20 Minutes With Michael Stapels
Rachel Fowler, Managing Editor | TLT 20 Minutes August 2017
This research chemist with Kao Chemicals GmbH discusses foam countermeasures and why he recommends ethercarboxylic acids for the formulation of metalworking fluids.
MICHAEL STAPELS - The Quick File
Michael Stapels is a research chemist for Kao Chemicals GmbH. He studied chemistry at the RWTH Aachen University in Germany where he received his doctorate in polymer chemistry in November 2001.
After a research associate position at the Unilever Research Laboratory Port Sunlight in the UK and other industrial R&D positions, he joined Kao Chemicals in October 2005. In his position as technical manager and group leader, he is focused in the development of additives for the metalworking industry, which includes the global technical customer support.
Stapels has published and presented papers at numerous technical conferences including STLE Annual Meetings and the TAE International Colloquium Tribology. He is a member of STLE and is volunteering in the Metalworking Fluid Education & Training Subcommittee.
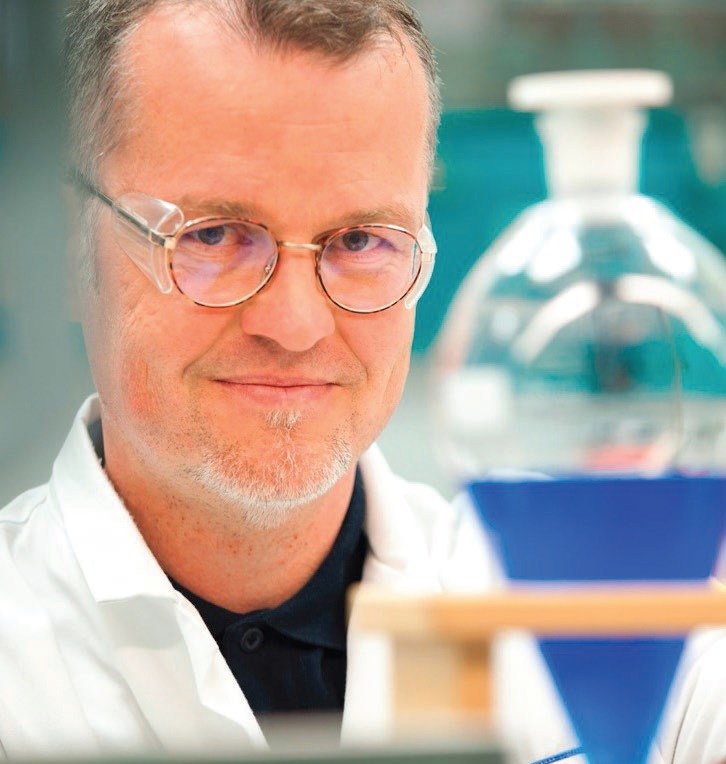
Dr. Michael Stapels
TLT: How did you become involved with the metalworking industry?
Stapels: My path to working in metalworking was somewhat indirect. My first contact to industry directly after the university was in the global R&D center of Unilever in Port Sunlight, UK. Here I was responsible for testing and optimizing cosmetic products. During this period I was introduced and captivated by the
art of formulation. The lessons learned in this early stage of my career are still the fundament even for my current position at Kao Chemicals where my team develops innovative surfactants and additives with special focus on the metalworking industry.
TLT: In Europe your company is known as The AKYPO® Co. Please explain this.
Stapels: First of all, this underlines that for our company and for our customer, the AKYPO® brand is a vital and essential part of our product portfolio. From a chemist’s point of view, AKYPO® is the brand name for so-called ethercarboxylic acids. Ethercarboxylic acids can be regarded as interrupted soaps with the addition of a number of ethylene oxide (and also now available in combination with propylene oxide) groups between the alkyl chain and the carboxylate group and can be represented by the following chemical structure:
R is derived from fatty alcohols and is between C
4H
9 and C
18H
37. The degree of ethoxylation is represented by n and usually lies between 2 and 20. M may be hydrogen (
free acid) or a cation such as sodium or magnesium. In metalworking application ethercarboxylic acids are typically neutralized with alkanolamines to give the corresponding ether carboxylate. Ethercarboxylic acids are very useful co-emulsifiers mainly for the formulation of soluble oils and semi-synthetics.
