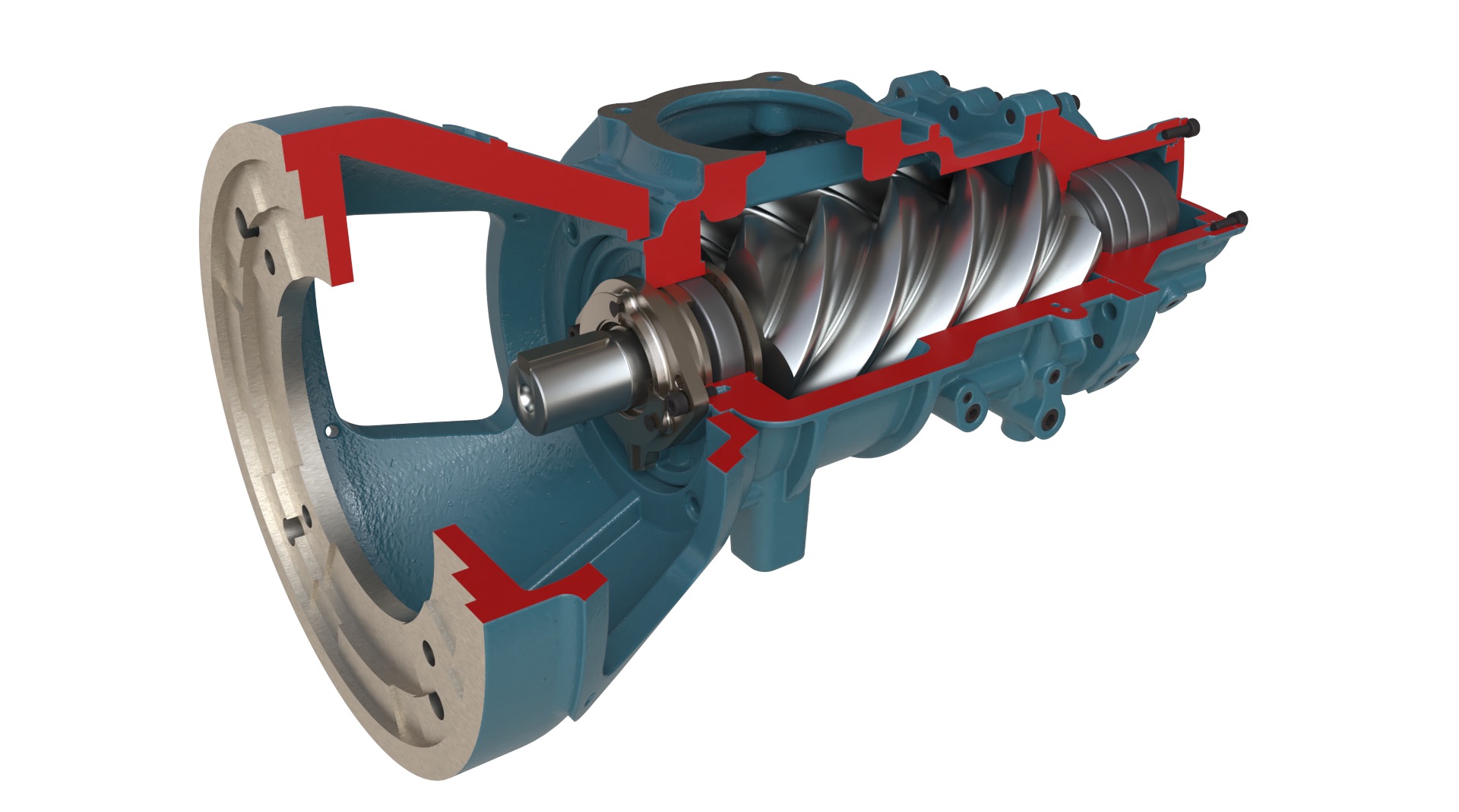
Figure 3. SKY airend – rotary screw airend with four bearing arrangement on discharge: roller, angular contact and ball. Figure courtesy of Kaishan Compressor.
