Introduction to detergents
Debbie Sniderman, Contributing Editor | TLT Webinars April 2018
An in-depth look at types, chemistries, functions and properties.
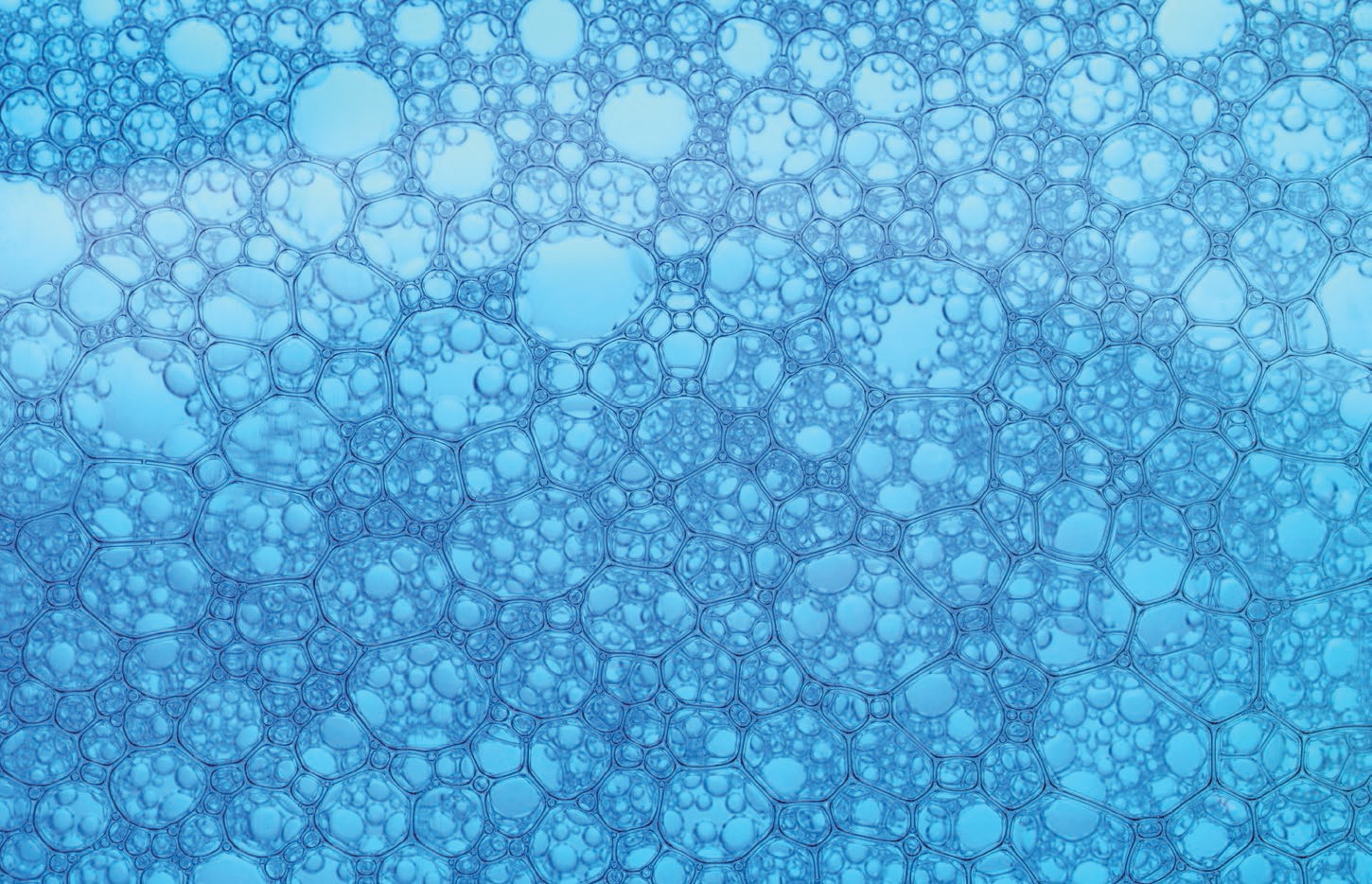
© Can Stock Photo / bach005
KEY CONCEPTS
•
Detergents and dispersants are the largest types of lubricant additives used in North America.
