Grease chemistry: Thickener structure
Jeanna Van Rensselar, Senior Feature Writer | TLT Webinars December 2017
The thickener largely determines the grease properties.
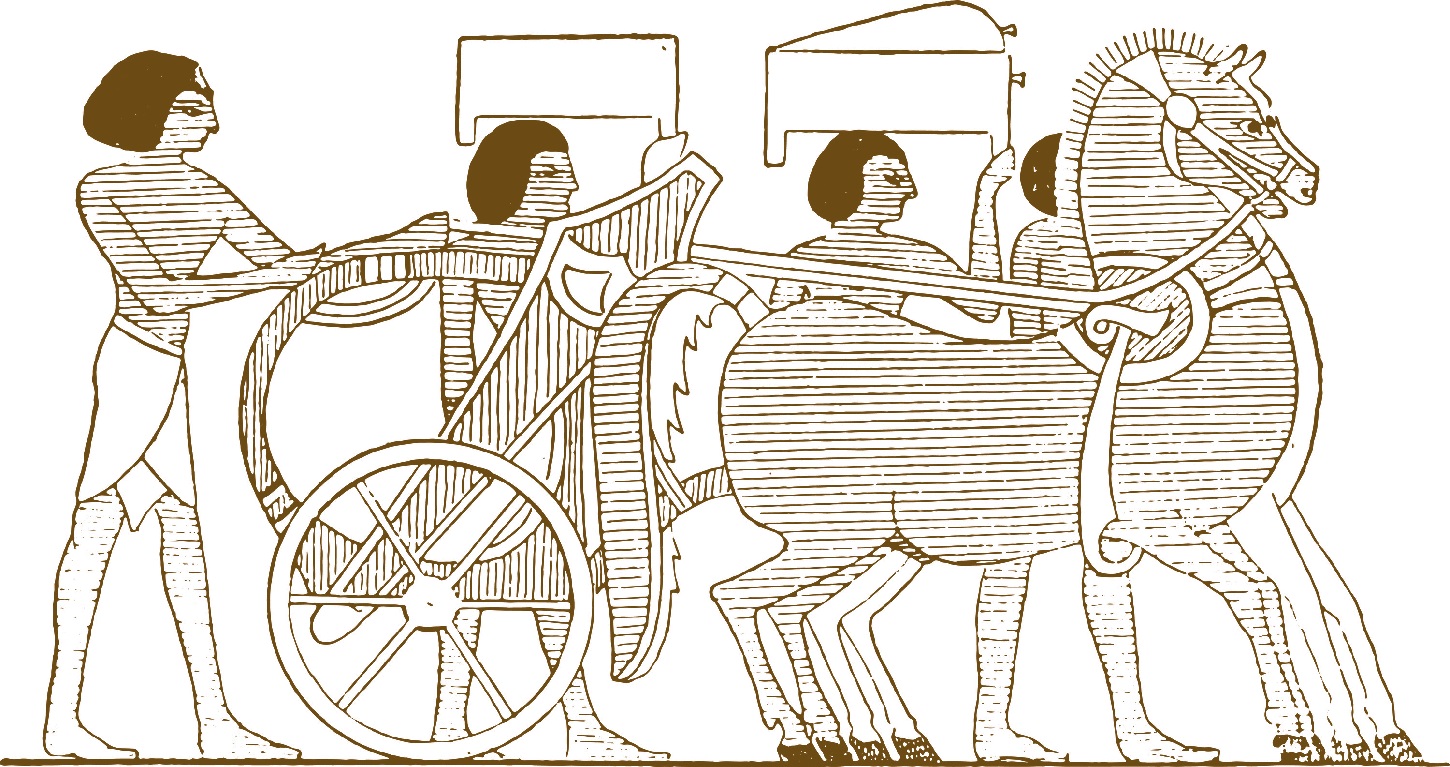

© Can Stock Photo / Morphart and © Can Stock Photo / urfingus
KEY CONCEPTS
•
Soap is the primary thickener for 90% of all greases.
•
Simple soaps have a metallic base with a single fatty acid; complex soaps have a metallic base and multiple fatty acids as complexing agents.
•
These soaps self assemble into micelles that allow a compound that is normally insoluble, such as soap, to dissolve.
MEET THE PRESENTER
This article is based on a Webinar originally presented by STLE Education on Sept. 16, 2015.
Grease Chemistry: Thickener Structure is available at
www.stle.org: $39 to STLE members, $59 for all others.
