In 2019, 7.3% of U.S. energy demand was met by wind energy, with that percentage predicted to increase to 20% by 2030.
Reducing premature bearing failures in wind turbines will make wind energy more cost competitive and reliable.
White etching cracks (WECs) and other bearing failure modes are being studied to identify causes and preventions.
With ever increasing energy requirements, the energy sector is seeing an unparalleled growth in renewable energy production, with wind energy in the lead. Land-based, utility-scale wind farms offer the lowest priced energy source currently available at between two to six cents per kilowatt-hour.
5
As of the fourth quarter 2019, the American Wind Energy Association reported there are 105,583 megawatts of wind energy operating in the U.S. with more than 59,800 wind turbines spinning across 41 states and two U.S. territories.
4 In 2019, 7.3% of U.S. energy demand was met using wind energy.
1 This percentage could be increased to 20% by 2030 and to 35% by 2050.
2
A wind turbine creates electricity when wind flows across the turbine blade and spins the rotor. The rotor is connected to a generator directly in a direct drive turbine or through a shaft and a series of gears (i.e., a gearbox) that speed up the rotation and allow for a physically smaller generator (
see Figure 1).
15 This translation of aerodynamic force to rotation of a generator is what creates electricity.
Figure 1. Simplified view of components of an upwind-facing, horizontal-axis wind turbine with agearbox drive.15 Figure courtesy of Union of Concerned Scientists, www.ucsusa.org.
Wind patterns across the globe vary over the year and can be unpredictable at times, with this variability in wind leading to fluctuating loads on wind turbine components. A typical wind turbine consists of more than a dozen bearings that are expected to work simultaneously and continuously for many years. As a result, wind turbine bearings and gearboxes are often susceptible to failure well before their designed service lives.
Bearing failures in wind turbines are a major cause of downtime in energy production for unplanned maintenance, repairs and replacements. This failure type is a primary cost and results in higher operations and maintenance (O&M) costs for the energy operator and in higher utility bills for the customer. The National Renewable Energy Laboratory’s (NREL) Gearbox Reliability Database (GRD) shows that 76% of gearboxes failed due to bearings, while 17% failed due to gear failures.
11 This shows the importance of reliable bearings and gearboxes for wind turbine operations to the economy and society.
Wind turbine bearings
The gearbox in a wind turbine consists of several bearings that translate the wind energy from the spinning blades into electrical energy (
see Figure 1). In the 21st Century, bearings are one of the most critical mechanical/tribological components used in a wide range of applications, including aerospace, automotive, energy, medical devices, sporting equipment and so on.
Wind turbine drivetrains include different types of bearings (
see Table 1). Bearings and gearboxes in wind turbines are designed and certified to last for at least 20 years; however, only a small percentage survive that long in the field. As a result, many bearing OEMs are taking special interest in bearings used in wind turbine applications with the desire to design stronger, tougher and more reliable bearings.
Table 1. Different bearing types used in wind turbine drivetrains
Source: Adapted from Andrew, J.M. (2019), "Fundamentals of wind turbines," TLT, 75 (8), pp. 32-40. Available here.
STLE-member Shawn Sheng, a senior engineer at NREL in Golden, Colo., notes that while gearboxes “do not fail as often as electronic components in a turbine, they appear to be the costliest to maintain throughout a turbine’s 20-year design life.” If not detected and mitigated early enough, Sheng says that these failures “can lead to entire replacement of these gearboxes, which require costly crane rental expense, in addition to revenue loss, capital cost on new or upgraded components, labor and other costs, which dramatically increase the cost of energy for wind power, impacting offshore wind even more.”
In 2007, NREL established the Gearbox Reliability Collaborative (GRC) to foster understanding of the root causes of premature gearbox failures and to improve gearbox reliability.
6 GRC research has found that the faults in most prematurely failed gearboxes are related to bearing failures in the intermediate and high-speed sections, with much of that failure occurring in as little as 5%-20% of the bearing’s design life.
