Special Report: Marine diesel cylinder engine oils: Lubrication challenges impacted by operating conditions and regulations
Dr. Neil Canter, Contributing Editor | TLT Tech Beat September 2017
With a .05% sulfur fuel cap coming in 2020, lube suppliers are helping ship owners reduce costs and remain compliant.
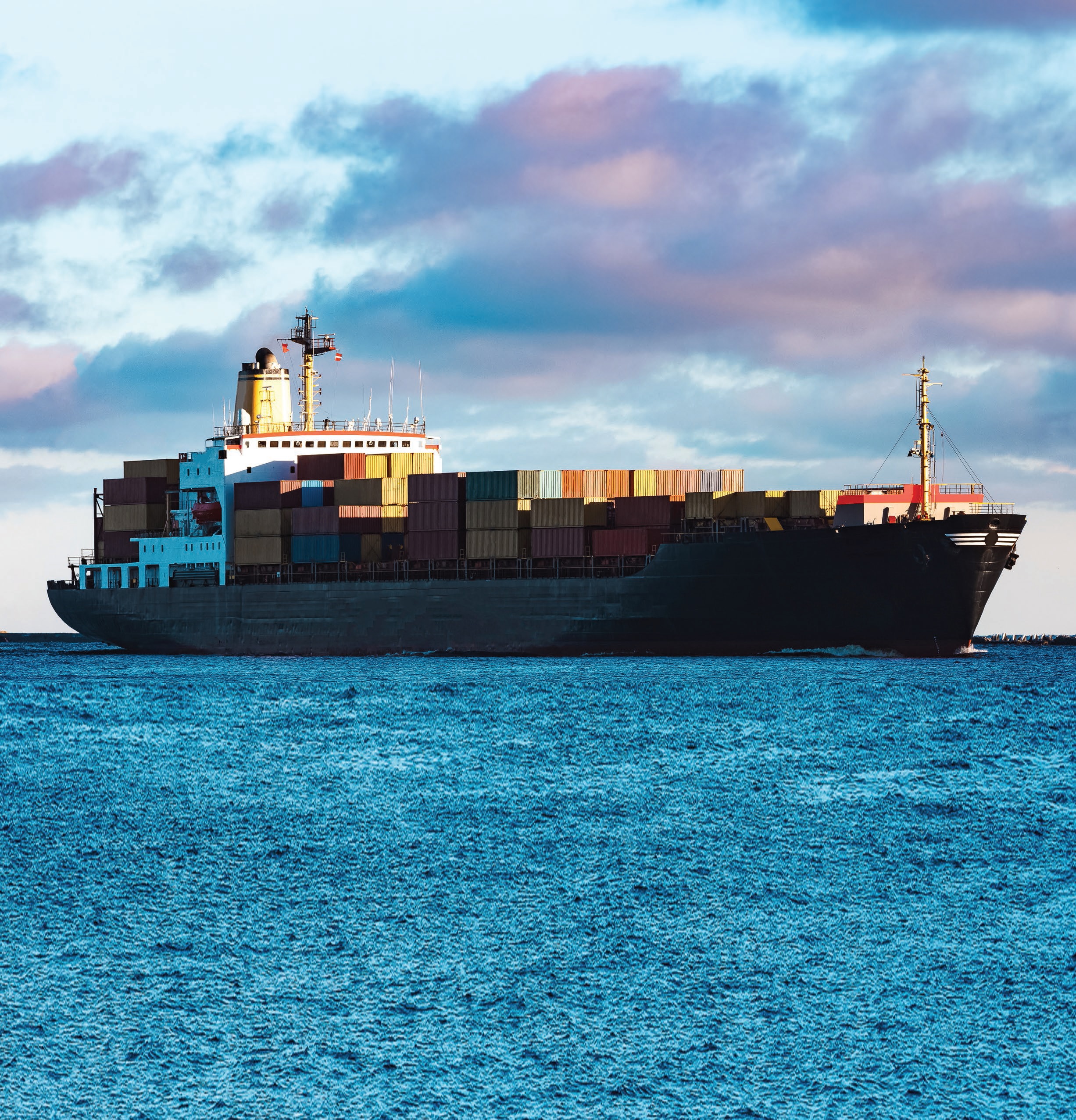
© Can Stock Photo / sengnsp
KEY CONCEPTS
•
Marine diesel cylinder lubricants provide a hydrocarbon film between rings and liners of engines in large container ships that transport cargo globally.
