Lubrication of worm gears
R. David Whitby | TLT Worldwide May 2013
Both polyalphaolefin and polyalkylene glycol synthetic oils are recommended for use in several applications.
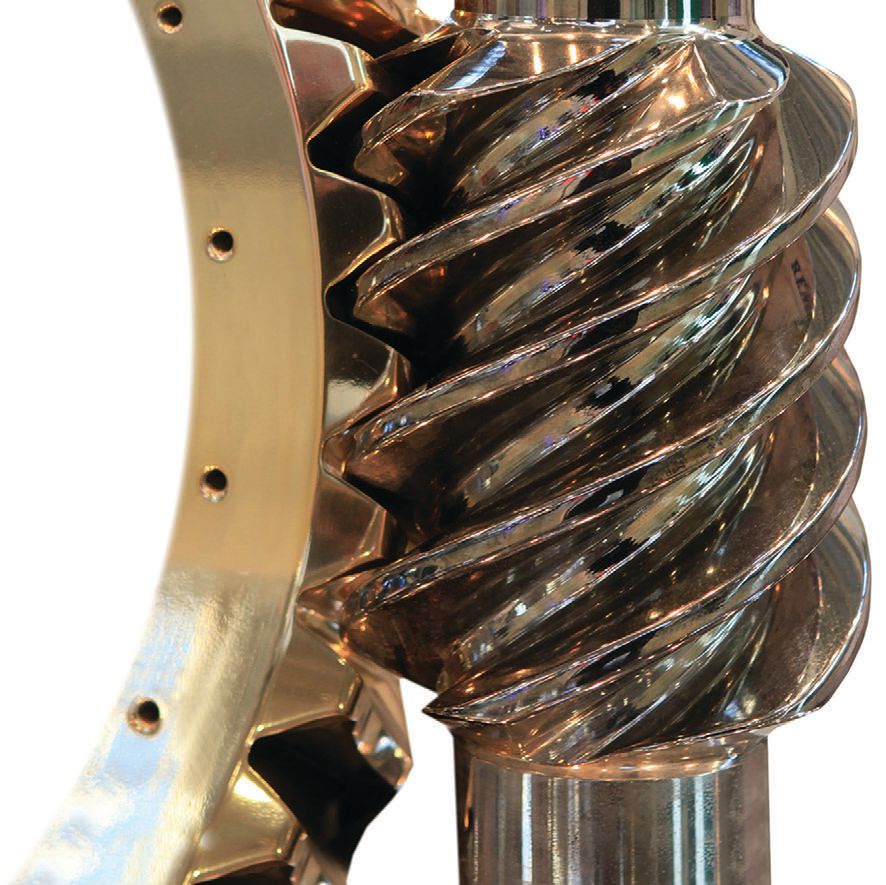
With worm gears, both sliding and rolling occurs as the teeth pass through mesh.
www.canstockphoto.com
WORM GEARS ARE DIFFERENT FROM ALL OTHER TYPES OF GEARS in that a spirally grooved screw moves against a toothed wheel. Uniquely, they can achieve large reductions in speed in a compact space and transmit high loads at high-speed ratios up to 60:1.
With all other types of gears, such as spur, bevel, spiral bevel, helical and hypoid, as the gear teeth mesh, they roll and slide together. The first contact is between a point near the root of the driving tooth and a point at the tip of the driven tooth.
At this point, the preceding teeth are still in mesh and are transmitting most of the load. As contact progresses, the teeth roll and slide on each other. Rolling is continuous throughout meshing, from root to tip on the driving tooth and from tip to root on the driven tooth. Sliding varies from a maximum velocity in one direction at the start of mesh, through zero at the pitch line, to a maximum velocity in the other direction at the end of mesh.
With worm gears, both sliding and rolling occurs as the teeth pass through mesh. Both this sliding and rolling are relatively slow in most cases due to the low rotational speed of the worm wheel. More important, rotation of the screw (worm) introduces a high rate of sliding. The combination of the two sliding actions produces a slide that in some areas is directly along the line of contact.
The high rate of side-sliding in worm gears results in significant frictional heating. Because the rolling velocity is generally quite low, the velocity tending to carry lubricant into the contact area is low. The sliding action tends to wipe the lubricant along the convergent zone and this, combined with the low rolling velocity, makes it necessary to use high viscosity lubricants, typically ISO 460 or 680 viscosity grades.
Compounded gear oils have been used extensively in worm gears with great success in a wide variety of applications. These are mineral oil-based with rust and oxidation inhibitors and acid-less tallow or synthetic fatty acid (the compounding agent), giving excellent lubricity to minimize sliding wear.
Gear oils that contain active EP additives are not normally recommended for worm gears, due to the constant wiping action of the high rate of sliding. Previously, there was a concern that sulfur-phosphorous EP additives would react with bronze gears. However, new non-active sulphur EP additive technology has reduced corrosive attack. EP gear oils work particularly well when shock loading occurs and also protect steel gears better than compounded gear oils.
Polyalphaolefin (PAO) or polyalkylene glycol (PAG) synthetic oils have become lubricants of choice for many worm gear applications due to their friction-reducing and extended life characteristics.
PAOs have relatively low coefficients of friction, which reduces the amount of internal friction created by the normal shearing of an oil film during operation. The high viscosity indices of PAOs also allow them to be used over a wider temperature range compared with mineral oils, as well as allowing the use of lower oil viscosities. Most formulations contain a small amount of organic ester or antiwear additive that improves boundary lubrication. Products that contain EP additives are also available. There are no major disadvantages, other than cost, when using PAOs. The use of PAOs in worm gearboxes has been shown to give increases in energy efficiencies of between 2% and 8% compared with equivalent viscosity mineral oils.
PAGs are excellent for worm gear applications. They possess superior lubricity properties and have good low- and high-temperature properties. The high viscosity indices of PAGs (up to 280) allows the use of lower viscosity grades, thereby minimizing internal friction and improving worm gear efficiency.
Most PAGs contain antiwear properties, but there are no formulations with EP additives. Besides cost, the major disadvantage of many PAGs is their incompatibility with other fluids, paints, seals and polycarbonate sight glasses. More recently, oil-soluble PAGs have been developed, which may provide the advantages of PAGs for worm gears without the disadvantages.
David Whitby is chief executive of Pathmaster Marketing Ltd. in Surrey, England. You can reach him at pathmaster.marketing@yahoo.co.uk.