KEY CONCEPTS
•
Surface chemistry, microstructure, operating conditions, and the surrounding environment all affect the performance of solid lubricants and antiwear coatings.
•
Modeling based on validated input data and computational methods, along with an understanding of each method’s strengths and limitations, produces the most meaningful results.
•
Rational design of solid lubricants requires integrating fundamental and applied science across a range of length scales.
How do you keep bearings and gears running smoothly when your system is running at ultra high or ultra-low temperatures or operating in a vacuum? Solid surface coatings and solid particle surface treatments reduce friction and wear in situations where oils and greases are impractical, including spacecraft mechanisms and the vacuum enclosures for high-speed rotating anode assemblies for X-ray diffractometers and medical imaging devices.
1 Although these applications are highly specialized, solid coatings like PTFE also appear in such everyday items as razor blades and air conditioner compressors.
Existing solid lubricants are finding new areas of application,
2 and new materials, composites, and surface structure modifications are pushing the envelope still further. A better understanding of the fundamental mechanisms behind solid lubrication and wear protection could advance the field to another level by pointing the way toward rational design.
Why use solid lubricants?
“We’ve been studying solid lubricants for a number of years now and [we are] basically trying to design new ones or modifications of old ones based upon an evolving understanding of how they perform under tribological contact,” says STLE Fellow Gary Doll, professor and director of the Timken Engineered Surfaces Laboratories at the University of Akron in Akron, Ohio. His current work involves developing surface coatings for use in pressure and temperature regimes that require solid lubricants. These include nickel and cobalt materials used for high-temperature hydraulics and silver and platinum coatings that are antimicrobials, as well as solid lubricants for medical implant devices.
Figure 1. Various forms of carbon include (left to right) graphite, graphene, diamond-like carbon (DLC), and diamond. Graphene, in which three-coordinate carbon forms single flat layers, and DLC, in which four-coordinate carbon forms an amorphous solid, are under development as solid lubricants. Courtesy of Wikimedia commons (graphite, graphene, and diamond) and Elsevier (DLC)
Doll’s group is looking at microstructural changes at the pressures and temperatures where velocity accommodation occurs to better understand the process. Velocity accommodation materials have stationary top and bottom layers with middle layers that move under shearing stresses. The group is also mapping out the thermodynamics of phase changes driven by temperature and pressure such as when reciprocating sliding builds up heat in the moving central layers of the film.
Solid coatings can be used alone, but they can also provide a boost to systems that use oil lubricants. Coating parts that are prone to rolling contact fatigue with titanium-doped MoS
2 can extend their service life by an order of magnitude, even when using oils without EP and antiwear additives, Doll says. He notes that manufacturers with established processes and product lines and consumers who are familiar with specific products might need to be convinced of these benefits, but eliminating toxic or environmentally harmful additives from oils is a more sustainable approach to their manufacturing, use, and disposal.
Beyond graphite and disulfides
Commercially available solid lubricants and antiwear coatings rely on tried-and true materials like graphite, metal disulfides, and PTFE. However, two newer solids, made from carbon (or mostly carbon), are gaining attention. These materials—diamond-like carbon and graphene—are available now for a few specialized applications, and they may show up in more commercial products in the near future.
Much of Julien Fontaine’s research involves wear-resistant, diamond-like carbon (DLC) coatings that resist wear and also provide a lubricating surface. These could find use in such applications as cutting tools, computer hard disks, car engine parts, microelectromechanical systems (MEMS), and biomedical devices. Fontaine, French National Centre for Scientific Research (CNRS) researcher working at the Tribology and System Dynamics Laboratory (LTDS) at the École Centrale de Lyon, is a member of a large team doing tribological research. He does laboratory-scale tribological testing that provides evidence of the mechanical, chemical, and physical processes involved in tribological contacts.
DLC’s chemical bonding scheme gives it a combination of useful properties. Materials in the DLC coatings family (they don’t form bulk phases) have hardness ratings that range from metal-like almost all the way up to diamond hardness. These coatings are wear-resistant materials, with metastable structures that are stabilized by residual stresses formed during coating deposition. Unlike diamond coatings, the surfaces of DLC coatings are smooth, and they undergo surface transformations under stress, both of which reduce friction (
see Lubrication and Wear Protection sidebar).
