Bio-based Greases: Back to the Future
Nancy McGuire, Contributing Editor | TLT Feature Article May 2014
Environmental concerns and improved technology are causing a resurgence for these plant-based lubricants.
www.canstockphoto.com
KEY CONCEPTS
•
Bio-based greases are a very small but growing segment of the market.
•
Environmental concerns and regulatory compliance are the main motivation for using bio-based greases.
•
The performance and price differential between bio-based and mineral greases is narrowing. In some cases, bio-based greases offer superior performance and/or price.
AFTER A 150-YEAR HIATUS, lubricating greases made from agricultural products are making a comeback. For some 4,000 years, animal fats, olive oil and other bio-based materials kept wheels and gears moving along smoothly. The shift toward petroleum-based lubricants came about only in the latter half of the 19th century (
1). Now uncertainties in petroleum prices and supply sources, coupled with an emerging awareness of environmental factors, are turning a small segment of the market back to lubricants made from renewable resources—mainly plants.
Can bio-based lubricants compete in a world of high-capacity generators, jet aircraft engines and 18-wheel trucks? This question is particularly challenging when the lubricants are greases, which require thickeners and additives and must perform under heavy loads and in hostile environments.
WHY BIO?
Bio-based greases are considered a specialty product today, representing between 1 and 5 percent of the market, depending on which source you consult. Performance wise, they lag behind mineral-based greases, but the gap is narrowing according to STLE-member Anoop Kumar, director of R&D and business development at Royal Manufacturing Co. in Tulsa, Okla. The main impetus for buying bio-based grease lubricants is to reduce harm to the environment. Not only are the base oils biodegradable, they tend to be made with fewer heavy metal and chlorinated additives. Even though these products have been on the market in the U.S. since the 1990s (and since the 1980s in Europe), a significant amount of development work remains to be done before the products can truly be considered mainstream. “This is a learning curve for us,” says Bill Mallory, Royal Manufacturing’s owner and CEO.
Bio-based greases are somewhat more expensive in the U.S. than their mineral based counterparts, notes Mallory. The difference varies with the application and the quantity, but “it’s about 25 percent more expensive for bio,” he says, adding that the differential is less than it used to be because of the rising price of petroleum relative to seed oils.
STLE-member Lou Honary, professor and founding director of the University of Northern Iowa’s National Ag-Based Lubricants Center in Waterloo, Iowa, notes that for large-quantity applications, bio-based greases can actually be price competitive with mineral greases. He cites the example of rail curve greases used to prevent track and wheel flange wear on curved sections of railroad tracks: “In early 2000, bio-based rail curve greases were about twice the price of petroleum rail curve grease. Today, they are priced the same, and at large volumes [bio-based greases are] even lower priced than the petroleum version of the same products.”
Frank Lochel, research advisor for Cargill Industrial Solutions in Plymouth, Minn., notes that bio-based greases are far less expensive than the synthetic greases that are currently available. The initial purchase price is not the only factor in the overall cost, he says. “A high-cost grease for which the grease replacement rate is low may be less costly to use than a low-cost grease that needs frequent replacement.”
Disposal costs are another factor in the overall cost of a lubricant. Because solid and semi-solid lubricants are not easily liquefied, they are not easily recycled. Thus, biodegradability is of particular interest as an alternative to recycling.
ENVIRONMENTAL ASPECTS
Bio-based products are an attractive option for customers who must comply with regulations on the amount and type of lubricants they can release into the environment. European environmental standards are stricter than those in the U.S., and the main research in bio-based lubricants is occurring in Europe, according to Mallory. “They are making a conscious effort because they are more sensitive to environmental effects,” he says. “The U.S. is coming up to speed on this, as are South America and China.”
Part of the difficulty in the U.S. is a lack of clear standards on the manufacture and usage of biodegradable lubricants in general. Europe has a system for regulating biodegradable products, and product claims are clear and supportable. Because of this, some U.S. suppliers of environmentally acceptable lubricants use European standards to benchmark their products (
2).
Honary predicts that, “With the government’s lead-by-example initiative, advocacy by growers associations and advances in lubricant research and biotechnology of oil seeds, the U.S. market will progressively see more bio-based lubricants.”
Some progress is being made along this front. The USDA has issued a bio-preferred list of products (
3), and the U.S. military lists manufacturers of biodegradable lubricants among its preferred manufacturers (
4).
