Bearing the load
Mary Beckman, Contributing Editor | TLT Feature Article July 2019
Green tribology is propelling sliding and rolling bearings into a more sustainable future.
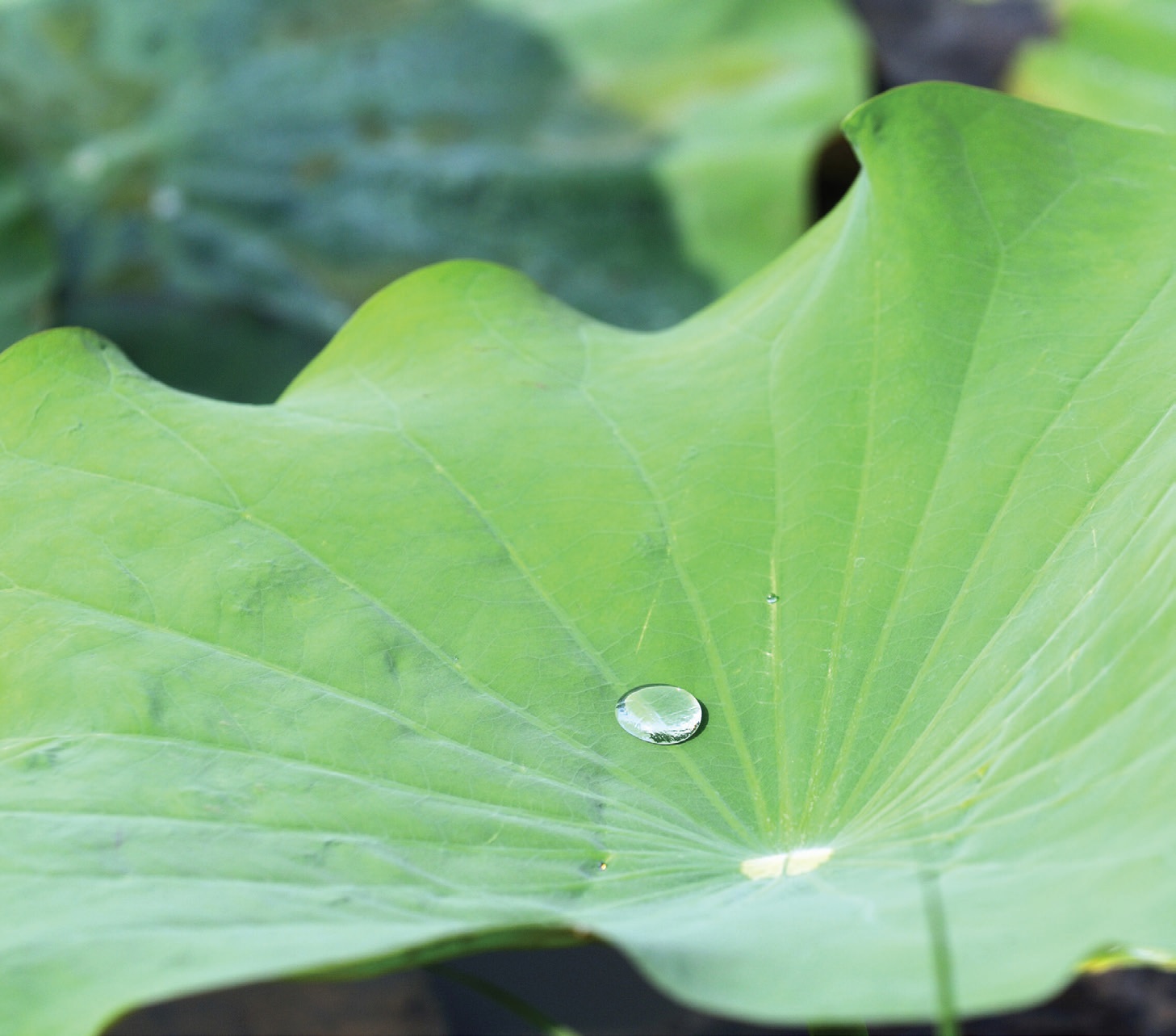
© Can Stock Photo / narapornm
KEY CONCEPTS
•
Because bearings are everywhere, incorporating green tribology concepts into their lubrication can significantly impact the environment.
•
Self-lubrication cuts down on the need for petroleum-based liquid lubricants.
•
Inserting tribological concepts such as dynamic friction can improve friction models.
As any kid doing maintenance on her first bike knows, bearings need a lot of grease to keep those wheels turning smoothly. But slopping that gloopy mess in and amongst the ball bearings in the wheel’s hub while catching slight whiffs of petroleum are good reminders that maybe there are more ecologically friendly ways to cut friction.