In one collaborative project, Fontaine, STLE-member Dr. Robert Carpick at the University of Pennsylvania, and their colleagues found that hard DLC coating surfaces (silicon oxide-doped hydrogenated amorphous carbon, for example) can transform under hydrogen, oxygen, or water vapor. The carbon on the surface assumes a graphite-like bonding scheme (sheets of fused six-membered rings rather than a diamond-like 3D network of linked tetrahedra) that releases molecules into the interface, reducing friction between the contacting parts (
see Figure 1). Under a vacuum, however, steel in contact with a harder DLC coating can break and produce particles that can adhere to the DLC surface or to each other, forming adhesive junctions that break again, accelerating wear. Under the high stresses involved in tribological contact, the steel particles can damage the bulk steel, as well as the DLC coating, resulting in catastrophic failure.
3
Graphene, another type of solid carbon, consists of single graphite-like layers. Because graphene flakes are only one atom thick, they are referred to as 2D solids. Although graphene lubrication is still in an early stage, practical applications have started to appear.
Graphene nanoplatelet lubricants are a particular area of interest for STLE-member Diana Berman. Berman, assistant professor of materials science and engineering at the University of North Texas in Denton, Texas, does lab-scale experimental research on frictional energy dissipation and losses at interfaces to understand the origins of macroscale behavior of materials. She and her colleagues are trying to understand how the easy shearing of 2D materials minimizes friction between surfaces. They are also looking at ways to manipulate the structures of these 2D materials to improve their performance still further. Some of their research involves ways to achieve superlubricity; that is, systems where the coefficient of friction is less than 0.01—non-zero, but too low to measure using conventional instruments.
4
Berman notes that when she and her collaborators started on their graphene research in 2012, the idea of using graphene as a lubricant was an academic exercise. Now, however, graphene lubricant sprays are available commercially in the form of dispersions and sprays. “We’ve been trying to understand the origin of macroscale tribological behavior by looking at nanoscale changes in the material,” Berman says, referring to her work on graphene particles on steel or silicon and how graphene compares to other types of coatings like DLC. Graphene attaches to a steel surface with relatively weak van der Waals forces, which allows the graphene to adapt to external stresses like shearing or sliding and to accommodate those stresses to minimize friction. In addition, graphene’s electron mobility enables it to protect the underlying surface from corrosion and other environmental effects.
Graphene particles move around on a steel surface, but eventually they are pushed to the sides, away from the points of contact. To get around this problem, Berman uses graphene particles suspended in a volatile liquid like ethanol, which is sprayed onto the solid surface. Lubricants that can be replenished easily in this way could prevent the type of wear problems associated with continuous coatings. In an industrial application, an injector system could continuously replenish the graphene in ethanol suspension at the contact site, she says. She notes that in the small setup they use for their laboratory testing, they need to add about one drop of their graphene suspension after about every 50 km of sliding.
These graphene coatings are on the order of 1-2 nm thick, in contrast with the micron-scale deposited coatings common with disulfides and DLCs. Graphene and other thin powder coatings have a high surface area, and they usually coat the substrate conformally, taking on the shape of the surface features. Because the lubricating mechanism for 2D materials relies on the coating’s attachment to the substrate rather than on adsorbed water or other species, 2D materials can operate well in a variety of environments.
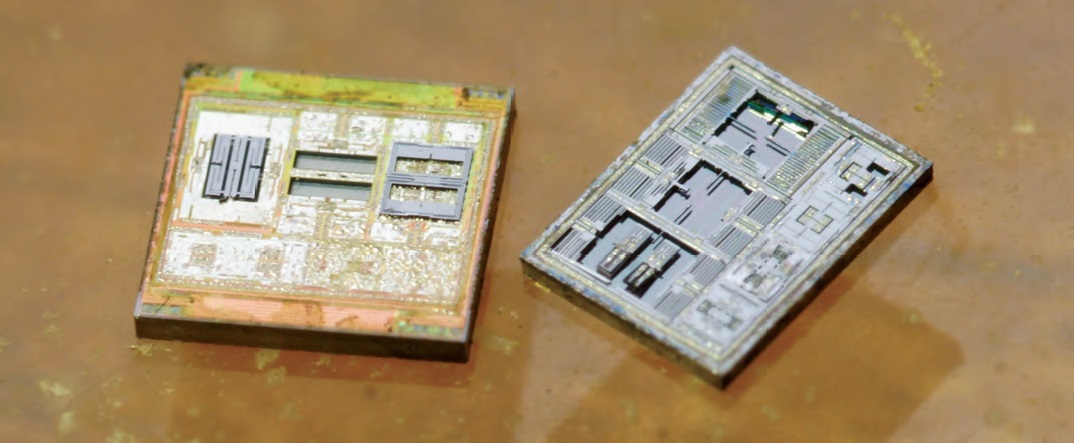
Dies for making MEMS gyroscope accelerometers, approximately 2.7 nm across. (Courtesy of ZeptoBars)
Deposition and texturing
The way a coating is applied influences its tribological properties. In addition to vacuum deposition, Doll also uses electrochemical solution deposition to develop new tribocoatings for steels. Previously, electrochemically deposited coatings had not resisted wear as well as those applied using physical or chemical vapor deposition. However, recent advancements show the promise of electrodeposition as a more economical alternative to vacuum deposition processes, and electrodeposition provides more control over the grain sizes of metal films.
