Formulating water-based MWFs in the 21st Century
Dr. Neil Canter, Contributing Editor | TLT Feature Article March 2017
Those companies that succeed will do so with an increasingly shrinking toolbox.
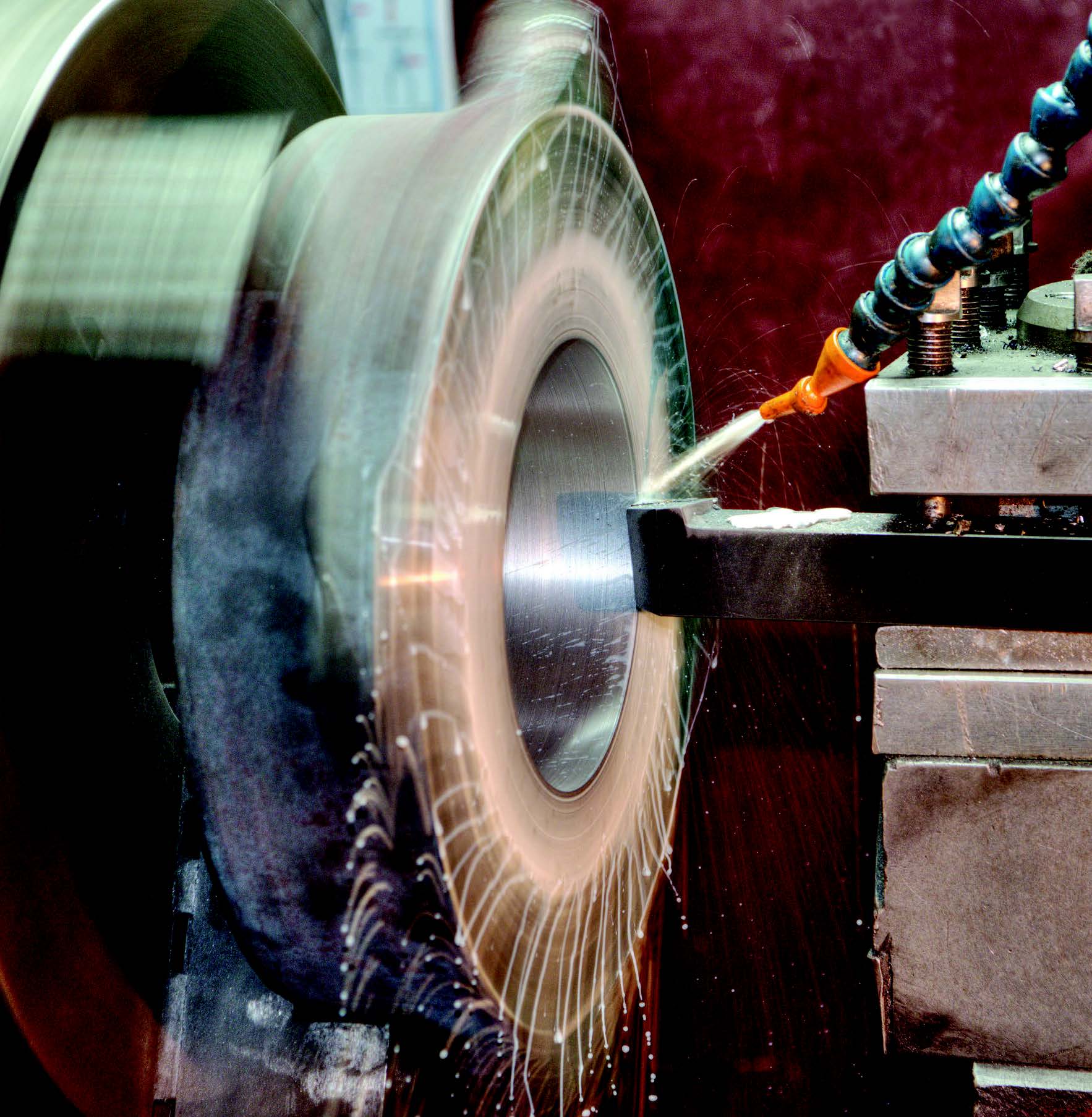
© Can Stock Photo / artfotoss
KEY CONCEPTS
• One of the biggest challenges in formulating MWFs in the 21st Century is how to work with changes occurring in regulations such as GHS, REACH and TSCA.
• New options will be needed for at least five of the additive types currently used in MWFs (including formaldehyde-condensate biocides and specific chlorinated paraffin types).
• The prospect of fewer raw material options will place more pressure on formulators to meet the concerns faced by their customers, end-users.
THE CHALLENGES IN FORMULATING water-based metalworking fluids (MWFs) continue to increase as end-users are demanding better performance over longer periods of time under severe conditions. With concerns about foam, hard water stability and microbial contamination, MWFs need to be complex formulations so they can fulfill their basic functions of lubricity, cooling, corrosion protection and flushing metal chips.
Of particular concern is fluids produced for metal removal applications. The list of additives that can be incorporated into an MWF is shown in Table 1. Finding the right combination of additives for specific machining applications while accounting for the operating conditions makes it imperative that the decision-making formulator have the proper information.
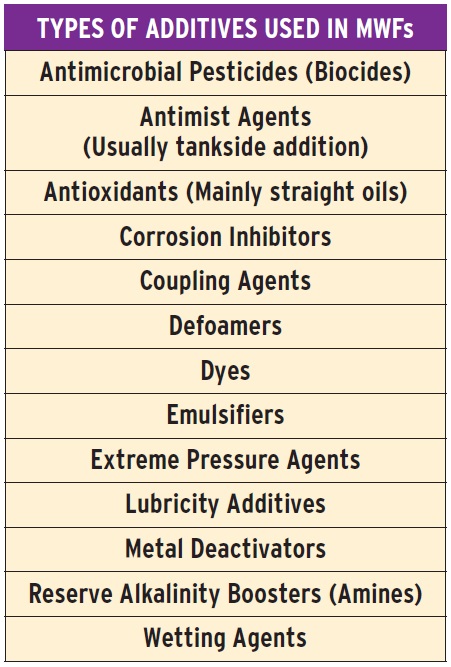
Table 1. MWFs are formulated with a wide range of additives. (Table courtesy of Chemical Solutions.)
This article obtains input on how metal removal fluids should be formulated in the 21st Century. Eleven industry experts were interviewed who have perspectives from the additive, consultant, formulator and end-user standpoints.
The following individuals were contacted.
1. Dr. Anthony Jarvis: Afton Chemical
2. Karen Harrington: Afton Chemical
3. Nicole Webb: ANGUS Chemical Co.
4. Dr. Fred Passman: Biodeterioration Control Associates, Inc.
5. Dr. Michael Stapels: Kao Chemicals GmbH
6. Gabe Kirsch: The Lubrizol Corp.
7. Dr. Ernest Galgoci: Münzing
8. Miles Free: Precision Machined Parts Association
9. Steve Thomas: Quaker Chemical Corp.
10. Gary Andrews: QualiChem, Inc.
11. Dr. James MacNeil: Qualice LLC
KEY PARAMETERS
To begin with, an assessment is made about the key parameters that MWF formulators must consider when preparing a product. STLE-member Gabe Kirsch, strategic product manager metalworking additives, North America for The Lubrizol Corp. in Wickliffe, Ohio, says, “The key parameters to consider are the overall cost of use, foam control, biostability, lubricity, corrosion and stain protection, temperature stability as the concentrate and as a dilution, odor, color and hard water stability when diluted and the final product GHS statements.”