Even greases that use bio-derived base oils may contain additives that make them less environmentally benign. Honary cites the example of greases for high-pressure applications that use zinc or sulfur additives. He notes that greases of all kinds may be contaminated with metal particles during use, and disposing of used greases must be done in compliance with local rules. Kumar notes that Royal Manufacturing substitutes more benign substances such as bismuth based additives for ones using heavy metals such as antimony, molybdenum or lead. Even though bismuth is the heaviest of these elements, it is more environmentally benign because it is less toxic than lead and it does not bio-accumulate.
Lubricants that are used close to waterways or otherwise exposed to the environment present their own set of challenges. The EPA requires that no visible oil sheen be evident downstream from facilities located in or close to waterways and that point discharges to waterways must contain less than 10 ppm mineral-based oil (
5). This affects not only construction operations close to waterways but also ships and other vessels that use metal cables coated with grease as a protection against corrosion. It is almost impossible to prevent spills and leakage completely, so environmentally acceptable materials are being substituted for their mineral-based counterparts.
HOW TO MAKE GREASE
To make grease, mix about three parts oil to one part soap. “Soap acts like a sponge with its cells filled with oil,” explains Honary. When the grease is subjected to shearing, mechanical shock, loading or other stresses, it releases oil, which flows into the gaps between mechanical parts and does the actual lubrication work.
In a chemical context, the word soap describes any product of a reaction between a metal hydroxide or other strong alkali and a fat or oil—the familiar sodium-based bath products, as well as the lithium-, calcium- or aluminum-based compounds required for making lubricating grease.
Fats are esters that contain saturated or nearly saturated hydrocarbon chains and are solid at room temperature. Oils, also esters, have a higher degree of unsaturation and are liquid at room temperature. (Saturation refers to the number of carbon-carbon double bonds in the carbon chains: greater saturation corresponds to fewer double bonds.)
Fats are classified by the number of fatty acid molecules attached to a molecule of glycerol. Triglycerides, for example, have three attached fatty acid molecules. When fats or oils react with a strong alkaline solution, they are hydrolyzed into the constituent fatty acids, which then react with the metal in the alkaline compound to form soap.
Lithium and calcium stearate soaps produce greases that have higher melting points than do the sodium and potassium stearates commonly used as washing soaps. Lithium soaps confer anti-corrosion properties, and they are more water-resistant than sodium soaps.
When soap and oil are mixed, the soap molecules aggregate to form a fibrous network. Oil droplets are contained in the spaces of the network—the holes in the sponge. Under operating conditions, the oil is squeezed out of the sponge and into the mechanical parts. A grease with good reversibility will re-absorb the oil when the stress is removed.
Bio-based grease manufacturing is more complicated than making mineral-based greases, explains Honary. Conventional grease-making processes require reaction temperatures as high as 220 C (428 F), which could oxidize many biodegradable base oils.
Also, the soap is formed
in situ by adding alkali to a mixture of fatty acids and base oils. This isn’t a problem when mineral oils are used, since they are non-polar and don’t react with the alkaline solution. Biobased oils, however, are esters formed from the same or similar fatty acids as those forming the soap, and they can react along with the fatty acids to produce a complicated soap structure that performs unpredictably at extreme temperatures.
Most of these issues have been addressed technologically, says Honary. Microwave-based processing has been an important advancement. Exposing the starting mixture to microwave radiation produces a faster, more uniform and complete reaction.
WHAT GOES INTO GREASE: BASE OILS
BASE OILS
Bio-based lubricants in the 21st Century use plant sources rather than sheep tallow and whale blubber. A variety of seeds and grains are used, and the products available in any given market depend largely on what crops are grown in that part of the world. In the U.S., common base oil feedstocks include soybeans, canola, rapeseeds, corn or castor beans. Palm oil is a common feedstock in Malaysia. Oils that have a greater hydrogen content (more saturation) are desirable, since they tend to be more stable toward oxidation than unsaturated oils, and they perform better at low temperatures.
Often, a base oil will be selected because it strikes the desired balance between oxidative stability and cost. Triglyceride oils are fairly inexpensive, but they require additives to prevent them from oxidizing, hydrolyzing (degrading when they come into contact with water) or degrading at high temperatures. Increasing the oleic acid content of the base oil can help prevent oxidation and reduce the coefficient of friction. Genetic engineering has quadrupled the oleic acid content of several plant oils over their naturally bred counterparts (20 percent in natural soybean oil versus more than 80 percent in some genetically engineered soybean oils, for example.)
