Extreme pressure/antiwear additives and friction modifiers
Jeanna Van Rensselar, Senior Feature Writer | TLT Webinars December 2018
These additives work together to protect the surface of the equipment.
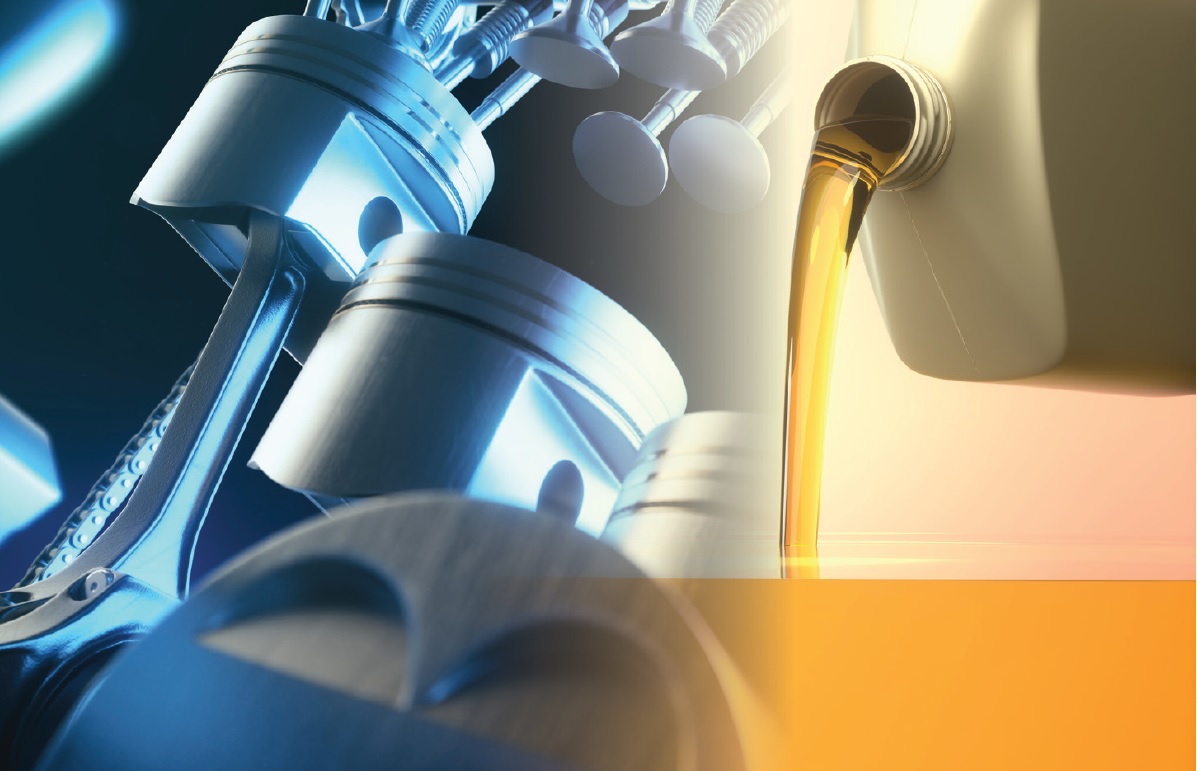
© Can Stock Photo / Rost9 and / iDesign
KEY CONCEPTS
•
Extreme pressure/antiwear additives mitigate the macroscopic welding and breaking of microscopic asperities by forming strong protective films.
•
Friction modifiers mitigate increased energy consumption and poor fuel economy by forming easy-to-shear films that reduce friction.
•
Formulators should consider synergistic, neutral or antagonistic behavior among additives to balance the lubricant for overall performance.
MEET THE PRESENTER
This article is based on a Webinar originally presented by STLE Education on April 5, 2017. Antiwear Additives and Friction Modifiers is available at www.stle.org: $39 to STLE members, $59 for all others.
Dr. Bridgett Rakestraw is currently a senior scientist in the Fuel and Lubricant Solutions Group at BASF in Tarrytown, N.Y. For the past four years she has been supporting the development of antioxidants in automotive and industrial applications. Before BASF Rakestraw was an adjunct professor in general chemistry at Sinclair Community College in Dayton, Ohio, for two years. She earned her doctorate in physical chemistry from the University of Cincinnati where she studied reactions of the troposphere. She received her bachelor’s of science degree in chemistry from Ball State University in Muncie, Ind. You can reach Rakestraw at
bridgett.rakestraw@basf.com.
Dr. Bridgett Rakestraw
For a lubricant to function effectively, the base oil and additives must function well together. The base oil removes heat from the system. It has a level of lubricity itself and serves as a mode of additive transport. The additives are divided into two categories: bulk oil active additives and surface active additives.
Surface active extreme pressure (EP), antiwear (AW) additives and friction modifiers are the focus of this article. EP/AW additives and friction modifiers often have similar mechanisms of delivery for the same or similar purpose of reducing wear and friction. In order to better describe EP/AW additives, friction modifiers and their activity, we first need to formally describe wear and friction through the basic lubrication regimes.