5 So far, Doll has looked at polymers like polypyrrole compounds and thin nickel films.
Doll uses laser ablation to produce micropatterned stainless steel surfaces with hydrodynamic textures for sliding contacts in devices like face seals, hydrodynamic bearings, spur gears, and splines. The solid lubricant coating is applied first, and the laser cuts a pattern through the coating and into the steel. By applying the coating first and patterning it afterward, he avoids flattening out the surface by filling up the low spots in the patterns with coating material.
In one project for face seal applications, his group textured hydrodynamic features into their contacting surfaces before they applied a solid lubricant coating. During operation, the hydrodynamic features provided good separation of the surfaces, while the solid lubricant assisted with touchdown and takeoff.
Making coatings that work
Compared with oils and greases, solid lubricants can provide greater surface separation, if the lubricant layer maintains a constant thickness at various loads and speeds, Doll says. However, when continuous coatings wear away, you can’t just refill a reservoir to replenish them. Restoring a surface coating requires taking the part out of operation, and in some cases, it’s more practical to replace the part entirely. Unlike oils, solid lubricants do not flush out contaminants like solid particles or water, and these contaminants can accelerate wear. Surface coatings are also less effective at channeling heat away from the contacting surfaces, since the coatings remain in place rather than circulating throughout the system as oils do.
Doll’s group is looking at various ways to improve lubricant coatings’ strong points and decrease their limitations. For example, they are examining microstructural effects such as when amorphous materials crystallize and orient with temperature and pressure—a phenomenon that can facilitate the velocity accommodation mechanism. MoS
2 can be doped with various elements to create an amorphous material with a much lower wear rate than the undoped crystalline solid. However, certain combinations of temperatures and pressures can drive dopant diffusion within the coating, forming crosslinked nanocrystallites. This in turn changes the functional behavior of the coating.
Doll’s research produced a surprising finding: harder coatings are not necessarily better for wear protection. Some hard diamond-like carbon coatings react chemically with oil additives, which accelerates wear. On the other hand, MoS
2 coatings can interact synergistically with oil additives, in part due to the chemical similarity between the coatings and the inorganic oil additives, so these softer coatings may actually perform better, he says.
Continuous coatings applied using vacuum deposition or similar techniques require that every part be coated separately, before a machine is assembled, Berman says. Parts must be positioned properly in the coating chamber, and even then, curved or complex shapes like cylinders, ball bearings, or gears can cast “shadows” that shield certain areas from the coating material. “In lab tests, you use these ideal, planar, polished substrates…and the coating works perfectly,” she says. But the coating may vary in thickness for real machine parts. Unlike continuous solid coatings, powder and particle suspensions can penetrate to every area of a substrate surface, generating coating protection even for parts that have complex shapes.
Self-assembled nanolayers once seemed like a promising route to nanostructured coatings for very small devices like microelectronics and MEMS switches, Berman notes. Self-assembly, in which coating molecules come out of solution and deposit themselves onto surfaces to form well-controlled, highly uniform layers, offers molecule-scale control over chemical composition and coating morphology. However, the bonding forces between this type of layer and a solid substrate are generally too weak to form a stable coating. Under frictional contact, the nanolayers are pushed to the side rather than providing lubrication. Berman says that several researchers are working on this problem, so these materials may eventually evolve into useful lubricant coatings.
Finding the right solid coating requires an understanding of the operating environment for which it is intended. Understanding fundamental lubrication mechanisms is essential to anticipating and avoiding failures as a mechanical system transitions from one environment to another. Graphite, for example, has a layered structure that shears easily. However, unlike inorganic layered materials that work best under dry conditions, graphite lubricants require a humid environment at ambient or close to ambient temperatures to be effective because adsorbed water is an essential part of graphite’s lubrication mechanism.