Dr. Anthony Jarvis, R&D manager for Global MWF Product Development at Afton Chemical Ltd. in Manchester, UK, focuses on the specific technical, economic and regulatory considerations that are required when formulating MWFs. “The key technical parameters that must be considered by formulators are foaming, resistance to microbial attack, hard water stability/emulsion stability, corrosion inhibition/staining and tool life,” he says. “The balance between the cost of the MWF and its life expectancy in the field is the paramount economic factor.
“With regard to regulatory issues,” Jarvis adds, “the use of substances that have regulatory concerns or are restricted under the chemical legislation of a specific region must be considered. MWF formulators will need to take into account reactive chemistry and minimize the GHS (the Global Harmonized System of Classification and Labeling Chemicals) classification and subsequent labeling of their products.”
STLE-member Dr. James MacNeil, product manager for Qualice LLC in Hamlet, N.C., feels that the regulatory factors will be the most significant issue and even more significant now and in the future than it was in the past. He raises three important questions that all formulators must consider in working with any additive.
1. Are the components registered in all of the countries where they may be used?
2. Are there any ongoing regulatory investigations clouding the future availability of the components?
3. Are there any possible exposure concerns?
MacNeil says, “One additional issue that must be examined is the potential interactions among components that could potentially generate a new material such as a salt that is not registered on one of the commercial country databases (such as the U.S. TSCA Inventory).”
STLE-member Nicole Webb, technical sales representative, MWFs for ANGUS Chemical Co. in Buffalo Grove, Ill., says, “Two of the most critical parameters to consider when formulating high-performance MWFs are cost and the life-cycle environmental, health and safety characteristics of the formulation. In today’s market, regulatory registration in multiple geographies is often mandatory, and unsatisfactory labeling or the presence of certain impurities such as formaldehyde, phenol, secondary amines and boron can be deal breakers.”
Webb continues, “Equally important is performance. For example, a fluid’s impact on foaming is a key selection criterion as machine sumps and footprints are becoming smaller and pumping rates and pressures are increasing. In addition, resistance to microbial degradation has become more important than ever, as fluid producers are formulating to eliminate registered biocides. Compatibility with a wide range of aluminum alloys, while avoiding phosphorus- and silicone-based inhibitors, also is becoming more important.”
Webb stresses that multifunctionality is becoming crucial due to the ever-growing list of complex needs formulators must assess in preparing MWFs. She says, “Formulators are no longer looking for one product to meet each performance criteria but, rather, products that meet multiple performance objectives, including labeling requirements.”
STLE-member Dr. Michael Stapels, technical manager for Kao Chemicals GmbH in Emmerich, Germany, stresses that fluid longevity is his most important key parameter, particularly with regard to robustness in the presence of bacteria, fungus and hard water. He says, “Foam control, along with workers’ health and environmental issues, will also play more important roles in the future. The latter issue is consistent with the more active role of regulatory authorities in influencing the additives that can be used in MWFs.”
STLE-member Dr. Ernest Galgoci, technology director for Münzing in Bloomfield, N.J., focused his comments on the use of defoamers. He says, “Key performance attributes include concentrate compatibility, initial and persistent defoaming, filterability and washability/paintability. As the end-use environments become more demanding (e.g., higher pressures, tougher filtration), these properties must be maintained or improved.”
ADDITIVES TYPES THAT WILL CHANGE
The MWF industry is facing the possibility that some additives widely used during the past 50-60 years may be restricted in the near future. Two examples that come to mind are the formaldehyde-condensate biocide, hexahydro-1,3,5-tris(2-hydroxyethyl)-s-triazine (HHT) (1) and two widely used chlorinated paraffins (medium- and long-chain chlorinated paraffins) (2).
STLE Fellow, Dr. Fred Passman, president of Biodeterioration Control Associates, Inc., in Princeton, N.J., cites a concern about the number of biocides that will be available to MWF formulators in the future. He says, “The number of biocides with MWFs among their end-use cites (approved applications) has shrunk dramatically in the U.S. over the past decade. ASTM E2169, Practice for Selecting Antimicrobial Pesticides for Use in Water-Miscible Metalworking Fluids, includes a table that lists all the biocide-active substances that are approved for use in MWFs (3). In 2001 the table listed 57 active substances. That number was down to 53 in 2012 and is currently at 48. At least seven of the active substances that remain on the list as of 2016 are formaldehyde-condensates that are likely to be removed from the table between now and the next five-year review of E2169 if regulatory pressure does not abate. The options are even more limited in Europe, where there are currently only 27 dossiers for biocidal substances to be used in MWFs.”
Consolidation in the biocide industry and the lack of new antimicrobial pesticide development also are contributing to this problem. Passman believes the lack of return on investment is a leading factor in reducing biocide options for formulators in the future. He says, “The global MWF biocide market is approximately $200 million. The current cost to complete toxicological testing needed to obtain a new pesticide registration in the U.S. is estimated to be between $250,000 and $500,000. Testing for EU (European Union) Biocidal Products Regulation dossiers is estimated to cost between $1 million and $5 million. Based on a return on investment analysis, no new antimicrobials are likely to ever again be developed specifically for use in MWFs. Instead, companies are looking at formulated blends of active substances, formulation of active substances with adjuvants or both.”
MacNeil believes that the types of chlorinated paraffins and phosphate esters currently offered to the marketplace may soon change. He says, “The concern expressed in the U.S. by the EPA about the persistence and bioaccumulation of medium- and long-chain chlorinated paraffins may lead to their restriction at some point in the near future. The problem with phosphate esters is due in part to the belief that the use of phosphorus additives contributed to the development of an algae bloom in Lake Erie in 2014 (4). This event may lead to a Great Lakes initiative involving both Canada and the U.S. that significantly restricts the discharge of phosphorus-based additives.”
One way end-users may comply is by minimizing the use of products containing phosphorus-based additives at their facilities near the Great Lakes.
Stapels indicates that water-dilutable MWF formulations will switch from anionic to nonionic emulsifiers. He says, “The trend will move more to nonionic emulsifier-based formulations where the formulator can match high performance with compliance with registration issues and minimization of labeling on safety data sheets. Nonionic emulsifiers (fatty alcohol alkoxylates) and their anionic derivatives (ethercarboxylates) can offer a greater flexibility to meet future requirements.”
An example of the superior performance of nonionic emulsifiers combined with ethercarboxylates is shown in Figure 1. Anionic and nonionic emulsifier-based semisynthetic formulations (see Table 2) are evaluated for foam height over time at water hardness levels ranging from <100 ppm to 250 ppm.
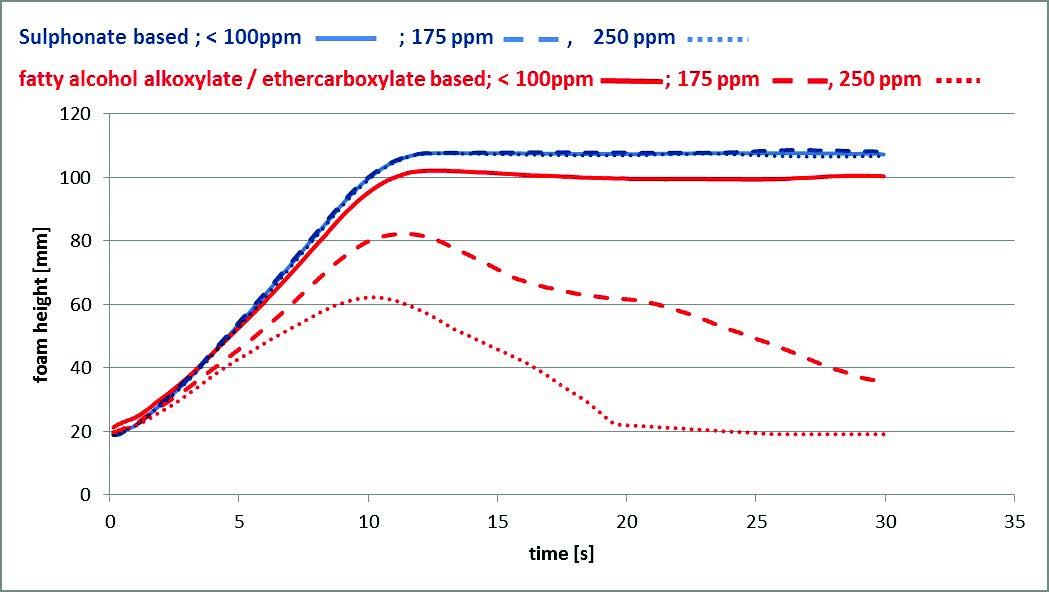
Figure 1. Foam control improves for a semisynthetic fluid based on a fatty alcohol alkoxylate and an ethercarboxylate when the water hardness increases above 175 pm. In contrast, an anionic-based semisynthetic fluid displays comparable foam generation at all water hardness levels tested. (Figure courtesy of Kao Chemicals GmbH.)
