Electric vehicles make grease’s future uncertain
Lynne Peskoe-Yang, Contributing Editor | TLT Grease February 2020
How do you predict the needs of engines with still-evolving specs?
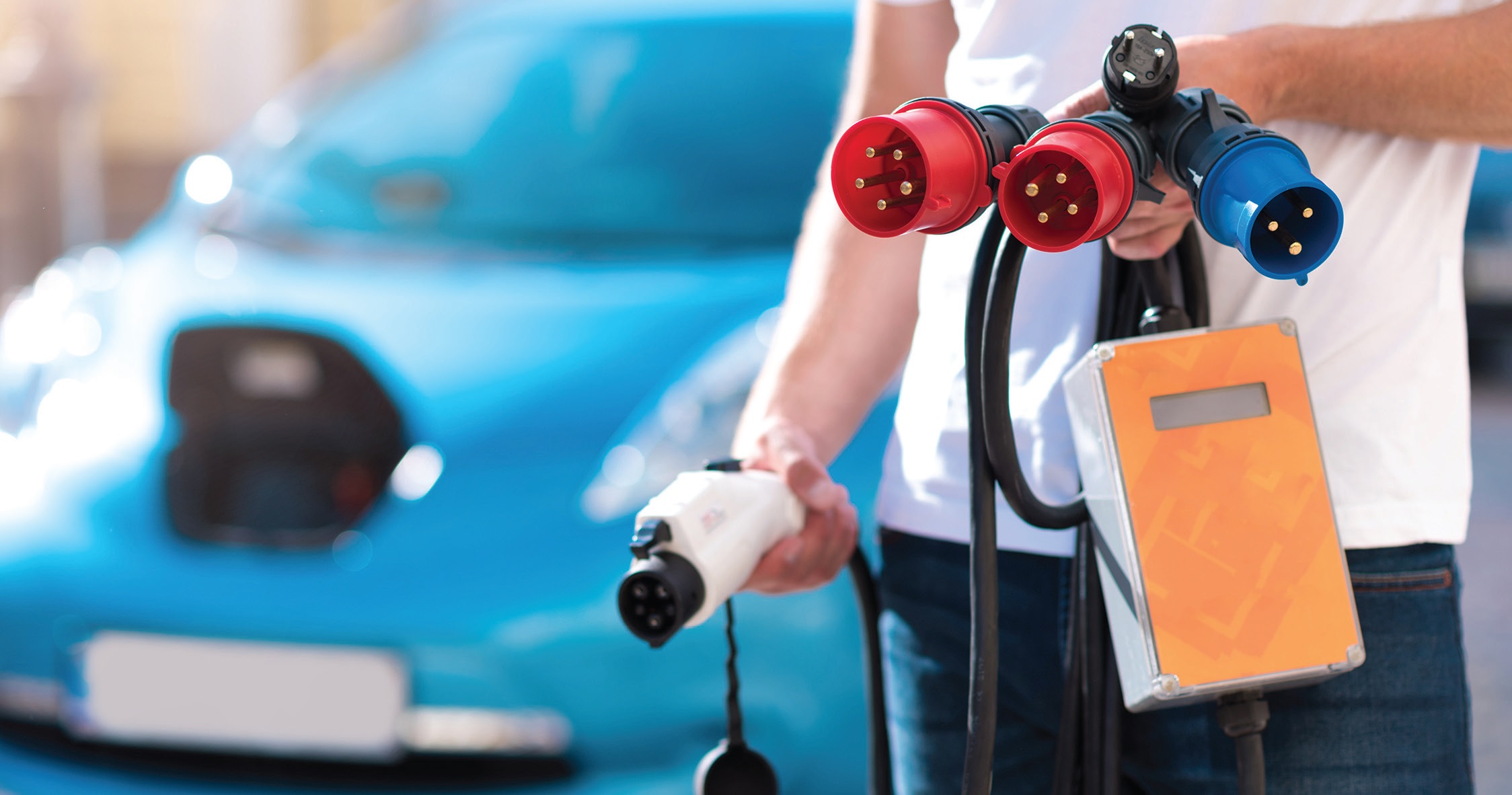
EV engines deliver a whole new set of challenges to lubricant marketers—gear oils, coolants and greases will require reformulation.
According to predictions from Grand View Research, an India- and U.S.-based market research consultancy, demand for electric motors will continue to grow steadily in the new decade, driven primarily by factors like fuel savings, government incentives for green vehicles and other products and increasing consumer awareness of the impact of fossil fuel use on climate change.