Rotary screw compressor lubricants are formulated with various additives to improve chemical and physical properties of base oils. They help prevent downtime from unscheduled maintenance and extend the life of the equipment. Lutzow says, “Bearing failures in compressors are not very common, and typically most bearings outlive the compressor, but there are some issues that can shorten the expected bearing life. These issues include inadequate lubrication, unforeseen contamination, unexpected loading and/or electrical current passage.”
The blend of selective additives and their amounts in the formulation depend on specific operating conditions. This includes the type of gas compressed and the pressure, compatibility of materials, environmental temperatures and climate zones. Some of these additives can be antiwear (AW), extreme pressure (EP), rust and corrosion inhibitors, antioxidants, detergents, dispersants, pour point depressants, viscosity index improvers antifoam agents, etc. Tang explains that from the rotary screw compressor’s OEM perspective, the bearing lubricant properties that they are most interested in regarding bearing lubrication depend on the application: “The properties such as viscosity, wear protection, corrosion protection and water absorption/demulsibility are all important for a proper lubricant.”
As for water absorption, Lutzow explains, “It’s common for compressor OEMs to design for operation at higher oil temperatures to reduce the moisture content.” He notes that “even water levels as low as 200-500 ppm could start to harm bearing service life.”
While explaining AW and EP effect on demulsibility, Hunter says, “Many AW and EP additives have little negative effect on the demulsibility property of the oil, while others can act as emulsifiers, destroying the demulsibility performance. Other additives might need to be incorporated to overcome the negative effect and improve the demulsibility performance back to that of the oil alone.”
For bearing wear protection, AW and EP additives are utilized. Regarding their differences and typical uses, Hunter explains, “There is no clear distinction regarding the use of the terms
antiwear and
extreme pressure. Both additive types form a large group of chemical additives that protect metal surfaces during boundary lubrication by forming a protective film or barrier that reduces wear of contacting surfaces.”
Hunter continues, “However, one can loosely distinguish between the two types based upon operating speed and load (pressure and temperature). Additives that perform best under milder conditions, typically higher speeds and lower loads, are referred to as AW additives, and those that perform best under more severe conditions, typically lower speeds and high loads (resulting in high temperatures), are EP additives (
see AW and EP Chemistries Explained by Dr. Maureen Hunter).”
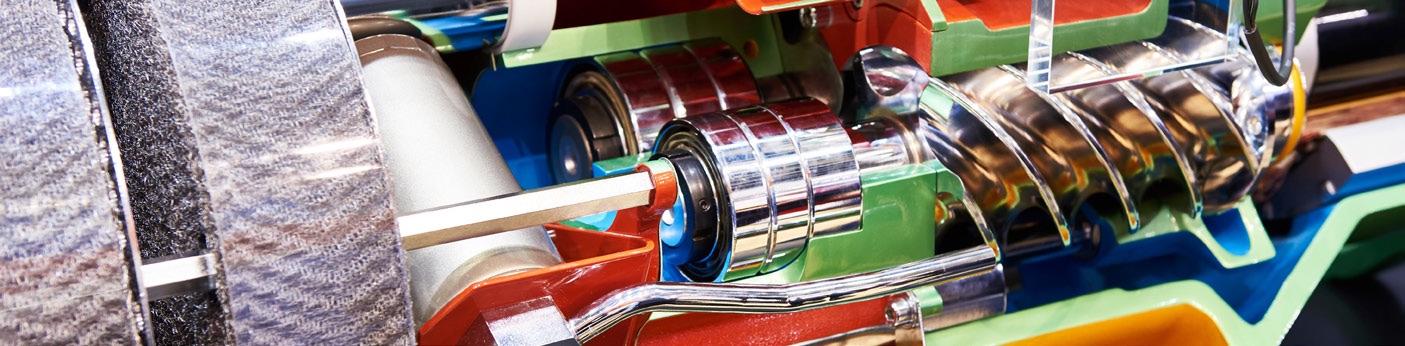
AW and EP chemistries explained by Dr. Maureen Hunter
A wide variety of AW and EP additive chemistries are commercially available and have been reported in the literature and in patents. The more common chemistries are reported below. AW additives are primarily used to protect machine parts from wear and loss of metal. Chemistries typically include:
• Phosphorus additives
– Di- and trialkyl and aryl phosphites
– Dialkyl alkyl phosphonates
– Phosphate esters
•
Phosphorus/nitrogen additives
– Alkyl phosphoric acid – amine salts
•
Sulfur/phosphorus additives
– Dialkyl dithiophosphates
o Metal salts
o Organic esters
– Ashless phosphorothionates and thiophosphates
•
Sulfur/nitrogen additives
– Dialkyl dithiocarbamates
o Metal salts
o Methylene bridged
o Esters.
