Hydraulic systems take center stage
Jean Van Rensselar, Contributing Editor | TLT Feature Article January 2011
Emerging technologies make them a cost-effective, energy-conserving alternative to electronics.
KEY CONCEPTS
• Fluid power systems must become more efficient to compete with or complement advancements in power electronics and internal combustion engines.
• Simple measures such as choosing the correct fluid have the most immediate promise for improving fluid power system efficiency.
• More efficient hydraulic power could be one of the primary solutions to global energy challenges.
Hydraulic equipment is amazing in its strength and agility. Relatively compact, easy to service and sturdy, it produces a significant amount of power for its size.
Consider space shuttles. Capable of maintaining a consistent orbit for up to 17 days, they offer the perfect environment for transformative experiments in a number of scientific disciplines. None of this would be possible without hydraulics—especially the hydraulic components of the solid rocket boosters.
The NASA shuttle’s two solid rocket boosters, located on either side of the orange external propellant tank, are instrumental during the first two minutes of powered flight, providing about 83% of liftoff propulsion. Each powerful booster produces 80% more liftoff thrust than an F-1 jet engine. The booster’s hydraulic power unit operates from t minus 28 seconds until the booster’s separation from the orbiter and external tank.
There are two self-contained, independent hydraulic power units on each booster, each consisting of an auxiliary power unit, fuel supply module, pump, hydraulic reservoir and hydraulic fluid manifold assembly. The auxiliary power units are fueled by hydrazine and generate mechanical shaft power that drives a hydraulic pump, which produces hydraulic pressure for the booster’s hydraulic system. The gearbox drives the fuel pump, its own lubrication pump and the hydraulic power unit’s hydraulic pump.
The hydraulic pump operates at 3,600 rpm and supplies hydraulic pressure of about 3,050 psi. Each shuttle’s hydraulic systems are reusable for 20 missions.
For their size, hydraulic systems are among the most powerful in the world, yet compared to mainstream alternatives they are inefficient and technologically poor. The good news is that researchers and the hydraulic industry are working on important breakthroughs.
The impetus for change is partly a challenge from cutting- edge electromechanical alternatives but also a response to a long-overdue need for better fluid power technology.
Paul Michael is a research chemist at the Milwaukee School of Engineering’s (MSOE) Fluid Power Institute. He has been formulating and testing hydraulic fluids for more than 30 years and is current Chairman of the national Fluid Power association (NFPA) Fluids Committee.
“There are several reasons for the current focus on improving hydraulic system efficiency,” Michael said. “Energy expenditures in the U.S. have increased by 25% in the last decade. High energy costs and the down economy have motivated businesses to find ways to reduce consumption. In addition, it is clear that at least some of the interest is driven by a desire to reduce carbon emissions.”
THE SITUATION
Although the threat of emerging electromechanical solutions into power ranges high enough to compete with hydraulics will be a slow process, experts agree that the hydraulic fluid and equipment industries need to get going on new technology now.
From a sustainability standpoint, fluid power is similar to power electronic and engine technology; improved efficiency is required for the development of smaller machines that consume fewer resources and produce fewer emissions.
Since 1980 there have been more than 15 improvements in the chemistry of engine oil for diesel and gasoline engines. Arguably, there have been no significant improvements in hydraulic fluids—they are essentially the same as they were 30 years ago (1). Experts agree that without concerted improvements, hydraulics could become an obsolete power source within the next 30 years.
One of the most promising means of improving the efficiency of hydraulic equipment is optimization of friction, wear and lubrication at the moving interfaces. STLE-member Ashlie Martini, assistant professor at Purdue University’s School of Mechanical Engineering in West Lafayette, Ind., says. “Tribology is definitely going to be a key enabler for the next generation of hydraulics.”
