What are the tribology and lubricating issues that will be most impacted by 3D printing?
TLT Sounding Board September 2017
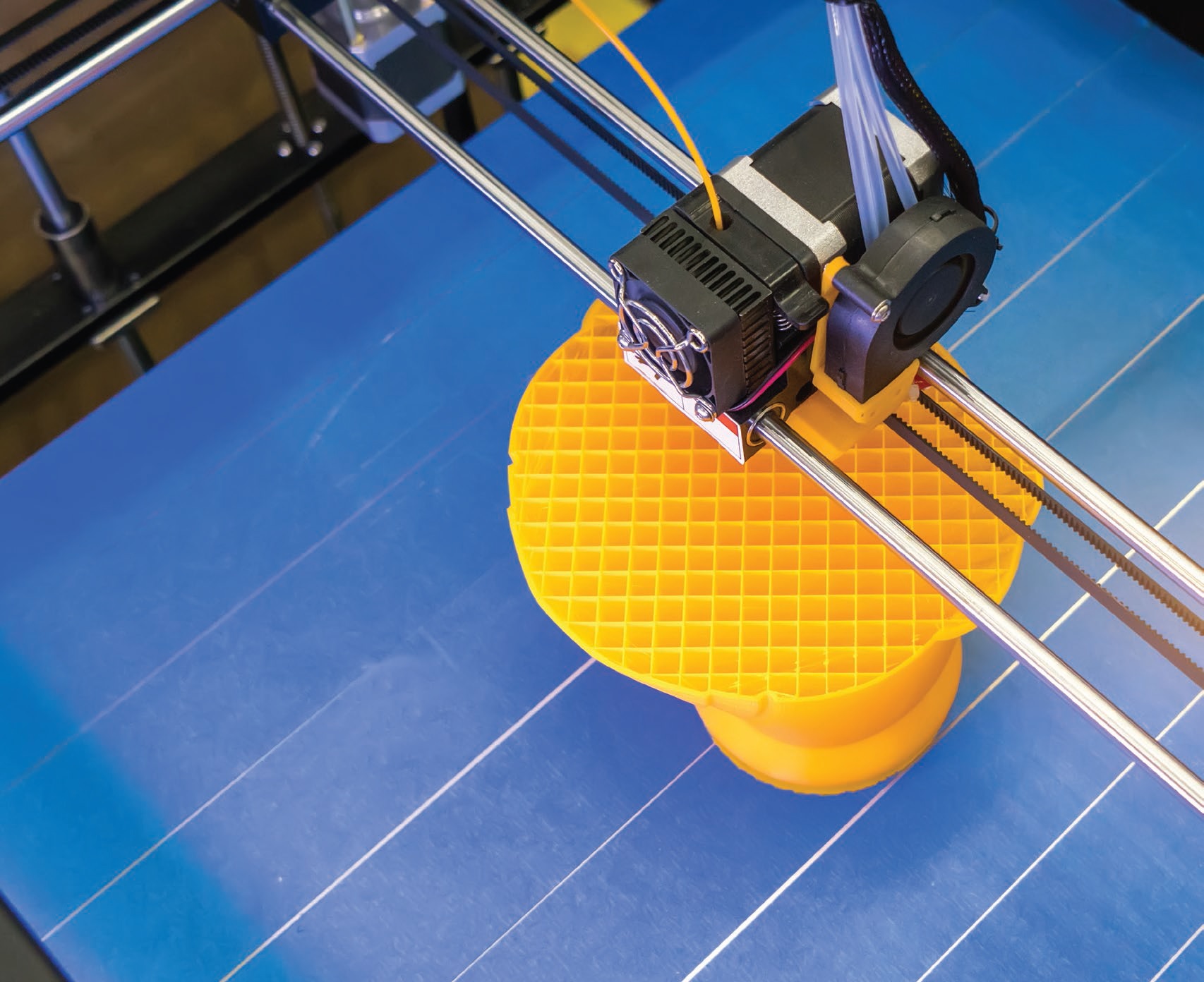
© Can Stock Photo Inc. / dashark
TLT readers responding to this month’s survey agreed that while 3D printing’s short-term impact on the lubricants industry might be minimal, long term the story could be significantly different. Among the potential key changes readers listed: the amount of machining fluids needed could be drastically reduced (especially metalworking fluids), blending could become more complex and the cost to produce additives could go down. At the same time, several readers noted many key lubrication principles remain unchanged with 3D printing—you still need the proper lubricant for the job, you must deliver it in the right location and you have to keep the lube and surface cool. Despite 3D printing’s reputation as a miracle worker, readers noted that the process does have practical limitations; it’s nowhere near providing the preciseness required for the bearing industry. Perhaps the most prevalent attitude to come from this month’s survey was captured in the comment of one reader: “3D printing is definitely here to stay,” he said. “However, its role in manufacturing tribological components needs much more R&D.”
One issue is having lubricants that are compatible with the 3D-printed material. As a supplier of lubricants, the impact would be to be able to make recommendations based on materials in use and the application.
Vast reduction in waiting for parts time if objects can be printed on site. It also would allow for realistic mockups of new concepts for tooling and parts.
3D printing will bring about new product development cycles.
I could imagine more economically made, lubricant-impregnated bearings, bushings, etc.
Definitely, tribology issues will impact 3D printing because you still have issues related to friction and wear.
Potential is vast and would affect tribological work and research, in development of liquid and grease-free materials for moving parts.
Impact could be great, really great. It could change completely the way we think about lubrication.
Many moving pieces, usually working at high temperatures, high speed. There will be a need for a cheap performance lubricant that can work in those conditions.