6
STLE-member Harpal Singh, principal engineer at Sentient Science in West Lafayette, Ind., states, “Bearings are key elements that enable rotational motion and support radial and axial loads in a wind turbine.” Singh notes that bearing failures in wind turbines can be expensive due to lost production, replacement component costs and maintenance costs, with the total cost of wind turbine gearbox replacement varying depending on the turbine location, turbine type, gearbox type, etc. Gearbox failures on land-based turbines are assumed “to cost about $250,000-$300,000 per failure event.”
Types of bearing failures in wind turbines
Sheng reports that NREL’s research “tries to help industry improve wind turbine drivetrain reliability, both inherent and operational, through testing, modeling/analysis, failure mode investigation and O&M research, leading to reduced O&M cost and making wind power more cost competitive.” Sheng focuses on failure data collection and statistical analysis, fault diagnostics and prognostics research.
NREL’s research on wind power reliability focuses on gearboxes, blades and how turbines interact with the electric grid.
14 NREL collects gearbox failure data in its GRD, whose goal is to quantify the magnitude of the problem and identify top failure modes and root causes, while directing wind turbine gearbox reliability research and development and providing a benchmark for evaluating technology advancements.
11
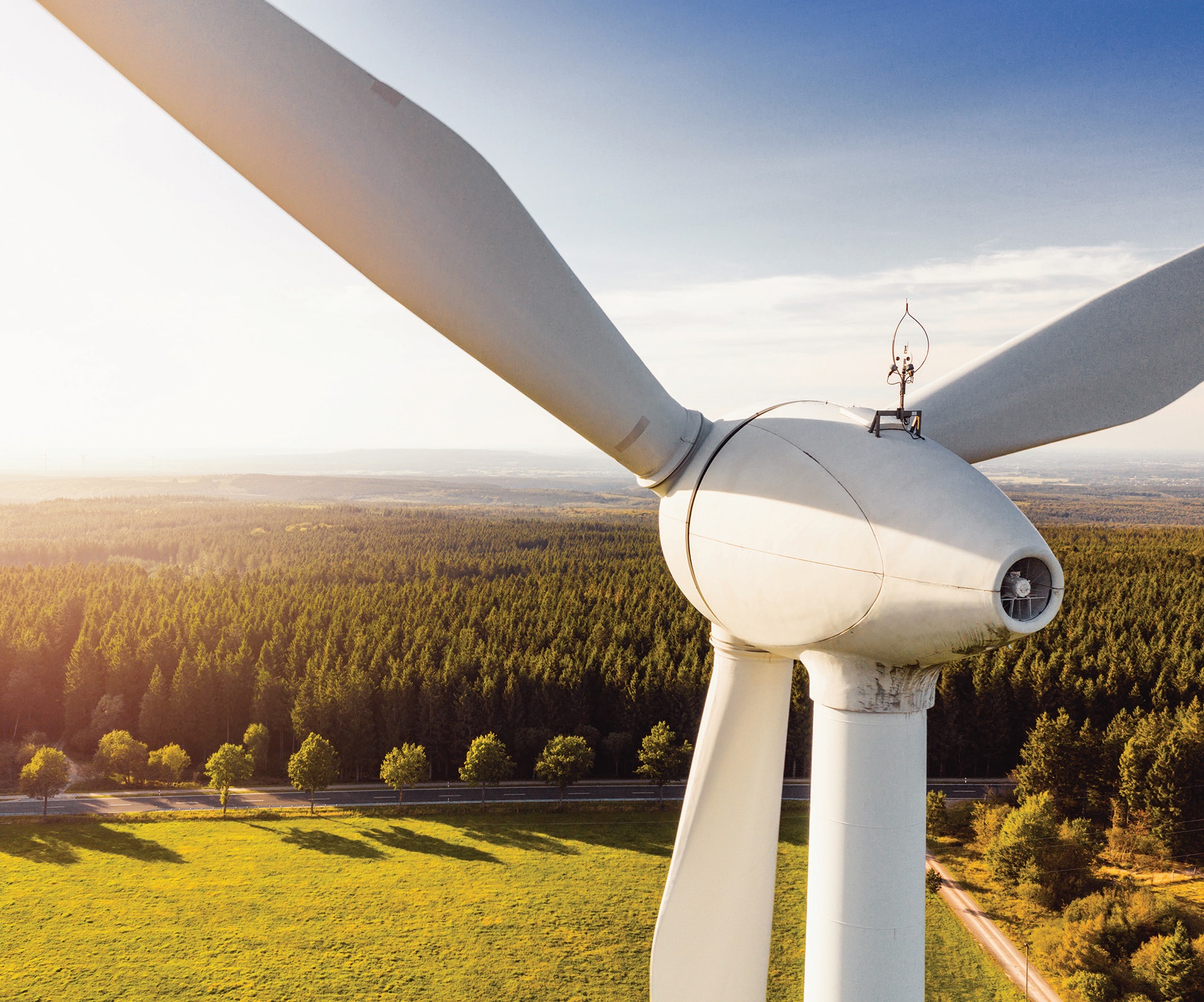
Main bearing failures caused by micropitting, white etching cracks in gearbox bearings and generator bearing failures are identified as research priorities.