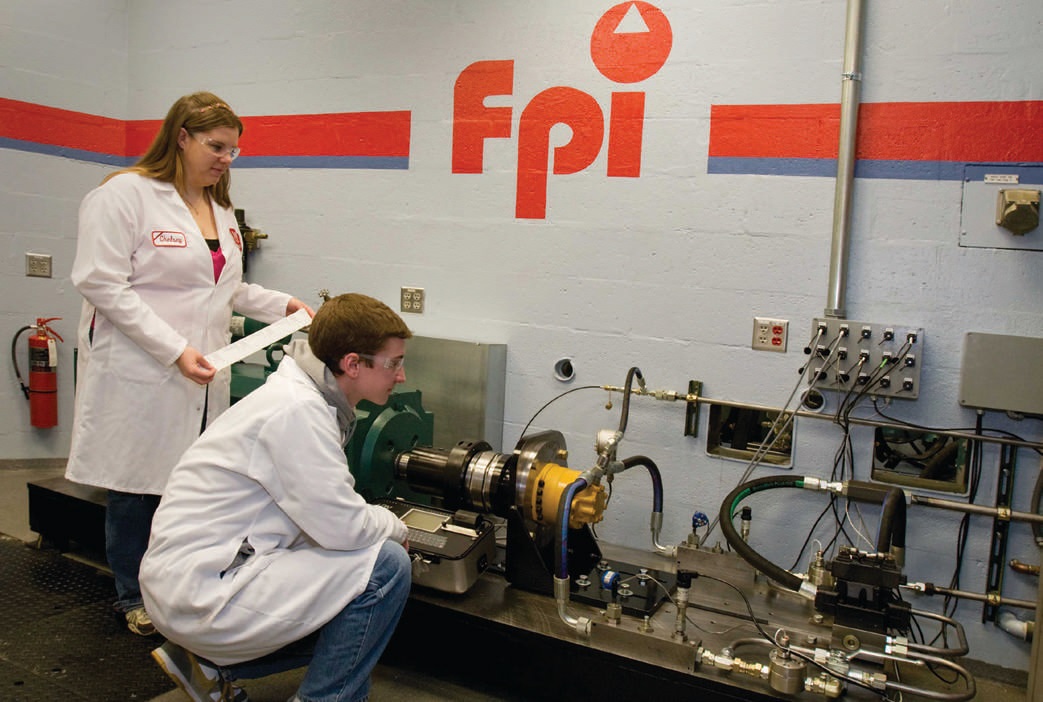
Milwaukee School of Engineering (MSOE) students Chelsey Jelinski and Brian Blazel examining the MSOE dynamometer used for efficiency testing of hydraulic motors.
THE CCEFP
The Center for Compact and Efficient Fluid Power (CCEFP) in Minneapolis is working on this. It is a network of researchers, educators, students and industries focused on changing how fluid power technology is researched, applied and studied. Established in June 2006, the CCEFP is a National Science Foundation (NSF) Engineering Research Center. In addition to its NSF grant, the center is supported by seven participating universities—a team of 38 faculty from the universities (each with distinguished academic records and interests that are unique and cross-disciplinary) is engaged in work on 25 research projects and four test beds.
Other CCEFP supporters include 52 partner companies that provide $750,000 annually in financial support as well as in-kind donations and expert advice on a project-by-project basis.
“The greatest benefit of the CCEFP is that it fosters collaboration which is essential when investigating complex research problems.” CCEFP faculty member Michael said. “Also, there is a synergy when industry and academia work together. Industry provides a reality check for CCEFP faculty researchers while industry benefits from new technology and skilled college graduates.”
CCEFP collaborators are in the process of creating hydraulic and pneumatic technology that is compact, efficient and effective. To that end, research goals include:
• Dramatically improving the energy efficiency of fluid power in current applications.
• Improving the efficiency of transportation by developing fuel-efficient hydraulic hybrid vehicles.
• Developing mobile human-scale fluid power devices.
• Making fluid power clean, quiet, safe and easy to use.
