Eco-friendly fluids for the lubricants industry
Mike Johnson & Mark Miller | TLT Best Practices October 2010
Developing a good preventive maintenance program can go a long way toward protecting the environment.
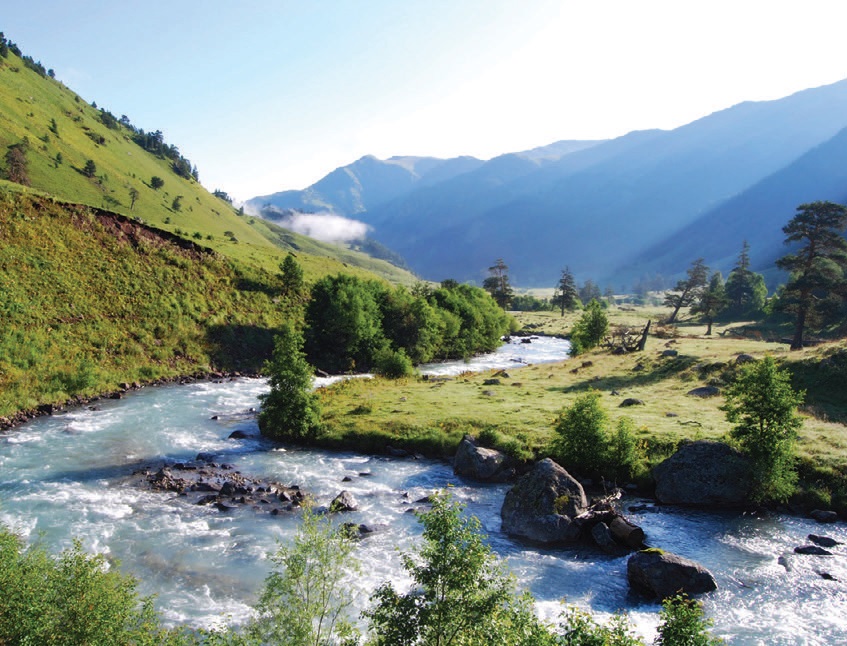
KEY CONCEPTS
•
As awareness of biodegradable fluid increases, state and federal agencies have become more lenient regarding fines and clean-up costs.
•
The two measures of degradation, primary and ultimate, differ appreciably.
•
It is essential that buyers understand precisely what degree of primary degradation exists for a finished lubricant before making a purchase.
If you’ve been reading or watching the news, you know green initiatives are taking place everywhere. Biofuels, wind energy and renewable fibers are just a few of the environmental initiatives making headlines. For the past several years, the lubricants industry has been quietly looking into eco-friendly, readily biodegradable and non-toxic fluids.
Our industry is responding because a vast quantity of industrial lubricants are finding their way into the environment. In fact, the National Oceanic and Atmospheric Administration estimates 700 million-plus gallons of petroleum enter the environment each year, more than half of which is through irresponsible and illegal disposal. Industry experts estimate that 70% to 80% of hydraulic fluids leave systems through leaks, spills, line breakage and fitting failure. Petroleum is persistent and toxic. It damages living organisms including plants, animals and marine life for many years. In addition, the Coast Guard, EPA and local governments are increasing the range of responsibility of lubricant releases by adding significant fines and cleanup costs.
In addition to regulatory pressure, equipment operators are frequently faced with clients and stakeholders concerned with petroleum hydraulic fluids entering the environment. Even a small amount of petroleum could contaminate an area and cause it to be classified as hazardous.
ENVIRONMENTAL RELEASE
As demands on lubricant systems increase, the likelihood of accidental release of fluids increases. Increased operating temperatures, pressures and working cycles shorten the life of circuit components. The single best approach to protecting the environment, as well as machining equipment and operations, is to prevent leaks and spills through good routine maintenance. A good preventative maintenance program will:
1.
Increase productivity since equipment is utilized more.
2.