•
There are two main types of detergents: neutral and overbased.
•
Maintaining a detergent’s concentration in a reasonable range is essential.
MEET THE PRESENTER
This article is based on a Webinar originally presented by STLE Education on Dec. 8, 2016.
Introduction to Detergents is available at
www.stle.org: $39 to STLE members, $59 for non-members.
Dr. James Wei is senior chemist at LANXESS Canada (formerly Chemtura Canada). He has more than 20 years of experience in academia and industry in such areas as new additives (detergents) development, lubricant products, formulation and process, metalworking lubrication and materials lubrication. He obtained his bachelor’s of science degree in chemical physics from the University of Science and Technology of China and his doctorate in physical chemistry from the Chinese Academy of Sciences.
Wei performed research at the University of California-Berkeley as a post-doc and Argonne National Laboratory as a visiting scientist. He has received several academic awards, including STLE’s Al Sonntag Award for publishing excellence. Wei is a member of STLE, ACS and SAE International. He also is a reviewer of ASME Journal of Tribology. He has more than 30 papers and several U.S. patents. You can reach Wei at
james.wei@lanxess.com.
Dr. James (Jianjun) Wei
Detergents and dispersants are the largest types of lubricant additives used in North America. They are widely used in automotive engine oils at up to 10 wt%, marine engine oils at up to 30 wt% due to the use of heavy fuel oil with high sulfur content, metalworking fluids as emulsifiers in coolants or antiwear agents in straight oils, industrial lubricants, rust and corrosion inhibitors and in grease manufacturing.
Historically, additives began in the 1930s when complex engines were developed that needed better lubricants. The first detergents, calcium carboxylate, sulfonates, phosphonates and phenates, were developed in the early 1940s. Overbased sulfonates and salicylate have been used since the 1950s, and oil-soluble sodium detergents have been in use since the 1980s. Currently the common types of detergents are sulfonates, phenates and salicylates (
see Figure 1).
Figure 1. Additive use by type (North America, 2006). (Figure courtesy of LANXESS.)
Detergents are important lubricant additives. In oil they serve many functions. They neutralize inorganic or organic acids formed by oxidation or combustion byproducts such as sulfuric acid. They provide high-temperature detergency and engine cleanliness, protect against rust and corrosion, reduce friction and wear, provide dispersancy and act as oxidation stabilizers (
see Figure 2).
Figure 2. Typical detergents. (Figure courtesy of LANXESS.)
Detergent structures
Detergents are the metal salts of organic acids that act as surfactants that are active on surfaces. They are composed of three parts: soap, solid and oil. The soap portion is an organic salt that ranges from 17-70 wt%. The solids are metal carbonates, hydroxide or oxide and form the source of the detergent’s base at 0-50 wt%. The oil portion is a diluent, such as a Group I oil, at 10-60 wt%.
The hydrophilic-lipophilic balance (HLB) scale is most often used to describe the degree of a detergent’s parts to determine its solubility in water and oil. Surfactants with low HLB are lipophilic, or oil soluble, and high HLB are hydrophilic, or water soluble.
Their molecules are asymmetric in both shape and chemical compatibility, and their most common structures have polar hydrophilic heads that attach to metals and non-polar oleophilic hydrocarbon tails. Detergents can form micelles, where polar head aggregates are surrounded by tails. This structure results from the thermodynamic driving force to minimize contact with incompatible phases. In detergent systems, hydrophilic heads want to minimize contact with oil phase. There is a critical micelle concentration above which micelles form, and all additional surfactants added to the system go to micelles. Micelle structures can be used to create very small particles such as metal carbonates and form high base detergents.