Paul Shiller received his doctorate in physical chemistry from Case Western Reserve University in Cleveland, studying the surface reactions at fuel cell electrodes. He holds a master’s of science degree in chemical engineering also from Case Western Reserve University, where he studied the characteristics of diamond-like films. Shiller holds a master’s of science degree in chemistry studying the spectro-electrochemistry of surface reactions, and he received a bachelor’s of engineering degree in chemical engineering from Youngstown State University.
Shiller joined The Timken Co. as a product development specialist for lubricants and lubrication in 2004. He then became a tribological specialist with the Tribology Fundamentals Group at the Timken Technology Center in North Canton, Ohio. In 2011 he moved to the University of Akron in an industrial innovation/collaboration effort as a research scientist. He is currently a research assistant professor at the university working in the Timken Engineered Surfaces Laboratory. You can reach Shiller at
paul.shiller@uakron.edu.
Paul Shiller
GREASE WAS FIRST USED ON CHARIOT AXLES MORE THAN 3,000 YEARS AGO. Today more than 80% of bearings are lubricated with grease. Lithium soap greases, the most prevalent, were introduced in the early 1940s. Lithium complex greases, introduced in the 1960s, are becoming the most prevalent in North America.
A soap is, by definition, a metal salt of a fatty acid. The National Lubricating Grease Institute defines grease as, “a solid to semi-solid product of dispersion of a thickening agent in a liquid lubricant. Additives imparting special properties may be included (
1).”
Grease making is a relatively simple time-temperature process: a one-pot batch method. For a soap grease, fatty acids are added; if it is non-soap, the other constituents are put into base oil. Common acids include the high-molecular-weight fatty acids, stearic acid and 12-hydroxystearic acid and short-chain complexing acids such as tallow, azelaic acid and sebacic acid. Once the acid gets up to temperature (i.e., the fatty acid melts) the metal base is added. The process is called
saponification or soap making. So basically acid + base = soap + water (
see Figure 1).
Figure 1. Greasing-making process: basically acid + base = soap + water.
Then, because there needs to be very little water in lubricants, all the water is removed. Once that is done, the material is cooled and gelled—this is the point where the mixture becomes a grease. Next the mixture is adjusted for consistency by adding base oil (additives might be added, as well). It may have to be reheated, recooled and tested several times to get the consistency that is required for the product. Most people think grease is primarily thickener, but in actuality it is mostly oil. Soap concentration in oil is typically 10%-20%.
TYPES OF THICKENERS
The thickener defines the type of grease. There are three or four different types of materials that go into thickeners. The focus in this article is on organic thickeners such as lithium stearate, sodium dodecylsulfate and diurea. There are simple greases and complex greases, depending on the types of fatty acids used.
•
Simple soaps. The main thickener used in grease is a metallic soap. These metals include lithium, aluminum, sodium and calcium.
•
Complex soaps. Greases with complex soap thickeners are becoming more popular because of higher operating temperature and superior load-carrying abilities. Complex greases are made by combining the metallic soap with a complexing agent. The most widely used complex grease is lithium based, made with a conventional lithium soap and low-molecular-weight organic acid as the complexing agent.
•
Non-soaps. Non-soap thickeners make sense in special applications such as bentonite clay for high temperatures where it does not melt (
2).
Common thickeners include:
Soaps (comprising about 90% of all greases used)
•
Lithium. Because lithium soaps are very efficient thickeners, lithium 12-hydroxystearate greases are the most prevalent. Lithium greases provide good lubricity and have great shear stability, thermal resistance and relatively low oil separation. Antioxidants are added to improve oxidative resistance (
see Figure 2).
•
Calcium. These greases have better water resistance than lithium greases. They also have good shear stability. However, they have low-dropping points, do not have good operating temperature range and can only be used in operating conditions up to 110 C (230 F).
•
Sodium. These greases offer high-operating temperature, up to 175 C (347 F) but are confined to operating conditions no higher than 120 C (248 F) because of poor oxidative stability and high oil bleed. They also are not very water resistant. However, they do provide good lubricity and shear stability.
•
Aluminum. These have excellent oxidative resistance and good water resistance. But they have a low-dropping point of only 110-115 C (230-239 F). Their usage is generally limited to operating conditions less than 80 C (176 F). When these greases overheat in bearings, they cause sharp torque increases.
Figure 2. Thickener fiber/micelle structure of two grease compounds.
Non-Soaps
•
Urea. A polyurea thickener is a reaction product of a diisocyanate with monoamines and/or diamines. This class includes diurea, tetraurea, urea-urethane and others. The ratios of the ingredients determine the characteristics of the thickener. Since polyurea thickeners do not contain metallic elements, they are ashless and, thus, more oxidatively stable.