Better utilize in-shop maintenance since there is less emergency work.
3.
Improve control of spare-part inventory and reduce parts usage.
4.
Reduce equipment downtime.
5.
Reduce safety hazards.
6.
Increase equipment life.
7.
Reduce fines and cleanup costs due to environmental release.
8.
Reduce downtime related to environmental release.
OIL SPILLS
Even with the best maintenance program, there is still potential for a hydraulic fluid or lubricant spill, which is why we are seeing increasing regulatory pressures from EPA, the Coast Guard and other environmental organizations. While small releases will not result in a Resource Conservation and Recovery Act (RCRA) cleanup, large spills will. All petroleum hydraulic fluid spills are reportable events. These events involve a great deal of cleanup cost, administrative procedures and punitive fines that can range from tens of thousands to hundreds of thousands of dollars.
While spilling large quantities of biodegradable hydraulic fluid is still considered under the RCRA to be a reportable event, agencies are required to evaluate biobased oils differently than petroleum-based oils. As awareness of biodegradable fluid increases, state and federal agencies are becoming more lenient regarding fines and cleanup costs. In fact, there are case studies of equipment releasing several hundred gallons of vegetable-based hydraulic fluid into environmentally sensitive areas with no fines and minimal cleanup expense. In most instances, the operator was able to continue working while cleanup efforts were underway. Since the fluids were biodegradable and non-toxic, there was no long-term negative effect to the ecosystem.
There is a common misperception that the Coast Guard or other agencies approve oils based on the oil not leaving a sheen. This is not true. The Coast Guard does not approve, recommend or endorse any fluids. Furthermore, the Coast Guard does not approve or recommend any test procedures, but, rather, follows United States statute laws. The oil sheen that is frequently referenced is inferred from the Clean Water Act as “any substance that leaves a sheen, emulsification or discoloration as a pollutant and be subject to appropriate fines and regulations governing pollutants (
1).” The Coast Guard also relies on the guidelines as outlined by equipment manufacturers and highly favors the use of biobased and biodegradable fluids.
MEASUREMENTS OF BIODEGRADATION
There is no uniform definition of environmental safety. Many factors are taken into account including biodegradability, ecotoxicity, bioaccumulation and renewability.
While throughout the U.S. and internationally there is a wide range of definitions pertaining to “environmentally preferable” status, the ASTM and the ISO have taken initiatives to clarify environmental performance and testing methodology.
The ASTM D5864 defines biodegradation as “the process of chemical breakdown or transformation of a substance caused by organisms or their enzymes.”
Figure 1 shows two commonly used measurements of biodegradation. The first is primary degradation, which measures reduction of the carbon and hydrogen bonds (C-H) in the initial solution; this is the reduction of the amount of the lubricant. The most widely used test that measures this decrease is the CEC-L-33-A-93.
Figure 1. A simplified Biodegradation Reaction Chart.
The second measurement of biodegradation is secondary degradation or ultimate degradation. This measures the evolution of CO
2 through biodegradation. The usual test for this is the OECD 301 or the ASTM D5864. The ASTM D5864 defines ultimate biodegradation as “degradation achieved when the test substance is totally utilized by microorganisms resulting in the production of CO
2, water, inorganic compounds and new microbial cellular constituents (biomass or secretions, or both).”
The ASTM D6064 has defined levels of biodegradability for both primary and secondary degradation as a function of degree of degradation, time and test methodology (
see Table 1).
Table 1. Defined levels of biodegradability for primary and ultimate degradation.
There are two widely used designations for biodegradability: readily and inherently. Readily biodegradable is defined as “breaking down rapidly in the environment by a defined amount in a specific time frame.” Inherently biodegradable means “has the propensity to breakdown with no defined amount or time frame.”
