Condition monitoring of metalworking fluids
Jane Marie Andrew, Contributing Editor | TLT Webinars January 2019
A variety of tests are available to evaluate metalworking fluids.
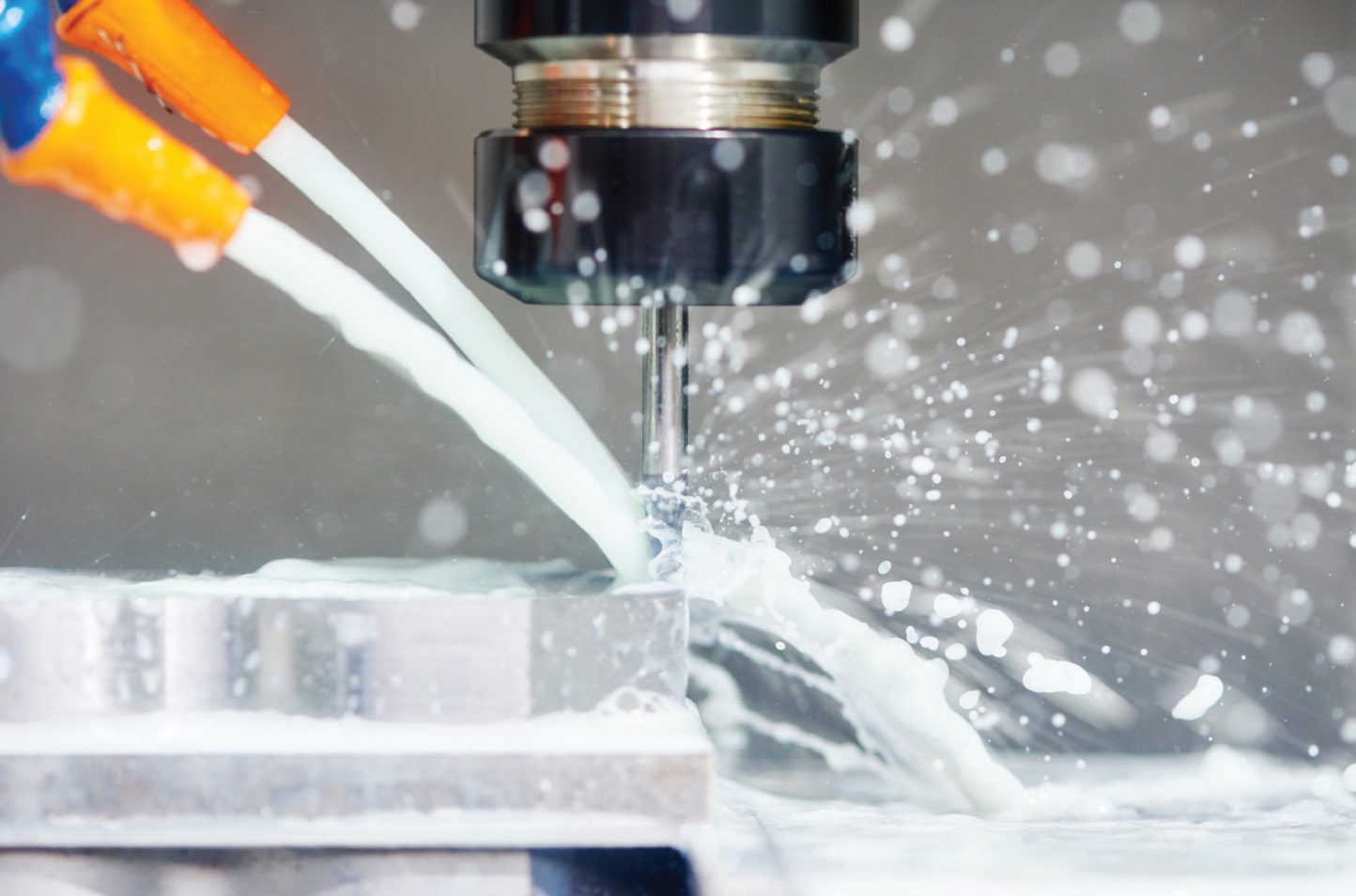
© Can Stock Photo / kadmy
KEY CONCEPTS
•
The condition of MWFs must be monitored to ensure optimum fluid performance over an extended operating time.
