Silicone and dry-film lubricants
Jeanna Van Rensselar, Senior Feature Writer | TLT Webinars September 2017
A Dow Corning engineer discusses the unique features of today’s fluids.
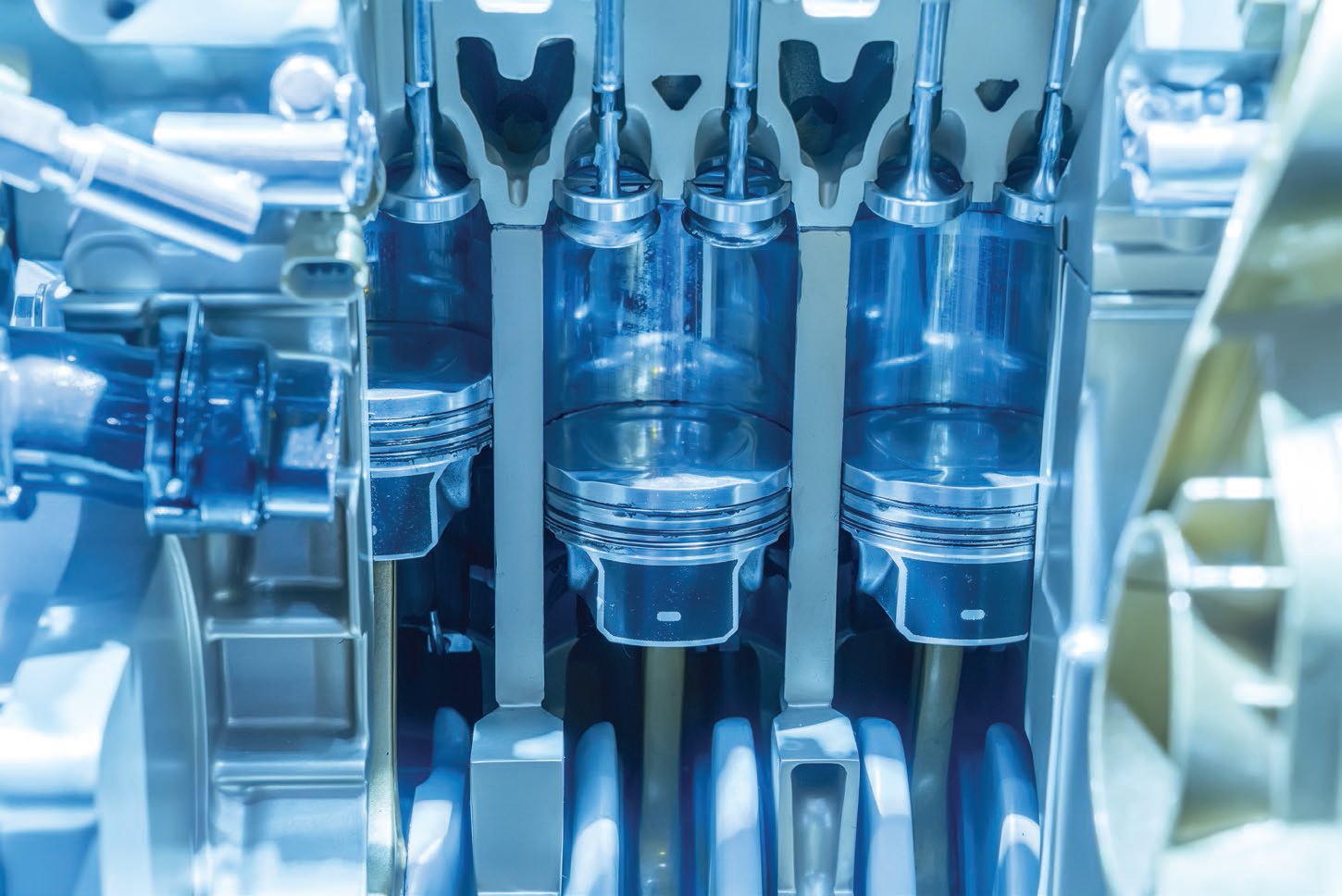
© Can Stock Photo / dashark
KEY CONCEPTS
•
A new copolymer silicone fluid has improved lubricity and increased additive acceptance vs. traditional silicone lubricants.
