TLT: How did you get started in tribology, and what are the goals and applications of your current research?
Argibay: I began my professional career in the Tribology Group at Sandia National Laboratories as a postdoctoral fellow in 2011. It was immediately apparent to me that the cross-section of technical challenges at Sandia, primarily in the aerospace, energy and defense sectors, would be extremely captivating. This remains true today. The national lab environment has provided me, and so many others, with seemingly endless exposure to wonderfully topically diverse and interdisciplinary problems, which are a welcome and persistent reminder of the important role that tribology research continues to have on society.
The focus of my research is primarily metals tribology, which remains a constant in my life since my very first project as a graduate student in professor Greg Sawyer’s lab at the University of Florida. The same fundamental questions we sought to answer then, such as “what atomistic processes define the macroscale friction and wear behavior of metallic interfaces?”, continue to motivate my research today. However, with increasingly sophisticated answers to questions like these, it also has been possible to inform the development of better (higher efficiency, performance and reliability) electrical contacts—key components of electrical systems found in everything from wind turbines, electric vehicles, spacecraft and personal electronic devices like cell phones and tablets.
More specifically, this work is often motivated by substantial problems of reliability and efficiency in high-risk applications, mainly in the areas of power generation and aerospace systems, where performance requirements and application environments are increasingly more demanding, as are tighter failure tolerance margins. This means that I spend a great deal of time supporting engineering teams developing devices that rely on electrical contacts, one of the few areas that typically precludes the use of organic lubricants and electrically non-conductive solid lubricants. The longevity and damage-tolerance of devices, like power and communication slip rings found on wind turbines and spacecraft, and the search for out-of-the-box, next-generation solutions to these engineering needs, continues to motivate a deeper fundamental understanding of metals deformation processes to aid development of better alloy design models.
These efforts, which were born from a need to find higher reliability and more cost-effective solutions to practical engineering problems, led to remarkable new (and generally applicable) fundamental mechanistic insights linking microstructural evolution and the strength of metals. These discoveries, in turn, informed a subsequent effort to engineer a more wear-resistant electrical contact material, in the form of nanocrystalline alloys, with extraordinary nanocrystalline stability. A subset of these highly stable nanocrystalline alloys were chosen, based on the nobility of the constituent metals (Pt and Au), as ideal candidates to replace the widely used electroplated “hard” gold alloys. This is the subject of ongoing technology maturation efforts between Sandia scientists and industry partners. This full-spectrum of activities, from basic science to applied R&D, illustrates the kind of work that goes on in our group, i.e., identifying a materials challenge with high societal impact potential (e.g., electrical contact technology), distilling fundamental mechanisms driving performance (e.g., nanocrystalline stability), and searching for science-based, innovative solutions (e.g., alloying techniques to mitigate undesirable thermo-mechanically driven microstructural evolution).
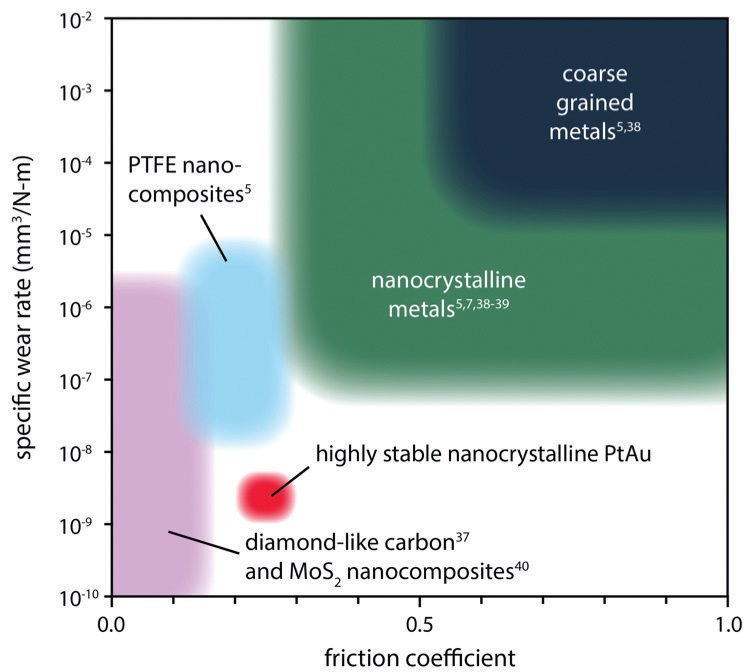
A class of binary alloys with highly thermodynamically stable nanocrystallinity showed remarkable wear resistance, an order of magnitude better than other alloys, and comparable to other state-of-the-art, non-metallic solid lubricants like diamond-like carbon coatings.