•
The most important way to test an in-use MWF is to use a refractometer to measure concentration.
•
Other tests can be used to evaluate concentration in a different manner, determine the condition of the fluid and assess the degree of biological contamination.
MEET THE PRESENTER
This article is based on a Webinar originally presented by STLE Education on Aug. 22, 2018.
Condition Monitoring of MWFs is available at
www.stle.org: $39 to STLE members, $59 for all others.
Neil Canter received his doctorate in chemistry from the University of Michigan in 1983 and his bachelor’s of science degree in chemistry from Brown University in 1978. He has worked in the MWF industry for more than 30 years. Neil runs his own consulting company, Chemical Solutions, in Willow Grove, Pa., and specializes in commercial development, marketing, product development and regulatory support for the MWF industry. He is a member of the American Chemical Society, SAE and STLE and writes TLT’s monthly Tech Beat column. Neil also wrote the chapter "Chemistry of Metalworking Fluids" in the book Metalworking Fluids, Third Edition, published by CRC Press. He is a member of STLE’s board of directors, MWF Steering Committee, MWF Education & Training Subcommittee and Education Committee. You can reach Canter at
ncanter@chemsolutions.com.
Dr. Neil Canter
End-users would like to use metalworking fluids (MWFs) for an extended period of time without removing them. To accomplish this goal, MWFs must be monitored periodically to assess their condition and make necessary changes to ensure the fluid can operate at an optimum level.
Monitoring is about measurement, of course. As W.E. Deming pointed out, you cannot manage what you do not measure. But before measuring an MWF system, the end-user or fluid manager must decide what needs to be managed. A good monitoring protocol has three features.
1)
It has a clear rationale. That is, it centers on control limits that have been chosen to support specific operational priorities, for example, concentration. The protocol specifies test methods suitable to these chosen control limits.
2.)
It specifies a testing schedule to ensure that tests are conducted and recorded systematically—whether before a shift, daily, weekly, monthly or on some other appropriate schedule.
3.)
It specifies procedures to develop and maintain historical data and to evaluate these data for trends (positive and negative) that may require corrective action.
With a monitoring protocol in place, end-users and fluid managers will have the right data to guide both short- and long-term decisions about process changes (
see Best Practices for Condition Monitoring of MWFs).
BEST PRACTICES FOR CONDITION MONITORING OF MWFs
Administration
•
Make sure test operators are well trained.
•
Have the same one (or few) individual(s) do all tests.
•
Make sure results are charted, logged electronically and promptly interpreted.
•
Make sure there’s a regular schedule and ensure staff adhere to it.
Equipment and tests
•
Use digital equipment (digital refractometer, pH meter).
•
Practice lab safety when running these test methods.
•
Consider ATP testing instead of the dip slide test to more efficiently conduct biological analyses.
Sample selection and sampling
The first factor to consider is where to collect a sample from the MWF system. The easy approach is to sample the MWF in a place that is convenient. However, when it is necessary to determine whether changes in a specific parameter are affecting the system, the best sample location may be difficult to reach. Before deciding where to sample, the fluid manager or end-user must understand what MWF parameters will be tested. For a given system, sampling should always be done in the same location.
Some simple sampling choices can go a long way toward improving the efficiency and validity of a monitoring program:
•
New container or reused container? A new container must be used! Otherwise the monitoring program is invalidated because of contamination. Keep a stock of new containers on hand.
•
Glass container or plastic? Glass allows for better evaluation of the condition of the fluid (e.g., the state of emulsion), but caution must be exercised in transporting or shipping the sample because of the possibility of breakage. For samples that must be shipped, high-density polyethylene containers might be a better choice.
