Deburring metal parts
R. David Whitby | TLT Worldwide January 2020
Vibratory finishing and barrel tumbling are the most frequently chosen options.
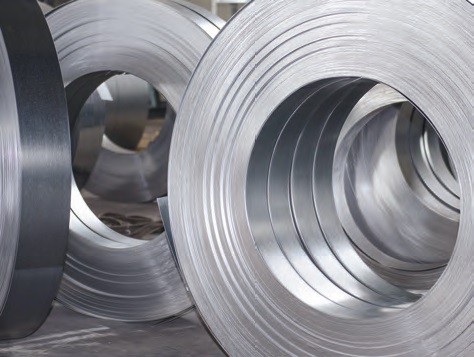
Making flat parts from metal sheets almost always generates small burrs and sharp edges that can cause costly manufacturing problems.
Manufacturing metal parts can involve many types of production engineering processes, including milling, grinding, turning, cutting and drilling. Some of these methods can leave the parts with rough edges or protrusions of material. These imperfections are known as burrs.
The process of removing burrs is called deburring. Left alone, metal burrs potentially can cause costly issues for manufacturers. Deburring is essential to ensure the quality and functionality of metal parts.
Making flat metal parts from sheets using stamping, blanking, punching, shearing or laser cutting almost always results in the generation of small burrs or sharp edges. There are a number of ways to remove these from metal parts, but the two most often used are vibratory finishing and barrel tumbling. Both rely on the effects of friction and wear.
Both types use pre-formed media such as stone, ceramic or plastic. Water is added to carry away burrs and dirt and to carry the media. Chemicals also might be used to improve the action or to clean parts. An abrasive is often added to enhance the cutting and deburring ability of the tumbling media. The abrasive does not act mostly on the parts but helps to keep the tumbling media rough enough to do the job.
A barrel tumbler rotates a load so the parts slide down the barrel like rocks down a hill. It can remove large exposed burrs but is not ideal for parts with recesses. In the process, the parts are abraded and deburred as they bump and scrape against the media and each other.
A vibratory tumbler creates a scrubbing action of surrounding media against the parts and is generally used for very smooth surfaces. A vibratory tumbler produces an action similar to filing, applying an upward, angular force that causes a shearing action where parts and media rub together. The larger the parts or media, the faster the cutting action will be. A vibratory tumbler grinds at an applied force that is five to 10 times the force exerted by the free-falling action of a barrel tumbler. Compared with a barrel tumbler, a vibratory tumbler is very effective for recessed areas and is faster. The cutting action of a barrel tumbler occurs on about 20%-30% of the load, while the entire load is cut with each pulse of a vibratory tumbler, giving a shorter cycle time.
A vibratory tumbler can be used on fragile parts with small radiuses, since there is no tearing action or unequal forces to cause bends or distortion. A barrel tumbler excels at deburring parts with heavy radiuses or where more material needs to be removed and corners can be rounded off. While the speed and amplitude of vibration used will vary in different machines, high speeds and small amplitudes are generally used for fine finishes or delicate parts, while large amplitudes are used for heavier cutting. High speeds and large amplitudes can roll burrs in or peen metal into holes and mushroom edges.
Other deburring processes can be used, including media blasting, sanding, wire brushing, abrasive flow machining and electrochemical, thermal energy and manual deburring. In the last process, a skilled craftsperson can remove burrs by hand using specialized tools. This is flexible and cost effective, but it requires a significant investment of time, making it unsuitable for finishing a large quantity of parts.
Thermal deburring burns away burrs in a sealed chamber, quickly targeting burrs on multiple surfaces and many pieces at once. The process uses the thermal energy of an explosive gas mixture. The parts are loaded into an explosion-proof chamber, which is then sealed, clamped with approximately 220 metric tons, evacuated of air and filled with an oxygen and fuel mix, which is pressurised to 0.5 to 1.9 MPa (73 to 276 psi). An electrical igniter then ignites the mixture, causing all burrs to burn away. The peak temperature reaches 3,000 C (5,432 F).
Electrochemical deburring is used on precision work pieces and edges that are hard to reach, such as intersecting holes. The process uses a salt or glycol solution and electricity to dissolve the burr. The electric current is applied with a specialized tool to reach the burr location. Burrs are removed in five to 10 seconds, while the rest of the work piece is unaffected.
David Whitby is chief executive of Pathmaster Marketing Ltd. in Surrey, England. You can reach him at pathmaster.marketing@yahoo.co.uk.