TLT: Why do you recommend the use of ethercarboxylic acids for the formulation of metalworking fluids?
Stapels: In water-miscible metalworking fluids formulations, emulsifiers constitute one of the most essential components. As an integral part of metalworking fluid concentrates, the emulsifier stabilizes the resulting emulsion and furthermore should facilitate tramp oil removal and filtration during their whole lifetime. In addition, emulsifiers need to fulfill a whole range of further requirements such as:
•
Low-foaming tendency
•
Good heat stability
•
Good toxicological and dermatological profile.
Keeping in mind that the largest component of the bulk fluid in a metalworking process is water—typically 90% or more—it is obvious that the water quality has a major influence on fluid stability and longevity. On the one side, water quality (hardness) differs drastically from region to region, and on the other side the electrolyte load of the fluid will increase during processing. The decreasing water quality affects the cutting fluids balance negatively. Using ethercarboxylic acids in the emulsifier package decreases the fluids sensitivity toward water quality significantly and thus enables long-time use of a high-performance cutting fluid without regional restrictions or modifications.
TLT: What are typical misconceptions you are confronted with when introducing ethercarboxylic acids to metalworking fluid formulators?
Stapels: There are three major misconceptions:
1.
Ethercarboxylic acids are foaming too much.
2.
Ethercarboxylic acids are too expensive.
3.
There is no need for hard water control because our fluids are used in soft water areas and/or only with water from a water treatment system.
Let me start with the last point: You should never underestimate the effect of evaporation losses and the quality of the topping up water. As a rule of thumb you might calculate the following: Assuming a 1,000 L bath with a moderate water quality of 250 ppm, depending on the evaporation losses topping up of about 50-200 liters per day is necessary. If the topping up water quality also has a 250 ppm load, you end up after one or two months with bath water quality of about 1,000 ppm—which is a significant load!
There also are some hidden sources for increasing water hardness such as magnesite-bonded grinding wheels.
On the other hand, when using a water treatment system, you might decrease the load of Ca
2+ and Mg
2+ ions in your system on the cost of an increasing Na+ concentration, which also negatively influences the emulsion quality and stability.
I will only briefly comment on the price and cost situation. For judging the performance of ethercarboxylic acids, you should keep in mind that the recommended use is not as a main emulsifier but as a co-emulsifier with all its impacts on dosage. If you find an optimal balance in your formulation you will be for sure able to reduce fluid maintenance costs and efforts significantly, but most important the fluid lifetime will be enhanced. These factors should definitely be considered in your price/performance analysis.
TLT: You also mentioned foam. What kind of countermeasures/recommendations do you provide to potential users?
Stapels: I would like to highlight two major points:
•
Large product range
•
Formulation know-how.
As The AKYPO® Co. we offer a broad range of different ethercarboxylic acids. They differ in C-chain length and degree of alkoxylation. For metalworking applications there are two main groups: short-chain ethercarboxylic acids—based mainly on Hexanol (C6) or Octanol (C8)—and long-chain ethercarboxylic acids
traditionally based on Oleylalcohol. If you combine these two groups of ethercarboxylic acids in such a way that they are fitting perfectly to the rest of your formulation, you will end up in a formulation that provides both extraordinary hard water control and very good foam control.
As the foam control becomes more and more critical over the years, we developed special grades of ethercarboxylic acids where we additionally insert a block of propylene oxide between the hydrophobic tail and the hydrophilic head group of the molecule. These kinds of ethercarboxylic acids are a viable alternative to standard products because they have significantly lower foaming potential in combination with more efficient emulsification. The concept of propoxylation in order to reduce foaming is not limited to ethercarboxylic acids. Thus, it also finds widespread use in our industry (e.g., in alkoxylated alcohols (nonionic emulsifier) and alkoxylated phosphate esters (anionic emulsifier)).
