Special Report: GF-6, PC-11 and dexos1™: New engine oil specifications mean new additive challenges
Dr. Neil Canter, Contributing Editor | TLT Tech Beat September 2015
Additive suppliers will need to develop new additives and formulation approaches to meet specification deadlines.
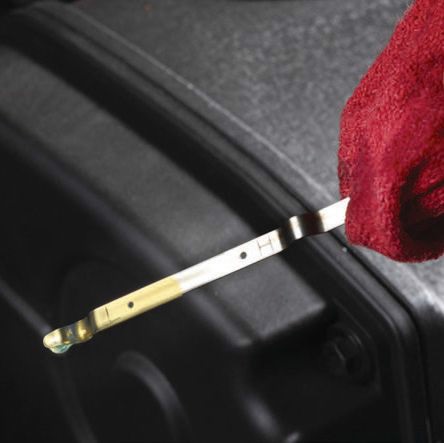
www.canstockphoto.com
KEY CONCEPTS
•
The implementation of two subcategories in the upcoming GF-6 specification for PCMOs means that additive formulations may need to be designed differently for GF-6A and GF-6B.
•
For the new HDEO specification, PC-11, the new lower viscosity oil subcategory, PC-11B represents a significant challenge because of the potential need to incorporate new friction modifiers with more effective antiwear additives.
•
Implementation of the second generation GM specification, dexos1™ prior to GF-6 may require the lubricants industry to reformulate PCMOs again.
THE LUBRICANTS INDUSTRY IS IN THE MIDST OF DEVELOPING PRODUCTS for not one but three new engine oil specifications at the same time. Further complicating the issue—two of the specifications are further organized into specific subcategories.
With passenger car motor oils (PCMOs), the new specification is known as GF-6 (
1). It is further segmented into two subcategories: GF-6A and GF-6B. GF-6A will cover existing engine oil grades while GF-6B will cover new grades with viscosities lower than 0W-20. The impetus for the new grade comes from the request by automotive manufacturers to recommend lower viscosity grades for their vehicles. GF-6B covers engine oil viscosities lower than 0W-20. Recently the Japanese automaker Honda requested two lower viscosity grades (0W-12 and 0W-8) be added to the Engine Oil Viscosity Grade Classification System.
The second engine oil specification, known as PC-11 (
1, 2), is for heavy-duty engine oils (HDEOs). Further segmentation of this engine oil category is made based on backward compatibility. Two subcategories are based on a difference in high-temperature high-shear (HTHS) viscosity rates. The subcategory, PC-11A, will be compatible with the current HDEO category (API CJ-4) and have an HTHS of 3.5 minimum; the second subcategory, PC-11B, is for new lower viscosity engine oils with an HTHS of 2.9-3.2.
At the time of this article’s publication, the first license date for PC-11 will be in December 2016. GF-6 will probably move to a March 2018 first license date.
The third engine oil specification is the second generation GM specification known as dexos1™ that is due to be implemented in September 2016.
Efficiency performance mandates continue to affect the automotive industry. In the U.S. sweeping legislative changes put into effect by the National Highway Traffic Safety Administration (NHTSA) in 2012 require a fleet-wide average of 54.5 mpg (U.S.) by 2025 (
see Figure 1). Fuel economy performance is being raised not just in terms of the level of fuel economy but also in terms of durability over a longer time period. Efficiency is at the forefront of GF-6, PC-11 and GM specifications—three current specification upgrades greatly impacting the industry (
see Figure 2).
Figure 1. Improved fuel efficiency is a key requirement that PCMOs will need to meet in the upcoming GF-6 specification. (Figure courtesy of The Lubrizol Corp.)
Figure 2. The lubricants industry is facing a major challenge in developing products for three specifications where efficiency improvements are required. (Figure courtesy of The Lubrizol Corp.)
The development of these new engine oil specifications means that there are certainly additive challenges that the lubricants industry must meet. Input on how the industry is responding has been obtained from the following companies:
•
Afton Chemical Corp.
•
Chemtura Corp.
•
Chevron Oronite Co.
•
Croda
•
The Dow Chemical Co.
•
Evonik Oil Additives USA
•
Infineum USA LP
•
The Lubrizol Corp.
•
Vanderbilt Chemicals LLC.
GF-6 UPGRADES
The proposed ILSAC GF-6 specification will enable a new level of performance for passenger car engine oils in the era of efficiency. Martin Birze, The Lubrizol Corp.’s regional business manager, passenger car additives in Wickliffe, Ohio, says, “The proposed GF-6 specification is a significant upgrade that addresses the demands of new engine technology. This technology requires higher-performing engine oils to enable efficiency while also delivering the higher fuel economies required by mandated regulations.
“GF-6 is unprecedented in its proposed inclusion of six new engine tests. Four are replacement tests being updated with new hardware, and two are entirely new tests. The specification will push the industry’s approach to engine oil formulation to greater heights.”