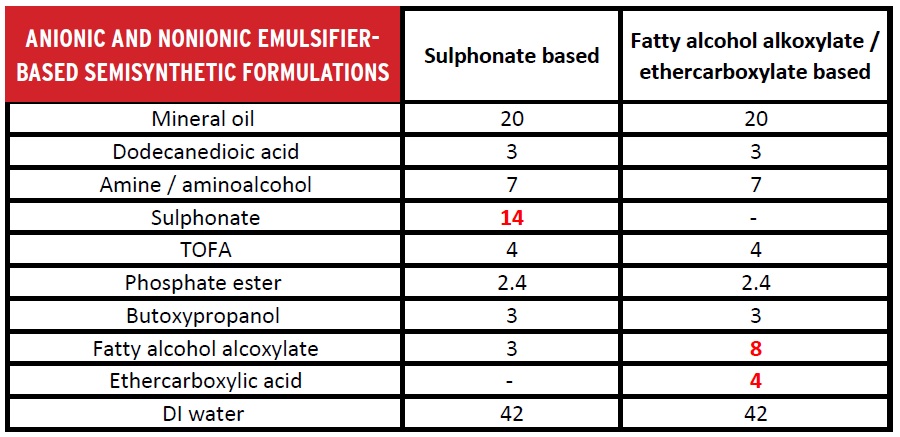
Table 2. The semisynthetic MWF formulations evaluated for foaming under a variety of water hardness conditions are listed (for results, see Figure 1). (Table courtesy of Kao Chemicals GmbH.)
Stapels says, “The anionic- (sulfonate) based semisynthetic displays comparable foam generation at all of the water hardness levels evaluated. In contrast, foam declines for the nonionic/ethercarboxylate-based semisynthetic over time once the hardness level increases above 175 ppm because foam is reduced due to the formation of dispersed calcium salts of the ethercarboxylates.”
Jarvis feels that regulatory trends will be the key market driver in prompting changes in the additive types offered to the formulator. Specifically, Jarvis comments, “Substances with chemical registration concerns that are restricted or banned in particular territories will need to be replaced. Biocides, boron compounds and chlorinated paraffins are examples of MWF components that have come under recent scrutiny in various geographies.”
Two other additive components, sulfonates and amides, also are likely candidates for replacement in consideration of certain performance concerns. Jarvis explains, “These two components function as good food sources for bacteria, thus making fluids formulated with them particularly vulnerable to microbial contamination. Additionally, they have a tendency of contributing to the generation of excessive foam.”
Jarvis also admits that state-of-the-art, high-performance replacement additives are likely to be more expensive, but they will offer a better value for the benefits they ultimately deliver.
Defoamers are a class of additives that will continue to be frequently modified to meet evolving demands of new and existing MWFs, according to Galgoci. “Even though advanced defoamer technology that provides significant improvements in the key defoamer performance attributes has recently been introduced, further innovations will be needed to meet evolving requirements,” he says.
Webb agrees that regulatory restrictions will force the movement away from specific additive types. She says, “A trend we expect to continue is increased regulatory and end-user restrictions around the use of biocides, especially formaldehyde-condensates, chlorinated paraffins, secondary amines and boric acid.”
One other aspect that Webb points out is formulators will need to continue to work with ingredients that have more environmentally responsible profiles. She says, “Formulators are and will be looking for products that do not readily bioaccumulate. For example, phosphorus-based additives, used in fluids that can be discharged into inland waterways and lakes, may be more restricted due to the potential for eutrophication.”
Kirsch also is in agreement that the biocides and chlorinated paraffins currently available to the formulator will undergo the most change over the next few years. He adds, “We also believe that changes in the base oil market will lead formulators to switch from naphthenics to paraffinic base oils that are gradually becoming more available.”
NEW ADDITIVE OPTIONS
Five of the additive types where new options will need to be available in the near future are alternatives to medium- and long-chain chlorinated paraffins, biocides, emulsifiers, defoamers and corrosion inhibitors. MacNeil says, “In our view, the best alternative to medium- and long-chain chlorinated paraffins is very long-chain chlorinated paraffins.” Very long-chain chlorinated paraffins have a chain length that ranges between C21 and C30. Further details on the performance characteristics of very long-chain chlorinated paraffins can be found in a recent article (2).
Jarvis adds, “We believe that polymeric ester lubricants also are viable alternatives to chlorinated paraffins.”
Kirsch says, “Chlorinated paraffins have a variety of replacement options that include overbased sulfonates, sulfurized additives, phosphorus additives and very long-chain chlorinated paraffins chemistries. Many of these work in synergy with each other.”
With biocide options in decline, formulators might need to turn more to bioresistant performance additives. Passman says, “A growing number of bioresistant performance additives has been developed and adopted by MWF formulators over the past 15-20 years. Several complex amine products appear to have good bioresistance properties but no apparent biocidal performance. In contrast, there are molecules being marketed as bioresistant performance additives, even though the only demonstrable performance is biocide activity. For formulators using the latter chemicals and end-users using MWF containing chemicals that are actually unregistered biocides, it is caveat emptor. If personnel who are exposed to MWFs develop health issues, use of unregistered biocides might turn out to be a critical issue in litigating claims made by affected workers. It will be interesting to see how this plays out in the future as more formulators claim their MWFs are biocide-free but bioresistant.”
One type of bioresistant performance additive is long-life amines. Webb says, “Long-life amines are a good way to achieve fluid longevity while working within the lower limits of biocide requirements. The best way to observe the benefits of these amines is to formulate within the specified usage requirements of both the amine and the biocide. While long-life amines can help formulators achieve desired performance benefits with the added benefit of using less biocide, we do not recommend formulating biocides below manufacturers’ recommended use levels. Not only does under-dosing give microbial organisms the opportunity to acclimate to the biocide—thus rendering it in ineffective against current and future microbial attack—it also prevents the long-life amine from functioning at its full potential. Combinations of long-life amines and biocides often provide better cost and performance results compared to individual additives that are used separately.”
Long-life amines exhibit multifunctional properties enabling the fluid to display such beneficial characteristics as improved corrosion, aluminum staining, pH stability, cobalt leaching and lubricity. Webb say, “Figure 2 shows a study involving two similar semisynthetic formulations (containing 20% naphthenic oil) with the biocide 1,2-benzoisothiazolin-3-one (BIT). We compared an amine package containing 3-amino-4-octanol (3A4O) and a combination of 2-aminobutanol (AB) and 2-amino-2-ethyl-1,3-propanediol (AEPD) versus a combination of monoethanolamine (MEA) and triethanolamine (TEA). In addition to the benefit of superior microbial control, we found that the semisynthetic formulated with 3A4O and AB/AEPD also display superior corrosion control, pH stability and lubricity.”

