Aesthetics in lubricating greases
Debbie Sniderman, Contributing Editor | TLT Feature Article May 2018
Unraveling the mysteries behind color, odor and texture.
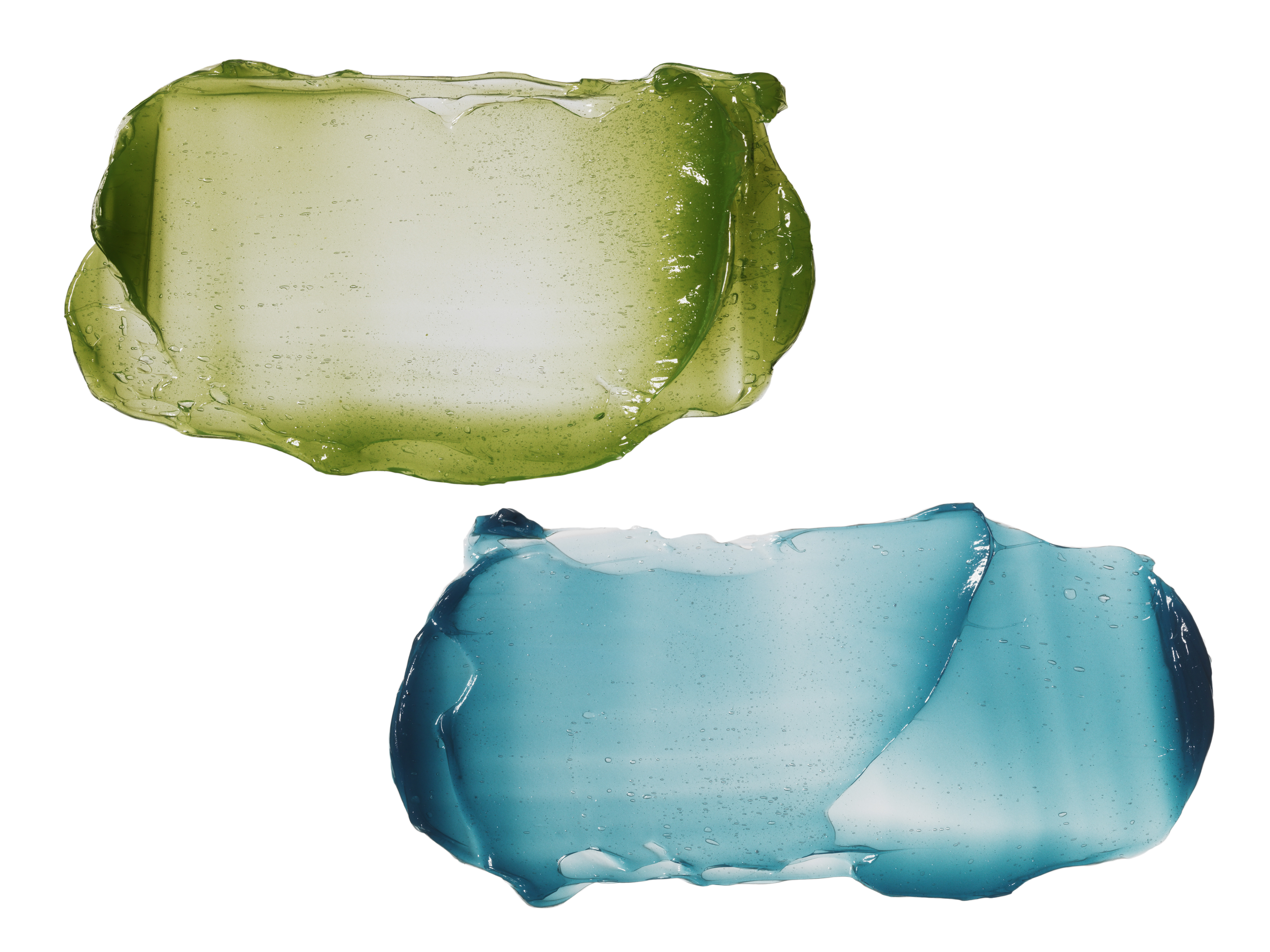
Photo courtesy of Axel Americas.
KEY CONCEPTS
•
Although dyeing is the norm, a grease’s color doesn’t indicate anything about its performance.
•
Odor from additives have become more significant over the last few decades.