STLE-member Kaustav Sinha, global project manager for Chevron Oronite Co. LLC in Bellaire, Texas, overseeing the GF-6 development, provides an overview of the six new engine tests being developed for GF-6.
Says Sinha: “The Sequence IIIH oxidation/deposit and Sequence IVB valve train wear tests will get engines and test procedures developed by two new Original Equipment Manufacturers (OEMs), Chrysler and Toyota, respectively. Ford is refreshing the Sequence V sludge performance test and also developing two brand new tests (low speed pre-ignition (LSPI) and chain wear) for the category. GM is refreshing the Sequence VI fuel economy test.”
STLE Fellow Dr. Simon Tung, global OEM liaison manager for Vanderbilt Chemicals LLC in Norwalk, Conn., says, “In moving beyond GF-5 requirements, GF-6 will incorporate increased fuel economy through the oil change interval, enhanced oil robustness for spark-ignited internal combustion engines, formulations to help minimize the occurrence of low-speed engine pre-ignition and wear protection for various engine components.”
Tung makes two additional important points about the reason for developing GF-6. He says: “Each of the new tests addresses requests by OEMs based upon the needs of modern, high-tech engines. With these new technologies come new requirements of the lubricants that enable them. The new tests also address the increasingly limited availability of older engine parts. Simply put, engines used to run tests under GF-5 are reaching the end of their useful life, and parts are limited or unavailable, necessitating replacement tests to meet new engine requirements.”
Tiffany Murphy, marketing manager for PCMO for Afton Chemical in Richmond, Va., says, “The GF-6 category will again seek to define an engine oil with improved durability characteristics and better fuel economy performance to help equipment manufacturers meet the future EPA CAFE targets.”
STLE-member Dr. Frank DeBlase, Chemtura Fellow-petroleum additives in Middlebury, Conn., has focused his research on novel antiwear agent, antioxidant and friction modifiers. Says DeBlase on the new subcategory GF-6B: “The new lower viscosity GF-6B oil (0W-16 or 5W-16), with a lower high-temperature high-shear (HTHS) viscosity, should deliver improved fuel economy and lower green-house gas emissions but will require additional engine protection. Therefore, new tests are being developed to assess increased fuel economy performance and engine durability. These requirements will be addressed by new lubricant and additive technologies.”
Scott Davis, key account manager–lubricants for Croda in New Castle, Del., stresses the challenge of meeting more rigorous fuel economy requirements. He says, “A key objective of GF-6 is to improve fuel economy versus GF-5. The Sequence VIE fuel economy test replaces the VID with the proposed limits for the newer test being on average about 50% higher.”
STLE-member Ashish Kotnis, senior research scientist for The Dow Chemical Co. in Midland, Mich., offers this analysis of the upgrade for the Sequence IVB valve train test: “The new test includes a more severe duty cycle, which is a highly transient cycle compared to the original test. In addition, the test duration increases from 100 hours to 200 hours, which makes the test more severe from a valve train wear perspective.”
Steve Haffner, North America crankcase market manager for Infineum USA L.P. in Linden, N.J., gives his perspective on GF-6. He says, “The new PCMO specification is being developed to protect the newer hardware being introduced into the field including smaller displacement, direct-injected gasoline engines. These new oils will be expected to deliver enhanced oil robustness and wear protection as well as increased fuel economy throughout the oil change interval.”
ADDITIVE CHALLENGES FOR GF-6A AND GF-6B
At this time there is some disagreement among the respondents about the status of the two GF-6 subcategories and even if there will be two sets of specifications or one.
Murphy says: “The new GF-6B category defines the performance requirements for ultra-low viscosity grades below SAE XW-20 and as such is distinct from GF-6A with no overlap at all. The viscosity grades appropriate to GF-6B will only be recommended by selected OEMs for specific engines and vehicles.
“So the challenge, in a sense, is greatest for the oil marketer to ensure that such oils are clearly identified by consumers and are only used in the appropriate applications. From a development perspective, it is important to ensure that the performance limits defined for GF-6B oils are appropriate to this category and are not simply an extension of GF-6A.”
Haffner raises the point that the industry is unsure if there will be one specification or two subcategories. He says, “The two subcategories may be required to reduce end-user misapplication. The GF-6B specification is currently designed for oils operating at viscosity ranges less than the Xw-20 and these oils will not be back serviceable, so misapplication is a concern for some OEMs.”
DeBlase believes that changes in the treat rate of certain additives and use of more durable base oils arbe needed for GF-6 in general and specifically GF-6B. He states, “The lower viscosity GF-6B oils will likely require more effective friction modifiers and antiwear additives. Maintaining boundary lubrication and wear protection by using more sulfur- and phosphorus-containing metal antiwear and friction modifiers might compromise pollution control devices or generate higher deposits. The preferred choice to mitigate this problem is additional organic friction modifiers and antiwear additives for even greater boundary lubrication while maintaining elastohydrodynamic lubrication.”
