I know I’m getting a little rusty, but…
Dr. Robert M. Gresham, Contributing Editor | TLT Lubrication Fundamentals December 2018
Corrosion sounds simple on the surface but is a highly complex topic.
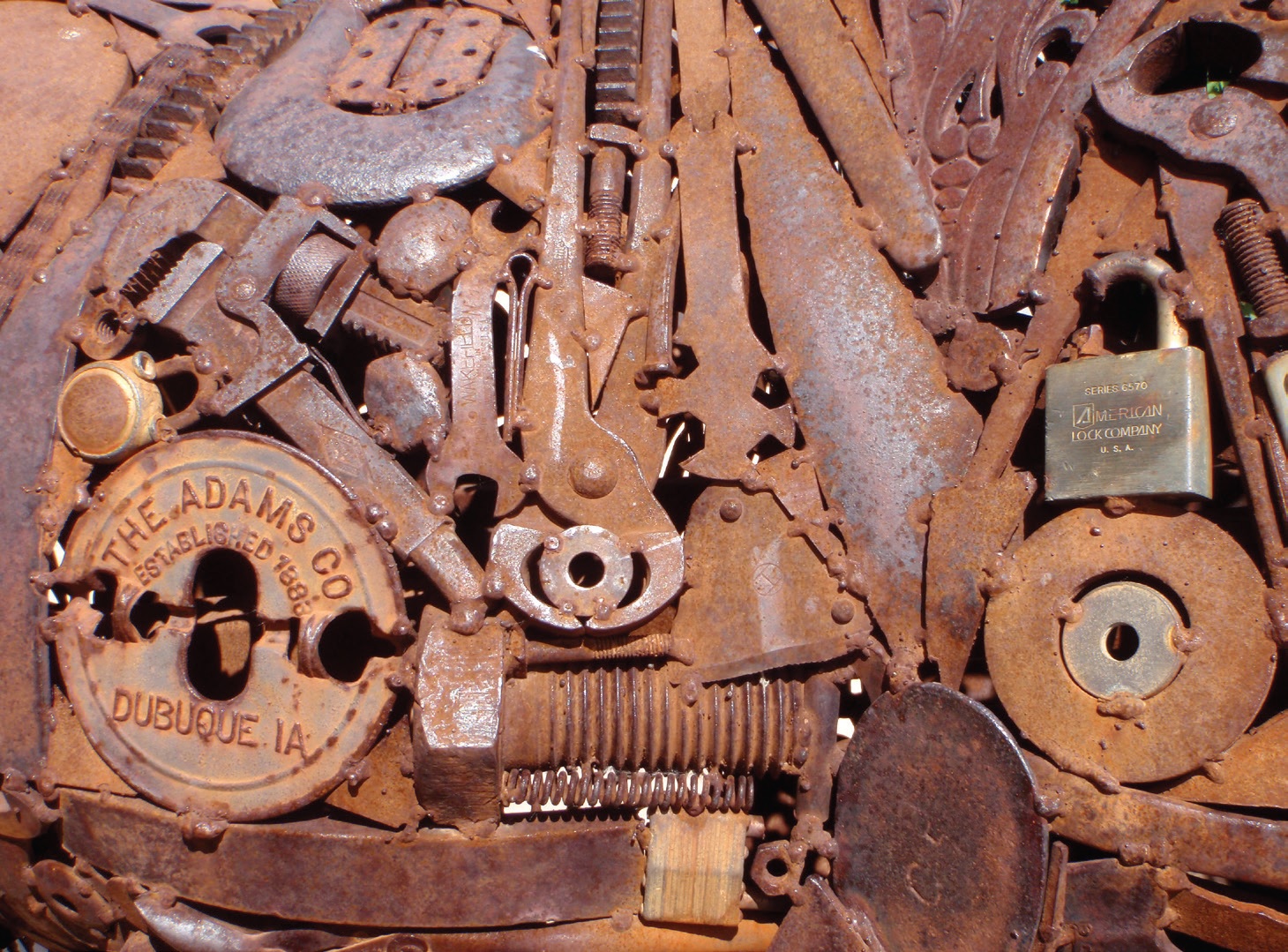
Surprisingly, early iron was inherently more corrosion resistant than later iron products.
“Rusted Metal Patterns” by Heath Alseike is licensed under CC BY 2.0. Available at www.flickr.com/photos/99624358@N00/4746391656.
Interestingly, from the time of the Iron Age the whole subject of rust and corrosion has been a troublesome topic. The early Greeks noticed that metallic things degraded in the sea faster than in fresh water. For centuries people observed corrosion but really didn’t know much about it, didn’t understand it and didn’t know how to control it. They just kind of lived with it. Also, surprisingly, early iron was inherently more corrosion resistant than later iron products. It is presumed that this early iron had less sulfur in it, perhaps as a result of being processed with charcoal as opposed to other fuels such as coal or petroleum-based fuels.