•
How smooth or buttery a grease is depends primarily on the type of thickener chosen.
Although lubricating greases are produced and sold in much smaller amounts compared to lubricating oils, the majority of roller bearings are lubricated with grease. There are several kinds of lubricating greases available with notably distinct differences in colors, tackiness level and smell.
One grease manufacturer analyzed customer complaints and found the majority pertained to either color, appearance, tackiness or smell; few related to actual performance. There is a prevailing practice to use colored and tacky greases, but how much these parameters influence the performance of lubricating greases besides providing aesthetic value is a big question.
Who uses dyed greases?
In the 1980s there were almost no dyed greases on the market. Today they are the norm, and the majority of greases in North America are dyed or colored. Without a dye or a black ingredient like molybdenum, they would appear tan or brown—unexciting colors from a marketing perspective. No one wastes time dying bulk greases like those used for coating post-tension steel strands in concrete. Most grease is used in drums and pails in industrial plants where identification is important. The automotive industry also commonly uses dyed greases.
Recently more dyed greases are used in Asia as companies there are becoming more influenced by automotive and major OEM requirements. Their lists of approved globally available greases tend to be dyed.
“Using colored grease is more a reflection of an advanced manufacturing economy in that part of the world,” says STLE-member Chuck Coe, president of his consultancy Grease Technology Solutions LLC in Round Hill, Va. “Greases used in less-developed countries are less likely to be dyed. For instance, in the past lower-end commodity greases sold in South America weren’t dyed. Now more high-end greases made in the U.S. are imported there that are dyed. In those places, a dyed grease is more likely to be higher performing but not because of the dye.”
No specs
It’s easier to see and touch with the senses than to know how well grease is performing in an application. But the eye can’t always tell if it is the same.
Coe says there are almost no industry specs for grease. One published grease standard is ASTM D4950, Standard Classification and Specification for Automotive Service Greases, which contains nothing about color. Most OEMs specify a color so users don’t mix greases.
In terms of evaluating lubricating grease sensory issues, the industry is making little progress. Adhesion and tackiness are important, and people are trying to develop analysis techniques acceptable to the industry. How smooth or buttery a grease appears is primarily an artifact of the type of thickener chosen. Coe says not much is done to test or control it.
“These specs specify grease performance,” Coe notes. “If there is a benchmark standard preferred grease, alternate greases may or may not require color to match the benchmark. They may describe a grease as being tacky, smooth, buttery or have some other texture, listing a visual test method. But I haven’t seen color specified in an OEM spec having to match a standard.”
The spectrum of color for Royal Manufacturing Co.’s (now part of AXEL Group and operating as AXEL Royal LLC) greases. (Photo courtesy of AXEL Royal LLC.)
Value of aesthetics
There is value in the aesthetics of grease. But STLE-member Bill Mallory, former owner and CEO of Royal Manufacturing Co. in Tulsa, Okla. (now part of AXEL Group and operating as AXEL Royal LLC), says it’s minor when selecting grease for lubrication but major for consistency. “The first thing people see about grease is its color, then its thickness,” he says. “These are the items users will look at. Smell is not generally important. But in order to buy the same brand or type tomorrow that is used today, it should have the appearance of what was used yesterday.”
Some grease additives have a pungent odor, so some people can tell if it’s present in a grease by its smell. Many people like to feel its tackiness between their fingers. Some even taste it, but Mallory doesn’t recommend the practice: “It makes them happy but is not very analytic. Using different techniques to evaluate the grease is basically a comfort zone for the user and perhaps the seller. Most people in the field don’t evaluate grease based on aesthetics. They rely on the manufacturer to make sure it meets performance specifications. Every batch of grease is put through a series of tests.”
Color
It is generally perceived that blue grease is better in a wet environment, red grease is better in a high-temp environment, black grease is heavy duty, white is food grade and green grease has environmental friendliness, but this is a misconception. Colors may lubricate the eyes, but they don’t have anything to do with the quality of a grease in application. Dyes and polymers don’t significantly affect performance unless used excessively.
Some colors have become more popular than others, the result of successful marketing by grease producers. Examples are blue lithium complex greases, usually top-tier multi-purpose products and tacky greases with added polymers that are usually red. But the dyes are added only for cosmetic reasons and product identification. Constantin Madius, commercial product manager at Axel Americas in North Kansas City, Mo., says, “The color doesn’t add anything to the performance.”