Making lubricants that work under varying environmental conditions often requires combining more than one material to take advantage of their different properties. These mixed lubricants are sometimes called chameleon coatings. For example, mixtures of graphite and MoS
2 provide lubrication in humid and dry environments, respectively. Graphite is also more effective at lower temperatures, while MoS
2 provides lubrication at higher temperatures. This mixture, now a commercial product, is used in the aerospace industry, where aircraft move between idling on the runway and the high engine temperatures and cold surrounding temperatures at flying altitudes. Chameleon coatings are still in a very early stage of commercialization, and “it’s difficult to say how widely they are used,” Berman says.
Figure 2. Solid lubricants can be used alone or with liquid lubricants to maintain separation between surfaces. (Copyright Fraunhofer IWM, used with permission).
Lubrication and wear protection
Solid lubricants and wear protection coatings address different problems, and they work best in combination with each other. Julien Fontaine, French National Centre for Scientific Research (CNRS) researcher working at the Tribology and System Dynamics Laboratory (LTDS) at the École Centrale de Lyon, notes that traditional solid lubricants are soft materials like graphite, MoS
2, soft metals, or polymers, that are easy to shear. They provide lubrication by ensuring that shear occurs between the layers of the lubricant coating rather than on the substrate surface.
The effectiveness of solid lubricant layers depends on the operating environment. Some, like graphite, require humidity to be effective, while others, like MoS
2, work better in a dry atmosphere or under vacuum. Some coatings are relatively inert, while others react under stress or in the presence of physisorbed water, which can react with substrate surfaces, debris, and tribofilms. Wear protection coatings are hard materials, and they can fracture under stress if they are too brittle. Thus, developers are working on wear protection materials that combine hardness and toughness, with nanoscale structures that retard crack propagation.
Wear protection coatings guard against the formation of adhesive junctions between hard surfaces under sliding contact, which can break again under plastic deformation or fracture.
There are several approaches to combining wear protection with lubrication, Fontaine says. One traditional approach is to cover a wear-resistant coating with a layer of solid lubricant. Another option, composite coatings, involve a tradeoff between optimum performance of the individual components and achieving the greatest range of properties. A third approach is to use a hard material that undergoes surface transformations under stress to provide lubrication.
Wear marks penetrate a solid antiwear coating on a titanium aircraft hydraulic line. (Courtesy of U.S. Air Force/John McClure)
Computational models
“Why is there friction at all, and how can it be controlled in the context of solid lubricants?” asks Lars Pastewka, professor in the department of microsystems engineering at the University of Freiburg in Germany. “We do molecular dynamics calculations for surfaces in contact with each other to understand how energy dissipation works,” Pastewka says. He performs molecular dynamics (MD) and related types of simulations to study surface chemistry and friction, with a focus on energy dissipation and microstructural changes within various tribosystems, at length scales from tens of nanometers up to about one micrometer where surface roughness becomes important (
see Figure 2).
Surface chemistry influences friction, but Pastewka also studies the ways that friction between solid surfaces changes the materials. For example, friction energy released into metallic surfaces sliding past each other often changes the microstructure of the metals, above and below the surface.
6 The fundamental aspects of these processes are not well understood, he says, but understanding microstructural changes and finding ways in which surface chemistry influences energy dissipation could be important in the design of reliable interfaces—and, ultimately, the devices that incorporate these interfaces.
MD models are typically constructed to study a specific problem, Pastewka says. Molecular mechanics calculations are useful for studying molecular conformation changes in response to a specific stimulus, but they do not simulate breaking chemical bonds. Tribological processes, especially under severe conditions, involve covalent bond breaking, so Pastewka uses reactive model calculations, including empirical models and tight binding calculations. He also does some boundary element calculations for surfaces that deform elastically under loads. Since many solid lubricants are framework solids rather than molecular solids, he uses force fields derived from solid-state chemistry for his reactive models, even though the modeling methods themselves come largely from liquid chemistry. “We always need to combine different simulation methods,” he says.
What happens when surfaces interact depends in large part on the load, he says. For example, model carbon surfaces terminated with hydrogen atoms, under low loads, slide past each other with little to no wear. As load increases, morphological changes occur below the surface. Subsurface atoms in carbon, for example, can change their coordination numbers under a load.
