Are synthetic chemical markers needed in lubricants?
Debbie Sniderman, Contributing Editor | TLT Feature Article September 2017
Lube suppliers are using chemicals, dyes, DNA and other markers to prove the authenticity of their products.
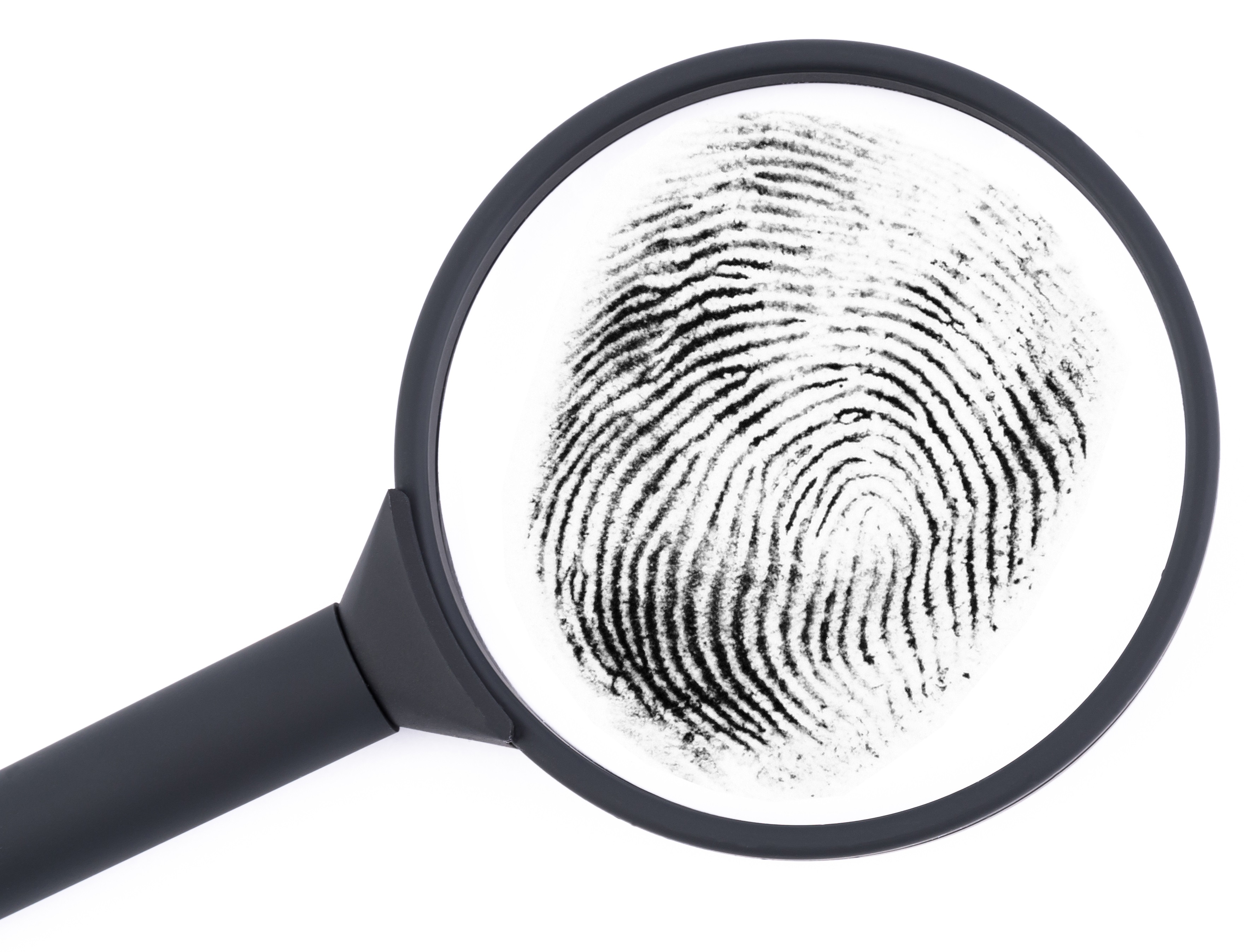
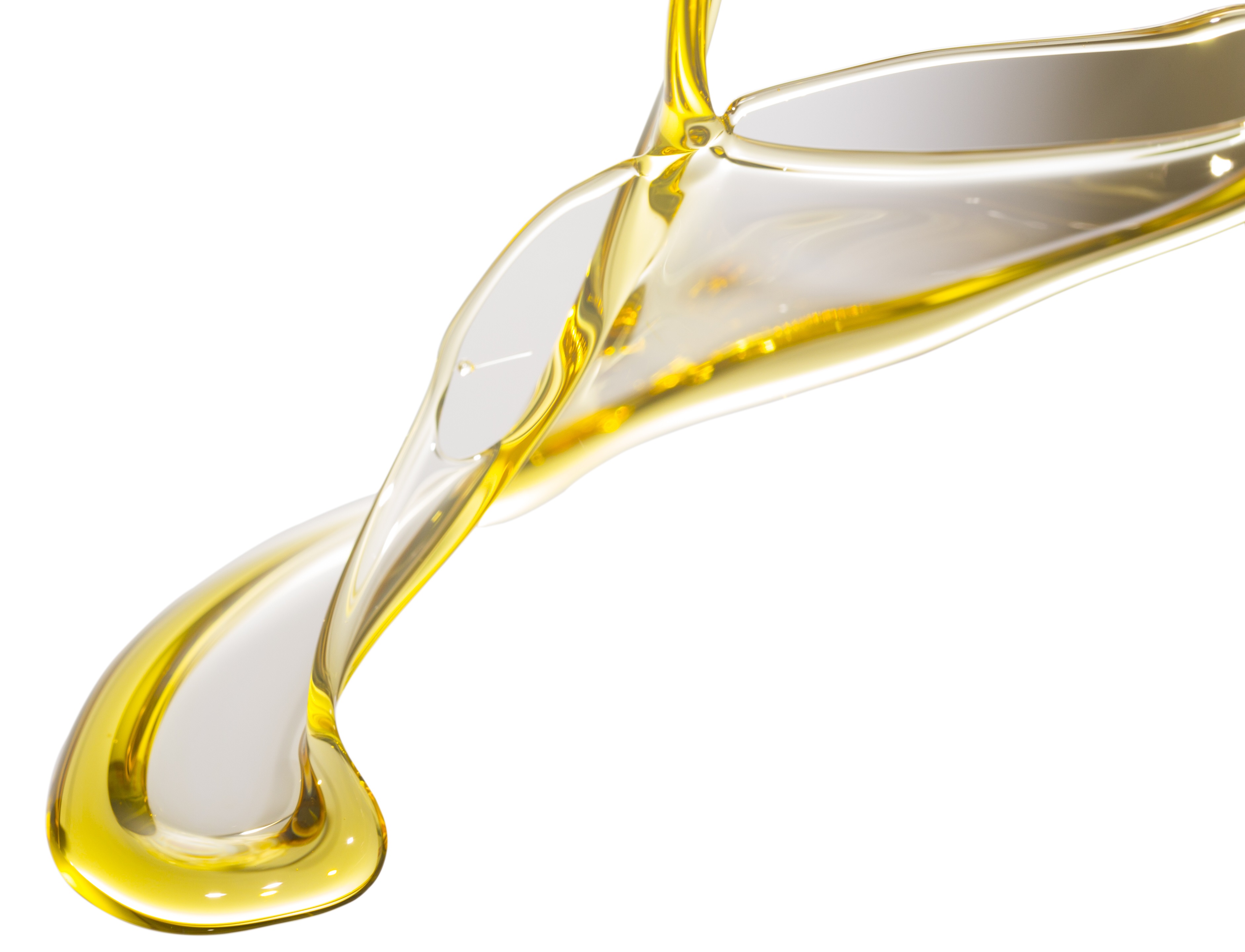
Photos courtesy of Dow Chemical.
KEY CONCEPTS
•
Adding synthetic chemical markers to lubricants is important when authenticity is a critical factor.
•
Encapsulated DNA markers offer an unlimited number of unique sequences without toxicity, and the technology is cost effective.
•
There is a growing demand for new chemical markers to provide more information about a lubricant over its lifetime.
CHEMICAL MARKERS CAN OFFER LUBRICANTS their own unique fingerprints. The authenticity of lubricants can be vital in maintaining operational excellence of equipment.
Yet, how do consumers or equipment end-users really know what they are buying? Is it really the genuine brand? And for equipment under warranty and where lubricant replenishment occurs by an end-user after a period of operation, how does an equipment builder know the correct lubricant has been used when an issue arises?
Chemical marker technology is advancing fast. The category of markers contains both dyes, which are readily visually identifiable, and markers, also known as tracers, which need some sort of analysis to detect. Markers have application in some markets and are becoming well established. This article explores whether there is a need for chemical markers or tracers in lubricants and the market segments where they are useful. Also presented are advancements in marker technologies and information about how analytical techniques have advanced enough to detect complex unique markers.