Singh identifies five of the most common failure modes observed in wind turbine bearings:
•
Axial cracking is characterized by the presence of a crack in the axial direction largely caused by improper fits, improper shaft grooving, rotation of rings and microstructural alterations (also called white etching cracks [WECs]) in bearing material.
•
Scuffing/smearing is a type of adhesive wear that occurs in two mating surfaces when material transfers from one surface to another under frictional heating.
•
Spalling is characterized by pitting and flaking of material from the raceways and rolling elements caused by “geometric stress concentration from deflection and misalignment, inclusions and defects in the material subsurface and high localized stresses from nicks, dents and debris.”
•
Micropitting, or surface-initiated fatigue, is caused by inadequate lubrication resulting in the contact surfaces no longer being separated, and leading to asperity shear, plastic deformation and break off. Asperity breaking causes microspalls, which can grow into macrospalls/spalling over time.
•
Dents/indentations result when the lubricant is contaminated with foreign abrasive particles or when debris generated within the system is entrapped between raceways and rolling elements.
A 2016 Department of Energy report notes that some bearing failures and their underlying physics are not well understood and remain a research priority.⁶ Main bearing failures caused by micropitting, WECs in gearbox bearings and generator bearing failures are identified as research priorities, but until the failure modes are well understood, the mitigation strategies being developed might only partially address these failures.
6
Sheng identifies scuffing and axial cracking as the top two failure modes for gearbox bearings, while fracture and cracking appear to be the top failure modes for gearbox gears. Sheng notes that axial cracks or WECs have attracted research attention, but “there is still no consensus on the root causes and solutions to completely get rid of this failure mode, although case carburized bearing steel with increased retained austenite and diamond-like carbon coating appear helpful with its mitigation.” While axial cracking occurs on the surface, WECs, typically thought of as precursors to axial cracking, occur in the subsurface.
White etching cracks and bearing failure analysis
Bearings in wind turbine applications are known to show premature damage, typically as cracks in the bearing steel, with the crack faces often showing evidence of white etching matter. Based on their appearance, these are called WECs, and they are known to cause premature damage to the bearings.⁹ WECs also are called white structure flaking (WSF), irregular white etching cracking (Ir-WEC) and brittle flaking. The cracks are thought to form first from the intensity of local shear stress, then the white etching matter is thought to form later from the rubbing of the crack faces against each other.
9,10
While axial cracking occurs on the surface, Singh describes WECs as the “premature bearing failures caused by extensive subsurface crack networks associated with altered microstructure.” WECs appear white when etched with Nital and observed under an optical microscope (
see Figure 2). They show a grain size of 5-300 nanometers, with a hardness 10%-50% higher measured in microstructure adjacent to these cracks, compared to the unaltered microstructure.
Figure 2. White etching matter observed under an optical microscope. Figure courtesy of Mohan Paladugu, “Lubricant-induced white etching cracks: Mechanism and effects of surface finishing,” STP1623 on 12th International Symposium on Rolling Bearing Steels: Progress in Bearing Steel Metallurgical Testing and Quality Assurance, ASTM International, Denver, Colo., June 2019.