Figure 2. A semisynthetic fluid containing an amine mixture with 3-amino-4-octanol (3A4O) and a combination of 2-aminobutanol (AB) and 2-amino-2-ethyl-1,3-propanediol (AEPD) displays superior microbial control, corrosion control, pH stability and lubricity compared to the same semisynthetic formulated with a combination of MEA and TEA. (Figure courtesy of ANGUS Chemical Co.)
The growing possibility that MWF formulators operating in the developed world may need to rely on non-formaldehyde-condensate biocides leads to the question about how best to work with these types of biocides. Passman responds, “Past testing by professor Ed Bennett and his students using the protocol that would become the basis for the main ASTM bioresistance test (ASTM E2275) (5) showed that the number of different MWF formulations in which microbicides that were not formaldehyde-condensates were effective was dramatically more limited than the number in which formaldehyde-condensate microbicides were effective. These results mean that it is more important now than in the past to conduct rigorous lab and field trials with every MWF formulation that includes a non-formaldehyde-condensate biocide.”
Passman continues, “Formulating with multiple active biocides (or active substances plus adjuvants) will become increasingly important. In the future, MWF formulators may need to formulate with components that are compatible with the biocide(s) used instead of the opposite approach, which has been done historically.”
Passman also points out that there may be renewed interest in the use of synthetic MWFs because there are already numerous examples that are quite bioresistant.
Webb indicates that long-life amines have been successfully used with many of the non-formaldehyde-condensate biocides currently available. She says, “While every formulation is different, we have had success with various biocides, such as BIT, morpholine/dimorpholine derivative, ortho-phenylphenol, n-butyl-1,2-benzoisothiazolin-3-one, sodium pyrithione and quaternary amine biocides.”
The switch to nonionic emulsifiers from anionic emulsifiers will enable the formulator to operate in a wider area as shown in the foam versus fluid life-time/water-hardness graph in Figure 3. Stapels says, “At water hardness levels less than 100 ppm, defoamers are needed in both sulfonate-based anionic emulsifier and fatty alcohol ethoxylate-based nonionic emulsifier formulations. With increasing water hardness over the lifetime of the MWF, defoaming action will start with the generation of calcium/magnesium soaps. Good foam control can be established if a good soap disperser (such as an ethercarboxylate) is used. At even higher water hardness levels, fluid stability becomes more of a factor as anionic emulsifiers will tend to precipitate out leading to the splitting of the MWF emulsion compared to formulations using nonionic emulsifiers, which are more stable.”
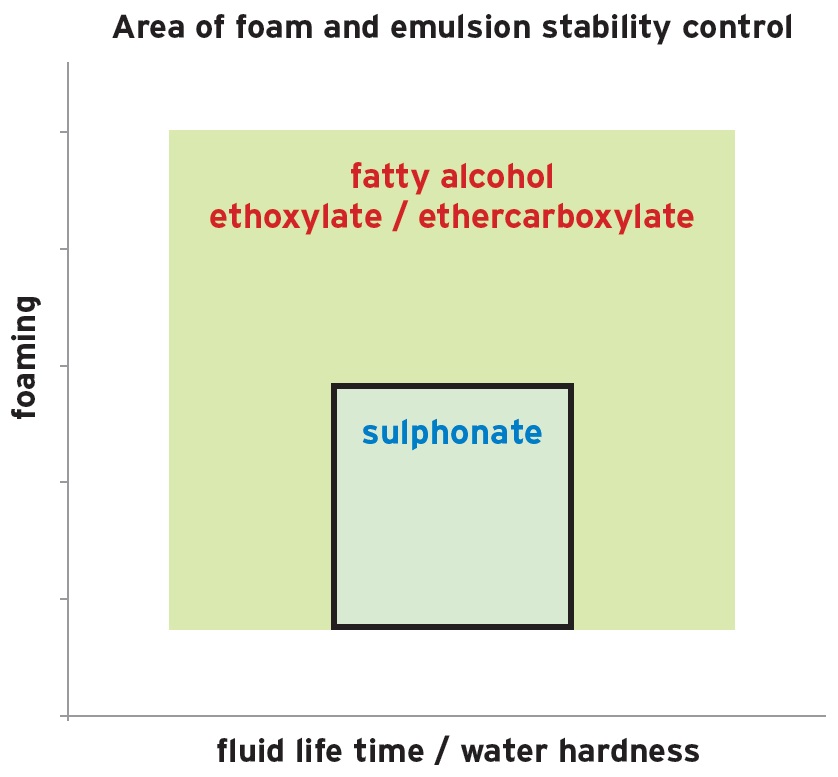
Figure 3. This graph of foam versus fluid life time/water hardness shows that fluids containing nonionic emulsifiers will be more effective over a wider operating range that fluids formulated with anionic emulsifiers. (Figure courtesy of Kao Chemicals GmbH.)
For the future, Stapels believes that formulators will seek to work with emulsifiers that enable them to minimize regulatory labels on safety data sheets. He says, “Fatty alcohol ethoxylates such as oleyl alcohol ethoxylated with two to five moles of ethylene oxide are known to work very well but may face regulatory labeling that could cause difficulties for formulators. A good option is to switch to fatty alcohol alkoxylates based on propylene oxide-ethylene oxide (POEO) that can be designed with minimum labeling on safety data sheets. Ethercarboxylates also should be examined because special grades neutralized with amines or inorganic bases do not require any labeling up to treat rates between 10% and 20% in the MWF concentrate.”
Jarvis also proposes an alternative for replacing sulfonate-based anionic emulsifiers. He says, “Polymeric esters have been found to not only work well in replacing sulfonates but also as an alternative for amides.”
The main defoamer chemistry used currently is based on siloxane. Galgoci believes that there is a market perception that all siloxane-based defoamers will cause paint defects and filtration issues. He says, “Although the view that siloxane-containing defoamers will cause problems is mostly true for those defoamers based on silicone, there are proven siloxane chemistries available that do not have these negative characteristics. The current non-silicone alternatives are based on mineral oil and/or polyether glycols, but these chemistries are intrinsically inferior to siloxanes in defoaming performance. Therefore, there is an opportunity to develop improved non-silicone offerings because only products with limited effectiveness exist at this time.”
Galgoci indicates that siloxane defoamer technology is available that does not adversely affect downstream processes such as coatings. He says, “We have evaluated the paintability of the new technology (NT) products that differ based on their carrier fluid. The results indicate that these defoamers do not generate any defects in coatings as shown in Figure 4.”