Types of wear
Wear is defined as the progressive loss of substance from the operating surfaces of a body resulting from relative motion. Even surfaces that appear smooth to the naked eye will have microscopic peaks and troughs called asperities (the high and low points). The asperities can participate in different types of wear modes depending on the application.
Types of wear include:
1.
Adhesive wear. This occurs when two objects are in sliding contact. The asperities may be sheared off, resulting in fragments detaching from one surface and attaching to another.
2.
Abrasive wear. This happens when there is a presence of particulate matter such as soot in the lubricant. The particulate matter can cause damage between the surfaces in contact.
3.
Pitting wear. In applications that have cyclic loading, the loading can weaken the surface of the equipment material. A crack may occur from repeated stress and cause pitting or particle separation from the surface of the equipment.
4.
Tribo-chemical wear. Additives (or chemicals entering the lubricant during use) in the lubricant chemically react with the surface of the equipment. The reaction weakens the surface allowing pieces to be more easily cracked and separated.
5.
Corrosive wear. Tribo-chemical wear could result in corrosive wear, which is the weakening of material due to the corrosive nature of the constituents in the lubricant.
Lubrication regimes
There are four basic modalities of lubrication:
•
Boundary lubrication. Characterized by a thin lubricant film where the load is carried by the asperities. In this mode, opposing surfaces meet and damage can occur unless it is prevented by the presence of protective surface films (via additives) that promote sliding (easy shearing) rather than welding of surface asperities.
•
Hydrodynamic lubrication. Characterized by complete separation of moving parts by viscous fluid film. The load is carried by the lubricant.
•
Mixed lubrication. A combination of both hydrodynamic and boundary lubrication. It is characterized by a film with intermediate thickness, and the load is carried by the lubricant and asperities.
•
Elastohydrodynamic lubrication. Characterized by a thick lubricant film where the load is carried entirely by the lubricant. It is where the interface region between the moving parts elastically deforms under the contact pressure creating larger oil film areas and greater load-carrying ability.
A common way to demonstrate the different lubrication regimes in relation to friction is known as a Stribeck curve (
see Figure 1). The coefficient of friction is indicated on the Y-axis. This is defined as the resistance that one surface has when moving over another. The amount of friction will vary depending on the lubrication regimes the equipment is operating in. The X-axis is a ratio of
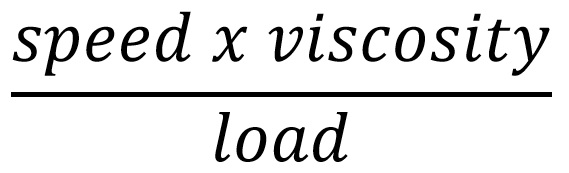
that describes the conditions under which the lubricant works.
Figure 1. The Stribeck curve. (Figure courtesy of BASF.)
For a piece of equipment just starting operation, lubrication begins at the boundary layer regime where the speed is low and the load may be higher. Upon entering the mixed regime, the coefficient of friction decreases inversely to an increase in speed. At some point the equipment will reach the elastohydrodynamic and hydrodynamic regimes and the viscosity of the lubricant takes over to prevent wear. There, in elastohydrodynamic and hydrodynamic regimes, the coefficient of friction continues to decrease to the lowest point possible. This could be considered the sweet spot or the ideal operating environment for efficient equipment lubrication. EP/AW additives and friction modifiers have higher activity in the boundary and mixed regions where viscosity has little or no effect.
EP/AW additive activity
EP/AW additives are designed to mitigate the macroscopic welding and breaking of microscopic asperities on opposing moving surfaces. Symptoms of wear can range from polishing to scoring and even harsher scuffing and seizure. Both EP and AW wear phenomena are usually present at the same time; the nature of the application determines which type of activity predominates. The distinction between EP and AW additives is not clear cut. In general, AW additives are designed to deposit surface films under normal operating conditions and thereby reduce the rate of continuous wear. EP additive films are expected to form by reacting rapidly with a surface under severe stress and prevent more extreme modes of failures. In general, EP additives are used for applications that have high loads and low speeds, and AW is for low load and high-speed conditions.
The chemical and physical nature of the EP/AW additives determines which type of protection predominates. Solid additives like graphite deposit protective films made of lamellar layers that slide easily over each other. Chemical additives, however, react with the surface to form a protective film and usually contain sulfur, phosphorous, nitrogen or chlorine. The mechanism of action for EP/AW additives are executed through polar interactions, physical adsorption, chemisorption (chemical bonding) or tribofragmentation (chemical reactions) (
see Figure 2).
Figure 2. Stearic acid chemisorption onto an iron surface. There is initial absorption of stearic acid to the metal surface through polar interactions. Then chemical reactions occur on the surface to form iron oxides. (Figure courtesy of BASF.)