The CCEFP wants to make a transformative impact (and perhaps create new industries in the process) by reducing polluting petroleum usage and increasing the ways in which fluid power improves the quality of life for certain individuals. Some CCEFP members set an ambitious goal of 10% average energy savings through the use of new hydraulic fluids.
PRIMARY RESEARCH AREAS
The NFPA and the National Center for Manufacturing Sciences (NCMS) in Ann Arbor, Mich., created a strategy of research objectives for technical advancements in hydraulics. The six resulting initiatives are:
1. Increase energy efficiency.
2. Improve reliability by increasing uptime, eliminating leaks, reducing maintenance requirements and making fluid power safe and easy to use.
3. Reduce the size of components and systems while maintaining or increasing power output.
4. Build smart fluid power components and systems, including self diagnostics and plug-and-play (easy to use) functionality.
5. Reduce environmental impact by lowering noise and eliminating leaks.
6. Improve energy storage, recovery and redeployment capabilities of fluid power components and systems.
Those six research areas can be boiled down into the following four:
1. Improving system monitoring and maintenance
2. Optimizing fluid selection
3. Developing new fluids
4. Redesigning systems & components.
While it’s only natural to consider system redesign as a starting point for improving the efficiency of hydraulic systems, fine-tuning maintenance protocol and setting standards for fluid selection could actually have a much bigger and more immediate impact on overall efficiency, performance and reliability.
“The fluid is the only thing that you can change without changing the hardware to improve efficiency,” explains Michael. “This makes optimizing the fluid chemistry an obvious priority.”
Let’s examine the four emerging research areas in more detail.
1. Improving system monitoring and maintenance. A pump’s efficiency can be reduced by as much as 50% before it reaches the end of its life. That reduced efficiency often goes undetected because of the closed nature of hydraulic systems. Among the problems contributing to inefficiency are:
• Internal leaks
• Deteriorating piping and valve losses
• Changes in process requirements and control strategies.
Regular, comprehensive efficiency tests on all system components—especially the pump and motor—can quantify energy efficiency, pinpoint areas for improvement and provide the basis for a cost-benefit analysis of proposed improvements. The potential energy savings can be easily determined by computing the difference between actual system operating efficiency and the manufacturer’s original design for operating efficiency.
Daily hydraulic system inspections can catch leaks and other hydraulic system problems before they force equipment shutdown.
STLE-member Don Smolenski is an interested end-user and technical fellow at General Motors where he has worked for 31 years. His expertise is in hydraulics, engine oil, metal-removal fluids and anything related to them, including engine test development. He was instrumental in developing Gm’s LS2 Maintenance Lubricant Standard.
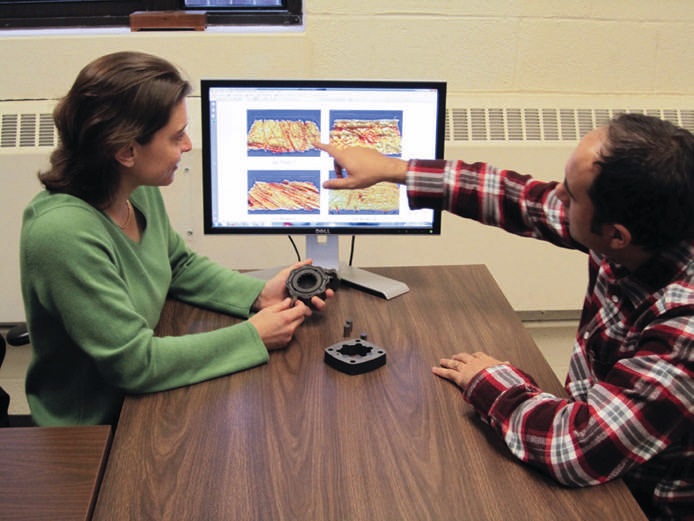
Purdue University professor Ashlie Martini and her student Jose Garcia looking at the surface roughness of components in hydraulic motors.