In view of this radical shift in priorities from consumers and regulators, vehicle engineers are confronting an array of new problems exclusive to the bearings of the new electric standard. The push for vehicle electrification has changed the prevailing wisdom around many of the most essential substances involved in motor engineering, from engine hardware to chasses. Even basics like grease must adapt to the changing needs of an electric future.
The science of grease
Grease is a critical component in the operation of 80% of motor bearings in the world. Chemically, grease is distinct from liquid lubricants like motor oils because of the presence of particles of a thickening agent––usually a type of soap complex––which are dispersed throughout the oil phase to produce a solid or semi-solid substance. The dispersion is often enhanced with additives that impart special properties to improve load-carrying capacity, manage viscosity levels or minimize the effects of corrosion and wear.
“Every grease is a unique formulation,” explains STLE-member Dr. Kuldeep Mistry, an engineering researcher and product development specialist at The Timken Co. in North Canton, Ohio. The base oils that perform the essential lubricating function of the grease are formulated for specific environments, while the thickener “acts like a sponge to retain and appropriately release the oil” over a sustained period, Mistry says. He adds that is why grease stays in place longer than oil alone—the presence of the thickener means the grease “tends to stay put within the bearing and requires less maintenance” than liquid lubricants.
That variability means there is a grease for every bearing on every occasion, as long as engineers know what to look for. Choosing the right grease may involve a consultation with a lubrication expert to review the special properties of each product, as the list of possible components is extensive. Most base oils are affordable petroleum-based mineral oils, for example, but synthetic oils can add a level of heat resistance that is essential for some industrial applications; similarly, thickening agents also vary widely in terms of temperature suitability.
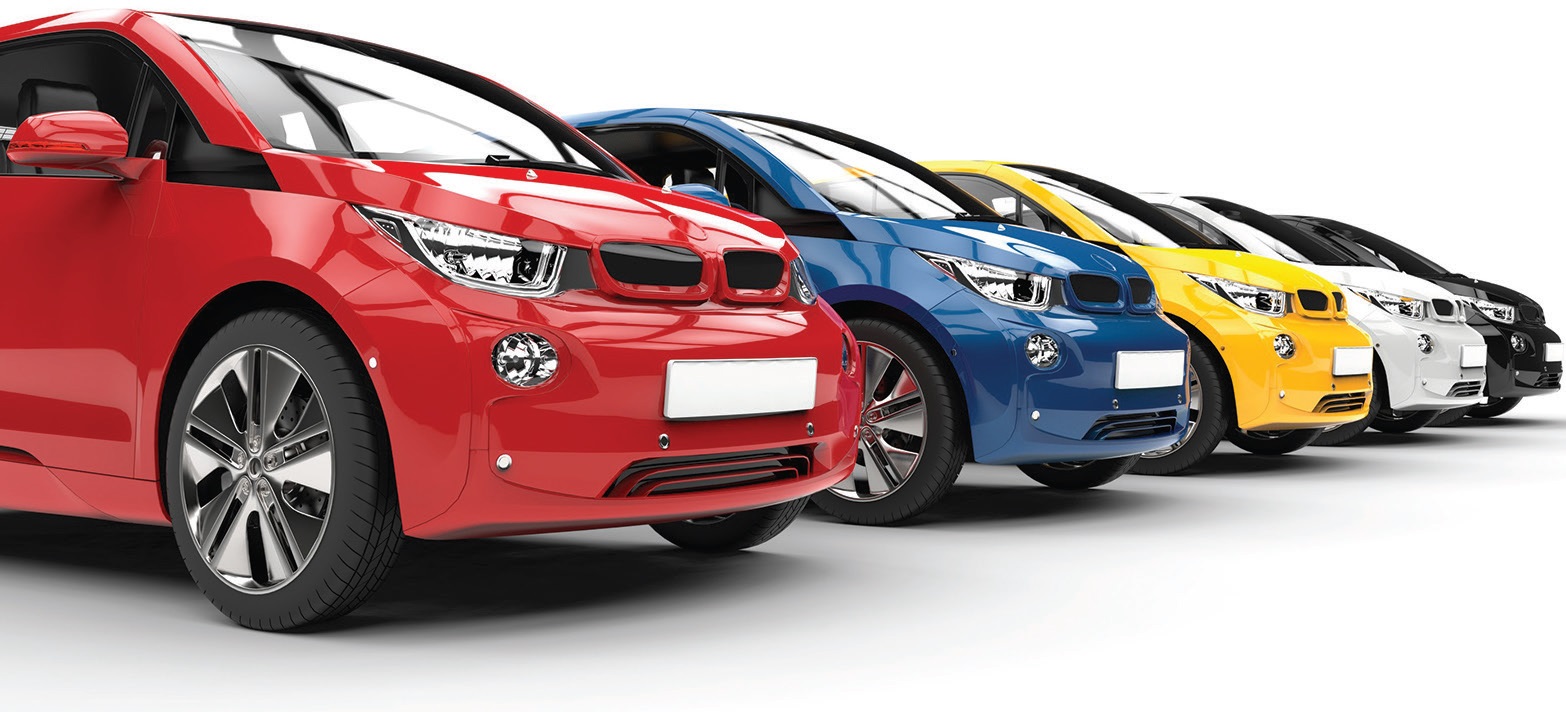
The range of temperatures, especially on the high end, is much wider with electric vehicles.