•
The level of sulfur allowed in marine fuels has differed in specific geographical locations globally, leading to the development of different lubricant options. This issue may be resolved when the IMO implements a 0.5% sulfur fuel cap in marine fuels in 2020.
•
With the challenges of operating shipping fleets, operators have turned to slow steaming that has reduced fuel costs but led to the development of cold corrosion due to the lower steaming temperatures. The most important strategy to minimize cold corrosion is to monitor engine wear.
THE MARINE ENGINE OIL SEGMENT would appear at first glance not to be a transportation lubricant category where much change is occurring or where lubricant suppliers are challenged. After all, there has been a good deal of attention paid to the newest automotive engine oil specifications developed and under development in the EU and in North America (
1).
In contrast to lubricants affected by the 2013 U.S. Vessel General Permit Regulation (VGP), (
2) marine engine oils are not impacted because they do not interface with the sea.
The engine oils used in slow speed, two-stroke diesel engines are known as marine diesel cylinder lubricants (MDCLs). This once-through lubricant allows the functioning of these large ocean-going vessels to transport cargo globally. Marie-Claire Soobramanien, global product manager marine diesel engine oils for The Lubrizol Corp. based in Hazelwood, UK, summarizes the roles of MDCLs by saying,
“MDCLs provide a hydrocarbon film between rings and liners. They are typically monograde, SAE 50 high-viscosity lubricants that exhibit good dispersancy, provide a gas seal between rings and liners, control corrosive wear, display good detergency by ensuring high temperature cleanliness at the top of the cylinder, up to 300 C and avoid adhesive and abrasive wear. An MDCL demonstrates good deposit control in pistons, in the ring zone and in the undercrowns. It must have good thermal and oxidative stability and spreadability over a large surface area.”
But strong competition and the onset of regulations impacting the composition of the diesel fuel used in these two-stroke engines is having an effect on how MDCLs are formulated. The purpose of this article is to discuss the key operating and regulatory issues facing additive suppliers and finished lubricant manufacturers.
Input on MDCLs was obtained from representatives at the following companies: Chevron Marine Lubricants, Chevron Oronite, Cockett Marine Oil, ExxonMobil Marine Lubricants and The Lubrizol Corp.
OPERATING AND REGULATORY FACTORS
Ian Thurloway, global brand & market manager for Chevron Marine Lubricants based in London, believes that the overcapacity present in sea trade is forcing operators of large-container ship fleets to focus on running costs. He says, “With the continuing long-term down cycle in the global economy, ship operators are reducing fuel costs by moving to 2-stroke engine slow steaming. The problem is this approach may lead potentially to increasing maintenance costs because of cold corrosion if cylinder feed rates are not optimized or the wrong cylinder lubricant is used.”
Regulations also are a major factor facing ship operators. Thurloway continues, “With a raft of legislation including increased Emission Control Areas (ECAs) and a cap on sulfur content in marine fuels to be implemented by The International Maritime Organization (IMO) on the horizon, ship operators and lubricants suppliers must now think hard about solutions.”
Dick Wolpert, product line specialist for Chevron Oronite in Richmond, Calif., provides further details on the problems faced by ship operators. He says, “The current shipping business environment is creating pressure on ship operators to economize and aggressively reduce operating expenses. World trade continues to be flat with slow growth prospects. The shipping industry has seen examples of business failures of shipping companies and bulk carriers. There have been consolidations, merger activities and shipping alliances formed. The business outlook drives toward a strong cost focus to implement fuel and lubricant savings initiatives.”
