Predictive maintenance polishes up mining
Mary Beckman, Contributing Editor | TLT Mining January 2021
Systems are more cost effective than regularly timed maintenance.
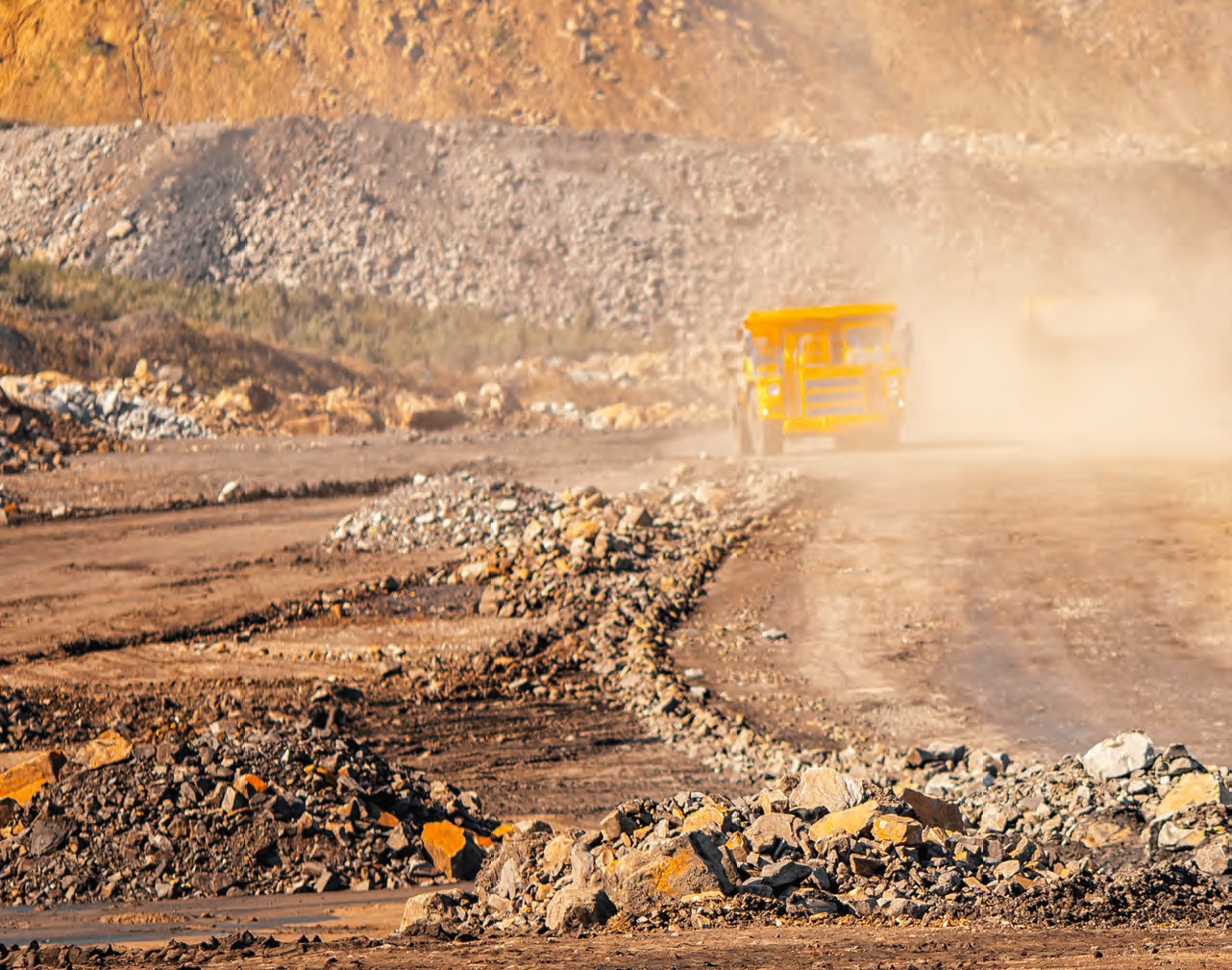
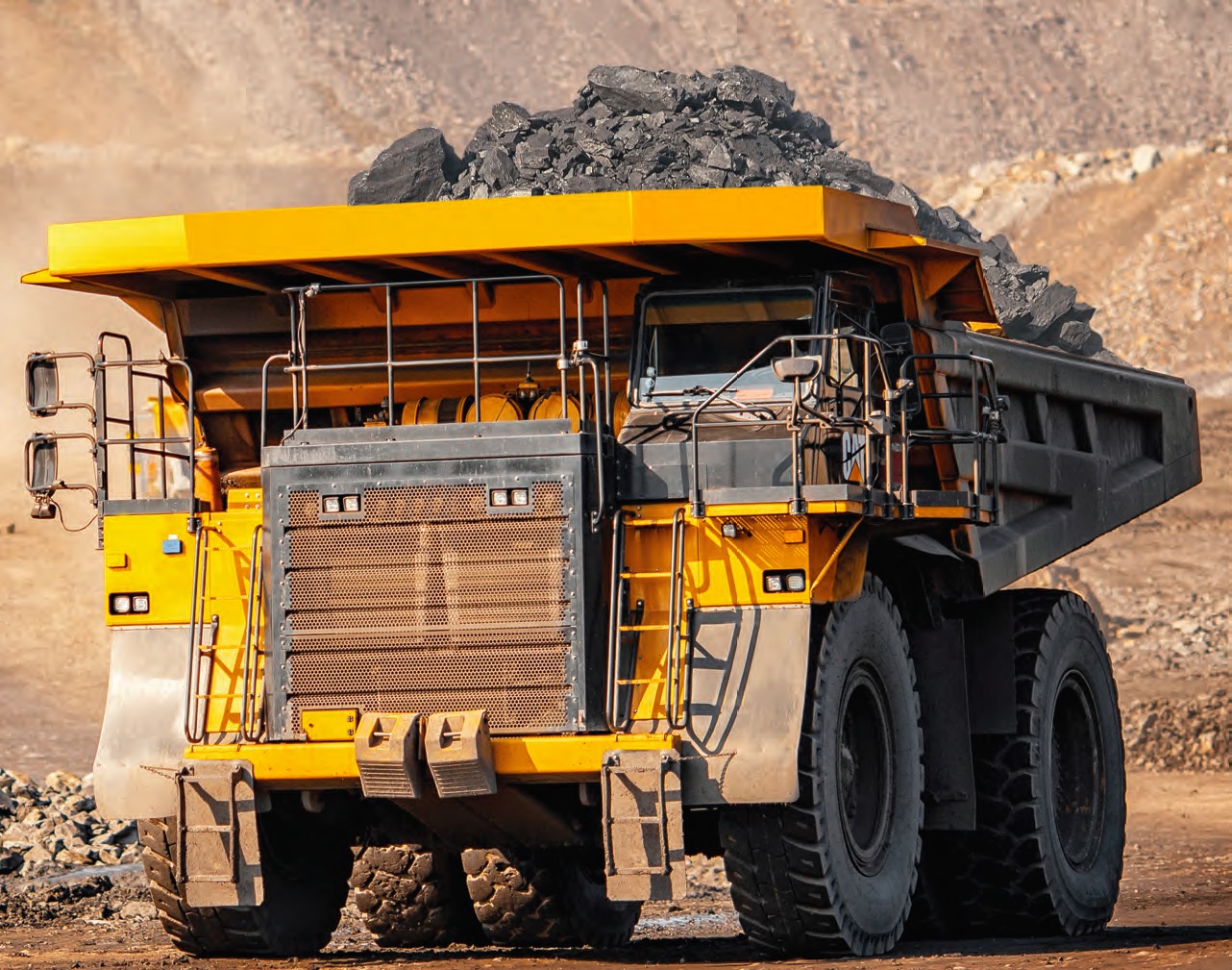
KEY CONCEPTS
•
Predictive maintenance can be more cost effective than preventive maintenance.
•
Scheduled maintenance intervals don’t maximize the life expectancy of the equipment or component.
•
Predictive maintenance reduces human error.