Types of EP/AW additives
AW additives such as tricresyl phosphate (TCP) and zinc dialkyl dithiophosphate (ZDDP) are often used for low-load and high-speed conditions and sulfur (S) and phosphorous (P) containing additives under EP higher loads and low-speed conditions. ZDDP is used widely as an AW additive due to its performance and cost effectiveness. ZDDP also functions as a secondary antioxidant (peroxide decomposer). TCP is an ashless organic additive that was used as early as the 1930s in lubricants as an EP/AW additive. TCP currently is used in aviation applications, but its toxicity is of concern due to a neurotoxic isomer. Examples of additional S and P containing EP/AW additives are sulfurized olefins and phosphate esters, among others.
TESTING EP/AW ACTIVITY
4 Ball Test (ASTM D4172). The 4 Ball Test is a bench wear test that was developed to evaluate anti-weld properties of lubricants under conditions of high-pressure sliding velocity. The test consists of 1-1/2 inch diameter bearings arranged into a tetrahedron. The lower three bearings are held in a clamp, and the fourth bearing is made to rotate against them. Lubricant is introduced, and a load is applied to the top bearing against the lower three. After a prescribed amount of time, the test is disassembled, and the wear scars are measured.
Conestoga Vane Pump (ASTM D7043). This test measures vane pump wear. The test is run for 100 hours at a constant temperature and pressure. The weight loss of the vanes is measured after completion of the test. Values <100 mg of wear are considered good according to most standards.
FZG Failure Load Stage (ASTM D5182). This is a good place to start for gear oil testing. It is intended to measure the scuffing capacity of the oil. Scoring also happens in the FZG equipment and is included in the test criteria. Regarding the typical values measured for scuffing: greater than 10 is good. Different modifications can be made to this test.
Sequence IVA Engine Test. The Sequence IVA was developed to evaluate wear in automotive lubricants. It is a 100-hour test cycling between 50 minutes at 800 rpm and 10 minutes at 1,500 rpm with the engine held at constant torque. The cam wear is measured at seven locations using a profilometer. For (1996) GF-3, 120 micrometers was the maximum wear allowed, but now with (2004) GF-4 and (2011) GF-5, 90 micrometers is the maximum. The GF-6 pass/fail criteria is currently under development.
Friction modifier activity
Friction modifiers are designed to mitigate the increased energy consumption and poor fuel economy that result from the motion resistance of contacting bodies. A friction modifier forms a film on the metal surface that decreases friction between moving parts and reduces the energy needed to move them. A friction modifier could improve the lubricant by causing an earlier onset of the mixed lubrication regime or reducing friction over all regimes, but typical friction modifiers work mainly in the boundary regime where viscosity is ineffective.
Friction modifiers are usually long-chain molecules with polar ends that physically or chemically adsorb onto a metal surface to form a film. Chemically absorbed films form under the mild conditions of the boundary and mixed lubrication regime. Physically absorbed films form through polar attraction to the metal surface, leaving a non-polar tail solubilized in the oil. The weaker Van der Waals forces of the non-polar ends of the friction modifier cause the molecule to arrange in a parallel multilayer matrix. The non-polar ends are easily removed or sheared in a mechanism that lowers friction in the system.
Friction modifier vs. EP/AW activity
The major difference between friction modifiers and EP/AW additives are their mechanical properties. EP/AW additives and friction modifiers all operate in the boundary and mixed lubrication regimes. EP/AW additives, however, form strong films on the equipment’s asperities that are difficult to shear off or remove. This usually results in a higher coefficient of friction in a lubricant when compared to one that has friction modifier. Friction modifier films are “weaker” to allow for easy shearing off of their outer layers, hence reducing the friction coefficient.
Types of friction modifiers
There are organic and metallo-organic types of friction modifiers, and both can complement their easy-shear nature. The organic friction modifiers include long-chain carboxylic acids like stearic acid, as well as a variety of amides, polymers and partial esters.
FRICTION MODIFIER TESTING
Mini Traction Machine (MTM). The MTM is an instrument used to evaluate the frictional properties of fuels and lubricant. It consists of a bearing on rotating disk where traction coefficient is measured under a wide range of rolling and sliding conditions, temperatures and pressures.
High Frequency Reciprocating Rig (HFRR) (ASTM D6079). The HFRR is a on a stationary disk. The friction coefficient is measured under a wide range of frequencies, strokes, loads and temperatures; it also is used for wear measurements.
Additional considerations
There is much to consider when using a variety of additives in a final lubricant formulation. Some additives have synergistic behavior, meaning they produce an effect together that is greater than their individual performance combined. On the other hand, there are additives that have an antagonistic effect against other additives and compete. For example, surface active additives such as friction modifiers could work against AW additives as they are both competing for the surface. Therefore, the careful balance of the additives must be considered to achieve optimal performance of the lubricant.
Jeanna Van Rensselar heads her own communication/public relations firm, Smart PR Communications, in Naperville, Ill. You can reach her at jeanna@smartprcommunications.com.