Next are some choices that take more judgment:
•
Dip or drain? This choice depends on the nature of the operation and what question needs to be answered. Dipped (or grabbed) samples must be taken about 1 to 1.5 inches (2.5-3.8 cm) below the surface. For drained samples, typically the tap is flushed by draining more than two volumes of fluid and then the bottle is filled to 70% or 80% of capacity.
•
Clean side or dirty side? The measurements are similar—concentration of MWF, pH, alkalinity, concentration of tramp oil, microbial populations, sediment—but the best test location depends on the condition of the MWF. For troubleshooting, a sample should be taken from the dirty side.
•
Chemical problem or biological problem? The choice of what category to test first and which method to use depends on the source of the problem.
Finally, collection methods must be consistent and systematic. Some methods might be sensitive to variation among operators, which means it may be important to have the same person collect the sample every time.
Testing methods
Testing methods can be considered in three categories, depending on their objective: concentration tests, condition tests and biological analysis. Table 1 summarizes the test methods discussed in this section.
Table 1. Summary of MWF condition monitoring tests
(Table courtesy of STLE.)
Concentration tests
Whether the MWF appears to be functioning well or problems have been detected, the most important monitoring test is to check the concentration of the fluid.
The best approach for measuring concentration is to use either an analog or digital
refractometer. This technique is fast, easy, portable and powerful. To revisit basic physics, a refractometer measures concentration by determining the difference in how fast light travels through the MWF system compared to water.
To use an analog refractometer, the user places a drop of fluid on the device, then looks through an eyepiece to determine where a line falls on a Brix chart within the instrument; the position of the line on the chart gives the “Brix reading.” The reading is multiplied by a factor provided by the manufacturer of the MWF to obtain the concentration.
Digital refractometers (
see photos) are recommended because they are not only faster but also more precise and accurate than analog units. A digital unit reads out the concentration directly, eliminating the conversion step in the analog method. Both lab and portable models are available.
Digital refractometers.
Refractometers are easy to use in both the lab and the field and are compatible with all water-dilutable MWFs. Both types are sensitive to temperature changes and should be stored in a controlled-temperature environment. (Leaving a refractometer in a vehicle over the weekend in a northern winter is an invitation to trouble.)
An
alkalinity titration measures the amount of acid required to drop the pH of the fluid to 4.5. This amount is the buffering capacity of the MWF (also called reserve alkalinity), which correlates to its ability to handle changes in contamination. If an MWF has significant buffering capacity and if minimal contaminants are added (or created) that change its alkalinity, the alkalinity titration can be used to estimate the concentration. The alkalinity titration can be used to analyze all water-dilutable MWFs.
In formulating MWFs, alkanolamines such as triethanolamine (TEA) are the key additive type used to maintain the pH near 9 for a diluted fluid. Alkanolamines are known as reserve alkalinity boosters.
The alkalinity titration is a wet-chemical process that must be done in a lab. It is relatively easy to perform and easy to automate for production analysis. Some contaminants and additives can affect the result. For example, microbial growth and acidic contaminants can reduce the reserve alkalinity of a fluid. On the other hand, metal cleaners used by end-users are typically highly alkaline with pH values into the 11-12 range—that is, higher than MWFs. Thus, contamination with metal cleaners may increase the reserve alkalinity.
For emulsifiable oils and semisynthetic fluids, the acid break method can be used to determine the concentration of the MWF. Mineral acids (such as sulfuric acid) or salts are added to split the emulsion, usually with the aid of heat and centrifugation. If a clean split occurs, the separated oil is proportional to the emulsified oil. Note that this method will not work for a water-dilutable, synthetic fluid because this formulation does not produce an emulsion when diluted. A potential complication is the development of a “rag layer” between the oil layer and the water layer. The rag layer may indicate either an incomplete split or the presence of hydrolyzed soaps and/or esters. Further treatment with mineral acids and/or salts is needed to eliminate the rag layer.