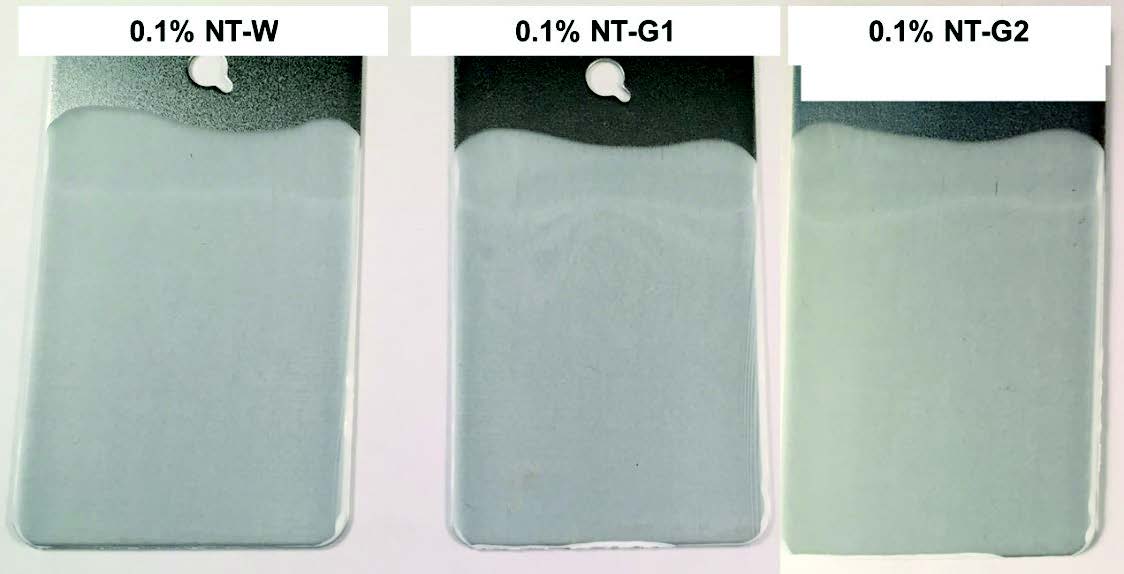
Figure 4. No defects are seen in steel panels that were treated with semisynthetic fluids containing 0.1% of each of the three NT defoamers in the concentrate and diluted to 5% in deionized water prior to painting. (Figure courtesy of Münzing.)
The three new defoamers are designated here as NT-W, NT-G1 and NT-G2. NT-W is water-based while NT-G1 and NT-G2 are based on two different polyglycols. Test samples were prepared by treating the three NT defoamers at 0.1% in a semisynthetic MWF concentrate followed by dilution to 5% in deionized water.
Steel panels were submerged in the three diluted MWFs for one minute followed by controlled rinsing of the panels with tap water, drying at 50 C, application of a white primer using a drawdown bar, air drying the coatings and evaluating for defects.
In contrast, polydimethylsiloxane (silicone) defoamers produce many defects as shown in Figure 5. Galgoci says, “We evaluated silicone-based defoamers as a 100% active material and as a 10% emulsion in water to show that these two defoamers will readily produce defects on painted steel panels.”
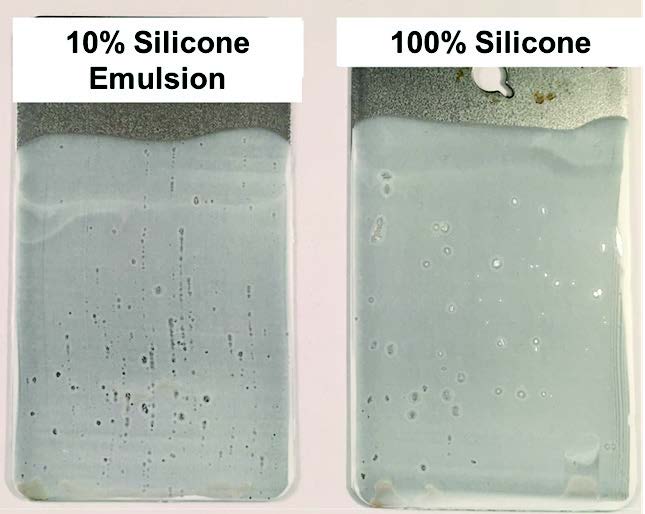
Figure 5. Defects are seen in steel panels treated with silicone-based defoamers as a 100% active material on the right and as a 10% emulsion in water on the left prior to painting. (Figure courtesy of Münzing.)
A cylinder-recirculation test was used to evaluate the efficacy of the NT defoamers. Galgoci says, “We recirculated the MWFs containing the NT defoamers for a four-hour period and evaluated the level of foam produced. An MWF with no defoamer (blank) and with a control defoamer were used as references. Both NT-G products showed superior performance at one-sixth of the use level of the control defoamer.” A graph of the data is shown in Figure 6.
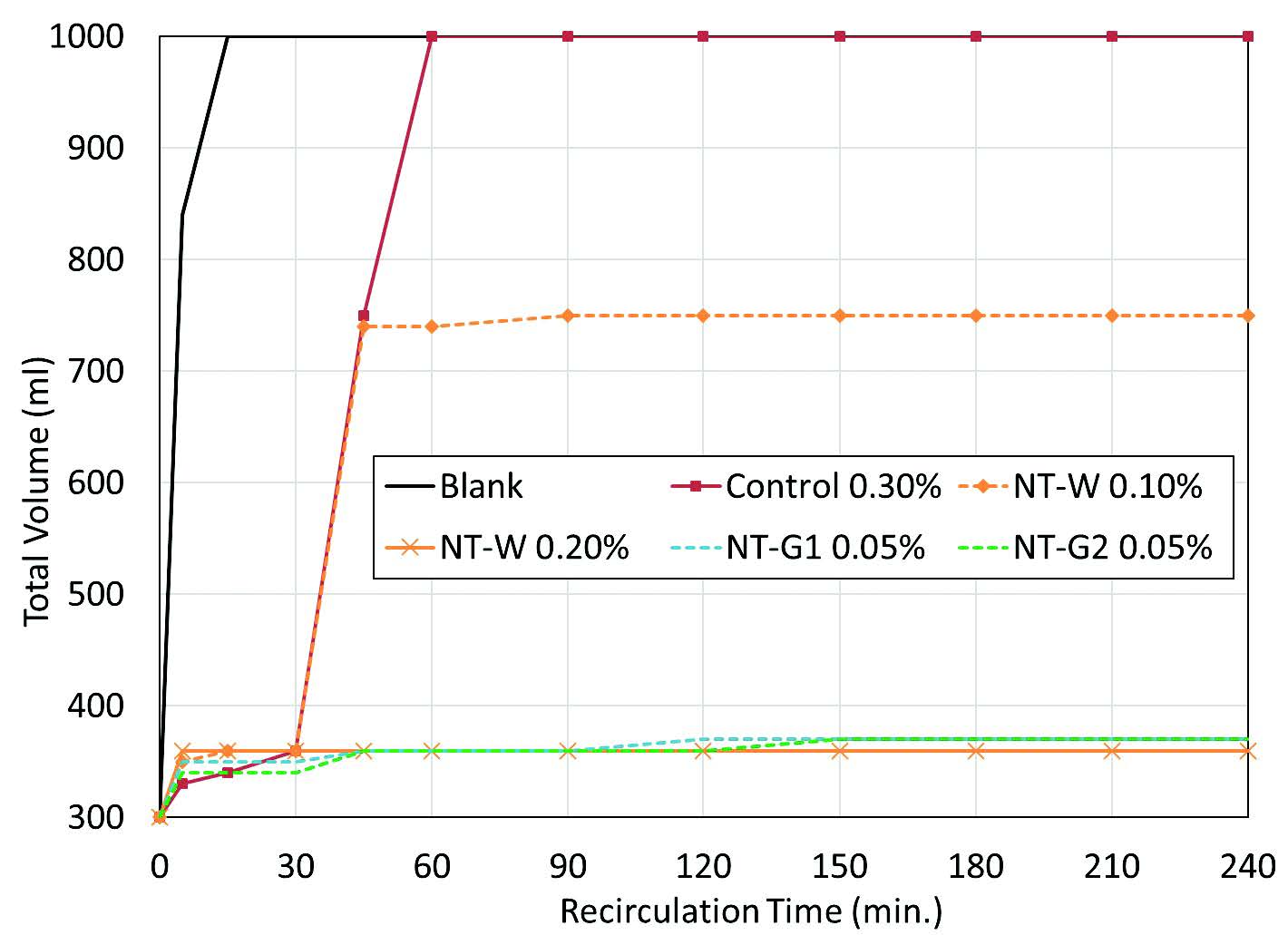
Figure 6. Results from a four-hour cylinder-recirculation test are shown in the total volume versus recirculation time graph. Superior performance is seen with MWFs formulated with the NT-G products at one-sixth the treat rate of the control defoamer. (Figure courtesy of Münzing.)