•
Organophilic clay. These thickeners include minerals bentonite and hectorite. The minerals are purified to remove non-clay material—ground to the desired particle size—and chemically treated to make the particles more compatible with organic chemicals. Clay thickeners have no defined melting point, so they can be used in high-temperature conditions.
•
Other. Other non-soap greases include teflon, mica and silica gel.
•
Calcium sulfonate. This is not strictly a soap but is a metal salt of a sulfonic acid detergent. These greases have a high operating temperature and good water resistance.
MICELLES
Thickeners all self assemble into threadlike molecular structures, called micelles, that allow a compound that is normally insoluble to dissolve. Micelles form when soaps and detergents are added to water. The individual molecule has a strongly polar head and a non-polar hydrocarbon chain tail. When this type of molecule is added to water, the non-polar tails aggregate into the center to form a ball-like structure (micelle). This aggregation is due to Van der Waals Forces between the molecules (
see Van der Waals Forces). Because they are hydrophobic, the polar head of the molecule faces outward for interaction with the water molecules on the outside of the micelle, while the tail faces inward (
see Figure 3).
VAN DER WAALS FORCES*
Van der Waals Forces are relatively weak, short-range attractive forces that act on neutral atoms and molecules and arise because of the electric polarization induced in each of the particles by the presence of other particles. These forces include attraction and repulsion between atoms, molecules and surfaces, as well as other intermolecular forces. The forces result from a transient shift in electron density. As the electrons orbit the nucleus within an atom, the electron density may tend to shift more to one side. This generates a transient charge (i.e., an induced dipole) to which a nearby atom can either be attracted or repelled. When the inter-atomic distance of two atoms is greater than 0.6 nm, the force is so weak that it is not strong enough to be observed. When the inter-atomic distance is below 0.4 nm, the force becomes repulsive.
*Wikipedia entry: Van der Wals Force. Available at https://en.wikipedia.org/wiki/Van_der_Waals_force.
Figure 3. Micelle concept showing ionic head/non-polar tail formation. Non-polar tails aggregate into the center to form the ball-like micelle structure.
Since lubricants are non-polar environments, these micelles are reverse or inverse micelles. The non-polar tails face outward and the ionic head faces inward. So it is the micelle structures in thickeners that allow the thickener to hold onto the lubricant (
see Figure 4).
Figure 4. Reverse micelle concept. Since lubricants are non-polar environments, these micelles are reverse or inverse micelles. The non-polar tails face outward and the ionic head faces inward.
DARCY’S LAW AND OIL BLEED
In 1856 Henry Darcy first studied and published flow through porous media. Darcy’s law is an equation that describes the phenomenon. The law is based on the results of Darcy’s experiments on the flow of water through sand beds. It is a simple mathematical statement that summarizes the following properties of water flow:
•
If there is no pressure gradient over a distance, the conditions are hydrostatic (no flow occurs).
•
If there is a pressure gradient, flow occurs from high pressure to low pressure.
•
The greater the pressure gradient, the greater the rate of discharge.
•
The discharge rate of fluid will often be different—through different formation materials or the same material in a different direction—even if the same pressure gradient exists in both cases (
3).
Darcy’s law can be used to understand oil bleed—a term to describe how grease is released from the thickener for the purposes of lubrication. One of the primary criteria for selecting lubricating grease is its ability to bleed oil—which is dependent on the microstructure of the thickener.
There are a few ways to measure oil bleed. For the cone bleed test, the grease is put in a cone where it resides for 30 hours at 100 C (212 F) before measuring how much oil has dripped. The log of cone bleed is a linear function of the log of the percent soap.
GREASE AGING
The aging of grease follows closely with the aging of lubricating oils with the addition of the thickener reactions. The thickener structure contributes to the aging of the lubricants through oxidation and hydrolysis. When the thickener oxidizes, the hydroxy group can be oxidized to a ketone then ultimately to an acid group severing the chain. Thickener hydrolysis occurs when soap thickeners hydrolyze to the fatty acid and the metal base. The electrostatic effects that keep the reverse micelles stable are lost in this reaction.
REFERENCES
1.
From Maintenance Technology,
Grease Basics. Available
here.
2.
Even though the thickener may be able to withstand high temperatures, the base oil will oxidize quickly at elevated temperatures.
3.
From Wikipedia entry:
Darcy’s Law. Available at
https://en.wikipedia.org/wiki/Darcy%27s_law.
Jeanna Van Rensselar heads her own communication/public relations firm, Smart PR Communications, in Naperville, Ill. You can reach her at jeanna@smartprcommunications.com.