Getting one’s bearings
The primary role of grease in the automotive space is the lubrication of bearings. Bearings are small but essential pieces of hardware within a motor that restrain the motion of moving parts to the desired direction and manage friction between nearby parts. Bearings are designed to help redistribute force to minimize machine wear within the motor. The rising popularity of electric vehicles changes more than the favored energy source for the vehicle––even the bearings are altered by the new design.
The National Lubricating Grease Institute (NLGI) is a nonprofit trade association responsible for developing internationally recognized grease standards in cooperation with ASTM International and the Society of Automotive Engineers (SAE). Under the NLGI’s Certification Program, the highest standard an automotive chassis or wheel-bearing grease can achieve is the GC-LB certification, according to STLE-member Joe Kaperick, a research scientist and customer technical service advisor at Afton Chemical in Richmond, Va. Kaperick says that although the NLGI GC-LB certification is still in widespread use in the industry, “It is no longer the primary specification used by automotive manufacturers due to evolutions in automotive grease applications, design changes and lack of continued communication between organizations in the automotive grease community.”
Grease for EV bearings
During the past 30 years, demands on automotive grease have changed dramatically. The need for service greases has decreased in favor of bearings and chassis components that come filled-for-life, requiring no re-greasing during maintenance. Today, the NLGI GC-LB specification is used mostly as a marker of quality for certain grease applications, while the pressure to formulate new kinds of greases for the changing market falls to equipment manufacturers.
These new applications are heavily influenced by the demands of electric vehicles. Gear oils, coolants and greases all have to be re-formulated to work while in close contact with electric modules, sensors and circuits, according to Mistry. Lubricants will have to be compatible with a broad range of electrical hardware, including “everything from copper wires and electric modules to special plastics and insulation materials,” says Mistry. “Low-viscosity lubricants will rise in popularity for these applications, thanks to their fuel-economy advantage.” However, “The low-viscosity fluids reduce the film thickness in the application,” Mistry warns. “The reduced film thickness increases the operating temperature and reduces the calculated fatigue life of the bearings.”
The future is electric
Electric vehicle engines deliver a whole new set of challenges to grease formulation. The range of temperatures is much wider, especially on the high end, which puts pressure on bearing lubricants to avert damage to bearings and to minimize noise and torque, according to Mistry.
The thinner lubrication films that result from low-viscosity lubrication also can be supplemented by a performance-enhancing surface coating. To meet these needs, the NLGI has initiated several industry working groups to conduct research and make recommendations for new specifications that will address performance subcategories like water resistance, load-carrying capacity, saltwater corrosion resistance, long life and low-temperature performance.
Grease will continue to be an essential part of engine functioning, says Mistry: “Electric vehicles will have more use of the lubricating grease in comparison to internal combustion engine-powered conventional vehicles because more components will be lubricated by the greases.”
But the greatest challenge to electric vehicle grease is predicting the needs of motors whose specifications are continually evolving. “It is difficult to quantify exactly what issues electric vehicles’ lubricating grease will face, partly because it is not 100% clear how future electric vehicles will run,” says Mistry.
Adds Kaperick: “The current goal [of the NLGI working groups] is to gather feedback on various tests and limits through discussion with all stakeholders to define these first upgraded specifications by the end of June 2020.”
Lynne Peskoe-Yang is a freelance writer based in Tarrytown, N.Y. You can contact her at lynnepeskoeyang@gmail.com.