Ultrasound monitoring
Jeanna Van Rensselar, Senior Feature Writer | TLT Best Practices January 2021
With so many applications, this fast and simple condition monitoring tool is proving instrumental for many industries.
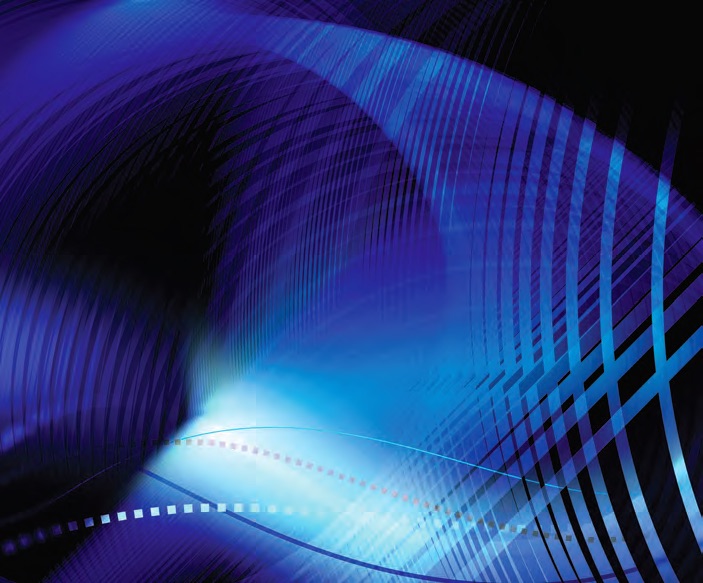
KEY CONCEPTS
•
Ultrasound is any sound pressure wave with a repetition frequency higher than 20 kHz. This characteristic of ultrasound, especially around 30-40 kHz, is particularly noteworthy for inspectors listening for symptoms of asset failure.
•
Ultrasound device manufacturers are always mindful of one of the primary attractions of ultrasound: the favorable ease-of-use/benefit ratio.
•
The average cost of an ultrasound system is $2,500-$20,000. It is not uncommon for an inspector to recover those costs the first time the device is used.
The popularity of ultrasound in machinery maintenance programs is due to ease of use, flexibility and low cost for implementation. While it has been traditionally considered a companion to routine predictive technologies, such as infrared imaging and vibration analysis, standalone ultrasound programs are becoming more mainstream.
In contrast to infrasound and audible sound, ultrasound is any sound pressure wave with a repetition frequency higher than 20 kHz (kiloHertz). This characteristic of ultrasound, especially around 30-40 kHz, is particularly noteworthy for inspectors listening for symptoms of asset failure.
The first signs of change in an asset’s condition can be picked up in ultrasound frequencies. Because of this, in many applications, ultrasound is often the best way to find defects that can lead to asset failure, allowing for remediation before any further deterioration occurs.
Greg Inverso, CMRP, senior regional manager, UE Systems, explains, “Ultrasound equipment detects friction, which is a primary contributor to machinery wear. By frequency tuning, we can detect change in the amplitude (decibels, dBs) and hear the sound quality of the operating equipment. This is done by heterodyning, which will enable us to not only hear the quality of sound but also analyze it. (Heterodyning is defined as combining a high-frequency signal with another to produce a lower frequency signal.) Whether through trending or comparison methods, ultrasound is capable of detecting bearing failures and lack of lubrication and will prevent over-lubrication.”
Ultrasound data collection equipment—usually probes—detects, quantifies and analyzes friction and the potential impact on equipment. It measures compressed air leaks and detects faulty, blocked, leaking and correctly operating steam traps. Users can set alarms that flag the onset of adverse conditions.
Allan Rienstra says, “Ultrasound detectors give condition monitoring technicians superhuman hearing. The plant environment can be very noisy. Ultrasound detectors don’t care. They are tuned to hear higher frequencies exclusively and block out competing sounds from production machinery. Inspections can, therefore, be carried out at any time of day. There is no need to wait for a quiet time to perform a leak inspection, find an electrical anomaly or listen for lubrication problems in rotating machines. Most ultrasound inspectors collect their data during peak production times.”
The equipment and its evolution
Basic ultrasound equipment detects and converts ultrasound to audible sound that can be monitored with headphones. Nearly all ultrasound equipment can create a bar graph display or a decibel measurement. Some ultrasound devices can capture a time-specified wave signal for software analysis. While many additional functionalities are available, manufacturers are always mindful of one of the primary attractions of ultrasound: the favorable ease-of-use/benefit ratio.
Rienstra explains, “Of all the condition monitoring technologies available to maintenance technicians, ultrasound must be considered the one that requires the least amount of training time to produce competent inspectors (
see Compatible Technologies). That being said, at SDT, we are huge promoters of training, especially training that produces conscientious, safe inspectors.”