DeBlase continues, “The longer drain intervals required in GF-6 will be assisted by more oxidation-resistant base oils such as gas-to-liquid synthetic oils, polyalphaolefins, polyolesters or polyalkylene glycols. Extended drain intervals also will require the use of more or better antioxidants and additives capable of providing sustained boundary lubrication over high mileage intervals.”
Kotnis explains that the challenge in moving to GF-6B is that oils are thinner at higher temperatures, which impacts the film thickness and can result in a faster transition from the elastohydrodynamic lubrication to a mixed lubrication regime. He says, “Special additive technologies are being developed to protect the engines that will use these lower viscosity grade oils. For example, data shown in Figures 3 and 4 show how a Group V co-base stock incorporated into currently used base oils can increase the viscosity index (VI) of the base oils and reduce the friction seen in a commercial 5W-20 engine oil.”
Figure 3. Incorporation of a Group V co-base stock in different base oils leads to an increase in VI independent of the base oil used. (Figure courtesy of The Dow Chemical Co.)
Figure 4. Friction reduction is observed in traction coefficient testing when a Group V co-base stock is added to a commercial 5W-20 engine oil. (Figure courtesy of The Dow Chemical Co.)
Phil Hutchison, Asia Pacific regional technical manager for Evonik Oil Additives in Singapore, offers this analysis on the role of VI improvers: “The real choice affecting VI improver selection will be deciding the contribution the oil marketer can realize from an improvement in fuel economy. Careful selection of the VI improver, such as the use of a comb polymer, can reduce viscosity at intermediate oil temperatures and directly influence fuel economy. The VI improver type should be considered as a formulation tool alongside other additives such as friction modifiers and can be selected to achieve the desired fuel economy performance level.”
The proposed ILSAC GF-6 upgrade encompasses two specifications: GF-6A and GF-6B. The principle difference between the categories concerns viscosity grade and HTHS performance. GF-6A and GF-6B provide the same level of durability performance, but for GF-6B the aim is lower HTHS to deliver further fuel economy benefits.
Ray Calder, Lubrizol’s global business manager, passenger car additives in the U.K., looks at the different lubricant regimes in play in an engine as shown in Figure 5. He says, “Advances in engine hardware technology along with lower viscosity are increasing the need to protect the engine—particularly where metal parts touch during boundary operation. During boundary operation, additives become critical to protecting parts and enhancing performance. The performance of the lubricant in this regime is outside of the influence of viscosity effects, relying on additives to keep parts protected and vehicles efficient. Creating this performance differentiation in the boundary regime through additives brings about a new era of additives science that challenges us to change our perspectives on how we look at the role of additive chemistry in lubricant formulations. Our approach is an innovative technology called Surface Activated Additive Systems (SAAS).”
Figure 5. The trend toward lighter and smaller engines means that new additives must be developed for use in lubricants that will need to operate in the boundary layer. (Figure courtesy of The Lubrizol Corp.)
Tung expresses concerns that excessive engine wear and durability could be found in using low viscosity, GF-6B engine oils. He says, “Lower viscosity grade oil might not be able to have enough oil film thickness to protect engine wear as higher viscosity grade oils. The improvement in fuel economy performance seen with lower viscosity engine oils also may have a negative impact on durability because the oil film is less robust under the most extreme loading and high-temperature conditions encountered with emerging engine technologies. Enhanced fortification of specific additive components or a different formulation shape may be required to deliver the antiwear and durability requirements needed in GF-6B engine oils.”
Davis comments on GF-6A and GF-6B: “There is substantial overlap between GF-6A and GF-6B. Essentially the only difference between the two subcategories is the GF-6B HTHS viscosity is lower.”
Sinha believes that finding the right additive balance is needed for successfully developing engine oils for GF-6A and GF-6B. He says, “Mitigation of low-speed pre-ignition (LSPI) combined with delivering fuel economy, engine cleanliness and wear performance in a cost effective manner will be key to developing additives and products for GF-6A and GF-6B. While GF-6B is primarily driven to provide fuel economy benefits via rheology, wear and deposit performance with these oils will need to be closely monitored to understand and design an appropriate additive system. GF-6B also will drive the need for higher quality base stocks to meet the oxidation and volatility requirements.”
ADDITIVE TRADEOFFS
The lower viscosity present in GF-6B may require additive formulations to be tailored differently for each GF-6 subcategory. Sinha provides an example of how a different approach may be needed to meet the requirements of the Sequence IVB test. He says, “Delivering fuel economy without sacrificing wear protection is key to formulating for both GF-6A and GF-6B. Sequence IVB valve train wear development work has shown differences in bucket lifter wear between a 5W-20 and 0W-16 formulation. Hence, striking the right balance in a cost effective manner will be key.”
Haffner feels that no trade off will be present in formulating for both subcategories. He says, “GF-6B products are not expected to trade off performance versus GF-6A products. We anticipate they will use similar chemistries, but until all tests are defined it is too early to know for sure.”