Cargill has developed a line of industrial base oils using byproducts from vegetable oil refining processes, says Lochel. They have isolated a solid fatty acid stream (Agri-Pure 138) that was evaluated successfully as a partial or full replacement for oleic acid in metalworking fluids. This product is now being evaluated for its potential as a low-cost replacement for the fatty acids used in greases. He notes that Cargill uses primarily soybean oil for its grease applications because it is readily available and relatively inexpensive.
“On the positive side, vegetables oils have intrinsically lower coefficient of friction than their mineral oil counterparts. This allows additives such as antiwear and EP [extreme pressure] to be used at substantially lower levels than for mineral oils. “This lowers overall product toxicity,” says Lochel. “In instances where very low levels of additives are acceptable, these vegetable oil-based greases are safer for use in food processing equipment.”
Table 1. Greases typically contain about 75 percent oil. This is the component that does the lubricating.
(For more information, see Refs. 2, 6)
APPLICATIONS AND PERFORMANCE
Although bio-based greases may be used for many of the same applications that use mineral-based greases, they tend not to perform as well, according to Kumar. They do offer some advantages in lubricity, the lubricant’s ability to reduce friction.
Biodegradability is a double-edged sword. The ability of a lubricant to break down in the environment eases disposal problems and reduces the damage from leakage and spills. On the other hand, degradation reduces the shelf life and service life of a grease. Greases used as sealants (metal cables, open gears, gasket protectors) must often stand up to harsh environmental conditions—the same environment in which they are expected to break down after they have served their purpose.
Figure 1. Chemical components of grease.
The food industry would seem to be a natural fit for bio-based greases, but most food-grade lubricants use non-biodegradable USP White Mineral Oil. Kumar explains that the overriding concern for food-grade lubricants is the safety of materials that might come into contact with food. This concern overrides any concern for biodegradability at present.
Honary notes that bio-based greases may be used for any application that currently uses mineral-based greases, as long as they meet National Lubricating Grease Institute (NLGI) specifications for that particular application and the manufacturer’s recommendations are followed. For example, a bio-based grease containing a base oil with a high flash point or fire point could offer an advantage in situations involving high temperatures or the danger of fire, he says.
Figure 2. Micrograph of a soap matrix.
WHAT GOES INTO GREASE: THICKENERS
THICKENERS
Thickening agents provide a spongy matrix that stores the lubricating oil, holding it in place between gears and bearings, the fibers of a metal cable or along the bend of a railroad track. Soaps are the most common type of thickeners. The fatty acids for the soaps can come from olive, castor, soybean or peanut oils, and making them can be as simple as adding an alkaline solution to form the metal salts of the fatty acids.
Lithium hydroxide is the go-to alkali for many types of greases. Lithium soaps show better resistance to water than sodium soaps, and they perform better at high temperatures than calcium soaps, factors which work to offset the higher cost of lithium soaps. However, in many cases lithium greases have been superseded by other types of lubricants for high-temperature and high-performance applications.
Calcium soaps may be used to make greases for low-speed, low-load applications. They offer good water resistance, but they do not perform well at elevated temperatures.
Complex soaps are used for high temperature applications. These soaps can raise the dropping point of a normal soap-thickened grease as much as 100 F (38 C). The maximum usable temperature for a grease is limited by the flash/ignition/ evaporation point of the encapsulated oil — about 350 F, or 180 C (
5).
Aluminum Complex Grease. (Courtesy of Lou Honary, UNI-NABL)
Table 2. Greases typically contain about 20 percent thickeners. These are usually soaps, although some greases use organo-clay, polymer, or silica-based thickeners.
(For more information, see Refs. 7, 8)
To make a complex soap, two chemical reactions are carried out simultaneously. Fatty acids are reacted with an alkali, as in a normal soap, while the alkali also reacts with an inorganic acid or a short-chain organic acid to form a metallic salt called a complexing agent. The base oil is present during this process, and it becomes encapsulated in the complex soap matrix. Organic complexing agents are commonly made using acetic, lactic or adipic acids. Carbonates, borates or chlorides may be used to form inorganic complexing agents, although chlorides produce a less environmentally benign product.