Pastewka and his colleagues studied one extreme example of this type of transition in which the subsurface structure in diamond changed under conditions similar to gem polishing.
7 The four-coordinate carbon in the bulk transitioned to three-coordinate just below the surface, and to a two-coordinate scheme on the surface. The surface phase, an amorphous solid, was much softer than the bulk diamond. The calculations used to produce these data conserved the number of atoms, so the models did not simulate wear directly. However, amorphous carbon is known to be more susceptible than diamond to wearing away under shear. Under ambient atmospheric conditions, oxygen further eroded the amorphous layer, oxidizing two-coordinate carbon to form CO
2. Pastewka cautions that although friction may be similar from one system to the next, wear is material-specific, so these results should not be extrapolated to other systems.
One-stop tribo-testing
Fontaine’s lab uses a custom-designed tribometry system, the Environment Controlled Analytical Tribometer, that can operate under ultra-high vacuum (10
–7 Pa) or up to one atmosphere of pressure of a pure gas like dry oxygen or water vapor (
see Figure 3). In this controlled environment, the factors that contribute to friction and wear can be examined in isolation. This device performs friction experiments, as well as indentation, scratching, and fracture tests. Although most testing is done at ambient temperature, the system can test materials anywhere from –100 C to about 550-600 C, which is useful for replicating real-world conditions in some of the industry-related work that Fontaine’s lab performs.
The central tribometer and several instrument chambers can be used together or independently, under the same or different atmospheres and pressures. One chamber is set up for surface preparation, ion gun etching, and adsorption studies. An X-ray photoelectron spectrometer documents chemical changes at the contacting surfaces. A mass spectrometer checks the initial quality of the environment in the tribometer chamber and keeps track of gases and other species released into the environment during tribological testing.
The custom tribometer uses a 6-axis force sensor, developed in Fontaine’s laboratory, that improves the resolution of measurements of forces and torques between the contacting solids. Because no commercial transducers could operate in a vacuum and measure the small forces they want to study, Fontaine and his colleagues developed and patented their own sensor, working with Prevac, a vacuum components vendor.
Molecular simulations are useful for gaining insight into mechanisms, but they do not currently generate quantitative outputs with the precision needed for the rational design of solid lubricant materials, Pastewka says. Even if you know what the molecule looks like, it’s not trivial to calculate its macroscopic properties, he adds. Surface effects, like termination species and interactions with the environment, are difficult to model on scales relevant to macroscopic properties. Even though MD calculations yield only rough estimates of macroscopic properties, the insight into molecular processes gained from these calculations is useful as a foundation for assisting in lubricant design, especially for aspects of a process that are difficult to observe in the laboratory.
Finding a way to transfer results between models at different length scales is one of the main challenges to producing a multiscale simulation of tribological effects. At present, Pastewka says, there is no easy method for coupling the molecular models he generates to models at the machine element scale. Some researchers are bridging the length scales on a case-by-case basis, but exploring load and pressure scenarios at scales relevant to lubricant development will require a much more robust ability to pass information between models.
As more groups get into codeveloping open-source modeling software resources, establishing community standards and ensuring interoperability is becoming a big problem, Pastewka says. Collaborations are starting to form, but “it’s in its infancy,” he adds. Standardizing and documenting codes for certain computational tools, like interatomic force models, would greatly assist in sharing code modules between programs and comparing results from different simulations. “These types of projects always involve a big effort and you need, of course, money to do that,” he says. “But I think, in the end, they turn out to be very useful.”
Modeling calculations are only as good as the physical and theoretical data that go into them. Pastewka cites the Open Knowledgebase of Interatomic Models (OpenKIM,
https://openkim.org/ ), a repository of interatomic potentials, as an example of the type of well-curated database required for generating the most meaningful results. His group operates a Web-based repository of laboratory surface roughness data, including optical profilometry and AFM scans, for use in calculations (
https://contact.engineering/ ). The intention is to enable researchers to run their own calculations using measured surface topography data. “Such efforts could be extended to include macroscopic properties such as viscosities of molecular fluids,” Pastewka says. “This would enable us to better judge the accuracy of a molecular model for a specific problem. It would also speed the time to discovery, since at present we spend much time on validating molecular models before applying them to a tribological problem.”
“There are still a lot of loose ends between simulation and experiment,” Pastewka cautions. Tribological processes are the aggregate outcome of many different physical and chemical processes. Disentangling these processes makes it difficult to make quantitative predictions about a given system.