Many AW additives are polar chemistries that first adsorb on the metal surface and then chemically react with the metal surface under loaded conditions. The films that form also help protect the base oil from oxidation catalyzed by metal ions and help protect the metal from damage by corrosive acids. Some phosphorus-containing AW additives have corrosion-inhibiting properties. Some phosphites, dithiophosphates and dithiocarbamates have secondary antioxidation properties. Phosphate esters are mainly used because of their high-temperature stability and excellent fire-resistance properties.
EP additives are primarily used to inhibit welding and catastrophic seizure of opposing asperities caused by metal-to-metal contact (adhesive wear). Chemistries typically include:
•
Sulfur additives of various total and active sulfur content
– Sulfurized olefins
– Sulfurized esters
– Sulfurized triglycerides (fatty oils)
•
Sulfur/nitrogen additives
– Dimercaptothiadiazoles
– Mercaptobenzothiazoles
•
Sulfur/chlorine additives
•
Chlorinated paraffins.
Many EP chemistries react with the metal surface under high loads that cause high temperatures. Sulfur-containing chemistries are commonly known in the lubricant industry as “sulfur carriers.” The different raw materials used to produce these additives have a significant impact on the properties and performance of the different sulfur carriers. One of the most important characteristics of sulfur carriers is sulfur activity as measured in accordance with the ASTM D1662 test. The active sulfur content primarily depends on the S
1-S
5 chain length in the molecule. Sulfur-containing additives with a very low active sulfur content (1%-1.5%) not only provide EP properties but also provide AW properties and are compatible with yellow metals. Some low active sulfur chemistries also can boost antioxidation properties. Inactive sulfurized triglycerides also can improve a lubricant’s lubricity (friction reduction under low-pressure conditions) by forming a physically adsorbed film on the metal surfaces because of their high polarity. Chlorine-based EP additives are rarely used outside of metalworking applications because of corrosion concerns.
AW additives protect against wear and the loss of metal surfaces, and the EP additives decrease wear due to high localized pressure, preventing seizures. As stated previously, they perform similar functions. Hunter explains, “Both AW and EP additives prevent metal-to-metal contact by forming a film that yields under the shear stress imposed during boundary lubrication conditions. It is the heat from the friction generated between moving surfaces that provides the energy for chemical reaction between the additive and the metal surface to form sacrificial, protective films. These films fill the asperities, thereby reducing friction by preventing metal-to-metal contact, which can prevent surface wear and welding. However, the films are labile at high temperatures and are removed by the moving surfaces in contact. New films must form on the nascent metal for continued protection.” Figure 4 shows the temperatures at which different AW and EP chemistries react to form protective films.
Figure 4. Effective temperature ranges of AW and EP additive chemistries. Figure courtesy of King Industries, Inc., originally created by Rhône-Poulenc.