Compatible technologies
Allan Rienstra says that ultrasound is considered by many to be closely symbiotic with several technologies. Over the years, SDT has mapped performance with vibration analysis, infrared thermography and oil analysis and noted that decisions are enhanced by inspections that include two or more complementary techniques.
•
Vibration analysis. Ultrasound and vibration analysis form the most complete alliance for condition monitoring. Ultrasound finds bearing failures at very early stages (stage 1 and stage 2), while vibration only notes anomalies as they enter stage 3 and 4. Since ultrasound can be performed by a less experienced inspector, ultrasound is an excellent first line of defense against early bearing failure, especially failures that are caused by poor lubrication practices. While vibration analysis is not ideal for assets that rotate slowly (less than 300 RPM), ultrasound will provide insights on these low-energy, low-friction and low-impact defects.
•
Infrared. “These two technologies allow you to, ‘hear what you cannot see and see what you cannot hear,’” Rienstra says. When inspecting electrical systems, he recommends using ultrasound prior to opening high voltage cabinets or moving close to substation components. Partial discharge is prevalent in these assets but doesn’t always generate heat that is visible with a thermal camera. Moreover, sudden changes in environment can create a dangerous arc flash event. It is better to keep panels closed and inspect them with ultrasound from the safe side and at a distance.
Inverso says, “It’s very useful for plant technicians. With a holster, you can keep your hands free for lubrication. It’s as simple as watching your dBs on your device and, as they go down, not only will the dBs go down, but it will also get quieter in your headset. You stop lubing once your dBs stop going down. It’s that simple. If you have a condition-based system, it will tell the tech which equipment needs lube and which doesn’t. This will free up valuable time for other things.”
What it detects
The RMS (root mean square), or effective value, defines the energy in the signal. It is a reliable metric since it is both stable and repeatable. Rienstra explains that, quipped with high-frequency piezo-ceramic crystals, sensors detect sources of low-frequency ultrasound (around 40 kHz) that are then converted to corresponding audible signals. During this heterodyning conversion, the qualities and characteristics of the original ultrasound are preserved, thereby giving humans the ability to hear sounds far beyond their normal range.
“Ultrasound detectors have evolved in leaps and bounds in the past 10 years,” Rienstra says. “There are two innovations that should be considered significant contributions to the utilization of ultrasound as a frontline defense against unplanned downtime. The first is dynamic signal analysis, for which continuous data is acquired for a user-defined time frame. The second is the advent of four static condition indicators.”
These four indicators are:
•
Overall RMS. This displays the RMS average dBμV (decibels-microvolt) value for the entire acquisition time, providing guidance about the bearing’s lubrication condition as well as a comparative trend against previous measurements.
• Max RMS. This takes the overall RMS and breaks it down into quarter second samples. If the acquisition time is set to three seconds, that means there will be 12 blocks of quarter second samples. The loudest of the 12 is the max RMS and is a good indication of signal stability for the duration of the acquisition time.
•
Peak. This is the single loudest measured value for the acquisition time. It is the loudest of 24,000 possible measurement samples. High peak values indicate impacting as the probable cause of high overall RMS dBμV values and would lead to the conclusion that there are defects present in the asset.
•
Crest factor. This is a linear ratio between peak and overall RMS and is designed to return a comparison that tracks impacting relative to friction. When overall RMS rises, but peak does not, this is indicative of friction. When peak rises without overall RMS, this is indicative of impacting. When they rise together, it is indicative of early stage failure. When overall RMS continues to rise and peak falls, the failure defects are then critical.
Misconceptions
Following are some misconceptions about ultrasound technology that STLE member Allan Rienstra, director of international business development, SDT Ultrasound Solutions, has experienced over his 30 years in this industry:
•
Expecting to find pressure and vacuum leaks beyond the threshold of the instrument’s capabilities. Ultrasound detectors work well for compressed air and vacuum leaks as long as there is enough difference in pressure to produce turbulence. Very small leaks such as those associated with refrigerant in air conditioning systems, unless the system is very large, are not detectable with ultrasound.
•
Believing that ultrasound is the only condition monitoring technology needed or that ultrasound is “the best” for any given inspection.
•
Believing that ultrasound requires no training. While ultrasound is indeed simple to use, it does require training—especially safety training.
Applications
Ultrasound is incredibly versatile. “The biggest misconception is that ultrasound is just used for leak detection (
see Misconceptions above),” Inverso says. “In fact, ultrasound is not just used for leak detection but also for electrical inspections and various mechanical applications, including bearings, pumps, valves and steam traps (
see Real-World Applications). In addition, if you looked at an I-P-F chart for condition-based monitoring, ultrasound is the first indication of an issue.”
Real-world applications
Greg Inverso has been in the industry for nearly 10 years and has witnessed the many benefits of ultrasound. One instance that stands out involved a facility that was on a time-based lubrication schedule with one piece of equipment failing well before it should—a bearing was failing every nine months.