Typical detergents are formed when substrates are combined with a metal. The metals can vary between Mg, Na, Ba and Ca, in which Ca is most extensively used due to its lower cost. There are three typical acid substrates all which have R groups composed of alkyl chains with C10-C36. Alkyl benzene sulfonic acids form typical sulfonate detergents. Sulfurized alkyl phenols form phenate detergents, and alkyl salicylic acids form salicylates. There also are other detergents such as carboxylates and phosphonates. New detergents continue to be developed for improved performance and to meet new regulations for environmental protection such as low ash or ashless detergents that are metal free, as well as high-performance sulficylates, which are the reaction product of salicylate and sulfonate.
Neutral and overbased
There are two main types of detergents: neutral and overbased. Neutral detergents are prepared by reacting an acid with a stoichiometric amount of base. The products have low Base Numbers (BNs). Commercial neutral detergents have BNs ranging from 5-30 due to the presence of unreacted base (e.g., hydroxide, or blending with a small amount of overbased detergent).
Neutral sulfonates provide many functions. They work when their polar heads adsorb on surfaces and remove polar particles there. In this way, they inhibit rust and corrosion by removing water and forming a water-repelling barrier film. This film can prevent surface contact and reduce friction like a friction modifier.
Overbased detergents are prepared by reacting an acid with an excess amount of base in the presence of carbon dioxide (CO
2), forming metal carbonate. They have a high BN (50-650) and are often named by their BN (e.g., 300 BN), but it is not accurate. The actual chemical definition of an overbased detergent is specified by BN, the soap content, percent sulfate ash, degree of overbasing and metal ratio.
The BN is the theoretical amount of potassium hydroxide (KOH) present in the detergent and is related to the ability to neutralize acids. Its unit is mg KOH/g sample. Detergents with higher BNs have better neutralization ability.
Soap content refers to the amount of neutral salt, which is related to the detergent’s cleaning ability. Detergents with high soap content have better cleaning ability. Sulfate ash measures the metal content. It’s obtained from residue following combustion of a detergent in the presence of sulfuric acid. The degree of overbasing (conversion) means the ratio of equivalents of the metal base to those of the acid substrate. The metal ratio refers to the total equivalents of metal per equivalent of acid.
The general formula of an overbased calcium sulfonate is (RSO
3)
aCa
b(OH)
c(CO
3)
d where a, b, c and d represent moles of the different groups. Knowing these values allows the metal ratio, BN, percent soap content and the percent of sulfated ash content to be theoretically calculated.
Detergents can be classified in many ways: metal type, carbonate type, carrier type, acid substrate type, etc. For the example of sulfonates, metal types include Ca, Mg, Ba and Na, corresponding to calcium sulfonates, magnesium sulfonate, etc. Carbonate types can be amorphous and crystal calcite sulfonate. There are sulfonates with different carrier types, for example, mineral oil based common in most cases and fuel oil based, which is only in Mg sulfonates.
Sulfonates can have natural or synthetic acid substrate types. Natural sulfonic acids are derived from byproducts of white oil manufacturing or from sulfonation of Group I base oils and create natural sulfonates. Synthetic sulfonic acids are derived from synthetic alkylates and generate synthetic sulfonates.
Of all of the sulfonates, Ca sulfonates make up about 65% in total detergent consumption and are the most important (
see Figure 3).
Figure 3. Lab sample of a pure overbased sulfonate detergent. A plant sample can be even darker. (Figure courtesy of LANXESS.)
Making detergents
Detergents are made differently depending on acid substrates. The process for sulfonates involves alkylation, sulfonation to form strong sulfonic acids and neutralization/carbonation steps to produce neutral and overbased products. For salicylates/phenates, the process involves alkylation, neutralization to form salicylate/phenate weak base salts or carbonation to form overbased products.
Overbased calcium sulfonates. Overbased sulfonates are formed by the carbonation reaction. The products are bright, clear and oil soluble. They have BN values up to 500 and Ca content between 5%-20%. Their structure has a spherical CaCO
3 core with a 1-10 nm radius surrounded by a shell containing a very small amount of unreacted Ca(OH)
2 and a 1-5 nm monolayer of surfactant.