CURRENT USE
According to Rick Butler, former research and development manager while at Chemtool Inc. in Crystal Lake, Ill., chemical markers are commonly used in lubricants by toll blenders that mix and process products for their customers. They’re needed to make sure toll blenders create formulas to customers’ specifications, using customers’ ingredients and are used to identify the product in the field.
Blenders commonly use two types of markers today, antimony and fluorescent UV dyes. The dyes appear invisible when used in small amounts and can be checked with a UV/visible spectrophotometer (
see Figure 1).
Figure 1. Dyes are commonly added to lubricants for identification and to distinguish product grades. (Figure courtesy of Dow Chemical.)
“All lubricants from toll blenders have them,” he says. “Markers are added as a critical ingredient so customers can check samples the blender made and verify the formula is accurate and substitutes aren’t used.”
Markers also are commonly used in grease. Most grease contains colored, oil-soluble dyes so users can visually identify which grease to use. “A machine in a steel mill may use eleven different grease chemistries, each with a different color. It is difficult to produce that many distinguishably different shades, but we do, and they are helping people keep them straight,” Butler says.
Carine Bove, marketing manager for performance lubricants and fuel additives at Dow Chemical in Saint-Denis, France, says many dye and marker products go into greases, motor oils, hydraulic fluids, vehicle fuels and other formulations that can be used for detection, colorization and product differentiation.
Diesel and gasoline fuel markets are the largest and most popular industry for markers that are commonly used to differentiate grades of products, like super-premium or regular gasoline.
In the UK and U.S., fuel is taxed lower in vehicles that operate off-road than fuel used in on-road commercial vehicles. Fraudsters are known to sell cheaper off-road fuel for commercial use at fuel retailers, costing the government in tax revenues. Chemical markers added to fuel at parts per million (ppm) levels can determine the authenticity of the fuel and track down fraudsters.
Dyes in fuels visibly mark whether they are for taxable or non-taxable applications. They also can indicate branding, unauthorized usage and protect against theft. Un-dyed or unmarked “clear” over-the-road diesel fuel that appears yellowish is used in highway equipment that pays fuel tax. Red-dyed diesel fuel is used in off-road vehicles such as mining, farming, marine and construction equipment to indicate a reduced or non-taxable application.
Zahid Asif, research scientist at Dow Chemical in Philadelphia, says, “There also are options to include tracers and markers in product packaging as an additional way to trace a product. Special labels or adding something into a pail or drum as the source of the tracer may thwart those who may try to reuse a drum with their own product and reseal it. Chemical markers in the packaging are one way for customers to control the product. But the best way is to mark a lubricant with a chemical marker that can be monitored both qualitatively and quantitatively.”
Dr. Michela Puddu, CEO of Haelixa LLC, a startup company based in Zürich, Switzerland, producing smart DNA tracers, says markers have many uses today. Chemical markers are solutions applied into or onto a product and are dyes, nanoparticles or any other substance with a unique chemical molecular identity that can be analyzed in a specific way. Added to raw materials or finite products, the tracers can track them through every step of processing and distribution, ensuring product authenticity and quality all the way to the end-user (
see Figure 2).
Figure 2. Added to raw materials, DNA tracers can track them through every step of processing and distribution, ensuring quality products to end-users and retailers. (Figure courtesy of Haelixa Oil.)
She says quantifying tracers also can check if oils or other specialty chemicals were diluted or mixed with cheaper products to detect product tampering.
MOST USEFUL INDUSTRIES
STLE-member Daryl Beatty, product development manager at American Chemical Technology, a synthetic lubricant manufacturer in Lake Jackson, Texas, says the stakeholders most interested in using markers are upper echelon lubricant suppliers who sell top-tier products that have some liability associated with it. “Anyone producing sophisticated products that couldn’t be duplicated doesn’t mind going through the trouble and expense preventing duplication,” he says.
Market segments most interested are in the aviation industry where there are regulations and high-value equipment. “ExxonMobil makes a jet turbine lubricant that can’t go bad. This is a prime opportunity for markers. If a plane crashed and engines failed, the stakes are so high there would be tracers to categorically say whether this machine was running on their fluids,” he says.