“The customer was following the manufacturer’s guideline for lubrication by putting in a specific amount of lube after every 700 hours of operation,” Inverso explains. “Just by lubing that equipment more frequently and putting in the correct amount of lube using an ultrasonic grease caddy, they increased the asset life five times (
see Figure 1).”
Another example Inverso cites is a company that instituted a condition-based monitoring system. “Within a few months, we found two things,” he says. “First, we found a 24% reduction in the amount of grease they were using. Second, we found a bearing that was in failure mode. We detected this fault by analyzing, not only the increase in dBs from our baselines, but also by recording the sound wave and analyzing with our software to determine it was an outer race problem.”
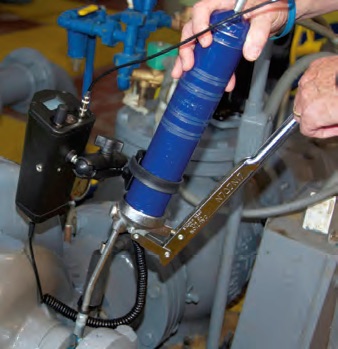
Figure 1. UP digital grease caddy lubricating a bearing. Figure courtesy of UE Systems, Inc.
Common industry-specific applications
•
Mechanical condition monitoring. Bearing defects cause friction and impacting. Lubrication issues, under-lubrication or over-lubrication, lead to increased bearing friction and eventually impacting. These faults can be detected with ultrasound before the bearing reaches the point of no return and while corrective maintenance can still be performed.
•
Bearing lubrication monitoring. Lubrication reduces unwanted friction and metal-to-metal contact. Ultrasound excels at detecting friction, impact and turbulence—flagging increased levels of friction, resulting from subpar lubrication conditions.
•
Air and gas leak detection. When compressed air flows through a leak, it produces turbulence and the characteristic high-frequency hissing. While the hissing is audible in isolation, it can be very difficult to hear on a noisy production floor. Ultrasound is easier and more effective at detecting air leaks than other traditional tests.
•
Electrical fault detection. Ultrasound is effective for both open and enclosed electrical equipment across a range of voltages. Electrical apparatuses such as switchgears, transformers, insulators or disconnects and splices can all fail, but before they do, faults can be detected. Unlike electrical infrared thermography inspection, ultrasound devices can detect discharges in their earliest stages, long before they begin to generate heat.
•
Steam trap testing. When steam flows through steam traps and piping, it can create a turbulent flow. Ultrasound can detect that turbulence, even through dense piping.
•
Valve condition monitoring. Ultrasonic inspection can quickly identify functioning and malfunctioning valves so they can be tagged and repaired quickly to avoid diminished production.
•
Hydraulic systems monitoring. It’s counterintuitive, but internal leakages are actually more detectable with ultrasound than external leakages. Installing an ultrasound contact sensor above, on and below the direction of flow will detect turbulence.
•
Tank tightness testing. Ultrasonic tightness testing involves collecting and amplifying the sounds generated by leaks that contribute to the depressurization of the tank.
•
Marine applications. Since ultrasound equipment is so versatile and adaptable, it makes sense in applications that are mobile and remote, checking all necessary deck, engine, electric, cargo and safety-related equipment.
Gianfranco (John) Spampinato, head of maintenance at the LANXESS Corp. Fords, N.J. site, explains, “Utility leaks can cost hundreds of dollars in lost revenue. Loss of vacuum is difficult to troubleshoot slowing down our operation with some leaks causing discoloration of our product, requiring costly rework. Due to the hundreds of miles of pipes on site, which are located 20 feet above the ground, it was difficult to determine where the leak was originating. We began using an ultrasound probe 18 years ago to help locate air, nitrogen and steam leaks. An additional new device by UE Systems was purchased two years ago to assist in finding vacuum leaks on our reactors (
see Figure 2).”
Figure 2. UE Systems’ new device running bearing condition monitoring routes. Figure courtesy of UE Systems, Inc.
Conclusions
“The ROI for ultrasound is rather immediate,” Rienstra points out. “The average cost of a system is $2,500-$20,000. It is not uncommon for an inspector to recover those costs the first time the device is used. The easiest way to realize ROI is through compressed air leak management. It is not unreasonable to reduce an organization’s energy bill in the compressor room by 30% through a concerted effort to reduce leaks.”
To sum up the benefits, Inverso concludes, “With ultrasound, you will see an immediate reduction in lubrication cost and cost avoidance in not only machinery failures but just as important downtime at the facility. These cost benefits can be immediate and astronomical, depending on the facility. Ultrasound is an excellent way to gauge equipment health—whether you just want to lubricate correctly or you want to have a condition-based monitoring system.”
Jeanna Van Rensselar heads her own communication/public relations firm, Smart PR Communications, in Naperville, Ill. You can reach her at jeanna@smartprcommunications.com.