Mining is no longer boxy ore cars, pickaxes and canaries.1 Mining uses massive equipment and huge trucks in expensive operations that can become less profitable if too many machines break down at the same time.
So, mining companies try to keep their equipment running smoothly by employing a preventive maintenance strategy, one that uses planned maintenance schedules. The timing of replacing parts and fluids is generally determined by original equipment manufacturers (OEMs) and sometimes required for warranties. Preventing failures by replacing parts regularly is cheaper than repairing unexpected failures themselves.
But companies are finding that preventive maintenance has some competition—a plan that relies on monitoring the equipment nearly continuously, called predictive maintenance. With the advent of sensors and analytical equipment, a digital eye can be kept on trucks and other mining equipment. When needed, mechanics can swoop in before disaster strikes—or, in some cases, change outs can be delayed until necessary.
Analysts like Jory Maccan see big advantages, but change always requires overcoming resistance.
“The culture of a company can heavily influence how predictive maintenance can be implemented successfully,” says Maccan, reliability fleet analyst at Imperial Oil.
Ethan Clark of Signet Monitoring & Analysis, Inc. says predictive maintenance is valuable enough that he convinced some of his clients to let him use predictive maintenance over preventive maintenance.
“I would say it probably took six months to convince the local equipment distributor. A lot of it depends on the relationship between the equipment owners and local distributor,” he says.
Predicting money saved
Some dollars help predictive maintenance make sense. Sean Gladieux of Caterpillar Global Mining provides an example where predictive maintenance really helped out. A mining truck had some issues with a high-pressure pump, identified by the predictive maintenance system. Although it was not scheduled for maintenance, the company went ahead and took it out of service for 12 hours to fix it, at a cost of about $75,000. If it had failed unexpectedly, the costs would have totaled $990,000-$550,000 in lost productivity, $375,000 for parts and more than $65,000 in labor. That’s close to a million dollars lost for just one truck.2
“Predictive maintenance is certainly more cost effective than preventive maintenance or crash maintenance,” says Clark.
“Predictive maintenance technologies often use sensors to monitor equipment systems. For example, when engine after-treatment systems are close to plugging up,3 we can use onboard exhaust pressure sensors to identify this condition and plan a diesel particulate filter changeout,” says Emlyn Eager, fleet maintenance engineer at BC Transit but formerly of Finning, the world’s largest Caterpillar dealer, where he worked with a lot of mining equipment.
With predictive maintenance, the goal is to identify the failure before it occurs and change the component just prior to the failure. This will maximize the service interval of the component without incurring the added expense of a catastrophic failure in service.
Often service intervals are premature,” says Clark. “Whether it’s the OEM, the engine manufacturer, the bearing supplier or whoever, they want their product to run between routine maintenance checks.”
When there’s a change in the monitoring trend, Clark says, that means either equipment, the cause or the source of the change needs to be investigated and potentially fixed.
Close but not failing
Predictive maintenance overlaps with condition-based maintenance. Predictive-based maintenance uses advanced statistics to get a jump on what data that you might find from condition-based maintenance and catch failures before they happen.
“It’s similar in that you’re targeting changing components at the end of life,” says Eager. “Predictive maintenance monitors equipment and uses symptoms to predict when equipment is about to fail.”
In recent years, predictive maintenance technology has undergone major changes and made significant improvements, according to Eager. Early on, mechanics had to manually download onboard data from mobile equipment. How often workers could do that—or how often they could check on the equipment—depended on how often they could get out to the equipment, or the equipment to them.
Then the systems became WiFi-enabled (or cellular-enabled), and maintenance departments could wirelessly download data onto their computer—often in real time. Now cellular data allows managers to monitor equipment on the move.
“We have been gathering data from a lot of equipment, and this helps us learn and trend the data to understand when failures are going to occur,” says Eager.
Nowadays, the big thing in predictive maintenance is artificial intelligence platforms like computer dashboards that collect data and make decisions, offering suggestions to managers or mechanics.
“It’s the leading edge of what’s happening in the industry and where I see a lot of maintenance programs heading toward,” says Eager.
Preventing unnecessary work
Predictive maintenance can catch potential failures not only before they fail, but also can prevent unnecessary services.