Complex soaps commonly contain lithium or aluminum as the metal component, and calcium sulfonates are used in some applications. Aluminum complex grease has a very fine fiber structure and a high dropping point. It provides good mechanical and thermal stability, along with good water resistance.
For specialized applications, non-soap thickeners offer performance features that offset their greater cost. Polyurea thickeners are often used for ball bearings, providing resistance to water and oxidation. Polyurea is metal-free, but manufacturing it requires organic amines and toxic diisocyanate compounds.
R and R’ are hydrocarbon chains of various lengths, and n is the number of times the basic monomer unit is repeated in the polymer chain.
Organo-clay thickeners are made by treating the surfaces of dispersed clay particles (typically, bentonite) with organic amines or ammonia compounds. The resulting thickener has an amorphous, gel-like structure, rather than the fibrous structure typical of soap thickeners. The clay component provides heat resistance, and the organic compounds aid in compatibility between the clay and the organic components of the grease.
Fumed silica, made from branch-like aggregates of amorphous silica microparticles, is used as a thickener for high-temperature applications. This form of silica has a high surface area and a very low density. It makes an effective gelling agent, and it can be used to make greases for cable fillers.
For some applications that require a lubricant to perform under extreme conditions, bio-based greases may actually outperform their mineral-based counterparts. “Lubricants that can withstand these more severe operating conditions, plus contaminants such as dirt, sludge and water, will be more valued by the industry,” says Dan Deneen, director of business development for lubricants at Solazyme in South San Francisco, Calif., in a recent survey (
9). “For these value-added applications, polyol esters derived from fatty acid feed stocks between C
8 and C
18 have worked well, because they exhibit good cost performance, a wide temperature operating range and good oxidative and thermal stability.”
Kumar warns that generally speaking mineral-based greases perform better in harsh environments (marine applications, for example), but some bio-esters come close to matching this performance.
Multi-colored soy greases (Courtesy of Lou Honary, UNI-NABL)
COMPATIBILITY
Mixing lubricating greases is a tricky business. Mixing incompatible greases results in performance that is significantly inferior to that of either grease used alone—for example, a marked increase in softening or bleeding. Incompatible products can cause blockages and degradation. Base oil can migrate out of one grease and into the other, leaving behind a plug of thickener and additive material.
Manufacturers generally recommend against mixing different types of greases, especially when one is mineral-based and the other is bio-based. However, they sometimes provide information on the compatibility between specific types of grease. (Ref. 5 shows one example of a compatibility chart.)
Incompatibility can occur when two types of grease have differing metallic soap structures, explains Lochel. The soap matrix can contract, causing the base oil to be expelled, a phenomenon called synerisis. He recommends that bio-based and mineral-based greases not be mixed.
Compatibility requires case-by-case evaluation, states Kumar. He has done extensive work in this area, and he has developed a reference chart for specific types of greases. Why not put compatibility data on product packaging? Mallory notes that it’s impractical to issue this type of general statement because of the wide variety of grease formulations, and that compatibility really must be determined for specific pairings of greases.
Honary states, “Most bio-based greases can be mixed with mineral-based greases without negative impact as long as they are made of the same soaps.” For example, two greases that both use a lithium soap might work well together. He notes that several NLGI papers have explored the mixing of bio-based and mineral-based greases.
WHAT GOES INTO GREASE: ADDITIVES
ADDITIVES
Grease manufacturers add a host of other materials, many of them proprietary, to achieve a set of desired properties: heat resistance, corrosion resistance, EP/antiwear characteristics and so on. The choice of additives can lessen the biodegradability or increase the toxicity of a grease; thus, performance factors must be weighed against environmental factors. The physical and chemical properties of bio-based oils are very different from those of mineral oils, and they require different additives.
Metal-free additives, referred to as ashless additives, can provide corrosion protection and EP/antiwear properties without sacrificing safety to the environment and personnel. These materials include sulfurized fatty materials and succinic acid derivatives.
Solid lubricants, such as molybdenum disulfide or graphite, can be used to further reduce friction, especially for high-temperature applications. These compounds have layered crystal structures, and the solids form flakes that slide past each other easily. These additives are used for lubricants meant for high-temperature and high-pressure applications. Greases with solid additives must be changed more frequently to prevent the solids from accumulating in components and causing wear.