DeBlase sees things a bit differently, particularly when using molybdenum friction modifiers. He states, “Adding high amounts of molybdenum friction modifiers to GF-6A formulations will create lubricants that have difficulty passing the TEOST 33C deposit test (which is still required for GF-6A). Increasing molybdenum may be the preferred approach for GF-6B oils, with GF-6B having dropped the TEOST 33C requirement. However, there is still a potential for deposit formation in GF-6B that will have to be addressed with other additives such as dispersants, detergents and much higher antioxidant treat rates or newer antioxidant chemistry.”
Kotnis gives examples of potential additive differences between GF-6A and GF-6B. He says, “GF-6B oils might end up using less VI improvers with more advanced Group III, IV and V base stocks compared to GF-6A oils. Since the films formed with the lower viscosity base oils will be thinner, some advances in the antiwear additives like zinc dialkyldithiophosphates (ZDDPs) and boron-containing additives might be required for engine wear protection. Also, since these oils need to have the same weighted piston deposits and viscosity increase in the Sequence IIIH test, they might require improved detergent technology.”
In formulating for GF-6A and GF-6B, Birze contends that managing boundary lubrication is an essential area of focus for additive innovation. He says, “Lighter viscosity lubricants, advanced hardware and changing operating conditions cause a shift toward boundary lubrication. Lubricants in each subcategory will need to pass all the same GF-6 tests. However, with GF-6B, lower viscosities will require unique formulations in order to maintain durability and robustness. The selection and balance of additive chemistry and other components is critical. SAAS technology delivers a thick film of protection—a complex layer of additive technology tailored to the application.”
LSPI AND TIMING CHAIN WEAR TEST
Tung provides background on both new tests for GF-6. He says, “The LSPI test was developed to address issues around gasoline direct injection (GDI) technology that OEMs are utilizing to reach fuel economy goals. LSPI can occur at low engine speed and high loads that are prevalent in GDI and turbocharged gasoline direct injection (TGDI) engines. LSPI is a new issue due to modern powertrain systems and can be difficult to predict. The test also assumes greater importance because most OEMS recently indicated that their next generation engine oil requirements will include an LSPI frequency assessment as well as specifications around turbocharger deposit control.”
Tung continues, “The timing chain wear test is being developed in response to new engine technology. Contaminants from combustion enter the lubricant sump as a result of blow-by and accumulate in the lubricant leading to increased timing chain wear. The test will effectively measure a lubricant’s ability to minimize timing chain wear as it relates to induced wear by the soot-like particles produced by GDI engines.”
One of the proposed tests for the GF-6 specification evaluates an oil’s ability to prevent LSPI, a critical challenge as GDI engines become common. Automakers have mitigated LSPI by introducing additional fuel to the engine at the points where LSPI is likely to occur. The fuel helps cool the cylinder, reducing the likelihood of LSPI. However, Birze is concerned that this approach can reduce performance. He says, “While effective, this method is necessarily counterproductive, as the additional fuel prevents the engine from achieving peak fuel economy. Lubricant formulations can be part of a solution that may alleviate the need for using additional fuel.”
Murphy says, “It is too early to provide a definitive answer about how these two tests will impact the selection of additives for GF-6. But these new tests shift the emphasis of formulation in a different direction to other tests within the GF-6 category, so it will clearly be a challenge for oil formulators to ensure that the holistic performance of future technology platforms with enhanced durability and fuel economy properties will be achieved.”
Kotnis speculates about how formulations might need to be adjusted to meet the LSPI and timing chain wear tests. He says, “One hypothesis for pre-ignition is that some of the particles in dirty oil, like soot, can cause the pre-ignition to occur. A second hypothesis is that lower molecular weight and thus more volatile components in the engine oil can mix with fuel in GDI engines, which can form an ignitable mixture at low temperatures that can produce the knock. To minimize the knock, more purified oil with lower NOACK volatility oil might be needed.”
Kotnis continues, “GDI engines tend to produce more soot, which can impact timing chain wear. There might be advancements in dispersant technology required to keep this soot dispersed to reduce timing chain wear.”
With regard to LSPI, Sinha believes that the right additive balance must be developed. He says, “As noted in Figure 6, the frequency of LSPI can vary depending upon the engine oil formulation. Based on years of R&D work in this area, we understand the formulation levers required to show discrimination between low and high LSPI events. Engine wear upon oil degradation is one phenomenon that has been observed across both the Sequence IVB valve train and chain wear tests. Based on our work, it could either be a combination of all or part of the additive system (dispersant/detergent/antioxidant/antiwear), depending on the outcome of the ongoing test development activities.”
Figure 6. The frequency of LSPI occurring is dependent upon the engine oil formulation. (Figure courtesy of Chevron Oronite Co. LLC.)
Haffner feels that the two tests can potentially have a large impact on additive selection. He says, “LSPI is stochastic (as GM has termed it), occurring at very low engine speeds and prior to ignition, while timing chain wear tests look at lubricant contamination and the effect this can have on timing chain wear.”