A similar test procedure was used to evaluate the compatibility of the defoamers with a nylon filter (30-micron pore size) that was placed inline as the semisynthetic MWFs were recirculated. The test was conducted for two hours or until a total volume (fluid + foam) of 1,000 mls was reached.
Galgoci says, “The NT-W defoamer demonstrated excellent compatibility with the filter and superior defoaming performance. In contrast, the conventional defoamers did not perform as well due in part to incompatibility with the filter.” The results are summarized in Figure 7.
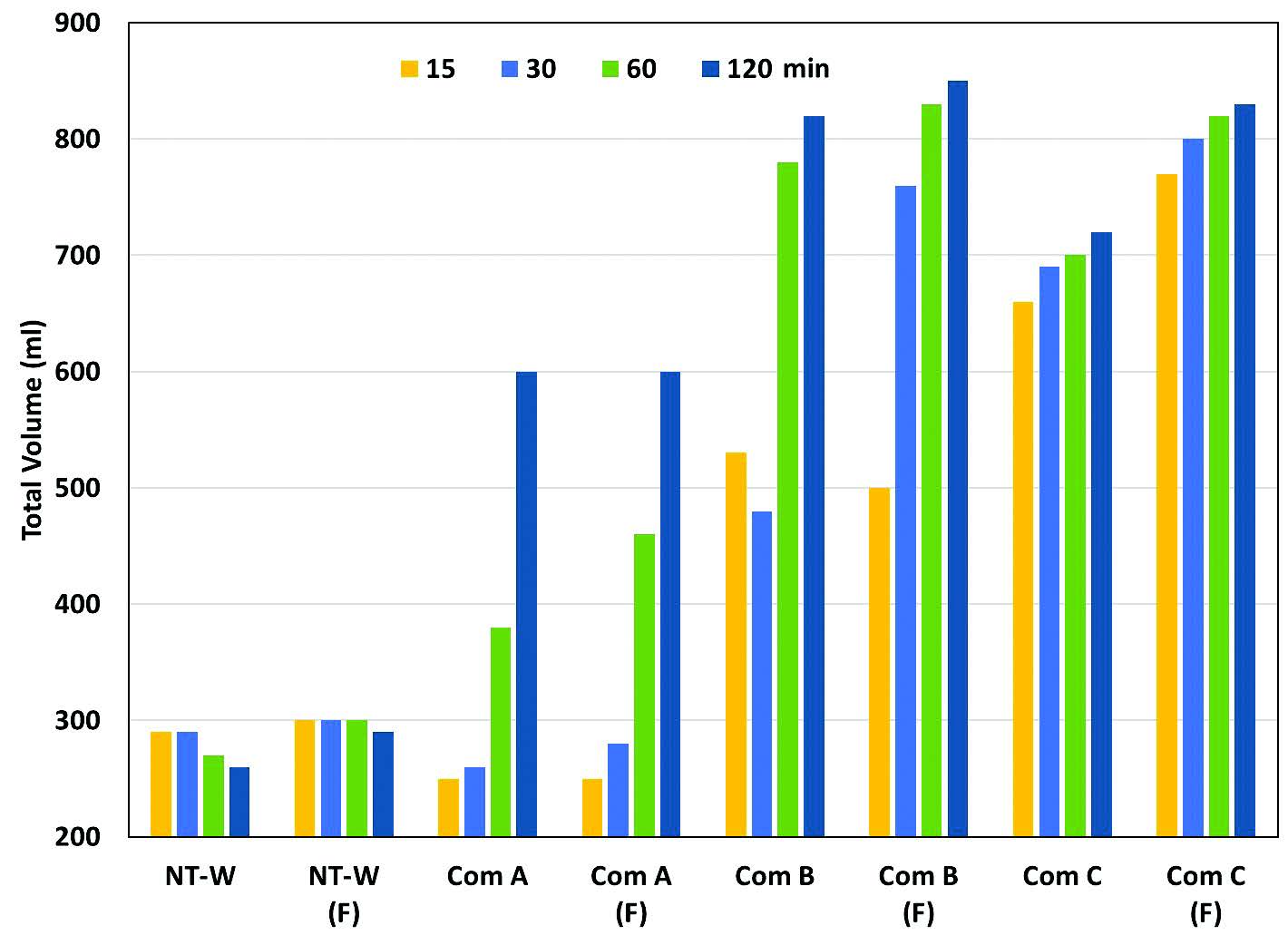
Figure 7. The effect of a nylon filter (30-micron pore size) on the performance of four defoamers used at a 0.25% treat rate in a semisynthetic fluid concentrate further diluted to 5% in deionized water is shown in the chart. The NT-W defoamer displays excellent compatibility as the total volume (fluid + foam) produced over two hours is virtually identical no matter if the fluid is filtered (data has an [F] underneath) or not filtered. Conventional defoamers show inferior performance when filtered. (Figure courtesy of Münzing.)
The sudden phase out in 2016 of one of the premium corrosion inhibitors used in water-based MWFs has led formulators to identify alternatives. While other dibasic acids are being used, there also may be a reason to work with other amines besides MEA and TEA.
Webb says, “We evaluated a series of dibasic and monobasic acids with a combination of AB/AEPD and compared cast iron chip test results with MEA. The results shown in Figure 8 indicate that the AB/AEPD demonstrates better performance. We also found additional benefits when the AB/AEPD acid salt is supplemented with 3A4O.”
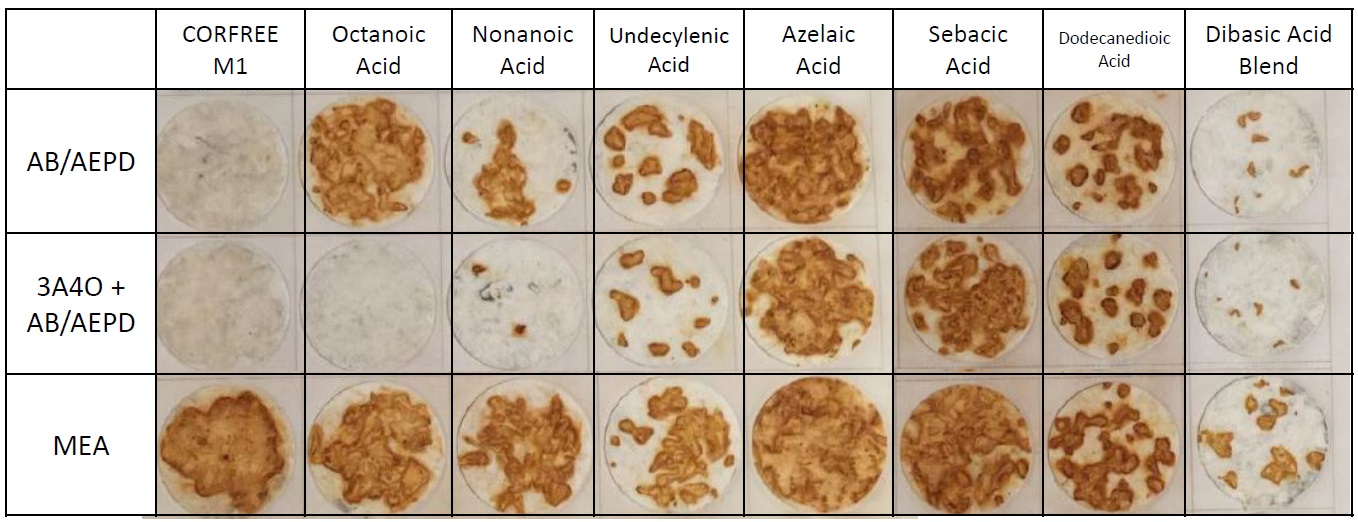
Figure 8. Cast iron chip test results are shown for a series of dibasic and monobasic acids neutralized with a blend of 2-aminobutanol (AB) and 2-amino-2-ethyl-1,3-propanediol (AEPD), supplemented with 3-amino-4-butanol (3A4O) and compared to MEA. Superior performance is seen when 3A4O is combined with AB/AEPD. (Figure courtesy of ANGUS Chemical Co.)