Madius continues, “It’s important not to switch to another brand or grease from another producer just because it has the same color. That could have devastating effects on the equipment to be lubricated. A color doesn’t guarantee performance level.”
An un-dyed grease is usually amber or yellowish-brown. Few additives give grease a color. If it is not stored properly, grease oxidizes due to contaminants. Leaving a lid open exposes it to UV light or a high degree of moisture and can change the color of un-dyed grease. This may or may not affect the color when dye is added. The surface layer that contacts the contaminants and undergoes oxidation clearly is different from the grease underneath.
Manufacturers use different techniques to control the level and consistency of color in a given grease. Different batches may require different amounts of dye to maintain the same color. Some use in-house colorimetry equipment, and others use eye matching against a standard. It’s not very scientific. People measure the color from a manufacturing quality control perspective, not to predict performance in the field, which tackiness can indicate.
Coe agrees that color is mainly an identifier that helps keep different greases separate from others and the dyes don’t affect anything in terms of performance. “Subjectively, people may have preferred colors based on their experience. Some users identify grease by its color and have a bias toward its performance if it’s the right color. But dyes are used at very low concentrations and don’t physically or chemically affect the grease at all,” he says.
There are perceptions around color because some additives that do impact performance, molybdenum disulfide or graphite, cause the grease to be gray or black. But the grease is not heavy duty just because it’s black.
Difficulties testing color
Over the years, evaluating and testing grease has evolved. Penetration tests then dropping point tests were used mostly to make sure that manufacturing was correct and consistent. Then mobility testing, FTIR, four-ball EP and Karl Fischer Titration analyses started to be performed to determine if grease is made correctly and is suitable for high-temperature or extreme-pressure applications. There are many more tests available today to determine the quality and usage areas of grease.
However, according to Mallory, there are no test methods that accurately measure the color of grease. “Colorimetry is used, but color doesn’t remain consistent over time. Grease drifts away from color standards after a few weeks or months. We have to change our lab’s color standards every few months to make sure they have the same color today as years ago,” he says.
Also, many factors affect the apparent color of grease. It can appear to have different colors in different types of lighting. And the type of base oil used can make it look brighter or duller. Exposure to air when left in a room, normal oxidation or water will change its color. “Lighter greases will darken and look creamier over time. Air or air bubbles gives a grease a brighter look. Removing water or air bubbles from grease returns it back to its normal color,” says Mallory.
While color is an important part of grease presentation, it is not an indication of quality. “Even greases without added colors tend to change color, too,” says Mallory. Color indicates you’re buying a brand that you want to look the same every time it’s purchased. It helps buyers assume that all of the rest of the components in the grease are the same.
Photo courtesy of Grease Technology Solutions LLC.
Complexity using dyes
Madius says using dyes reduces flexibility in the manufacturing plant, especially when it comes to planning. When producing colored grease, plants have to ensure the color won’t contaminate the following batch produced. One way to do this is by extensively cleaning. Another way is with wash outs that create color-contaminated oil that can be re-used in the next batch of color.
“Manufacturers plan in color sequence from light to dark. Start with the red greases, then green and end up with the blue, usually the darkest color used. It’s easier to go in this order to minimize contamination in the kettles,” Madius explains.
Usually the gray and black products are kept separate from the non-moly and graphite containing products. They require separate equipment in the production line because of contamination issues. “Only a few greases have the color come from additives. The majority of colored grease are dyed to a specific color. It adds a lot of complexity,” Madius says.
Whenever manufacturers create grease with color, they have to flush equipment, tanks and piping that touch the grease so the coloring agents won’t interact with the next batch. “We clean equipment whenever changing from producing one grease to another, but we have to be more thorough when using colors. It’s harder to get out of the pumps and pipes and adds time to the manufacturing process,” says Mallory. “Most greases are amber colored and are color compatible to a point. When artificial colorants, molybdenum or graphite powders are used, cleaning becomes very important.”
Texture and tackiness
Grease can have a smooth or fibrous texture, which can affect pumpability. Long-fibered greases are more difficult to pump through central systems than a smooth, buttery grease. Pumpability also could imply adhesion properties of a grease. Coe says users prefer both types depending on their experience, preference and, sometimes, what looks nicer.