In a 2017 Tribology Letters article, white etch areas were found to precede crack formation, and cracks are prerequisites for white etch formation.
3 The article confirmed that the microstructural alterations detected in the studied bearings were observed to have different crack morphology that could be initiated by different mechanisms, including material, mechanical, thermal and chemical phenomenon.
3
While what drives the occurrence of WECs in bearings is still being debated, Singh notes that it is thought to be driven individually or by a combination of multiple factors, including:
•
The presence of hydrogen resulting from lubricant decomposition, stray current, corrosion or water;
•
Mechanical and tribological factors, including high, normal or transient loads or frictional stress; and
•
Electrothermal and electrical effects.
Mohan Chand Paladugu, a materials science specialist with The Timken Co. in North Canton, Ohio, notes that WECs “are seen as the main damage mode” for bearing damages from wind turbine gearboxes and are “known to cause very premature bearing damages.” As previously noted, Paladugu confirms that premature bearing damage adds “significant costs to the maintenance of wind turbines.”
In WEC-induced failures in wind turbine gearboxes, Paladugu notes, “subsurface cracks are seen in the bearing raceways, and these cracks seem to be oriented in the over-rolling direction.” The white appearance of some of these cracks, in optical metallography observations, are the cause of the WEC name.
In recently published articles, WEC damage was generated in metal subsurfaces under the influence of subsurface shear stresses but was caused by the tribochemical reactions occurring at the rolling contact.
12,13 In other words, although WECs form in the subsurface, their formation is a surface-driven phenomenon. This was demonstrated by applying abrasive particles on the raceway surfaces and testing the bearings in an oil that causes WECs.
13
Paladugu concurs that WEC damage is caused by a combination of multiple factors, including “significant slip at the rolling contact, combined with reactive oil additive chemicals, in the lubricant or reactive oil additive chemicals in the lubricant, combined with stray electric currents.” Tribochemical reactions are thought to drive atomic hydrogen into the steel, which results in deformation damage and cracking in the raceway subsurfaces. Paladugu notes that it is possible to generate white etching material through other ways, “but those ways do not seem to cause premature bearing damages under the typical loads in application.”
Testing the role of lubricants in generating WECs found that bearings were damaged prematurely when the tests were performed in an oil with reactive additives.
12,13 The reports concluded that a tribofilm is formed, as a consequence of reactive additive elements, in the lubricant oil, and associated tribochemical reactions drove the formation of the subsurface cracks in steel.
12,13,14
While WEC damage can be mitigated by avoiding reactive lubricant additives, Paladugu notes that the lack of the reactive additives might result in other problems such as micropitting of gears and bearings. Chemically modifying the steel surfaces at the rolling contact is one way to avoid WEC damage by avoiding the tribological reactions. Paladugu lists using black oxidized bearing components or using bearing components made of high chrome steels that form surface passivation oxide layers as ways to avoid these tribological reactions.
Paladugu says that current trends in bearing designs that would improve bearing performance include “preloaded tapered rolling bearings, where roller skidding, axial and radial loads can be better controlled.”
Computational solutions for detection and prediction of early failures
Computational solutions include algorithms or models that detect or predict impending failures of components. Sheng reports that “various computational solutions are investigated in the literature for diagnostics and prognostics of component failures,” and although more of this work has been performed in applications other than wind turbines, some has been done. Sheng divides these solutions into “data domain, physics domain or hybrid data-physics domain integrated approaches.” In regard to the wind industry, Sheng finds that for field deployment, diagnostic solutions in the data domain are more mature and widely used than prognostics, but both areas have been and will continue to be active areas of research in the foreseeable future.