“All markers tend to be expensive. While there are some markers that are useful in new fluids, identifying markers in used fluids after they have been abused for a year at high temperature, may take extensive analysis, which also can incur high costs. It may be too expensive to use markers in industrial lubrication markets to definitively say if compressor lubricants used in a warranty claim were OEM or similar products made by aftermarket producers. It may not make sense. The solution shouldn’t cost more than the problem trying to be solved. With all the costs that go into putting markers into every fluid and performing analyses, it may be cheaper to pay a warranty claim,” says Beatty.
Those least likely to use markers are aftermarket suppliers who serve standard industrial markets and see no need for their use. “Some fluids we make are very similar to OEM fluids, and we don’t need a marker because we don’t need to distinguish between OEM and our aftermarket offerings. As a supplier, we are happy with the idea that the fluids are similar,” he says.
Bove says everyone from lubricant marketers, environmental agencies and governments to equipment users can benefit from adding markers to lubricants. “Manufacturers usually mark their products as part of their reputation, to offer customers a guarantee that their product is indeed inside and to protect their brand. If there is an issue of another product being sold under their trade name, they want to make sure the product sold is theirs and not a lower quality one. For consumers, markers ensure the product is the brand they intended to purchase, not one of lower quality or deteriorated in a way that may damage their equipment. Using low-quality engine oil when expecting premium oil may cause engine issues. When there is no waste management system, adding markers to lubricants will help reduce the amounts that are dropped in the field. It also could help environmental agencies locate illegal waste disposal and fight against it,” she says.
There also is a need for new markers that can detect and indicate the quality of a lubricant over time as it degrades or oxidizes, says Asif.
ADVANCEMENTS
There is a lot of interest in using nanoparticles as tracers. When added to fluids, they need to have a high surface-to-volume ratio. Minute volumes are used, making them invisible and reducing the effect they have on the product they’re in.
Smart tracers go beyond simply marking a product and are able to monitor properties of a product to ensure its quality. They can be used as a quality tool, indicating when something has been exposed to light, a high temperature or damaging stresses or events. They typically involve chemicals that are sensitive to the property to be measured. A dye could change color or particles could aggregate where the aggregate size correlates to temperature. Exposure produces a change in the molecule or chemistry and the change is detected with a standard technique.
Another emerging trend in marker technology is quantum dots. These fluorescing nanocrystals have applications in the fuel industry. They can be detected with UV light sources when added to liquids. They offer the advantage of very simple detection and a simple application. But they are still in development and not yet commercially available.
New encapsulated DNA markers can be applied to lubricants. An unlimited number of DNA sequences can be generated to provide as many unique “signatures” as needed, and “biologically identify” or label products. The encapsulated DNA markers are invisible to the naked eye and do not alter product appearance and properties (
see Figure 3). Furthermore, the DNA markers are harmless, as both the DNA and the encapsulant are non-toxic.
Figure 3. Unlimited information can be coded into invisible DNA sequences creating unique tracers inside fluids. (Figure courtesy of Haelixa Oil. Credits to: nexus 7/shuttertock.com.)
Data can be encrypted inside the DNA sequence, and users can build their own code and use it to write into the product. It is a compact way of putting huge amounts of product information like place of origin, manufacturer, batch number or production date into a product, something that can’t be done with other chemical markers.
“With chemical markers, there are only a few options for materials and a limited number of distinct fingerprints. There are only a few colors of dyes available, and they will be repeated. There aren’t enough to have a different one for each product, manufacturer, batch or place of origin. DNA makers allow a much deeper level of labeling,” Puddu says.
Also, DNA markers are not easy to copy or reproduce and are difficult to remove. They can be detected at extremely low levels, making the technology cost-effective.
Haelixa has advanced DNA marker technology with its encapsulation, a strategy for protecting and attaching the delicate DNA to real products. DNA molecules are put in capsules that are sub-micro spheres of approximately 100 nm in diameter. This protection stabilizes them so they can survive in conditions they otherwise couldn’t. The capsules can be compatible with any fluid, water or oil, and exposure to temperature, shock, sunlight and UV light doesn’t damage the trackers inside.
Encapsulated DNA markers can be embedded into raw materials or applied to the surface of almost any product, from packaging to fabrics, fuels, plastics or other industrial materials, ensuring transparency and supply chain integrity.
TECHNICAL CHALLENGES
Long-term oxidative stability and thermal stability in a used fluid are the main challenges for using markers in complex lubricant formulations. Some people test new fluids at the beginning of their life to see if distributors are honest. But most test them after a breakdown occurs, at the end of a fluid’s life and after it has been exposed to high temperatures and oxygen, when it is difficult to guarantee.