With 3D printing technology development, demand on lubricants might be becoming less.
It seems best suited to manufacturing structural parts that are difficult to machine. I haven’t seen anything with it that uniquely affects the field of lubrication.
Very little. I think the impact in certain areas is overrated.
3D printing is continuing to extend its reach into a diversity of industries. This technology has the potential of being an economical disruptor due to its ability to form almost anything while replacing many processes and equipment that are currently required.
How much impact do you think 3D printing has had to date on the manufacture of bearing, coatings and surface engineering?
I’ve seen some meaningful activity in this area
19%
Not a tremendous impact, but I’ve seen a few interesting things here and there
24%
Very little
32%
I’ve seen absolutely nothing relating to 3D printing
25%
Based on responses sent to 13,000 TLT readers.
More opportunities to promote tribology and metrology products.
The most valuable uses are for prototyping and obsolete part replacement. I have even heard of someone that created a new part for a 3D printer with a 3D printer.
The surface roughness that can be achieved from 3D printers is not as per the requirements of bearing industry. I was told that finest surface roughness that can be achieved is 10 micro-inches. Also I am not sure if 3D printers can produce complex geometrical parts such as bearing components.
With 3D printing, there is good potential to form small intricate passages for either cooling or lubricant supply. Getting lubricant to the right location is highly important—keeping the lubricant and surfaces cool is critical, just as with other forms of manufacturing.
Very intricate part designs can be created by 3D printing that cannot be produced by current machining (subtraction manufacturing) processes. The need for machining fluids might be drastically reduced.
It certainly has the potential to reduce metalworking fluids consumption. There is still a need for corrosion preventatives, but that is not where the volume is in lubricant consumption.
I am not too familiar with the components that are manufactured with 3D printing. However, I would be concerned that component quality may be inferior, making lubrication and tribology issues more challenging with these components.
None that I can recognize at the current time.
Greater complexity in blending, with the potential to lower additive cost.
Stamping and machining processes will be different. And the characteristics of lubricants will be changed.
Lubricants to lubricate the 3D printing equipment.
Interlayer material property variation and porosity. Impact will be changes in process technology for surface modification. Right now we work with nominally non-porous surfaces that are quite homogeneous. That is going to change.
Have you heard of or seen any tribologically optimized material tailored for 3D printing of parts such as bearings, bushings, self-lubricating adaptive parts or anything else?
I’ve seen materials like these first hand
13%
I haven’t seen anything but I know others who have
17%
No, I’ve not seen or heard of anything along these lines
70%
Based on responses sent to 13,000 TLT readers.
© Can Stock Photo Inc. / Suljo
Material properties, clearances, form, etc. Could have positive effect on reducing stocked spares and delivery times.
In-depth study of the lubrication engineering would be required. Product formulators will have to optimize and design more advanced packages to cater to the challenges emerging from 3D printing.
Hopefully lower costs.
It makes sense for certain applications that traditional machining can’t fulfill. It is currently limited by extreme high costs and very long production times.
This is a difficult question to answer, as 3D printing has the potential to make parts available that are un-manufacturable (for whatever reason) other ways. There are parts yet to be dreamt up and printed that will have tribological needs yet unseen by the industry.
I’ve observed 3D printing applications to make plastic components of models of devices in engineering labs. This enables engineers to save time, material and effort versus working with machinists to build models. While this is a great advantage, I haven’t seen 3D printing of metal objects and don’t anticipate that 3D printing will impact the lubes and grease industry in the near term.
Surface roughness and porosity may play an important role in the tribology of lubricated functional dynamic surfaces. At this point it offers quick prototype construction and fit and function trials of new designs. In the future, production metal components 3D printed may reach the marketplace as the technology is developed for mass production.
Molded parts.
We will respond to the Brave New World as it emerges from the fertile minds of our brilliant whiz kids of every age.
This is a very new technology, and many companies are investing time and money to support it. However, ASTM standards are trying to catch up with all the parts being made since there are issues with powder quality, build density/porosity, build consistency, post-processing, surface roughness of the part and consistent microstructure and composition of the part. Thus, more research is needed to address these issues. The powder bed fusion process has recently been demonstrated to build gears. AISI 316 steel has recently been additively manufactured so other steels may be on the way. Cost analysis studies also need to be performed. 3D printing is definitely here to stay. However, its role in manufacturing tribological components needs much more R&D.
As long as we have internal combustion engines, my particular function has a reason to continue.
Use of oil and additives on materials. It could replace castings on equipment.
3D printing is definitely making it easy to produce parts that are otherwise time consuming and expensive to make. However, the surface finish is almost always compromised, thereby increasing friction. A post machining operation is not always possible for all parts, too.
In the short term, very little. I am retired but do some consulting with a technical college that is developing its abilities with 3D printers.
Although this practice is not widespread, I foresee that there will be a need to have better lubrication to avoid too many deposited layers being removed during post-additive-manufacturing finishing steps. Equal cases could be made for tool life increasing due to looser layers of material or decreasing due to rougher initial tool/workpiece contact surfaces.
The 3D printing I have seen for the most part still requires lubricant for end products. I believe it impacts various parts manufacturer employees more than anyone.
Do you agree that 3D printing could usher in a third Industrial Revolution?
Yes
27%
No
13%
Maybe
60%
Based on responses sent to 13,000 TLT readers.
Editor’s Note: Sounding Board is based on an email survey of 13,000 TLT readers. Views expressed are those of the respondents and do not reflect the opinions of the Society of Tribologists and Lubrication Engineers. STLE does not vouch for the technical accuracy of opinions expressed in Sounding Board, nor does inclusion of a comment represent an endorsement of the technology by STLE.