A specific operational challenge within rotary screw compressor operation can be fluid flow to bearings at compressor startup—and specifically startup at colder ambient temperatures in which boundary or mixed lubrication regimes can occur. Hunter explains, “Boundary lubrication is generally an undesirable condition because there is increased friction and wear, energy losses and material damage. Machinery can experience boundary lubrication during startup and shutdown, even if it normally runs under hydrodynamic conditions.”
Hunter continues, “Under harsh operating conditions of high loads, low speeds and low lubricant viscosity, the lubricant film thickness might decrease to boundary lubrication conditions. This is because the film thickness and surface roughness are about the same dimension. When this occurs, AW and EP additives are needed to protect the surfaces.” The Stribeck curve is used to understand the different boundary lubrication regimes; it also measures efficacy of product friction. The product that demonstrates the lowest coefficient of friction is likely the best choice (
see Figure 5).
3 Hunter explains, “If the hydrodynamic oil film is maintained between the metal surfaces, boundary lubrication, where the two surfaces are mostly in contact with each other, will not occur, and AW and EP additives are not required to perform their function.”
Figure 5. The Stribeck curve demonstrates lubrication regimes; the optimal product is the one with the lowest coefficient of friction through various regimes.
Lutzow explains, “When the operating conditions result in a thin oil film, there is an elevated risk of damage for bearings. Lubricant additives are an option when these conditions occur. However more often the rotor speed, lubricant viscosity and oil flow characteristics of screw compressors generate suitable oil films to separate these surfaces and, as a result, it’s less common for compressor oils to be selected with an additive package. One industry trend that started almost 10 years ago is the practice of slowing the compressor speed as a method of controlling flow. This practice has been managed within the existing bearing solution. However, as environmental regulations are adjusted, greater compressor speed reductions might be required, which would result in greater risk to the oil film thickness. All these factors are considered, and when doing bearing life modeling and calculations, our primary focus is a balance of the bearing required viscosity versus the operating viscosity of the oil at operating temperature.”
As a rule of thumb, for applications in which bearings become exposed to high loads or the operating viscosity is lower than the reference viscosity, oils with EP/AW additives should be used.
4 Tang recommends using AW and EP additives to extend warranty of rotary screw compressors, as the AW and EP additives “extend the service life of the bearings.” However, the formulation of lubricants for rotary screw compressors requires multiple tests to select the right chemistry and to understand its’ effectiveness due to a potential variety of operating conditions. The following properties could be tested:
4
•
Wear by DIN 51819, DIN 51350 pt.5 and ASTM G99
•
Load-carrying capacity by DIN 51350 pt.4 and the Almen-Wieland test machine
•
Friction and wear characteristics by ASTM D6425 and the two-disc test
•
Thermal stability by ASTM D2070.
The impact of EP and AW additives in screw compressor applications should be tested in the finished lubricant under conditions matching end-use applications. Lutzow explains, “EP/AW additives can help limit the fatigue of bearing contacting surface asperities when limited oil film thickness is available. They work by conditioning the material surfaces and offering a protective layer between contacting components. While in many cases these additives can be beneficial, it’s important that testing is completed for each specific operating condition, as there is the possibility for chemical attack on the bearings and compressor components.”
REFERENCES
1.
Abdan, S., Stosic, N., Kovacevic, A., Smith, I., and Deore, P. (2018, November), “Identification and analysis of screw compressor mechanical losses,”
IOP Conference Series: Materials Science and Engineering, 425 (1), p. 012015.
2.
Gardner Denver (2020), “Fixed speed screw air compressor (4-290 kW (5-400HP): L-Series screw compressor. Available
here.
3.
Gresham, R.M. (2017), “What’s a friction modifier?” TLT,
73 (12), pp. 24-25. Available
here.
4.
Schaeffler (2019), “Lubrication of rolling bearings,” p. 81. Available
here.
Dr. Yulia Sosa is a freelance writer based in Peachtree City, Ga. You can contact her at dr.yulia.sosa@gmail.com.