The acid break method gives an accurate measure of the emulsified oil. It can be performed in the field, although extreme care is required because of the highly dangerous acids involved. When combined with the cationic titration test (described next), the results may give an idea of the future stability of the emulsion.
Another wet-chemical technique, the
cationic titration method, can be used for MWFs with anionic emulsifiers such as sodium petroleum sulfonate and amine salts of fatty acids. The procedure involves titrating the anionic emulsifiers in the fluid with a cationic emulsifier known as Hyamine®. Once all of the anionic emulsifiers react with the Hyamine, a weakly anionic indicator (bromphenol blue) reacts with excess Hyamine to form a water-insoluble complex that migrates into a solvent layer, leading to the final endpoint for the test method. This procedure is extremely difficult to reproduce and depends significantly on the skill of the operator. A variation of the method uses compounds that produce different colors in the layers, making the test somewhat easier to carry out.
This test produces accurate results, but it is limited to the class of MWFs that use anionic emulsifiers, and it is not suitable for use in the field.
Condition tests
Once the concentration of the MWF is determined, additional testing is needed to assess the condition of the MWF. Tests that are conducted include pH, conductivity, corrosion, tramp oil and suspended solids.
MWFs typically operate in a
pH range between 8.5 and 10.0, which prevents most corrosion issues with ferrous metals. (End-users should verify the optimum pH range with their MWF supplier.) In a properly maintained system, the pH should remain stable.
A drift in the pH can signal a range of issues:
•
Out-of-spec fluid concentration
•
Excessive biomass
•
Contamination
•
The presence of free oil and/or an invert emulsion
•
Buildup of chips, fines, swarf and other residues.
In general, most contaminants lower the pH of the fluid. Highly alkaline cleaners will increase the pH of the fluid. Remove free oils and residues before testing (e.g., by skimming or centrifuging) because such contaminants can interfere with the pH probe.
pH can be measured with color-changing paper strips or with handheld or countertop meters. The best results are achieved with either a handheld or countertop meter. Paper strips should only be used if no meter is available, because the pigment degrades over time. For meters, countertop units are preferred because they are more accurate. A key caution for all pH meters: The probes are delicate! The electrodes
must be maintained correctly by keeping them in an electrode storage solution; otherwise they will deteriorate, resulting in costly replacement and recalibration.
Conductivity is a measure of the concentration of ions in an MWF. Changes in ion concentration can make the MWF less stable. For emulsifiable or semisynthetic systems, a large change in conductivity is a danger sign. As with pH meters, lab units are preferable, but handheld units will still give reasonable results.
Ferrous corrosion is a concern because water-dilutable MWFs are in close proximity to the steel alloys used in machining operations. A standard test for evaluating ferrous corrosion is the cast iron chip test (ASTM D4627). The objective in this test is to find the lowest concentration for which no corrosion is seen (the break point). In this method, the fluid is evaluated at specific concentrations in 100 ppm water. The cast iron chips are placed on filter paper in the fluid for 24 hours, after which the paper is removed and examined for corrosion. It can be important to run some variations of such corrosion tests. For example, depending on the hardness of the water, testing at 200 ppm or 500 ppm may be needed to accurately determine how the fluid will perform under adverse operating conditions.
Tramp oil and
invert emulsions can be detrimental to the MWF system and must be monitored. Tramp oil—a catchall term for various insoluble, oil-based contaminants—enters the MWF from other parts of the metalworking process. Invert emulsion, or cream, forms when water droplets are dispersed in a continuous oil phase (the inverse of the usual oil-in-water emulsion). Both are measured by centrifuging the MWF in Babcock bottles; the oil volume is measured from graduations on the bottles.
Suspended solids also can be evaluated by centrifugation, especially while measuring tramp oil and invert emulsion, but the results are of marginal accuracy. Filtration methods, although time consuming, are far more accurate.