•
Dry-film lubricants are polymeric resin-based coatings that excel in performance in the boundary lubrication regime.
•
Market drivers in automotive applications include friction reduction, long-term engine life, fuel economy and reduction in emissions.
MEET THE PRESENTER
This article is based on a Webinar originally presented by STLE Education on Nov. 2, 2016. “Silicone and Dry-Film Lubricants” is available at
www.stle.org: $39 to STLE members, $59 for all others.
Gary Weber is an application engineer with the
Molykote® brand Specialty Lubricants Division of Dow Corning Corp. He has worked for Dow Corning for 10 years in research and development, manufacturing and reliability engineering. His primary focus technology is dry-film lubricants and anti-friction coatings for automotive applications. He holds a bachelor’s degree in mechanical engineering from Saginaw Valley State University. You can reach Gary at
gary.weber@dowcorning.com.
Gary Weber
UNLIKE MINERAL OIL-BASED LUBRICANTS, synthetic lubricants do not occur naturally and must be manufactured. Synthetic lubricants include synthetic hydrocarbons (PAOs), organic esters, polyglycols, phosphate esters and silicones.
The silicone structure is composed of an Si-O base with a bond energy of about 460 kJ/mol and a bond angle of about 143 degrees. This is compared to a carbon base, which has a bond energy of about 348 kJ/mol and a bond angle of about 110 degrees. The energy required to break an Si-O bond is greater than the energy required to break a C-C bond.
Si-O has a low glass transition temperature (148 K), permanent shear stability with very low monomeric friction and high oxidative stability (PDMS [573 K] to PPMS [649 K]). Silicone also has good chemical and thermal stability.
Silicone lubricants, which are good for extreme-temperature lubrication, have a wide viscosity range and a very high viscosity index (VI) compared to organic fluid lubricants. They also are highly compressible, which is especially beneficial in applications that involve absorbing shock loads such as motion-dampening fluids, dashpots and hydraulic arrestors.
FLUIDS AND APPLICATIONS
Dow Corning has six lubricating families ranging from greases, compounds and anti-friction coatings (or dry-film lubricants) to pastes, dispersions and oils. For silicone grease and compound production, there are three basic siloxane lubricant fluids:
•
Dimethyl silicone (the basic silicone structure) used in fluids and compounds with 0.65 cSt to 60,000 cSt viscosity and high VI.
•
Phenyl-methyl silicone used for both fluids and greases with 50 cSt to 30,000 cSt viscosity.
•
Fluorosilicone has great chemical inertness and, thus, is used for specialty fluids and greases with 300 cSt to 10,000 cSt viscosity. It also has improved polarity over the other silicone fluids, which allows for good lubricity.
An understanding of how viscosity relates to other variables in a given application is essential. Considerations include:
•
Viscosity/temperature relationship
•
Viscosity/pressure relationship
•
Viscosity/shear relationship
•
Newtonian and non-Newtonian flow behavior and dilatant behavior
•
Viscosity/time relationship
•
Thixotropic behavior and rheopexy behavior
•
Measurement of viscosity and flow behavior.
Figure 1 shows how the viscosity of a common mineral oil compares to the viscosity of silicone fluids as temperatures change. This is the basic definition of VI. A common VI for a mineral oil is 95 to 100, whereas the VI for basic dimethyl silicone fluids can be above 300 and even close to 400.
Figure 1. Viscosity index properties: dimethyl silicone fluids.
COMPARISON TO OTHER BASE FLUIDS
Looking at the base oil comparison table (
see Table 1), silicones have historically not been compatible with most additives because most of them on the market are designed for mineral oil-based fluids. Given the bond energy and bond angle differentials between silicone and mineral oils, silicones have:
•
Enhanced flexibility
•
A lower glass transition temperature
•
A high thermal stability.
Table 1. Base oil comparisons
NEXT-GENERATION SILICONE FLUIDS
Today’s silicones have very unique properties. Generally, strengths include:
•
Oxidation stability
•
Thermal stability
•
Viscosity index
•
Chemical resistance
•
Elastomer/polymer lubricity
•
Low temperature.