It wasn’t until the 1800s that more rigorous observations of corrosion processes were made. Real progress had to wait for early in the 20th Century when corrosion was determined to be a chemical and electrochemical phenomenon, which resulted in this observed oxidation of various metals. By the 1920s methods to prevent or reduce corrosion were developed. These methods centered around coating the metal part with various goos of petrolatum, wax, fatty acid soaps and the like. As with many of the developments in the lubrication industry, World War II accelerated the development of the technology and chemistries to help control corrosion. So let’s take a closer look.
As said above, corrosion is a chemical and electrochemical process. To make it easier, let’s think of it as primarily an electrochemical process where, in the case of iron corrosion, we see:
In an acid environment:
Anode: Fe → Fe2++ 2e-
Cathode: 2H+ + 2e- → H2
Thus: Fe + 2H+ → Fe2+ + H2
In a neutral or alkaline environment:
Anode: Fe → Fe2+ + 2e-
Cathode: O2 + 2H2O + + 2e- → 4OH-
Thus: 2Fe +O2 + 2H2O → 2Fe2+ + 4OH-
The Fe2+ (or in some cases, Fe3+) goes on to react with other species in the system usually to form the oxides (Fe2O3, common red rust, or Fe3O4, the black oxide, magnetite, which also can be magnetized). Without going into any more of the chemistry, which can be quite complex in some systems, the fundamental purpose of the corrosion inhibitor is to disrupt the anodic, cathodic or a combination of the two processes.
So how do we cause this disruption? Generally speaking, through the use of three approaches: oil coatings, soft coatings and hard coatings—each of which, in some fashion, form a barrier to protect the iron.
Oil coatings are usually temporary coatings to protect metals often between metalworking operations or during storage in a warehouse. Oil coatings may or may not contain anticorrosion additives.
Soft coatings are usually made from a variety of wax-like materials, petrolatum or even greases. These too may contain anticorrosion additives. They can, depending on the application, last for months or even years.
Hard coatings are for longest lasting protection in extreme environments. They range from inorganic coatings like zinc phosphate, zinc galvanizing (iron parts are dipped in hot molten zinc) or chromate conversion coatings (which are thin coatings applied from a bath to iron or to enhance galvanized coatings or other electroplated coatings such as cadmium coatings). Hard barrier coatings also can be the result of electroplated processes to apply a non-corrodible or slowly corrodible metal such as cadmium to the surface of the metal.
Finally, hard organic coatings can be the result of paint-like (organic resin-based) coatings, often with corrosion inhibitors in their formulations, applied by dipping, spray of through electrostatic and electroplate-like processes and are either air dried or oven cured. As you might expect, cost rises with the different types of barrier coatings, while at the same time increasing performance as well. Determining the right coating is dependent on the application, the environment and the degree of protection needed.
Getting into the chemical weeds a bit, these coatings in turn can be designed or formulated to interrupt the corrosive processes in a variety of ways:
• Anodic processes, by forming proactive oxide film (like aluminum and to a lesser extent zinc).
• Cathodic (or oxidative) processes use ions such as nitrites or chromates to passivate the iron. Chromates do so by being reduced in the system from Cr6+ to Cr3+, which in turn oxidizes the Fe2+ to Fe3+, which is less soluble in aqueous solutions forming a protective oxide film.
• Nonoxidizing anions such as silicates, carbonates, phosphates and molybdates appear to promote passivating oxide films on anodic sites of the metal surface.
• Cathodic inhibitors inhibit or retard the reduction of O2 or H+ or precipitate on the cathodic areas of the metal.
• Hydrogen inhibitors retard formation of hydrogen in acidic media by precipitating compounds of such chemicals as As (As2O3 or Na3AsO4), Sb and Bi on the cathodic areas of the metal.
• Cathodic precipitates, used in neutral or slightly alkaline solutions, act to form insoluble hydroxides (like Ca, Mg and Zn) on the surface of the metal.
• Oxygen scavengers reduce corrosion by capturing free oxygen in the system with ions such as SO3, Na2SO3 or alkylated phenols and diphenylamines.
• Nonionic inhibitors that adsorb on the surface of metals to provide a barrier to cathodic or anodic corrosion. These are often seen in oil coatings or lubricating oils.
Clearly you can see that corrosion control is one of those topics that sounds simple enough on the surface—“Just put a barrier coating on it,” as they say. But as you get into it, you find that it is indeed a highly complicated topic with complex chemistries occurring in a wide variety of environments that can lead to corrosion. Indeed, we are still learning about how to control corrosion in a wide variety of materials besides just iron. We have only touched on the surface of this subject here; there are many books on the subject.
A skilled formulator has to thwart these corrosive chemistries and environments with his own arsenal of complex chemistries whether used in oil coatings, soft coatings or hard coatings—not a simple task.
Bob Gresham is STLE’s director of professional development. You can reach him at rgresham@stle.org.