Going green could have a large impact on the environment because bearings are ubiquitous. They are used wherever rotation is needed—in automotive or bicycle wheel axles, cranes, turntables, ceiling fans, computer hard disk drives, spacecraft and even toys like fidget spinners (
1).
They’re more than instruments of spin, though. Bearings generally support the weight of a device while at the same time allow for rotational motion on a shaft. Engineers have to design bearings that sustain a load without damaging the surfaces the bearings contact. And those bearings have to last.
To optimize a bearing’s lifespan, engineers analyze its geometry, materials, surface finishes and lubricants to find a cost-effective and practical solution.
“Discovering novel green lubricants, materials and surface-texturing processes could help prolong the life of a bearing by mitigating unwanted friction and wear, meaning more run time and less cost,” says Rob Morien, senior engineer at Rexnord Industries, LLC, in Milwaukee, Wis., and a TLT technical editor.
The lotus and the engineer
About a decade ago, the founding father of tribology, British mechanical engineer H. Peter Jost, proposed a kind of tribology that supported environmental sustainability and energy efficiency in its applications, calling it green tribology (
2).
The term is a large umbrella, including biomimetic tribology that takes its cues from nature; the control of friction and wear, which contributes to energy efficiency and can partake in environmentally friendly lubrication or surfaces; and the tribological aspects of green technology such as wind turbines or solar panels.
One of the earliest discoveries that pushed green tribology forward, says mechanical engineer Michael Nosonovsky of the University of Wisconsin-Milwaukee, was figuring out how to copy the lotus flower’s performance of its world-famous self-cleaning act.
Long a symbol of purity in India and China, and more recently a staple in teaching labs, the lotus flower repels water droplets on its leaves. Drops rolling down its leaves pick up dirt as well, washing off mud and grime and leaving the leaf a spotless green.
Once nanotechnology advanced enough to allow researchers to mimic the surface, green tribology took off. The key to the flower’s self-cleaning ability lies in microscopic surface features—a hierarchy of tiny bumps and rough surfaces—that make the leaf surface superhydrophobic.
“In nature there are perfect or almost perfect solutions of certain problems which engineers can borrow and mimic to develop new technology,” says Nosonovsky. “The lotus effect is the most successful biomimetic concept in surface science. There are many other ideas. The gecko effect mimics the adhesion of a gecko foot; the sharkskin effect mimics reduction of drag in water. We can learn something from nature, from biology.”
Nosonovsky adds that although technically tribology refers to the friction of two solid surfaces interacting, examples like the lotus leaf are relevant because lubrication—often a liquid but sometimes part of the solid surface itself—is used to mitigate that friction.
“In bearings, self-lubrication in the form of solid coatings, such as molybdenum disulfide (MoS
2), graphite, diamond, diamond-like carbon and others, are important trends,” says mechanical engineer Vahid Mortazavi at Zoomlion NA in Milwaukee. “Although self-cleaning coatings are not being used in the bearings industry, they could be. Self-cleaning materials is a new field for mechanical engineers. But even if the engineered surfaces perform well, they are not wear resistant enough. Wear is a serious issue in bearings, and a large amount research is needed to show new paths in this field.”
One of the biggest challenges in producing new coatings is they are highly dependent on the testing environment.
Mortazavi says, “For example, if we move them from a humid environment to a dry one, they might not perform in the same way. We transfer the surfaces to different locations, and these materials perform very differently.”
A model of friction
Controlling friction and wear to improve energy usage and sustainability is a function of green tribology in which bearings can play a role. At its essence, tribology can improve energy efficiency by providing better models of friction at the microscopic scale, which can improve overall design, Nosonovsky says.
Traditionally engineers model friction using concepts that are centuries old and don’t take into account tribological effects. Basically, engineers use classical laws of sliding friction to determine how much friction will arise between surfaces. Known as the Amontons-Coulomb laws, they determine friction by multiplying the perpendicular load by the coefficient of friction.
The key here is the coefficient of friction is found experimentally for whatever material the surfaces of interest are made of—and is unreliable. In one study researchers sent the same samples to different labs to determine friction coefficients. The coefficients still differed by a factor of two (
3).
The margins of error appear because the interactions of the surfaces at the scale at which friction occurs are much more dynamic than bulk material would suggest. For example, the distribution of material at the interface is usually heterogeneous, causing more friction in some spots and less in others as the two surfaces slide against each other.
“There’s no reason why the coefficient of friction should be constant in these situations,” says Nosonovsky. “There is no physical law behind that.”
Nosonovsky says using tribological concepts can improve models of friction. Called dynamic friction modeling, these methods take into consideration that the coefficient of friction can change depending on the sliding velocity of the interacting surfaces and other parameters.