Figure 3. Researchers at the Ecole Centrale de Lyon have developed a multifunctional tribometry system in which several instruments share a controlled environment. (Courtesy of Morgane Demoreuille for Ecole Centrale de Lyon)
Rational design
Although rational design for solid lubricants isn’t being done today, “we’re getting close,” Doll says. One underlying motivation for understanding the thermodynamics and kinetics of these systems is to move beyond a trial and error approach toward a more scientific approach to novel material discovery.
“We really need very accurate measurements and studies to understand what is going on in the contact,” Fontaine says, adding that this information assists modelers in simulating the most relevant parts of a system (
see One-Stop Tribo-Testing sidebar). “My personal goal in research is to try to understand how it is possible to achieve extremely low friction,” he says. Ultimately, Fontaine is working to provide the basic science that can assist in a rational design strategy for real-world products. “We are trying to build that bridge. That’s my motivation in understanding how DLC coatings can achieve low friction—these are hard materials,” Fontaine says. It all gets down to, “How do you make a hard surface lubricious? That’s what we are trying to do, and we hope that the understanding we get can allow us to help other people optimize their coatings in order to achieve better performance in industrial systems.”
“If you just choose a material that looks good and start running it, it’s difficult to predict when that material will fail,” Berman says. “Predicting the weaknesses of a lubricant is difficult using only the knowledge from practical applications.”
If you’re designing a new system with no prior tribological testing, she notes, you typically do a literature search for all the published materials and coatings. Then you select a subset of materials to test based on the environment and temperature requirements, the anticipated loads, adhesion, and other factors. But this approach can miss the larger picture of interactions and failure mechanisms that a database of basic materials and properties would provide. Berman cites one study where the researchers did a literature search and picked 20 candidate materials, more or less at random, for testing. “It wasn’t really effective because they didn’t have a fundamental view,” Berman says. “If any of those 20 materials had worked well, they would have declared their work done, but it doesn’t prove that this selection was wise because they didn’t really understand the basics of why one material was better than another one.”
“This type of approach doesn’t tell you if the material you chose was truly the best material for the application, or if some better alternative exists outside the set of materials you tested,” Berman continues. A well-developed database of basic material properties could point the way to a promising material, even if it has not yet been cited in the literature for a particular tribological application.
Building a solid bridge
Although a truly rational approach to designing solid lubricant and wear protection systems is not yet a reality, academic and industrial researchers are tackling the problem from several angles. Their hope is that as the results of computational simulations, lab-scale model systems, and macroscale component testing increasingly overlap and reinforce each other, they will form the foundations of an understanding that bridges the knowledge gap between molecules and mechanical applications.
REFERENCES
1. Andrew, J.M. (2019), “Solid Lubricants,” TLT,
75 (8), pp. 24-30.
2. Mutyala, K.C., Singh, H., Fouts, J.A., Evans, R.D., and Doll, G.L. (2016), “Influence of MoS
2 on the Rolling Contact Performance of Bearing Steels in Boundary Lubrication: A Different Approach,” Tribology Letters,
61, 20,
click here.
3. Koshigan, K.D., Mangolini, F., McClimon, J.B., Vacher, B., Bec, S., Carpick, R.W., and Fontaine, J. (2015), “Understanding the Hydrogen and Oxygen Gas Pressure Dependence of the Tribological Properties of Silicon Oxide-Doped Hydrogenated Amorphous Carbon Coatings,” Carbon,
93, pp. 851-860,
click here.
4. Berman, D. Erdemir, A., and Sumant, A.V., (2018), “Approaches for Achieving Superlubricity in Two-Dimensional Materials,” ACS Nano,
12 (3), pp. 2122-2137,
click here.
5. Fowler, R. (2016), “20 Minutes with Gary Doll,” TLT,
72 (5), pp. 22-24.
6. Gola, A., Schwaiger, R., Gumbsch, P., and Pastewka, L. (2020), “Pattern Formation during Deformation of Metallic Nanolaminates,” Phys. Rev. Materials,
4 (1), 013603.
click here.
7. Pastewka, L., Moser, S., Gumbsch, P., and Moseler, M. (2011), “Anisotropic Mechanical Amorphization Drives Wear in Diamond,” Nature Materials,
10, pp. 34-38,
click here.
Nancy McGuire is a freelance writer based in Silver Spring, Md. You can contact her at nmguire@wordchemist.com.