While this work is ongoing, and despite recent strides, it appears to be only just beginning. As we learn about the mechanistic origins of metal wear and friction, we continue to uncover new potential routes for the design of materials solutions with better tribological properties. We are currently exploring synergistic alloy/environment combinations that promote tribochemical processes with self-healing and anti-fragile properties.
TLT: What are the primary projects you are interested in at the moment?
Argibay: My group is currently exploring ways to de-risk metals additive manufacturing (AM) via alloy optimization. We are specifically exploring high-entropy alloys as a “materials solution” to metals AM, where the focus over the past few decades has been on process development to print conventional, widely utilized, and well characterized alloys like steels. In the process of understanding the fundamental limitations of printing steel, it became evident to our team that centuries of optimization of materials, like steels, strongly suggested that these are impractical materials for engineering parts using AM methods.
Our group currently has several major projects aimed at developing cost-effective AM-processed alloys with superior strength-to-weight, among other properties, than (even) conventionally processed steels. This work intersects with previously mentioned discoveries, in the context of electrical contacts, regarding the links between microstructural evolution and friction behavior (shear strength). We recently published some of these results and are working on additional manuscripts focused on results of tribological investigations of these materials. We are excited to see how this work is received by the tribology community.
Journal cover in Advanced Materials, where the work on low wear electrical contact alloys was published, showing a snapshot of large-scale molecular dynamics simulations of grain boundary decohesion of PtAu at high tensile stress.
TLT: Are there opportunities for young tribologists to join you at Sandia?
Argibay: The DOE national laboratory system, of which Sandia is a member, offers extensive opportunities to host and mentor students and support graduate student research. In my experience, my managers and colleagues have viewed their role in fostering the creation of the next generation of scientists as a high priority, and one of great strategic importance to the organization and the country that we serve. We are always looking for ways to support young tribologists, whether that is by having them join us for summer (or year-round) internships or establishing collaborations with their faculty advisers.
TLT: You are an experimentalist who recently worked very closely with theoreticians. How important are these collaborations for fundamental studies in tribology?
Argibay: Engineering challenges facing our society only continue to grow in complexity, something that is abundantly clear in tribological applications. Dismayingly, I’ve witnessed first-hand the disconnect that can occur between theoreticians and experimentalists and engineers. I would urge both theoreticians and experimentalists to establish lasting collaborations and have patience while they try to learn each other’s language, so to speak. The synergy and productivity that I’ve seen on the other end of this process is nothing short of astonishing.
This “impedance mismatch” clearly stems from difference in the end goals. Theoreticians tend to focus on abstract problems, too often in a way that appears (but is typically not!) of little practical relevance to those tasked with development of new materials and devices. Experimentalists and engineers, on the other hand, are often constrained by practical considerations, like limited budgets and narrow scopes of work, that do not allow for a high degree of abstraction, lest they fail to deliver practical solutions to pressing engineering problems.
Sandia has a long history of scientific and engineering achievement, and this is in no small part due to the importance and priority that is given by management to bringing together complementary interdisciplinary teams with the aim of finding non-incremental solutions to real-world problems. This commitment to innovation, with a focus on the kind of research that is far too risky for the private sector to justify, in economic terms, is precisely what government-funded research organizations, like Sandia, aim to deliver.
Nic Argibay next to the newly acquired Variable Temperature UHV Tribometer in the Tribology Laboratory at Sandia National Laboratories. In his hand is a PtAu coated coupon, one of a new class of alloys with remarkably high wear resistance.