If the marker degrades, it disappears and doesn’t serve its function. It has to withstand the rigors of use. Elemental markers like antimony don’t degrade, but fluorescent dyes can break down and fluoresce at wavelengths they weren’t intended to. Other materials in a lubricant also can fluoresce at wavelengths near but not exactly at the same wavelength as the marker. If these markers change, overlapping fluorescence can occur, which is undesirable.
A marker also should be stable in sunlight and pass other absorption tests. It should be identifiable at whatever background level is present and not be removable. It also must be inert and not react with anything it comes in contact with.
Bove says the biggest challenge is the uniqueness of the molecule used for the marker because there are a limited number of molecules and combinations available. Along with a high demand for marking many specific applications or regions, more molecules are needed.
Even DNA markers without uniqueness limitations have other challenges. When chemical or DNA tracers are added to a fluid and then mixed, they must mix easily and be soluble in the fluid they are added to. Having a stable dispersion also is important. If they settle and form sediment on the bottom, they can impact the life or usefulness of the fluid and lose the marker in the bulk of the fluid.
It’s also important to record and analyze markers in an easy way from a sample on the spot. They should be stable enough and avoid requiring multiple steps before analysis. Normally portable devices have lower sensitivities, making it a challenge to ensure efficient readings. Some analysis techniques don’t allow portability at the required sensitivity or offer cost effectiveness in the portable format, like mass spectrometry. There are a number of portable analysis techniques with decent sensitivity available, so applying these to DNA markers means unique instruments don’t need to be developed, helping balance outcome, cost and portability.
WARRANTIES AND EQUIPMENT RELIABILITY
OEMs often recommend specific approved lubricants for use in their equipment, which are replaced or replenished by users. For equipment under warranty, chemical markers also could help avoid the use of non-OEM approved products and help improve operational reliability of equipment, but attitudes vary widely throughout the industry.
Beatty says, “Equipment specs provide several fluid choices. The main factor for reliability is using an appropriate fluid. It’s not always that OEM products are good and non-OEM products are bad. Often inappropriate products are used. People put rotary screw compressor fluid in a centrifugal compressor. There are factors other than viscosity to consider. Once they depart from OEM recommendations, they sometimes make bad choices of what to use.”
Butler says fluorescent dye markers have been used in many fluids, not only lubricants, for decades. Layout fluids, paint-like coatings containing antimony, could be applied onto gears such as in a car or truck differential to show the location of rubbing wear.
He says markers also are used in other single-purpose machine marker fluids to check the structural integrity of expensive parts. They contain either ultraviolet fluorescent dyes detectible by blacklight or magnetic fines detectible by magnets and help detect leaks or other microcracks that aren’t visible to the naked eye.
According to Beatty, there are two problems with fluorescent UV tracer dyes. “The first is using the right amount to get the fluid to light up enough to distinguish the glow difference between fluids with and without tracers. Some base stocks light up on their own, especially when they contain impurities or certain additives. The second is producing a compound that is stable at high temperatures for long periods of time, to be reliable as it ages. Aromatic ring compounds were not good choices for these, but others were found that don’t break down,” he says.
“Improving equipment reliability with markers is a gray area,” Butler says. “Machine tool builders used to specify lubricants to be used in their machine, otherwise the warranty was void. But a court ruling found that to be a restrictive restraint of trade, so now consumers and industrial equipment owners can get oil or grease from anywhere and anyone as long as it meets API specs and won’t void warranties.”
FOOD PROCESSING
While chemical markers could help improve the use of authenticated, food-grade-approved lubricants in the food-processing industry where safety standards are very high and quality is critical, it is unlikely they will raise the environmental, health and safety standards of the food-processing industry any time soon.
“It would be beneficial. Everyone would love to be able to quickly identify their product,” Beatty says.
Problems arise because the markers themselves need to be food grade or food compatible. When they are introduced into lubricants that will have indirect contact with food, they would need to be made from materials on the U.S. Food and Drug Administration (FDA) HX-1 category list. If they were going to have direct contact with food and will be eaten by people or animals, they are regulated and have to be on an FDA list.
“Just getting a new ingredient onto one of these lists takes a lot of effort for a manufacturer and involves heavy testing. Once a marker ingredient is on the list, anyone else could use it too, making it not so secret,” Beatty says.
Dow has some food-grade markers with indirect food-grade approvals, but they are not used in the lubricant space. Food-compatible DNA markers also are used in the food industry as a tracer and their short sequences end up in the food, but again, not in food-grade lubricants.