GM’S LS2 Fluid Selection Standard
STLE-member Don Smolenski was instrumental in developing General Motors’ LS2 Fluid Selection Standard, which has a purpose of—among other things—ensuring that users choose hydraulic fluids with the best properties for the application. Some of the standard’s specific goals are to:
• Improve equipment reliability and prolong life.
• Improve the likelihood of using the proper fluids in plant applications.
• Reduce the number of unnecessary fluids in the plants.
• Provide plants with a list of approved lubricants.
• Support fluid selection and application best practices.
Developers believe that the standard will reduce usage, repairs, spill and leak remediation, worker accidents and disposal costs. A detailed cost analysis estimated that, implementing the standard, a machine using 100 gallons of hydraulic fluid a month could reasonably produce a savings upward of $1,440 a month.
“A big part of the efficiency equation is keeping the machinery maintained,” he says. “An example is using breathers that aren’t sucking a lot of moist air into the hydraulic systems.”
2. Optimizing fluid selection. “In Gm plants we’ve tried to reduce costs in a number of areas with the volume of chemicals and the volume of energy,” Smolenski says. “If we can save 3%-5% in hydraulic fluids, we can save a lot of money operating our plants.
“One of the issues is that there are elegant ways of measuring energy savings in a lab and then there’s the real world,” he adds. “In order to convince somebody to make the switch to a more efficient fluid, you have to show them that it really does work in the plant.”
Smolenski believes the best comparative statistic is measuring the difference in the machinery’s kilowatt hours from one fluid to another.
“That’s what you pay for at the end of the day,” he says. “A more efficient system has demonstrated reduced kilowatt hours.”
The performance of hydraulic pumps and motors is a critical factor in overall hydraulic system reliability. Volumetric (leakage flow) efficiency and hydromechanical (friction) efficiency are the two elements of hydraulic efficiency. The overall efficiency of a hydraulic pump is the product of both factors, and both must be considered when selecting viscosity. The Catch-22 is that as fluid viscosity increases, volumetric efficiency tends to increase, while hydromechanical efficiency tends to decrease.
“I’ve been really interested in the whole viscosity index issue,” Smolenski says. “New research has shown that viscosity can have an effect but not the effect that we thought. I thought there would be some sort of breakeven point between internal leakage and hydromechanical losses, but there wasn’t. It appears that it’s the heavier fluids that have the most promise.”
At low operating temperatures, particularly at startup, high viscosity negatively affects the mechanical efficiency of the hydraulic system, resulting in reduced system performance, lubricant starvation and cavitation (air bubbles). High-viscosity fluids can create excessive pressure drops at the pump inlet, promoting cavitation. This causes metal fatigue, spalling and ultimately diminishes pump longevity. High viscosity in low-temperature conditions can lead to loss of the lubricating barrier and high contact temperatures, which will accelerate wear and may cause the pump to stop working altogether. Because of this and to prevent cavitation, pump manufacturers specify maximum startup fluid viscosity limits.
One of the primary jobs of a hydraulic fluid is providing a lubricating film to reduce wear on dynamic pump components. The effectiveness of that film in a hydraulic pump is dependent on a balance between such factors as viscosity, pressure, sliding speeds and antiwear additive chemistry. As temperatures rise, the film thins and may rupture, creating destructive metal-to-metal contact and straining the pump. Wear tends to occur in pump locations that have a bearing on volumetric efficiency. Poor viscosity resulting from high temperatures creates a cycle of rising temperatures, increased wear and internal leakage.
STLE-member Scott Bair, CCEFP member and Regents’ Researcher at Georgia Tech’s Center for High Pressure Rheology in Atlanta, is currently studying elastohydrodynamic lubricating films under extreme contact pressures up to 300,000 psi.