PC-11 UPGRADES
Kyle Fricke, senior marketing specialist for HDEO for Afton Chemical in Richmond, Va., discusses the move by the lubricants industry from CJ-4 to PC-11. He says, “The PC-11 category represents a clear performance improvement compared to CJ-4. The OEMs want oils with improved robustness characteristics to cope with increased thermal stress placed on them with the latest emissions compliant engine design platforms.”
Fricke continues, “Use of CJ-4 oils is anticipated to decline as the industry moves to the new higher-quality products, although a number of market and economic factors can influence the speed of that transition. With the introduction of PC-11, the market is expected to transition to alternative viscosity grades (i.e., away from traditional 15W-40) at a greater pace than simply through the use of new grades in new trucks. This means a significant increase in use of 10W-30, 5W-xx and 0W-xx oils. However, this will not simply be a change at the PC-11A or CK-4 performance level as different customer segments will be attracted by the potential operational cost savings associated with the move to low viscosity, fuel efficient PC-11B oils and some OEMs or operating companies may promote the use of low phosphorus or universal oils.”
Figures 7 and 8 show the transition from the current HDEO product tiers to the larger number of viscosity grades that will probably be offered in the post PC-11 market.
Figure 7. The current North American PC-11 product tiers are shown. (Figure courtesy of Afton Chemical.)
Figure 8. A larger number of viscosity grades will probably be offered in the post North American PC-11 market. (Figure courtesy of Afton Chemical.)
Proposed Category 11 (or PC-11) is the next heavy-duty engine oils performance category, superseding the existing API CJ-4, in development by the American Petroleum Institute. This new category is scheduled for first licensing on Dec. 1, 2016. PC-11 was designed to meet industry needs for higher performance, greater fuel efficient heavy-duty engine oil technologies while enhancing engine durability. According to Keith Corkwell, Lubrizol’s global business manager-heavy-duty diesel engine additives in Wickliffe, Ohio, “The continuing drive for fuel economy improvements is likely to command more fuel efficient engine oils enabled with lighter HTHS viscosity without compromising durability. Today, the U.S. market is dominated by SAE 15W-40 lubricants in diesel engines, but it is likely that, with the advent of PC-11, we will see increased use of SAE 10W-30 and 5W-30 oils.”
PC-11 has been driven by the U.S. Government, which is emphasizing the need for improved fuel economy and reduced carbon dioxide emissions. Haffner adds, “PC-11 oils also will offer improved protection from higher engine temperatures, improved shear stability and a reduction in engine oil aeration.”
Tung says, “The primary driver for PC-11 came from a regulation issued by the NHTSA in 2011 limiting greenhouse gas emissions and requiring fuel economy improvements for medium- and heavy-duty trucks during a 2013-2018 phase-in period. The EMA then asked API to develop PC-11.”
Tung continues, “Besides fuel economy improvement and carbon dioxide emission reductions, other needs for PC-11 are driven by increasing biodiesel use and the need for improved protection from higher engine temperatures, improved shear stability, adhesive wear protection and reduction or elimination of engine oil aeration. In summary, PC-11 development is focused on better fuel economy and green environmental compatibility with emerging powertrain technology and emission system complexity.”
Gary Parsons, global OEM and industry liaison manager for Chevron Oronite in San Ramon, Calif., provides details on the new engine tests for PC-11. He says, “The Volvo T-13 is used to assess the thermal stability and resistance to oxidation/nitration. Performance in this test is targeted at helping ensure engine oils will continue to perform during extended drain intervals. The Caterpillar C13A test measures the engine oils ability to resist aeration. Aeration of engine oil can lead to a degradation of performance in engines equipped with variable valve timing.”
DeBlase expressed concern that moving to lower viscosity HDEOs may lead to the need to adjust the additives used. He states, “Ring scuffing could be an issue as it is increased upon moving to lower viscosity HTHS. A short-term resolution is to increase the treat rate of metal, phosphorus and sulfur containing additives to respond to the potential wear, but phosphorus and metal limits need to be taken into account.”
ADDITIVE CHALLENGES FOR PC-11A AND PC-11B
Haffner contrasts PC-11A as offering increased engine protection at traditional viscosities such as SAE 15W-40 while PC-11B is the so-called “fuel economy grade” designed to meet the evolving market needs for fuel economy. He says, “PC-11A is recommended by on- and off-road OEMs and will be fully backward compatible. The durability requirements will be the same for PC-11A and PC-11B to ensure that the new fuel economy grades are risk-free. But, similar to GF-6B, PC-11B oils may have little or no back serviceability and not all OEMs are expected to recommend PC-11B at least at the start.”
Commenting on PC-11A and PC-11B, Corkwell notes, “PC-11A is designed as a broad fit for existing trucks, requiring higher levels of protection and performance for end-users than those established by API CJ-4. While lubricants classified under PC-11A are broadly backward compatible to existing commercial vehicles, this category nevertheless represents a major step up for performance and will require significant investment. PC-11B reflects the increasing adoption of low-viscosity lubricants in engine hardware and will standardize these advanced products without sacrificing protection and durability.” Using more fuel-efficient engine oils has the dual benefit of achieving environmental goals while at the same time reducing the cost of operations for the fleet.”