Limitations include:
•
Lubricity—metal-to-metal
•
Compatibility with other oils
•
Additive acceptance
•
Film formation.
o
Dimethyl silicone lubricants are excellent elastomer lubricants—seals, O-rings, water applications, etc.
o
Phenyl silicone lubricants have excellent viscosity/temperature performance and thermal and oxidative stability.
o
Fluorosilicone lubricants have excellent chemical resistance.
Dow Corning recently combined the high-temperature capability of fluouro silicone with the lubricity of phenyl silicone (
see Figure 2). The result is a new line of high-performance silicone fluids that can be used in various lubricants—including
Molykote® G-9000 grease, which has the following characteristics:
•
A temperature range of -35-220 C (-31-428 F)
•
Low surface tension
•
Excellent oil and additive compatibility
•
Excellent thermal stability.
Figure 2. Lubricating fluids and greases: mixed, hydrodynamic and elastohydrodynamic regimes.
Working with Northwestern University, Dow Corning developed a computer model to understand the structural property behavior of various silicone molecules to design next-generation silicone lubricating fluids for optimized viscosity-rheology and lubricity to maximize tribological behavior. Starting at the molecule level, the model takes a systematic approach to determine the rheology and then translates the rheological behavior to tribological properties via the following:
•
Molecule→Rheology
o
Molecular structure
o
Molecular mass distribution
o
Volume structure
o
Volume pressure temperature
o
Viscosity structure
o
Viscosity pressure temperature
o
Pressure viscosity index.
•
Rheology→Tribology
o
Film thickness
o
Stress-strain relation
o
Asperity friction
o
Film friction
o
Wear.
Using this model, Dow Corning can engineer a silicone molecule with specific tribological properties before having to create the silicone molecule in the lab.
DRY-FILM LUBRICANTS
Tribology is comprised of three different lubrication regimes: boundary lubrication, mixed lubrication and hydrodynamic lubrication. Dry-film lubricants perform primarily in the boundary lubrication regime, which correlates to lambda ratios of 1 or less (
1).
Dry-film anti-friction coatings (AFCs) have multiple uses. Uses in transportation applications include body components, chassis and brakes, powertrain components and interiors. In automotive applications, AFCs have the following advantages:
•
Reduced friction and wear
•
NVH, corrosion and stick-slip prevention
•
Several application methods
•
Lower temperature performance
•
Long-term lubrication—they should survive the lifetime of the part.
How is an AFC different from paint? A paint is made up of a binder (main ingredient) and a small amount of pigment. In an AFC, the bulk of the material is the solid lubricant, not the binder.
TYPICAL COMPOSITION AND FORMULATIONS
Anti-friction coatings are composed of four main ingredient types:
•
Organic solvent—the carrier of the solid lubricant and binder
•
Solid lubricant and pigment—provide lubricity (low-friction coefficient, antiwear) and influence color
•
Binder—adheres the solid lubricant to the substrate
•
Additives—used for wetting, dispersing, anti-settling, etc.
Solvent. Considerations for solvent selection include:
•
Surface tension
o
Wettability → adhesion (ability to coat and ultimately adhere)
o
Bubbling/foaming
•
Solubility to resin
•
Boiling point/vapor pressure
•
Minimizing premature cross linking
•
Environmental health and safety.
EHS challenges with PAI-based AFCs. PAI resin has excellent chemical resistance, but it is a challenge to find suitable solvents for its dilution (coating manufacture, application process). The most efficient family is dipolar aprotic solvents (diols-derivatives like NMP, NEP, GBL and others).
•
NMP (CAS #872-50-4) was traditionally the most used, most widely available and cheapest. In recent years, it was flagged as a potential toxic reproduction hazard.
•
NEP, GBL and other solvents have begun to be utilized as replacements for NMP.
•
Regulations continue to change, and therefore solvent selection continues to change along with it. The
Molykote® brand has taken a proactive stance and formulated all NMP out of new AFC products over the past couple of years.
Solid lubricant. There are three primary solid lubricants: PTFE (Teflon®), graphite and MoS2. All three provide a low coefficient of friction under different conditions, including load, environment, temperature and speed of a given application.