Users who want grease to work not only as a lubricant but for its sealing ability typically favor tacky grease with polymers added to improve their performance. In bearings, for example, grease can protect against both solid and liquid contaminants that come from the surrounding environment. Tackifiers increase viscosity to create a stickier material and also can enhance the ability to act as a sealant. They also can help grease stick to metal surfaces, having an adhesive quality.
Grease tackiness depends for the most part on the percentage and type of polymer in the grease. “Small amounts of polymers can be there for cosmetic purposes. But if the right types and amounts of polymer are present, it can improve water resistance and wet adhesion to metal surfaces, which affect a grease’s performance,” Coe says.
Tackier is not necessarily better, and excessive quantities may adversely affect the greases’ properties. “If it is too tacky and stringy, it will be too cohesive and the grease will stick to itself rather than stick to a surface. The force needed to rotate a bearing also would increase if the grease was too tacky, the opposite of what lubricants should do. We want them to decrease friction and energy consumption. Polymers with a high degree of tackiness are usually easy to shear, which means they quickly lose their tackiness when worked,” Madius explains.
According to Coe, tackiness is full of myths and truths. One myth is that tackier greases have better water resistance. Another myth is that tacky grease will stay put better. These could be true, and typically they are, if enough of the correct polymer was used to change a grease’s properties. But this is not true if just enough polymer was added to provide a cosmetic level of tackiness.
Subjective tests like hitting grease with a hammer to see if it stays put or a finger test pulling the grease between a finger and thumb to see how stringy it is may fool the eyes or fingers into thinking it is or feels tacky enough to have improved adhesion. “There are better and more repeatable ways to approach adhesion and cohesion testing and measuring, and the industry is developing new methods as we speak,” says Coe.
Photo courtesy of Axel Americas.
Odor
Additive packages that affect odor can indicate some qualities about grease, but the smell doesn’t predict the performance. For example, heavy-duty extreme-pressure greases typically use a gear oil additive package that tends to give a sulfurous smell. To some the sulfur smell indicates a good, heavy-duty grease. Some prefer a mild odor to help confirm that the grease was manufactured properly. If it was overheated during manufacturing or stored in tanks that overheated, it could produce an undesirable burnt smell. To others the gear oil smell is offensive, and strong odors can be a workplace issue where people are sensitive to health and safety.
“Odor from additives have become more significant over the last few decades. More manufacturers are choosing additives with the lesser odor. Grease formulators don’t necessarily have a goal to produce a grease that smells a certain way, but they typically want minimal smell,” says Coe.
White grease in double row spherical roller bearing. (Photo courtesy of Grease Technology Solutions LLC.)
The food industry
In the food-processing industry, grease and other lubricants are used as protective anti-rust films, release agents on gaskets or seals of tank closures, and as lubricants for machine parts and equipment. The NSF International is a non-profit testing, inspection and certification organization that evaluates and registers incidental food contact lubricants from the standpoint of safe toxicology. NSF reviews grease formulations (and labels) to ensure products are acceptable for use in a food facility and offers voluntary registration to grease producers.
Where there is possibility of incidental food contact, preparations must comply with FDA regulation 21 CFR, Section 178.3570. This regulation specifies which substances can and can’t be included and in what amounts. The NSF Registration Guidelines also specify odor and color limitations that manufacturers must comply with in order to register their products for use in a food-processing facility.
NSF guidelines state that products should not leave a detectable odor. In cases where a finished product or an ingredient may produce a detectable odor, NSF will conduct odor testing to verify the absence of a detectable odor when the product is applied and used according to manufacturers use instructions. The concern around odor in a lubricant is that a fragrance may mask an inspector’s ability to detect unsanitary conditions or cleaning or spoilage issues in the food processing facility.
Regulations also specify that colorants or any other components can’t have unfavorable toxicology. And, per the USDA, no red colorants can be used. This is a visual safety measure when processing meat or poultry, since red colors would not be seen or detectable if it contaminated the meat supply.
Sarah Krol, global managing director of Food Safety Product Certification at NSF in Ann Arbor, Mich., says the majority of lubricant and grease formulations submitted for NSF registration do not have intentionally added colors or dyes in their formulations. Grease formulators seeking NSF registration understand that fragrances and dyes are not desirable in a food facility from a compliance standpoint, and most formulate according to the requirements outlined in the FDA regulation.
Debbie Sniderman is an engineer and CEO of VI Ventures, LLC, an engineering consulting company. You can reach her at info@vivllc.com.