TLT: How significant is the impact of formulation on the fluids performance. Can you provide an example of improved behavior just by an optimized formulation?
Stapels: Let’s choose a low-oil semi-synthetic formulation based on sulfonates as a starting point (formulation A, basis in
Figure 1).This basis formulation shows a very high foaming potential (
see Figures 2 and 3). Accordingly the use of defoamers will be unavoidable for the final application. Typically the first tests of formulators with ethercarboxylic acids and/or nonionics is their addition to existing formulations, so
to formulate on top (formulation B).
Figure 1. Semi-synthetic metalworking fluid formulations with different emulsifier packages.
Doing so, the improvement in foaming behavior is somewhat limited (
see Figures 2 and 3). Therefore, we usually do not recommend to formulate ethercarboxylic acids on top but to consider—if possible—the whole emulsifier package. In the given example we optimized the amount of sulfonate, fatty acid, ethercarboxylic acid as well as the nonionic emulsifier. The resulting optimized formulation (formulation C) shows an excellent foaming profile as well as a significantly increased hard water tolerance due to the presence of ethercarboxylic acid.
Figure 2. Time dependent plot of foam height for 10% w/w dilutions of formulations containing different emulsifier packages at a water quality of 250 ppm. Measurement includes 10 s of foaming and 20 s of foam collapse, tested with a Krüss DFA100 Dynamic Foam Analyzer.
Figure 3. Foam height 15 s after shaking for 10% w/w dilutions of formulations containing different emulsifier packages at a water quality of 250 ppm.
TLT: How does your lab support the metalworking industry?
Stapels: As a strategic decision, our lab in Germany has its main focus on the metalworking industry. The team is a sound mixture of synthesis and formulation scientists working hand in hand in the lab.
Accordingly, one important pillar for us is to provide mutual support by our experienced technical sales managers and scientists to our customers and also to keep contact to the end-users. Here we can take advantage from our geographic position in the middle of Europe where a relevant number of global key accounts are easily accessible. It also is very important to understand regional differences from a technical point of view in order to provide the best solution to our customers.
From my point of view, our success is invigorated by our close contact to our customers and the vivid discussion and joint developments over the last decade. In order to strengthen this even more, we are extending our international presence by joining important meetings, conferences and education courses.
The other important pillar for our support is the synthesis and product know-how developed over decades. As a chemist you have lots of possibilities to change a molecule—just to mention raw material, synthesis strategies including change stoichiometry, production conditions, catalyst, etc. For example, additives coming along with the same CAS number may exhibit drastically different behavior in the final application. The more you understand the impact of the chemistry on the performance in metalworking, the more reliable you will be for any customer since metalworking applications are very sensitive to performance fluctuation.
TLT: Describe an important instrument the lab has recently acquired for supporting research in additives.
Stapels: My current favorite is an analytical centrifuge that measures instantaneously the extinction of transmitted light across the full length of a sample. This sounds somewhat sophisticated, but with this tool we are able to perform physically accelerated, direct and efficient stability testing and ranking of our formulations. By looking at the whole sample, we can measure stability as well as understand the causes of instability (e.g., flocculation). Obviously accelerated emulsion testing, determination of HLB values and increased understanding of instability is a benefit for a producer of emulsifiers, but the last point—ranking our formulations—gives a particular link to metalworking application.
Let me explain why. During this interview I talked quite a lot about foam. Everybody in our industry knows that the quality of an emulsion has a huge impact also on the foaming performance as a rule of thumb (with all its limitations): The more instable the emulsion, the less foamy it is. When comparing the foaming performance of different formulations, it is very important to be aware even of minor changes in the emulsion quality. And this is exactly the point where a standard rapid measurement with the analytical centrifuge is benefitical (statistically very robust!) by providing a so-called instability index—which is an objective figure allowing to predict the long-term emulsion stability.
Accordingly we are now able to collect routinely the
instability index of our emulsion and correlate other test results (i.e., foaming performance) with this information.
You can reach Michael Stapels at michael.stapels@kaochemicals.de.