Wolpert continues, “Besides a trend toward slower and reduced load operation to save fuel consumption, newer engine designs are concentrating on further enhancing fuel efficiency, which can affect combustion conditions and the performance requirements of additives and engine lubricants.”
ECAs have now been established in selected Asian river basins, Europe’s North Sea and in North American coastal waters to restrict the use of heavy fuel oil (HFO). Wolpert feels that the next very significant regulatory factor looming on the horizon is the year 2020 implementation of a 0.5% sulfur cap for marine fuels globally. He says, “This represents a dramatic shift from the current 3.5% average sulfur levels outside of the existing ECAs.”
In Wolpert’s assessment of the impact of the pending IMO sulfur cap, he says, “The shipping industry is presented with a diverse set of alternatives and potential directions, ranging from installation of on-board emissions control equipment to allow the continuing use of existing HFO or switching to alternative fuels that satisfy the 0.5% sulfur threshold. It is not clear which fuel alternatives will be available in sufficient quantity or at acceptable economics. Alternative marine fuel types could emerge, which might be a mix of low-sulfur fuels (0.5% sulfur), or distillate fuels, or adoption of liquid natural gas as a marine fuel. Each of these would have distinct lubricant and additive performance requirements, creating the need to identify and develop alternative additive formulations.”
Caroline Huot, global head-lubricants, Cockett Marine Oil (Asia) Pte. Ltd. in Singapore, emphasizes that changes in engine design and new ship operating conditions led to changes in the lubricants used. “Traditionally, the shipping industry had burned heavy-sulfur-containing fuels,” she says. “This led to corrosion problems that were tackled a long time ago with high alkalinity-containing lubricants (SAE 50) exhibiting BN (base number) 70. New types of engine designs (long strokes and super long strokes) and new operating conditions (working at partial load, slow steaming) generated the need for higher BN-100 cylinder oils to counter the cold corrosion phenomenon that appeared quickly in 2010 on newly built ships. While addressing ship owners’ economic concerns and the desire for more eco-friendly operations, the result has been an increase in cost and complexity of operations that has not been fully resolved to the satisfaction of ship operators. We now see BN-140 cylinder oils appearing on the market, but this still leaves unresolved how the industry can deal with both cold corrosion damages and the need for lower-BN formulations required with the lower sulfur regulation to be initiated in 2020 by the IMO.”
Huot points out that it is uncertain whether the marine lubricant industry will be ready with products to meet the 2020 deadline. She says, “In moving to new, lower-sulfur-containing fuels, the challenge is more on the side of lubricity and detergency (piston and liner cleanliness, avoiding any undesired mineral deposit build up) while the question of viscosity to be chosen remains for the moment on the higher side. Field experience is far from extensive enough to draw effective lessons from experiences as the number of vessels using lower-sulfur-containing fuels is still minor. The lubricant industry is still trying to work out the best options for meeting the IMO requirements in 2020, and there is every expectation that the delay will last from three to five years due to the long development cycle.”
Soobramanien says, “For a number of years, the shipping market has been under a financial crisis. Overcapacity in the shipping industry, combined with a drop in freight rates, is leading to higher operating costs with fuel representing approximately 60% of the total. To compensate for the higher cost, large vessels are now running under slow steaming, which can lower engine speeds by 20%-25% and may reduce fuel consumption by 50%.”
To address the more stringent IMO emission regulations, OEMs have developed more efficient engines with longer strokes and higher operating pressures.
Iain White, global marketing manager for ExxonMobil Marine Fuels and Lubricants, indicates that many of the factors affecting the marine lubricant suppliers are regulatory driven. He says, “There are a lot of changes due to the reduction of sulfur content of fuels and implementation of ECA areas.”
LOW-SULFUR-CONTAINING FUELS
With the movement to lower-sulfur-containing fuels that will be accelerated as 2020 gets closer, lubricant suppliers face uncertainty about fuel quality. Soobramanien says, “There is a lot of speculation about the type of 0.5%-sulfur-containing fuels that may exist to satisfy the IMO regulation. Various fuel options are possible such as (1.) blends of residuals, (2.) hydrotreated residuals, (3.) heavy fractions from hydrocarbons and lighter hydrotreated fractions and (4.) desulfurized HFOs. These combinations may lead to a wide range of viscosities and lubrication issues.”