Biological analyses
For systems using water-dilutable MWFs, a pivotal issue is microbial contamination. Two important distinctions must be made between sampling strategies for chemical versus biological tests: sampling location and timing.
First, the ideal place to get a biological sample is not from the fluid but rather from a surface, because that is where colonies are established. That kind of sampling may not be feasible, however, especially when time is critical for making decisions about remediation. The best compromise is to collect samples at the intersection of the surface and the fluid. Biofilms present their own brand of sampling trickiness. The best strategy is to draw down the MWF by an inch or two (several centimeters), if feasible, and collect a sample of the newly exposed film.
A second distinction is that for biological samples, time matters. The traditional method for identifying microbial contamination has been a culture test, which can take days. In this method, a sample is applied to a culture medium, and microbial populations are allowed to grow, typically for 1-3 days. (For mycobacteria, which are of commercial concern because of health risks, the necessary incubation period could be as long as two weeks.) This delay can render culture tests useless for operational decisions. Another issue is that microbes do not stop growing just because they have been collected in a sample. The longer an analysis is delayed, the less accurate the results might be. If culture testing is appropriate but cannot be done immediately, there are ways to compensate: Samples can be stored in a cool, dark place (to slow growth) and shipped by overnight delivery.
Traditional culture tests, such as the well-established dip slide test, use a specially designed vial with an attached dip paddle coated with a culture medium. A sample is obtained by dipping the paddle in the MWF; the sample is incubated in the sample vial at just above room temperature for 24-48 hours for bacteria and three days for fungi. Growth is measured on a log scale of colony-forming units (CFU) per milliliter.
A push for faster results and better accuracy has resulted in effective new chemical tests. One of these is based on a biological molecule called
adenosine triphosphate (ATP), a key molecule in the metabolism of all living cells. ATP levels are a measure of microbial populations because they reflect metabolic activity. This test is very sensitive to small quantities of ATP and is both rapid and portable. A recently developed test method (ASTM E2694-16) eliminates interference from complex organic fluids such as MWFs.
A second chemical test uses
catalase, an enzyme present in all fungi and most bacteria except anaerobes (bacteria that do not require oxygen to grow). Catalase catalyzes the decomposition of hydrogen peroxide within cells. Thus, like ATP, catalase is a marker for metabolism and, by extension, population. The catalase test is more broadly sensitive than dip slides, because it easily reveals fungi (which are notoriously slow to culture) and also signals the presence of microbes that cannot easily be cultured.
© Can Stock Photo / nd3000
Applying monitoring data
The objective of a condition monitoring program is to track key parameters that affect an MWF system over time and to use the data to take corrective action when a problem is occurring.
For example, Figure 1 shows how a specific MWF system was tracked over a nine-month period. After five months, the data showed that the system’s tooling costs (dark blue curve), bacteria levels (light blue curve) and tramp oil levels (yellow curve) all increased, while the concentration of the MWF (purple curve) declined. Corrective measures were taken to increase the concentration, which facilitated a decline in tooling costs, bacteria levels and tramp oil. This example shows how data obtained from monitoring specific properties of an MWF system can be applied to improve the operating condition of the fluid and reduce costs.
Figure 1. Plotting test results together over time can reveal trends that need corrective action. Here, correcting the concentration (around August) has reduced tooling costs. (Figure courtesy of STLE.)
The key to maintaining MWFs at an optimum performance level over a long period is to use the test methods discussed here as part of a fluid management program. Condition monitoring is essential to identify potential issues with MWF systems and quickly resolve them. Further information on the condition monitoring tests discussed in this article can be found in the 3rd edition of Metalworking Fluids (
1).
REFERENCE
1.
Byers, J. (2018), “Laboratory Evaluation of Metalworking Fluids,” in
Metalworking Fluids, 3rd Edition, edited by J. Byers (CRC Press, Boca Raton, Fla.), pp. 188-215.
Jane Marie Andrew is a free-lance science writer and editor based in the Chicago area. You can contact her at jane@janemarieandrew.com.