Oil viscosity specifications
The following specification sets, each with advantages and disadvantages, are designed to define oil viscosity in varying temperature environments (2):
• ISO 3448 (ASTM D 2422) – ISO VG Classification
• ASTM D 6080-97 – Fresh & Sheared Oil Viscosities
• NFPA T2.13.13-2002 – Viscosity Grade Selection Criteria
• Swedish Standard SS 15 54 34 – Full Formulations Specification
• Denison HF-O – Fresh & Sheared Oil Viscosities
“The high pressure substantially changes the behavior of the liquid in the film,” Bair explains. “We can measure these changes in behavior and generate predictions of the film thickness and friction. Mechanical efficiency of fluid power systems can be directly improved by the reduction of friction at high-pressure contacts.”
Smolenski concludes, “The point is that rather than fooling around with exotic additives, we might improve efficiency simply by using an optimized viscosity. We could just start using a heavier grade of the same product—if the research does bear out.”
Selection of the proper viscosity grade allows equipment to start easily at low temperatures and achieve the oil flow rates needed for efficient operation at high temperatures.
Viscosity variations associated with low starting temperatures and high operating temperatures contribute to system inefficiency and unreliability. At low temperatures, too much viscosity may result in poor mechanical efficiency, difficulty starting and wear. As oil temperatures increase, viscosity decreases, resulting in lower volumetric efficiency, overheating and wear.
At Gm Smolenski is working with SAE TC-2 and GM LS2 fluid specification development.
“The two sets of specifications are pretty much parallel,” he says. “We wanted to buy fluids using a performance-based standard instead of by name brand. We knew that if something passed LS2, it was going to work. Having that standard in place has been very important.”
“Using just the expertise of people in our plants to set specifications, we came to the conclusion that if a fluid could meet the specs, it could work in 99.9% of applications in the plant,” Smolenski says. “In our manufacturing plants, the fewer choices of fluid the better. Fewer types mean less chance of misapplication and bigger volume discounts.”
Smolenski adds that it’s the small changes that have the biggest impact.
“It’s a matter of fully utilizing what’s out there, not necessarily designing anything radical,” he says. “I knew I could save money in the plant just by paying attention to details, and we were able to save more than 20% on maintenance fluids and cutting fluids by using 50% rerefined oils. We couldn’t have done that without a good standard.”
“We are just trying to simplify things. There is nothing magical; it’s not real high tech. Find a good fluid and keep it clean, cool and dry—it should be able to run forever.”
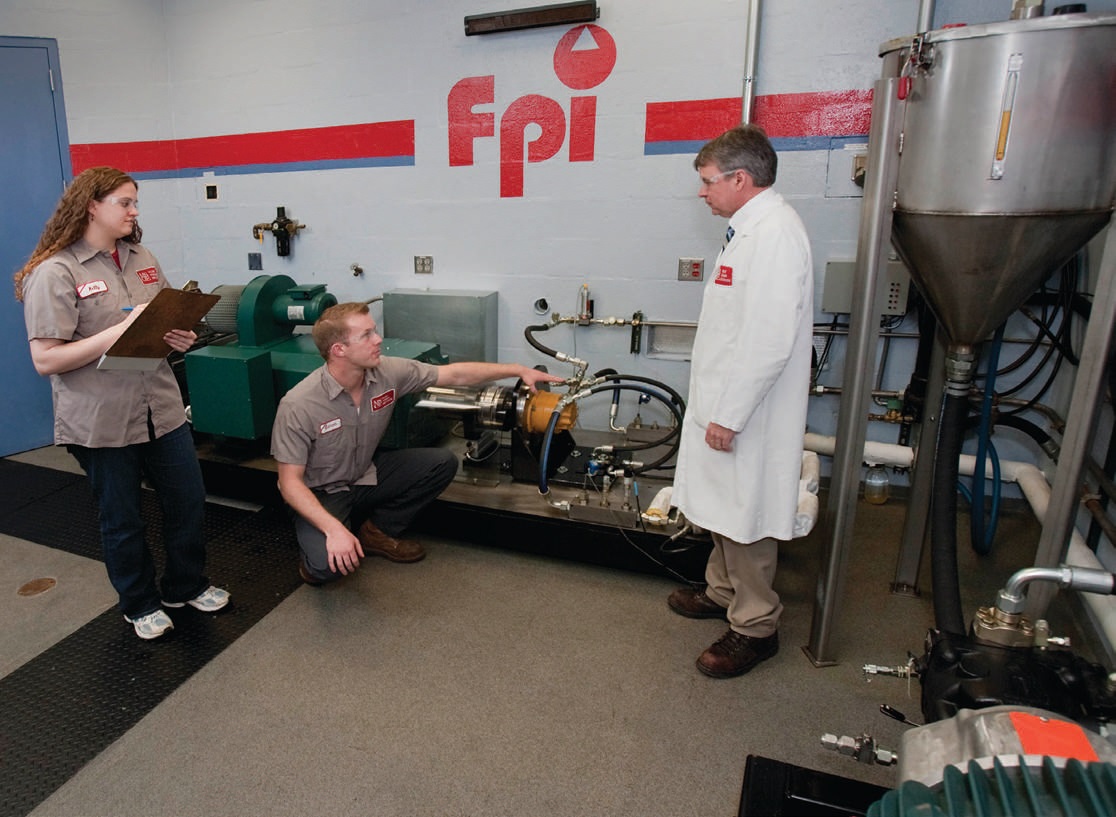
MSOE professor Paul Michael (right) examines a hydraulic motor with graduate students Kelly Burgess (left) and Aaron Kimball.