Adding to the problem is that ECAs are requiring ships to use fuels containing no more than 0.1% sulfur. Soobramanien says, “The two key marine engine OEMs are recommending that MDCLs contain much lower BNs. MAN Diesel & Turbo recommends 15-40 BNs to deliver deposit and wear control with deposits at the back of the rings possibly being an issue. Winterthur Gas & Diesel recommends BNs between 15 and 25.”
Soobramanien continues, “Reduction in sulfur may lead to a number of issues in the field, including lacquer formation, wear and deposit control. The lubricant industry is speculating that additives may be needed to enhance thermal oxidative stability to prevent lacquer and deposit problems and improved thin film strength to prevent scuffing.”
Further amplifying the uncertainty is that Soobramanien notes the marine engine OEMs have not yet confirmed the lubrication needs for their engines when 0.5% sulfur fuel is mandated in 2020.
Huot indicates that low-sulfur-containing fuels will necessitate lubricant formulation changes. She says, “Lubricant suppliers will need to focus more on dispersancy and detergency properties. The process for meeting the 0.5% sulfur cap will mainly require the use of fuel blends raising significant quality issues while decreasing feed rates. Issues formulators will need to tackle include making sure the carry away residue from combustion is minimized through proper use of detergents and lubrication films need to be resilient.”
Wolpert believes that the chemical constituents of the lubricant additives will not change in moving from a high-sulfur-containing HFO to a low-sulfur fuel. He says, “The concentration of the additives used in the MDCLs will need to be adjusted. For a low-sulfur HFO, a traditional 70-BN lubricant is not suitable because it is important that the fuel sulfur level and lubricant are matched. If too little base is available, then the acids of combustion will not be neutralized and will attack the piston liners, leading to corrosive wear. If too much base (in the form of calcium carbonate) is present, this inorganic substance does not burn and could form hard deposits leading to the potential for abrasive wear.”
Wolpert advises that OEM guidelines for lubricants are 40 BN for fuel sulfur levels below 1%, 70-80 BN for sulfur levels between 1%-2% and 70-100 BN for fuels above 2% sulfur. He says, “In formulating 40-BN lubricants, the traditional 70-BN additive formulations are not suitable to use in a simple down-treat. The lubricant does need to supply BN for acid neutralization, but it has a second function to deliver detergency to prevent the formation of piston deposits. 40-BN formulations typically need to have specific additives that deliver sufficient cleanliness performance at the lower BN level.”
White feels that the reduction in the sulfur level of fuel may require not just reducing the BN but also rebalancing the formulation to achieve optimum performance. He says, “It is not just a case of lowering the detergent treat rate but also making other changes to the MDCL formulation.”
Thurloway believes that with the emphasis on reducing SOx emissions, low-sulfur-distillated or compliant fuels will need to be used. Lubricants and additive technologies are already available that are compatible with these fuels.
He says, “There will still be a need for lubricants that can handle high-sulfur-containing fuels. The result is that lubricant suppliers will need to offer MDCLs with BNs ranging from 25 to 140 BN. We firmly believe that one size does not fit all, and careful consideration must be made to eradicate knock-on issues with excessive wear and deposits.”
MULTIPLE FUELS
The current need for ship owners to meet lower sulfur-emission regulations in ECAs, yet wish to continue to use higher sulfur-containing fuels outside of ECAs until 2020, leads to the prospect that multiple fuels will be used and, as a consequence, multiple MDCLs may be required. Thurloway says, “Most ships are able to store more than one lubricant, so we advocate using the correct base number lubricant for the fuel being burnt. Trips into ECA areas in many cases require a lower BN lubricant for a period of time to minimize the chance of experiencing damage to the engine.”