A readily biodegradable product degrades more than 80% within 21 days (primary degradation) as measured by one test type and >60% in 28 days (ultimate degradation) as measured by another test. This type of degradation is preferable because in most cases, the fluid will degrade long before environmental damage has occurred. Because of this, they require little in terms of long-term bioremediation. Vegetable-based lubricants and some synthetic products can be considered readily biodegradable.
An inherently biodegradable product breaks down very slowly over time, usually in terms of years. These types of products can persist in the environment for several years, continuing to cause substantial damage. They require long-term remediation due to environmental persistence. Typically, these products are petroleum-based such as conventional lubricants. Figure 2 illustrates the difference in degradation timing of a readily biodegradable product compared to an inherently biodegradable product.
Figure 2. Contrast of permissible degradation over time between inherently vs. readily biodegradable products.
Looking at Figure 2, it is easy to see the difference between a readily biodegradable product and an inherently biodegradable one.
Figure 3 shows the range of biodegradability for several generically defined types of basestocks, according to the CEC-L-33-A-93 test method (
2). It is essential that the buyer understand precisely what degree of degradation exists for a finished lubricant before making a purchase.
Figure 3. Range of biodegradability for several commonly referenced basestocks.
It is also essential that those with responsibility to market or select fluids for their biodegradability characteristics clearly understand the terminology and be careful to avoid confusion within marketing literature. A common error has occurred wherein products have been assigned the “ultimately biodegradable” status and described as having the highest biodegradability classification, per ASTM D5864.
Following are four key points that must be clarified:
1.
Ultimate biodegradation is the evolution of the end product of biodegradation (CO
2 and H
2O mostly for lubricants). The ASTM D5864 clearly defines ultimate biodegradation as “degradation achieved when the test substance is totally utilized by microorganisms resulting in the production of CO
2, water, inorganic compounds and new microbial cellular constituents (biomass or secretions, or both).”
2.
ASTM D5864 Standard Test Method for Determining Aerobic Aquatic Biodegradation of Lubricants or their Components is a test method, not a hierarchy.
3.
Section 2.1 of ASTM D5864 is Section 2 “Referenced Documents,” 2.1 “ASTM Standards.” Nothing to do with levels or biodegradability or ultimate anything.
4.
ASTM D6046—D2 Standard Classification of Hydraulic Fluids for Environmental Impact does create an environmental hierarchy. It does define ultimate biodegradation in Section 3. 1.22, which not surprisingly is the same as in ASTM D5864.
ECOTOXICITY
Another measurement to determine environmental effect of a lubricant is ecotoxicity. Historically, tests for ecotoxicity have concentrated on the aquatic environment with a number of standard test procedures. Most typically, the tests are for acute toxicity. This is a measurement of the concentration required to kill various organisms over a short period of time, ranging from 24-96 hours.
Depending on the tests and its end points, the toxicity of a fluid is described by a loading rate in parts per million (ppm) of fluid that has a 50% effect (EL50) or causes 50% mortality (LL50) after the stated time. In other words, it defines the contaminant concentration at which half of the sample organisms die.
The ASTM D6064 has defined levels of ecotoxicity, as shown in Table 2.
Table 2. ASTM Ecotoxicty Classification.
While the most benign level, per the ASTM, is 1,000 ppm, well-formulated environmentally preferable products can have LL50 rating in excess of 1,000 ppm.
PERFORMANCE OF BIOFLUIDS
There is a wide variety of performance levels among biodegradable products. When an environmentally preferable product is required outside common temperature ranges, a biodegradable synthetic is usually required. While offering biodegradation, these products can operate in temperatures in excess of 400 F and still offer long fluid life. As would be expected, these products are significantly more expensive.
Care must be taken in choosing the appropriate product for the specific application. Responsible Environmentally Preferable Product (EPP) suppliers can clearly indicate their definition of environmentally preferable. The Federal Trade Commission has been very specific in its requirements for environmental claims and states, “look for evidence that give some substance to the claim, the additional information that explains why the product is environmentally friendly.”