Boric acid-based compounds, which have come under recent regulatory pressure in the EU, are widely used in ferrous corrosion inhibitors. Jarvis says, “There are now boron free options that demonstrate comparable efficacy.”
MACHINING OF NEW ALLOYS—CGI
Commercialization of new alloys such as compacted graphite iron (CGI) is leading formulators to look to additive suppliers for new options to assist them with developing suitable MWFs. Kirsch says, “Finding additives to facilitate CGI machining at economical speeds and feeds still proves somewhat elusive. There also are growing markets for forming of new steels and other metals, and specialty additives may play a major role in facilitating the increasing use of these new alloys.”
Jarvis sees the value in using laboratory-based testing to determine if fluids containing new additives will be effective in machining CGI and other new alloys. He says, “The development of laboratory-based testing methodologies that are relevant to and can be correlated with real-world performance is required.”
FORMULATOR PERSPECTIVE
Two representatives from MWF formulators were asked to comment on what challenges they face in preparing MWFs, where performance deficiencies are seen and what additive types need to be upgraded to help with overcoming the deficiencies.
STLE-member Gary Andrews, technical director for QualiChem, Inc., in Salem, Va., focuses on the compromises that need to be made in developing global formulations. He says, “Our biggest challenge is developing a fluid that will meet the regulatory requirements for as many regions and countries as possible. GHS has made this more difficult.”
Steve Thomas, senior research chemist for Quaker Chemical Corp. in Conshohocken, Pa., focuses on minimizing microbial contamination, durability and good long-term control of foam as three areas that are challenging to deal with in developing products. He says, “There are a couple of aspects to the microbiological control issue that makes it difficult; the customer’s expectations and requirements have frequently changed and government regulations have also changed. From the customer perspective, the MWF is expected to have the ability to control microbial growth built into the formulation and not rely on post-add type treatments with biocides.”
Thomas continues, “An added challenge is that many customers are looking at metalworking products more critically than in the past. Some customers now require the metalworking coolant to provide resistance against mycobacteria, which is a type that behaves differently from the gram-negative types of bacteria (i.e. Pseudomonas). The fact that mycobacteria is not detectable by the commonly used dip slides requires the metalworking formulating staff to use more sophisticated and time-consuming detection methods. The differences between behavior of gram negative types versus mycobacteria affect the requirements to the formulation; each type may require different raw materials and biocides to inhibit growth.”
Thomas expresses concern that with these added challenges the formulator has fewer raw materials to use in finding acceptable solutions. He says, “During the past years, the number of acceptable biocide/biostatic materials has been reduced. Many metalworking customers also are now restricting the use of the following materials: formaldehyde-condensate biocides, phenolic biocides and certain amines (i.e., diethanolamine, dicyclohexylamine and monoethanolamine).”
Thomas feels there is a need to assist formulators with finding better ways to develop products with good microbiological control. He says, “Resistance to microbial growth can only be achieved by increasing the operating concentration of the MWF. That change, though, can lead to other performance problems such as foam and also makes the machining process more costly to the end-user.”
This comment by Thomas leads directly to his request for more additives that help control microbiological growth that are accepted by the EPA and the end-user.
In trying to develop MWFs that are very durable, Thomas indicates that the goal is to perform well despite wide differences in water quality. Specifically, the challenge is to maintain good fluid cleanliness under a range of water conditions. The critical aspect of coolant cleanliness is the absence of hard water soaps (soap scum) in the coolant. The challenge to the formulator is providing a formulation that runs with a minimal amount of hard water soaps, even under a wide range of high water hardness. Most end-users use tap water rather than a softened water to replenish the water lost via evaporation. This practice will slowly build up the level of hard water ion regardless of the initial water hardness. Coolant systems that start below 100 ppm CaCO3 (calcium carbonate) can eventually reach levels of 500-1,000 ppm CaCO3. He says, “Coolant cleanliness has become more difficult due to the recent trend of end-users trying to extend the life of an MWF system for several years between a dump and re-charge.”
Andrews indicates that there is another factor to consider in preparing durable MWFs. He says, “Formulating bacterially robust fluids, which also are safe for exposure to workers, is challenging. Fluids that present a harsher environment for bacteria also tend to be harsher on worker’s skin.”
Cleaner-running metalworking coolants, with the absence of hard water soaps, can be a greater challenge for the formulator because they may be foamier. In many instances, a better strategy for maintaining foam control is needed, one that places more importance on the formulation, rather than the antifoam additive, according to Thomas.
“It is generally known that the effectiveness of antifoam ingredients diminishes with prolonged use by the end-user,” Thomas says. “When conducting laboratory testing on new formulations with the antifoam component removed, a more effective product can be developed. A common approach is to use specific levels of fatty acids that react with hard water to form foam-suppressing calcium soaps. However, the challenge to the formulator is to balance the improvements in foam control without producing excessive amounts of insoluble hard water soaps. The risk is that these soaps will drag out a significant amount of the lubricity components (fatty esters and mineral oil) resulting in higher depletion/usage, increased frequency of product additions needed to maintain concentration and higher operating costs.”
Andrews also sees the need for further improvement in the antifoam and defoamer technology available to the formulator. He says, “With more machines and applications moving to higher and higher coolant delivery pressures, development of better additives for foam control would be welcomed.”
When asked about the effectiveness of current antifoams/defoamers, Andrews says, “One of the largest shortcomings in my opinion is stability in the neat MWF and persistence in field use, especially when small micron filtration is concerned. Higher coolant pressures are leaving defoamers that were once industry standards now largely insufficient. Any raw material supplier that can develop a defoamer to meet these challenges should find significant interest from formulators.”
Thomas provides his perspective on antifoams/defoamers: “The effectiveness of individual antifoams varies widely, and there are some good products commercially available. Generally, the selection of an antifoam is done by comparative foam testing. The formulator often does the comparative testing while taking into consideration of the cost contribution of the antifoam at the required dosage rate.”
Thomas adds, “A higher level type of evaluation that is sometimes done is to evaluate the compatibility/stability of the antifoam component in the concentrate and diluted fluid. Many antifoam materials will slowly settle to the bottom of an MWF and some amount of effectiveness can be lost. The antifoam also can lose effectiveness after aging due to changes in how well the material is dispersed; it can sometime degrade to the appearance of a flocculated suspension. The task of the formulator is to do evaluations that can provide a good prediction of long-term stability and loss of effectiveness over time.”
Andrews does not see cost-equivalent chlorinated paraffin replacements. “It is generally up to the formulator to find those combinations of boundary and extreme pressure (EP) lubricant additives that can come close to matching the performance of chlorinated paraffins in most applications,” he says.