White agrees that ships need to carry more than one MDCL today, but this will change. He feels that once the IMO regulation is implemented in 2020, the rule change will make it simpler for ship owners. White says, “Only low-BN lubricant will be needed past 2020 to work with 0.1% and 0.5% sulfur-continuing fuel. Ship owners also have the option of installing a scrubber to deal with high-sulfur-containing fuel, which will mean the use of high-BN lubricants.”
White indicates that a tradeoff exists in having new ships use low-sulfur fuel or install a scrubber. He says, “Fuel choice will be compliant fuel versus high-sulfur fuel oil (HSFO) with the economics becoming clearer once the difference in cost between the two fuels is known in 2020. The scrubber payback period currently looks like it will be between three to five years, whereas post 2020, the economic return on investment for using a scrubber will be better.”
Soobramanien reveals that marine engine OEMs offer guidelines on MDCL feed rates for various BNs to address various sulfur levels in fuels. She says, “MAN Diesel & Turbo goes further by offering an automated cylinder oil mixing system that uses combinations of high (>100 BN) and low-BN MDCLs to help the ship handle a range of sulfur-containing fuels. Other options include blending lubricants onboard the ship by using a detergent additive for high-BN applications blended with system oils. One example is iCOLube, introduced by Lukoil, that uses a high-BN MDCL with used or fresh system oils.”
System oil is a separate fluid used in a ship to lubricate the crankcase.
Huot states that changes in the way lubricant suppliers service this global market is impacting the availability of MDCLs to ship owners further complicating how they can deal with using multiple fuels. She says, “There are now at least six types of different MDCLs sold on the market, and a typical ship will require the use of at least three of them if moving from an HFO area to a low-sulfur HFO area to an ECA. Considering that a maximum of two tanks are available in most ship designs and that drum storage on deck is only a last resort (due to being a possible hazard), regular availability has become a major issue. Switching between fuels is still a gray area as ship owners are uncertain about how to manage the transition, establish accurate feed rates and limit the risk of costly wear. In using MDCLs, too much and too less are both harmful and might cost way more than just the cost of the lubricant.”
From Huot’s perspective, the good news is that the choice after 2020 for ship owners will be whether to install a scrubber. She says, “We believe most ship owners will not decide to use a scrubber after 2020.”
COLD CORROSION
Wolpert indicates that cold corrosion occurs as a consequence of slow steaming that reduces engine load leading to lower combustion chamber temperatures and lower cylinder liner temperatures. He says, “Under these conditions, more sulfuric acid, a combustion product from the sulfur present in the fuel, condenses on the liner surface and causes corrosive wear that is often termed cold corrosion. MDCLs with 70 BN are not adequately formulated to neutralize the increased acid levels.”
Wolpert believes that different lubricants and operating adjustments are needed to minimize cold corrosion. He says, “One solution has been to introduce lubricants with higher base levels (100 BN) and higher lubricant feed rates, sometimes above 1.2 grams per kilowatt-hour. These operating adjustments have been approved by the engine manufacturers to prevent corrosion. In addition, OEMs have begun to support the use of 140-BN lubricants as one means to provide adequate basicity for neutralization, yet reduce overall feed rates to reduce lubricant consumption and total operating costs.”
While Soobramanien sees cold corrosion in some older vessels following slow steaming guidelines, the problem seems to be prevalent among newer engines in recently built ships. She says, “Newer engines are operating at higher pressures resulting in more of the sulfur in the fuel being converted to sulfuric acid. Extreme corrosive wear can be observed in modern engines even under normal operation.”
Huot agrees that cold corrosion is widely seen in marine diesel engines and indicates that a condition monitoring program is essential to make sure any operating issues can be promptly handled. She says, “Serious cold corrosion is found in at least one engine out of 10 since the appearance of new designs in 2010. Without monitoring, a ship operator cannot know what is occurring. Testing needs to be done each time that refueling takes place because significant shifts in sulfur levels are possible that may impact engine operation and the onset of cold corrosion.”