DeBlase stresses the need for using antioxidants to meet the requirements for both PC-11 subcategories. He states, “The use of higher treat rates and more effective antioxidants can help handle future viscosity decreases with PC-11. Longer drain intervals require that higher temperature decomposition of antioxidants needs to be minimized in order to maintain the oil viscosity specification (more demanding for PC-11B), which can rapidly increase at the end of the antioxidant performance life.”
Gerald Shaw, America’s region automotive engine oil product line manager for Chevron Oronite in Bellaire, Texas, believes that a key challenge is maintaining wear performance between the two subcategories since PC-11B is a lower viscosity oil with lower oil film thickness. Shaw says, “The two subcategories overlap significantly in what is needed in formulating for the oil’s performance. The biggest challenge is the application of advanced antiwear systems to help ensure wear performance with lower viscosities.”
Fricke says, “The application range of the new PC-11 specification represents the biggest change for the market and for both equipment operators and oil marketers. PC-11 will introduce a more restrictive specification for oils that meet the performance requirements of both heavy-duty diesel and gasoline engines—universal or mixed-fleet oils—with a tighter specification on phosphorus levels for these oils for exhaust catalyst compatibility. There also is greater interest in the development of the new PC-11 category from global OEMs who have developed a closer association with North American OEMs through the lifetime of the CJ-4 category.”
Tung summarizes, “PC-11A and PC-11B must ensure that the low HTHS oils still deliver the same level of engine protection as defined in current API CJ-4 engine tests and in the upcoming PC-11 engine tests.”
MEETING NEW PC-11 REQUIREMENTS
DeBlase predicts that proper base oil and additive selection will be critical. He states, “PC-11 requirements for fuel efficiency will likely be met by a combination of base oil improvements and increased usage of antioxidants, friction modifiers and antiwear additives. However, in diesel engines the development is more challenging, due to the hotter operating temperatures expected and needed to maintain viscosity. The impact of treat rates on air release may need to be addressed, and the proper use of additives such as oil-compatible high molecular weight polymeric silicone antifoams, considered.”
Hutchinson says, “Further fuel economy improvement within PC-11B should be possible by careful selection of the VI improver type with comb polymers being optimal. The key for PC-11B will be a VI improver delivering a good HTHS 150 C before and after shear combined with low oil viscosity at more intermediate temperatures so fuel economy is optimized without a compromise in durability.”
Shaw states that a fresh additive approach is needed in formulating PC-11 engine oils to meet the new requirements of the specification. He says, “Fuel economy can be enhanced by designing lower friction formulations through unique components such as a novel heavy-duty friction modifier. Improved oxidation and wear protection can be achieved by carefully balancing antioxidation systems and using an innovative valve train antiwear component.”
Tung focuses on three new PC-11 tests that evaluate aeration control, wear, corrosion and oxidation and scuffing. He says, “The Caterpillar C13 has been developed because the test currently used for aeration in API CJ-4 does not adequately address Caterpillar’s aeration concerns. Mack T-13 addresses several criteria including ring and liner wear, bearing corrosion, oxidation and nitration control as defined by lead levels in the used oil and oil consumption. Daimler DD13 addresses scuffing of rings, liners and bearings. This DD13 scuffing test, still under development by Daimler, has the objective of minimizing future concerns of scuffing wear by low-viscosity engine oils.”
PC-11 engine oils will need to address higher engine temperatures and shear stability. According to Corkwell, “One way to make an engine more fuel efficient is to make it more thermally efficient, and manufacturers are increasingly exploring this route. When an engine runs at a hotter temperature, so does the oil lubricating it, and protection becomes more challenging due to the drop in viscosity. Oxidation also is more likely to occur at higher temperatures. For these reasons, PC-11 engine oils will need to be more oxidatively and thermally stable.”
Corkwell continues, “PC-11 will require high-shear stability of lubricants, helping them maintain the same level of protection after passing through the various parts of engines. New requirements will ensure that lubricants still offer the same protection under these conditions and that the original design viscosity does not drop below acceptable levels.”
One area of concern that PC-11 does not examine is adhesive wear and scuffing—the point at which two pieces of metal at the microscopic level adhere to each other under intense heat and subsequently damage each other upon movement. Corkwell explains, “No test for this problem, which can cause catastrophic engine damage, exists in the older categories and will not exist within the finalized version of PC-11. Adhesive wear within an engine is an either/or scenario. The problem occurs or does not occur with no middle ground. However, through extensive industry activity, we have been able to advance the development of a scuffing test that relates to real-world experience. While outside of PC-11, once finalized, it is expected that a scuffing test will become part of OEM approval requirements, due to the associated benefits this testing brings.”
