Used oil analysis
Lynne Peskoe-Yang, Contributing Editor | TLT Lubrication Fundamentals November 2020
While oil has a limited lifetime, analysis can help diagnose a multitude of issues.
Used oil analysis, or UOA, is a series of physical and electrochemical tests on a sample of used oil to learn about both the oil performance and the condition of the rest of the machine. Typical tests include the use of a spectrograph, which detects and measures specific elements in the sample; a ferrograph, which pumps the sample across a magnetic field and sorts iron-containing wear particles by size; and various means of pH and viscosity testing to analyze the quality of the oil itself.
The telltale lubricant
The purpose of used oil analysis is primarily to examine the effect of usage on the oil. Oil itself has a limited lifetime and shows characteristic signs when it nears the end of its peak performance. A lubricant’s most important quality is its viscosity, which tends to decrease over time with use, overheating and contamination, leading to potentially disastrous results. “If the oil is too thin, loss of oil pressure and metal-to-metal contact will occur,” explains Edward Eckert, tribology diagnostics manager at ALS Global. Used oil analysis also can point technicians to oil-related maintenance issues, including the tendency to wait too long between oil drains.
The secondary purpose of UOA is to provide information about the less accessible components in the asset. “UOA also can pick out issues related to environmental ingress, coolant leaks, fuel system concerns, overheating [and] cross-contamination with another lubricant,” says STLE-member Roger L. Young, a senior field technical advisor for Imperial Oil. As the oil moves through the system, it picks up debris, including metals from internal wear and contamination from other systems or from the outside environment. These events leave characteristic traces in the used oil. By testing the pre-circulated fluid, technicians can diagnose a multitude of engine issues, as well as minimize wastage and overuse of the oil itself.
A diagnostic battery
Elemental analysis, a key component of used oil analysis, can reveal problems throughout the machine long before they become emergencies. Technicians use spectrographs to determine the relative presence of trace elements in the sample and to identify residue from various internal problems, including component breakdown, intrusion from internal systems like coolants and other fluids and contamination from the environment.
Each problem leaves traces in the used oil sample. Elevated iron, aluminum and chromium levels, for example, “would indicate cylinder wear and possible piston scuffing,” as many pistons are made from these metals, Eckert says. Other combinations must be compared to data from the rest of the engine. High levels of lead and copper together, with or without elevated tin, suggest bearing wear, while the presence of both excessive aluminum and potassium is difficult to read without insight about the age and condition of the engine.
To diagnose external contamination, UOA technicians look for the hallmarks of the most common and destructive contaminants first, including soot, fuel, coolant and oxidation byproducts. But the most dangerous substance that finds its way into the sample is more familiar. “Dirt is the most severe type of contamination, as dirt is abrasive and will ‘dust’ the engine in no time,” warns Eckert. The composition of dirt actually varies by location, typically a 3-4:1 ratio of silicon to aluminum, depending on geography. Thus, even the location of the engine’s operation is essential information for proper UOA.
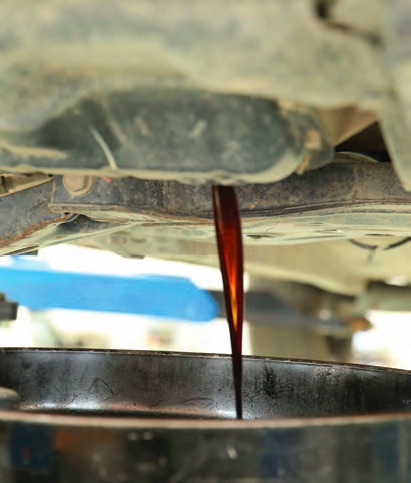
Sample etiquette
“There are many factors that can affect accuracy such as workforce experience, training, technique, work environment and even proper tools and resources to do the job correctly,” Young explains. “Depending on how the sample was affected, it can make the results slightly unreliable or a total loss.” The most common problems with UOA samples include mislabeling, contamination and mistakenly sampling filtered oil or oil from the wrong place in the system. “If the sample is contaminated by the environment, the results could indicate false positives for contamination,” says Young.
However, “it is easy for a seasoned individual to recognize when a sample is a bad sample,” says Eckert. For example, the sample might be too clean, the results might not fit the trends for this particular machine, or there might be traces of brand-new chemicals in the oil, which would suggest a mislabeled sample. All these insights depend on full knowledge of not only the materials involved but the effects of usage on previous oil samples.
Oil behavior in different applications can vary widely, even if the lubricants are the same. “Knowing the make and model of the engine is extremely important in the evaluation of an engine sample,” explains Eckert. Problems like fuel dilution, overheating and excessive soot leave characteristic traces in the UOA sample depending on the way they manifest in a particular engine, providing more clues to the technician seeking to diagnose the issue.
Baseline measurements, like an analysis of an unused sample of the same oil in the UOA sample, also can help technicians isolate and diagnose problems that might otherwise be hidden by quirks of the machine or its environment.
Customer education
Unfortunately, the measurements are only useful if they come from consistent samples. For engine diagnostics, change over time is itself an important metric. The best UOA insights come from technicians who have all available information on the specific machine application, the oil used and the trends from previous UOAs on an accurate timeline. As Eckert tells customers, when analyzing the results of a UOA, “the trend is your friend.”
The OEM has the final word on where, how and how often each oil should be sampled, but other information can supplement the manufacturer’s knowledge to help customers care for a specific application. Young and Eckert both regularly direct customers to explanatory videos and articles to see how professionals conduct UOAs in similar settings. As a technical advisor, Young also gives seminars on lubrication technology where sample best practices are discussed and demonstrated.
For Eckert, education is the key to correct sampling practice. “When samples are not taken properly, it is due mostly to lack of training and education in how to properly take an oil sample. Being consistent, taking the sample from the same place and practicing good sampling techniques will ensure quality and reliable data from the lab.”
Lynne Peskoe-Yang is a freelance writer based in Tarrytown, N.Y. You can contact her at lynnepeskoeyang@gmail.com.