There are several sources of acid species in used lubricating oils. Acids are formed by oxidation in high-temperature operation, during the combustion process (e.g., heavy fuel oil forms sulfuric acid), by decomposition of additives and as a consequence of corrosion. Reserve alkalinity can neutralize these acids and work together with the soap to protect surfaces.
In an overbased sulfonate, the source of base includes carbonate and a small amount of free hydroxide. The hydroxide should react first followed by the carbonate because hydroxide is a stronger base. Therefore both BN and free alkalinity are very important for the performance of sulfonates.
During carbonation, several possible CaCO
3 types may form. Amorphous carbonate is the desirable form. There are several types of crystalline carbonates such as vaterite, an undesirable fibrous structure, and aragonite, also undesirable, and calcite, a layered structure that has limited use due to its excellent lubricity. While the calcite core sulfonates can be used in rust preventives (RP oil), greases and industrial lubricants and sulfonates with amorphous structures are widely used and dominate the market.
CaCO
3 can be converted from an amorphous structure to a crystalline one. One way is by overcarbonation, which has excess CO
2 as an input. Slow filtration is observed during overcarbonation. Calcite crystalline structure contains two parallel layers consisting of CO
3 and Ca similar to those of solid lubricants (e.g., MoS
2, graphite and boric acid). Normally FTIR is used to identify the presence and type of calcium carbonate (
see Table 1). It’s easily distinguishable from amorphous with a broad peak. Also, particle size is different.
Table 1. Identification of 2 Types of Calcium Carbonates (Table courtesy of LANXESS.)
Sulfonates containing Mg, Ba and Na. Magnesium sulfonates are used as fuel additives (600 BN) and oil additives (400 BN). Their BNs can go as high as 650. Mg fuel additives are used for corrosion prevention in fuel oil burning cases. Barium sulfonates are used for rust- and corrosion-prevention applications, and low BN sulfonates are available. The use of Ba sulfonates is decreased due to its toxicity. Sodium sulfonates are used for metalworking fluids and rust preventives. Neutral sulfonates are common. It is hard to achieve high BN due to water solubility of Na carbonate.
Detergent performance. Detergent performance depends on many factors, the type of detergent soap (sulfonate, phenate or salicylate) (
see Table 2) and soap content, the molecular configuration of non-polar alkyl chains (whether linear or branched type, etc.), the molecular weight of the detergent soap, the metal ratio, BN level and metal type, etc.
Table 2. Properties of Sulfonate, Phenate and Salicylate (Table courtesy of LANXESS.)
Note: Some data cited from book: R.M. Mortier, M.F. Fox and S.T. Orszulik, Chemistry and Technology of Lubricants, 3rd Edition, Springer, 2010.
Detergency and dispersancy. All detergents have very good or excellent detergency and also some dispersancy. Detergents and dispersants are often used together in oil formulations. They are related but not the same. Detergency is the ability to keep surfaces clean, while dispersancy is the ability to keep large particles in solution.
In engines, high-temperature cleanliness is extremely important. The mechanism of detergency is due to polar metal soaps preferentially coating a surface and removing polar components from surface, preventing deposits from forming there.
Dispersancy comes about when the metal soap and/or micelle structures trap particles and hold them in suspension. Detergents’ suspending abilities are not as good as commercial dispersants (e.g., PIB-succinimide) because dispersants are metal free, non-basic and have higher molecular weight.
Panel coker tests are used to test the amount of detergency and display the appearance of the deposit. They show the amount of deposit on the surface measured in mg (
see Figure 4).
Figure 4. Panel coker test shows detergency rate of selected detergents. At conditions specified, individual sulficylate, sulfonate and blend of sulfonate and phenate show better detergency (lower mg deposited on the surface) than individual salicylate, phenate and blend of sulfonate and salicylate. (Figure courtesy of J. Wei and W. Mackwood, Presentation at 71st STLE Meeting.)