Addressing the challenges of simultaneously developing additive technologies for three specifications, Birze concludes, “GF-6, PC-11 and second generation dexos1 technology require significant resources. Additive suppliers need to cover a wide range of capabilities and invest in them. Only by doing this can we create innovations, test them and confidently bring them to market.”
Haffner feels that the new PC-11 requirements will be met by examining the critical areas of fuel economy in heavy-duty diesel engines and learning how to maintain engine durability in a low-viscosity regime. He says, “The new additive platforms for PC-11 will offer the ability to cover multiple viscosity grades to suit the diverse needs of the market.”
LOWERING PC-11 PHOSPHORUS LIMIT
As explained by Fricke, universal oils that can operate in both gasoline and diesel engines will need to operate at a lower phosphorus limit (800 ppm as compared to 1200 ppm) to meet the GF-6 specification. He says, “Universal oils are low total base number, low phosphorus engine oils that are specially engineered to comply with gasoline after-treatment systems and not poison the catalysts. These oils will be new to the marketplace, replacing the “CJ-4/SN” claim capability.
Fricke continues, “In all probability, the biggest concern will be convincing consumers that the new oils entering the market will continue to protect their equipment in an identical fashion to traditional 15W-40 engine oils. For example, owners/operators may be wary of lower phosphorus engine oils because many of them have been conditioned to think that ZDDP is one of the most critical additives in a finished fluid. Market acceptance will undoubtedly be slow at first.”
Phosphorus reduction means that the best method to evaluate the efficacy of universal oils is through wear testing. The Cummins ISM engine test that measures engine wear and deposits under heavy-duty operating conditions is the desired technique to use. Shaw presents data from that test (
see Figure 9) showing the results of an advanced approach. He says, “Use of ashless antiwear components in a balanced formulation affords better results than what are seen with conventional formulations. All other performance attributes also are met with this new formulation.”
Figure 9. Use of ashless antiwear components in combination with a lower phosphorus content can achieve better wear results in the Cummins ISM engine test. (Figure courtesy of Chevron Oronite Co. LLC.)
Haffner makes the case that formulation costs will increase in trying to develop a universal oil. He says, “In general, it is more costly to formulate at a lower phosphorus level. ZDDPs are one of the most cost effective antiwear/antioxidant additives available and low ZDDP formulations need to be supplemented with alternative additives. One of the real issues with low phosphorus HDEO formulations is the level of comfort of OEMs and end-users due to the lesser amount of field experience that exists, in particular in older engines.”
DeBlase foresees the need to use fortifying organic additives to assist in boosting the performance of low-phosphorus-containing HDEOs. He states, “With the higher operating temperatures associated with diesel engines and the potential for oil thinning, especially if shearing of the VI improver takes place, a negative impact on wear tendencies may occur. This issue could be more pronounced for the lower viscosity oils needed to meet PC-11B.”
ROLE OF VI IMPROVERS
The growing importance of VI improvers as additives to not only enable engine oils to operate efficiently over a wide temperature range but also to assist with friction reduction raises the question about the role of this additive type in both GF-6 and PC-11 (
3). Hutchinson says, “Viscosity control at different temperatures will be the key in using VI improvers as a significant tool to achieve high levels of fuel economy in both engine oil specifications. High HTHS 150 C viscosity, both before and after shearing, required for durability and also to meet the engine oil standards, will be required alongside lower oil viscosity at intermediate temperatures (40 C, 80 C and 100 C) to deliver fuel economy. The proven abilities of comb polymers will make them ideal choices in GF-6 and PC-11.”
Haffner says, “The main noteworthy comment is that the amount of VI improvers required in low-viscosity engine oils such as SAE XW-16 will be reduced. But note that any contribution from VI improvers to reconcile lower viscosity with engine durability will be of greater importance.”
Ian Atherton, senior marketing manager for engine oils for Afton Chemical in Richmond, Va., indicates that VI improver use will be associated with shear stability. He says, “The PC-11 specification requirements are still being finalized, but it is anticipated that the new specification will result in more utilization of 25 SSI VI improvers compared to more traditional 35 SSI polymers. Some oil marketers would likely still be interested in maintaining heavy-duty grades on a 35 SSI VI improver if the specification enables them to make a 15W-40 grade with this polymer. However, it is clear that, particularly for grades outside of 15W-40, the market will likely have to use a 25 SSI option.”
Alex Boffa, global VI improver technology manager for Chevron Oronite in Richmond, Calif., sees VI improver benefits for both GF-6 and PC-11. He says, “VI improvers will play a critical role in GF-6 in determining the overall rheological profile of the lubricant, which in turn controls viscous losses that impact fuel economy. However, VI improvers also must be efficient in thickening in order to minimize polymer contributions to piston deposits for both passenger car and heavy-duty oils. For PC-11, heavy-duty engines operate in a severe environment that can lead to mechanical breakdown of the polymer chain. Certain VI improver polymer architectures provide higher stability for extended shear, which can be a benefit for extended drain intervals in heavy-duty applications.”