As part of a condition monitoring program, Huot advises, “The lubricant supplier needs to assist the ship owner with finding the optimum lubricant feed rate, perform condition monitoring and reduce downtime costs.”
Thurloway feels that specially formulated 140-BN MDCL can be designed to minimize cold corrosion in the most modern ultra long stroke slow speed engines using a high-sulfur-containing HFO. He adds, “Cold corrosion can be managed effectively using the correct base number lubricant in conjunction with MDCL oil monitoring to ensure that the correct feed rate is used.”
Figure 1 shows how condition monitoring is done to evaluate the iron content, a measure of wear in the lubricant, as a function of feed rate and BN for older engines (in red) and newer engines (in blue). Thurloway says, “A new engine type requires about three times as much 70-BN lubricant dosage to attain the same corrosion protection level.”
Figure 1. Iron content is determined as a measure of wear in a 70-BN MDCL while the feed rate is varied in old design engines and newest design engines. (Figure courtesy of Chevron Marine Lubricants.)
Changing the base number of the lubricant has a significant impact on cold corrosion and feed rate as shown in Figure 2. Thurloway says, “Moving from a 70-BN lubricant (blue) to a 100-BN lubricant (orange) reduces cold corrosion at lower feed rates. But to bring the feed rates down to historically low levels, a 140-BN lubricant is required (green line).”
Figure 2. Iron content is measured in MDCLs with three different BNs as a function of feed rate in the newest design engines. (Figure courtesy of Chevron Marine Lubricants.)
White provides details on how cold corrosion is monitored. He says, “To minimize cold corrosion, selection of the right MDCL and the feed rate are the critical parameters. New marine diesel engines typically do not operate at their maximum continuous rating due to slow steaming, which has become the norm now.
To determine the right lubricant, White feels that the best approach is to use a scrape-down oil analysis program. He says, “We can give guidance to ship operators, but the right MDCL for a specific engine can only be properly determined by doing a field trial. We recommend following the OEM guidelines and running a five-day sweep test starting at the high end of the feed rate initially before reducing it every 24 hours.”
White indicated that monitoring equipment is placed on a ship, and the engineer runs the testing and sends the results remotely to the lubricant supplier. He says, “The most important issue is to make sure that there is no increase in iron content due to cold corrosion and abrasive wear and that the residual BN level remains within the recommended limits.”
Three concerns that must be minimized are over-lubrication, under-lubrication and catastrophic wear that can be caused, for example, by catalytic (cat) fines. White says, “Overlubrication is not necessarily beneficial because there is concern about too much lubricant in the cylinder causing a build-up of deposits. Figure 3 is a graph of total iron versus total base number (TBN) that shows condition monitoring in an overlubricated engine. The optimum operating condition for the engine is found at TBN levels between 20 and 45. If higher lubricant treat rates are observed as shown with the latest samples having TBNs above 70, then the engine operating condition can be impacted.”
Figure 3. Overlubrication of a diesel cylinder engine as shown by the TBN of the latest samples can negatively effect the operating condition of the engine. (Figure courtesy of ExxonMobil Marine Fuels and Lubricants.)
White says, “Figure 4 is a graph of total iron versus total base number (TBN) that shows condition monitoring in an under-lubricated engine. The optimum operating condition for this engine is found at TBN levels between 20 and 35. Underlubrication means that most of the data points are below a TBN of 20 and results in high wear as shown by the increase in total iron content.”
Figure 4. Underlubrication of a diesel cylinder engine is shown by the low TBN values and the high iron content in most of the samples that indicate high wear levels. (Figure courtesy of ExxonMobil Marine Fuels and Lubricants.)
A similar graph (
see Figure 5) is provided for an engine with cat fines which are hard, abrasive particles mainly consisting of spent aluminum and silicon catalysts that carry through in the fuel oil from the catalytic cracking process at the refinery. The cat fines particles can cause significant abrasive damage during the combustion process in the marine diesel engine.