As to what Andrews is looking for, “An additive that can actually match the performance of chlorinated paraffins in both metal cutting and metal forming applications at an equivalent cost. Often great claims are made on a new additive only to find out that in reality, the product does not perform as advertised. Chlorinated paraffins provide exceptional EP performance for the cost. This is the reason why they are so difficult to replace without having a major impact on finished formulation cost.”
In answering whether formulators have the needed raw materials to develop products that can be used in machining applications with new alloys such as CGI, Thomas says, “The move to new alloys is a big factor, and the formulator must examine each case for their effects on such things as lubrication, staining and chemical attack. The currently available additives appear to be sufficient if the formulator thoroughly examines their behavior.”
END-USER PERSPECTIVE
Miles Free, director of industry for research and technology for the Precision Machined Parts Association in Brecksville, Ohio, provides some perspective on the challenging issues facing end-users who are working with MWFs. He says, “The one issue that no one is paying attention to is that MWFs are designed for machines, when formulators should be designing them for people. MWFs placed in machines are very intimate, cosmetic products. The MWF industry fails to realize that they are in the cosmetics business, and machine oils/coolants/fluids used have a greater share of skin than Proctor and Gamble, Unilever and Colgate-Palmolive combined. What biocides and formulations would the MWF industry be using if it recognized that it is in the cosmetics business and not the machining fluid business?”
A number of additional issues also are faced by end-users. Free says, “Rust and corrosion used to be big issues, but now seal deterioration, polymer compatibility and customer requirements that ban certain ingredients from being applied can further complicate machine shops’ decision making. Replacement and disposal of MWFs can lead to additional costs and regulatory issues. Clean out costs when replacing fluids across a fleet of machines can be equal to 3%-4% of a machine shop’s annual production schedule when considering lost production time, disposal and clean-out costs. This puts a considerable amount of pressure on the end-user decision maker who may lose two full days of production to switch all of the machines in a shop to a new fluid because of new mandates or requirements that were unexpected.”
The main performance deficiency seen by Free is the inability of end-users to effectively minimize microbial contamination. He says, “Most end-users fail to establish/maintain biological control over their fluid systems. There is a growing perception among end-users that the bacteria and fungi present are becoming more resistant to the biocides that are still available with the EPA continuing to restrict the amount and types in use.”
Free continues, “Failure to get the machine fully clean before adding a new MWF condemns the new product to a much more abbreviated operating life. Mold and fungus are the most difficult contaminants to clean. End-users need to use steam cleaning in heavily contaminated systems. This can happen over a weekend. There is uncertainty about whether machine shops and the MWF industry understand that MWF systems are huge living ecosystems. It can be considered that MWF systems are huge aquariums with the end-users not being able to select the fish or the plants.”
Free identifies two applications where suitable MWFs are not available and need to be upgraded. He says, “Machining magnesium and grinding carbide are two operations where fluid options are limited. Cobalt leaching also can be a problem in applications using carbide tooling.”
Free feels the MWF industry needs to better balance improvements in lubricity with improvements in cooling. He says, “Unfortunately this type of problem is difficult to overcome because the machine shop has to resolve too many factors including tool material, coating, workpiece material, geometry, fluid access and other process parameters.”
New alloys such as CGI can be difficult to machine, but the larger problem from Free’s standpoint is the growing complexity machine shops face in making metal parts. He says, “The landscape for machining is changing at an unprecedented rate due to regulations, applications, material selection, limitations on materials and additives, end-user requirements and process and system constraints. The complexity faced with these new developments and regulations does not make it any easier to operate a machine shop.”
GHS, REACH AND TSCA
Changes in regulations may represent the biggest single challenge in formulating MWFs in the 21st Century. The significant impact of GHS and the pending completion of REACH registration by June 2018 are reducing the number of additives available for the formulator to use in preparing new products.
The additive representatives interviewed were asked about how these two regulations will impact what raw material options are available to the formulator. Kirsch says, “GHS tends to amplify the hazard statements for previously existing materials. This may not necessarily lower material availability, but it will limit the attractiveness of certain additives previously seen as less hazardous. Formulators often wonder what has changed with a specific raw material when the actual change is not based on any chemical changes to a product but, rather, with changes in regulatory-related interpretations of chemical data.”
Jarvis says, “With respect to GHS and product classification, formulators and end-users are becoming increasingly sensitive to labeling requirements and expectations. As such, certain components may be less desirable than others in some formulations.”
With regard to EU-REACH, Jarvis sees a similar concern for what raw materials formulators can use, but there are additional issues. He says, “The higher cost and more time-consuming administration of REACH requirements will result in MWF additive suppliers dropping certain products from their portfolios. The consequence of this will be that formulators are left with fewer options available to them.”
STLE-member Karen Harrington, customer technical service specialist, MWF Product Development for Afton Chemical in Bedford Park, Ill., adds, “As companies have fewer substances registered globally, prior to using a substance in a formulation, formulators will have to consider whether a reacted, intermediate substance is properly registered in the markets that they are produced for prior to using them.”
In the EU, Stapels believes that the most feasible way additive supplies will be able to keep developing new products and comply with REACH is to claim the additives as polymers, which remain exempt from registration. He says, “Every raw material used in the EU that is not a polymer faces a high registration cost under REACH, making it difficult to justify future use. In extreme cases, the raw material producer and customers of a specific chemical substance are sharing the registration fees. But developing a new raw material that is not a polymer is extremely risky and expensive.”
Stapels also has concerns with developing new additives for the U.S. He reveals that registration of new raw materials under TSCA is becoming very difficult discouraging raw material suppliers from offering new additives for formulators and says, “The time needed for the EPA to approve a new chemical substance under TSCA is becoming very long. We started the effort to register a new chemical substance more than two years ago and still have not received approval by the end of 2016. This substance has been used successfully in the EU for over 25 years without any incident.”
Galgoci indicates that GHS has led to the reformulation of some defoamers. He says, “Reclassification of some of the raw materials has led us to reformulate with less hazardous alternatives. In some cases, extensive modifications were required, while others needed only minor adjustments. For the more significant revisions, several alternatives were required to ensure performance across the affected set of MWFs.”
Webb believes that GHS is a useful system to compare and contrast the health and environmental hazards of different additives. But REACH may offer fewer raw material options to formulators. She says, “All manufacturers selling products in the EU must now present a minimum data set to meet REACH registration requirements. This can potentially result in fewer products being available for MWFs, as some companies may choose not to invest in the environmental and toxicological data necessary to register a raw material, such as additives sold at low volumes where there is no cost/benefit in obtaining a registration.”
Regulatory drivers will have a significant impact on what options are available to the formulator. It appears that the cost and time needed for complying with regulations will further restrict what raw materials can be used, leaving the formulator with fewer options. Those companies that are able to work with an increasingly shrinking toolbox of raw materials will be best positioned to successfully formulate in the 21st Century.
REFERENCES
1. Passman, F., Canter. N., Rotherham, R., Byers, J. and Eachus, A. (2016), “MWF Biocides Part II,” TLT, 72 (3), pp. 46-57.
2. Canter, N. (2016), “Status of medium- and long-chain chlorinated paraffins,” TLT, 72 (3), pp. 34-44.
3. ASTM E2169-12 (2012). Available at the ASTM Website: www.astm.org.
4. Pelley, Janet (2016), “Taming toxic algal blooms,” CEN, 94 (12), pp. 21-23.
5. ASTM E2275-14 (2014). Available at the ASTM Website: www.astm.org.
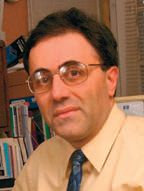
Neil Canter heads his own consulting company, Chemical Solutions, in Willow Grove, Pa. You can reach him at neilcanter@comcast.net.