DEVELOPING ADDITIVES FOR GF-6 AND PC-11
Most respondents to the question of the difficulty in developing additive technologies for GF-6 and PC-11 simultaneously cited the large commitment in R&D resources and time needed. The industry contacts indicate that many of the chemistries are common to both specifications but the formulations are different because the environments in gasoline engines and heavy-duty diesel engines are quite different.
STLE-member Mark Sztenderowicz, global manager, automotive engine oils product development for Chevron Oronite in Richmond, Calif., details the significant challenge faced by the lubricants industry in working on two major engine oil specifications at the same time. He says, “Historically there have been substantial gaps in time between heavy-duty diesel and passenger car performance updates leading to new API categories. This has helped to spread out the effort and allow resources to be focused on one or the other. In this case, however, resources needed to develop new heavy-duty and passenger car lubricants are stacked together, leading to severe demands in every area. Engine and bench test laboratories are being pushed to new extremes with all of the new test demand; blending facilities are being stressed to generate all of the test oils needed; demands on technical staff are at all-time highs and the investment required to accomplish all of this is perhaps the highest seen by the lubricants industry.”
Tung provides a perspective about how little time additive companies may have to develop new formulations once precision matrix studies are completed. He says, “The most difficult issue for the lubricants industry to develop new additive technologies for GF-6 and PC-11 at the same time is about the uncertainty of final performance limits for both specifications until December 2016 or even later after all precision matrix jobs’ verification. Additive companies only have approximately a half-year time frame to develop a new formulation to meet GF-6 requirements. In addition, all performance limits for all engine sequence tests are still not well established. Further complicating the process is that performance limits for GF-6A and GF-6B have not been established as their own performance limits are still being debated.”
DEXOS1
The dexos1 specification is the automaker’s way of ensuring the right oil is used to enable optimum vehicle performance, particularly with GDI and TGDI technology.
The second generation dexos1 spec includes more tests and greater performance demands far beyond current ILSAC industry specifications. Adding to the demands of managing upgrades to GF-6 and PC-11 is the mandatory transition to GM’s second generation dexos1 in August 2016, ahead of the first license for GF-6 and PC-11.
Birze says, “Much of the significance of second-generation dexos1 stems from its unprecedented focus on fuel economy and enabling GDI/TGDI engines. Second generation dexos1, which contains 13 tests, sets higher standards for fuel economy and durability performance than the current dexos1.
Haffner expresses concern that the lubricants industry may have to reformulate GF-6 products again once second generation dexos1 is introduced. He says, “Considering the qualification and licensing protocols introduced by GM, most products will probably require new formulations which will impact logistics. With GF-6 only 18-24 months after the planned introduction of second generation dexos1, PCMOs may need to be reformulated again to meet GF-6.”
Parsons adds, “Formulators must develop products to meet next generation dexos without knowing how or whether they will necessarily link to GF-6 once it is introduced. Since dexos1 is more than one year in advance of GF-6, short-term priority must be given to dexos.”
Tung discusses the challenge of meeting GM’s new engine oil specification. He says, “During this spring at the Fuels & Lubes Asia Conference, GM manager Angela Willis made an outstanding presentation on the perspective of GM on fuel economy and engine oils. She told the audience, “Second generation dexos1 builds in several performance improvements, especially around LSPI and fuel economy.”
Willis emphasized that GM has introduced a vehicle fuel economy test that is a new concept for North American engine oil specifications. The challenge is to have formulations that provide top notch, LSPI and fuel economy performance without compromising other properties such as oxidation, deposit and sludge control and wear performance.”
Tung believes that GM sees the new dexos1 specification as a benefit to the industry by allowing additive and oil companies to start formulating engine oils around LSPI prevention and fuel economy. In addition, this new GM specification will stimulate all additive and petroleum companies to accelerate preparations for the upcoming ILSAC GF-6 specification.
Davis ideally states that desire of most in the lubricants industry regarding GF-6 and dexos1. He says, “Although GF-6 and dexos1 have different performance criteria, most of the lubricants industry would like to develop one engine oil that meets both specifications.”
The automotive lubricants industry is now facing an unprecedented demand to develop products for two new industry-wide specifications and a third specification for a specific OEM. Additive suppliers will need to develop new additives and formulation approaches to meet specification deadlines that are timed to be in close proximity to each other. The hope is that by using a strong knowledge base and efficiently using its resources, the lubricants industry will be able to meet the strict timelines for all three specifications.
REFERENCES
1.
Van Rensselar, J. (2013), “PC-11 and GF-6: New engines drive change in oil specs,” TLT,
69 (1), pp. 30-38.
2.
McCarthy, S. (2014), “The future of heavy duty diesel engine oils,” TLT,
70 (10), pp. 38-50.
3.
Canter, N. (2013), “Fuel economy: The role of friction modifiers and VI improvers,” TLT,
69 (9), pp. 14-27.
Neil Canter heads his own consulting company, Chemical Solutions, in Willow Grove, Pa. Ideas for Tech Beat can be submitted to him at neilcanter@comcast.net.