“Engineers might benefit from using more of the models that physicists use, which can accurately predict certain phenomenon,” he says. “There are some interesting results in dynamic friction modeling, which also can be used by engineers, for example, in friction-induced tribological films that reduce friction and protect against wear. But it’s a matter of time for new ideas to penetrate from physics and mathematics into applications.”
© Can Stock Photo / cookelma
A solid way to cut friction
Tribological films are one way that researchers have been making bearings and other surfaces self-lubricating.
“Self-lubrication is when you have a material that produces lubrication by itself. You have friction which triggers, through heat generation or through some other effects, processes that release lubricant that is embedded in the material. You can have liquid lubricant, a tribofilm that forms at the interface, or you may have solid lubricant such as solid graphite,” says Nosonovsky.
“The major advancements are happening in solid lubricants now,” says Mortazavi. “In big spacecraft, they can’t use liquid- or grease-lubricated contacts because of the temperature and pressure the surfaces encounter. Because of that, the aerospace industry asked, how can we eliminate the need for liquid or grease lubrication? And that’s how we arrived at the idea of using solid lubricants.”
Tribological films, or tribofilms, arise through a process called self-organization at the interfaces of two materials. Friction between two materials creates a lot of heat, which dissipates and causes a temperature gradient at the interface. High temperatures at the interface decrease farther away from the interface. This gradient can result in diffusion of flow over the material and a nonhomogeneous distribution of the material inside.
“Tribofilms form at the interface and the process results in self-organized structures,” says Nosonovsky. “Frictional self-organization is something interesting and important. It is related to frictional instability mathematically, which may lead to self-organized structure on the frictional interface.”
Using composites with a metal matrix and graphite particles takes advantage of self-organization to provide solid lubrication, says materials scientist Pradeep Rohatgi at the University of Wisconsin-Milwaukee. For example, a bearing made out of copper or aluminum contains particles of graphite embedded in the surface. As the surface of the bearing wears down, the graphite smears, forming a film of graphite. The exceedingly low coefficient of friction corresponds to graphite, not the metal the tribofilm is sandwiched between.
Mica, talc and molybdenum disulfide also are possible solid lubricants, but graphite is the most popular because it is the cheapest and has the lowest friction coefficient.
Bearings with these qualities are commercially available, says Rohatgi, but are usually made with the more expensive process of powder metallurgy. Over the years, he and his team have developed a cost-efficient casting method.
“But solid-lubricant-dispersed metals still have not been used on a large scale,” says Rohatgi. “More trials are needed, and industry has to be aggressive to incorporate these new bearings, particularly the bearings made by low-cost casting techniques. The research has been ahead of its use, but now we would like industry to begin to test and use them.”
Using the casting method is not only cheaper but can be used to make very large components. “One example is for large ships with big engines. Their engine bearings are very large, up to two or three feet long. They cannot be made by powder metallurgy,” Rohatgi says.
In powder metallurgy, copper-graphite or silver-graphite bearings are made by mixing copper powder with graphite powder. The bearings are pressed and sintered. But to make components in bulk, a foundry casting process is much cheaper.
In Rohatgi’s process, manufacturers create a suspension of solid lubricant particles in metallic melts and then solidify the suspension to produce a bearing. Before solidifying, engineers can centrifuge the suspension of copper melt and graphite, causing the solid lubricant to come to the inner periphery of a cylindrical bearing, where it is needed for solid lubrication.
“It allows you to make much cheaper functionally gradient bearings where the solid lubricant is exactly where you want it,” says Rohatgi. “In this case the solid particles of lubricant are embedded throughout the cross section. So even if the bearing wears, the next layer also has solid lubricant in it. So despite wear, the solid lubricant properties continue to be exhibited.”
Patterning friction
Some researchers are trying to understand how self-organizing surfaces lead to tribofilms. Mortazavi and Nosonovsky are exploring a kind of self-organization of surfaces due to reaction-diffusion mechanisms caused by friction, called Turing systems. The researchers used computer simulations to suggest a theoretical framework for many different experimental observations of self-organized patterns reported by different researchers (
4).
“As designers, we don’t know from the start what will be the real-contact mechanisms and what kind of tribofilm those mechanisms will produce,” says Mortazavi. “What we can do—by fully examining materials and carefully understanding the combination of materials—is predict their effects and their interactions.”
To get that understanding, they started to model the surfaces at the microscopic level. They looked closely at how various materials interacted with each other, at the effect of surface roughness and how the surface roughness evolves during wear.
“We can choose different combinations of materials in different applications in a way that frictional contact between these two surfaces generate desired films and patterns and reduce friction and wear,” Mortazavi says. “We can select the materials based on their characteristics, surface-roughness distribution shape, the size of patterns and their arrangement. For example, we might find that for certain kinds of applications, a particular combination of materials might lead to these kinds of patterns that we desire.”
They are hoping with enough research they will be able to eventually determine how films might be formed and what the main parameters are that influence film formation.