Figure 5. The presence of a high level of cat particles in a diesel cylinder engine can cause high levels of abrasive wear even if the engine is operating under optimal conditions as shown from data plotted on this graph. (Figure courtesy of ExxonMobil Marine Fuels and Lubricants.)
Figure 5 shows that under these conditions, most of the latest samples exhibit high abrasive wear even though the engine is operating under optimal condition.
GROUP II BASE OIL
Group I base oil production capacity is declining and generally being replaced by Group II base oil capacity, making Group II more widely available. Wolpert says, “Group I has historically been preferred for marine engine oils because it offers the best solvency power (for aromatic and polar species) which provides better capability to handle contamination with exposure to HFO. Group II base oil can, in principle, replace Group I up to 100% with little impact to overall performance, especially in MDCL because this lubricant is once-through and therefore will not be exposed to HFO and loaded up with contaminants.”
Wolpert continues, “Lubricant additive system compatibility and foaming tendency need to be confirmed when making a transition from Group I to Group II base oils in MDCL oils.”
Soobramanien says, “MDCLs in Group I and II base oils should perform satisfactorily in engines operating on low- and high-sulfur fuels.”
Huot says, “Group II base oils have been in use for some time, particularly in the U.S., but also in countries where their quality is compatible with the requirements of MDCLs. The issue is the quantity of thickener needed to reach the intended marine engine oil viscosity. Attempts to work with lower viscosity base oils (SAE 40) by eliminating the need for Bright Stock were short lived and ineffective. While the trend in the lubricant industry is to move from Group I to Group II base oils, the optimum marine engine oil formulations in the mainstream are still based on Group I.”
Thurloway predicts that MDCL suppliers will be able to formulate their products in the future with both Group I and Group II base oils. He says, “There is some growth in Group II base oil use, but this tends to be more in regions with supply constraints. The market share for Group I base oils may be down due to reduced capacity, which means we are prepared to use both Group I and Group II base oils in our current and future MDCL offerings.”
NATURAL GAS
The use of natural gas as a fuel is growing due to greater availability, lower cost and more efficient combustion, leading to lower emissions levels that can meet the upcoming IMO regulation. These factors are becoming apparent with greater availability of liquefied natural gas (LNG) at some ports.
Huot says, “The shift to LNG is coming quicker than most people believe. A good number of bunker barges, liquefaction plants and terminals are in operation in locations such as Scandinavia, Rotterdam, Belgium and Zeebrugge, Belgium. In the U.S., the ports of New York and Long Beach also will have access to LNG in the near future. We determined that some new ships under construction will be using LNG and there are a number of ships undergoing retrofits that will switch to LNG. One fuel supplier has established key scale-able LNG hubs that has been quite successful on a small scale to date. The purpose of the hubs is to develop cooperative relationships with ship owners in key geographical locations.”
Huot continues, “Field experience with LNG is still quite limited, and more is needed to define the key operating parameters so that the proper lubricant formulations can be recommended and ships can achieve optimum performance. We believe that this will occur and that a valid business case exists for using LNG as an alternative fuel over the long term.”
Thurloway says, “LNG is already used in some ships and will become more prevalent in the coming years with the continuing implementation of emissions constraints and rolling out of LNG bunkering infrastructure.”
Soobramanien is mindful that LNG use, while limited, may lead to a lubrication challenge in case of dual fuel application, depending upon the length of operation of high-sulfur fuels. She says, “LNG has recently been introduced as a fuel for 2-stroke engines, and only a few ships are running on LNG or LNG + distillates or HFO. The concern is that using high-sulfur fuels may lead to deposit and wear problems.”
White also agrees that natural gas use as a fuel is in its infancy. He predicts that demand for natural gas-powered ships will grow and adds, “Our energy outlook estimates that 10% of the marine ships operating by 2040 will be using natural gas.”
CARBON DIOXIDE AND NOx EMISSIONS
Besides reducing the sulfur level of fuels in an effort to lower SOx emissions, trends are in place to also reduce NOx and carbon dioxide emissions. NOx emissions are being regulated by geographical region. White says, “Ships built after Jan. 1, 2016, must comply with Tier III NOx regulations in North America and the U.S. Caribbean ECA.