Resin/binder. This is the heart of the AFC (
see Table 2). Resin types include fluoropolymer, polyamideimide, epoxy, phenolic, polyurethane and silicone. Selection considerations include:
•
Solvent compatibility
•
Solubility: sedimentation during filtering
•
Dispersability/wettability to solids and substrate
•
Evaporation speed of solvent influence on cured film.
Table 2. Resin/binder performance
The resin selection is influenced by application requirements such as durability, flexibility, adhesion, hardness or brittleness, corrosion protection and lubricity.
PRETREATMENT AND APPLICATION METHODS
Pretreatment is the key to reaching the lifetime effectiveness of the coating. Effective methods include degreasing, sandblasting, phosphating, anodizing, acid etching and alkaline detergent washing. Corrosion resistance can be increased by the use of phosphating and, to some extent, electrophoretic coating (e-coat) as well. Optimal pretreatment methods for various materials include:
•
Steel phosphating (zinc or manganese)
•
Aluminum anodizing, phosphating, alkaline detergent wash
•
Galvanized parts phosphating (zinc or manganese)
•
Die-cast zinc phosphating (zinc or manganese)
•
Stainless—cannot be phosphated (possible acid treatments).
The choice of application method depends on the viscosity of the coating and the intended use. Spray is the most popular, with other options being brush, roll coating, dip spinning (centrifuging) and screen printing (an ink).
The total cost of an AFC application includes material cost, surface preparation cost and application process cost, with the application method having a strong influence on the total cost of the solution. The actual coating material accounts for less than half of the total cost.
Once the film is applied, the final step is curing. This depends on resin chemistry but can be ambient, heat or UV cure.
PERFORMANCE AND TESTING
Performance requirements include:
•
Film hardness—measured by pencil hardness test (6B through 6H) (
2)
•
Temperature—performance range is generally between -200-450 C (-328-842 F), with resin type being the typical limiting factor
•
Adhesion to substrates—can vary greatly, but surface prep is key
•
Flexibility of cured film (mandrel bend test)—varies with resin type
•
Compatibility with additives and fluids
•
Low and/or consistent coefficient of friction over the temperature range.
Common AFC test methods include:
•
Linear oscillating: SRV, Cameron Plint, UMT, etc.
•
Pin on disk/ball on disk
•
Adhesion test methods—lap shear, cross hatch
•
Salt fog corrosion testing
•
Ring on block
•
Ring on plate
•
Taber abrasion.
ADDITIONAL COATING TECHNOLOGIES
Market drivers in automotive applications include friction reduction, long-term engine life, fuel economy and reduction in emissions. Applications include piston pins, con rods, camshafts, bearings, valves, bushings, tappets, valve guides and gears.
There are a number of high-wear-resistant physical or chemical vapor deposition coatings currently on the market—such as TiN, CrN, TiAlN and DLC ceramic films—that provide high hardness but cannot match the low-friction performance of AFCs. Each category has its own strengths and weaknesses.
AFCS
•
Low friction
•
Polymer based—upper temperature limits
•
Easy to apply (in solvent)
•
Good flexibility
•
Good adhesion
•
Low hardness such that higher wear resistance may be desired in some applications
•
Relatively low-working temperature
•
Environmental issues.
DEPOSITION COATINGS
•
Low or high friction
•
Ceramic, metallic or inorganic
•
Vapor deposition (expensive)
•
Usually brittle
•
Difficult to achieve good adhesion
•
Very high hardness with wear resistance
•
Relatively high-working temperature
•
Environmental issues.
Dow and Dow Corning have long been leaders in the field of coating technologies—silicones, dry film and others. A comprehensive research program and a dedication to constant improvement ensure continued industry leadership for the foreseeable future.
REFERENCES
1.
Lambda ratio: ratio of fluid film thickness to composite surface roughness.
2.
The value is the hardest pencil that does not scratch or mark the coating surface.
Jeanna Van Rensselar heads her own communication/public relations firm, Smart PR Communications, in Naperville, Ill. You can reach her at jeanna@smartprcommunications.com.