TLT: When studying the performance and properties of solid lubricants, what are the biggest challenges?
Argibay: I would like to paraphrase my adviser in response to this question, who, in response to my own question as a young student, “What in the world made you get into tribology?”, once told me that one of the wonderful and exciting things about tribology research is how complicated and interdisciplinary the problems (and answers) can be. Interdisciplinary problems, like those we tend to find in our field, often push researchers outside their comfort zones. Ideal surfaces and surface reactions are complicated enough before adding stochastic processes like wear and contact mechanics to the mix. It also is often impractical to isolate and study individual mechanisms since these are so often synergistic. For instance, the constant removal of material that competes with adsorption and film formation rates, further complicated by aging phenomena, can significantly change the properties of the surface that we then spend great deals of time and resources trying to analyze. This generalized example highlights a clear need for increasingly higher fidelity
in situ characterization capabilities. Efforts to elucidate fundamental mechanisms of friction and wear are often confounded by our inability to interrogate surface, interface and bulk properties in conditions that are relevant to the application, motivating the need for this new insight. The development of better analysis tools will probably continue to be a major focus area for experimentalists in the near future.
TLT: What instruments do you use to study solid lubricants, and if you could have one new instrument that does not exist today, what would it be?
Argibay: Our team primarily relies on custom-built and highly modular testing systems for the bulk of our tribology research, though we also routinely use commercially available systems such as nanoindenters, electron microscopes and X-ray spectroscopic tools for surface analysis and materials characterization. We are very fortunate at Sandia to have access to state-of-the-art, fully staffed materials characterization and analysis labs and, equally important, a remarkable cadre of subject matter experts who can assist with data analysis and interpretation.
One exciting ongoing project, in collaboration with Brookhaven National Laboratory, is the development of a microtribometer that can be operated on synchrotron beamlines. This will enable opportunities for analysis of tribological processes with unprecedented fidelity, either in situ or with minimal time between contact events and analysis, using techniques such as near edge X-ray absorption fine structure (NEXAFS). This work is currently led by STLE-member John Curry, a recent addition to the research staff at Sandia, who was formerly a postdoc and year-round graduate student intern in our group while completing his doctorate at Lehigh University.
TLT: Where do you see tribology research in the next five years?
Argibay: While the winds may be changing, driven by a growing need to transition from fossil fuels to sustainable energy sources as the impacts of climate change continue to worsen and grow public awareness, there is no doubt that tribology and lubrication (including petroleum-based solutions) will continue to play a critical role in keeping our society moving forward and productive for the foreseeable future. It is evident that we, as a community, must—and can—lead rather than react to these changes. I believe that the emergence of new design constraints, dictated by changing socioeconomic interests, presents an opportunity for tribologists rather than a threat. In an increasingly electrified world, there will be no shortage of need for new materials and lubrication techniques that can meet increasingly demanding efficiency requirements.
The next five years at Sandia will likely see a continued push for technology maturation of more agile and cost-effective advanced manufacturing techniques such as laser-based consolidation of metal powders and the use of these tools in the fabrication of materials for structural and tribological applications. Concomitantly, the continued development of data science and machine learning-based tools for alloy optimization will likely be a major focus, as will be their integration with high-throughput additive manufacturing and materials characterization tools to accelerate insertion of new materials into high-risk applications, where the maturation cycle has historically been generational.
You can reach Nic Argibay at nargiba@sandia.gov.
Any subjective views or opinions that might be expressed in this interview do not necessarily represent the views of the U.S. Department of Energy or the United States Government. This effort was funded by the Laboratory Directed Research and Development program at Sandia National Laboratories, a multi-mission laboratory managed and operated by National Technology and Engineering Solutions of Sandia, LLC., a wholly owned subsidiary of Honeywell International, Inc., for the U.S. Department of Energy’s National Nuclear Security Administration under contract DE-NA0003525. Any subjective views or opinions that might be expressed in the paper do not necessarily represent the views of the U.S. Department of Energy or the United States Government.