Reduced O&M costs can be achieved by wind power plants through prognostics and health management (PHM) technologies, but prognostics activities are still generally at the research and development stage.⁷ The focus of the prognostics research, in relation to wind turbines, has been on remaining useful life (RUL) prediction.⁷ This research has indicated that bearing axial cracking is the prevalent wind turbine gearbox failure mode experienced in the field, while, in contrast, rolling contact fatigue is normally the only failure mode represented in the bearing design life calculation. The probability of failure is used as a component reliability assessment and RUL prediction metric and can be expanded to other drivetrain components. PHM technologies can be applied to both land-based and offshore wind turbines.
7
The wind industry has been exploring ways to mitigate the impacts of these bearing and gearbox failures in wind turbines in areas ranging from design to new materials or lubricants and to O&M practices.
8 Condition-based maintenance, accomplishable under a PHM framework, has been explored for its ability to improve O&M practices in wind turbines. Numerous future research opportunities exist for wind turbine PHM technologies.
8
Sheng notes that computational solutions enable a “maintenance paradigm shift from time or usage-based maintenance to condition-based or predictive maintenance.” These types of computational solutions can help improve efficiency, reduce human errors and save costs. While validation is challenging, cross-validation during the development of computational solutions is a typical approach, which uses a portion of the data for training and another portion for testing.
Comparing model predicted outputs with future actual measurements, from the modeled physical phenomena or system, also is another possibility. It is always better to start with something simple, integrate validation in model development and then gradually increase the system complexity.
Conclusions
The review of current trends in wind turbine bearings is important, not only for reducing the cost of energy, but also for ensuring the future of sustainable and zero-emission energy sources. As the wind industry adopts more advanced data analytics capabilities, more cost-effective prevention and maintenance can be performed to enhance wind energy. Sheng says that “wind power has become an integrated piece of the energy solution around the world, and its capacity will continue to increase, helping to address global climate change.”
FURTHER READING
Andrew, J. M. (2019), “Fundamentals of wind turbines,” TLT,
75 (8), pp. 32-40. Available
here.
REFERENCES
1. U.S. Energy Information Administration, “What is U.S. electricity generation by energy source?” Available
here.
2. Office of Energy Efficiency & Renewable Energy, “Wind Vision: A New Era for Wind Power in the United States.” Available
here.
3. Singh, H., Pulikollu, R. V., Hawkins, W. and Smith, G. (2017), “Investigation of Microstructural Alterations in Low- and High-Speed Intermediate-Stage Wind Turbine Gearbox Bearings,”
Tribology Letters, 65, Article number 81. Available
here.
4. American Wind Energy Association, U.S. Wind Energy Quarterly Market Report, Fourth Quarter 2019. Available
here.
5. Office of Energy Efficiency & Renewable Energy, “Advantages and Challenges of Wind Energy.” Available
here.
6. National Renewable Energy Laboratory. “Wind Turbine Drivetrain Reliability Collaborative Workshop.” Available
here.
7. Prognostics and Health Management of Wind Turbines—Current Status and Future Opportunities. Available
here.
8. Paladugu, M. and Hyde, R. S. (2020), “Material composition and heat treatment related influences in resisting rolling contact fatigue under WEC damage conditions,”
International Journal of Fatigue, 134, 105476. Available
here.
9. Paladugu, M. (2020), “Influencing Factors Associated with WECs: Similarities of WEC Damage Symptoms between the Field and Laboratory Testing.” Available
here.
10. Paladugu, M. and Hyde, R. S. (2017), “Microstructure deformation and white etching matter deformation along cracks,”
Wear, 390-391, pp. 367-375. Available
here.
11. NREL Gearbox Reliability Database. Available
here.
12. Paladugu, M., Lucas, D. R. and Hyde, R. S. (2018), “Effect of lubricants on bearing damage in rolling-sliding conditions: Evolution of white etching cracks,”
Wear, 398-399, pp. 165-177. Available
here.
13. Paladugu, M. and Hyde, R. S. (2019), “Influence of raceway surface finish on white etching crack generation in WEC critical oil under rolling-sliding conditions,”
Wear, 422-423, pp. 81-93. Available
here.
14. NREL Wind Power Reliability Research. Available
here.
15. Union of Concerned Scientists, “How Wind Energy Works.” Available
here.