3. Developing new fluids. “In the vast majority of hydraulic fluid power applications, the impact of the fluid on energy consumption has never been a consideration,” Michael says. “Price is often the primary consideration as long as the fluid meets viscosity and certain minimum performance standards. Over the years, engine builders have developed a more sophisticated approach. Lubricants are optimized during the design process in order to meet fuel economy, tailpipe emission and vehicle performance objectives. This higher level of integration, where hydraulic components and fluids are optimized for efficiency and performance, is being developed through the CCEFP.”
In commercial vehicles and mobile fluid power uses, many experts have come to the conclusion that operating temperatures and energy efficiency considerations call for multigrade hydraulic fluids (3). Because of their excellent shear stability, multigrade hydraulic fluids are often recommended for equipment where the operating temperatures vary widely.
In recent years, a variety of laboratory tests and field trials have documented efficiency improvements in fluid power systems that use certain types of multigrade hydraulic fluids (4). These studies have examined the amount of diesel fuel that is necessary in heavy equipment vs. the amount of work produced, and a significant payback in fuel usage and/or productivity has been demonstrated.
Smolenski is intrigued and encouraged by the prospect of new fluid development.
“Years ago we tested and found a couple of fluids that looked promising, but they had properties that weren’t good for a hydraulic system,” he says. “For example, they had an emulsifier in them, and we wanted to shed water. The upside was that we could see there were possibilities.”
Michael says, “With a positive displacement pump, in theory the flow rate doesn’t change with pressure. In reality, as system pressure increases, the pump internal leakage flow also increases. This results in a reduction in pump volumetric efficiency. Increasing the viscosity of the fluid can mitigate pump internal leakage losses. Since viscosity index improvers increase viscosity, volumetric efficiency can be enhanced using shear stable multigrade oils.”
On face value, it’s logical to conclude that improving fluid power efficiency could be as simple as switching to a higher viscosity fluid. This may be the case in applications where temperatures are stable and higher volumetric efficiency can translate into increased productivity. But from a more considered standpoint, system architecture, duty cycle and operating temperatures need to be considered. While the pump may be the source of power in a hydraulic system, it is important to recognize that every element in a circuit can impact efficiency.
MSOE researchers are studying how fluid properties effect hydraulic motors. “We have identified fluids that can increase the efficiencies of hydraulic motors by as much as 18%,” Michael explains.
Collaborative research between Afton Chemical Corp. and MSOE has shown that hydraulic motor efficiency depends upon the motor type, pressure and fluid used. Correlations between a fluid’s boundary and mixed lubrication frictional properties have been found and the relative effect of these properties depends upon motor type and pressure. These studies indicate that properties other than viscosity can have a profound effect on low-speed hydraulic motor efficiency.