Thurloway lists several other options for reducing NOx emissions, including combustion tuning, 2-stage turbo charging and water admission (either by direct injection, emulsion of water in fuel and humidification of charge air). He says, “The use of SCRs seems to be the most adopted option. SCRs are relatively new in the marine industry and experience is limited. However, research work shows that the impact on poisoning by the lubricant and marine fuel is manageable with the products available today.”
An additional regulation facing ship owners was IMO’s implementation of an Energy Efficiency Design Index (EEDI) on ships built after Jan. 1, 2013. White says, “EEDI regulates the allowable carbon dioxide emissions. The base line for this was determined by ship size and type.”
As the EEDI concept is being introduced for newly built ships, IMO has developed the Ship Energy Efficiency Management Plan (SEEMP), a management tool to assist ship operators in managing the energy efficiency of their vessels. Soobramanien says, “IMO has established a series of baselines for the amount of fuel each type of ship burns for a certain cargo capacity. Ships built in the future will have to beat the baseline by a set amount, which will get progressively tougher over time. By 2025 all new ships will be a massive 30% more energy efficient than those built in 2014.”
Soobramanien points out that the reduction in carbon dioxide emissions will not impact the current lubricant additive technology used in formulating MDCLs.
Figure 6 lists a summary of the reduction in the emissions of SOx, NOx and carbon dioxide emissions by geographical region and by implementation date.
Figure 6. A summary of the reduction in the emissions of SOx, NOx, and carbon dioxide by geographical region and by implementation date is shown. (Figure courtesy of The Lubrizol Corporation.)
FUTURE TRENDS
Huot indicates that two future trends for the industry to deal with are issues with fuel blend contamination and dual fuel-2-stroke marine diesel engines. She says, “Fuel blend contamination will be one of the biggest challenges for the marine industry. The cat fines problem previously seen will come back as a major issue because any fuel stream that has a low-sulfur level irrespective of the degree of contamination will be used for blending. The objective of ship owners is to meet the 0.5% sulfur maximum target at all costs. A misconception exists that ship owners will burn straight cut distillates. Instead, ship owners will purchase whatever fuel is available that meets the sulfur regulation at the lowest cost.”
OEMs are starting to develop engines that operate on more than one fuel. Huot says, “The OEM Wärtsilä has just introduced a new hybrid product that is the first hybrid module of its kind in the marine industry. The fully integrated hybrid power module combines engines, an energy storage system and power electronics optimized to work in unison through a newly developed energy management system (EMS). Future lubricant formulations will have to cater to very diverse requirements.”
In addition to the regulation issues, Soobramanien believes that there will be changes to the system oil. She says, “System oil will be affected by changes in the cylinder and additional hydraulic and lubrication duties such as fuel injection, turbochargers and cross head bearings.”
White feels that the various regulatory changes affecting SOx, NOx and CO
2 will continue to lead to changes in engine designs as the marine industry strives for better efficiency. He says, “Lubricants will need to adapt to changes in engine designs where there are increases in operating temperatures and pressures.”
Changes in MDCLs will be impacted by regulatory drivers that are in the process of being implemented. Ship owners will be striving to reduce operating costs in today’s competitive environment and will need to choose between using low-sulfur fuel or scrubbers after the IMO regulation becomes effective in 2020. Lubricant manufacturers and additive suppliers will need to continue to develop solutions in the future to meet these ongoing changes in the marine industry.
REFERENCES
1.
Canter, N. (2015), “GF-6, PC-11 and dexos1™: New engine oil specifications mean new additive challenges,” TLT,
71 (9), pp. 10-24.
2.
Sniderman, D. (2017), “VGP 2013: Propelling marine lubricants,” TLT,
73 (5), pp. 32-40.
Neil Canter heads his own consulting company, Chemical Solutions, in Willow Grove, Pa. Ideas for Tech Beat items can be sent to him at neilcanter@comcast.net.