“The intake and the exhaust valves of a mining haul truck offer a great argument for setting up a predictive maintenance system,” says Clark.
A typical 20-cylinder engine will take a worker a 12-hour shift to remove all the valve covers and then set all of the valves. But every time the worker does this, they find not all the valves need fixing.
“What we found is that very few of them actually require setting the valve,” says Clark. “The big advantage to predictive maintenance is it’s usually just two or three valves that need to be adjusted.”
Instead of opening up 20 cylinders and removing valve covers, often you only have to do three or four. Not only are they saving the time that it takes to set three valves compared to a 20-cylinder engine, but there are other advantages as well.
“A 20-cylinder engine—that’s 40 adjustments,” says Clark. “If you’re removing the valve cover, that creates the possibility of contamination from dirt and debris getting in and disturbing the valves. There’s also less chance for human error when you only adjust the intake and exhaust valves that you need to adjust. All of this reduces the chance for mechanical failure as well.”
Ultimately, not all maintenance types benefit from predictive systems, especially if they aren’t cost-effective to handle that way. The OEM will likely keep oil change and air filter maintenance intervals that are time based.
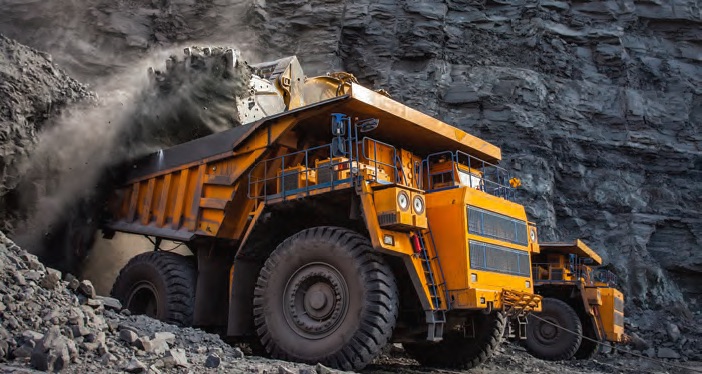
Complex science and technology
One of the more common tools in predictive maintenance is vibration analysis.
“With vibrational analysis, it’s combining two worlds—complex science and a mobile mining world that has never used it,” says Eager.
Vibration analysis is usually performed on stationary equipment. But a mining haul truck comes in for service, at which point it is stationary, says Clark.
“We’ve been looking at the intake and the exhaust valve opening and closing events. So, before the truck is due to come in for a scheduled service, we’ll analyze the intake and exhaust valve opening and closing events and determine how many require valve adjustments. We can take that 12-hour procedure down to two or three hours by setting just the intake and exhaust valves that require adjustment.”
Other predictive maintenance technologies exist that have yet to take hold in mining. For example, Clark says that measuring the exhaust temperature on each cylinder provides a lot of information. “If one cylinder doesn’t get enough fuel, that temperature is going to change,” says Clark. “And the driver in the cab of the truck doesn’t know that one cylinder is cutting out. And now the other 19 cylinders are trying to do the same work that all 20 of them are supposed to do. All he knows is his speed slowed down a little bit, so he puts his foot on the throttle a little bit more.” Although the overall exhaust temperatures are typically measured, keeping track of each cylinder would predict whether there’s a fuel delivery problem.
Clark also is developing systems with torsional analysis, which would tell him when vibration dampeners are starting to deteriorate and fail.
Managers interested in predictive systems would do well to perform a cost-benefit analysis. In the mining industry, time is money. Every second the equipment is up and running means more dollars in the company’s pocket. But other industries, such as public transport, would require a stronger return on investment due to differences in funding.
But the cost-benefit analysis should include not just repair and replacement cost. Component life also should be figured in.
“The big savings aren’t just because you’re catching and preventing catastrophic failures, but you’re running components for their full life instead of trading them out on a schedule that is sometimes premature,” says Clark.
REFERENCES
1. Click here.
2. Click here.
3. Click here.
Mary Beckman is a freelance science writer based in Richland, Wash. You can contact her at mbeckman@nasw.org.