RohMax Oil Additives, for example, has developed and produced shear stable polymers that work well for hydraulic applications. These polymers make hydraulic fluid breakdown-resistant under the high-pressure conditions that are present in most industrial equipment.
“The viscosity aspect is the most interesting thing to me,” Smolenski says. “But a question that nags at me is how our pump sizes play into this. Can you save 5%-10% just by dropping the pump size down by 20% if the system was overdesigned?”
Michael agrees that smaller is the way to go. He explains that, to that end, there are only two ways that a smaller pump can do the same job—raise the system pressure or increase efficiency. This is because the power output of a pump is the product of flow rate (pump size) and pressure. For this reason, researchers at the CCEFP are working on projects that reduce size and improve efficiency.
4. Redesigning systems and components. The CCEFP vision has been continuously modified and refined over three years. Right now, it is working with two fundamental observations:
1. It is not well known how fluid power scales with size as measured by weight or power.
2. The competitive advantage of fluid power is greatest in mobile applications.
Working with those observations, the four CCEFP test beds address the following four areas:
1. Mobile Heavy Equipment (50 kW-500 kW): Specific research on an excavator.
2. Highway Vehicles (10 kW-100 kW): Specific research on a hydraulic hybrid passenger vehicle.
3. Mobile Human Scale Equipment (100W-1kW): Specific research on a compact rescue robot.
4. Human Assist Devices (10W-100W): Specific research on orthosis (devices that support or correct human musculoskeletal deformities and/or abnormalities).
Spanning four orders of magnitudes of power and weight, the test beds represent mobile applications where experts believe that fluid power is the best solution. In addition, they encompass current and future fluid power applications, influence adjacent applications and have the potential to ameliorate important human needs.
One specific CCEFP goal is to develop high-speed valves that can toggle quickly with fairly high flow rates and small pressure drops (practical high-speed valves).
There are promising research projects for new valve designs. One at the University of Minnesota is a pulse-width modulated rotary valve that will eliminate acceleration and deceleration and allow for switching at significantly faster speeds (5).
Another is a high-speed poppet valve at Purdue University’s Maha Fluid Power Research Center (6). the Purdue team has developed a prototype that is a pressure-balanced, three-way, two-position poppet sealing valve. While this valve development is important, the challenge is to use the valves in actual hydraulic systems, something the Purdue team is working on.
A goal of the poppet valve project is to optimize valve modeling and develop equation structures that focus on how fluid, mechanical and electromagnetic mechanisms interact in high-speed on/off valves.
Purdue is conducting hydraulic systems research in two major areas: developing energy-saving hydraulic drive systems and developing and optimizing pumps and motors. Current projects include:
• Investigating new circuit solutions
• Creating appropriate mathematical models and simulations
• Advancing actuator and drive line control concepts
• Developing methods for online prognostics and condition monitoring for agricultural and other mobile machines.
When the Purdue team recently analyzed a 5-ton miniexcavator during a typical trenching cycle, they discovered that only about 15% of the engine energy was expended in useful work, while more than 40% of the engine energy was dissipated in valve losses.
The team is working to discover what physically influences the energy dissipation in pumps and motors with the goal of developing appropriate models and then describing those influencers and their effects.
To that end, they are developing custom, in-house software tools and using them to predict the conditions and load-carrying ability of the flow through sealing and bearing gaps considering non-isothermal gap flow, the micro-motion of parts and fluid-structure interaction.
The ultimate goal is to predict energy dissipation and to find new methods for pump and motor design. The result of this research should be:
• Improved efficiency of pumps and motors
• Increased power density
• Decreased design time, with more accurate results.
Within the CCEFP, energy efficiency is viewed as a capstone goal enabled by foundational improvements in valves, pumps, motors and fluids. The organization is currently trying to create more compact fluid power systems by reducing size and weight. This will enable the development of hydraulic-powered human-scale assistive devices and wearable tools for home and industrial use.