Many would be EPP suppliers use misleading environmental claims such as “inherently biodegradable” or “food grade.” Suppliers should be able to support performance claims with testing data. These data can include standard industry tests (ASTM), field testing and equipment manufacturer tests.
ISO 6743/4 ENVIRONMENTAL HYDRAULIC FLUIDS CLASSIFICATION
There are four main classifications of environmentally preferable fluids as defined by ISO 6743/4: HETG-vegetable-based, HEPG-glycol-based, HEES-ester-based and HEPR-other synthetic-based.
Conventional Vegetable-based Fluids (HETG). Early work in the field focused on lubricants made from vegetable oils (natural esters or HETG). Vegetable-based fluids are readily biodegradable, but performance is most suited to cool and dry operating conditions. Equipment operators must take care to ensure that such parameter boundaries are not violated.
When HETG biodegradable oils are blended with vegetable oil, the resulting vegetable-based fluids can only withstand operating temperatures under 180 F. As a result, vegetable-based fluids, when exposed to heat, have a limited life expectancy. Another issue with vegetable-based fluids is that they become unstable when exposed to wet environments or contaminated with water.
Synthetic Esters (HEES). The second phase of biodevelopment focused on synthetic esters (HEES). This classification of fluids is one of the most common synthetic biodegradables in the market. The strengths and weaknesses of synthetic esters are well known and well documented.
Similar to vegetable-based fluids, synthetic esters are readily biodegradable. Synthetic esters also perform well in standardized oxidation tests, which determine the life of the lubricant under test conditions. When new, clean, cool and dry, synthetic esters offer excellent performance.
Esters are synthesized by the reaction of a triglyceride (typically vegetable oil) with an acid and an alcohol. This reaction makes the ester and forms water and heat as a byproduct. Expressed chemically:
Vegetable oil + alcohol + acid ↔ synthetic ester + water + heat.
The double-headed arrow indicates that the reaction goes both directions. Therefore, when water is present, the reverse reaction occurs and is known as hydrolysis. This reforms the alcohols, acids and triglycerides. In machine service, the acids can cause rust and wear, seal degradation and corrosion to yellow metals. Consequently, ester-based fluids must either be maintained in a cool, dry state to obtain maximum performance.
PAO-based Fluids (HEPR). The remaining classification is the HEPR group. This classification embodies fluids derived from PAO basestocks such as bio-polyolefin. One distinct advantage of PAO-based fluids is that they can be tailor-made to fit specific requirements. These fluids do not hydrolyze (break down when mixed with water) and, as such, are much more stable in hot, wet conditions. Bio-olefins are typically compatible with Buna N, viton and all common elastomers, as well as adhesives used in filters. A drawback is its high price base vs. other fluids.
SUMMARY
Millions of gallons of petroleum products are improperly disposed of or accidentally lost into the environment each year. Regulations are imposed on producers by federal, state and local authorities with increasingly costly penalties associated with the losses.
Producers and users of lubricants are applying vigilance to reduce losses and reduce risk associated with eventual losses. There are multiple classifications of fluids that fit the biodegradability requirement that have varying degrees of performance.
In an effort to improve environmental performance, manufacturers, miners and ocean-going vessels must choose lubricants that can offer optimum long-term performance and environmental safety. The real proof of performance is how the fluids withstand the conditions under which they operate.
REFERENCES
1.
The Federal Clean Water Act, Section 311.
2.
Shubkin, R. and Rudnick, L. (1999),
Synthetic Lubricants and High Performance Functional Fluids, 2nd Edition, p. 815. Marcel Dekker, AG.
Mike Johnson, CLS, CMRP, MLTII, MLA1, is the principal consultant for Advanced Machine Reliability Resources, in Franklin, Tenn. You can reach him at mike.johnson@precisionlubrication.com.
Mark Miller is the CEO of Terresolve Technologies in Cleveland. You can reach him at mmiller@terresolve.com.