WATERWAYS
Chemical markers could be added to lubricants that can leak into waterways to trace the source of the leak back to a manufacturer or equipment user. But it is questionable if their use could help raise environmental health and safety standards of the lubricant industry.
Puddu says it is technically feasible. “With encapsulated DNA markers, you can not only detect spillage in water, but you can tell where the leak came from and use it as a tool to assign liability. Even at low dilutions, analyzing at parts per trillion (ppt) level, a few particles of DNA are enough and would be possible to detect. Encapsulated DNA markers also form stable oil dispersions so there is no risk of the markers partitioning into the water and getting lost.”
Beatty says even though it is possible, it is not likely to be successful. “Looking at a tiny amount of oil in water, it is tough to isolate just the lubricant. The marker may be water soluble and partition into the water. When it is in the presence of more water than oil, even if it wants to stay in the oil, a lot of it will wash out. Also, there is a question of if any marker is still present once a used fluid had leaked. Some markers are stable, but others degrade over time.”
To actually raise EH&S standards, someone would have to take interest and request their use. Bove says neither customers nor environmental agencies have approached Dow Chemical requesting their use. “It could be possible, but it is up to specific agencies to have an interest in detecting them. There’s a stronger argument for using markers in fuel markets where they are included to prevent bad handling or disposing chemicals into the environment, and people are trying to remove the markers. Fuels have government interactions, and we’re moving in the direction of adding stronger and higher amounts of markers. With lubricants, the interactions are with manufacturers whose main concern is brand identification, not with governments who would have a clear interest in the environments,” she says.
DETECTION TECHNIQUES
Chemical markers are typically added at ppm or parts per billion (ppb) levels, raising the question if modern analytical techniques are advanced enough to detect unique markers.
Butler says markers are used at the 30-50 ppm level in fuels and antifreeze and around 300 ppm in grease. “There are lower levels in oil and industrial fluids, and there are no problems detecting a few ppm of antimony that don’t occur naturally using inductively coupled plasma (ICP) mass spectrometry system. Standard analytical equipment can go down to the ppb range. The same thing applies with fluorescence; you can tune to specific wavelengths to see if there is a lot of product.”
Bove agrees, adding that modern techniques are advanced enough to provide both qualitative and quantitative information about a marker. If a drum of lubricant is mixed together with another, the markers there will be detectible down to around 2%. “Every year there are new markers that have a cost to include. Lower detection rates continue to drive the need for more advanced detection methods to be as minimum as possible,” she says.
Portable analytical equipment used by government fuel inspectors in the UK can easily detect markers in fuels in minutes. But some lubricant formulations are much more complex. “Whoever makes the markers will have a prescription for how to detect them. Some markers will be easily detected using Fourier transform infrared spectrometry and liquid chromatography techniques. But with sophisticated forensic-type markers that are included at the ppm level, you really have to know what you’re looking for to find them. No one in the lubricant industry would go to that much trouble. There’s not that much incentive to spend a lot of time to see if someone has a marker in their product. Most use reliable, simple analytical techniques to quickly identify their products,” according to Beatty.
Puddu says that the level of DNA markers is extremely low—at the ppt level or 1 nanogram per 1 liter of fluid. “The lower the level added, the cheaper it is to use. There’s always an interest in detecting at lower levels, especially where dilutions can occur. DNA offers a unique opportunity in this space, because DNA analysis has been developed to analyze single molecules. It has come very far,” she says.
AUTHENTICATING
Consensus is that there is a need for chemical markers to be added to lubricants when authenticity matters. Without them, it’s hard for consumers or equipment end-users to know what they’re buying. They trust bottles, labels and packaging when they’re available and hope they are buying the right product.
“Lubricants often come from bulk tanks, so trusting the source becomes important. Many times products are sold mislabeled. Bottles are refilled with cheaper fluids,” says Beatty. “Without a tracer, there’s no way to tell. With markers it’s easy to detect but unlikely anyone would ask. If someone performs an analysis, it can be identified and can go to court.”
It seems unlikely that chemical markers in lubricants will raise EH&S standards in food processing or in our waterways until a demand or government regulation exists. The technical potential of tracing a source is there. But the industry is not yet feeling the pull in that direction.
For More Information:
American Chemical Technologies:
http://americanchemtech.com
Dow Chemical: Click
here.
Haelixa:
www.haelixa.com/index.html
Debbie Sniderman is an engineer and CEO of VI Ventures, LLC, an engineering consulting company. You can reach her at info@vivllc.com.