Corrosion prevention. Detergents also prevent rust and corrosion by several mechanisms. Metal soap coats the surface, preventing water from getting to it and displacing water on the surface. Carbonates and hydroxides neutralize acidic materials, which promote corrosion.
The rust prevention effectiveness of traditional sulfonate increases with ionic radius, with barium having the highest, then Ca, then Mg and Na having the lowest. Mg fuel additives prevent corrosion in exhaust gases from fuel oil burning in turbine and boiler in power generation applications. The mechanism of high BN magnesium sulfonates is as follows. MgCO
3 reacts with SO
3 and SO
2 to form MgSO
4 at room temperature. At high temperatures, MgCO
3 decomposes to MgO, which reacts with the corrosive impurities that come from fuel oil such as Vanadium pentoxide and forms noncorrosive compounds.
V
2O
5 + MgO → MgO.V
2O
5
Rust tests (ASTM D665 A/B), humidity cabinet tests (ASTM D1748) and salt fog tests (ASTM B117) are typically used to evaluate corrosion performance of detergents.
Antiwear and friction reduction. Controlling friction and wear is important for all lubricants. Overbased detergents have good antiwear functions, and some detergents (neutral and overbased) have good friction reduction. Four-ball wear testing (ASTM D4172) shows improved wear scar diameters when calcite or amorphous carbonate particles are included to base oils, with calcite having better results than amorphous carbonate. Other common friction tests also are used to determine the antiwear properties and performance of detergents (
see Figure 5).
Figure 5. Pouring detergent. (Figure courtesy of LANXESS.)
CaCO
3 particles can act as a lubricant by two mechanisms. When carbonate particles deposit on surfaces, they prevent direct contact with the surface. And during contact with high pressure and temperature, the transformation of amorphous to crystalline calcite also provides excellent lubrication (
see Figure 6).
Figure 6. Crystalline structure of CaCO3. (Figure courtesy of LANXESS.)
Oxidation stability. Oxidation stability is crucial to the quality and lifetime of lubricants. Most lubricating oils contain commercial antioxidants such as phenolic and aminic products. Detergents with phenolic functional groups such as phenates and salicylates have inherent antioxidation characteristics, and detergents without these groups, such as sulfonates, do not. This has been confirmed by Pressure Differential Scanning Calorimeter (PDSC) testing of detergents in engine oil by looking at oxidation induction time. Rotating Pressure Vessels Oxidation Testing (RPVOT, ASTM D2272) also is used to evaluate oxidation stability in detergents.
Detergents also control deposit, measured by Thermo-oxidation Engine Oil Simulation Test (TEOST, ASTM D7097), hot tube tests and engine tests. Other properties also may be important depending on application, such as the Demulsibility Test (ASTM D1401), hydrolytic stability test or others.
Selecting detergents
Detergents are widely used in lubricant formulations (
see Figure 7). They play a key role in maintaining engine cleanliness, providing corrosion protection and deposit control as well as several other performance enhancements. Depending on the specific applications, operating conditions such as temperature, speed, pressure and material type, detergent specifications, properties, performance and cost, proper detergents can be selected.
Figure 7. This motor oil is a fully formulated engine oil, which contains detergents and other additives. (Figure courtesy of LANXESS.)
There also are a few rules of thumb to keep in mind when selecting detergents. It’s important to maintain the detergent’s concentration in a reasonable range. Too much may cause excessive deposit and interfere with other additives, and too little impairs performance. Compatibility between detergents and other additives such as dispersants, antiwear and antioxidation agents also is critical to consider. Sulfonates and salicylate are incompatible and form sediment in base oil. They should not be blended. Sulfonates are often used with phenate to improve performance. They must pass the sediment test to show good compatibility prior to use. Some combinations between detergents and dispersants show synergistic effects and some show antagonistic effects by looking at the thermal oxidative stability of base stocks.
Debbie Sniderman is an engineer and CEO of VI Ventures, LLC, an engineering consulting company. You can reach her at info@vivllc.com.