Reducing rolling bearing failures
R. David Whitby | TLT Worldwide July 2013
Review these key factors to detect the cause of the problem.
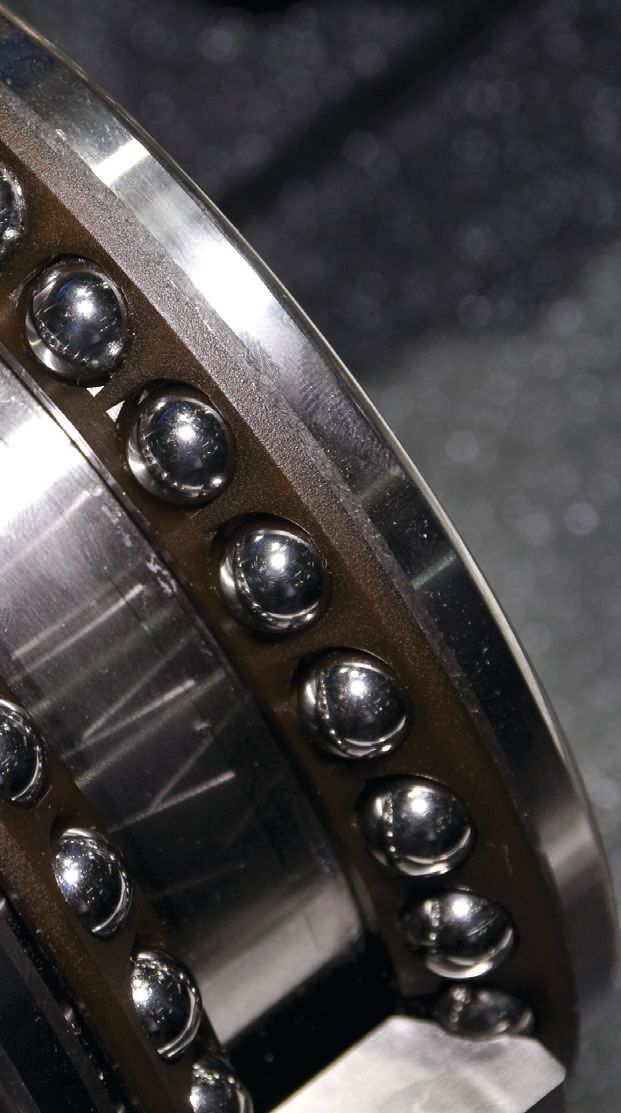
Bearings can lose 75 percent of their life due to the ingress of water.
www.canstockphoto.com
BEARINGS ARE THE MOST COMMON ELEMENTS in mechanical equipment and can last for a very long time. Rolling bearings, also known as antifriction bearings, can fail in service by a number of different mechanisms and causes. Fortunately, less than 1 percent of rolling bearings do not reach their expected life.
When a bearing does fail prematurely, it is often due to causes that are avoidable and interrelated such as bearing selection, installation, lubrication, operational stress and operating environment. Some bearings are damaged even before they are assembled on the machine (for example, by fretting corrosion during transportation). Bearings should be inspected prior to assembly into a machine to avoid this problem.
It is rare for an incorrect bearing to be selected. However, if applied loads become too high, premature fatigue may occur. If loads are too low, skidding and improper loading of the rolling elements can occur. In both cases, the bearing may become noisy or overheat. Bearing temperatures should stabilize in operation between 10 C and 40 C higher than ambient temperature but should always be below 100 C. Higher temperatures are often a sign of trouble.
During installation, it is critical to use the correct tools and induction heaters, if required. The entire inner-ring face should be a press fit on the shaft. A fit that is too tight will create too much preload, while a fit that is too loose will create insufficient preload, which may allow the shaft to rotate or creep in the bearing. When fitting the bearing, misalignment or shaft deflection should be avoided. The correct radial-internal clearance determined in the original design must be maintained.
When induction heaters are used to fit a bearing, the inner race heats faster than the outer race. The resulting thermal differential will reduce the bearing’s internal clearance. If this differential is too high, all internal clearance in the bearing can be eliminated and damage to the balls, rollers and races can occur.
Oils and greases used in bearings are intended to provide the rolling and sliding surfaces with a thin film of lubricant to avoid metal-to-metal contact. The lubricant also reduces friction and abrasion, prevents corrosion and conducts heat generated by friction.
Bearing failures associated with lubrication result from using the wrong type of lubricant, mixing oil and grease or having too little or too much lubricant. Too much lubricant causes fluid churning, resulting in excessive heat due to fluid friction. Bearing manufacturers can provide guidance on the correct viscosity of oil or consistency of grease, as well as the amounts of lubricant to be used to avoid overheating.
One of the more common causes of bearing failure in the road-wheel hubs of vehicles is damage to the hardened bearing surface caused by incorrect fitting or as a result of an impact load during driving. The surface damage acts as an initiation site for rolling-contact fatigue failure. Surface fatigue wear is caused by fatigue stress cycles, resulting in crack formation in surface regions of contacting surfaces and separation of material known as pitting.
Fatigue causes surface and subsurface cracks, which eventually spread, link up and form discrete particles that will detach from the surface. These may contribute to three-body wear abrasion of the surface. The roughened surface resulting from the pits adds to further cyclical stress and the fatigue process accelerates.
Many environmental factors, particularly dust, dirt, water, corrosive chemicals and external heat, can cause premature failure of bearings. Proper sealing methods need to be used. Ingress of dirt into bearings is one of the most common causes of premature failure, which is why greases are the preferred lubricant of choice for rolling bearings.
Rolling bearings are among the most sensitive components with regards to water contamination. Bearings can lose 75 percent of their life due to the ingress of water and are sensitive not only to emulsified water but also to dissolved water. Water contributes to corrosion and rolling contact fatigue.
Attention to all these issues will help to reduce premature bearing failures.
David Whitby is chief executive of Pathmaster Marketing Ltd. in Surrey, England. You can reach him at pathmaster.marketing@yahoo.co.uk.