Research at Purdue University, sponsored by the NSF and the NFPA, is centered on a method for reducing the draw of mobile hydraulic system power. Basically, the method replaces traditional flow control valves with variable displacement pumps. Instead of connecting multiple hydraulic actuators in parallel to a single pump, each actuator is controlled by smaller, individual pumps.
This approach promises lower power losses and the ability to recover energy while performing certain tasks. The system also can adjust engine speed and pump displacement to keep the engine operating close to peak efficiency. These developments, once implemented, could significantly increase fuel efficiency (7).
DIGITAL TECHNOLOGY
Purdue’s valve research and test implementation is part of a movement toward digital hydraulics in high-speed applications where existing technology is too slow and there is an opportunity to appreciably improve system efficiencies. These high-speed valves could be important components of more efficient hydraulic systems.
In addition, digital technology has the potential to spur new developments in fluid power that could include motor, pump and valve innovations. Digital valves also could significantly reduce or eliminate leakage and boost performance and efficiency.
While research is promising, many new technologies still need to prove their worth in real-world applications.
“I have had some discussion with Paul Michael trying to plant-trial these things as they come forward,” Smolenski says, “But that requires a lot of coordination at the plant level, especially when most plants are already short-handed.”
U. S. DOE monitoring and maintenance guidelines
The U.S. Department of Energy has the following recommendations for testing, identifying and maintaining hydraulic system efficiency:
• Survey the priority pumps and conduct efficiency tests.
• Identify misapplied, oversized pumps with operating points below the manufacturer’s pump curve (if available) and estimate energy savings of restoring system to its original efficiency.
• Identify pumps with flow rates of 30% or more than the BEP flow rates or with system imbalances greater than 20% (check system pressures and cycle times).
• Determine the cost-effectiveness of proposed improvements.
IN THE END…
So who stands to profit from more efficient hydraulic systems?
“End-users will benefit first because we will see cost savings immediately,” Smolenski says. “I think fluid suppliers will have an opportunity to create a great marketing tool if they are on the leading edge and they can show definite proof about the claims they’re making. Pump manufacturers will certainly benefit if they spec those kinds of fluids and can claim lower energy consumption.”
The use of fluid power is so prevalent that improvements in its use, driven by the research at a number of institutions, including the CCEFP, could have a profound impact on the way people live, especially if it can free assistive device users from dependence on electronics. While there are still many issues to resolve, more efficient hydraulic power could also be one of the primary solutions to global energy challenges.
“There’s obviously a lot more focus on cost in the manufacturing sector—on anything that can cut costs right now,” Smolenski said. “It’s also about competitiveness in general, taking all the fat out. Hydraulics still has many advantages over electronics and it has the potential to be much more cost competitive. Basically, now is just the right time for hydraulics to take center stage.”
REFERENCES
1. A straight-grade mineral oil, plus a 1% to 2% zinc-based antiwear additive package.
2. Energy Tips – Pumping Systems, Pumping System Tip Sheet #4, Sept. 2005, The U.S. Department of Energy.
3. Steven N. Herzog and Paul W. Michael, Hydraulic Fluid Selection for Improved Fuel Economy.
4. Steven N. Herzog and Paul W. Michael, Hydraulic Fluid Selection for Improved Fuel Economy.
5. Developed by a team led by professor Perry Li at the University of Minnesota.
6. Explored by a team led by John Lumkes at Purdue University.
7. This research is currently being conducted by graduate students Chris Williamson, Josh Zimmerman and Edward Hughes at Purdue University as part of the CCEFP.
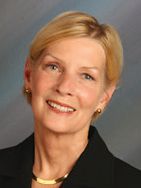
Jean Van Rensselar heads her own communication/public relations firm, Smart PR Communications, in Naperville, Ill. You can reach her at jean@smartprcommunications.com.