Accumulated wear particles must be taken into account when evaluating the environmental effects of disposing of used greases. Even the most environmentally benign grease product can become a pollutant if it contains metal particles or other substances that have eroded into the grease.
Table 3. Greases typically contain about 5-10 percent additives to provide stability, extend the operating temperature range, enable the grease to perform under high pressure, or otherwise enhance its performance.
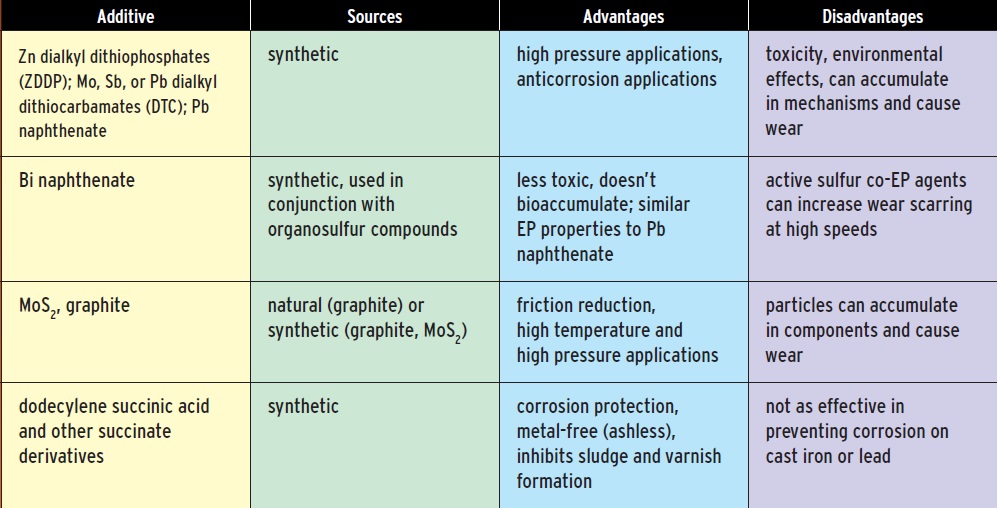
THE FUTURE
Lochel predicts that as regulations promoting bio-based lubricants increase, the demand for compatible additives also will increase. Because vegetable oil base stocks are based on oxygen-containing esters rather than hydrocarbons, it can be difficult to find additives that are soluble in these oils. The next generation of bio-based greases may use complex esters, oils derived using new chemical processes. New feed stocks may come into play, using oils from exotic plants or algae, or mixtures of bio-based oils with mineral synthetic oils.
Honary foresees a new generation of bio-based greases moving into extreme applications, including aviation greases and specialized military applications, as well as a growing market for bio-based greases in more mainstream markets.
Bringing bio-based lubricants, including greases, into the U.S. market mainstream will require well-defined, enforceable standards for the performance claims and terminology that manufacturers use. Standards set by the NLGI and the European markets are a start, and customer demand can drive further progress. Environmental regulations will continue to drive the move toward bio-based products, but petroleum price fluctuations and better- performing bio-based products will add further incentives for going green with grease.
REFERENCES
1.
Carnes, K. (2005), “The Ten Greatest Events in Tribology History,” TLT,
61 (6), pp. 38-47.
2.
Rostro, B.-C. (2007), “Everything Old Is New Again,” TLT,
63 (12), pp. 26-37.
3.
USDA Bio-Preferred Catalog: Click
here.
4.
Military Specification Lubricants Suppliers, ThomasNet.com, click
here.
5.
U.S. Army Corps of Engineers Engineering and Design Manual 1110-2-1424: Lubricants and Hydraulic Fluids—Click
here.
6.
Schaefer, T.G., “Esters in Synthetic Lubricants,”
Bob Is The Oil Guy (blog), click
here.
7.
Johnson, M. (2008), “Understanding Grease Construction and Function,” TLT,
64 (6), pp. 32-38.
8.
“Grease Bases used in the Manufacture of Lubricants,” Techni-Tips No. 56, Lubrication Engineers Inc., click
here.
9.
Challener, C., “Base oils supplement: Betting on bio for better base oils,”
ICIS Chemical Business, Feb. 20, 2012, click
here.
Nancy McGuire is a free-lance writer based in Silver Spring, Md. You can contact her at nmcguire@wordchemist.com.