In recent research, Mortazavi says, they see tribofilms forming, but it doesn’t take long for the films to get destructed and eliminated. They are following up to learn how to identify the films, how they form and how to help those patterns and films last longer than they currently do (
4).
The liquid way
While some researchers work on solid lubrication, green tribology also reduces friction the old-fashioned way in the form of biodegradable lubricants derived from biological sources such as biomass. STLE-member Pradeep Menezes, materials engineer at the Surface Engineering and Tribology lab, University of Nevada, Reno, says that biologically derived lubricants can be designed to handle higher loads and last longer than traditional petroleum-based products.
Some of the advantages of biolubricants are:
•
higher lubricity lending to lower friction losses
•
improved efficiency affording more power output
•
better fuel economy
•
lower volatility resulting in decreased exhaust emissions
•
higher viscosity indices
•
higher shear stability
•
higher detergency eliminating the need for detergent additives
•
high dispersancy
•
rapid biodegradation resulting in decreased environmental and toxicological hazards.
While some biolubricants come directly from biological oils, others such as ionic liquids also show promise (
5). Ionic liquids are essentially organic and inorganic salts that melt at low temperature, so they are generally in a liquid state at ambient temperatures. For example, melting table salt, sodium chloride, above its 800 C temperature creates a liquid of positively charged sodium ions and negatively charged chloride ions that would burn your steak beyond edibility. Ionic liquids that melt at more practical temperatures include phosphonium and imidazolium-based ionic liquids.
Menezes says these ionic liquids can be produced from bio-based feedstocks such as fructose. Ionic liquids have advantages over older biolubricants derived from plant oils. Plant oil lubricants oxidize, turn solid at low temperatures, are inconsistent in their chemical makeup and deteriorate. To address these disadvantages, some lubricant producers chemically modify the biolubricants or add stabilizers.
Phosphonium and imidazolium-based ionic liquids, however, interact chemically with metal or ceramic surfaces in such a way that they exhibit very low coefficients of friction. Ionic liquids are stable at high temperatures and have low volatility. They also can be designed to have characteristics of traditional biolubricants such as polar molecules (
6).
“These properties of ionic liquids can help overcome the environmental, commercial and sustainability limitations of petroleum-based oils, natural oils and green solid-powder lubricants,” says Menezes.
Inviting surface
To ensure bearings make the most of green lubrication, researchers have used several methods to texture the surface. One, called laser shock peening, enhances wear resistance of bearings while being flexible and easily controlled during use.
Other surface texturing processes such as grinding, etching, embossing and laser surface texturing (LST) create patterned textures on surfaces to control the coefficient of friction and improve how long the lubrication lasts.
In LST, engineers shoot ultrashort laser pulses at surface materials and generate surface micro-features such as very tiny dimples. These micro-dimples serve as reservoirs for lubricant or micro-taps for wear debris in both lubricated and dry sliding, ultimately resulting in the sought-after coefficients of friction.
Unfortunately, these surface textures degrade due to low wear resistance. Pockmarking the surfaces with lasers causes a heat-induced softening and generates tensile residual stresses.
To counter these deficiencies, Menezes and his team have developed an indirect-laser shock surface patterning, which provides enhanced wear resistance and better coefficients of friction (
7). This method creates the wear resistance surface and arrays of micro-indentations simultaneously.
REFERENCES
1.
What are bearings? Available
here.
2.
Founding Father of tribology’ Peter Jost wins top Academy Award, Royal Academy of Engineering. Available
here.
3.
Nosonovsky, M. (March 2018), “Beyond the Sticking Point,”
Mechanical Engineering. Available
here.
4.
Mortazavi, V. and Nosonovsky, M. (2011), “Friction-induced Pattern Formation and Turing Systems,”
Langmuir,
27 (8), pp. 4772-4779. Available
here.
5.
Reeves, C. J., Siddaiah, A. and Menezes, P. L. (2017), “Ionic Liquids: A Plausible Future of Bio-lubricants,”
Journal of Bio- and Tribo-Corrosion,
3 (18). Available
here.
6.
Reeves, C. J., Siddaiah, A. and Menezes, P. L. (2019), “Friction and Wear Behavior of Environmentally Friendly Ionic Liquids for Sustainability of Biolubricants,”
ASME: Journal of Tribology,
141 (5), 051604-051604-11. Available
here.
7.
Mao, B., Siddaiah, A., Menezes, P. L. and Liao, Y. (2018), “Surface Texturing by Indirect Laser Shock Surface Patterning for Manipulated Friction Coefficient,”
Journal of Materials Processing Technology,
257, pp. 227-233. Available
here.
Mary Beckman is a free-lance science writer based in Richland, Wash. You can contact her at mbeckman@nasw.org.